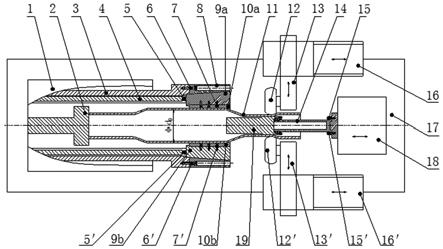
大尺寸胀压成形汽车桥壳用阶梯形管坯缩径
‑
热旋压成形方法
技术领域
1.本发明涉及一种金属管件的塑性成形技术领域,特别是涉及一种大尺寸胀压成形汽车桥壳用阶梯形管坯缩径
‑
热旋压成形方法。
背景技术:2.汽车桥壳属于大尺寸变径异型截面管类零件,在汽车上既是承载件又是传力件,要求有较高的强度、刚度。目前主要用铸造方法和冲压焊接方法制造汽车桥壳,铸件的强度、刚度大,但费材、耗能且生产有污染,冲压焊接件质量轻,但焊缝性能偏低。胀压成形法是制造汽车桥壳的新方法,先将一定规格的无缝钢管两端减径制备出阶梯形管坯,再对阶梯形管坯中部液压胀形,最后对其内部充液后用模具压制成形,制得的汽车桥壳管件整体成形无焊缝,制件强度、刚度高,材料利用率高。
3.胀压成形汽车桥壳用阶梯形管坯,中间直管部分外径大两侧直管外径小,中部外径与两侧外径的比值大于1.60,中部直管与两侧直管之间锥形过渡;长度尺寸较大,一般大于1450mm。
4.胀压成形汽车桥壳用阶梯形管坯理论上可以通过缩经或旋压方法制备。中国专利(cn201310191336.6)公开的重型卡车无焊缝桥壳的整体成形方法,对无缝钢管两端进行多道次大变形自由推压缩径(管坯缩径前后外径的比值一般在1.6
‑
2.0)得到阶梯形管坯,但缩径后管坯壁厚增加50%以上,致使缩径后的管件重量大,而且端部出现翘曲、易产生轴向开裂。中国专利(cn201310191757.9)公开的管坯双侧反向芯轴推压缩径模具及工艺,缩径前先在管坯内部置入芯轴,使用缩径凹模对管坯两端由外向内推压缩径的同时,置于管坯内部的芯轴由内向外运动,该方法在一定程度上解决了缩径后壁厚增加值大及端部翘曲的问题,但缩径成形过程中管坯中部易失稳,而且缩径后退模困难、管坯容易抱死在缩径凹模与芯轴之间。
5.中国专利(cn201710538600.7)公开的高精度管类缩径旋压用组合模具。主要由置于管坯内部的固定芯模、活动芯模、过渡环及尾顶盘等组成,活动芯模紧套在固定芯模外,固定芯模与尾顶盘通过过渡环夹紧活动芯模,这种组合模具适用于两端外径大中部外径小的阶梯形管坯减径旋压,旋压过程较为稳定,旋压后管件成形质量好。中国专利(cn201010288774.0)公开的无缝气瓶正向旋轮热旋压收口方法。先将钢管收口段(长度较短)加热到920~1050℃,对钢管收口段进行6~7道次半椭球形正向封口旋压,再对所得半椭球形封头进行3~4道次底部增厚旋压,最后对封头表面进行光整旋压。
6.胀压成形汽车桥壳用阶梯形管坯中部外径大两侧外径小、长度尺寸大,无法使用中国专利cn201710538600.7中的芯模结构,若采用中国专利cn201010288774.0公开的内容,仅依靠外部旋轮进行大变形减径成形,需要经过多道次旋压,成形时间长、制造成本高,而且很难保证管坯的壁厚要求和成形质量,大变形旋压后表面会出现凹凸不平现象。
