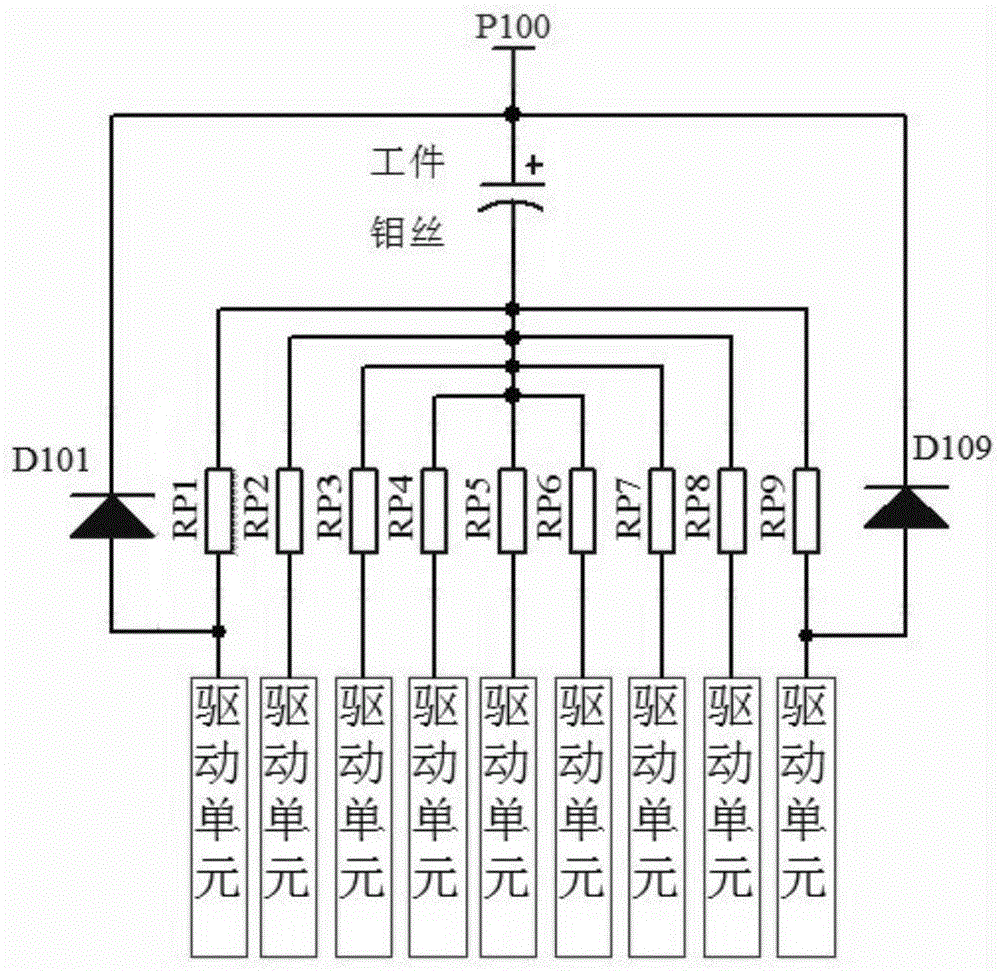
本发明涉及线切割机床
技术领域:
,尤其是涉及一种线切割机床控制装置。
背景技术:
:线切割加工是基于电火花加工原理发展起来的一种机械加工方法。由于结构简单、价格低廉,目前快走丝线切割加工机床在我国应用范围非常广泛。它是利用循环移动的钼丝作为工具电极,当把高频脉冲电压加在工件(接高频电压的正极)与钼丝(接高频电压的负极)之间时,钼丝对工件进行电火花放电,进而对金属工件进行蚀除、成型。高频脉冲电源作为线切割机床的重要组成部分,其性能的优劣直接影响着线切割加工的速度、精度、表面粗糙度、钼丝损耗、加工稳定性等。目前快走丝线切割加工中普遍存在丝损偏大乃至时常断丝的问题,不仅由于频繁换丝严重影响加工效率,而且由于钼丝消耗较多进而增加了加工成本。研究发现,脉冲电源在线切割机工作过程中对工具电极的冲击磨损是造成工具电极断丝的主要原因之一。试验证明,电压脉冲波形对加工产生影响的主要是放电电流,即电流状态是影响加工效率以及钼丝损耗的重要因素。图1为线切割高频脉冲电源工作原理图。图1中,p100为高频电源正极,高频电源正极p100与待切割工件相连。钼丝与限流功率电阻rp1~rp9相连,限流功率电阻rp1~rp9分别与对应的驱动单元1~驱动单元9相连,驱动单元中的场效应管的源极与高频电源负极g100相连。快恢复二极管d101~d109(图1中未画出d102~d108)的阳极分别与与驱动单元1~驱动单元9相连,快恢复二极管d101~d109的阴极与高频电源正极相连。线切割高频脉冲电源工作原理:高频电源正极p100接入直流电压,电压幅度一般为80v~100v。当开始线切割加工时,根据需要的切割加工放电电流选择相应的驱动单元工作。驱动单元工作时,高频电源正极p100、工件、钼丝、与其相连的限流功率电阻与驱动单元形成通电回路,工件与钼丝之间形成火花放电。如图2所示,申请号为201220329843.2的中国专利“一种高效率低损耗高频电源”提出了一种线切割高频脉冲电源控制电路,图3为其驱动电路。由图2和图3可知,该高频电源存在以下问题:(1)单片机输出的高频脉冲信号in与后级q1和q2组成的推挽放大电路没有进行隔离,后级放大电路可能会对单片机形成干扰;(2)单片机输出的高频脉冲信号没有经过功率放大,由于单片机的输出端口驱动能力很小,因此当6路in同时工作时,可能无法使后级的推挽放大电路正常工作;(3)推挽放大电路的输出直接通过电阻r111接入场效应管m1的栅极,进而驱动场效应管工作。该电路将使场效应管的输出脉冲上升沿过陡,而且上升沿的尖冲很大,使得钼丝中存在很大的冲击电流,进而增加钼丝的丝损,乃至容易形成断丝;(4)推挽放大电路的输出直接通过电阻r111接入场效应管m1的栅极,当推挽放大电路的输出出现干扰或较大抖动时,干扰或抖动信号将使场效应管误动作,进而影响加工稳定性。技术实现要素:有鉴于此,本发明的目的在于提供一种线切割机床控制装置,在保证加工速度的前提下,降低钼丝丝损,并大大降低断丝的概率,确保机床工作的稳定性。