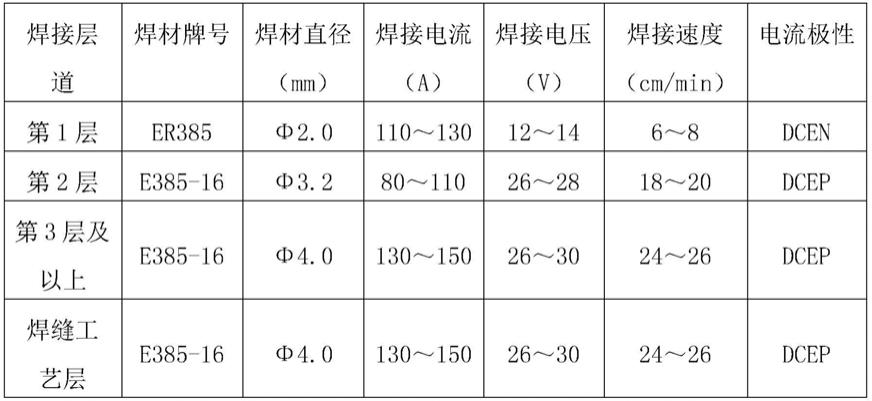
特种工业泵铸造缺陷的补焊修复方法
【技术领域】
1.本发明主要涉及石油、化工特种工业泵设备技术领域,具体为一种904l材质的特种工业泵铸造缺陷补焊修复方法。
背景技术:2.目前,在石油、化工行业里用的工业泵,大部分都是特种工业泵,其泵体、泵盖、叶轮等零件,均采用耐酸、耐碱、耐磨等特殊的不锈钢材料铸造而成;其中用904l材质铸造的泵是比较常见的特种工业泵之一。904l材料为超级奥氏体不锈钢,属低碳高镍、钼奥氏体不锈耐酸钢;具有很好的活化-钝化转变能力,耐腐蚀性能极好,在非氧化性酸如硫酸、醋酸、甲酸、磷酸中具有很好的耐蚀性;在中性含氯离子介质中具有很好的抗点蚀性,同时具有良好的抗缝隙腐蚀及抗应力腐蚀性能。故904l材料被广泛应用于石油、化工行业里特种工业泵的铸造原材料,但因特种工业泵的泵体、泵盖、叶轮等铸造零件,外形尺寸一般比较大,形状复杂,在铸造时,容易产生材质疏松、气孔、裂纹等铸造缺陷;尤其当铸造工艺设置的浇铸冒口、冷铁位置不合理,铸造工艺加强筋不当,金属液浇铸压力等参数不合理时,更容易产生疏松、气孔、裂纹、冷隔、未浇铸满等铸造缺陷。现阶段大部分工业泵生产企业,对使用904l材料铸造的泵零件,如产生的缩松、气孔等缺陷不严重,不影响产品使用强度和使用寿命时,一般进行原样让步接收使用;但对较严重的密集型气孔、疏松、裂纹等铸造缺陷,一是因焊接熔敷金属体积大,焊接产生的温度不能及时扩散降温,焊接应力集中等因素,易产生新的气孔和裂纹等缺陷,不易补焊合格;二是因去除缺陷、焊接工作量大,劳动强度高,所以大部分都作报废处理,重新铸造加工。但重新铸造加工,生产成本大大增加,生产周期也比较长,尤其是一些生产进度比较紧张的泵产品,或者在用户现场急需抢修的泵,不适合用此方法解决
3.由此可见,提供一种特种工业泵铸造缺陷的补焊修复方法是本领域亟需解决的问题。
技术实现要素:4.针对上述问题,本发明特种工业泵铸造缺陷的补焊修复方法易于实施、补焊质量可靠稳定,能满足泵产品的补焊质量要求和生产进度要求。
5.为解决上述问题,本发明特种工业泵铸造缺陷的补焊修复方法包括以下步骤:
6.步骤一:采用机械加工方法或手工打磨去除铸造缺陷,采用渗透探伤pt检测,确保缺陷去除干净。
7.步骤二:制作v形或u形焊接工艺坡口,坡口根部打磨加工成一定的r圆弧;焊接区及热影响区150mm范围内的油污、铁屑、锈迹、灰尘、水份等杂质清除干净。
8.步骤三:确定补焊工艺规范,先采用钨极氩弧焊填充焊接坡口根部,再采用手工电弧焊填充焊道盖面;焊材为焊丝er385及焊条e385-16;焊前不预热,焊接过程中控制层间温度不超过60℃,焊后立即快冷焊缝。
9.步骤四:补焊前将需要的焊材进行预处理,焊丝除油、锈、水份干净,保护气体氩气保持干燥;焊条放在烘箱内按规定温度烘干后,置于保温筒中待用。
10.步骤五:根据补焊工艺规范,对待焊区进行补焊;补焊按照逐层逐道进行焊接,并尽量采用多层道焊接,后一层焊道沿着前一层的方向进行;在每层道焊完后,需将焊渣、焊缝表面氧化皮、飞溅彻底清除干净,并去除不规则的焊瘤;每焊一道后立即用圆头小锤迅速锤遍焊缝。