技术实现要素:7.本发明的目的在于克服上述现有技术存在的不足,提供一种大尺寸胀压成形汽车桥壳用阶梯形管坯缩径
‑
热旋压成形方法。该发明的制件壁厚增加值较自由推压缩径减少15%~25%,减轻管件重量10%~15%;管坯两侧经过大变形减径时,中部不失稳、端部无翘曲、不开裂。并且生产效率高、制造成本低、成形质量好。
8.为实现上述目的,本发明提供的大尺寸胀压成形汽车桥壳用阶梯形管坯缩径
‑
热旋压成形方法,该方法包括以下步骤:步骤1:选用外径φd0、壁厚t0、长度l0的初始无缝钢管管坯。
9.步骤2:保持中部l
11
长度的部分不变,对其两侧进行自由推压缩径得到特定的缩径管坯,缩径部分外径减至φd1=(0.60~0.75)φd0、壁厚增至t1=(1.25~1.40)t0,缩径部分与中部初始管坯之间锥形过渡,半锥角c1=15~25
°
,管坯外径φd1的直臂部分与缩径后的锥面之间大圆弧过渡,过渡圆弧r1=40~100mm,两侧缩径部分的长度分别为l
12
、l
13
。
10.步骤3:加热缩径管坯右端缩径部分,加热温度t=900~1050℃。
11.步骤4:在旋压机上装卡管坯,将缩径管坯的左端放入旋压机空心主轴箱内,利用旋压机卡盘分块ⅰ、ⅱ及装在其上的夹持模分块ⅰ、ⅱ、ⅲ、ⅳ、
ⅴ
、
ⅵ
夹紧缩径管坯中部外径φd0的右端部分,利用顶杆顶住管坯的左端面,将前段小径后段大径的阶梯形芯棒从管坯右端置入管坯内腔,旋轮驱动系统带动管坯前后两侧旋轮ⅰ、ⅱ置于管坯缩径部分与锥形部分的过渡处。
12.步骤5:管坯右侧正旋压减径,旋压机主轴驱动卡盘分块ⅰ、ⅱ带动缩径后管坯转动,位于管坯前后两侧旋轮ⅰ、ⅱ工进正旋压,同时芯棒驱动系统带动阶梯形芯棒同步向管坯外端移动,使管坯右侧部分外径由φd1减径至φd2,φd2=(0.80~0.90)φd1,壁厚由t1增加至t2,t2=(1.05~1.15)t1,长度由l
12
增加至l
21
;减径后的管坯内表面接触阶梯形芯棒大直径段外表面,管坯外径φd2的直臂部分与正旋压后的锥面之间大圆弧过渡,过渡圆弧r2=100~160mm。
13.步骤6:管坯右侧反旋压减薄,旋轮驱动系统带动前后两侧旋轮ⅰ、ⅱ沿水平方向由管坯外端向内工进反旋压,同时芯棒驱动系统带动阶梯形芯棒在管坯内部同步由右向左移动,使右侧正旋压减径后的管坯内径不变,外径由φd2减径至φd3,壁厚由t2减至t3,长度由l
21
增加至l
31
,满足t3=(1.05~1.20)t0。
14.步骤7:旋轮驱动系统将前后两侧旋轮ⅰ、ⅱ快速移动至管坯的外端,同时阶梯形芯棒向外移动,将阶梯形芯棒大径的后段移出管坯,小径的前段位于管坯内腔。
15.步骤8:管坯右端反旋压减径增厚,旋轮驱动系统带动前后两侧旋轮由管坯外端向内工进反旋压,使管坯右端长度l
42
的部分外径由φd3减径至φd4,φd4=(0.80~0.90)φd3,壁厚由t3增加至t4,t4=(1.05~1.15)t3;端部外径φd4的部分与外径φd3的部分之间锥形过渡,半锥角c2=15~25
°
