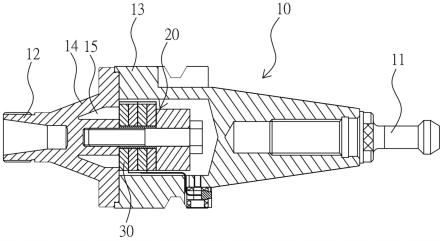
一种机床的超声波刀把构造
【技术领域】
1.本发明涉及一种加工用具,尤指涉及一种机床的超声波刀把构造。
背景技术:2.由于超声波振动辅助装置(ultrasonic vibration-assisted device,uvad)所产生的高频率振动,非常适合用于加工难切削(硬且脆)的材料,故广泛被应用在许多高端产业的零件加工上。而在uvad中,超声波主轴配合刀把对难切削材料进行加工,现今已经成为制造加工业者频繁使用的主力机具。虽在使用超声波主轴与刀把对难切削材料进行加工之时,改善刀把功能(几何形状与超声波驱动单元(含压电片)),确实可以达到提升切削效率与增加产品加工质量之目的,然鲜少文献针对超声波刀把几何形状进行探究。
3.随着科技不断地进展,新的材料亦如雨后春笋般的不断被研发出来,以符合现今高端产业产品零件特异功能之所求。且消费端产品对一些难加工材料(例如钛基合金、镍基合金、玻璃、陶瓷及硬化钢)的需求,更是有与日俱增得趋势。而探究其因,实乃难加工材料具有强度高、耐蚀、硬度高、脆性大与耐磨性佳等优点,故广泛被应用在航天、国防、能源、化工、医疗与光电半导体等高价值产业端零件上。然现今一般传统的加工技术,并未能随科技潮流之进展趋势,确切地对难加工材料提供有效的解决之策。目前有些业者已改采非传统加工技术以进行加工制程之优化改善,且已获致不错之效果。其中,超声波振动辅助加工是目前非传统加工方法中,最频繁使用解决难加工材料的一种有效之制程。
4.在1927年,美国物理学家wood与loomis最早做了超声波加工试验,其利用强烈的超声波振动对玻璃板进行雕刻与快速钻孔,然当时超声波振动技术并未应用在工业加工用途上。直至1951年,美国制作出第一台实用的超声波打孔机,为日后超声波加工技术的发展与应用开启了另一新页。同时,超声波振动辅助加工目前已被广泛应用于钻孔、车削、铣削、抛光、磨削、挤压、抽拉、放电加工与焊接等多样生产加工制程上。然随着不同之加工制程需求,其超声波振动辅助加工系统亦会有所不同,而此问题之解决需求,端赖产学研界共同一起努力。一般而言,超声波振动辅助加工是沿着一维、二维或三维之特定的方向对工具或工件施加超声波振动,以进行超声波振动辅助加工的目的。
5.请参阅图1,现有技术中机床得超声波刀把构造,主要包括:刀把本体40,该刀把本体40包括沿轴线延伸且适用于装设在机床主轴(图未示出)的装设部41、沿该轴线相反于该装设部41且适用于供刀具设置的加工刀具座42以及连接该装设部41及该加工刀具座42且沿该轴线的径向突出该装设部41的环部43;安装于该刀把本体40内的超声波驱动单元50,其具有一组压电片60以依电压振荡信号产生超声波机械振动;在加工刀具座42之中间处有一锥度形状的部位,此谓之锥型喇叭44,系用以将该组压电片60所产生之微小振幅进行放大。
6.超声波振动辅助加工有别于传统加工,系其于传统加工的基础上,增加一个纵向、横向或纵横向振动的切削方式,将连续的切削运动转变为非连续接触的切削运动,藉以改善刀具与工件之间的切削加工性能。kumabe于1979年发现振动切削可以降低切削力、改善
工件表面质量与减少刀具的磨耗。wang等人研究发现,将纵向扭转耦合旋转超声波加工用于脆性材料(如石英玻璃),与传统的超声波钻孔相比,可将钻孔出口处的边缘碎裂尺寸减小至45%左右。wang等人进行8mm厚石英玻璃的新颖实验,且确认边缘碎裂的减少与石英玻璃的未钻孔厚度之间存在直接的相关性。singh等人研究发现,进给速度与超声波功率均会显著影响旋转超声波加工对玻璃边缘碎裂的行为,且边缘碎屑尺寸初期会随着超声波功率增加而减小,直至特定进给速率超过60%时为止。同样地,wang等人研究振动钻削对复合材料层板(玻璃纤维、碳纤维与印刷电路板)之轴向推力影响。虽然加入振动辅助会使钻头与工件的冲击微裂缝扩大,但是加入振动辅助也会降低钻孔的扭矩。singh等人研究,超声波辅助切削可使刀具与被加工材料周期性的分离、降低加工温度与切削力,以达到增加刀具寿命的目的。至于在超声波辅助钻孔部份,singh与khamba观察切削可藉由超声波辅助振动方式顺畅的排出孔外,超声波辅助振动可以减小切削所造成之摩擦。郭桂林等人利用田口方法探讨超声波振动辅助对内螺纹攻牙之影响。他们分析结果显示,主轴转速与振动频率对攻牙之轴向推力与扭矩有相当程度的影响。对m3