11.步骤六:补焊后打磨清理焊渣、飞溅干净,补焊部位表面打磨光滑,并与母材齐平。
12.步骤七:采用渗透探伤pt或超声波探伤ut检测补焊部位,以检验补焊质量。
13.进一步的,采用的焊材er385和e385-16,可保证熔焊的焊缝化学成份和抗腐蚀性与904l母材近似或相同。
14.进一步的,焊接工艺坡口制作成v形或u形,坡口根部有一定r圆弧,在焊接时产生的焊接应力分布均匀平缓,填充焊缝金属量小。
15.进一步的,焊缝尽量采用多层道焊接时,后一层焊缝对前一层焊缝有热处理的作用,能细化晶粒,提高焊缝接头的塑性。
16.进一步的,每层道焊缝焊后立即用圆头小捶迅速锤遍焊缝,可减少焊接应力、防止较大的焊接变形。
17.进一步的,904l材质在焊后对焊缝立即进行快冷,相当于焊缝进行固溶处理,可减少裂纹倾向,改善焊缝金属和接头的组织和性能。
18.再者,本发明特种工业泵铸造缺陷的补焊修复方法易于实施、补焊质量可靠稳定,能满足泵产品的补焊质量要求和生产进度要求。
【附图说明】
19.图1是本发明特种工业泵铸造缺陷的补焊修复方法的流程图。
20.图2是焊接工艺坡口形状及焊接层道示意图。
21.1-第1层焊道;2-第2层焊道;3-第3层及以上焊道;4-工艺层焊道;5-铸件母材。
【具体实施方式】
22.本发明所提到的方向用语,例如「上」、「下」、「前」、「后」、「左」、「右」、「内」、「外」、「侧面」等,仅是附图中的方向,只是用来解释和说明本发明,而不是用来限定本发明的保护范围。
23.参见图1,给出了904l材质的特种工业泵铸造缺陷补焊修复方法,具体实施方式和流程步骤如下:
24.步骤1:根据泵铸造零件的外观质量检验报告和探伤检测报告,确定铸造缺陷位置、大小和深度,然后采用机械加工方法去除缺陷。采用机械加工方法去除缺陷时,可通过车、镗、铣、钻等机床加工去除缺陷,也可采用手持式电动旋转锉、电磨头等打磨工具打磨去除缺陷干净,通过肉眼观察,必要时采用渗透探伤pt检测缺陷是否去除干净。
25.步骤2:如图2所示,在铸件母材5上,将焊接工艺坡口加工成v形或u形焊接坡口。清除焊接坡口及坡口150mm范围内热影响区域的油污、铁屑、锈迹、灰尘、水份等杂质干净,并保持干燥。制作v形或u形焊接工艺坡口时,可用手持式电磨头或金属旋转锉等打磨工具。v
型坡口夹角一般为60~70
°
,坡口根部打磨加工成一定的r圆弧。如铸造缺陷为裂纹性质的缺陷,则在制作补焊工艺坡口时,还应在裂纹两末端制作止裂孔,孔大小为φ8~φ10mm,深度根据裂纹深度确定,以防止补焊时裂纹延伸开裂。
26.步骤3:补焊工艺规范确定:对904l材质的铸造缺陷补焊,先采用钨极氩弧焊填充焊接坡口根部,再采用手工电弧焊填充焊道盖面。氩弧焊焊丝为er385,采用纯氩气(ar,纯度99.9%)保护,焊条为e385-16。补焊时,焊前不预热,焊接过程中控制层间温度不超过60℃(可采用红外线测温仪测量),焊后立即进行快冷焊缝。焊接工艺参数如表1所示。