,管坯端部外径φd4的直臂部分与反旋压后的锥面之间大圆弧过渡,过渡圆弧r3=40~100mm。
16.步骤9:取件,旋压机主轴停止转动,芯棒驱动系统带动芯棒退出,前后两侧旋轮系统带动前后旋轮ⅰ、ⅱ径向退出,夹持模分块ⅰ、ⅱ、ⅲ、ⅳ、
ⅴ
、
ⅵ
松开夹持的管坯,顶杆驱动系统带动顶杆向右移动,顶出管坯,卸料取件。
17.步骤10:对于管坯缩径后的左侧部分,按步骤3
‑
步骤9进行,完成缩径管坯左侧部
分的旋压加工。
18.所述旋轮ⅰ、ⅱ正旋压减径时轴向进给速度与主轴转速比值f1=0.4~1.0mm/r;反旋压减薄时旋轮ⅰ、ⅱ轴向进给速度与主轴转速比值f2=0.1~0.5mm/r;反旋压减径增厚时旋轮ⅰ、ⅱ轴向进给速度与主轴转速比值f3=0.1~0.5mm/r。
19.一种用于大尺寸胀压成形汽车桥壳用阶梯形管坯缩径
‑
热旋压成形方法的旋压机,所述旋压机由主轴箱、底座、卡盘驱动系统、旋轮驱动系统、芯棒驱动系统、芯棒组件、顶杆驱动系统及顶杆组成,其中:所述主轴箱为空心结构,内部设置卡盘驱动系统,所述卡盘驱动系统由主轴、拉杆、铰链ⅰ、ⅱ、夹盘、卡盘分块ⅰ、ⅱ及夹持模分块ⅰ、ⅱ、ⅲ、ⅳ、
ⅴ
、
ⅵ
组成,卡盘驱动系统驱动拉杆纵向移动时,通过铰链ⅰ、ⅱ带动卡盘分块ⅰ、ⅱ及夹持模分块ⅰ、ⅱ、ⅲ、ⅳ、
ⅴ
、
ⅵ
沿夹盘楔形面纵向移动,使夹持模分块ⅰ、ⅱ、ⅲ、ⅳ、
ⅴ
、
ⅵ
夹紧、松开管坯,卡盘驱动系统转动时带动夹持的管坯一起转动。
20.所述旋轮驱动系统水平布置在前后两侧,由旋轮ⅰ、ⅱ、纵向进给组件ⅰ、ⅱ及在其上横向运动的径向进给组件ⅰ、ⅱ组成,旋轮ⅰ、ⅱ通过轴承安装在径向进给组件ⅰ、ⅱ上,由径向进给组件ⅰ、ⅱ带动实现径向进给与退出,纵向进给组件ⅰ、ⅱ由电机通过丝杠或由液压缸驱动实现纵向移动。
21.所述芯棒驱动系统由电机通过齿轮齿条机构驱动实现纵向移动,芯棒组件由芯棒、轴挡卡簧、轴承、轴承盖及芯棒支撑轴组成,芯棒组件通过芯棒支撑轴安装在芯棒驱动系统上。
22.所述顶杆驱动系统由电机通过丝杠或由液压缸驱动实现纵向移动,顶杆由顶杆驱动系统带动纵向移动,用于顶住管坯左端面,旋压时可随管坯同步旋转,旋压后向右移动将旋压后管坯顶出。
23.所述夹持模分块ⅰ、ⅱ、ⅲ、ⅳ、
ⅴ
、
ⅵ
由6块相同结构的扇形体组成,每块扇形体左右两侧面夹角为45
°
,扇形体的轴向长度l6=(1.00~1.20)φd0,外表面为圆柱面,其直径φd1=(1.30 ~1.50)φd0;内表面由圆柱面和圆锥面组成,圆柱面的直径φd2=(1.03 ~1.05)φd0,圆锥面的半锥角c3与缩径后管坯的半锥角c1相等,圆锥面的轴向长度l
61
=10~15mm。
24.所述芯棒为前段小径后段大径的阶梯形轴,右端带有阶梯形圆孔用于安装轴承及芯棒支撑轴,旋压时芯棒可随管坯同步旋转;所述芯棒前段直径φd
x1
、长度l
x1
根据阶梯形管坯端部的外径φd4、壁厚t4及长度l
42
确定,直径φd
x1
=φd4‑
(2.05
‑
2.10)t4,l
