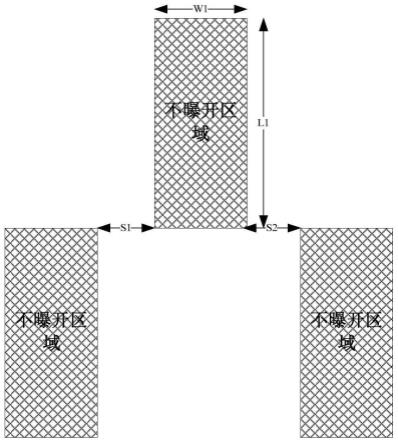
1.本发明属于微电子技术领域,具体涉及一种基于光学显微镜光刻线宽测试结构及检验方法。
背景技术:2.随着集成电路特征尺寸及线宽的不断减小,片上的几何尺寸和形状偏差对集成电路成品率的影响日益增加,通常认为集成电路中线边缘粗糙度、侧壁夹角、侧壁轮廓及线宽等参数是需要关注的,如文献1“http://www.veeco.com/products/metrology and instrumentation.”中所述的,尤其是各层的关键尺寸大小对于得到高良率的产品至关重要,如图1所示,因此需要在生产过程中有更快更精准的的测量方法,以及时发现工艺过程中的异常,并改善工艺,防止工艺异常对产品的良率的影响扩大化。
3.在目前的数字和模拟器件工艺流程中,cd(critical dimension)的测量已经成为生产线中在线(in-line)监控关键工艺结构的重要手段,这当中包括了扫描电子显微镜cd-sem、ocd、光学显微镜等,其中cd-sem主要应用在光刻和刻蚀工艺之后的关键尺寸测试,重点监测逻辑区域(logic)以及静态存储区域(sram,static radom access memory)的线宽和微观结构。ocd主要利用光散射原理来测量关键尺寸,如文献2“半导体制造中测量和检测技术概述”中所述的,它不仅用来测试cd,更多的是测量深度、高度等微观结构,在现在的生产过程中,ocd更加侧重于2d、3d图形的测试,在90nm工艺节点以下工艺中,ocd已经趋于成熟。
4.在几何学上通常将线宽定义为样本两个侧面之间的垂直距离,随着关键尺寸越来越小,容错率也越小,因此必须要尽可能的量测所有产品的线宽,如图2所示,可见关键尺寸的量测重要性越发关键,而以条(line)为例,传统集成电路线宽cd测试图形为3个”l”形状的cd bar测试结构,如图3所示,通过cd-sem对中间的"l"形结构进行测试,测量“l”形结构的两条侧边的垂直距离的间距,从而确认线宽尺寸的大小是否满足在线规范。
5.cd-sem在集成电路制造生产中,一直起着至关重要的作用,基本所有的光刻和刻蚀工艺后,都会有cd-sem测试步骤,它可以测试多种微观结构的各种尺寸,如线宽、孔直径、边缘形貌等,它对测试结果没有复杂的要求,可以在每一步工序后观测不同功能区域的不同图形结构,确认该结构是否满足设计需求,但是由于生产环境的复杂性以及机台的不稳定性,采集到的图像会不可避免的产生运动模糊或失焦模糊,如图4所示,需要相关设备人员定期进行调节,这在一定程度上会降低生产效率。
6.ocd是指光学测试cd,主要是通过光谱散射,与测试膜厚的椭圆偏振光谱仪的原理相同,如文献3“大规模集成电路中关键尺寸测量方法与应用的重要性研究”中所述的,它可以一次性测试开口宽度、深度、侧壁角度以及侧壁各层的宽度等信息,而这些信息cd-sem恰恰无法得到,同时在cd-sem测试的仅仅是1~2微米的图形,其测量重复性差,误差大,特别是在测量193nm的光刻胶关键尺寸时,cd-sem对光刻胶的坍缩影响使其无法进行重复多次测试,而ocd使用的是光学散射效应,就不存在该问题。但是ocd也存在一些局限性,例如部
分型号机台要求测试结构必须是栅格结构,并且大小也有特定要求,同时在测试时也需要较多的测试结构基本信息,如目标尺寸、结构高度、具体膜质结构等,测试的便利性不如cd-sem。