27.表1:焊接工艺参数
[0028][0029]
步骤4:补焊前将需要的焊丝除油、锈、水份干净,保护气体保持干燥;焊条放在烘箱内,在250
°
~280℃温度下烘焙1h,然后放入100℃的焊条保温筒中随用随取。
[0030]
步骤5:根据补焊工艺规范,对待焊区进行补焊,补焊按照逐层逐道进行焊接,并尽量采用多层道焊接。先进行第1层焊道1氩弧焊打底焊接坡口根部,然后第2层焊道2用焊条e385-16,φ3.2进行堆焊,第3层及以上焊道3用焊条e385-16,φ4.0进行堆焊,最后一道盖面焊缝4的焊高略高于母材约1mm。逐层逐道焊接时,后一层焊道沿着前一层的方向进行;尽量采用交叉的多层多焊道进行,直至完成全部焊接;在每层道焊完后,需将焊渣、焊缝表面氧化皮、飞溅彻底清除干净,并去除不规则的焊瘤;每焊一道后立即用圆头小锤迅速捶遍焊缝,以减少应力、防止裂纹产生、防止较大的焊接应力变形。
[0031]
步骤6:补焊完成后,清理焊渣、飞溅等干净;对补焊部位表面进行打磨光滑,并与母材齐平,满足外观质量要求和无损探伤检测要求。
[0032]
步骤7:对补焊部位采用渗透探伤pt或超声波探伤ut检测,检验补焊质量是否符合要求。铸件缺陷修复工作完成并合格后,补焊返修记录存入产品质量档案。
[0033]
实施例1:本发明的一种特种工业泵铸造缺陷补焊修复方法的实例,具体实施步骤如下:
[0034]
第一步:清除铸造缺陷。泵体铸件材质为904l,铸造缺陷有一处密集型气孔;根据无损探伤报告确定缺陷位置和深度,采用电磨头打磨清除气孔缺陷干净。肉眼观察打磨部位无可见气孔后,进行渗透探伤pt检查,确定缺陷去除干净。
[0035]
第二步:制作v形焊接工艺坡口。根据打磨开后的坑槽形状,用手持式金属旋转锉,将坑槽修磨成v形坡口,坡口夹角为65
°
,坡口根部修磨成约r5的半圆弧;清除焊接坡口及坡
口150mm范围内热影响区域的油污、铁屑、锈迹、灰尘、水份等杂质干净,并用丙酮清洗焊接坡口,保持干燥。
[0036]
第三步:确定焊接工艺规范:铸件材质为904l材质,缺陷补焊时,先采用钨极氩弧焊填充焊接坡口根部,再采用手工电弧焊填充焊道盖面;氩弧焊焊丝为er385,采用纯氩气(ar,纯度99.9%)保护,焊条为e385-16;补焊时,焊前不预热,焊接过程中控制层间温度不超过60℃,焊后立即进行快冷焊缝。
[0037]
第四步:焊材预处理。补焊前将需要的焊丝er385除油、锈、水份干净,保护气体(ar,纯度99.9%)保持干燥;焊条e385-16,φ3.2、φ4.0放在烘箱内,在250℃温度下烘焙1h,然后放入100℃的焊条保温筒中待用。
[0038]
第五步:对待焊区进行补焊,补焊时按照逐层逐道进行焊接,并采用了多层道焊接:先进行第1层焊道氩弧焊打底焊接坡口根部,然后第2层焊道用焊条e385-16,φ3.2进行堆焊,第3层及以上焊道用焊条e385-16,φ4.0进行堆焊,最后一道盖面焊缝的焊高略高于母材约1mm;用红外线测温仪测量,层间温度为45℃;焊后用风机对焊缝吹冷风,进行快速冷却。焊接工艺参数值记录如表2所示。在每层道焊完后,将焊缝表面的焊渣、氧化皮、飞溅等彻底清除干净,并去除不规则的焊瘤;每焊一道后立即用圆头小捶迅速锤遍焊缝。