x1
=(1.10~1.20)l
42
,后段直径φd
x2
根据反旋压减薄后的外径φd3和壁厚t3确定,直径φd
x2
=φd3‑
(2.05
‑
2.10)t3,长度l
x2
=(0.80~1.20)φd3。
25.本发明的有益效果是:大尺寸胀压成形汽车桥壳用阶梯形管坯,左右两侧经过大变形减径后,壁厚增加值较自由推压缩径减少15%~25%,减轻管件重量10%~15%;管坯两侧经过大变形减径时,中部不失稳、端部无翘曲、不开裂;生产效率高,制造成本低,成形质量好。
附图说明
26.图1是大尺寸阶梯形管坯缩径
‑
热旋压成形方法初始无缝钢管;图2是大尺寸阶梯形管坯缩径
‑
热旋压成形方法缩径后管坯;图3是大尺寸阶梯形管坯缩径
‑
热旋压成形方法右侧减径正旋压示意图;
图4是大尺寸阶梯形管坯缩径
‑
热旋压成形方法右侧减径正旋压后管坯;图5是大尺寸阶梯形管坯缩径
‑
热旋压成形方法右侧减薄反旋压后管坯;图6是大尺寸阶梯形管坯缩径
‑
热旋压成形方法右端增厚减径反旋压示意图;图7是大尺寸阶梯形管坯缩径
‑
热旋压成形方法右端增厚减径反旋压后管坯;图8是大尺寸阶梯形管坯缩径
‑
热旋压成形方法制备阶梯形管坯;图9是大尺寸阶梯形管坯缩径
‑
热旋压成形方法热旋压用的夹持模分块主视图;图10是大尺寸阶梯形管坯缩径
‑
热旋压成形方法热旋压用的夹持模分块左视图;图11是大尺寸阶梯形管坯缩径
‑
热旋压成形方法热旋压用芯棒组件;图12是大尺寸阶梯形管坯缩径
‑
热旋压成形方法热旋压用阶梯形芯棒。
27.在上述附图中,1.主轴箱,2.顶杆,3.主轴,4.拉杆,5、5
′
.铰链ⅰ、ⅱ,6、6
′
.螺钉ⅰ、ⅱ,7、7
′
.螺钉ⅲ、ⅳ,8.夹盘,9a、9b.卡盘分块ⅰ、ⅱ,10a、10b、10c、10d、10e、10f.夹持模分块ⅰ、ⅱ、ⅲ、ⅳ、
ⅴ
、
ⅵ
,11.管坯,12、12
′
.旋轮ⅰ、ⅱ,13、13
′
.旋轮径向进给组件ⅰ、ⅱ,14.芯棒支撑轴,15、15
′
.螺钉
ⅴ
、
ⅵ
,16、16
′
.旋轮纵向进给组件ⅰ、ⅱ,17.底座,18.芯棒驱动系统,19.芯棒,20.轴挡卡簧,21.轴承,22.毡圈油封,23.螺钉
ⅶ
,24.轴承盖。
具体实施方式
28.实施例针对某轴荷11t的胀压成形桥壳用阶梯形管坯,缩径
‑
热旋压成形方法,包括以下步骤:步骤1:选用外径φd0=φ273mm,壁厚t0=12mm,长度l0=1480mm的初始无缝钢管管坯11。初始无缝钢管管坯如图1所示。
29.步骤:2:保持中部l
11
=622mm长度的部分不变,对其两侧进行自由推压缩径得到特定的缩径管坯11,缩径部分外径减至φd1=φ200mm、壁厚增至t1=15.1mm,缩径部分与中部初始管坯11之间锥形过渡,半锥角c1=20
°
,管坯11外径φ200mm的直臂部分与缩径后的锥面之间大圆弧过渡,过渡圆弧r1=50mm,两侧缩径部分的长度分别为l
12
=352mm、l
13
=352mm。阶梯形管坯缩径
