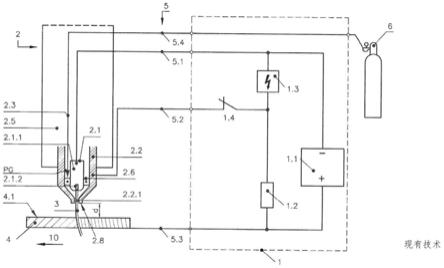
1.本发明涉及用于等离子切割工件的方法和布置结构。
背景技术:2.热学上高度加热的导电气体被称为等离子体,所述气体由正离子和负离子、电子以及被激发的且中性的原子和分子组成。
3.使用不同的气体作为等离子气体,例如单原子的氩气或氦气和/或双原子气体(氢气、氮气、氧气)或空气。这些气体通过等离子弧的能量电离和离解。
4.等离子束可以在其参数方面强烈受喷嘴和电极的构型影响。等离子束的这些参数例如是射束直径、温度、能量密度和气体的流速。
5.在等离子切割中,等离子体例如通过可以是气冷或水冷的喷嘴来收束。为此,喷嘴具有喷嘴孔,等离子束流过喷嘴孔。由此,能量密度可以达到2
×
106w/cm2。在等离子束中出现高达30000℃的温度,该温度与气体的高流速相关联地在所有导电材料上实现非常高的切割速度。
6.等离子切割现今是一种用于切割导电材料的常规方法,其中,按照切割任务使用不同的气体和气体混合物。
7.等离子燃烧器通常由一个等离子燃烧器头和一个等离子燃烧器杆组成。在等离子燃烧器头中紧固有电极和喷嘴。等离子气体在所述电极和喷嘴之间流动,所述等离子气体通过喷嘴孔喷出。在大多数情况下,等离子气体通过安置在电极与喷嘴之间的气体引导部来引导并且可以被置于旋转中。现代的等离子燃烧器还具有用于第二介质的供应部,所述第二介质要么是气体要么是液体。喷嘴于是被喷嘴保护罩(也称为第二气体罩)包围。喷嘴特别是在液体冷却的等离子燃烧器中通过例如在de 10 2004 049 445a1中所描述的喷嘴罩来固定。冷却介质于是在喷嘴罩与喷嘴之间流动。第二介质在喷嘴或喷嘴罩与喷嘴保护罩之间流动并且从喷嘴保护罩的孔喷出。这影响了由电弧和等离子气体所形成的等离子束。所述第二介质可以通过设置在喷嘴或喷嘴罩与喷嘴保护罩之间的气体引导部而置于旋转中。
8.喷嘴保护罩保护喷嘴和喷嘴罩免遭热量或者工件的溅出的熔化金属的影响,特别是当等离子束刺入待切割的工件时。此外,在切割时围绕等离子束获得定义的气氛。
9.为了等离子切割非合金和低合金的钢(也称为结构钢、例如按照din en 10027-1标准的s235和s355),通常使用空气、氧气或氮气或其混合物作为等离子气体。空气、氧气或氮气或其混合物通常同样也用作第二气体,其中,等离子气体和第二气体的成分和体积流量通常是不同的,但也可以是相同的。
10.为了等离子切割高合金的钢和不锈钢、例如1.4301(x5crni10-10)或1.4541(x6crniti18-10),通常使用氮气、氩气、氩气-氢气-混合物、氮气-氢气-混合物或氩气-氢气-氮气-混合物作为等离子气体。原则上也可以使用空气作为等离子气体,然而在空气中的氧气组分导致切割面氧化并且因此导致切割质量变差。氮气、氩气、氩气-氢气-混合物、
氮气-氢气-混合物或氩气-氢气-氮气-混合物通常同样也用作第二气体,其中,等离子气体和第二气体的成分和体积流量通常是不同的,但也可以是相同的。
11.在等离子切割中存在下述需求,即,以尽可能高的质量切割或切出最为不同的轮廓,例如小的内部轮廓、大的内部轮廓和外部轮廓。
12.小的轮廓具有如下周长和/或如下直径,所述周长等于或小于材料厚度的六倍,所述直径等于或小于材料厚度的两倍。大的轮廓具有如下周长和/或如下直径,所述周长为大于材料厚度的六倍,所述直径为大于材料厚度的两倍。
13.在cnc控制的牵引系统中,在数据库中至少存储有用于切割材料(材料种类和材料厚度)的基本切割参数、例如切割电流、等离子燃烧器间距(等离子燃烧器尖端与工件表面之间的间距)、切割速度、等离子气体、第二气体、电极、喷嘴。
技术实现要素:14.因此,本发明的目的在于,提供一种用于等离子切割工件的方法,利用所述方法能够以高质量切割或者说切出最为不同的轮廓、例如小的内部轮廓、大的内部轮廓和外部轮廓。
15.按照第一方面,所述目的通过一种用于等离子切割工件的方法来解决,在所述方法中使用等离子切割燃烧器,所述等离子切割燃烧器包括至少一个等离子燃烧器体、电极和喷嘴,所述等离子体切割燃烧器用于从特别是板状的、具有材料厚度的工件切割一部分,其中,所述等离子切割燃烧器中等离子束从喷嘴喷出的部位形成等离子燃烧器尖端,并且在所述方法中,借助于牵引系统沿着轮廓以切割速度v相对于工件表面顺进给方向牵引所述等离子切割燃烧器,使得所述部分的至少一个小的内部轮廓被切出,所述小的内部轮廓的周长小于或等于工件的材料厚度的六倍或者所述小的内部轮廓的直径小于或等于工件的材料厚度的两倍,以及使得所述部分的至少一个外部轮廓和/或所述部分的大的内部轮廓被切出,所述大的内部轮廓的周长大于工件的材料厚度的六倍或者所述大的内部轮廓的直径大于工件的材料厚度的两倍,其中,所述等离子燃烧器尖端在切割期间具有相对于工件表面的切割间距ds,其中,与所述部分的待切割的外部轮廓的周长的至少一个小的局部或最大的局部和/或所述部分的待切割的大的内部轮廓的周长的至少一个大的局部或最大的局部相比,所述部分的待切割的小的内部轮廓的周长的至少一个小的局部或最大的局部以在等离子燃烧器尖端与工件表面之间的不同的切割间距ds来切割。
16.按照第二方面,所述目的通过一种用于等离子切割工件的方法来解决,在所述方法中使用等离子切割燃烧器,所述等离子切割燃烧器包括至少一个等离子燃烧器体、电极、喷嘴和第二气体罩,其中,所述等离子切割燃烧器中等离子束从第二气体罩喷出的部位形成等离子燃烧器尖端,并且在所述方法中,借助于牵引系统沿着轮廓以切割速度(v)相对于工件表面顺进给方向牵引所述等离子切割燃烧器,使得所述部分的至少一个小的内部轮廓被切出,所述小的内部轮廓的周长小于或等于工件的材料厚度的六倍或所述小的内部轮廓的直径小于或等于工件的材料厚度的两倍,以及使得所述部分的至少一个外部轮廓和/或大的内部轮廓被切出,所述大的内部轮廓的周长大于工件的材料厚度的六倍或者所述大的内部轮廓的直径大于工件的材料厚度的两倍,并且所述等离子燃烧器尖端在切割期间具有相对于工件表面的切割间距ds,其中,与所述部分的待切割的外部轮廓的周长的至少一个