第一方面,本发明实施例提供了一种线切割机床控制装置,包括脉冲产生单元、光耦隔离单元、放大单元和驱动单元;所述脉冲产生单元用于产生脉冲信号;所述光耦隔离单元用于接收并输出脉冲产生单元输出的脉冲信号,以及隔离放大单元的模拟信号与脉冲产生单元的数字信号;所述放大单元包括依次相连的反相放大模块、延时模块和推挽放大模块,所述反相放大模块用于接收光耦隔离单元输出的脉冲信号并进行反相放大,所述延时模块用于对反相放大电路输出的脉冲信号的上升沿进行延时,所述推挽放大模块用于对延时模块输出的脉冲信号进行进一步的放大;所述驱动单元包括依次相连的交流耦合栅极驱动模块和场效应管;所述交流耦合栅极驱动模块用于接收推挽放大模块的输出脉冲信号,降低所述脉冲信号的上升沿和下降沿的震荡,将处理后的脉冲信号发送至场效应管,还用于降低场效应管的输入阻抗,为场效应管提供负偏压;所述场效应管用于接收交流耦合栅极驱动模块的输出信号并驱动高频电源工作。结合第一方面,本发明实施例提供了第一方面的第一种可能的实施方式,其中,所述延时电路包括电阻r106和电容c102;所述电阻r106的一端连接反相放大模块的输出端,另一端连接第一电源;所述电容c102的一端连接在反相放大模块的输出端和推挽放大模块的输入端之间,另一端接地。结合第一方面的第一种可能的实施方式,本发明实施例提供了第一方面的第二种可能的实施方式,其中,所述反相放大模块包括电阻r105、电容c101和三极管q101,所述电阻r105和电容c101并联;电阻r105和电容c101的输入端均连接光耦隔离单元的输出端,输出端均连接三极管q101的基级;三极管q101的发射极接地,集电极连接电阻r106一端;所述推挽放大模块包括三极管q102、三极管q103和电阻r107,所述三极管q102和三极管q103的基极均连接三极管q101的集电极,三极管q102的发射极和三极管q103的发射极相连后连接电阻r107的一端,三极管q102的集电极接第一电源,三极管q103的集电极接地,电阻r107的另一端接地。结合第一方面,本发明实施例提供了第一方面的第三种可能的实施方式,其中,所述栅极驱动电路包括电阻r108、电容c103和电阻r109;所述电阻r108的一端接推挽放大模块的输出端,另一端接电容c103的一端,所述电容c103的另一端分别接电阻r109的一端和场效应管的栅极,电阻r109的另一端接地;场效应管的漏极接钼丝。结合第一方面的第三种可能的实施方式,本发明实施例提供了第一方面的第四种可能的实施方式,其中,所述电阻r108的阻值为10ω~100ω;所述电阻r109的阻值为1kω~10kω。结合第一方面,本发明实施例提供了第一方面的第五种可能的实施方式,其中,所述场效应管的栅极还连接有瞬态抑制二极管v1,所述瞬态抑制二极管v1的另一端接地。结合第一方面的第三种可能的实施方式,本发明实施例提供了第一方面的第六种可能的实施方式,其中,还包括电阻r_off和二极管d_off,所述电阻r_off和二极管d_off串联后并联在电阻r108两端。结合第一方面,本发明实施例提供了第一方面的第七种可能的实施方式,其中,所述光耦隔离单元包括电阻r101、电阻r102、光耦合器u101、电阻r103和电阻r104;所述电阻r101的一端和光耦合器u101的低电平输入端分别接脉冲产生单元的输出端,电阻r101的另一端接第二电源;所述光耦合器u101的高电平输入端接电阻r102的一端,电阻r102的另一端接第二电源;光耦合器u101的第一输出端接电阻r104,第二输出端分别接电阻r103的一端和反相放大模块的输入端;电阻r104的另一端接地,电阻r103的另一端接第二电源。