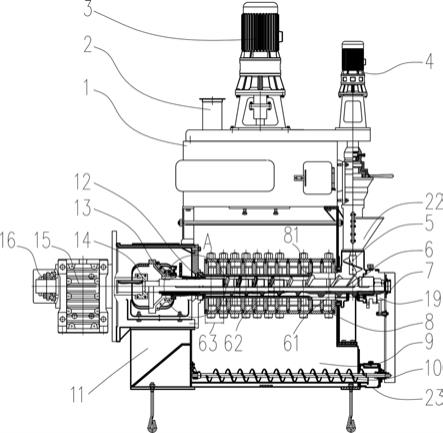
1.本实用新型涉及榨油设备制造领域,特别是一种螺旋榨油机。
背景技术:2.现有的大型螺旋榨油机一般用于棉籽、菜籽、葵花籽、花生等高含油植物油料的压榨制油,为提高榨油效率,通常将螺旋轴设置为具有不同螺距的多段结构。例如中国专利文献 cn202895733u中一种单螺旋轴榨油机记载的结构。通常螺旋轴设置的结构是将进料口设置在靠近减速器的一端,而出料口设置在远离减速器的一端,例如中国专利文献cn 202367960u中记载的结构。而发明人发现,对于大型的榨油机构而言通常轴的直径较大,处理效率较高,而且轴的长度达到2米,而在低速高负载工况下,榨油轴存在变形的问题,越是在螺距小的一端,负载更大,变形也相对越大。很容易增大减速器、轴承和一些活动机构的磨损,影响设备的使用寿命。现有的大型榨油机构的油渣含油率很难低于12%。
技术实现要素:3.本实用新型所要解决的技术问题是提供一种螺旋榨油机,能够延长设备,尤其是螺旋轴和减速器的使用寿命。优选的方案中,能够降低油渣的含油率。
4.为解决上述技术问题,本实用新型所采用的技术方案是:一种螺旋榨油机,包括可转动的榨油轴,榨油轴的表面设有螺旋齿片,榨油轴设置在固设的榨膛内,榨膛的内壁设有用于过滤的栅网,栅网包覆在螺旋齿片的外围,榨油轴的一端通过联轴器与减速器连接,榨油轴的另一端通过轴承座支承在机架上,榨油轴的外壁设有初榨段和复榨段,所述的初榨段的螺旋齿片与栅网间的空间容积较大,复榨段的螺旋齿片与栅网间的空间容积较小,复榨段位于榨油轴靠近连接减速器的一端。
5.优选的方案中,复榨段的外接圆直径小于初榨段的外接圆直径;
6.与复榨段相对应的榨膛的内径小于与初榨段相对应的榨膛的内径;
7.在两段的榨膛之间设有内锥面连接环。
8.优选的方案中,与初榨段相对应的榨膛内壁与初榨段螺旋齿片顶部的间隙大于与复榨段相对应的榨膛内壁与复榨段螺旋齿片顶部的间隙。
9.优选的方案中,在榨膛靠近减速器的一端设有固设的出渣法兰,在出渣法兰上设有出渣口,出渣口靠近榨膛的一端内径较小,远离榨膛的一端内径较大;
10.出渣口位于榨油轴的外围。
11.优选的方案中,在榨油轴的外壁还设有出渣轴套,出渣轴套靠近榨膛的一端外径较小,远离榨膛的一端外径较大,出渣轴套靠近榨膛的一端伸出到出渣口之外。
12.优选的方案中,在出渣口靠近榨膛的一端还设有倒锥形段,倒锥形段入口的内径较大,远离入口的内径较小,倒锥形段的长度小于整个出渣口长度的1/3。
13.优选的方案中,所述的减速器中,螺旋齿蜗轮的轴一端与联轴器连接,另一端通过圆锥辊子轴承支承在机架上,以承受径向力和轴向拉力;
14.螺旋齿锥齿轮与螺旋齿蜗轮啮合连接;
15.螺旋齿蜗轮和螺旋齿锥齿轮的齿均采用硬齿面结构。
16.优选的方案中,螺旋齿锥齿轮和螺旋齿蜗轮密封设置在减速器的壳体内,在壳体上设有进油口和回油口,进油口和回油口通过管路与润滑油箱连接,进油口的管路上设有注油泵,通过循环的润滑油给螺旋齿锥齿轮和螺旋齿蜗轮接触位置的齿面降温。
17.优选的方案中,榨膛位于榨油箱内,榨油箱的底部设有绞龙轴,绞龙轴通过传动机构与榨油轴连接,由榨油轴带动绞龙轴旋转。
18.优选的方案中,在榨油箱的上方还设有加热进料斗,加热进料斗内设有由拌和电机驱动的拌和装置,加热进料斗内设有加热装置,用于加热油料;
19.在加热进料斗的顶部设有进料口,在加热进料斗底部的一侧设有供料口,供料口内设有由送料电机驱动的送料轴,送料轴外壁设有螺旋叶片;
20.供料口的底部位于榨油轴的初榨段上方。
21.本实用新型提供的一种螺旋榨油机,通过改进的榨油轴布置结构,使重载的位置更靠近减速器,减少榨油轴远端的变形,从而提高榨油轴的使用寿命。减速器采用了螺旋齿蜗轮与螺旋齿锥齿轮传动的结构,传递扭矩能达到13000n