7.目前主流线宽检测技术主要采用cd-sem及ocd技术,但这两种技术由于本身测试特点都会对产能产生影响,对于集成电路生产制造而言这并不是最优的解决方案,尤其对线宽达到2μm及以上层次,采用这两种技术测试cd反而会影响产能。
技术实现要素:8.为了克服上述现有技术的缺点,本发明的目的在于提供一种基于光学显微镜光刻线宽测试结构及检验方法,以解决现有技术测试,尤其对线宽达到2μm及以上层次测试cd影响产能的问题。
9.为了达到上述目的,本发明采用以下技术方案予以实现:
10.本发明公开了一种基于光学显微镜光刻线宽测试结构,包括两组监控结构,所述监控结构包括cd上限观察图形和cd下限观察图形;cd上限观察图形和cd下限观察图形均包括若干个长方形结构,且若干个长方形结构构成品字形。
11.优选地,所述cd上限观察图形的长方形结构的长大于宽,上方的长方形结构与下方的长方形结构的水平间距相等,且水平间距等于监控层光刻线宽规范。
12.优选地,所述cd下限观察图形的长方形结构的长大于宽,上方的长方形结构与下方的长方形结构的水平间距相等,且水平间距等于监控层光刻线宽规范。
13.优选地,所述cd上限观察图形和cd下限观察图形的属性相反。
14.优选地,当层光刻图形为条时,cd上限观察图形为不曝光的区域,cd下限观察图形为曝光的区域。
15.本发明还公开了一种基于光学显微镜光刻线宽检验方法,包括:
16.观察cd上限观察图形,当构成品字形的下方左侧的长方形结构的内侧边与上方的长方形结构的左侧边在一条直线上,下方右侧的长方形结构的内侧边与上方的长方形结构的右侧边在一条直线上时,则判定当层线条图形的尺寸达到规定的上限;
17.观察cd下限观察图形,当构成品字形的下方左侧的长方形结构的内侧边与上方的长方形结构的左侧边在一条直线上,下方右侧的长方形结构的内侧边与上方的长方形结构的右侧边在一条直线上时,则判定当层线条图形的尺寸达到规定的下限。
18.优选地,所述cd上限观察图形中上方的长方形结构与下方的长方形结构的水平间距相等,水平间距为零时,则判定当层线条图形的尺寸达到规定的上限。
19.优选地,所述cd下限观察图形中上方的长方形结构与下方的长方形结构的水平间距相等,水平间距为零时,则判定当层线条图形的尺寸达到规定的下限。
20.与现有技术相比,本发明具有以下有益效果:
21.本发明提出的一种基于光学显微镜的光刻线宽测试结构,cd上限观察图形和cd下限观察图形均包括若干个长方形结构,且若干个长方形结构构成品字形,结构简单,光刻版设计及工艺实现容易,该结构只需要设计若干个同尺寸的长方形即可实现,同时大尺寸的长方形在工艺实现中也避免了小尺寸图形易出现的漂胶等异常;同时显微镜检验便捷,可以通过检验品字型结构上下两个长方形的侧边是否在一条直线上,来判别该层线宽是否超
过范围,其图形和结构设计科学合理,辨识度高,可满足光刻工艺线宽≥2μm的层次在线检验的要求,为高质量完成光刻工艺打下基础。与传统的lcd bar结构相比,该结构可以实现仅使用光学显微镜的情况下,对光刻线宽大小进行判别,不额外引入其他专用设备,同时提升了线宽检测步骤的效率,提升了产能,具有制作效率高,成本低等特点。
22.进一步地,长方形结构的长大于宽,上方的长方形结构与下方的长方形结构的水平间距相等,且水平间距等于监控层光刻线宽规范,在显微镜观测中,长方形结构相较于正方形更加容易辩识;这样设置是由于在显微镜中观测直线时更加容易辨别,当上方的长方形结构与下方的长方形结构侧边在一条直线时,就可以很方便的辨别该层线宽已达到该层的规范上限或下限。
附图说明