结合第一方面,本发明实施例提供了第一方面的第八种可能的实施方式,其中,所述场效应管和钼丝之间还连接有过流保护电路。结合第一方面的第八种可能的实施方式,本发明实施例提供了第一方面的第九种可能的实施方式,其中,所述放大单元的输出端至少连接两个并联的驱动单元。本发明实施例带来了以下有益效果:本发明的脉冲发生单元和放大单元之间设置了光耦合单元,能够避免后级的放大单元对脉冲发生单元产生的干扰;放大单元包括反相放大模块和推挽放大模块,能够进一步的增强带载能力,从而驱动多个驱动单元;在反相放大模块和推挽放大模块之间设置了延时电路,通过延时电路产生的延时来降低脉冲上升沿过冲幅度,进而降低冲击电流对钼丝的损耗;在驱动单元的场效应管前设置了交流耦合栅极驱动模块,能够避免前级的推挽放大模块输出的脉冲信号出现的干扰或过抖,导致场效应管的误动作,增加场效应管的稳定性。附图说明为了更清楚地说明本发明具体实施方式或现有技术中的技术方案,下面将对具体实施方式或现有技术描述中所需要使用的附图作简单地介绍。图1为线切割机床控制装置工作原理图;图2为专利一种线切割高频脉冲电源控制电路的控制单元电路图;图3为专利一种线切割高频脉冲电源控制电路的驱动单元电路图;图4为本发明脉冲发生单元和光耦隔离单元的电路原理图;图5为本发明放大单元的电路原理图;图6为本发明驱动单元的电路原理图;图7为本发明实现的线切割加工电流波形图;图8为本发明的系统原理图。具体实施方式为使本发明实施例的目的、技术方案和优点更加清楚,下面将结合附图对本发明的技术方案进行清楚、完整地描述,显然,所描述的实施例是本发明一部分实施例,而不是全部的实施例。基于本发明中的实施例,本领域技术人员在没有做出创造性劳动前提下所获得的所有其他实施例,都属于本发明保护的范围。参照图8,本实施例提出的线切割机床控制装置,包括脉冲产生单元、光耦隔离单元、放大单元和驱动单元;所述脉冲产生单元用于产生脉冲信号;所述光耦隔离单元用于接收并输出脉冲产生单元输出的脉冲信号,以及隔离放大单元的模拟信号与脉冲产生单元的数字信号;所述放大单元包括依次相连的反相放大模块、延时模块和推挽放大模块,所述反相放大模块用于接收光耦隔离单元输出的脉冲信号并进行反相放大,所述延时模块用于对反相放大电路输出的脉冲信号的上升沿进行延时,所述推挽放大模块用于对延时模块输出的脉冲信号进行进一步的放大;所述驱动单元包括依次相连的交流耦合栅极驱动模块和场效应管;所述交流耦合栅极驱动模块用于接收推挽放大模块的输出脉冲信号,降低所述脉冲信号的上升沿和下降沿的震荡,将处理后的脉冲信号发送至场效应管,还用于降低场效应管的输入阻抗,为场效应管提供负偏压;所述场效应管用于接收交流耦合栅极驱动模块的输出信号并驱动高频电源工作。具体地,脉冲产生单元采用单片机mcu产生高频脉冲,进一步地,延时电路包括电阻r106和电容c102;电阻r106的一端连接反相放大模块的输出端,另一端连接第一电源;电容c102的一端连接在反相放大模块的输出端和推挽放大模块的输入端之间,另一端接地。进一步地,参照图4,光耦隔离单元包括电阻r101、电阻r102、光耦合器u101、电阻r103和电阻r104;电阻r101的一端和光耦合器u101的低电平输入端分别接脉冲产生单元的输出端,电阻r101的另一端接第二电源;光耦合器u101的高电平输入端接电阻r102的一端,电阻r102的另一端接第二电源;光耦合器u101的第一输出端接电阻r104,第二输出端分别接电阻r103的一端和反相放大模块的输入端;电阻r104的另一端接地,电阻r103的另一端接第二电源。