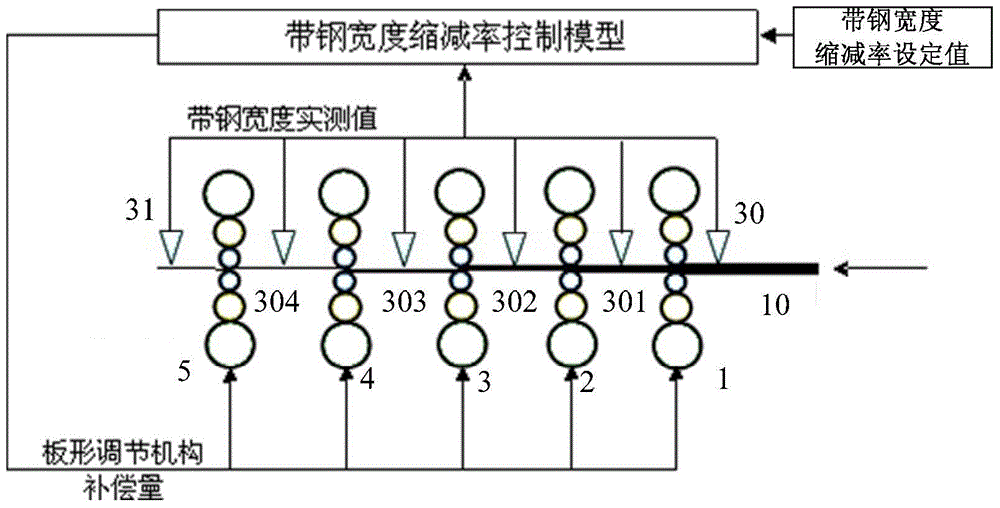
本发明涉及专门适用于金属轧机或其加工产品的控制设备或方法,尤其涉及一种防止薄带钢冷轧过程特别是冷连轧过程断带的控制方法。
背景技术:在冷轧薄带生产实践中,由于来料带钢边部缺陷、或者带钢边部轧裂、或者带钢边部张应力过大等原因,薄带钢冷轧过程中断带现象时有发生,轻则造成冷轧生产过程中断、钢卷废品,重则造成轧辊报废甚至设备损坏,严重影响薄带钢冷轧机组产能和产品质量。冷轧轧制过程中轧制工艺参数选择不合理,使得冷轧过程中带钢边部偏紧,宽度缩减量偏大,是造成冷轧过程薄带钢边裂断带的主要因素之一。中国发明专利“一种控制冷轧薄带钢断带的动态增厚轧制法”(发明专利号:ZL200510046497.1授权公告号:CN100411760C)公开了一种控制冷轧薄带钢断带的动态增厚轧制法,利用冷连轧机现有的焊缝跟踪系统,准确测量带钢的焊缝位置,其特征是针对焊缝前后带钢容易发生断带的现象,在焊缝前后50米范围内,将带钢厚度增加到原目标厚度的1.0-1.5倍,并通过两个楔形轧制过程来实现局部动态增厚轧制,降低薄料生产时的断带率。显然,该发明的方法仅适用于降低带钢头尾断带率。中国发明专利申请“一种防止高硅带钢断带的冷轧方法”(发明专利申请号:201010562032.2公开号:CN102476131A)公开了一种防止高硅带钢断带的冷轧方法,高硅带钢的Si含量≥2.3wt%,开始冷轧时,入口带钢温度大于45℃;冷轧过程中对带钢喷射乳化液,轧制方向入口乳化液流量小于等于3500升/分钟,轧制方向出口乳化液流量1500~4000升/分钟,在保证工艺润滑的前提下确保带钢温度在45℃以上。该发明的方法同样主要用于减少带钢头尾断带。日本专利JP10005838A提出了一种冷轧过程防止带钢发生边裂的方法:在检测带钢轧后和轧前边缘降率的基础上,通过调整轧机的板形调节机构,将带钢轧后和轧前边缘降率偏差控制到一定值以上、或者降低带钢边部张应力,以达到抑制带钢边裂的目的。但是,基于射线检测带钢厚度原理的边缘降检测仪通常比较昂贵,并且不容易检测准确。日本专利JP59033006A提出了一种降低冷轧过程带钢断带发生率的方法:在冷轧机出口配置一套带钢边部裂纹长度检测仪,用于实时检测轧后带钢的边部裂纹长度。当实测带钢边部裂纹长度超过一定值时,通过调整轧机主传动或轧机压下机构,减小带钢张力,以降低断带发生的可能性。但是,实时检测轧后带钢的边部裂纹长度也存在检测设备成本高和检测精度低的问题,同时,调整带钢张力还容易影响带钢厚度控制精度。
技术实现要素:本发明的目的是提供一种防止薄带钢冷轧过程断带的控制方法,可以通过检测带钢冷轧前后的宽度,根据宽度缩减率偏差对各机架的板形调节机构进行补偿,从而降低带钢边部张应力以避免断带的发生,减少薄带钢冷轧过程断带发生率,提高冷轧机组的产能。