小的局部或最大的局部和/或所述部分的待切割的大的内部轮廓的周长的至少一个大的局部或最大的局部相比,所述部分的待切割的小的内部轮廓的周长的至少一个小的局部或最大的局部以在等离子燃烧器尖端与工件表之间的不同的切割间距ds来切割。
17.按照第三方面,所述目的通过一种用于等离子切割工件的方法来解决,在所述方法中使用等离子切割燃烧器,所述等离子切割燃烧器包括至少一个等离子燃烧器体、电极、喷嘴和第二气体罩,其中,所述等离子切割燃烧器中等离子束从第二气体罩喷出的部位形成等离子燃烧器尖端,并且在所述方法中,借助于牵引系统沿着轮廓以切割速度v相对于工件表面顺进给方向牵引所述等离子切割燃烧器并且从特别是板状的工件切割一部分,其中,最早在冲击工件表面的等离子束已经达到在待切出切下的轮廓上的如下位置时,该位置距尚要切过的切割棱边的距离处于工件材料厚度的最高50%,更优为最高25%的范围内,或者该位置距所述等离子束尚要切过的切割棱边的距离处于最高15mm,更优为最高7mm的范围内;或者该位置处冲击工件表面的等离子束接触切割棱边时,从第二气体罩流出的第二气体sg的成分和/或体积流量和/或质量流和/或压力,和/或在等离子燃烧器尖端与工件表面之间的切割间距ds发生改变。
18.按照第四方面,所述目的通过一种等离子切割工件的方法来解决,在所述方法中使用等离子切割燃烧器,所述等离子切割燃烧器包括至少一个等离子燃烧器体、电极、喷嘴和第二气体罩,其中,等离子切割燃烧器中等离子束从第二气体罩喷出的部位形成等离子燃烧器尖端,并且在所述方法中,借助于牵引系统沿着轮廓以切割速度v相对于工件表面顺进给方向牵引所述等离子切割燃烧器,并且等离子切割燃烧器从特别是板状的工件切割一部分,其中,最晚在冲击工件表面的等离子束已经达到在待切出的轮廓上的如下位置时,该位置距已经切过的切割棱边的距离502处于工件厚度的最高25%的范围内,或者该位置距已经切过的切割棱边的距离502处于最高7mm的范围内;或者在冲击工件表面的等离子束已经经过切割棱边时,从第二气体罩流出的第二气体sg的成分和/或体积流量和/或质量流和/或压力,和/或在等离子燃烧器尖端与工件表面之间的切割间距ds发生改变。
19.在按照第一方面和按照第二方面的方法中可以规定,在切割所述部分的小的内部轮廓时的切割间距ds小于在切割所述部分的外部轮廓和/或所述部分的大的内部轮廓时的切割间距ds。
20.特别地,在此可以规定,在切割所述小的内部轮廓时的切割间距ds为在切割所述部分的外部轮廓和/或所述部分的大的内部轮廓时的切割间距ds的40%至80%之间。
21.按照另一种特别的实施形式,在切割所述部分的小的内部轮廓时相对于工件表面顺进给方向牵引等离子切割燃烧器的切割速度v小于在切割所述部分的外部轮廓和/或切割所述部分的大的内部轮廓时的切割速度v。
22.特别地,在此可以规定,在切割所述部分的小的内部轮廓时相对于工件表面牵引等离子切割燃烧器的切割速度为在切割所述部分的外部轮廓和/或切割所述部分的大的内部轮廓时的切割速度v的20%至80%之间,优选40%至80%之间。
23.有利地,首先切割一个所述小的内部轮廓/多个所述小的内部轮廓,接着切割一个所述大的内部轮廓/多个所述大的内部轮廓,并且然后切割所述部分的一个所述外部轮廓/多个所述外部轮廓。
24.在按照第三方面和按照第四方面的方法中可以规定,所述切割棱边通过切割同一
个轮廓形成。
25.有利地,使用空气、氧气、氮气、氩气、氢气、甲烷气或氦气或其混合物作为第二气体。
26.特别地,在此可以规定,所述混合物由氧气和/或氮气和/或空气和/或氩气和/或氦气组成或者由氩气和/或氮气和/或氢气和/或甲烷气和/或氦气组成。
27.按照一种特别的实施形式,从第二气体罩流出的第二气体sg的成分和/或体积流量和/或质量流和/或压力通过:通入氧化性的气体或气体混合物和/或还原性的气体或气体混合物;和/或提高氧化性的气体或气体混合物和/或还原性的气体或气体混合物的体积流量;和/或提高氧化性的气体或气体混合物和/或还原性的气体或气体混合物的质量流;和/或提高氧化性的气体或气体混合物和/或还原性的气体或气体混合物的压力来实现。
28.特别地,在此可以规定,改变所述第二气体的成分,使得在所述第二气体中氧化性的气体或气体混合物和/或还原性的气体或气体混合物的占比的提高为至少10vol.%。
29.备选地,可以规定,在所述第二气体中氧化性的气体或气体混合物和/或还原性的气体或气体混合物的体积流量、质量流或压力的提高为至少10%。
30.有利地,所述氧化性的气体或气体混合物包含氧气和/或空气。
31.特别地,在此可以规定,所述氧化性的气体是氧气。
32.此外可以规定,所述还原性的气体或气体混合物包含氢气和/或甲烷。
33.特别地,在此可以规定,所述还原性的气体是氢气。
34.按照一种特别的实施形式,从第二气体罩流出的第二气体sg的成分和/或体积流量和/或质量流和/或压力通过:切断氮气、氩气、空气、氦气或混合物;和/或降低氮气、氩气、空气、氦气或混合物的体积流量;和/或降低氮气、氩气、空气、氦气或混合物的质量流;和/或降低氮气、氩气、空气、氦气或混合物的压力来实现。
35.特别地,在此可以规定,改变所述第二气体的成分,使得在第二气体中气体或气体混合物的占比的降低为至少10vol.%。