具体地,光耦合器u101的作用为高频脉冲信号数字/模拟隔离。单片机mcu接收到上位机发出的高频控制信号control后,发出高频脉冲数字信号pwm1,经上拉电阻r101接至第二电源p5,确保高电平时信号被钳位在+5v。pwm1接至光耦合器u101的阴极输入端2,当pwm1为高电平时,光耦合器u101不导通,当pwm1为低电平时,光耦合器u101导通。进一步地,参照图5,反相放大模块包括电阻r105、电容c101和三极管q101,电阻r105和电容c101并联;电阻r105和电容c101的输入端均连接光耦隔离单元的输出端,输出端均连接三极管q101的基级;三极管q101的发射极接地,集电极连接电阻r106一端;推挽放大模块包括三极管q102、三极管q103和电阻r107,三极管q102和三极管q103的基极均连接三极管q101的集电极,三极管q102的发射极和三极管q103的发射极相连后连接电阻r107的一端,三极管q102的集电极接第一电源,三极管q103的集电极接地,电阻r107的另一端接地。具体地,光耦合器u101不导通时,其c极输出端p1.1为高电平,此时图5中,高频脉冲信号输出放大电路中的三极管q101导通,第一电源p15、电阻r103、电阻r105//电容c101、三极管q101的be结、高频电压的负极g100形成回路。p1.1刚转换为高电平时,由于电容c101两端电压不能突变而近似于短路,因此三极管q101迅速导通,三极管q101的be结最大导通电压vbe=1.0v,因此此时p1.2的电位被迅速钳位为1.0v。p1.1维持高电平时,电容c101两端电压逐渐充电至电阻r105的分压电压值。三极管q101型号为mmbt2222a,三极管q101的be结导通电压vbe=1.0v,因此电容c101两端电压值为:(15-1.0)×(5.1/(10+5.1))=4.7v,此时p1.1的电位为:4.7+1.0=5.7v。光耦合器u101由不导通转换为饱和导通状态时,第一电源p15、电阻r103、光耦合器u101的ce结、电阻r104、高频电压的负极g100形成回路。光耦合器u101ce结的饱和导通电压vce(sat)=0.1v,此时p1.1的电位迅速变为:(15-0.1)×(1/(10+1))+0.1=1.5v。由于电容c101两端电压不能突变,因此此时p1.2的电压迅速变为:1.5-4.7=-3.2v,三极管q101迅速截止。因此,单片机mcu发出的高频脉冲数字信号pwm1经过上述电路后,在进行隔离的同时,后级放大电路能迅速跟随高频脉冲数字信号的电平变化。图5高频脉冲信号输出放大电路由两级放大电路组成,p1.1到p1.3之间为反相放大器电路,p1.3到p1.4之间为推挽功率放大器电路。此处反相放大器电路和推挽功率放大器电路的主要作用为增强带载能力,以便后级多个驱动单元。与此同时,其另外一个作用就是利用电阻r106和电容c102给脉冲的上升沿产生约7.4μs的延时,从而降低脉冲上升沿的过冲幅度,进而降低冲击电流对钼丝的损耗。在图5电路中,三极管q102型号为mmbt2222a,当三极管q101截止时,电源p15经电阻r106给电容c102充电,当充电至三极管q102饱和导通时。