本发明解决上述技术问题所采用的技术方案是:一种防止薄带钢冷轧过程断带的控制方法,用于多机架冷连轧机组以及单机架冷轧机组的轧制过程控制系统,其特征在于包括以下步骤:(a)根据带钢的钢种、厚度、宽度以及轧制工艺参数,确定宽度缩减率给定值Rw_set;(b)通过设置在机组入口和出口的带钢宽度检测仪,实时检测冷轧机组的入口带钢宽度实测值和出口带钢宽度实测值;(c)确定带钢宽度缩减率的实际值Rw_act;(d)比较带钢的宽度缩减率实际值Rw_act与宽度缩减率给定值Rw_set的大小;若Rw_act>Rw_set,则转步骤(e);否则,返回步骤(b)执行下一检测循环;(e)确定各机架的带钢宽度缩减率偏差ΔRwi;(f)根据各机架的带钢宽度缩减率偏差ΔRwi确定各机架的板形调节机构补偿量;所述的板形调节机构补偿量包括各机架轧机板形调节机构的工作辊弯辊力、中间辊弯辊力和中间辊窜辊量的实时补偿量,可依公式(1)计算得到ΔFwi=-αFwiΔRwi/KRwiFwiΔFmi=-αFmiΔRwi/KRwiFmi(1)ΔIMRi=-αIMRiΔRwi/KRwiIMRi式中,i=1,2,…,n,其中,n为冷连轧机组成机架总数;ΔFwi、ΔFmi、ΔIMRi分别为第i机架的工作辊弯辊力、中间辊弯辊力和中间辊窜辊量的实时补偿量,ΔRwi为第i机架的宽度缩减率偏差;αFwi、αFmi、αIMRi分别为第i机架板形调节机构的工作辊弯辊力、中间辊弯辊力、中间辊窜辊量补偿量优先系数,可根据轧机各个板形调节机构的响应速度及其对带钢宽度缩减率影响效率的差异确定,应满足以下关系:αFwi+αFmi+αIMRi=1.0,0≤αFwi≤1.0,0≤αFmi≤1.0,0≤αIMRi≤1.0;KRwiFwi、KRwiFmi、KRwiIMRi分别为第i机架的轧机工作辊弯辊力、中间辊弯辊力、中间辊窜辊量对第i机架轧机带钢宽度缩减率的影响系数,可根据带钢的钢种、厚度、宽度以及轧制工艺参数确定;(g)将各机架轧机板形调节机构工作辊弯辊力、中间辊弯辊力和中间辊窜辊量的实时补偿量,发送到冷轧机组基础自动化级,对各机架的板形调节机构进行补偿,通过降低带钢边部张应力避免断带的发生。本发明的防止薄带钢冷轧过程断带的控制方法的另一种技术方案,适用于至少2台机架轧机组成的冷连轧机组,其特征在于:所述的宽度缩减率给定值Rw_set包括各机架的宽度缩减率给定值Rwi_set,i=1,2,…,n;所述的入口带钢宽度实测值和出口带钢宽度实测值包括各机架的入口带钢宽度和出口带钢宽度实测值{W0i_act,W1i_act},i=1,2,…,n;所述的带钢宽度缩减率实际值Rw_act包括带钢经第i机架轧制后的带钢宽度缩减率实际值Rwi_act;带钢宽度缩减率实际值Rw_act可根据第i机架的入口带钢宽度和出口带钢宽度实测值,依公式(2)确定Rwi_act=(W0i_act-W1i_act)/W0i_act(2)式中,i=1,2,…,n,n为冷连轧机组成机架总数;Rwi_act为第i机架轧制后的宽度缩减率实际值;W0i_act为第i机架入口带钢宽度实测值;W1i_act为第i出口带钢宽度实测值;所述的步骤(d)比较第i机架轧机轧制后的宽度缩减率实际值Rwi_act与该机架宽度缩减率给定值Rwi_set的大小,若Rwi_act>Rwi_set,则转步骤(e);否则,返回步骤(b)执行下一检测循环;所述的步骤(e)根据第i机架轧机轧制后的宽度缩减率实际值Rwi_act与该机架的宽度缩减率给定值Rwi_set,确定第i机架的宽度缩减率偏差ΔRwi=Rwi_act-Rwi_set,式中,Rwi_act为第i机架轧机轧制后的宽度缩减率实际值,Rwi_set为第i机架的宽度缩减率给定值。