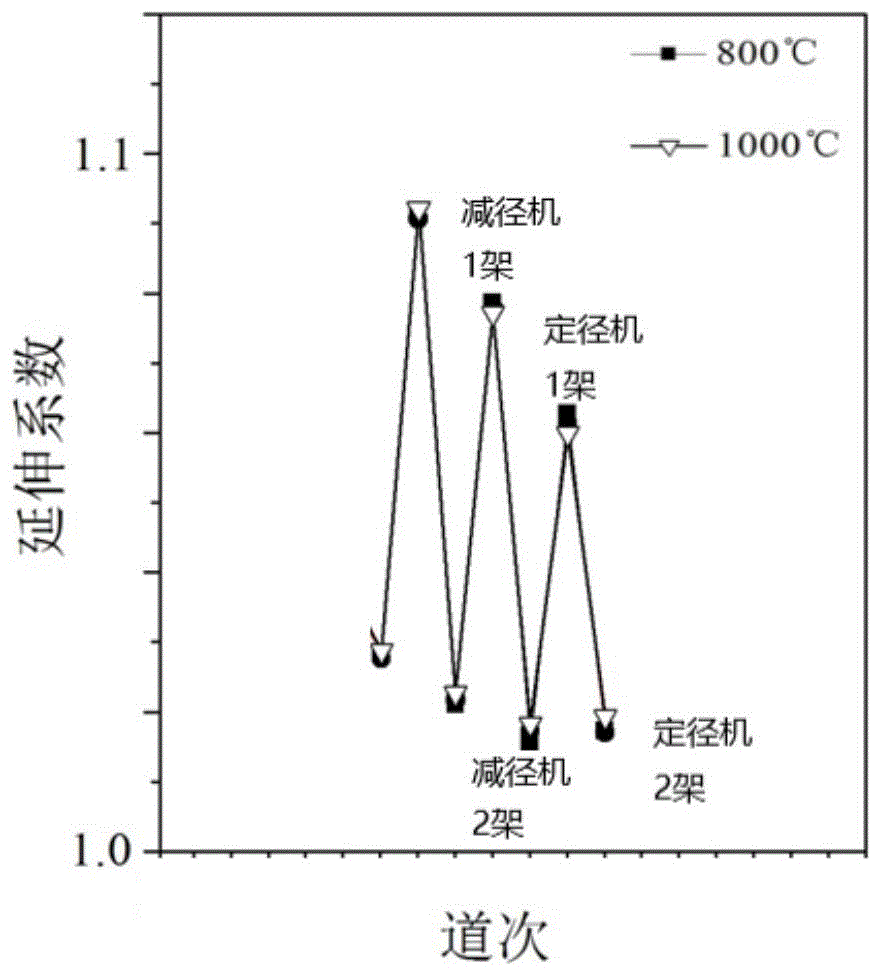
本发明涉及金属材料加工
技术领域:
,具体涉及一种控制线材轧制尺寸精度的方法。
背景技术:
:大国制造和国家战略需要大量高品质的特殊钢线材,其表面和尺寸精度一直是用户关注的重点。目前,用户对表面质量缺陷的要求已经达到20μm深度,通过在线涡流探伤实现对线材的全覆盖检测;对尺寸精度的要求从b级精度到100%c级精度,尺寸波动在±0.1mm以内。而钢厂在生产过程中由于产量和效益直接挂钩,迫切需要解决高速生产过程中的高精度问题。为达到高效率生产的目的,各厂都在成品前增加减定径重载轧机或者双模块轧机。其中包括进口摩根型、达涅利型、西马克型以及国产mini轧机,进口机型可以达到120m/s的轧制速率,国产轧机可以达到100m/s的轧制速率。但是进口减定径轧机在生产胎圈钢丝、钢帘线等小规格硬线以及焊接用钢盘条时总是出现尺寸波动,甚至出现吐丝断和缩颈。表现为在生产小规格硬线类产品时,经常发现吐丝机吐丝的过程中有盘条吐出多个断头,也有可能未断,但表现为缩颈现象。小规格硬线盘条多被生产用于拉丝材的母料,胎圈钢丝用盘条及钢帘线用盘条被用于生产汽车用子午线轮胎,对拉拔性能和尺寸精度的要求非常高,尺寸波动的产生将极大影响盘条的拉拔性能,而吐断也严重影响产线的产能和钢厂的效益。对于尺寸精度的控制,一直以来就是钢厂生产关注的重点。为保证大盘重下的通条尺寸精度,钢厂在不断提高轧制速率、缩短轧制时间的基础上,通过加热炉实现梯形加热,控制钢坯头尾的温度差,保证由于后尾在出加热炉后停留时间长、温降大导致的通条尺寸波动。另外,首钢高线采用烧焦气补充加热的方式来弥补,三明钢铁通过自动烧钢模型来控制炉内温度梯度,同时还开发了加热炉黑匣子在线过程温度检测系统,来优化钢坯的加热温度和头尾温度差;而最近几年兴起的双蓄热式技术,也通过分段分散的弥散燃烧来保证炉温的温度场和流场。这些方式都是从加热源头保证线材在轧制阶段温度的均匀性,从而消除由于温度差异而导致的宽展、延伸不同出现的尺寸波动。另一方面中冶京诚和大型设计院在设计高线产线过程中尽量采用全连轧的设计理念,实现粗轧、中轧微张力,预精轧大活套,精轧微张力的控制方式,力争做到头尾失张状态下的尺寸精度。而邢钢、首钢、宝钢更是在孔型上根据品种特性进行专业化设计,根据钢种的特性、表面摩擦力、轧制工艺进行专有孔型设计。首钢更是在这方面进行深入研究,开发了基于大数据和有限元的孔型设计软件,为智能轧钢奠定了基础。但是在生产小规格线材产品过程中的尺寸精度波动问题一直困扰钢厂,有时候为达到用户的需求需要进行头尾剪切各30圈以上,成材率损失在0.1%左右。即便产线配置了高精度的重载轧机和减定径装备,仍然在减径机和定径机之间出现张力过大而导致拉钢缩颈和拉断问题。目前,小规格线材轧制都采用减定径机组生产,减定径机组内的张力控制和料型控制是保证成品质量尤其是成品尺寸的关键。在实际生产过程中,轧钢现场的干扰因素非常多,如振动、电控、温度波动、来料尺寸波动等因素,都会对减定径机组的稳定运行产生影响。因此需要通过优化设备参数保证设备最佳运行状态,提高减定径机组自身的抗干扰能力。鉴于此,特提出本发明。技术实现要素:本发明的目的在于提供一种控制线材轧制尺寸精度的方法。