‑
热旋压成形方法缩径后管坯如图2所示。
30.步骤3:加热缩径管坯11右端缩径部分,加热温度t=900~1050℃。
31.步骤4:在旋压机上装卡管坯11,将缩径管坯11的左端放入旋压机空心主轴箱1内,利用旋压机卡盘分块ⅰ、ⅱ(9a、9b)及装在其上的夹持模分块ⅰ、ⅱ、ⅲ、ⅳ、
ⅴ
、
ⅵ
(10a、10b、10c、10d、10e、10f)夹紧缩径管坯11中部外径φd0=φ273mm的右端部分,利用顶杆2顶住管坯11的左端面,将前段小径后段大径的阶梯形芯棒19从管坯11右端置入管坯11内腔,旋轮驱动系统带动管坯11前后两侧旋轮ⅰ、ⅱ(12、12
′
)置于管坯11缩径部分与锥形部分的过渡处。
32.步骤5:管坯11右侧正旋压减径,旋压机主轴驱动卡盘分块ⅰ、ⅱ(9a、9b)带动缩径后管坯11转动,位于管坯11前后两侧旋轮ⅰ、ⅱ(12、12
′
)工进正旋压,同时芯棒驱动系统18带动阶梯形芯棒19同步向管坯11外端移动,使管坯11右侧部分外径由φd1=φ200mm减径至φd2=φ173mm,壁厚由t1=15.1mm增加至t2=16.1mm,长度由l
12
=352mm增加至l
21
=381mm;减径后的管坯11内表面接触阶梯形芯棒19大直径段外表面,管坯11外径φ173mm的直臂部分与正旋压后的锥面之间大圆弧过渡,过渡圆弧r2=120mm。阶梯形管坯缩径
‑
热旋压成形方法右
侧减径正旋压后管坯如图4所示。
33.步骤6:管坯11右侧反旋压减薄,旋轮驱动系统带动前后两侧旋轮ⅰ、ⅱ(12、12
′
)沿水平方向由管坯11外端向内工进反旋压,同时芯棒驱动系统18带动阶梯形芯棒19在管坯11内部同步由右向左移动,使右侧正旋压减径后的管坯11内径不变,外径由φd2=φ173mm减径至φd3=φ170mm,壁厚由t2=16.1mm减至t3=13.5mm,长度由l
21
=381mm增加至l
31
=453mm。阶梯形管坯缩径
‑
热旋压成形方法右侧减薄反旋压后管坯如图5所示。
34.步骤7:旋轮驱动系统将前后两侧旋轮ⅰ、ⅱ(12、12
′
)快速移动至管坯11的外端,同时阶梯形芯棒19向外移动,将阶梯形芯棒19大径的后段移出管坯11,小径的前段位于管坯11内腔。
35.步骤8:管坯11右端反旋压减径增厚,旋轮驱动系统带动前后两侧旋轮ⅰ、ⅱ(12、12
′
)由管坯11外端向内工进反旋压,使管坯11右端长度150mm的部分外径由φd3=φ170mm减径至φd4=φ150mm,壁厚由t3=13.5mm增加至t4=14mm;端部外径φd4=φ150mm的部分与φd3=φ170mm的部分之间锥形过渡,半锥角c2=20
°
,管坯11端部外径φ150mm的直臂部分与反旋压后的锥面之间大圆弧过渡,过渡圆弧r3=50mm。阶梯形管坯缩径
‑
热旋压成形方法制备的阶梯形管坯如图8所示。
36.步骤9:取件,旋压机主轴3停止转动,芯棒驱动系统18带动芯棒19退出,前后两侧旋轮系统带动前后两侧旋轮ⅰ、ⅱ(12、12