36.备选地,可以规定,在第二气体中气体或气体混合物的体积流量、质量流或压力的降低为至少10%。
37.以适当方式,降低等离子燃烧器尖端与工件表面之间的切割间距ds。
38.有利地,所述切割间距ds降低了至少25%和/或至少1mm。
39.按照另一种特别的实施形式可以规定,最早在冲击工件表面的等离子束已经达到在待切出的轮廓上的如下位置时,该位置距尚要切过的切割棱边的距离处于工件的材料厚度的最高50%,更优为最高25%的范围内;或者该位置距尚要切过的切割棱边的距离处于最高15mm,更优为最高7mm的范围内;或者在冲击工件表面的等离子束接触切割棱边时,相对于工件表面牵引等离子切割燃烧器的切割速度v发生改变。
40.有利地,最晚在冲击到工件表面的等离子束已经达到在待切出的轮廓上的如下位置时,该位置距已经切过的切割棱边的距离处于工件厚度的最高25%的范围内;或者该位置距已经切过的切割棱边的距离处于最高7mm的范围内;或者在冲击工件表面的等离子束已经过切割棱边时,相对于工件表面牵引等离子切割燃烧器的切割速度v发生改变。
41.特别地,可以规定,所述切割速度v提高。
42.最后,在此可以特别地规定,所述切割速度v提高了至少10%。本发明根据试验以
下述认识为基础:
43.如果以相同的参数切割不同的轮廓类型,如小的内部轮廓、大的内部轮廓和外部轮廓,则得到不同的切割质量。特别是,小的内部轮廓的切割质量变差并且在此特别是按照din iso 9013标准的垂直公差和倾斜公差变差,亦即切割面不再与工件表面近乎垂构成直角。令人惊奇地发现,在切割小的内部轮廓时,通过改变,特别是降低等离子燃烧器间距(切割间距)达到相对于外部轮廓或大的内部轮廓而言切割质量的明显改善。特别地,垂直公差和倾斜公差改善。如果为此还降低用于切割小的内部轮廓的切割速度,则达到进一步的改善。因为内部轮廓小,所以这对总切割时间仅有微弱影响。小的轮廓的切割速度可以为外部轮廓或大的内部轮廓的切割速度的20%至80%,更优为40%至80%。
44.使用不同的等离子燃烧器间距(切割间距),特别是对大的内部轮廓和外部轮廓使用更大的等离子燃烧器间距的另一项优点在于,切割过程的易干扰性比在使用小的切割间距时更低。在此,工件表面的杂质(例如由于等离子燃烧器尖端可能“撞到”飞溅的熔渣所造成的杂质)的干扰更少。按照这种方式和方法,在工件上达到内部轮廓的高切割质量和对于外部轮廓和大的内部轮廓的高生产率、高切割质量和高过程可靠性。不需要更换等离子燃烧器的磨损件。在所述不同的轮廓之间同样不需要更换等离子气体和第二气体。有利的是,可以仅以不同的等离子燃烧器间距(切割间距)和/或不同的切割速度来切割,因为可以非常快地进行这种更换。为此,仅需要用于传输电子信号的时间(例如《5ms),而不需要例如在更换磨损件时或者在更换气体时0.1秒至5秒的等待时间。与此关联的气体损耗和气体消耗也得以减少。
45.在牵引系统或等离子切割设备的控制部中,这样例如可以存储用于针对不同的轮廓(小的内部轮廓、大的内部轮廓、外部轮廓)切割同一材料,即用于相同的材料类型和材料厚度的不同的数据集,所述数据集随即配设于相应的切割任务。同样可能的是,对于小的轮廓规定等离子燃烧器间距(切割间距)和/或切割速度的固定的或可变的减少。
46.此外,至少在一种特别的实施形式中能实现以更好的质量切割还要更小的内部轮廓。这是些周长等于或小于材料厚度的三倍(或者所述轮廓的直径小于材料厚度本身)的轮廓。为此,再次减少切割速度,以便即使在这些轮廓中也达到高切割质量。减少的切割速度可以为大的轮廓的切割速度的40%至80%。
47.此外,切口末端对于内部轮廓的质量,但也对于外部轮廓的质量是特别关键的。特别是当等离子束达到如下点,在该点处等离子束又进入到已经通过同一切割产生的切割缝中并且切过该缝的工件棱边。在此,工件棱边可以被“跳过”,废料部分可以从所述轮廓“落下”并且所述等离子束可以接续在内部轮廓的已经存在的切割面上。
48.在跳过所述缝时通常留下干扰性的凸出部。在等离子束接续在已经存在的切割面上时发生“冲蚀”,所述冲蚀同样负面地影响切割质量。尝试通过降低切割速度来减少凸出部。然而这又增强了冲蚀。
49.已知的是,在各个切割过程之间,改变第二气体的成分,以便首先切割小的孔并且然后切割大的轮廓。在此,在不切割的时间段内进行切换并且具有为此需要时间的缺点。
50.在按照权利要求8所述的方法中应清楚的是,关键的是从第二气体罩的孔中喷出时或者在冲击等离子束时第二气体的成分,而在何处通过在等离子燃烧器杆中或上游的阀进行成分改变并非关键所在。
附图说明
51.本发明的其他特征和优点由所附的权利要求书和下文中的描述得出,其中借助示意性的附图详细描述本发明的多个实施例。图中:
52.图1示出按照现有技术的用于等离子切割的布置结构的示意图;
53.图2示出按照现有技术的用于等离子切割的另一种布置结构的示意图;
54.图3示出应从工件切出的部分的俯视图;
55.图4示出图3的细节图,在所述细节图中绘出用于切出内部轮廓的切割行程;
56.图4a示出在图3中所示出的工件之上的等离子切割燃烧器在点火时的侧视图;
57.图4b示出类似于图4a的侧视图,但其中示出的是点火之后正在切割之时的等离子切割燃烧器;
58.图5示出类似于图3的细节图,但其中绘出的是用于切出另外的内部轮廓的切割行程;
59.图6示出类似于图3的细节图,但其中绘出的是用于切出另外的内部轮廓的切割行程;
60.图7示出类似于图3的细节图,但其中绘出的是用于切出另外的内部轮廓的切割行程;
61.图8示出图3切出在图5至7中所示出的内部轮廓之后的部分的俯视图,在该俯视图中绘出用于切出外部轮廓的切割行程;
62.图9示出图5的细节图,以更准确地示出内部轮廓的切割过程的结束;
