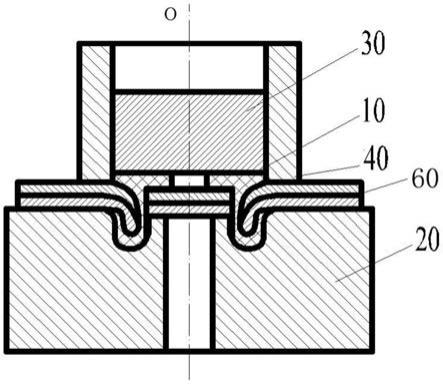
1.本发明属于薄板材料的机械变形连接技术领域,具体涉及一种自冲铆连接装置及其铆接方法。
背景技术:2.自冲铆(self piercing rivet,缩写spr)是近些年来快速发展的一种薄板材料新型机械变形连接技术。与传统铆接方法不同,自冲铆连接过程无须预先钻孔,半空心铆钉在冲头的作用下穿透上板,并且在下模引导下,中空铆钉脚在下板中不断扩张,最终与被连接材料形成力与结构封闭的机械内锁结构。在汽车、建筑、家用电器的结构件设计制造等领域,由于自冲铆连接技术具有快速高效、适应性强等特点,已成为轻合金——特别是铝合金薄板材料机械连接中首选重要技术之一。
3.然而,随着航空、航天,轨道交通等结构轻量化需求的不断增加,自冲铆连接所涉及的薄板材料的种类在不断扩展,从传统地高延展性材料,如5052铝合金等,逐渐扩展到了低延展性材料,如,铸铝,铝硅合金、先进高强度钢、超高强钢、碳纤维等。甚至是异种材料的连接,如,钢/铝,铝/碳纤维等铝合金。传统的自冲铆技术在面对低延展性材料的连接时,遇到了巨大的挑战。现有技术的自冲铆成型过程中,低延展性材料在成型模具中流程性差,导致了机械内锁不充分、材料开裂等问题,进而降低了结构件的连接强度和使用寿命。因此,开发适用于低延展性薄板材料连接“高效”、“可靠”的铆接技术是实际工程应用急待解决的技术问题。
技术实现要素:4.针对上述问题,本发明旨在提供一种适用于低延展性材料铆接的自冲铆连接装置,同时提供应用该装置进行自冲铆接的方法。
5.本发明解决问题的技术方案是:一种自冲铆连接装置,包括半空心的铆钉、中空的压边圈、设置于压边圈的中空腔内的上冲杆、设置于压边圈正下方的下模,在下模上、位于上冲杆正下方设有成型凹槽,所述上冲杆可在压边圈内上下移动,所述铆钉位于上冲杆与下模之间,所述铆钉包括钉帽、从钉帽下表面往下延伸的钉杆,钉杆具有敞开口朝下的中空腔,所述成型凹槽为圆环形凹槽,所述铆钉为可刺穿低延展性板料的铆钉;
6.所述铆钉刺穿板料后,钉杆下端径向扩张并向上翻卷,形成“u”型钩状结构,且钩状结构的上端与板料下表面抵接。
7.上述方案中,板料的部分材料进入了u型钩状结构的型腔内,形成相互咬合的关系。
8.现有技术中,自冲铆技术在铆接板材时,铆钉的钉杆不刺穿下层板料,只刺穿上层板料,在下层板料中钉杆扩张形成机械内锁。
9.上述方案改变原来的惯性思维,创造性的将下层板料也刺穿,巧妙的绕过了低延展性材料在成型模具中流程性差的不利因素,减少低延展性材料的流动,避免了低延展性
材料开裂等问题出现,通过“u”型钩状结构形成咬合内锁,保证了铆接的连接强度和使用寿命。
10.具体的,所述钉帽为圆盘形,所述钉杆为圆台体;
11.所述钉杆上端外径d
r1
大于钉杆下端外径d
r2
;
12.所述钉杆的中空腔为圆柱形腔,其内径为dk、深度为t1;
13.所述钉帽、钉杆、钉杆的中空腔、成型凹槽具有共同的中心轴o;
14.所述钉帽外径dm大于钉杆上端外径d
r1
;
15.所述钉帽和钉杆的连接界面区域设有第一过渡圆弧,所述第一过渡圆弧的半径rd满足关系为:rd≥0.5
·
(d
m-d
r1
)。
16.进一步的,所述成型凹槽深度为t
c2
,成型凹槽的内径为d
c1
,成型凹槽的外径为d
c2
,并满足条件:
17.0.98≤d
c1
/dk≤1,且dm/d
c2
<1;
18.在径向方向上,圆环形凹槽的内侧和外侧分别形成有内凸台和外凸台,所述内凸台的高度低于外凸台的高度;内凸台、外凸台、以及圆环形凹槽具有共同的中心轴线o。
19.进一步的,所述成型凹槽的侧壁与成型凹槽底面之间设有第二过渡圆弧,且第二过渡圆弧的半径rh满足关系:
20.rh≥0.25
·
(d
c2-d
c1
);
21.进一步的,所述铆钉的总长度lr与t
c2
满足关系:lr=(1.5~2)
·
t
c2
。
22.优选的,所述铆钉的总长度lr为9.5~10.5mm;钉帽外径dm为11.5~12.5mm;钉杆下端外径d
r2
为7.5~8.5mm;
23.所述钉杆的中空腔内径dk为5.5~6.5mm;钉杆的中空腔深度t1为6.5~7.5mm。
24.优选的,所述成型凹槽的内径d
c1
为5.5~6.5mm;成型凹槽的外径d