×
0.5mm的螺丝加工结果而言,郭桂林等人亦验证了加入超声波振动辅助之后,攻牙扭矩有23%的降低幅度。同时在共振频率加工下,可以得到最低的攻牙扭矩值。换言之,在共振频率加工之下,可以降低因攻牙扭矩过大,而导致螺丝攻牙被扭断的风险。此外,jin与murakawa以倾斜10-30
°
主切削角度的刀具,对硬化钢材料进行振动切削。他们发现无论是连续或不连续的振动切削,均可有效地抑制刀具切刃的碎屑产生,且可获致较好的加工表面。takeyama与kato则实验证明超声波辅助钻削铝合金,的确可以达到降低毛刺尺寸的效果。zhang等人从理论与实验论证,于最佳振动条件下,使得切削加工之轴向推力与扭矩最小,因而造成有更小之加工毛刺产生。sharma等人指出,使用凹圆形工具于旋转超声波加工玻璃是最好的刀具。zeng等人实验观察旋转超声波振动辅助加工碳化硅(sic)材料之刀具磨耗情况。其实验结果发现,刀具端面的磨耗较侧面磨耗大,且随着加工孔数的增加而使得刀具的磨耗亦增加。同时,整个旋转超声波振动辅助加工碳化硅材料期间,最大的切削力发生在刀具磨耗阶段。此外,sindhu等人指出,钻石晶粒的锋利切刃导致石英材料的磨粒磨损与脆性断裂,且裂纹的相互交联导致钻石晶粒被拉出,并于加工表面形成更深的凹槽。
7.根据上述文献所述,超声波振动辅助加工不仅可以降低于切削加工时之轴向推力与扭矩,而且还可以提升加工工件之表面精度与刀具的使用寿命。然而超声波振动辅助加工的对象系多元化,且其功率的输出并非是一固定值,其会随着加工之不同材料性质(如抗拉强度、弹性系数等)、喇叭的形状尺寸、温度、质量(工具头与工件)与加工条件(进给速率、主轴转速、振幅与工件锁固力大小等)而有所不同。换言之,超声波振动辅助加工系统是一个高度非线性且时变的系统,即使在固定的电压或频率切换下,其输出之相电压振幅及共振频率,非常容易受到外在负载的变动而改变。因此要稳定且有效率地进行超声波振动辅助加工,必须保证超声波系统始终是处于良好的共振作动状态。而在实际超声波振动辅助加工过程中,由于外在负载的变化、工具磨损、换能器发热等因素的影响,换能器的机械频率将会发生漂移的现象,因而使整个超声波振动系统开始产生失谐,导致工具端面的振幅减小或消失,造成超声波振动辅助加工的能力降低或丧失。为了保证超声波振动辅助加工能有效率的进行,具有适应负载变化自动追频功能的智能超声波振动辅助加工系统是必要的考虑因素。
8.另外,为使超声波驱动单元能于加工时提供所需之振动源,超声波驱动单元装置在机床主轴(刀把)已逐渐取代传统之夹持座。探究其因,系超声波驱动单元装置在加工机之主轴上,且配合超声波刀把装置,其于超声波振动辅助加工时所产生之效率会是最佳,且亦不会影响原有机器之使用功能与作息。然目前超声波驱动单元装置在机床主轴上之制作门坎技术,相较于夹持座显然复杂许多。有关于cnc机器主轴有无装置超声波驱动单元之实物照片,如图4a及图4b所示。至于与超声波主轴搭配使用之刀把于切削加工时,亦扮演着非常重要的角色,而超声波刀把之设计良劣,亦会影响整个超声波振动辅助加工之结果,然目前鲜少文献对此问题做一论述。
9.由上述的说明可知,本领域亟需一种新颖的超声波刀把构造。
技术实现要素:10.本发明之主要目的于提供一种机床得超声波刀把构造,其可藉由挖空加工刀具座内部的一部分以形成至少一个空室并减少加工刀具座的重量,以增加超声波机械振动的振动幅度,从而提升超声波刀把的加工性能。