为实现上述目的,本发明的技术方案如下:本发明涉及一种控制线材轧制尺寸精度的方法,所述方法包括以下步骤:(1)在轧制前确定轧辊辊径差、减定径轧机的辊径配比、减定径机组速比差、轧辊过钢量、导卫过钢量和轧制温度;(2)开始轧钢,轧钢过程中控制轧机振动值、轧制延伸系数、离合器档位、离合器速比和吐丝机超前系数。优选地,对于轧辊辊径差,将减径机一架和减径机二架的轧辊辊径差控制在±0.2mm以内,定径机一架和定径机二架的轧辊辊径差控制在±0.1mm以内。优选地,对于减定径轧机的辊径配比,相邻的减径机二架和定径机一架的辊径配比为(220±0.2)/(150±0.1)。优选地,对于轧辊过钢量和导卫过钢量,控制减径机轧辊过钢量≤1200吨,定径机轧辊过钢量≤800吨,导卫过钢量≤200吨,导卫时间≤3小时。优选地,将轧辊与钢材之间的摩擦系数控制在0.2~0.25。优选地,对于轧制温度,将减径机一架、减径机二架、定径机一架、定径机二架的轧制温度控制在880~920℃。优选地,将轧机振动值控制在0.8~1.2mm/s2,优选1mm/s2。优选地,对于减定径轧机的轧制延伸系数,将减径机二架的延伸系数控制在1.086±0.01,定径机一架延伸系数控制在1.055±0.01。优选地,对于离合器档位和离合器速比差,对成品前减径机和定径机的a、b、c、d中的4个档位和9个离合器进行优化组合,将减径机和定径机之间的速比差、转数差进行最小化。优选地,将减径机之间的速比差控制在0.02以内,减径机和定径机之间的速比差控制在0.06以内,定径机之间的速比差控制在0.02以内;将减径机之间电机的转数差控制在1000转/分钟以内,减径机和定径机之间电机的转数差控制在4000转/分钟以内,定径机之间电机的转数差控制在600转/分钟以内。优选地,将吐丝机超前系数控制在0.01~0.03。本发明的有益效果:本发明提供了一种控制线材轧制尺寸精度的方法。该方法通过控制减定径机组的轧制张力,能够稳定轧制生产,降低吐丝机吐断事故,提高生产效率,可用于钢厂的高线生产车间。通过在线材高速轧制过程中,控制成品道次前减定径机组高速轧制中出现的张力,能够降低轧制断线、缩颈问题。并通过对小规格线材高速轧制过程中,道次延伸率规律、减定径变速箱速比和传动关系进行分析,归纳总结了减定径各架次电机/辊轴速比的计算,对原有档位选择进行了最终优化,最终解决了减定径机组高速轧制过程的张力不稳定问题。将其用于生产φ5.5mm的小规格高速线材,轧制速度由原来的90~95m/s稳定提升至110m/s,产量提高12%,效益可达到60万元/月。该方法适合在棒线材轧钢厂推广,具有降本增效的优点。附图说明为了更清楚地说明本发明实施例或现有技术中的技术方案,下面将对实施例或现有技术描述中所需要使用的附图作简单地介绍,显而易见地,下面描述中的附图仅仅是本发明的一些实施例,对于本领域普通技术人员来讲,在不付出创造性劳动的前提下,还可以根据这些附图获得其他的附图。图1为轧制温度与延伸系数的关系图;图2为轧制温度与孔型充满度的关系图。具体实施方式为使本发明的目的、技术方案和优点更加清楚,下面将对本发明的技术方案进行详细的描述。显然,所描述的实施例仅仅是本发明一部分实施例,而不是全部的实施例。