[0039]
表2:焊接工艺参数值记录表
[0040][0041][0042]
第六步:补焊完成后,清理焊渣、飞溅等干净;对补焊部位表面用角磨机打磨光滑,并与母材齐平,满足外观质量要求和无损探伤检测要求。
[0043]
第七步:对补焊部位进行渗透探伤pt检测,结果显示无气孔、裂纹等缺陷;泵体经静水压强度试验,试验合格,补焊质量符合泵质量要求。
[0044]
实施例2:本发明的一种特种工业泵铸造缺陷补焊修复方法的实例,具体实施步骤如下:
[0045]
第一步:清除铸造缺陷。泵体铸件材质为904l,铸造缺陷有一条长35mm、深约10mm的裂纹,缺陷位置位于泵体端面上;根据无损探伤报告确定缺陷位置和深度,在铣床上,采用φ8mm的圆柱铣刀,铣削去除裂纹缺陷干净,沟槽宽铣至8mm;在裂纹两末端用φ10mm的圆柱铣刀制止裂孔φ10mm;肉眼观察铣削面无肉眼可见的裂纹后,进行渗透探伤pt检查,确定缺陷去除干净。
[0046]
第二步:制作u形焊接工艺坡口。根据铣削开的沟槽形状,用手持式金属旋转锉,将沟槽底部修磨成约r4的半圆弧;清除焊接坡口及坡口150mm范围内热影响区域的油污、铁屑、锈迹、灰尘、水份等杂质干净,并用丙酮清洗焊接坡口,保持干燥。
[0047]
第三步:确定焊接工艺规范:铸件材质为904l材质,缺陷补焊时,先采用钨极氩弧焊填充焊接坡口根部,再采用手工电弧焊填充焊道盖面;氩弧焊焊丝为er385,采用纯氩气(ar,纯度99.9%)保护,焊条为e385-16;补焊时,焊前不预热,焊接过程中控制层间温度不超过60℃,焊后立即进行快冷焊缝。
[0048]
第四步:焊材预处理。补焊前将需要的焊丝er385除油、锈、水份干净,保护气体(ar,纯度99.9%)保持干燥;焊条e385-16,φ3.2、φ4.0放在烘箱内,在250℃温度下烘焙1h,然后放入100℃的焊条保温筒中待用。
[0049]
第五步:补焊。对待焊区进行补焊,补焊时按照逐层逐道进行焊接,并采用了多层道焊接:先进行第1层焊道氩弧焊打底焊接坡口根部,然后第2层焊道用焊条e385-16,φ3.2进行堆焊,第3层及以上焊道用焊条e385-16,φ4.0进行堆焊,最后一道盖面焊缝的焊高略高于母材约1mm;用红外线测温仪测量,层间温度为48℃;焊后用风机对焊缝吹冷风,进行快速冷却。焊接工艺参数值记录如表3所示。在每层道焊完后,将焊缝表面的焊渣、氧化皮、飞溅等彻底清除干净,并去除不规则的焊瘤;每焊一道后立即用圆头小锤迅速捶遍焊缝一遍。
[0050]
表3焊接工艺参数值记录表
[0051][0052]
第六步:补焊完成后,清理焊渣、飞溅等干净;在立车机床上,对补焊的泵体端面进行车削,车削后尺寸和表面粗糙度符合图纸要求。
[0053]