11.为达成上述目的,一种机床得超声波刀把构造乃被提出,其具有:刀把本体,该刀把本体包括沿轴线延伸且适用于装设在该机床主轴的装设部、沿该轴线相反于该装设部且适用于供刀具设置的加工刀具座,以及连接该装设部与该加工刀具座且沿该轴线的径向突出于该装设部的环部,该加工刀具座在中间处设有锥型喇叭,且该加工刀具座内部被部分挖空,形成至少一个空室;以及安装于该刀把本体内的超声波驱动单元,用以依照电压振荡信号产生超声波机械振荡。
12.在一实施例中,该超声波驱动单元具有一组压电片。
13.在一实施例中,该空室具有左、右对称的几何形状。
14.在一实施例中,该空室具有上、下对称的几何形状。
15.前述之超声波刀把构造可藉由挖空加工刀具座内部的一部分以形成至少一个空室,减少了加工刀具座的重量,以增加超声波机械振动的振动幅度,从而提升超声波刀把的加工性能。
16.为进一步了解本发明之结构、特征及其目的,兹附以图式及较佳具体实施例之详细说明如后。
【附图说明】
17.图1为现有技术中机床的超声波刀把构造之剖面视图;
18.图2为本发明所提供的机床超声波刀把构造之剖面视图;
19.图3为将图2的机床之超声波刀把构造装设在机床主轴后的剖面视图;
20.图4a为cnc机床主轴无装置超声波驱动单元之实物照片;
21.图4b为cnc机床主轴有装置超声波驱动单元之实物照片;
22.图5a为加工刀具座的锥型喇叭改变前之几何形状剖视图;
23.图5b为加工刀具座的锥型喇叭改变后之几何形状剖视图;以及
24.图6为本发明所提供的加工刀具座的锥型喇叭几何形状剖视图。
25.符号简单说明:
26.10:刀把本体
ꢀꢀꢀꢀꢀꢀꢀꢀꢀꢀꢀ
11:装设部
27.12:加工刀具座
ꢀꢀꢀꢀꢀꢀꢀꢀꢀ
13:环部
28.14:锥型喇叭
ꢀꢀꢀꢀꢀꢀꢀꢀꢀꢀꢀ
15:空室
29.20:超声波驱动单元
ꢀꢀꢀꢀꢀ
30:压电片
【具体实施方式】
30.请一并参阅图2及图3,本发明所提供的机床之超声波刀把构造主要包括有:刀把本体10及具有一组压电片30的超声波驱动单元20。
31.其中刀把本体10包括沿轴线延伸且适用于装设在机床主轴90的装设部11、沿该轴线相反于装设部11且适用于供刀具设置的加工刀具座12,以及连接装设部11及加工刀具座12且沿该轴线的径向突出装设部11的环部13。加工刀具座12在中间处设有一锥度形状的部位,此谓之锥型喇叭14,其系用以将该组压电片30所产生之微小振幅进行放大。值得一提的是,加工刀具座12内部被部分挖空而形成至少一个空室15并减少加工刀具座12的重量,而此安排可以增强超声波振动辅助加工的共振效应。
32.超声波驱动单元20的该组压电片30系用以依照电压振荡信号产生超声波机械振动。
33.较佳地,设置于加工刀具座12内部的空室15具有左、右对称和/或上、下对称的几何形状。
34.以下说明本发明所提供的一种机床的超声波刀把构造,所依据的理论基础与实验方式:
35.本发明掌握之技术会先针对超声波驱动单元的等效电路做静态量测(扫频),以取得超声波驱动单元静态的共振频率与等效电阻。进而再将此重要数据做为超声波驱动单元等效电路动态量测(追频)或加工控制的一个非常重要的输入参数,于超声波振动辅助加工时可进行追频功能。
36.据此,本发明将先藉助田口实验法所规划的刀把参数(壁厚w、倒弧角h与槽长l)与l18直交表,对加工刀具座之锥型喇叭几何尺寸进行优化设计。接着,再以改良设计后之最佳超声波刀把于超声波振动辅助扫追频系统下,验证最佳超声波刀把对钛合金材料加工之效果。最后盼此改良后的刀具装置,可提升国内制造加工业者未来对难切削材料加工的效率与产品质量。
37.对有装置超声波驱动单元的cnc机器主轴而言,其所搭配使用的超声波刀把设计好坏与否,于超声波振动辅助加工的效率影响颇大。然现今产学界于超声波刀把设计均局限于如何将电源导入至其内部之换能器上,使其能于超声波振动辅助加工时,能产生所预期之功率输出。