本发明的防止薄带钢冷轧过程断带的控制方法的一种优选的技术方案,其特征在于:所述的宽度缩减率给定值Rw_set是带钢经过冷轧机组所有机架轧制后的宽度缩减率给定值Rw_set;所述的入口带钢宽度实测值和出口带钢宽度实测值是冷轧机组的入口带钢宽度实测值W0_act和机组出口带钢宽度实测值W1_act;所述的步骤(c)根据冷轧机组的入口带钢宽度实测值和机组出口带钢宽度实测值,依公式(3)确定带钢经冷轧机组轧制后的宽度缩减率实际值:Rw_act=(W0_act-W1_act)/W0_act(3)其中,Rw_act为冷轧机组轧制后的宽度缩减率实际值,W0_act为冷轧机组入口带钢宽度实测值,W1_act为冷轧机组出口带钢宽度实测值;所述的步骤(e)根据经过冷轧机组所有机架轧制后的宽度缩减率实际值Rw_act与宽度缩减率给定值Rw_set,确定冷轧机组整体的带钢宽度缩减率偏差ΔRw=Rw_act-Rw_set;然后将冷轧机组整体的带钢宽度缩减率偏差ΔRw分配到各个机架,得到第i机架的宽度缩减率偏差分配值ΔR'wi=βi(Rw_act-Rw_set),式中,βi为第i机架的带钢宽度缩减率分配系数,βi应满足以下关系:所述的步骤(f)使用第i机架的宽度缩减率偏差分配值ΔR'wi替代第i机架的带钢宽度缩减率偏差ΔRwi,计算确定各机架的板形调节机构补偿量。本发明的有益效果是:1.本发明的防止薄带钢冷轧过程断带的控制方法,通过检测带钢冷轧前后的宽度,对各机架的板形调节机构进行补偿,降低带钢边部张应力以避免断带的发生,从而减少薄带钢冷轧过程断带发生率,提高冷连轧生产过程的稳定性,提高冷轧机组的产能。2.本发明的防止薄带钢冷轧过程断带的控制方法,利用带钢宽度检测仪检测带钢冷轧前后的宽度,通过冷轧机组的现有的计算机轧制过程控制系统,实现板形调节机构进行补偿,其检测技术成熟,准确度高,设备投入成本低,可以在防止薄带钢冷轧过程断带,提高冷轧生产过程稳定性和成材率,降低生产成本的同时,在一定程度上提高冷轧带钢宽度控制精度。附图说明图1是本发明的防止薄带钢冷轧过程断带的控制方法用于冷轧机组结构示意图;图2是本发明的防止薄带钢冷轧过程断带的控制方法用于冷连轧机组结构示意图;图3是本发明的防止薄带钢冷轧过程断带的控制方法用于单机架冷轧机组的示意图;图4是运用本发明的控制方法前后冷连轧过程断带发生率示意图。具体实施方式为了能更好地理解本发明的上述技术方案,下面结合附图和实施例进行进一步地详细描述。实施例1:本发明的防止薄带钢冷轧过程断带的控制方法的一个实施例如图1所示,该实施例用于五机架冷轧机组的轧制过程控制系统。在本实施例中,在5机架轧机组成的冷轧机组的入口和出口,分别配置入口带钢宽度检测仪30和出口带钢宽度检测仪31,实时检测冷轧机组入口和出口沿带钢10的长度方向上各位置处的宽度实测值。