第七步:对补焊部位采用渗透探伤pt和超声波ut检测,结果显示无气孔、裂纹等缺陷;泵体经静水压强度试验,试验合格,补焊质量符合泵质量要求。
[0054]
实施例3:本发明的一种特种工业泵铸造缺陷补焊修复方法的实例,具体实施步骤如下:
[0055]
第一步:清除铸造缺陷。泵体铸件材质为904l,在距离泵体表面深约15mm的部位有一块长约25mm、宽约12mm的铸造冷隔层缺陷。根据实物标记的缺陷位置,在镗床上,装夹固定泵体,镗削去除铸造冷隔层缺陷干净;镗削的沟槽长约30mm,宽约15mm,肉眼观察镗削的切削面无肉眼可见冷隔层后,进行渗透探伤pt检查,确定冷隔层缺陷去除干净。
[0056]
第二步:制作u形焊接工艺坡口。根据镗削开的沟槽形状,用手持式金属旋转锉,将
沟槽底部修磨成约r6的半圆弧;清除焊接坡口及坡口155mm范围内热影响区域的油污、铁屑、锈迹、灰尘、水份等杂质干净,并用丙酮清洗,保持干燥。
[0057]
第三步:确定焊接工艺规范:铸件材质为904l材质,缺陷补焊时,先采用钨极氩弧焊填充焊接坡口根部,再采用手工电弧焊填充焊道盖面;氩弧焊焊丝为er385,采用纯氩气(ar,纯度99.9%)保护,焊条为e385-16;补焊时,焊前不预热,焊接过程中控制层间温度不超过60℃,焊后立即进行快冷焊缝。
[0058]
第四步:焊材预处理。补焊前将需要的焊丝er385除油、锈、水份干净,保护气体(ar,纯度99.9%)保持干燥;焊条e385-16,φ3.2、φ4.0放在烘箱内,在252℃温度下烘焙1h,然后放入100℃的焊条保温筒中待用。
[0059]
第五步:补焊。对待焊区进行补焊,补焊时按照逐层逐道进行焊接,并采用了多层道焊接:先进行第1层焊道氩弧焊打底焊接坡口根部,然后第2层焊道用焊条e385-16,φ3.2进行堆焊,第3层及以上焊道用焊条e385-16,φ4.0进行堆焊,最后一道盖面焊缝的焊高略高于母材约1mm;用红外线测温仪测量,层间温度为42℃;焊后用风机对焊缝吹冷风,进行快速冷却。焊接工艺参数值记录如表4所示。在每层道焊完后,将焊缝表面的焊渣、氧化皮、飞溅等彻底清除干净,并去除不规则的焊瘤;每焊一道后立即用圆头小锤迅速捶一遍焊缝。
[0060]
表4焊接工艺参数值记录表
[0061][0062]
第六步:补焊完成后,清理焊渣、飞溅等干净;对补焊部位表面用角磨机打磨光滑,并与母材齐平,满足外观质量要求和无损探伤检测要求。
[0063]
第七步:对补焊部位采用渗透探伤pt检测,结果显示无气孔、裂纹、夹渣等缺陷;泵体经静水压强度试验,试验合格,补焊质量符合泵质量要求。
[0064]
经过所述三个实施例,本发明特种工业泵铸造缺陷补焊修复方法,证明其补焊修复方法可行、操作易于实施、补焊质量可靠稳定,能满足泵产品的补焊质量要求和生产进度要求。
[0065]
此外,应当理解,虽然本说明书按照实施方式加以描述,但并非每个实施方式仅包含一个独立的技术方案,说明书的这种叙述方式仅仅是为清楚起见,本领域技术人员应当将说明书作为一个整体,各实施例中的技术方案也可以经适当组合,形成本领域技术人员可以理解的其他实施方式。