基于本发明中的实施例,本领域普通技术人员在没有做出创造性劳动的前提下所得到的所有其它实施方式,都属于本发明所保护的范围。本发明实施例涉及一种控制线材轧制尺寸精度的方法,该方法包括以下步骤:(1)在轧制前确定轧辊辊径差、减定径轧机的辊径配比、减定径机组速比差、轧辊过钢量、导卫过钢量和轧制温度;(2)开始轧钢,轧钢过程中控制轧机振动值、轧制延伸系数、离合器档位、离合器速比和吐丝机超前系数。轧制尺寸波动或者缩颈、吐断是机架间原有张力与导致张力波动的外部因素共同作用下的结果。如果机架间原有张力与外部因素造成的张力的合力大于轧件材料的能承受的强度极限,就会发生拉伸、缩颈、断裂。机架间张力(机架间原有张力与外部影响张力之和)是尺寸波动的动力,是产生缩颈和吐断的最根本条件。其中机架间原有张力主要针对精轧机和减定径机组这类由一台电机带动集体传动的轧机,各架次之间采用微张力轧制,影响微张力大小的主要因素有配辊设置、辊缝设置、轧槽的磨损情况以及最重要的相邻架次之间轧件辊轴转速的速比。而相邻架次之间轧件辊轴转速的速比是在轧件安装好后就设计和设定好,一般无法更改或很难更改。这种微张力一般在辊缝等设置后的一段时间内一直存在且变化较小。外部因素(如振动、电控、温度波动、来料尺寸波动)导致的张力波动对机架间原有张力发生共同作用,如果共同作用下的张力达到或超过这个温度下轧件的强度极限,就会造成吐断或缩颈。集体传动中各机架间的张力可通过孔型调整、辊环配辊、辊缝调整、改变变速箱速比的方法调整。但实际保证产品尺寸精度和料型,通过辊缝和孔型微调效果不佳。进一步地,对于轧辊辊径差,减径机一架和减径机二架的轧辊辊径差均为±0.2mm,定径机一架和定径机二架的轧辊辊径差均为±0.1mm。轧辊的辊径是影响张力的关键,在高速轧制过程中转速确定的情况下,辊径的微小差异都会导致前后轧机之间的张力放大。首先要保证相邻的减径机二架和定径机一架的辊径差,尽量降低这种由于辊期管理带来的辊径差隐患。配辊方式上,定径机组新辊不能直接开槽使用,需将其直径磨削至φ155mm后才能开槽使用。虽然会降低使用次数,增加辊耗及辊环修磨的工作量,但是可以保证最佳的使用状态。对于减定径轧机的辊径配比,在本发明的一个实施例中,减径机辊径为220mm,定径机辊径为150。因此相邻的减径机二架和定径机一架的辊径配比为(220±0.2)/(150±0.1)。需要说明的是,轧辊的表面使用状态是影响轧制摩擦力、宽展系数、延伸系数、前滑值等的重要因素,其中最重要的是前滑。轧制过程中轧件会发生前滑和后滑,以及横向金属流动,发生前滑和后滑产生了延伸,横向金属流动产生宽展。延伸系数是影响堆拉关系的重中之重,必须协调前滑或者后滑过程中轧辊速率和实际轧件速率的关系,才能从根本上形成微张力控制。表1为表面摩擦系数对轧钢前滑率的影响,可以看到,当摩擦系数大于0.25后,前滑率直线上升,因此需要将轧辊与钢材之间的摩擦系数控制在0.2~0.25。表1摩擦系数0.20.250.30.35前滑sh%0.570.81.41.5进一步地,对于轧辊过钢量和导卫过钢量,控制减径机轧辊过钢量不超过1200吨,定径机轧辊过钢量不超过800吨,导卫过钢量不超过200吨,导卫使用时间不超过3小时。轧辊和导卫过钢量越大,会导致线材的表面粗糙度越大。