63.图9a示出类似于图9的另外的细节图,但在切割过程的结束的稍晚的阶段中;
64.图9b示出图9a中a-a的剖视图;
65.图9c示出类似于图9a的另外的细节图,但在切割过程的结束的还要更晚的阶段中;
66.图9d示出图9c中b-b的剖视图;
67.图9e示出在切割时在工件的切割面上产生的沟槽及其通过等离子束偏转而引起的尾迹;
68.图10示出应从工件切出的部分的俯视图,所述工件由与图3中示出的工件所不同的材料制成;
69.图11示出图10的细节图,在所述细节图中绘出用于切出内部轮廓的切割行程;
70.图11a示出在图11中所示出的工件之上的等离子切割燃烧器在点火时的侧视图;
71.图11b示出类似于图11a的侧视图,但其中示出的是点火之后正在切割之时的等离子切割燃烧器;
72.图12示出类似于图10的细节图,但其中绘出的是用于切出另外的内部轮廓的切割行程;
73.图13示出类似于图10的细节图,但其中绘出的是用于切出另外的内部轮廓的切割行程;
74.图14示出类似于图10的细节图,但其中绘出的是用于切出另外的内部轮廓的切割行程;
75.图15示出图10切出图12至14中所示出的内部轮廓之后的部分的俯视图,在所述俯
视图中绘出用于切出外部轮廓的切割行程;
76.图16示出图12的细节图,以更准确地示出内部轮廓的切割过程的结束;
77.图16a示出类似于图16的另外的细节图,但在切割过程的结束的稍晚的阶段中;
78.图16b示出图16a中a-a的剖视图;
79.图16c示出类似于图16a的另外的细节图,但在切割过程的结束的还要更晚的阶段中;
80.图16d示出图16c中b-b的剖视图;以及
81.图17示出按照本发明的一种特别的实施形式的用于等离子切割的布置结构的示意图,所述布置结构用于实施按照本发明的一种特别的实施形式的用于等离子切割工件的方法。
具体实施方式
82.常见的用于等离子切割的布置结构在图1和2中示意性地示出。在此,切割电流从等离子切割设备1的电流源1.1经由电导线5.1流至等离子切割燃烧器2,经由等离子切割燃烧器2的电极2.1借助于由喷嘴2.2和喷嘴孔2.2.1所收束的等离子束3流至工件4并且然后经由电导线5.3流回至电流源1.1。等离子切割燃烧器2的供气经由管线5.4和5.5从供气部6至等离子切割燃烧器2进行。高压点火器1.3、先导电阻1.2、电流源1.1和开关触点1.4及其控制部位于等离子切割设备1中。用于控制气体的阀同样可以存在。但在此未示出这些阀。
83.等离子切割燃烧器2基本上包括具有射束产生系统的等离子燃烧器头和等离子燃烧器体2.7,所述射束产生系统包括电极2.1、喷嘴2.2、用于等离子气体pg的气体供应部2.3,所述等离子燃烧器体实现介质(气体、冷却水和电流)的供应并且容纳所述射束产生系统。等离子切割燃烧器2的电极2.1是不熔化的电极2.1,所述电极基本上由耐高温材料、例如钨、锆或铪制成并且由此具有非常长的寿命。通常,电极2.1由两个相互连接的部分组成:由良好导电和导热的材料(例如铜、银、其合金)制成的电极座2.1.1和具有低的电子逸出功(铪、锆、钨)的熔点高的发射嵌件2.1.2。喷嘴2.2通常由铜制成并且将等离子束3收束。在电极2.1与喷嘴2.2之间可以设置用于等离子气体pg的气体引导部2.6,所述气体引导部将等离子气体置于旋转中。在该实施形式中,等离子切割燃烧器2中等离子束3从喷嘴2.2喷出的部位被称为等离子燃烧器尖端2.8。等离子燃烧器尖端2.8与工件表面4.1之间的间距以d标记。该间距在该示例中相当于喷嘴2.2与工件表面4.1之间的间距。类似的情况适用于再下面所提到的切割间距ds或者说点火间距dz。
84.在图2中围绕等离子切割燃烧器2的喷嘴2.2附加地安置有第二气体罩2.4(喷嘴保护罩),以用于供应第二介质,例如第二气体sg。包括第二气体罩2.4与第二气体sg的组合保护喷嘴2.2免于在等离子束3刺入到工件4中时损坏并且围绕等离子束3获得定义的气氛。气体引导部2.9位于喷嘴2.2与第二气体罩4之间,所述第二气体罩可以将第二气体置于旋转中。在该实施形式中,等离子切割燃烧器2中等离子束3从第二气体罩2.4喷出的部位被称为等离子燃烧器尖端2.8。等离子燃烧器尖端2.8与工件表面4.1之间的间距同样以d标记。该间距d在该示例中相当于第二气体罩2.4与工件表面4.1之间的间距。类似的情况适用于再下面所提到的切割间距ds或者说点火间距dz。
85.对于切割过程,首先点燃先导电弧,所述先导电弧在电极2.1与喷嘴2.2之间以低
的电流(例如10a-30a)并因此低功率燃起,例如借助于通过高压点火器1.3所产生的高电压。先导电弧的电流(先导电流)通过电导线5.2由喷嘴2.2经由开关触点1.4和电阻1.2流至电流源1.1并且通过先导电阻(电阻)1.2来限定。该能量低的先导电弧通过部分的电离准备用于切割电弧的、在等离子切割燃烧器2与工件4之间的区段。如果先导电弧接触工件4,则通过由先导电阻1.2所产生的喷嘴2.2与工件4之间的电势差来产生切割电弧。该切割电弧于是在电极2.1与工件4之间以通常更大的电流(例如20a至900a)和因此也以更大的功率燃起。开关触点1.4断开并且喷嘴2.2相对于电流源1.1切换为无电势。这种驱动方式也被称为直接的驱动方式。在此,工件4受到等离子束3的热作用、动力学作用和电气作用。由此,所述方法非常高效并且可以在600a的切割电流下以0.2m/min的切割速度切割大厚度(例如180mm)的金属。
86.为此利用牵引系统使等离子切割燃烧器2相对于工件4或者说其表面4.1运动。所述牵引系统例如可以是机器人或cnc控制的牵引机器。牵引系统的控制部(未示出)与按照图1或2的布置结构通信。