控制过程包括以下步骤:(a)根据带钢的钢种、厚度、宽度以及轧制工艺参数,确定经过冷轧机组所有机架轧制后的宽度缩减率给定值Rw_set;宽度缩减率给定值Rw_set可以通过轧制实验或理论模型模拟计算获得。(b)使用入口带钢宽度检测仪30和出口带钢宽度检测仪31,实时检测冷轧机组的入口带钢宽度实测值W0_act和机组出口带钢宽度实测值W1_act;(c)根据冷轧机组的入口带钢宽度实测值W0_act和机组出口带钢宽度实测值W1_act,依公式(3)确定带钢经冷轧机组轧制后的宽度缩减率实际值:Rw_act=(W0_act-W1_act)/W0_act(3)其中,Rw_act为冷轧机组轧制后的宽度缩减率实际值,W0_act为冷轧机组入口带钢宽度实测值,W1_act为冷轧机组出口带钢宽度实测值;(d)比较经过冷轧机组所有机架轧制后的宽度缩减率实际值Rw_act与宽度缩减率给定值Rw_set的大小。若Rw_act>Rw_set,则说明冷轧过程中带钢边部偏紧,边部张应力过大,有发生断带的危险,需要转步骤(e),通过调整各个机架轧机板形调节机构,减小Rw_act与Rw_set偏差,使带钢边部变松,以避免断带的发生;否则,不需要进行调整,直接返回步骤(b)执行下一检测循环;(e)根据经过冷轧机组所有机架轧制后的宽度缩减率实际值与宽度缩减率给定值,确定第i机架的宽度缩减率偏差分配值ΔR'wi=βi(Rw_act-Rw_set),式中,Rw_act为宽度缩减率实际值,Rw_set为宽度缩减率给定值,βi为第i机架的带钢宽度缩减率分配系数,βi应满足以下关系:其中,n为冷轧机组成机架总数,在该实施例中,n=5。当带钢宽度缩减率较大时,如果完全通过某一个机架消除Rw_act与Rw_set偏差,则有可能会造成该机架出口板形剧烈变化,不利于保持轧制过程稳定。因此,本步骤将冷轧机组整体的带钢宽度缩减率偏差ΔRw=Rw_act-Rw_set,按照一定的比例,分配到各个机架,由各个机架分担消除带钢宽度缩减率偏差。(f)根据第i机架的宽度缩减率偏差分配值,依公式(1’)计算第i机架轧机板形调节机构工作辊弯辊力、中间辊弯辊力和中间辊窜辊量的实时补偿量,ΔFwi=-αFwiΔR'wi/KRwiFwiΔFmi=-αFmiΔR'wi/KRwiFmi(1’)ΔIMRi=-αIMRiΔR'wi/KRwiIMRi式中,ΔFwi、ΔFmi、ΔIMRi分别为第i机架轧机板形调节机构工作辊弯辊力、中间辊弯辊力和中间辊窜辊量的实时补偿量,ΔR'wi为第i机架的宽度缩减率偏差分配值;αFwi、αFmi、αIMRi分别为第i机架板形调节机构的工作辊弯辊力、中间辊弯辊力、中间辊窜辊量补偿量优先系数,可根据轧机各个板形调节机构的响应速度及其对带钢宽度缩减率影响效率的差异确定,应满足以下关系:αFwi+αFmi+αIMRi=1.0,0≤αFwi≤1.0,0≤αFmi≤1.0,0≤αIMRi≤1.0。由于冷轧机的各个板形调整时段都能够影响带钢的宽度缩减率,因此,本步骤需要根据轧机各个板形调节机构的响应速度、对带钢宽度缩减率影响效率的差异,赋予各个板形调节机构各自不同的补偿量优先系数。