′
)径向退出,夹持模分块(10a、10b、10c、10d、10e、10f)松开夹持的管坯11,顶杆驱动系统带动顶杆2向右移动,顶出管坯11,卸料取件。
37.步骤10:对于管坯11缩径后的左侧部分进行步骤(3)
‑
步骤(9)步,完成缩径管坯11左侧部分的旋压。
38.一种用于大尺寸胀压成形汽车桥壳用阶梯形管坯缩径
‑
热旋压成形方法的旋压机,所述旋压机由主轴箱1、底座17、卡盘驱动系统、旋轮驱动系统、芯棒驱动系统18、芯棒组件、顶杆驱动系统、顶杆2等组成。主轴箱1为空心结构,内部设置卡盘驱动系统,卡盘驱动系统由主轴3、拉杆4、铰链ⅰ、ⅱ(5、5
′
)、夹盘8、卡盘分块ⅰ、ⅱ(9a、9b)及夹持模分块ⅰ、ⅱ、ⅲ、ⅳ、
ⅴ
、
ⅵ
(10a、10b、10c、10d、10e、10f)组成,卡盘驱动系统驱动拉杆4纵向移动时,通过铰链ⅰ、ⅱ(5、5
′
)带动卡盘分块ⅰ、ⅱ(9a、9b)及夹持模分块ⅰ、ⅱ、ⅲ、ⅳ、
ⅴ
、
ⅵ
(10a、10b、10c、10d、10e、10f)沿夹盘8楔形面纵向移动,使夹持模分块ⅰ、ⅱ、ⅲ、ⅳ、
ⅴ
、
ⅵ
(10a、10b、10c、10d、10e、10f)夹紧、松开管坯11,卡盘驱动系统转动时带动夹持的管坯11一起转动。旋轮驱动系统水平布置在前后两侧,由旋轮ⅰ、ⅱ(12、12
′
)、纵向进给组件(16、16
′
)及在其上横向运动的径向进给组件ⅰ、ⅱ(13、13
′
)组成,旋轮ⅰ、ⅱ(12、12
′
)通过轴承安装在径向进给组件ⅰ、ⅱ(13、13
′
)上,由径向进给组件ⅰ、ⅱ(13、13
′
)带动实现径向进给与退出,纵向进给组件ⅰ、ⅱ(16、16
′
)由电机通过丝杠或由液压缸驱动实现纵向移动。芯棒驱动系统18由电机通过齿轮齿条机构驱动实现纵向移动,芯棒组件由芯棒19、轴挡卡簧20、轴承21、轴承盖24、芯棒支撑轴14等组成,芯棒组件通过芯棒支撑轴14安装在芯棒驱动系统18上。顶杆驱动系统由电机通过丝杠或由液压缸驱动实现纵向移动,顶杆2由顶杆驱动系统带动纵向移动,用于顶住管坯11左端面,旋压时可随管坯11同步旋转,旋压后向右移动将旋压后管坯11顶出。
39.所述旋压机用夹持模分块ⅰ、ⅱ、ⅲ、ⅳ、
ⅴ
、
ⅵ
(10a、10b、10c、10d、10e、10f)由6块相同结构的扇形体组成,每块扇形体左右两侧面夹角为45
°
,扇形体的轴向长度l6=300mm,外表面为圆柱面,其直径φd1=φ380mm;内表面由圆柱面和圆锥面组成,圆柱面的直径φd2=
φ276mm,圆锥面的半锥角c3与缩径后管坯的半锥角c1相等,c3=20
°
,圆锥面的轴向长度l
61
=15mm。
40.所述旋压机用芯棒19为前段小径后段大径的阶梯形轴,右端带有阶梯形圆孔用于安装轴承21及芯棒支撑轴14,旋压时芯棒19可随管坯11同步旋转;阶梯形芯棒19前段直径φd
x1
=φ143mm,l
x1
=160mm,后段直径φd
x2
=φ122mm,长度l
x2
=170mm。