23.图1为集成电路关键参数图;
24.图2为线宽测试图形图;
25.图3为传统条cd测试图形(line);
26.图4为cd-sem图像异常情况图;其中a为运动模糊图像,b为失焦模糊图像;
27.图5为本发明cd上限观察图形结构示意图;
28.图6为本发明cd下限观察图形结构示意图。
具体实施方式
29.为了使本技术领域的人员更好地理解本发明方案,下面将结合本发明实施例中的附图,对本发明实施例中的技术方案进行清楚、完整地描述,显然,所描述的实施例仅仅是本发明一部分的实施例,而不是全部的实施例。基于本发明中的实施例,本领域普通技术人员在没有做出创造性劳动前提下所获得的所有其他实施例,都应当属于本发明保护的范围。
30.需要说明的是,本发明的说明书和权利要求书及上述附图中的术语“第一”、“第二”等是用于区别类似的对象,而不必用于描述特定的顺序或先后次序。应该理解这样使用的数据在适当情况下可以互换,以便这里描述的本发明的实施例能够以除了在这里图示或描述的那些以外的顺序实施。此外,术语“包括”和“具有”以及他们的任何变形,意图在于覆盖不排他的包含,例如,包含了一系列步骤或单元的过程、方法、系统、产品或设备不必限于清楚地列出的那些步骤或单元,而是可包括没有清楚地列出的或对于这些过程、方法、产品或设备固有的其它步骤或单元。
31.下面结合附图对本发明做进一步详细描述:
32.目前主流线宽检测技术主要采用cd-sem及ocd技术,但这两种技术由于本身测试特点都会对产能产生影响,对于集成电路生产制造而言这并不是最优的解决方案,尤其对线宽达到2μm及以上层次,采用这两种技术测试cd反而会影响产能。为了解决这一问题提升产能,本发明提出了一种基于光学显微镜的光刻线宽测试结构设计及检验方法,通过该结构及方法可以实现在不使用专用线宽测试设备的情况下,对光刻工艺线宽≥2μm的层次进行在线检验,在保障工艺稳定的情况下,提高了生产线的产能。
33.为了避免显微镜检验无法检测及判定传统cd bar监控图形的问题,即使cd bar尺
寸大小能够在显微镜下分辨出来,也无法定量的判断cd的大小,本发明专利提出了一种基于光学显微镜的光刻线宽测试结构及检验方法。
34.一种基于光学显微镜光刻线宽测试结构,包括两组监控结构,所述监控结构包括cd上限观察图形和cd下限观察图形;cd上限观察图形和cd下限观察图形均包括若干个长方形结构,且若干个长方形结构构成品字形。所述cd上限观察图形和cd下限观察图形的长方形结构均长大于宽,上方的长方形结构与下方的长方形结构的水平间距相等,且水平间距等于监控层光刻线宽规范。且cd上限观察图形和cd下限观察图形的属性相反,当层光刻图形为条时,cd上限观察图形为不曝光的区域,cd下限观察图形为曝光的区域;品字形结构简单,光刻版设计及工艺实现容易,该结构只需要设计若干个同尺寸的长方形即可实现,同时大尺寸的长方形在工艺实现中也避免了小尺寸图形易出现的漂胶等异常;同时显微镜检验便捷,可以通过检验品字型结构上下两个长方形的侧边是否在一条直线上,来判别该层线宽是否超过范围,其图形和结构设计科学合理,辨识度高,可满足光刻工艺线宽≥2μm的层次在线检验的要求,为高质量完成光刻工艺打下基础。与传统的lcd bar结构相比,该结构可以实现仅使用光学显微镜的情况下,对光刻线宽大小进行判别,不额外引入其他专用设备,同时提升了线宽检测步骤的效率,提升了产能,具有制作效率高,成本低等特点;且长方形结构的长大于宽,上方的长方形结构与下方的长方形结构的水平间距相等,且水平间距等于监控层光刻线宽规范,在显微镜观测中,长方形结构相较于正方形更加容易辩识;这样设置是由于在显微镜中观测直线时更加容易辨别,当上方的长方形结构与下方的长方形结构侧边在一条直线时,就可以很方便的辨别该层线宽已达到该层的规范上限或下限。