87.在最简单的情况下,其使得等离子切割燃烧器2的运行开始和结束。然而,按照现有技术可以交换例如关于运行状态和数据的多个信号和信息。
88.在等离子切割中可以达到高的切割质量。这方面的标准例如是按照din iso 9013的垂直公差和倾斜公差较低。在遵循最优切割参数的情况下可以达到光滑的切割面和无毛刺的棱边,所述切割参数主要包括切割电流、切割速度、等离子切割燃烧器与工件之间的间距以及气体压力。
89.对于切口的质量而言,所述电极2.1,特别是其发射嵌件2.1.2和喷嘴2.2,特别是其喷嘴孔2.2.1以及第二气体罩2.4(如果存在的话)和特别地其孔处于共同的轴线上也是重要的,以便沿等离子切割燃烧器2相对于工件的任意运动方向在不同的切割棱边上保持相同的或至少仅微弱偏差的垂直公差和倾斜公差。
90.在等离子切割中,按照din iso 9013的品质2至4的垂直公差和倾斜公差现今是现有技术。这相当于最高3
°
的角度。
91.图3示例性地示出应从工件4切出的部分400的俯视图。待切出的部分400示例性地具有四个内部轮廓410、430、450和470以及示例性地具有一个外部轮廓490。工件在该示例中由结构钢制成,亦即由非合金或低合金的钢,例如按照din en 10 027-1的s235或s355制成。工件4的材料厚度4.3在此示例性地为10mm。示例性地使用氧气作为等离子气体,而示例性地使用空气作为第二气体。也存在如下可能性,例如使用包括空气和氧气的混合物作为第二气体。在特定的材料厚度区域中,这会产生更光滑、更垂直的切割棱边。
92.所述内部轮廓410示例性地是大的内部轮廓,所述内部轮廓430、450和470示例性地是小的内部轮廓。如果轮廓的周长等于或小于工件厚度的六倍,内部轮廓则为小的内部轮廓。在该情况下,因为工件厚度为10mm,长度为60mm。
93.圆形的内部轮廓430具有例如10mm的直径d430,周长u430例如为约31mm。正方形的内部轮廓450示例性地具有各10mm的边长s450并且因此具有40mm的周长u430。内部轮廓470示例性地是等边三角形并且例如具有各10mm的边长s470并且因此具有30mm的周长u470。
94.内部轮廓410在该示例中是正方形的并且具有例如各50mm的边长s410并因此具有200mm的周长u410。
95.外部轮廓示例性地是具有例如100mm的边长s490的正方形并且具有400mm的周长u490。从工件4可以切出多个部分400,但也可以切出最为不同的其他部分。
96.在该示例中,首先切出部分400的小的内部轮廓430、450、470,然后切出大的内部轮廓410并且最后切出外部轮廓490。这一点示例性地在针对内部轮廓430的图4、4a和4b中、在针对内部轮廓450的图5中、在针对内部轮廓470的图6中、在针对内部轮廓410的图7中和在针对外部轮廓490的图8中示出。
97.如在图4a中所示,为此等离子切割燃烧器2的等离子燃烧器尖端2.8在工件表面4.1上方间隔开定义的间距(点火间距dz,在此示例性地为4mm)地定位在起点411或者说431或者说451或者说471上。切割过程通过发送到等离子切割设备1上的牵引系统的接通信号(ein-signal)开始并且切割电弧或者说等离子束3如在图1和图2下所描述的那样启动。间隔开点火间距dz地,所述待切割的工件4被等离子束3刺穿(刺入)并且在定义的时间之后定位到不同的间距,(如示例性地在图4b中示出)在工件表面4.1上定位到切割间距ds,并且顺进给方向10以相对于工件表面4.1的切割速度v实施切割。切割间距ds在此小于点火间距dz。如在图4、5、6和7中所示出的,产生切割缝414或者说434或者说454或者说474。刺入在废料部分上进行,并且等离子切割燃烧器2被牵引经过短的区段,即所谓的刺入凹槽(einstechfahne)412或者说432或者说452或者说472或者说492,以获得最终要切出的轮廓,所述刺入凹槽是废料部分上的切割缝。等离子束3根据其电流和喷嘴孔2.2.1的直径(该等离子束穿过所述直径喷出)具有如下直径,所述直径导致切割缝414或者说434或者说454或者说474和494具有特定的缝宽度b414或者说b434或者说b454或者说b474和b494。出于该原因,等离子切割燃烧器2在切割时以平行于工件表面4.1延伸的、在穿过喷嘴2.2的喷嘴孔2.2.1的中点延伸的纵向轴线l与所希望的轮廓之间的间距(所谓的缝错位或缝补偿)来牵引。通常,最终可以实现最佳的切割质量的切割间距ds最迟随着达到要切出的轮廓410、430、450、470、490而达到。所述轮廓基本上随着切过切割棱边415或者说435或者说455或者说475或者说495而切割,所述切割棱边已通过刺入凹槽412或者说432或者说452或者说472或者说492的切割缝而形成。轮廓最终通过切割棱边413、433、453、473、493形成。
98.小的内部轮廓430、450和470在此示例性地以100a的电流、示例性地为1.5mm的切割间距ds和示例性地为1.4m/min的切割速度v来切割。大的内部轮廓410和外部轮廓490示例性地以100a的电流、3mm的切割间距ds和2.5m/min的切割速度v来切割。小的内部轮廓430、450和470在此以比大的内部轮廓410和外部轮廓490更小的切割间距ds和更小的切割速度v切割。小的内部轮廓和大的内部轮廓的环绕方向(进给方向10)在该示例中相同,外部轮廓490的环绕方向在该示例中与此相反,如从图4至图8中也可看出的那样。
