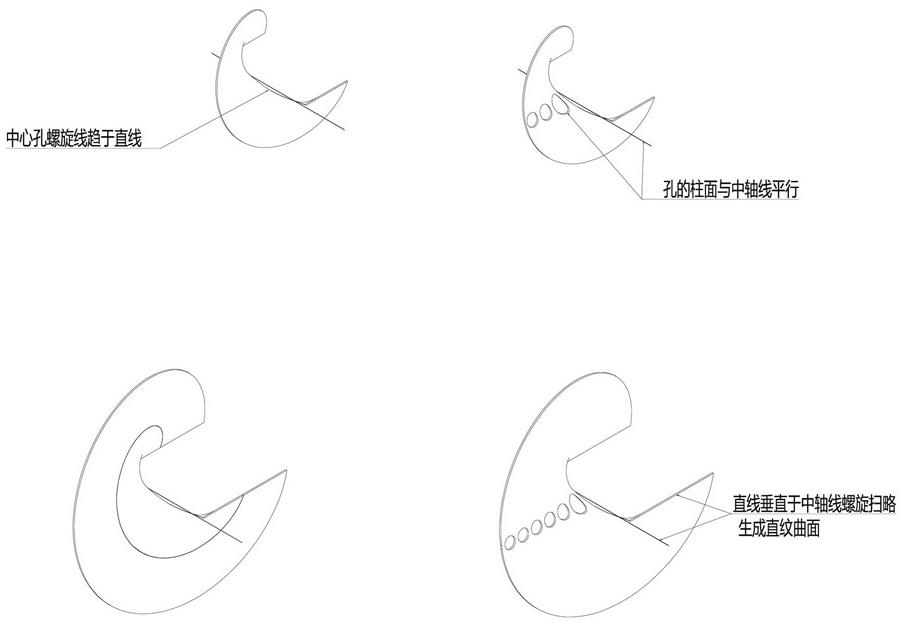
1.本发明涉及化工机械制造领域,特别涉及一种螺旋折流板的加工方法。
背景技术:2.螺旋折流板应用非常广泛,有中心假管孔的螺旋折流板,分片式螺旋折流板等等,其中一个有巨大价值的应用是管壳式换热器。在流程工业中,管壳式换热器在设备总投入中占比达到40~60%。百年来,管壳式换热器以弓形折流板为主,各种折流板结构的探索从未停止,其中,螺旋折流板结构在1925年就有专家提出,但由于加工困难,百年来,无数专家学者为之探索,均未有革命性突破。
3.现今螺旋折流板制造领域形成有共识,即用在管壳式换热器中的螺旋折流板板片的理想结构为(如图1):螺旋曲面特征为直纹曲面;无论外直径多么大,螺旋折流板为一个整体且中心孔螺旋线趋向于直线(或螺旋线与最中心的一根起实际作用的换热管接近贴合);螺旋折流板上的孔的柱面均与中轴线平行。
4.现有技术中采用的锻压、直接拉伸等机加工手段均无法获得满足中心孔螺旋线趋向于直线(或螺旋线与最中心的一根起实际作用的换热管接近贴合)、曲面形状为直纹曲面及孔柱面均与中轴线平行要求的螺旋折流板。在先专利(cn202010558873.x)公开了通过圆环板拉伸、拼接及拉伸的工艺手段制造螺旋折流板基板的加工方法,其加工对象为螺旋折流板基板未涉及管孔加工的技术手段,且经生产实践验证其存在一定技术局限性,即圆环板的内外径差值超过厚度的40倍以上时,由于内外螺旋线的变形量不一致,导致几乎无法加工出中心孔螺旋线趋向于直线(或螺旋线与最中心的一根起实际作用的换热管接近贴合)以及曲面形状为直纹曲面的螺旋折流板。实际上,螺旋折流板螺旋线的内外径差值都超过厚度的40倍,因此,现有加工方法无法实现理想结构螺旋折流板的工业化加工。
技术实现要素:5.申请提供了一种螺旋折流板的加工方法,解决或部分解决了现有加工方法无法实现理想结构螺旋折流板的工业化加工的技术问题;实现了提供一种能实现理想结构螺旋折流板的工业化加工的加工方法。
6.本技术所提供的一种螺旋折流板的加工方法,加工阶段分为:a内圈成型阶段、b内圈开孔阶段、c外圈成型阶段和d外圈开孔阶段,c外圈成型阶段和d外圈开孔阶段不是必须的,c外圈成型阶段和d外圈开孔阶段也可以多次交叉组合;a内圈成型阶段的螺旋折流板可由1~50圈螺旋扇环板拼接组成,c外圈成型阶段的螺旋折流板可由1~50圈螺旋扇环板拼接组成;a内圈成型阶段的步骤分为:a1下料、a2错位、a3多片拼接、a4拉伸、a5分割为若干螺旋扇环板,a6相邻螺旋扇环板相互拼接,当本圈螺旋扇环板为内侧第一圈时无需步骤a6相邻螺旋扇环板相互拼接,当内圈由多个螺旋扇环板组成时,步骤a1~a6反复循环;如果采用单片成型工艺,则不需要步骤a3多片拼接和步骤a5分割为若干螺旋扇环板,步骤a2错位
和步骤a4拉伸也可以合并为一个步骤;b内圈开孔阶段的步骤分为:加工孔可以选择在已经成型的螺旋折流板上加工产品所需的部分孔或者全部孔;c外圈成型阶段的步骤为:c1下料、c2错位、c3多片拼接、c4拉伸、c5分割为若干螺旋扇环板,c6相邻螺旋扇环板相互拼接,当外圈由多个螺旋扇环板组成时,步骤c1~c6反复循环,如果采用单片成型工艺,则不需要步骤c3多片拼接和步骤c5分割为若干螺旋扇环板,步骤c2错位和步骤c4拉伸也可以合并为一个步骤;d外圈开孔阶段的步骤分为: d1加工部分孔、d2翻面加工余下的孔,如果一次可以完成产品所需的孔,则不需要翻面加工孔;a内圈和c外圈的其中1圈或多圈螺旋扇环板还可采用碾压方法成型。