35.本发明还公开了一种基于光学显微镜光刻线宽检验方法,包括:
36.观察cd上限观察图形,当构成品字形的下方左侧的长方形结构的内侧边与上方的长方形结构的左侧边在一条直线上,下方右侧的长方形结构的内侧边与上方的长方形结构的右侧边在一条直线上时,则判定当层线条图形的尺寸达到规定的上限;
37.观察cd下限观察图形,当构成品字形的下方左侧的长方形结构的内侧边与上方的长方形结构的左侧边在一条直线上,下方右侧的长方形结构的内侧边与上方的长方形结构的右侧边在一条直线上时,则判定当层线条图形的尺寸达到规定的下限。
38.参见图5、图6,本发明公开一种基于光学显微镜的光刻线宽测试结构及检验方法。本测试结构呈现一种品字形cd监控结构,品字形cd监控结构由3个同样的长方形图形组成,同时要有2组监控结构,分别是cd上限观察图形,参见图5,长方形结构的长与宽尺寸分别是l1与w1,其中l1>w1,上方的长方形与下方的的长方形水平间距尺寸是s1与s2,其中s1=s2=监控层光刻线宽规范。cd下限观察图形,参见图6,长方形结构的长与宽尺寸分别是l2与w2,其中l2>w2,上方的长方形与下方的的长方形水平间距尺寸是s3与s4,其中s3=s4=监控层光刻线宽规范。cd上限观察图形和cd下限观察图形属性是相反的,其中l1=l2,w1=w2,s1=s2=s3=s4,以当层光刻图形为条(line)时为例,cd上限观察图形的3个长方形图形均为不曝光的区域,形成一个长方形的胶条,当上方的长方形与下方的长方形水平间距s1=s2=0时,说明该层图形超过规范上限,cd下限观察图形的3个长方形图形均为曝光的区域,形成一个长方形的曝开区,当上方的长方形区与下方的长方形区域水平间距s3=s4=0时,说明该层图形超过规范下限。
39.实施例1:
40.如图5及图6所示,品字形cd监控图形的中的长方形宽度w1=w2=4μm,长方形的长度l1=l2=16μm,上方的长方形与下方的的长方形水平间距尺寸s1=s2=s3=s4=0.2μm。当在显微镜中看到图5图形中的s1与s2缩短至0μm时,即上下两个长方形图形的两条侧边在一条直线上时,就可以判断出当层线条(line)图形的尺寸达到规定的上限,当在显微镜中看到图6图形中的s3与s4缩短至0μm时,即上下两个长方形图形的两条侧边在一条直线上时,就可以判断出当层线条(line)图形的尺寸达到规定的下限。
41.实施例2:
42.如图5及图6所示,品字形cd监控图形的中的长方形宽度w1=w2=4μm,长方形的长度l1=l2=16μm,上方的长方形与下方的的长方形水平间距尺寸s1=s2=s3=s4=0.4μm。当在显微镜中看到图5图形中的s1与s2缩短至0μm时,即上下两个长方形图形的两条侧边在一条直线上时,就可以判断出当层间隙(space)图形的尺寸达到规定的下限,当在显微镜中看到图6图形中的s3与s4缩短至0μm时,即上下两个长方形图形的两条侧边在一条直线上时,就可以判断出当层间隙(space)图形的尺寸达到规定的上限。
43.以上内容仅为说明本发明的技术思想,不能以此限定本发明的保护范围,凡是按照本发明提出的技术思想,在技术方案基础上所做的任何改动,均落入本发明权利要求书的保护范围之内。