99.图9和后续附图示出工件4的视图。在此,可以更准确地看见内部轮廓450的切割过程的结束。以下描述也适用于不同的内部轮廓410、430和470以及外部轮廓490。等离子切割燃烧器2的等离子束3已切割了切割缝454的局部,并且相同地越过由刺入凹槽452的切割缝所形成的切割棱边455切过。在大多数情况下,等离子束3与其进给方向10相反地后倾(nachlaufen),如在图4b中所示。其因此被偏转。等离子束的轻微偏转导致毛刺少或无毛刺的切口并且同时导致高的生产率。在图9e中示出在切割时在切割面4.2上产生的沟槽b,所述沟槽由于等离子束的偏转而后倾。切口沟槽的两个点沿切割方向的最大距离按照din iso 9013被称为沟槽尾迹n。
100.已经描述过下述问题,所述问题可能在内部轮廓的末端处切割时出现,即在切过切割棱边455时产生或留下的凸出部456,如在图9a中所示。该凸出部由于在切过刺入凹槽452的切割棱边455时顺进给方向10突然略过待切割的材料而产生。等离子束3可以说顺进给方向10在切割棱边上沿着切割缝的切割棱边跳过并且尾迹突然变小。这样产生凸出部456,所述凸出部在工件4的下侧上,亦即在等离子束3从工件4的喷出侧上通常比在等离子束3进入到工件中的工件表面4.1上还更明显地突出。在图9b中,这一点在凸出部456的区域中穿过切割缝454的剖切面a-a中可看出。
101.尝试通过降低进给速度v来抑制该效应。但这会导致在已经存在的切割棱边或者说切割面中产生特别是朝向工件4的下面的冲蚀部457,如在图9c中所示出的。图9d示出在冲蚀部457的区域中穿过切割缝454的剖切面b-b。
102.相同的问题也在切割外轮廓490的情况下在切过由刺入凹槽492所形成的切割棱边495时出现。
103.如已经在图3下所描述过的,在此示例性地切割结构钢。使用氧气作为等离子气体,而使用空气作为第二气体。通过在等离子束3切过切割棱边455时向第二气体的空气添加氧气来减少凸出部456的形成。因为切割速度v不必减少,所以也减少或甚至阻止了冲蚀部457的形成。如果提高第二气体罩喷出口处第二气体中的氧气占比以及切割速度,则还进一步改善切割面。切割速度v优选只在第二气体罩处喷出的第二气体的氧气占比升高时提高。氧气占比的升高应优选为在切割轮廓的大多数时间期间占体积流量的至少10%或者占总第二气体的10vol.%。这例如可以通过提高在第二气体中的氧气的压力和/或体积流量和/或质量流来达到。同样存在如下可能性,降低其他气体,例如空气或氮气的占比,例如通过减少压力和/或体积流量和/或质量流并且因此提高氧气占比。在切过切割棱边455并达到已经切割过的切割缝454之后,在越过至少一部分刺入凹槽或者整个刺入凹槽之后,首先减少切割电流并且最终切断切割电流。
104.在图9中示例性地示出在尚要切过的切割棱边455之前的或者说距尚要切过的切割棱边的距离500,在所述距离中可以改变从第二气体罩2.4流出的第二气体的成分、体积流量和/或压力,和/或改变等离子燃烧器尖端与工件表面之间的切割间距ds。该切割间距在此例如是例如10mm并且因此在该示例中相当于工件厚度。
105.在图9c中示例性地示出在已经切过的切割棱边455之后或者说距已经切过的切割棱边的距离502,在所述距离中可以改变从第二气体罩流出的第二气体的成分、体积流量和/或压力,和/或改变等离子燃烧器尖端与工件表面之间的间距。所述距离例如为7mm。
106.也存在如下可能性,使用氮气作为第二气体。这里也如在上面提到的条件下将氧气添加给第二气体并且氧气占比因此提高。
107.在第二气体中的氧气占比也可以达到占体积流量或质量流的100%,优选最高占80%。
108.在切割高合金的钢,例如1.4301(x5crni10-10)或1.4541(x6crniti18-10)时,可以使用氮气、氩气、氩气-氢气-混合物、氮气-氢气-混合物或氩气-氢气-氮气-混合物例如作为等离子气体。同样地,通常使用氮气、氩气、氩气-氢气-混合物、氮气-氢气-混合物或氩气-氢气-氮气-混合物作为第二气体。
109.图10示例性地示出应从工件4切出的部分400的俯视图。待切出的部分400具有四
个内部轮廓410、430、450和470以及一个外部轮廓490。所述工件由结构钢制成,亦即由非合金或低合金的钢,例如1.4301(x5crni10-10)或1.4541(x6crniti18-10)1制成。工件4的厚度在此示例性地为10mm。示例性地使用氩气-氢气-混合物作为等离子气体,而示例性地使用氮气作为第二气体。此外也存在如下可能性,即使用包括氮气和氢气的混合物作为第二气体。在特定的材料厚度区域中,这导致更光滑、更垂直的切割棱边。
110.内部轮廓410在该示例中是大的内部轮廓。内部轮廓430、450和470示例性地是小的内部轮廓。如果轮廓的周长等于或小于工件4的厚度4.3的六倍,内部轮廓则是小的内部轮廓。在该情况下,因为工件厚度为10mm,长度为60mm。
111.圆形的内部轮廓430例如具有15mm的直径d430。周长u430例如为约47mm。内部轮廓450示例性地是正方形并且具有例如各14mm的边长s450并且因此具有56mm的周长u430。内部轮廓470例如是等边三角形并且具有例如各15mm的边长s470并且因此具有45mm的周长u470。
112.内部轮廓410示例性地是正方形的并且具有例如各50mm的边长s410并且因此具有200mm的周长u410。
113.外部轮廓490在该示例中是正方形,所述正方形具有例如100mm的边长s490并且因此具有400mm的周长。从工件4就可以切出多个部分400,但也可以切出最为不同的其他部分。
114.在该示例中,首先切出部分400的内部轮廓430、450、470,然后切出大的内部轮廓410并且最终切出外部轮廓490。这一点示例性地在针对内部轮廓430的图11、11a和11b中、在针对内部轮廓450的图12中、在针对内部轮廓470的图13中、在针对内部轮廓410的图14并且在针对外部轮廓490的图15中示出。
