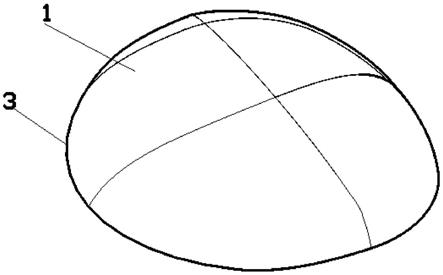
1.本技术涉及飞机制造领域的一种钣金制造技术,具体是一种适用于提升硬铝合金钣金零件综合力学性能的制备方法。
背景技术:2.硬铝合金是航空飞行器钣金零件使用最广泛的材料,如国产牌号2a12、国外牌号2024等硬铝合金具备重量轻、强度高、抗疲劳性能,塑性加工工艺性优良,热处理强化效果显著等优点。高强度、高塑性硬铝合金钣金零件将极大减轻飞机重量,降低油耗,延长服役寿命;因此硬铝合金钣金零件综合力学性能提升对飞机使用经济、安全技术指标十分重要。
3.公知,目前国、内对铝合金钣金零件材料常规制备方法主要有冷作硬化、喷丸强化、退火细化组织、淬火相变强化等。上述制备方法均存在强度与塑性指标提升相互矛盾问题,因此只能单方提高材料强度或塑性指标。尤其硬铝钣金零件,通常采用形变后直接加热到约500℃淬火快冷提高强度指标。主要缺陷如下:1)500℃高温停留时间长材料组织容易过烧或形成粗晶组织;2)硬铝合金主强化相al2cumg析出的敏感温度区间为300~400℃,过快冷却速度既不利于主强化相al2cumg的充分产生,又导致薄壁钣金零件产生变形甚至开裂;因此现有制备技术存在强度与塑性指标未完全发挥,或强度与塑性指标提升相互矛盾缺陷。
技术实现要素:4.为了充分提升硬铝合金钣金零件最终使用状态综合力学性能,克服现有制备技术组织过烧、粗晶、强化相析出不充分等缺陷,本技术的目的在于提供一种提升硬铝合金钣金零件综合力学性能的制备方法。通过充分利用形变、相变、细晶强韧化相结合,实现钣金零件使用状态强度及塑性指标双提升,显著提升综合力学性能指标。
5.一种提升硬铝合金钣金零件综合力学性能的制备方法,其特征在于包含以下内容:1)在常温下成形钣金零件半成品,该半成品含有大于钣金零件理论轮廓的补充面及法兰边,并对半成品表面冷加工强化;2)将冷加工强化后的半成品加热,然后采用匹配的凸模与凹模合模对热状态下半成品进行厚向挤压;3)将挤压后的半成品先进行加热固溶,再进行淬火冷却;4)将冷却后的半成品按照钣金零件理论轮廓切割得到钣金零件成品;5)将钣金零件成品进行热软整形即可。
6.进一步地,在步骤1)中,采用金属弹丸喷丸工艺对半成品表面进行冷加工强化。
7.进一步地,在步骤2)中,将半成品加热到400
±
10℃热状态下进行厚向挤压。
8.进一步地,在步骤2)中,在半成品加热前,对半成品外表面涂覆变厚度耐火漆,耐火漆的厚度从半成品的补充面向内涂漆厚度渐变减薄,在半成品冷却后再将半成品外表面涂覆的变厚度耐火漆清除。
9.进一步地,在步骤3)中,对半成品进行加热固溶时,先将半成品在350
±
10℃环境下预热,然后再在494
±
5℃盐炉内保温。
10.进一步地,在步骤3)中,对半成品进行淬火冷却时,先将半成品从494
±
5℃盐炉环境温度下转移到200
±
10℃盐炉内环境温度下预降温,再将预降温后的半成品转移到室温水中冷却。
11.进一步地,在步骤5)中,在对钣金零件成品热软整形前,对钣金零件成品外表面涂覆等厚度耐火漆,然后再将钣金零件成品置于凸模与凹模之间,将钣金零件成品与凸模和凹模一起加温到220
±
10℃热软整形。
12.本技术有益效果是:
13.1)本技术通过变形储能,使材料组织处于高能状态,利于热状态挤压前较低温度发生再结晶,加快组织再结晶形核率,利于晶粒组织细化;
14.2)本技术热状态施加沿厚向挤压,利于组织动态再结晶再次晶粒细化,愈合变形产生微观裂纹,提高材料组织致密度。
15.3)本技术对半成品预热,可以极大提高淬火盐炉升温效率,减少接近494前高温等待时间,避免组织粗大;
16.4)本技术半成品从高温494
±
5℃淬火盐炉转入200
±
10℃低温盐炉;既可延长强化相al2cumg析出时间,又减少极速冷却变形;
17.5)本技术220
±
10℃热软整形,低温热形变易保留变形组织,达到充分利用相变、形变、细晶复合强化效果。
18.下面结合附图和实施例对本技术进一步说明。
附图说明
19.图1是本技术适用的典型硬铝合金钣金零件结构示意图。
20.图2是本技术硬铝合金钣金零件的半成品结构示意图。
21.图3是本技术对硬铝合金钣金零件的半成品涂覆变厚耐火漆截面放大示意图。
22.图4是本技术对硬铝合金钣金零件成品涂覆等厚耐火漆截面放大示意图。
23.图5是本技术对硬铝合金钣金零件的半成品热状态厚向挤压原理示意图。
24.图6是本技术对硬铝合金钣金零件成品热状态整形原理示意图。