·
m,传动比为22~26,优选的为25.26。设置的循环润滑油能够辅助减速器降温,进一步延长减速器的使用寿命。榨膛与榨油轴的配合结构,进一步提高了出油率,经检测,以油菜籽为例,在初榨段尾端的油渣含油率为29%,在排渣口的油渣含油率为9%~11%,含油率较之前的设备降低1~3个百分点。
附图说明
22.下面结合附图和实施例对本实用新型作进一步说明:
23.图1为本实用新型的主视图。
24.图2为图1中a处的局部放大示意图。
25.图3为减速器的内部结构示意图。
26.图中:加热进料斗1,进料口2,拌和电机3,送料电机4,送料轴5,榨油轴6,初榨段61,复榨段62,光轴段63,传动机构7,榨膛8,内锥面连接环81,榨油箱9,内料桶91,绞龙轴10,排渣口11,出渣口12,倒锥形段121,保护罩13,联轴器14,减速器15,圆锥辊子轴承16,螺旋齿蜗轮17,螺旋齿锥齿轮18,机架19,出渣法兰20,出渣轴套21,供料口22、排油口23。
具体实施方式
27.如图1~3中,一种螺旋榨油机,包括可转动的榨油轴6,榨油轴6的表面设有螺旋齿片,榨油轴6设置在固设的榨膛8 内,榨膛8的内壁设有用于过滤的栅网,栅网包覆在螺旋齿片的外围,榨油轴6的一端通过联轴器14与减速器15连接,榨油轴6的另一端通过轴承座支承在机架19上,榨油轴6的外壁设有初榨段61和复榨段62,所述的初榨段61的螺旋齿片与栅网间的空间容积较大,复榨段62的螺旋齿片与栅网间的空间容积较小,复榨段62位于榨油轴6靠近连接减速器15的一端。油料例如棉籽、菜籽、葵花籽、花生等进入到初榨段61被互相挤压榨油,此处扭矩相对较低,而在进入到复榨段62后,油料的体积被进一步挤压,此处的扭矩相对较高,由于此处靠近减速器15,榨油轴6的变形相对较小,从而延长了榨油轴6的使用寿命。
28.优选的方案如图1中,复榨段62的外接圆直径小于初榨段61的外接圆直径;与复榨段62相对应的榨膛8的内径小于与初榨段61相对应的榨膛8的内径;由此结构,以使油料从初榨段61到复榨段62具有较大的压缩比,从而提高榨油效率。
29.在两段的榨膛8之间设有内锥面连接环81。由此结构,提高初榨段61的榨油效率,降低此处油渣的含油率。经测试采用该结构,能够降低初榨段61出来油渣的含油率1~2%。内锥面连接环81优选采用合金钢材质例如20crmnti、20crmnmo和17crnimo6,表面渗碳淬火处理。
30.优选的方案如图1中,与初榨段61相对应的榨膛8内壁与初榨段61螺旋齿片顶部的间隙大于与复榨段62相对应的榨膛8内壁与复榨段62螺旋齿片顶部的间隙。由此结构,使初榨段61能够容纳较多的油料,而在进入复榨段62之后,油料的体积大幅压缩,从而提高榨油效率,并配合内锥面连接环81的结构提高出油率。
31.优选的方案如图1中,在榨膛8靠近减速器15的一端设有固设的出渣法兰20,在出渣法兰20上设有出渣口12,出渣口12靠近榨膛8的一端内径较小,远离榨膛8的一端内径较大;
32.出渣口12位于榨油轴6的外围。由此结构,在出渣的位置能够避免堵塞,出渣顺畅。
33.优选的方案如图1、2中,在榨油轴6的外壁还设有出渣轴套21,出渣轴套21靠近榨膛8的一端外径较小,远离榨膛8的一端外径较大,出渣轴套21靠近榨膛8的一端伸出到出渣口12之外。由此结构便于引导油渣排出,并避免将榨油轴6抱紧,从而影响榨油轴6的转动。
34.优选的方案如图1、2中,在出渣口12靠近榨膛8的一端还设有倒锥形段121,倒锥形段121入口的内径较大,远离入口的内径较小,倒锥形段121的长度小于整个出渣口12长度的1/3。由此结构,能够在不影响排渣的前提下,进一步对油渣进行压榨,从而提高出油率,经测算,由此结构,进一步降低油渣的含油率1%~2%。