电源p15为15v,电阻r106为1kω,三极管q102的基极电流为15÷1=15ma,其ce结饱和导通电压为0.3v,因此p1.4电压为15-0.3=14.7v,故电容c102最大充电至15v。时间常数表示过渡反应的时间过程的常数。在电阻r、电容c串联的电路中,它是电阻和电容的乘积。若c的单位是μf,r的单位是kω,时间常数的单位就是μs。当电容的端电压达到最大值的1-1/e(此处e为自然指数)时即约0.632倍所需要的时间即是时间常数。在图5电路中,电阻r106给电容c102充电的充电时间常数为:1×4.7=4.7μs。此电路中电容c102的端电压达到最大值为15v,故充电时间为4.7÷0.632=7.4μs。高频脉冲信号输出驱动单元电路是高频脉冲电源的关键,如果不考虑谐波和emi等要求的话,场效应管开关速度越快越好,因为开关时间越短,开关损耗越小。对于一个场效应管,如果把栅极、源极之间的电压从0v升到管子的开启电压所用的时间越短,那么场效应管开启的速度就会越快。与此类似,如果把场效应管的栅极、源极之间的电压从开启电压降到0v的时间越短,那么场效应管关断的速度也就越快,专利文献中的驱动单元电路就是如此。但是,场效应管开关速度很快将容易引起米勒振荡。本实施例相较于专利文献中的放大电路和驱动单元电路进行了较大改进,使得场效应管开通延时7.4μs,在场效应管开关速度略微降低的情况下大大降低了电流冲击。进一步地,参照图6,栅极驱动电路包括电阻r108、电容c103和电阻r109;电阻r108的一端接推挽放大模块的输出端,另一端接电容c103的一端,电容c103的另一端分别接电阻r109的一端和场效应管的栅极,电阻r109的另一端接地;场效应管的漏极接钼丝。进一步地,电阻r108的阻值为10ω~100ω;电阻r109的阻值为1kω~10kω。高频脉冲数字信号pwm1为低电平时为高频有效信号。pwm1为低电平时,p1.1为低电平,三极管q101截止,p1.3为高电平,三极管q102导通,三极管q103截止,p15经三极管q102、电阻r108、电容c103给场效应管q104提供栅源电压vgs,场效应管q104导通,主回路闭合,工件与钼丝之间形成放电通道,进行线切割加工。反之,pwm1为高电平时,线切割加工停止。图6高频脉冲信号输出驱动单元电路中,电阻r108用于降低场效应管上升沿和下降沿的振荡。因为驱动线路走线会有寄生电感,而寄生电感和场效应管的结电容会组成一个lc振荡电路,如果直接把驱动信号接到场效应管栅极,在脉冲上升沿、下降沿会产生很大的振荡,导致场效应管急剧发热甚至爆炸,在场效应管栅极串联10ω~100ω的电阻,降低lc振荡电路的q值,使振荡迅速衰减。电容c103与电阻r108、电阻r109组成场效应管q104的交流耦合栅极驱动模块。该技术的优点是在关断时和在开关关断状态期间为栅极提供负偏压,以提高场效应管q104的关断速度和降低dv/dt的影响。以场效应管q104的型号选irfp250为例进行阐述。irfp250可承受的最大栅极-源极电压为±30v,irfp250饱和导通时栅极-源极电压为2~4v。当启动高频时,前文已经说明,p1.4的电压为14.7v,由于电容c103两端的电压不能突变,启动高频瞬间电容c103近似短路。