c2
为15.5~16.5mm;
25.所述内凸台的与外凸台之间的高度差t
c1
为1~2mm。
26.更进一步的,所述钉杆下端设有利于刺穿的倒直角部,倒直角尺寸lm满足关系式:lm≥0.5
·
(d
r2-dk)。
27.优选的,在第一过渡圆弧处沿周向设有多个防扭凸台。
28.进一步的,在钉帽中心开有与钉杆的中空腔连通的通孔,所述通孔直径mm小于钉杆中空腔的内径dk。
29.相应的,本发明还提供一种应用上述自冲铆连接装置的铆接方法,包括如下步骤:
30.步骤1:将待连接的板料置于压边圈和下模之间,铆接点对准上冲杆位置;铆钉被送入压边圈的中空腔内,并置于上冲杆正下方;压边圈逐渐靠近下模,直至与板料抵接;
31.步骤2:上冲杆在驱动力作用下,向下模高速运动,铆钉在上冲杆的推动下对板料进行剪切,钉杆完全刺穿板料;
32.步骤3:铆钉在上冲杆的带动下继续下行,直至钉杆与成型凹槽接触;在成型凹槽的约束下,所述钉杆径向扩张,向外、向上翻卷;最终钉杆的中空腔部位的材料与板料相咬合,形成“u”型钩状结构,且钩状结构的上端与板料下表面抵接;
33.步骤4:保压预定时间后停止施压,铆接完成。
34.进一步的,在钉帽中心开有与钉杆的中空腔连通的通孔;
35.步骤4之后,还包括步骤5:通过驱动推杆,插入所述钉帽的通孔中,将连接成形过程中镶嵌在钉杆中空腔内的材料推出,实现多余材料的落料。
36.优选的,步骤1中,压边圈与下模之间的压紧力为500n~800n;
37.步骤2中,上冲杆与下模之间的相对运动速度为20mm/s~40mm/s。
38.优选的,在步骤3之后,步骤4之前,还包括步骤3a:持续给上冲杆施压,直至钉帽与板料上表面平齐。
39.本发明的显著效果是:
40.1、解决低延展性铝合金、镁合金、铸铝,以及异种薄板材料的机械连接问题。避免了低延展性材料铆接过程中或使用过程中开裂等问题出现,通过“u”型钩状结构形成咬合内锁,铆接点具备较高的静态强度、动态疲劳寿命,保证了铆接的连接强度和使用寿命。
41.2、防扭凸台的设计,使得铆接点在使用过程中,具有防松功能。
42.3、无需在板料上预制孔,而是直接自冲铆接,铆接工作效率高;
43.4、整体装备结构简单,连接工艺可靠;
附图说明
44.下面结合附图对本发明作进一步说明。
45.图1示出了本发明自冲铆接成型的结构示意图;
46.图2示出了本发明一种具体的铆钉三维轴侧图;
47.图3为图2铆钉的剖视图;
48.图4示出了本发明另一种具体的铆钉三维轴侧图;
49.图5为图4铆钉的剖视图;
50.图6示出了本发明下模的三维轴侧图;
51.图7为图6下模的剖视图;
52.图8示出了本发明自冲铆接过程示意图,其中,(a)示出了铆钉准备刺穿板料的临界状态;(b)示出了铆钉刺穿板料的状态;(c)示出了最终铆接成型的状态;(d)示出了落料的状态。
53.图中:10-铆钉,11-通孔,12-钉帽,13-第一过渡圆弧,14-防扭凸台,15-钉杆,16-倒直角部,20-下模,21-成型凹槽,22-定位孔,23-内凸台,24-外凸台,30-上冲杆,40-压边圈,50-推杆,60-板料,211-内侧壁,212-外侧壁。
具体实施方式
54.为了便于描述,各部件的相对位置关系(如:上、下、左、右等)的描述均是根据说明书附图的布图方向来进行描述的,并不对本专利的结构起限定作用。
55.如图1~7所示,一种自冲铆连接装置,包括半空心的铆钉10、中空的压边圈40、设置于压边圈40的中空腔内的上冲杆30、设置于压边圈40正下方的下模20。在下模上、位于上冲杆正下方设有成型凹槽21。所述压边圈40为空心圆柱体结构。所述铆钉10包括钉帽12、从钉帽12下表面往下延伸的钉杆15。钉杆15具有敞开口朝下的中空腔。所述上冲杆30为圆柱体,上冲杆30插入压边圈40的空腔内,并可在压边圈40内上下移动。上冲杆30与压边圈同轴。所述铆钉10位于上冲杆30与下模20之间。
56.所述半空心的自冲铆钉10由合金钢制成。所述下模21由工具钢或硬质合金制成。下模20上沿其中心轴线o设有用于装配固定的定位孔22。
57.所述成型凹槽21为圆环形凹槽。所述铆钉10为可刺穿低延展性板料60的铆钉。