在材质选择上,减定径辊环采用wc材质,通过co机强化,高温高压压制成型烧结工艺制备得到;导卫采用tic材质,其质量轻,耐磨性好,能够减轻惯性降速对轧制堆拉关系的影响。按照正常的过钢量,减径机轧辊过钢量和定径机轧辊过钢量可以在1500吨以上,但是轧制时间越长,摩擦系数越大,宽展越大,对料型的影响越大。因此必须对轧辊的过钢量和导卫使用时间进行控制,保证最佳的使用状态。进一步地,对于轧制温度,将减径机一架、减径机二架、定径机一架、定径机二架的轧制温度控制在880~920℃,该温度下轧制的线材具有综合延伸性能和抗拉强度。轧件的强度相对于其室温下的强度差别很大,室温下线材的强度可达到600~1000mpa以上,但在950℃的高温下,线材的强度仅在120mpa左右。在高温条件下,温度对强度的影响尤其明显。高速轧制特别是集体传动的连续轧制,轧件温度随着道次增加不断增加,而且由于10%的形变储存能将转化为热能,在进入成品前的高速轧制过程实际上是一个快速升温的过程,很难准确测量轧件温度。温度对于吐断具有较大的影响且不可忽视,必须对轧制的温度进行精确地控制,保证在这一温度区间内材料的强韧性、宽展延伸性和孔型充满度。表2为不同轧制温度下的孔型充满度。表2轧制温度800℃900℃1000℃定径机1架1.11.00.9减径机2架1.050.951.05图1为轧制温度与延伸系数的关系图,表3对应不同温度和道次下的延伸系数。可以看出,在800~1000℃温度下减径机和定径机的延伸系数比较稳定。表3减径机1架减径机2架定径机1架定径机2架800℃1.0791.0151.0621.0161000℃1.0721.0191.0571.019图2为轧制温度与孔型充满度的关系图。表4对应不同温度和道次下的孔型充满度,可以看出在不同道次下,减定径机组的孔型充满度随着温度升高而降低。表4减径机1架减径机2架定径机1架定径机2架850℃1.070.781.120.82950℃1.020.761.060.78进一步地,轧机振动值为0.8~1.2mm/s2,优选1mm/s2。轧机振动值越大,对减定径机组轧制的稳定性、轧制过程的张力控制影响越大,对尺寸精度影响也就越大。因此要将轧机振动值控制在较低的程度。进一步地,对于减定径轧机的轧制延伸系数,减径机二架的延伸系数为1.086±0.01,定径机一架延伸系数为1.055±0.01。通过合理优化孔型,保证最佳的延伸系数是控制张力的基础。对于减定径机组四架轧机来说,成品前的三架轧机之间的延伸系数配比非常关键。申请人通过孔型设计软件来对不同钢种在轧制状态的塑性、延伸特性、摩擦系数进行收集,输入各架轧机的辊径、孔型参数、辊缝等参数,实现微张力状态下最佳孔型设计,来保证减径机二架和定径机一架的延伸系数。对此,需要进行:1)不同钢种的延伸系数计算。在计算机孔型设计中,允许选择不同的钢种进行孔型设计,并且可以用其它钢种对孔型进行校验,以保证孔型设计满足不同钢种要求。2)不同温度的延伸系数计算。根据不同的轧制工艺对轧件温度的要求,轧件的延伸系数随温度的变化而不同。在计算机孔型设计中,允许设定不同的轧制温度,以相应的轧件延伸系数进行孔型设计。3)不同辊径的延伸系数计算。在计算机孔型设计中,可以根据输入的轧辊直径,自动的对轧件宽度的计算结果进行修正,消除因辊径的变化产生的延伸系数计算误差。4)轧件延伸系数的修正。