35.优选的方案如图1、3中,所述的减速器15中,螺旋齿蜗轮17的轴一端与联轴器14连接,另一端通过圆锥辊子轴承16支承在机架19上,以承受径向力和轴向拉力;
36.螺旋齿锥齿轮18与螺旋齿蜗轮17啮合连接;
37.螺旋齿蜗轮17和螺旋齿锥齿轮18的齿均采用硬齿面结构。本例中采用了硬齿面的传动结构,进一步提高了减速器的使用寿命,所述的硬齿面结构采用为采用20crmnti、20crmnmo或17crnimo6等低碳合金钢,经过表面渗碳和淬火后的结构,齿的表面硬度可以达到hrc61以上。设置的圆锥辊子轴承16克服了螺旋齿蜗轮17和螺旋齿锥齿轮18传动过程中产生的轴向拉力。
38.优选的方案中,螺旋齿锥齿轮18和螺旋齿蜗轮17密封设置在减速器15的壳体内,在壳体上设有进油口和回油口,进油口和回油口通过管路与润滑油箱连接,进油口的管路上设有注油泵,通过循环的润滑油给螺旋齿锥齿轮18和螺旋齿蜗轮17接触位置的齿面降温。进油口、回油口和注油泵的结构在图中未示出。由此结构,通过循环的润滑油进一步的降低了减速器15的温度,延长了减速器15的使用寿命。
39.优选的方案如图1中,榨膛8位于榨油箱9内,榨油箱9的底部设有绞龙轴10,绞龙轴10通过传动机构7与榨油轴6连接,优选的,传动机构7为链传动机构,由榨油轴6带动绞龙轴10旋转。由此结构,能够避免油中所含的重质沉渣在榨油箱9的底部沉淀,造成后继清理困难。
40.优选的方案如图1中,在榨油箱9的上方还设有加热进料斗1,加热进料斗1内设有由拌和电机3驱动的拌和装置,加热进料斗1内设有加热装置,加热装置优选采用电热丝加热器或微波加热器,用于加热油料至60~85℃,优选为70~75℃,以提高出油率;本例中优选采用微波加热器,微波加热器能够降低油料中的水分,提高出油率。
41.在加热进料斗1的顶部设有进料口2,在加热进料斗1底部的一侧设有供料口22,供料口22内设有由送料电机4驱动的送料轴5,送料轴5外壁设有螺旋叶片;
42.供料口22的底部位于榨油轴6的初榨段61上方,用于给初榨段61进料。
43.使用时如图1中,油料通过进料口2送入到加热进料斗1内,启动加热装置,将油料加热到70~75℃,同时启动拌和电机3,带动加热进料斗1内的拌和装置,油料温度达到后,将供料口22位置的闸门开启,炒热的油料进入到供料口22内,启动送料电机4,带动送料轴5旋转,启动榨油电机带动榨油轴6旋转,榨油电机在图中未示出。送料轴5上的螺旋叶片将油料推送至榨油轴6的初榨段61,经过挤压后,油从榨膛8的栅网过滤后排入到榨油箱9内,在内锥面连接环81的位置,初榨的油渣经过一次挤压后进入到复榨段62,复榨段62的位置油渣被进一步的挤压,本例中的复榨段62的齿根圆直径进一步增加,使复榨段62的螺旋齿片之间的容积进一步减小,且榨油轴6的抗扭性能进一步提升,在复榨段62的螺旋齿片的螺距也不相同,靠近减速器15的一端螺距较小,远离减速器15的一端螺距较大。在榨油轴6复榨段62之后靠近减速器15的一端还设有光轴段63,该处没有螺旋齿片,在光轴段63油渣被进一步挤压并整形,以便于在经过出渣口12的倒锥形段121时再进一步被压榨,经过倒锥形段121后,油渣的压力消失,经过一根竖直杆后被破碎落入到排渣口11被排出。在联轴器14的外围设有保护罩13,用于避免油渣进入到联轴器14或减速器内。榨油轴6同时带动绞龙轴10旋转,绞龙轴10上设有螺旋叶片,一是将油液搅动避免沉淀,二是将油液从绞龙轴10一端的排油口排出。
44.上述的实施例仅为本实用新型的优选技术方案,而不应视为对于本实用新型的限制,本申请中的实施例及实施例中的特征在不冲突的情况下,可以相互任意组合。本实用新型的保护范围应以权利要求记载的技术方案,包括权利要求记载的技术方案中技术特征的等同替换方案为保护范围。即在此范围内的等同替换改进,也在本实用新型的保护范围之内。