KRwiFwi、KRwiFmi、KRwiIMRi分别为第i机架轧机工作辊弯辊力、中间辊弯辊力、中间辊窜辊量对第i机架轧机带钢宽度缩减率的影响系数,可根据带钢的钢种、厚度、宽度以及轧制工艺参数,通过轧制实验或理论模型模拟计算方法获得影响系数KRwiFwi、KRwiFmi和KRwiIMRi。(g)将各机架轧机板形调节机构工作辊弯辊力、中间辊弯辊力和中间辊窜辊量的实时补偿量,发送到冷轧机组基础自动化级,通过对各机架的板形调节机构进行补偿,降低带钢边部张应力避免断带的发生。实施例2:本发明的防止薄带钢冷轧过程断带的控制方法的另一个实施例如图2所示,该实施例用于五机架冷轧机组的轧制过程控制系统。在本实施例中,在5机架轧机组成的冷轧机组的入口和出口,分别配置入口带钢宽度检测仪30和出口带钢宽度检测仪31,在机架1、2、3、4和5之间,分别配置带钢宽度检测仪301-304,实时检测冷轧机组入口、出口以及机架之间,沿带钢10的长度方向上各位置处的宽度实测值。控制过程包括以下步骤:(a)根据带钢的钢种、厚度、宽度以及轧制工艺参数,通过轧制实验或理论模型模拟计算,确定各机架的宽度缩减率给定值Rwi_set,i=1,2,…,n,其中,n为冷轧机组成机架总数,在该实施例中,n=5。(b)使用配置在冷轧机组的入口和出口的入口带钢宽度检测仪30和出口带钢宽度检测仪31,以及分别配置在机架1、2、3、4和5之间的带钢宽度检测仪301-304,实时检测各机架的入口带钢宽度和出口带钢宽度实测值{W0i_act,W1i_act},i=1,2,…,n,其中,n为冷连轧机组成机架总数,在该实施例中,n=5。(c)根据第i机架的入口带钢宽度和出口带钢宽度实测值,依公式(2)确定带钢经第i机架轧制后的宽度缩减率实际值:Rwi_act=(W0i_act-W1i_act)/W0i_act(2)其中,Rwi_act为第i机架轧制后的宽度缩减率实际值,W0i_act为第i机架入口带钢宽度实测值,W1i_act为第i出口带钢宽度实测值,i=1,2,…,n,n为冷连轧机组成机架总数;在该实施例中,n=5。(d)比较第i机架轧机轧制后的宽度缩减率实际值Rwi_act与该机架宽度缩减率给定值Rwi_set的大小,若Rwi_act>Rwi_set,则说明该机架入口、出口附近的带钢边部偏紧,边部张应力过大,有发生断带的危险,需要转步骤(e),通过调整轧机板形调节机构,减小Rwi_act与的Rwi_set偏差,使带钢边部变松,以避免断带的发生;否则,不需要调整,直接返回步骤(b)执行下一检测循环;(e)根据第i机架轧机轧制后的宽度缩减率实际值与该机架的宽度缩减率给定值,确定第i机架的宽度缩减率偏差ΔRwi=Rwi_act-Rwi_set,式中,Rwi_act为第i机架轧机轧制后的宽度缩减率实际值,Rwi_set为第i机架的宽度缩减率给定值,i=1,2,…,n,n为冷连轧机组成机架总数;在该实施例中,n=5。