58.所述铆钉10刺穿板料60后,钉杆15下端径向扩张并向上翻卷,形成“u”型钩状结构,且钩状结构的上端与板料60下表面抵接。
59.板料60的部分材料进入了u型钩状结构的型腔内,形成相互咬合的关系。
60.所述钉帽12为圆盘形。所述钉杆15为圆台体。
61.所述钉杆15上端外径d
r1
大于钉杆15下端外径d
r2
。
62.所述钉杆15的中空腔为圆柱形腔,其内径为dk、深度为t1。
63.所述钉帽12、钉杆15、钉杆15的中空腔、成型凹槽21具有共同的中心轴o。
64.所述钉帽12外径dm大于钉杆15上端外径d
r1
。
65.所述钉帽12和钉杆15的连接界面区域设有第一过渡圆弧13。所述第一过渡圆弧13的半径rd满足关系为:rd≥0.5
·
(d
m-d
r1
)。
66.优选的,在第一过渡圆弧处沿周向设有多个防扭凸台14。防扭凸台14主要起到放松作用。一种具体的实施方式中,如图2和3所示,防扭凸台14为三角形凸起。另一种具体实施方式中,如图4和5所示,防扭凸台14为圆形凸起。
67.所述成型凹槽21深度为t
c2
,成型凹槽21的内径为d
c1
,成型凹槽的外径为d
c2
,并满足条件:0.98≤d
c1
/dk≤1,且dm/d
c2
<1。在径向方向上,圆环形凹槽的内侧和外侧分别形成有内凸台23和外凸台24。所述内凸台23的高度低于外凸台24的高度。内凸台23、外凸台24、以及圆环形凹槽具有共同的中心轴线o。所述成型凹槽21的内侧壁211的高度低于成型凹槽21外侧壁212的高度。
68.所述成型凹槽21的侧壁与成型凹槽21底面之间设有第二过渡圆弧,且第二过渡圆弧的半径rh满足关系:rh≥0.25
·
(d
c2-d
c1
)。
69.所述铆钉10的总长度lr与成型凹槽21深度t
c2
满足关系:lr=(1.5~2)
·
t
c2
。
70.优选的,所述铆钉10的总长度lr为9.5~10.5mm。钉帽12外径dm为11.5~12.5mm。钉杆15下端外径d
r2
为7.5~8.5mm。所述钉杆15的中空腔内径dk为5.5~6.5mm。钉杆15的中空腔深度t1为6.5~7.5mm。
71.所述成型凹槽21的内径d
c1
为5.5~6.5mm。成型凹槽21的外径d
c2
为15.5~16.5mm。所述内凸台23的与外凸台24之间的高度差t
c1
为1~2mm。
72.所述钉杆15下端设有利于刺穿的倒直角部16,倒直角尺寸lm满足关系式:lm≥0.5
·
(d
r2-dk)。
73.一种更优选的实施例中,在钉帽12中心开有与钉杆15的中空腔连通的通孔11。所述通孔11直径mm小于钉杆15中空腔的内径dk。设计通孔11的目的在于便于铆接后,使镶嵌在铆钉10中空腔内的材料落料,保证接头质量。
74.相应的,本实施例还提供一种应用上述自冲铆连接装置的铆接方法,如图8所示,包括如下步骤:
75.步骤1:如图8(a),将待连接的板料60置于压边圈40和下模20之间。铆接点对准上冲杆30位置。铆钉10被送入压边圈40的中空腔内,并置于上冲杆30正下方。压边圈40逐渐靠近下模20,直至与板料60抵接。优选的,压边圈40与下模20之间的压紧力为500n~800n。
76.步骤2:如图8(b),上冲杆30在驱动力作用下,向下模20高速运动。铆钉10在上冲杆30的推动下对板料60进行剪切,钉杆15完全刺穿板料60。优选的,上冲杆30与下模20之间的相对运动速度为20mm/s~40mm/s。
77.步骤3:如图8(c),铆钉10在上冲杆30的带动下继续下行,直至钉杆15与成型凹槽21接触。在成型凹槽21的约束下,所述钉杆15径向扩张,向外、向上翻卷。最终钉杆15的中空腔部位的材料与板料60相咬合,形成“u”型钩状结构,且钩状结构的上端与板料60下表面抵接。
78.步骤4:保压预定时间后停止施压,铆接完成。
79.为了保证铆接出的铆接点更加美观,或者某些工况要求更易装配,需要将铆钉10隐藏。那么,在步骤3之后,步骤4之前,还包括步骤:持续给上冲杆施压,直至钉帽与板料上表面平齐。
80.当所选用的铆钉10为在钉帽12中心开有与钉杆的中空腔连通的通孔11的铆钉时。上述步骤4之后,还包括步骤5:如图8(d),通过驱动推杆50,插入所述钉帽12的通孔11中,将连接成形过程中镶嵌在钉杆15中空腔内的材料推出,实现多余材料的落料。