因此,场效应管q104栅极p1.6的瞬间电压被拉升为电阻r109与电阻r108的分压值:14.7×(1000/(100+1000))=13.4v,场效应管q104饱和导通,因此p1.6被钳位至2~4v,按中间值3v估算。与此同时,p1.5的电压被逐渐充电至14.7v,电容c103两端压降为14.7-3=11.7v。当关闭高频时,由于此时三极管q103导通,因此p1.4的电压被迅速钳位至三极管q103的ec结的饱和导通电压0.4v。由于电容c103两端的电压不能突变,因此p1.6被钳位至0.4-11.7=-11.3v,场效应管q104迅速截止。进一步地,场效应管的栅极还连接有瞬态抑制二极管v1,瞬态抑制二极管v1的另一端接地。具体地,图6高频脉冲信号输出驱动单元电路中,电阻r109用于降低场效应管输入阻抗。因为场效应管栅极输入阻抗高,静电或者干扰可能导致场效应管误导通乃至损坏,因此在场效应管栅极与源极之间并联一个1k~10k的电阻以降低输入阻抗。如果担心附近功率线路上的干扰耦合过来产生瞬间高压击穿场效应管,可以在场效应管栅极与源极之间再并联一个15v左右的tvs瞬态抑制二极管v1,必要时增加此电路,tvs是一种反应速度很快的稳压管,其瞬间可以承受的功率高达几百至上千瓦,可以用来吸收瞬间的干扰脉冲。进一步地,还包括电阻r_off和二极管d_off,电阻r_off和二极管d_off串联后并联在电阻r108两端。具体地,切换场效应管时面临的一个常见问题是由于米勒电容器的寄生导通。这种效应在单电源驱动器(0~15v)中是明显的。由于这种栅极-漏极耦合,在场效应关断期间产生的高瞬态dv/dt可导致潜在危险的寄生导通(栅极电压,vgs)。解决这一问题的办法,除了可增加上述tvs瞬态抑制二极管v1外,可采用四种办法:第一种是改变栅极电阻,第二种是在栅极和漏极之间增加电容器,第三种是使用负栅极驱动,第四种是有源箝位技术。本实施例采用第一种方法即改变栅极电阻的方法。在图6中,增加电阻r_off和二极管d_off,必要时增加此电路。场效应管q104开通时,由于二极管d_off的反向截止作用,电阻r_off不起作用。场效应管q104关断时,电容c103上存储的电荷将通过通过电阻r108与电阻r_off并联、图5中的电阻r107和三极管q103快速释放,降低风险。本实施例提出的线切割高频脉冲电源,通过控制高频脉冲电压上升沿斜率,稍微降低开启速度,进而适当降低放电电流的上升沿斜率及过冲,以实现高效率低损耗线切割加工。图7为本实施例实现的线切割加工电流波形。进一步地,场效应管和钼丝之间还连接有过流保护电路。过流保护电路包括电阻r110和电阻r109,电阻r110和电阻r109并联后连接在场效应管的漏极和钼丝之间。具体地,本实施例还对场效应管q104进行了过流保护设计。图6高频脉冲信号输出驱动单元电路中电阻r109和电阻r110采用100mω/2w的小功率电阻,当场效应管q104的输出端电流过大时,由于电阻r109和电阻r110的功率为很小,因此将首先烧毁电阻r109和电阻r110,进而保护了场效应管q104。电阻r109和电阻r110的功率为i2r,因此其可承受的平均电流为4.5a,电阻r109和电阻r110并联可承受9a的平均电流,满足绝大多数快走丝线切割加工的要求。而电阻r109和电阻r110的并联电阻只有50mω,因此相对于整个线切割加工而言功耗可忽略不计。进一步地,放大单元的输出端至少连接两个并联的驱动单元。