115.如在图11a中所示,为此等离子切割燃烧器2的等离子燃烧器尖端2.8在工件表面4.1上方间隔开所定义的间距(点火间距dz,在此示例性地为5mm)地定位在起点411或者说431或者说451或者说471或者说491上。切割过程通过发送到等离子切割设备1上的牵引系统的接通信号(ein-signal)开始并且切割电弧或等离子束3如在图1和图2下所描述的那样启动。间隔开点火间距dz地,所述待切割的工件4被等离子束3刺穿(刺入)并且在所定义的时间之后定位到不同的间距,(如示例性地在图11b中示出)在工件表面4.1之上定位到切割间距ds,并且顺进给方向10以相对于工件表面4.1的切割速度v实施切割。切割间距ds在此小于点火间距dz。如在图11、12、13和14中所示出的,产生切割缝414或者说434或者说454或者说474或者说494。刺入在废料部分上进行,并且等离子切割燃烧器2被牵引经过短的区段,即所谓的刺入凹槽412或者说432或者说452或者说472或者说492,以获得最终要切出的轮廓,所述刺入凹槽废料部分上的切割缝。等离子束3根据其电流和喷嘴孔2.2.1的直径(该等离子束穿过所述直径喷出)具有如下直径,所述直径导致切割缝414或者说434或者说454或者说474或者说494具有特定的缝宽度b414或者说b434或者说b454或者说b474或者说b494。出于该原因,等离子切割燃烧器2在切割时以平行于工件表面4.1延伸的、在穿过喷嘴2.2的喷嘴孔2.2.1的中点延伸的纵向轴线l与所希望的轮廓之间的间距(所谓的缝错位或缝补偿)来牵引。通常,最终可以实现最佳的切割质量的切割间距ds最迟随着达到待切出的轮廓410或者说430或者说450或者说470或者说490而达到。所述轮廓基本上随着切过切割棱边415或435或455或475或495而切割,所述切割棱边已通过刺入凹槽412或者说432或者
说452或者说472或者说492的切割缝而形成。轮廓最终通过切割棱边413或者说433或者说453或者说473或者说493形成。
116.小的内部轮廓430、450和470在此示例性地以130a的电流、示例性地为2.0mm的切割间距ds和示例性地为1.0m/min的切割速度v来切割。大的内部轮廓410和外部轮廓490示例性地以130a的电流、3mm的切割间距ds和示意性地为1.4m/min的切割速度v来切割。小的内部轮廓430、450和470在此以比大的内部轮廓410和外部轮廓490更小的切割间距ds和更小的切割速度v切割。
117.小的内部轮廓和大的内部轮廓的环绕方向(进给方向10)在该示例中相同,外部轮廓490的环绕方向在该示例中与此相反,如从图11至图15中也可看出的那样。
118.图16和后续附图示出工件4的视图。在此,可以更准确地看见内部轮廓450的切割过程的结束。以下描述也适用于不同的内部轮廓410、430和470。等离子切割燃烧器2的等离子束3已切割了切割缝454的局部,并且相同地切过由刺入凹槽452的切割缝所形成的切割棱边455。在大多数情况下,等离子束3与其进给方向10相反地后倾,如在图9中所示,其因此被偏转。等离子束的轻微偏转导致少毛刺或无毛刺的切口并且同时导致高的生产率。在图9a中示出在切割时在切割面4.2上产生的沟槽b,所述沟槽由于等离子束的偏转而后倾。切口沟槽的两个点沿切割方向的最大距离按照din iso 9013被称为沟槽尾迹n。
119.已经描述过下述问题,所述问题可能在内部轮廓的末端处切割时出现,即在切过切割棱边455时产生或留下的凸出部456,如在图16a中所示。该凸出部由于在切过刺入凹槽452的切割棱边455时顺进给方向10突然略过待切割的材料而产生。等离子束3可以说沿进给方向10在切割缝的切割棱边上沿着切割缝的切割棱边跳过并且尾迹突然变小。这样产生凸出部456,所述凸出部在工件4的下侧上,亦即在等离子束3从工件4的喷出侧上通常比在等离子束3进入到工件中的工件表面4.1上还更明显地突出。在图16b中,这一点在凸出部456的区域中穿过切割缝454的剖切面a-a中可看出。
120.尝试通过降低进给速度v来抵制该效果,但这会导致在已经存在的切割棱边或者说切割面中产生特别是朝向工件4的下面的冲蚀部457,如在图15c中所示出的。图16d示出在冲蚀部457的区域中穿过切割缝454的剖切面b-b。
121.如已经在图10下所描述过的,在此示例性地切割高合金的钢材,使用氩气-氢气-混合物作为等离子气体,而使用氮气作为第二气体。通过对在等离子束3切过切割棱边455时向第二气体的氮气添加氢气来减少凸出部456的形成。因为切割速度v不必减少,所以也减少或甚至阻止了冲蚀部457的形成。如果提高第二气体罩喷出口处第二气体中的氢气占比以及切割速度,则还进一步改善切割面。切割速度优选只在第二气体罩处喷出的第二气体的氢气占比升高时提高。氢气占比的升高应优选为在切割轮廓的大多数时间期间占体积流量的至少10%或者占总第二气体的10vol.%。这例如可以通过提高在第二气体中的氢气的压力和/或体积流量和/或质量流来达到亦或通过在第二气体中通入氢气来达到。同样存在如下可能性,降低其他气体,例如氮气的占比,例如通过减少压力和/或体积流量和/或质量流亦或断开并且因此提高氢气占比。在切过切割棱边455并达到已经切割过的切割缝454之后,在越过至少一部分刺入凹槽或者整个刺入凹槽之后,首先减少切割电流并且最终切断切割电流。
122.在图16中示例性地示出在尚要切过的切割棱边455之前的或者说距尚要切过的切