38.从锥型喇叭前端有刀具质量(m)时,其共振条件为:
[0039][0040]
其中,α为波长常数,λ为质量系数,l为半波长共振的锥型喇叭长度,d1为锥型喇
叭大端直径,d2为锥型喇叭小端直径。若d1与d2以锥型喇叭大端面积s1及锥型喇叭小端面积s2替代,则方程式(1)变成:
[0041][0042]
再者,由ρ=v/m得知,s1/s2可以m1/m2替代。其中,ρ为锥型喇叭材料的比重,m为锥型喇叭的质量,v为锥型喇叭的体积,m1为改变前的锥型喇叭质量,m2为改变后之锥型喇叭质量。此时,方程式(2)可再改写成方程式(3),而方程式(3)可表示成:
[0043][0044]
从方程式(3)得知,当锥型喇叭前端有刀具,且α、δ与1为一定值时,因m1大于m2,故m1/m2之值会永远大于一。因此,改变后的锥型喇叭共振效应会随着m1/m2的值增加而增加。换句话说,改变加工刀具座之锥型喇叭的m1/m2值,则其即可增加超声波振动辅助加工的共振效应。据此,本发明改变目前使用的超声波锥型喇叭的质量,如图5a所示,而改变后之加工刀具座的锥型喇叭几何剖视图,如图5b所示。
[0045]
稳健制程设计(robust process design)的观念,是田口质量设计方法最核心的教条。利用直交表规划实验,信号杂音比(signal-to-noise,s/n)分析实验数据。直交表设计实验,可以使实验者以快速、经济的方式,同时研究多个可控制因子对质量特性及变异数的影响。信号杂音比分析实验数据,可使实验者容易获得最适合的参数组合,达到节省时间及成本之目的。通常于切削加工时比较在乎的是,加工时材料移除量愈大愈好,此种其值愈大愈好的特性,称为望大特性(higher is better,hb)。再者,于切削加工后所产生之工件表面粗糙度,则是希望愈小愈好,此种其值愈小愈好的特性,称为望小特性(lower is better,lb)。若有n个具有望大特性的实验数据值y(y1,y2,...,yn),其目标值y值愈大,则损失函数l(y)愈小,且l(∞)=0,l
′
(∞)=0,则单位的变异大小为:
[0046][0047]
反之,假设n个具有望小特性的实验数据值y(y1,y2,...,yn),其目标值y为零,则单位的变异数大小为:
[0048][0049]
田口质量工程,取o2之倒数就是s/n比,若对s/n比取对数再乘10,则称为分贝单位的s/n比,以符号η表示之,即:
[0050][0051]
应用以上公式,逐一计算加工后之材料移除率与表面粗糙度等质量参数及其水平的s/n比,即可建构出s/n的响应表,且应用此结果,则可得到影响切削加工后材料移除率与
表面粗糙度之最佳制程参数(如机具额定功率、主轴转速与进给速率,以及刀具材料与几何形状)。
[0052]
另外,变异数分析是基于总平方和(或总变异v)及自由度f之分割,即资料收集产生各种变异,而该变异总和即总变异,根据变异之加成分解成组间变异(各因素之变异)和误差变异(或称组内变异)。依据变异数分析理论,总变异数(v
t
)可表示如下:
[0053]vt
=∑vi+veꢀꢀꢀꢀꢀꢀꢀꢀ
(7)
[0054]
其中,vi为各因素之变异,ve为误差变异。求出变异数前,需先计算各制程参数和误差因素变动平方和如下:
[0055][0056][0057][0058]
se=s
t-∑saꢀꢀꢀꢀꢀꢀꢀꢀꢀꢀꢀꢀ
(11)
[0059]
其中,s
t
为总变异数平方和,sm为平均变异数平方和,sa为变数a的平方和,se为误差的平方和,ηi为每次实验值(i=1~9),η
ai
为变数a第i层次的和(i=1,2或i=1,2,3),n为变数a第i层次的重复次数。另外,推定因素是否显著,要看其是否大于误差变异,而此采f
a0
检定,将组间变异与误差变异相除,则可得f
a0
比值,其计算式如下:
[0060][0061][0062]
其中,fa为变数a的自由度,va为变数a的变异数,f
ao
为变数a的f值。至于判断f计算值要大于多少才有效果,国际上使用f检定表判断,故仅须查表即可得到f临界值(f
0.05,n1,n2
),其中,f
0.05,n1,n2
为统计学上自由度n1、n2且大于f分布95%之参考值,若变数a的f
a0
值大于f
0.05,n1,n2
值,可推论此变数a为显著因素,此即为f检定法。
[0063]
因本发明要探究加工刀具座的锥型喇叭振幅越大越好,而影响其振幅的主要因素,系锥型喇叭的质量比。故要测试超声波振动辅助加工之良劣,本发明会先以田口实验法所规划的刀把参数(壁厚w、倒弧角h与槽长l)与l18直交表,对加工刀具座之锥型喇叭几何尺寸进行优化设计。接着,再以获得改良设计后之最佳超声波刀把,于超声波振动辅助扫追频系统下,验证最佳超声波刀把对钛合金材料加工之效果。至于本发明要探究之加工刀具座的锥型喇叭几何剖视图,如图6所示。
[0064]
在超声波振动辅助加工时,为得到最大的机械功率输出,超声波驱动单元在共振频率附近的电性特征是必须明了。而本发明使用已发展出的超声波振动辅助扫追频系统,系整合发展用户虚拟仪表扫频与追频平台,使其能对单一或不同的超声波辅助加工系统于各种不同的加工条件下,进行实时有效地在线扫频、频率追踪与补偿功能的整合。其方法系藉由labview的资料撷取、资料分析与结果呈现等功能,透过资料撷取卡,并配合信号产生器(signal generator)、功率放大器(power amplifier)与电流传感器(current sensor),
将作用在超声波振动辅助加工平台之电流讯号撷取出来,并转换成计算机可接受之数字信号,以利日后进行实际的监控、测量与数据分析。
[0065]
此外,本发明之超声波振动辅助加工实验已于四川雷刀精密机械公司的fv-580型3轴切削中心机(machining center)上进行且证实本发明之超声波刀把构造可增强超声波机械振动的振动幅度。fv-580型3轴切削中心机(machining center)之控制器为三菱meldas-64sm型,主轴最大输出马力为15hp,最高转速为8,000rpm。而测试用之切削动力计则为瑞士kistler公司出品的type 9273,为压电式(piezoelectric)的转换器(transducer),可同时测得三方向的分力(fx、fy与fz)及轴向扭力(mz),其原理为内部的高刚性石英测量单元受到外部负载作用时会放出电荷,而电荷量与所受外部负载大小成正比,透过电荷放大器(kistler type 5011),将其类比电压信号,经由类比/数字之ni-6110s适配卡转换成数字的铣削数值,并储存于计算机硬盘中,再配合铣削应用软件,以计算出超声波振动辅助铣削之平均切削力与扭矩。而本发明所使用的刀具材质为碳化钨铣刀,且其刀具直径介于6~10mm之间。至于本发明所使用的测试材料为钛合金(ti-6al-4v),其主要考量是钛合金是难加工材料,且其为航天、军事与汽车等产业所喜好使用之材料。除此之外,下列一些相关的仪器设备也将会被使用:光学显微镜为olympus bhm-311n型,扫描式电子显微镜(sem)为akahi sx-25型。
[0066]
藉由前述所揭露的设计,本发明具有以下的优点:
[0067]
本发明之超声波刀把构造可藉由挖空加工刀具座内部的一部分以形成至少一个空室并减少加工刀具座的重量,以增加超声波机械振动的振动幅度,从而提升超声波刀把的加工性能。
[0068]
以上所述实施例仅表达了本发明的几种实施方式,其描述较为具体和详细,但并不能因此而理解为对本发明专利范围的限制。应当指出的是,对于本领域的普通技术人员来说,在不脱离本发明构思的前提下,还可以做出若干变形和改进,这些都属于本发明的保护范围。因此,本发明专利的保护范围应以所附权利要求为准。