线切割高频脉冲电源工作环境中一般有许多电磁干扰源,如工频干扰、电机起动、无线电台、雷击浪涌等,它们所产生的电磁波或尖峰脉冲,通过电容耦合、电感耦合、电源线等进入线切割高频脉冲电源,从而引起干扰。辐射型电磁骚扰很难控制,因为辐射型电磁骚扰的频率较高,能量的波长很短,很短的印制板布线或电源变压器线圈、电感等都可能成为收发天线。根据电偶极子模型磁偶极子模型理论,实际电路设计时,效应管驱动线路的环路面积要尽可能小,否则可能会引入外来的电磁干扰;走线要尽可能短,否则走线的电感会很大程度上影响芯片的瞬间输出电流。因此,在满足工作要求的前提下,必须尽可能减少器件数量,以降低印制板尺寸及走线长度。考虑到快走丝线切割机床生产加工成本问题,线切割高频脉冲电源工作环境一般都比较恶劣,多数都在高温、高湿、低温、电网谐波等环境下进行工作,因此其可靠性设计至关重要。对线切割高频脉冲电源而言,系统可靠度rs可用公式表达为:r(t)=e-λt。组成线切割高频脉冲电源的各个元器件可靠度之间被看作串联关系,假设每个元器件的可靠度为ri,则线切割高频脉冲电源的可靠度rs为:大部分电子产品在偶然故障期的失效均服从指数分布,因此可假定线切割高频脉冲电源元器件的失效也服从指数分布,则其总失效率λs计算公式为:线切割高频脉冲电源的生命周期用平均寿命mttf表示,当线切割高频脉冲电源的生命周期服从指数分布时,mttf的预计值为:mttf=1/λs(h)。因此,线切割高频脉冲电源的器件越少,其可靠性越高。综上,本实施例采用图8所示的线切割高频脉冲电源总体结构。9个功率限流电阻的接入采用9个驱动单元,分别为驱动单元1到驱动单元9。但隔离单元和放大单元分别只采用5路,分别为隔离单元1和放大单元1至隔离单元5和放大单元5。其中放大单元1连接驱动单元1,放大单元2连接驱动单元2,放大单元3分别连接驱动单元3和驱动单元4;放大单元4分别连接驱动单元5和驱动单元6;放大单元5分别连接驱动单元7、驱动单元8和驱动单元9。由于放大单元采用了两级放大,因此保证了后接2个及3个驱动单元的工作可靠性。为了使功率电阻可在1~9个之间进行选择,必须采用组合形式,表1为本发明线切割高频脉冲选择组合之一,满足工作要求的其它组合同样适用。表1本实施例线切割高频脉冲选择组合序号功率电阻选择(只)controlpwm选择1100000001pwm12200000010pwm33300000011pwm1+pwm34400000100pwm3+pwm45500000101pwm4+pwm56600000110pwm1+pwm3+pwm57700000111pwm3+pwm4+pwm58800001000pwm1+pwm3+pwm4+pwm59900001001pwm1+pwm2+pwm3+pwm4+pwm5最后应说明的是:以上实施例,仅为本发明的具体实施方式,用以说明本发明的技术方案,而非对其限制,本发明的保护范围并不局限于此,尽管参照前述实施例对本发明进行了详细的说明,本领域技术人员应当理解:任何熟悉本
技术领域:
的技术人员在本发明揭露的技术范围内,其依然可以对前述实施例所记载的技术方案进行修改或可轻易想到变化,或者对其中部分技术特征进行等同替换;而这些修改、变化或者替换,并不使相应技术方案的本质脱离本发明实施例技术方案的精神和范围,都应涵盖在本发明的保护范围之内。因此,本发明的保护范围应以权利要求的保护范围为准。当前第1页12