给定的钢种、温度、辊径的修正系数只是反映了轧件延伸系数随工艺条件改变的大致规律,但是对于特定的生产条件下的轧件的延伸系数计算总存在误差,因此需要进行修正。采用计算机孔型设计可以对每一个钢种、规格和工艺制度下的轧件的宽度修正,并且分别进行保存,以确保轧件宽度计算的准确,满足指导轧机调整的要求。进一步地,对于离合器档位和离合器速比差,对成品前减径机和定径机的a、b、c、d中的4个档位和9个离合器进行优化组合,将减径机和定径机之间的速比差、转数差进行最小化。在本发明的一个实施例中,将减径机之间的速比差控制在0.02以内,减径机和定径机之间的速比差控制在0.06以内,定径机之间的速比差控制在0.02以内;将减径机之间电机的转数差控制在1000转/分钟以内,减径机和定径机之间电机的转数差控制在4000转/分钟以内,定径机之间电机的转数差控制在600转/分钟以内。变速箱档位系统中a、b、c、d这四个档位之间的关系如下:a档位控制电机与减定径机组的总体速比;b档位控制减径和定径机组之间的速度匹配;c档位控制减径机组内的速度匹配;d档位控制定径机组内的速度匹配。减定径变速箱内有9个离合器,通过这9个离合器的不同位置组合来达到传递不同速比的目的。控制系统中将这不同组合归纳为a、b、c、d这四个不同的档位组合,即这档位的数字代表了一定的离合器位置。表5为减定径变速箱中各级传动机构部件组成。表5传动档位传动轴齿轮组离合器aa1、a2、a3ca1-ca9cl1、cl2、cl3bb1、b2、b3cb1-cb6cl4、cl5cc1、c2cc1-cc6cl6、cl7dd1、d2cd1-cd6cl8、cl9根据吐断分析定径机张力较大,即辊轴转速的比值较大。在不考虑与其它架次相对转速变动的情况下,辊轴转速比值q的计算公式如式1所示:q=(b减×减径机速比)/(b定×d×定径机速比)式1其中,b减代表减径机组选择的b级档位的速比,b定代表定径机组选择的b级档位的速比,d代表d级档位选择的速比。式中q值越大,则定径机的张力越大,从式中可以看q值决定的张力只与b和d的档位选择有关。对于常规硬线钢种,减径机两架轧机之间的延伸系数为1.086,减径机和定径机之间的延伸系数为1.035,理论线速度的比值要大于延伸系数,否则会造成堆钢。将其用于生产φ5.5mm的小规格高速线材,对减定径变速箱相关图纸和传动关系研究和对比分析,最终优化为a1、b4、c4、d4的档位选择。进一步地,将吐丝机超前系数控制在0.01~0.03。超前系数的计算公式为:(吐丝速率-轧钢速率)/轧钢速率。吐丝机是高速轧制过程中最后一个控制张力的环节,对于倾角一般为15~30°的吐丝机,合理设定超前系数对实现顺利轧制至关重要。尤其是线材头部在没有完全建立张力关系和尾部失张的条件下,超前系数的设定就是减定径机组轧制速率和吐丝状态的保证。过小的超前系数会造成堆钢,而过大的超前系数会造成张力过大,发生尺寸波动、缩颈和吐断。同时吐丝机超前系数的变化,会引起线卷直径大小及布圈的变化,系数过大,会卷直径偏小,同时沿吐丝机旋转方向左偏。同时过大的系数设置会导致吐丝瞬间失衡侧立,圈形不良无法集卷。超前系数系数过小,会造成轧制过程堆钢和憋钢。因此,本发明提供的控制线材轧制尺寸精度的方法,通过在线材高速轧制过程中,控制成品道次前减定径机组高速轧制中出现的张力,能够降低轧制断线、缩颈问题。