(f)根据第i机架的宽度缩减率偏差,依公式(1)计算第i机架轧机板形调节机构工作辊弯辊力、中间辊弯辊力和中间辊窜辊量的实时补偿量,ΔFwi=-αFwiΔRwi/KRwiFwiΔFmi=-αFmiΔRwi/KRwiFmi(1)ΔIMRi=-αIMRiΔRwi/KRwiIMRi式中,ΔFwi、ΔFmi、ΔIMRi分别为第i机架轧机板形调节机构工作辊弯辊力、中间辊弯辊力和中间辊窜辊量的实时补偿量,ΔRwi为第i机架的宽度缩减率偏差。αFwi、αFmi、αIMRi分别为第i机架板形调节机构的工作辊弯辊力、中间辊弯辊力、中间辊窜辊量的补偿量优先系数;由于冷轧机的各个板形调整时段都能够影响带钢的宽度缩减率,因此,根据轧机各个板形调节机构的响应速度、对带钢宽度缩减率影响效率的差异,赋予各个板形调节机构各自不同的补偿量优先系数。各补偿量优先系数应满足以下关系:αFwi+αFmi+αIMRi=1.0,0≤αFwi≤1.0,0≤αFmi≤1.0,0≤αIMRi≤1.0;KRwiFwi、KRwiFmi、KRwiIMRi分别为第i机架轧机工作辊弯辊力、中间辊弯辊力、中间辊窜辊量对第i机架轧机带钢宽度缩减率的影响系数,可根据带钢的钢种、厚度、宽度以及轧制工艺参数确定,KRwiFwi、KRwiFmi、KRwiIMRi可以通过轧制实验或理论模型模拟计算方法获得;(g)将各机架轧机板形调节机构工作辊弯辊力、中间辊弯辊力和中间辊窜辊量的实时补偿量,发送到冷连轧机组基础自动化级,对各机架的板形调节机构进行补偿,降低带钢边部张应力避免断带的发生。实施例3:图3是本发明的防止薄带钢冷轧过程断带的控制方法的另一个实施例,用于单机架构成的冷轧机组的轧制过程控制系统。在本实施例中,在单机架轧机组成的冷轧机组的入口和出口,分别配置入口带钢宽度检测仪30和出口带钢宽度检测仪31,实时检测冷轧机组入口和出口沿带钢10的长度方向上各位置处的宽度实测值。本实施例实际上是上述多机架冷轧机组中n=1并且βi=1的一个特例,控制过程包括以下步骤:(a)根据带钢的钢种、厚度、宽度以及轧制工艺参数,确定经过单机架冷轧机组轧制后的宽度缩减率给定值Rw_set;宽度缩减率给定值Rw_set可以通过轧制实验或理论模型模拟计算获得。(b)使用入口带钢宽度检测仪30和出口带钢宽度检测仪31,实时检测单机架冷轧机组的入口带钢宽度实测值W0_act和机组出口带钢宽度实测值W1_act;(c)根据冷轧机组的入口带钢宽度实测值W0_act和机组出口带钢宽度实测值W1_act,依公式(3)确定带钢经冷轧机组轧制后的宽度缩减率实际值:Rw_act=(W0_act-W1_act)/W0_act(3)其中,Rw_act为单机架冷轧机组轧制后的宽度缩减率实际值,W0_act为冷轧机组入口带钢宽度实测值,W1_act为冷轧机组出口带钢宽度实测值;(d)比较经过冷轧机组轧制后的宽度缩减率实际值Rw_act与宽度缩减率给定值Rw_set的大小。若Rw_act>Rw_set,则说明冷轧过程中带钢边部偏紧,边部张应力过大,有发生断带的危险,需要转步骤(e),通过调整轧机板形调节机构,减小Rw_act与Rw_set偏差,使带钢边部变松,以避免断带的发生;否则,不需要进行调整,直接返回步骤(b)执行下一检测循环;(e)根据经过冷轧机组轧制后的宽度缩减率实际值与宽度缩减率给定值,确定宽度缩减率偏差ΔRw=Rw_act-Rw_set。