7.作为优选,螺旋折流板的外径为50~10000mm,螺旋折流板所加工孔的直径为6~200mm,螺旋折流板的厚度为1~50mm。
8.作为优选,螺旋折流板的材质为金属。
9.作为优选,孔的加工方式可以采用线切割、水刀切割、激光切割或钻铣的其中一种或多种组合。
10.作为优选,步骤a1下料和步骤c1下料的形状为扇环形,扇环形可由1~50片小件拼接而成,扇环形角度为1~719度。
11.作为优选,无论是内圈还是外圈的螺旋扇环板,可以采用不同厚度尺寸组合,但采用厚度一致的螺旋扇环板更为理想。
12.本技术实施例中提供的一个或多个技术方案,至少具有如下技术效果或优点:本技术的螺旋折流板的加工方法制得的螺旋折流板具有较好的互换性,能尽可能的保证加工获得的螺旋折流板(如图1)的螺旋面为直纹曲面(垂直于轴线的直线绕轴线螺旋扫略),直纹曲面螺旋折流板从轴线到外径无断开,中心孔螺旋线趋向于直线,折流板所有管孔的柱面均与中轴线平行,继而获得满足形位精度指标要求的螺旋折流板,填补该领域技术空白。
附图说明
13.为了更清楚地说明本技术实施例或现有技术中的技术方案,下面将对实施例或现有技术描述中所需要使用的附图作简单地介绍,显而易见地,下面描述中的附图仅仅是本技术的部分实施例,对于本领域普通技术人员来讲,在不付出创造性劳动的前提下,还可以根据这些附图获得其他的附图。
14.图1为本技术实施例提供的直纹曲面螺旋折流板的结构示意图;图2为本技术实施例提供的加工方法4个阶段的过程示意图;图3为本技术实施例提供的内圈第1圈(最内圈)螺旋扇环板成型工艺线路图;图4为本技术实施例提供的内圈第n圈(非最内圈)螺旋扇环板成型工艺线路图;图5为本技术实施例提供的外圈螺旋扇环板成型工艺线路图;图6为本技术实施例提供的先成型后开孔的工艺线路图;图7为本技术实施例提供的成型和开孔反复交叉的工艺线路图。
具体实施方式
15.为使本技术实施例的目的、技术方案和优点更加清楚,下面将结合本技术实施例中的附图,对本技术实施例中的技术方案进行清楚、完整地描述,显然,所描述的实施例是本技术一部分实施例,而不是全部的实施例。基于本技术中的实施例,本领域普通技术人员在没有做出创造性劳动前提下所获得的所有其他实施例,都属于本技术保护的范围。
16.本技术的螺旋折流板的加工方法分为4个阶段(如附图2),即a内圈成型阶段、b内圈开孔阶段、c外圈成型阶段和d外圈开孔阶段,如果螺旋折流板直径不大,则只需要a内圈成型阶段、b内圈开孔阶段两个阶段。把大直径的螺旋折流板分为4个阶段的原因是:1)内圈的孔特别难加工,特别是靠紧轴线的大倾斜角度处加工孔,需要采用线切割开孔等加工方法,内圈成型后先加工孔后再拼接外圈、之后再加工孔会大大降低内圈开孔的设备尺寸和难度;2)内圈开孔后可以作为定位基准,有效解决了外圈开孔的相对位置查找定位问题。
17.扇环板拉伸成型为螺旋扇环板的过程中,扇环板的内圆弧周长l11对应于螺旋扇环板的内螺旋线长度l12,扇环板的外圆弧周长l21对应于螺旋扇环板的外螺旋线长度l22,通过理论计算得:(l11-l12)≠(l21-l22),及螺旋扇环板成型过程中内外螺旋线的变形量不一致,当扇环板的内外径差值越小,这种变形不一致的差值也越小,也越容易获得具有直纹曲面特征的螺旋扇环板,当扇环板内外径差值超过壁厚的40倍以上是,几乎无法拉伸获得具有直纹曲面特征的螺旋扇环板,所以想获得内外径差值超过壁厚40倍以上的螺旋扇环板,只能采用多片螺旋扇环板拼接的方式获得。