割棱边的距离500,在所述距离中可以改变从第二气体罩2.4流出的第二气体的成分、体积流量和/或压力,和/或改变在等离子燃烧器尖端与工件表面之间的切割间距ds。该切割间距在此例如是例如10mm并且因此在该示例中相当于工件厚度。
123.在图16c中示例性地示出在已经切过的切割棱边455之后或者说距已经切过的切割棱边的距离502,在所述距离中可以改变从第二气体罩2.4流出的第二气体的成分、体积流量和/或压力,和/或改变在等离子燃烧器尖端与工件表面之间的切割间距。所述距离例如为7mm。
124.图17示出按照本发明的一种特别的实施形式的布置结构,利用所述布置结构可以实现按照本发明的一种特别的实施形式的方法并且所述布置结构主要基于图1和图2。不过,经由管线5.5和5.6向等离子燃烧器2供应有第一种第二气体sg1和第二种第二气体sg2。磁阀y1和y2位于等离子燃烧器体2.7中并且开关第二气体sg1和sg2。第二气体1,例如氮气或空气在切割期间通过打开磁阀y1向等离子束3供应。在切过通过有刺入凹槽412或者说432或者说352或者说472或者说492形成的切割棱边415或者说435或者说455或者说475或者说495时,或者附加地打开用于第二气体sg2,例如氧气的磁阀y2并且与第二气体1混合。也存在如下可能性,即,通过关闭磁阀y1来切断第二气体1并且仅让第二气体2,例如氧气作为第二气体流向等离子束。
125.在牵引系统的控制部中根据待切出的轮廓的走向存储改变第二气体成分的时刻,并且将其作为信号发给等离子切割设备,所述等离子切割设备随即进行各阀的切换。
126.在切过由刺入凹槽形成的切割缝时用于切割和切口末端的第二气体的不同的成分存储在数据库中。
127.在一些情况下已证明,如果等离子燃烧器尖端2.8相对于工件表面4.1的切割间距ds在切割棱边415或者说435或者说455或者说475或者说495的附近降低,所描述的留下的凸出部546的效应或留下的冲蚀部457的效应会降低。通过将该间距降低例如1mm减少了凸出部。
128.在牵引系统的控制部中根据待切出的轮廓的走向存储改变切割间距ds的时刻并且将其发给牵引机器的间隔调节部或者说等离子切割燃烧器。
129.在此,在数据库中存储用于在切过由刺入凹槽所形成的切割缝时用于切割和切口末端的切割间距ds的值。
130.本发明在上述说明书中、在附图中以及在权利要求书中所公开的特征对于本发明在其不同的实施形式中的实现,既可以单独也可以以任意的组合,是至关重要的。
131.附图标记列表
132.1等离子切割设备
133.1.1电流源
134.1.2先导电阻
135.1.3高压点火器
136.1.4开关触点
137.2等离子切割燃烧器
138.2.1电极
139.2.1.1电极座
140.2.1.2发射嵌件
141.2.2喷嘴
142.2.2.1喷嘴孔
143.2.3等离子气体的气体供应部
144.2.4第二气体罩
145.2.5第二气体的第二气体供应部
146.2.5.1第二气体1的第二气体供应部
147.2.5.2第二气体2的第二气体供应部
148.2.6用于等离子气体的气体引导部
149.2.7等离子燃烧器体
150.2.8等离子燃烧器尖端
151.2.9用于第二气体的气体引导部
152.3等离子束
153.4工件
154.4.1工件表面
155.4.2切割面
156.4.3材料厚度
157.5输入管线
158.5.1切割电流的电导线
159.5.2先导电流的电导线
160.5.3工件-等离子切割设备的电导线
161.5.4等离子气体的管线
162.5.5第二气体1的管线
163.5.6第二气体2的管线
164.6供气部
165.10等离子切割燃烧器的进给方向
166.400待切出的部分
167.410大的内部轮廓
168.411起点、刺入点
169.412刺入凹槽
170.413切割棱边
171.414切割缝
172.415刺入凹槽的切割棱边
173.430小的内部轮廓
174.431起点、刺入点
175.432刺入凹槽
176.433切割棱边
177.434切割缝
178.435刺入凹槽的切割棱边
179.450小的内部轮廓
180.451起点、刺入点
181.452刺入凹槽
182.453切割棱边
183.454切割缝
184.455刺入凹槽的切割棱边
185.456凸出部
186.457冲蚀部
187.470小的内部轮廓
188.471起点、刺入点
189.472刺入凹槽
190.473切割棱边
191.474切割缝
192.475刺入凹槽的切割棱边
193.490外部轮廓
194.492刺入凹槽
195.493切割棱边
196.495刺入凹槽的切割棱边
197.500距尚要切过的切割棱边的距离
198.502距已经切过的切割棱边的距离
199.b沟槽
200.b414缝宽度
201.b434缝宽度
202.b454缝宽度
203.b474缝宽度
204.b494缝宽度
205.d430小的内部轮廓的直径
206.d等离子燃烧器尖端-工件表面的间距
207.ds等离子燃烧器尖端-工件表面的切割间距
208.dz等离子燃烧器尖端工件表面的点火间距
209.l纵向轴线
210.n沟槽尾迹
211.pg等离子气体
212.sg第二气体
213.sg1第二气体1
214.sg2第二气体2
215.s410大的内部轮廓的边长
216.s450小的内部轮廓的边长
217.s470小的内部轮廓的边长
218.s490外部轮廓的边长
219.u410大的内部轮廓的周长
220.u440小的内部轮廓的周长
221.u450小的内部轮廓的周长
222.u470小的内部轮廓的周长
223.u490外部轮廓的周长
224.v切割速度
225.y1第二气体1的磁阀
226.y2第二气体2的磁阀。