(f)根据宽度缩减率偏差,依公式(1”)计算轧机板形调节机构工作辊弯辊力、中间辊弯辊力和中间辊窜辊量的实时补偿量,ΔFw=-αFwΔRw/KRwFwΔFm=-αFmΔRw/KRwFm(1”)ΔIMR=-αIMRΔRw/KRwIMR式中,ΔFw、ΔFm、ΔIMR分别为轧机板形调节机构工作辊弯辊力、中间辊弯辊力和中间辊窜辊量的实时补偿量,ΔRw为宽度缩减率偏差;αFw、αFm、αIMR分别为板形调节机构的工作辊弯辊力、中间辊弯辊力、中间辊窜辊量补偿量优先系数,可根据轧机板形调节机构的响应速度及其对带钢宽度缩减率影响效率的差异确定,应满足以下关系:αFw+αFm+αIMR=1.0,0≤αFw≤1.0,0≤αFm≤1.0,0≤αIMR≤1.0。由于冷轧机的各个板形调整时段都能够影响带钢的宽度缩减率,因此,本步骤需要根据轧机各个板形调节机构的响应速度、对带钢宽度缩减率影响效率的差异,赋予各个板形调节机构各自不同的补偿量优先系数;KRwFw、KRwFm、KRwIMR分别为轧机工作辊弯辊力、中间辊弯辊力、中间辊窜辊量对带钢宽度缩减率的影响系数,可根据带钢的钢种、厚度、宽度以及轧制工艺参数,通过轧制实验或理论模型模拟计算方法获得影响系数KRwFw、KRwFm和KRwIMR。(g)将轧机板形调节机构工作辊弯辊力、中间辊弯辊力和中间辊窜辊量的实时补偿量,发送到冷轧机组基础自动化级,通过对板形调节机构进行补偿,降低带钢边部张应力避免断带的发生。以上实施例中的各个机架都是以六辊轧机为例建立带钢宽度缩减率自动控制模型,通过对轧机板形调节机构工作辊弯辊力、中间辊弯辊力和中间辊窜辊量的实时补偿,实现板形调节机构的补偿。对于其它机型轧机,可以按照同样方法建立类似的带钢宽度缩减率自动控制模型。以下通过具体实施数据进一步说明本发明的防止薄带钢冷轧过程断带的控制方法的技术效果:以本发明实施例2的方式,将本发明的防止薄带钢冷轧过程断带的控制方法,应用于某1420mm五机架六辊冷连轧机组,在该机组入口即第1机架轧机入口,安装一套具有带钢宽度检测功能的横断面仪,作为入口带钢宽度检测仪30,在该机组出口即第5机架轧机出口,安装一套带有带钢宽度检测功能的多功能仪,作为出口带钢宽度检测仪31,试验钢卷的钢种为硬质镀锡原板带钢,入口厚度2.0mm,宽度960mm,出口厚度0.18mm。通过统计比较,采用本发明的控制方法前后的冷连轧过程断带发生率如图4所示。从图4可以看出,采用现有技术未采用本发明的对比钢卷的断带发生率约为2.6%,采用本发明的控制方法后,试验钢卷的断带发生率降低到1.2%左右。由此可见,采用本发明的防止薄带钢冷轧过程断带的控制方法后,断带发生率明显降低,冷轧生产过程的稳定性和成材率都可以得到提高。本技术领域中的普通技术人员应当认识到,以上的实施例仅是用来说明本发明的技术方案,而并非用作为对本发明的限定,任何基于本发明的实质精神对以上所述实施例所作的变化、变型,都将落在本发明的权利要求的保护范围内。