18.a内圈成型阶段可以由1~50圈螺旋扇环板拼接而成,内圈螺旋扇环板的成型工艺分为第1圈(最内圈)螺旋扇环板成型工艺(如附图3)和第n圈(非最内圈)螺旋扇环板成型工艺(如附图4),第1圈螺旋扇环板成型工艺与第n圈螺旋扇环板成型工艺的区别在于第1圈螺旋扇环板成型后内螺旋线趋向于直线,第n圈螺旋扇环板成型后内螺旋线与半成品折流板的外螺旋线接近相贯。内圈螺旋扇环板成型工艺均可分为:1)多片成型工艺;2)单片间接成型工艺;3)单片直接成型工艺。内圈螺旋扇环板多片成型工艺的步骤为:a1下料、a2错位、a3多片拼接、a4拉伸、a5分割,具体可以为:将拉伸后的多片内圈螺旋扇环板再分割为多个独立的内圈螺旋扇环板。
19.内圈螺旋扇环板单片间接成型工艺的步骤为:a1下料、a2错位、a4拉伸,具体可以为:先将扇环形板的两个径向端部进行错位,再将错位后的扇环形板拉伸形成螺旋折流板内圈。内圈螺旋扇环板单片直接成型工艺的步骤为:a1下料、a4拉伸,具体可以为:直接将扇环形板拉伸形成螺旋折流板内圈。
20.c外圈成型阶段可以由1~50圈螺旋扇环板拼接而成,外圈螺旋扇环板的成型工艺如附图4,第n圈螺旋扇环板成型后内螺旋线与半成品折流板的外螺旋线接近相贯。外圈螺旋扇环板成型工艺均可分为:1)多片成型工艺;2)单片间接成型工艺;3)单片直接成型工艺。外圈螺旋扇环板多片成型工艺的步骤为:c1下料、c2错位、c3多片拼接、c4拉伸、c5分割,具体可以为:将拉伸后的多片外圈螺旋扇环板以轴线截面分割为多个独立的外圈螺旋扇环板。
21.外圈螺旋扇环板单片间接成型工艺的步骤为:c1下料、c2错位、c4拉伸,具体可以为:先将扇环形板的两个径向端部进行错位,再将错位后的扇环形板拉伸形成螺旋折流板外圈。外圈螺旋扇环板单片直接成型工艺的步骤为:c1下料、c4拉伸,具体可以为:直接将扇
环形板拉伸形成螺旋折流板外圈。
22.a内圈成型阶段完成后即进行孔的加工,内圈可以由1~50圈螺旋扇环板组成,当折流板尺寸不大时,一次或多次完成孔的加工即可,如果折流板尺寸过大,则加工内圈的全部或部分孔,然后进入c外圈成型阶段和d外圈开孔阶段,外圈可以由1~50圈螺旋扇环板组成,c外圈成型阶段和d外圈开孔阶段可1次或多次交叉进行。d外圈开孔阶段的步骤分为: d1加工部分孔、d2翻面加工余下的孔,如果一次可以完成产品所需的孔,则不需要步骤d2翻面加工余下的孔;另外,外圈开孔以内圈管孔为定位基准,在螺旋折流板外圈位置上以中心孔向外缘的方向开设外圈管孔。
23.a内圈和c外圈的其中1圈或多圈螺旋扇环板还可采用碾压方法成型,即用钢带通过碾压成型机加工绞龙的方法,该方法制作出的螺旋扇环板内螺旋线厚,外螺旋线薄,仅适用于内外螺旋线直径差值较小的情况,该方法能够实现加工,当内外螺旋线直径差值较大时,几乎很难或者无法加工出螺旋扇环板。
24.具体实施实例参见附图,加工用于管壳式换热器的外径1000mm、螺距500mm、厚度5mm的直纹曲面螺旋折流板,加工方法如下:a1下料扇环板内径约200mm,外径约350mm,扇环形角度359度,厚度5mm,每片板子分别进行a2错位,然后a3多片拼接,拼接可采用焊接方式,控制各片板子的同心度,接着a4拉伸,直到板子的螺距约为500mm后拆卸,进行a5分割工作,得到内螺旋线直径约15mm,外螺旋线直径约165mm的螺旋折流板第1小圈。