并通过对φ5.5mm的小规格线材高速轧制过程中,道次延伸率规律、减定径变速箱速比和传动关系进行分析,归纳总结了减定径各架次电机/辊轴速比的计算,对原有档位选择进行了最终优化,最终解决了减定径机组高速轧制过程的张力不稳定问题。实施例1将本发明的方法用于生产焊线er70s-6中,控制成品前减径机一架和减径机二架的轧辊辊径差均为0.2mm,定径机一架和定径机二架的轧辊辊径差均为0.1mm。控制减定径轧机的辊径配比,相邻的减径机二架和定径机一架的辊径配比为220/150。合理控制轧辊和导卫过钢量,减径机轧辊过钢量不超过1100吨,定径机轧辊过钢量不超过700吨,导卫时间为3小时。成品前四架减定径轧制温度控制在920℃,此温度下材料抗拉强度为150mpa。控制减径机二架的延伸系数为1.086,定径机一架延伸系数为1.055。采用a1、b4、c4、d4档位设置,减径机之间的速比差控制在0.02以内,减径机和定径机之间的速比差控制在0.06以内,定径机之间的速比差控制在0.02以内;减径机之间电机的转数差控制在1000转/分钟以内,减径机和定径机之间电机的转数差控制在4000转/分钟以内,定径机之间电机的转数差控制在600转/分钟以内,吐丝机超前系数控制在0.02。通过该措施,实现生产的焊线中95%能达到er70s-6c级精度,基本消除了缩颈和吐断问题,轧制速率达到110m/s,提高生产效率10%。实施例1-2至实施例1-11的轧制过程与实施例1相同,区别在于改变轧辊辊径差、轧辊和导卫过钢量、轧制温度、延伸系数和吐丝机超前系数。相应的轧制速率和材料抗拉强度见表6。从表6可知,改变上述参数,轧制速率和材料抗拉强度均有所下降,因此实施例1-1、1-4和1-6具有最好的轧制效果。表6实施例2将本发明的方法用于生产焊线82a中,控制成品前减径机一架和减径机二架的轧辊辊径差均为0.1mm,定径机一架和定径机二架的轧辊辊径差均为0.1mm。控制成品前减定径轧机的辊径配比,相邻的减径机二架和定径机一架的辊径配比为220.2/150.1。合理控制轧辊和导卫过钢量,减径机轧辊过钢量不超过1200吨,定径机轧辊过钢量不超过800吨,此温度下材料抗拉强度170mpa,导卫时间为3小时。成品前四架减定径轧制温度控制在880℃,控制减径机二架的延伸系数为1.096,定径机一架延伸系数为1.065。采用a1、b4、c4、d4档位设置,减径机之间的速比差控制在0.02以内,减径机和定径机之间的速比差控制在0.06以内,定径机之间的速比差控制在0.02以内;减径机之间电机的转数差控制在1000转/分钟以内,减径机和定径机之间电机的转数差控制在4000转/分钟以内,定径机之间电机的转数差控制在600转/分钟以内,吐丝机超前系数控制在0.03。通过该措施,实现生产的焊线中98%能达到c级精度,消除了缩颈和吐断问题,轧制速率达到112m/s,提高生产效率12%。以上所述,仅为本发明的具体实施方式,但本发明的保护范围并不局限于此,任何熟悉本
技术领域:
的技术人员在本发明揭露的技术范围内,可轻易想到变化或替换,都应涵盖在本发明的保护范围之内。因此,本发明的保护范围应以所述权利要求的保护范围为准。当前第1页12