25.图中编号说明:1.钣金零件,2.半成品,3.理论轮廓,4.补充面,5.法兰边,6.外表面,7.变厚度耐火漆,8.等厚度耐火漆,9.凸模,10.凹模,11.成品。
具体实施方式
26.参照附图1至附图6,本技术涉及的硬铝合金钣金零件,如图1所示,是一个半球形薄壁结构,为了提升该类硬铝合金钣金零件综合力学性能,根据本技术的发明方案,以图1钣金零件1为例,其制备过程如下:
27.步骤1)在常温下成形常规厚度2.0mm钣金零件1的半成品2,该半成品2含有大于钣金零件1理论轮廓3的补充面4及法兰边5,并对半成品2表面冷加工强化,使材料组织处于高能状态。需要补充说明两点:一是半成品2表面冷加工强化可以采用落锤冲击,榔头敲击,金属弹丸喷丸等工艺处理,为了达到更好的表面强化储能效果优选金属弹丸喷丸工艺方法;二是形变储能后材料组织能量越高,越易于低温退火细化晶粒组织。
28.步骤2)将冷加工强化后的半成品2加热,然后采用匹配的凸模9与凹模10合模对热
状态下半成品2进行厚向挤压。操作方法为:在半成品加热前,先对半成品2外表面6涂覆变厚度耐火漆7;再将半成品2加热到温度400
±
10℃,保温时间60
±
20分钟,热状态下进行厚向挤压,使材料动态再结晶细化晶粒;最后将半成品2室温冷却后清除外表面6涂覆的变厚度耐火漆7,完成热状态挤压动态再结晶细化晶粒退火制备过程。
29.需要补充说明三点:一是涂漆厚度从外向内渐变减薄,补充面4涂漆厚度约0.2倍材料厚度,零件区涂漆厚度约0.1倍材料厚度;其目的是合模时,凸模9、凹模10在补充面4区可先将材料密封避免金属软化外流,在漆层及模具共同作用下提高整体厚向挤压效果。二是热状态金属软化,金属与漆层体积膨胀,厚向挤压既可愈合冷变形或原材料微观裂纹,又可破碎粗晶组织,显著细化晶粒提高致密度。三是厚向挤压时凸模9、凹模10为室温,可提高退火制备过程过冷度加速再结晶形核率,利于细化晶粒。
30.步骤3)将挤压后的半成品2先进行加热固溶,再进行淬火冷却。加热固溶时,先将半成品2在350
±
10℃环境下预热,然后再在494
±
5℃盐炉内保温,使强化合金元素溶解。淬火冷却时,先将半成品2从494
±
5℃盐炉环境温度下转移到200
±
10℃盐炉内环境温度下预降温,再将预降温后的半成品2转移到室温水中冷却。
31.需要补充说明三点:一是加热固溶350
±
10℃预热,目的之一是缩短494
±
5℃盐炉入炉后升温、保温时间,减少晶粒组织粗大,氧化等缺陷。二是加热固溶350
±
10℃预热,目的之二是避免晶粒长大,因该温度处于再结晶温度下限,既可充分预热又降低预热组织长大。三是淬火冷却时200
±
10℃盐炉预降温时间3
‑
5分钟,目的是延长主强化相al2cumg析出敏感温度区间300~400℃的时长,增加主强化相al2cumg数量进一步提高强化效果。
32.步骤4)将冷却后的半成品2按照钣金零件1理论轮廓3切割去除补充面4及法兰边5,得到钣金零件1的成品11。
33.步骤5)将钣金零件1的成品11进行热软整形。操作方法为:在对钣金零件1成品11热软整形前,先对钣金零件成品11外表面6涂覆0.2倍材料厚度等厚度耐火漆8,再将钣金零件成品11与凸模9和凹模10一起加温到220
±
10℃合模热软整形,并保压3
‑
5分钟。
34.需要补充说明的是:一是为了进一步提高厚向挤压形变强化效果,半成品2外表面6涂敷的等厚度耐火漆8的厚度更厚,约0.2倍板料厚度。二是整形温度为220
±
10℃,低温加热其实质加速时效硬化,同时低温热挤压变易保留变形组织,实现再次强化效果提高。
35.因此经过步骤1)至步骤5)制备的钣金零件1,主要通过热状态厚向挤压显著细化晶粒提高塑性指标,同时通过淬火预降温增加主强化相al2cumg数量提高相变强化效果,并且经低温热整形保留变形组织再次强化。充分利用形变、相变、细晶强韧化相结合,实现钣金零件1使用状态强度或塑性指标双提升,显著提升综合力学性能指标。
36.本技术还需需要补充说明两个方面:一是本技术优先适用于二系硬硬铝合金(国产牌号2a12、国外牌号2024)钣金零件,五系铝合金采用其中部分方案适当改变参数也可达到提高综合力学性能目的,七系铝合金调整温度、时间等参数也可达到提高综合力学性能目的;因此本技术公开范围不仅限于说明书公开内容,其他相似方法提升铝合金综合力学性能应属本技术应用范围。二是本领域内薄壁结构件热处理强化效果与加热、冷却方式、材料壁厚等紧密相关,尤其壁厚与保温时间关系最为紧密,因此类似材料工程应用时根据产品调整部分参数实现综合力学性能提升也应属本技术应用范围。