25.a1下料扇环板内径约250mm,外径450mm,扇环形角度359度,厚度5mm,每片板子分别进行a2错位,然后a3多片拼接,拼接可采用焊接方式,控制各片板子的同心度,接着a4拉伸,知道板子的螺距约为500mm后拆卸,进行a5分割工作,得到内螺旋线直径约165mm,外螺旋线直径约365mm的螺旋折流板第2小圈,进行a6相邻螺旋扇环板相互拼接,得到内螺旋线直径约为15mm,外螺旋线直径约为365mm,厚度约为5mm的螺旋折流板。
26.进入b内圈开孔阶段,对成型的螺旋折流板的中间加工5~20个倾斜角度较大的孔。
27.c1下料扇环板内径约415mm,外径715mm,扇环形角度359度,厚度5mm,1)当采用多片成型工艺时步骤如下:每片板子分别进行c2错位,然后c3多片拼接,拼接可采用焊接方式,控制各片板子的同心度,接着c4拉伸,直到板子的螺距约为500mm后拆卸,进行c5分割工作;2)当采用单片间接成型工艺时步骤如下:每片板子分别进行c2错位,接着c4拉伸,直到板子的螺距约为500mm;3)当采用单片直接成型工艺时步骤如下:每片板子分别进行c4拉伸,直到板子的螺距约为500mm。三种工艺均可得到内螺旋线直径约365mm,外螺旋线直径约665mm的螺旋折流板第3小圈,进行c6相邻螺旋扇环板相互拼接,得到内螺旋线直径约为15mm,外螺旋线直径约为665mm,厚度约为5mm的螺旋折流板。
28.c1下料扇环板内径约700mm,外径1035mm,扇环形角度359度,厚度5mm,考虑到节约材料,扇环板可以由多片小角度的拼接而成,例如用6块扇环形角度约59度的扇环板拼接成一片扇环形角度约为356度的扇环板。1)当采用多片成型工艺时步骤如下:每片板子分别进行c2错位,然后c3多片拼接,拼接可采用焊接方式,控制各片板子的同心度,接着c4拉伸,直到板子的螺距约为500mm后拆卸,进行c5分割工作;2)当采用单片间接成型工艺时步骤如
下:每片板子分别进行c2错位,接着c4拉伸,直到板子的螺距约为500mm;3)当采用单片直接成型工艺时步骤如下:每片板子分别进行c4拉伸,直到板子的螺距约为500mm。三种工艺均可得到内螺旋线直径约665mm,外螺旋线直径约1000mm的螺旋折流板第4小圈,进行c6相邻螺旋扇环板相互拼接,得到内螺旋线直径约为15mm,外螺旋线直径约为1000mm,螺距约500mm,厚度约为5mm的螺旋折流板。
29.以b内圈开孔阶段加工的孔作为定位基准,进入d外圈开孔阶段,步骤分为: d1加工部分孔、d2翻面加工余下的孔,如果一次可以完成产品所需的孔,则不需要步骤d2翻面加工余下的孔。
30.至此,具有直纹曲面特征、内径趋向于直线的、外径约1000mm、螺距约500mm、厚度约5mm的螺旋折流板加工完成。
31.加工过程c外圈成型阶段和d外圈开孔阶段也可以多次交叉组合,但对于提高效率意义不大。
32.加工过程中,a内圈和c外圈的其中1圈或多圈螺旋扇环板可采用碾压方法成型,即用钢带通过碾压成型机加工绞龙的方法(该方法是成熟工业生产技术),该方法制作出的螺旋扇环板内螺旋线处法向厚度偏厚,外螺旋线处法向厚度偏薄,仅适用于内外螺旋线直径差值较小的情况,该方法能够实现加工,但对于提高效率意义不大,也不具备经济性。
33.以上所述的具体实施方式,对本发明的目的、技术方案和有益效果进行了进一步详细说明,所应理解的是,以上所述仅为本发明的具体实施方式而已,并不用于限制本发明,凡在本发明的精神和原则之内,所做的任何修改、等同替换、改进等,均应包含在本发明的保护范围之内。