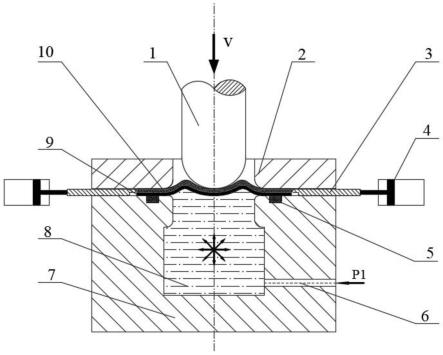
1.本发明涉及金属板材加工领域,适合提高大型曲面薄壁件成形质量的充液拉深工艺方法。
背景技术:2.由于航空航天及汽车领域中,对一些高端设备的零部件有着高精度,高轻量化的要求,如火箭油箱底部的曲面薄壁件,以及汽车覆盖件的获取都需要对高性能的铝合金、钛合金等进行精密的成形。但它们往往伴随着难变形、塑性差等缺点,充液拉深技术通过将传统的刚性凹模替换成柔性介质的软模,进而提高这些板料的贴模性、拉深比等成形性能。
3.在大型曲面薄壁件的充液拉深成型过程中,成形件的失稳开裂缺陷得到一定的抑制,但由于凸模相对来说有一定的锥度,使得板料悬空区的面积增大,在变形过程中悬空区的板料不存在厚向应力的束缚,无法抑制在变形过程中所产生的切向应力,进而产生明显的起皱缺陷。通过上层辅助板料的引入,可以为下层成形板料的悬空区提供一定的厚向应力以及板间的有益摩擦,并配合较大的液室压力,可以进一步抑制悬空区的起皱。并在此基础上配合预胀工艺,通过形成的软拉延筋减少板料的切向应力可以明显改善悬空区板料的起皱趋势,但同时也增加了板料径向拉力,从而导致板料在整体上一定程度的减薄。由此可见,在保证薄壁曲面零件成形精度的同时,进一步提高它的壁厚显得尤为重要。
技术实现要素:4.针对现有技术的以上缺陷,本发明提出了一种提高大型曲面薄壁件成形质量的充液拉深工艺方法,通过促进上层辅助板料优先变形,从而更好的带动下层板料进行变形。
5.为实现上述目的,本发明提出了一种提高大型曲面薄壁件成形质量的充液拉深工艺方法,其包括如下步骤:
6.s1将预成形的板料和辅助成形板料先后放置在凹模上方,并与凹模保持同轴状态,然后通过通道将液室内的液体加到与下层板料齐平的位置,紧接着合模,将凸模下行至与上层板料齐平的位置并保持不动。
7.s2通过液压泵对液室加压,进行板料预胀的工序。同时通过异型阶梯顶杆对上层板料持续施加固定的径向压力,使其充分贴模,从而提高下层板的贴模性。
8.s3加载合理的凹模液压的同时,凸模下行进行充液拉深,在此阶段,在较大的液室压力作用下,两层板料紧紧的贴合在一起,上层板料对下层板料有一定的支撑作用,从而减少了曲面零件悬空区起皱的程度,同时异型阶梯顶杆对上层板料持续施加固定的径向压力直至变形结束,通过促进上层板料充分变形,从而更好的带动下层板料均匀变形,进一步提高薄壁件底部和悬空区的壁厚值。
9.s4该充液拉深成形工序完成,卸压开模取件。
10.所述步骤s2具体为:通过外接的液压泵将液室压力加到一定的压力后,保压一段
时间,使双层板料反胀贴模,与此同时,液压缸对异型顶杆施加推力,进而对上层板料产生径向压力,促使上层板相对下层板提前变形并充分贴模。上层板的提前变形通过板间摩擦力带动了下层板的变形,使得成形板料在预胀阶段变形充分。
11.所述步骤s3具体为:继预胀液室压力后充液拉深阶段设定单调递增的液室加载路径直至成形结束,此阶段的径向压力与预胀时相同。通过对上层板设置不同的径向压力,对比最终成形件的贴模性和壁厚分布,并选择最优的径向压力对板料进行成形。
12.总体而言,通过本发明所提供的以上技术方案与现有技术相比,主要具有以下的技术优点:
13.1.由于双层板料的存在,增大了板料的相对厚度,可以采用较高的液室的压力,改善零件的贴模性。同时上层板料相对下层板料较厚,可以给成形板料的悬空区一定的支撑力,从而大大降低了下层板料的起皱低风险。
14.2.在双层板充液拉深之前,进行预胀处理,形成的软拉延筋可以减小板料悬空区的切向应力,进一步缓解悬空区的起皱问题,同时增大的径向拉应力可以进一步带动法兰区的板料向中心流动。
15.3.采用阶梯异型顶杆单独对上层板料进行径向加压,促进其相对下层板料提前变形,在上层板料提前变成形的同时,下层板料在上层板料的有益摩擦力的带动下充分变形,进一步提高成形件在底部和悬空区的壁厚值。
附图说明
16.图1为具有异型阶梯顶杆对上层板料径向加压的充液拉深成形装置;
17.图2为本发明实施例1的零件尺寸及形状;
18.图3为本发明实施例1的最优液室压力加载曲线图;
19.图4为本发明实施例1的成形零件的轮廓对比图;
20.图5为本发明实施例1的成形零件的壁厚分布图;
具体实施方式
21.为了使技术方案和优点更加清楚明白,以下结合具体实施例,并参照附图,对本发明进一步详细说明。
22.图1所述装置包括凸模(1)、压边圈(2)、凹模(7)、液室(8)、橡胶密封圈(5)、异型阶梯顶杆(3)和液压缸(4)。其中异型阶梯顶杆(3)一端连接液压缸(4),另一端被进行阶梯处理,其中上层要比下层突出一块,以便更好地接触上层板料。如图1所示其围绕板料进行周向布置,液压缸(4)通过活塞对顶杆施加压力。
23.s1将预成形的板料和辅助成形板料先后放置在凹模上方,并与凹模保持同轴状态,然后通过通道(6)将液室内的液体加到与下层板料齐平的位置,紧接着合模,将凸模下行至与上层板料齐平的位置并保持不动。
24.s2通过液压泵对液室加压,进行板料预胀的工序。同时通过异型阶梯顶杆(3)对上层辅板持续施加固定的径向压力,使其充分贴模,从而提高下层板的贴模性。
25.s3加载合理的凹模液压的同时,凸模下行进行充液拉深,在此阶段,在较大的液室压力作用下,两层板料紧紧的贴合在一起,上层板料对下层板料有一定的支撑作用,从而减
少了曲面零件悬空区起皱的程度,同时异型阶梯顶杆(3)对上层板料持续施加固定的径向压力直至变形结束,通过促进上层板料充分变形,从而更好的带动下层板料均匀变形,控制破裂,进一步提高薄壁件底部和悬空区的壁厚值。
26.s4该充液拉深成形工序完成,卸压开模取件。
27.实施例1
28.本实施例将该方法应用到薄壁半球形零件的双层板料充液拉深研究中,具体的零件尺寸如图2所示。成形板料材料选择的是aa6061-t6铝合金,根据零件尺寸,选用170mm的圆形坯料,板料厚度为0.5mm。上层板料的选择为1cr18ni9ti不锈钢,厚度为1.5mm,两层板间的摩擦系数默认为0.1。应用有限元软件的网格划分工具对曲面网格进行划分,并对此方法的成形过程进行模拟分析来验证其过程的可靠性。
29.实施步骤如下
30.1.通过三维建模软件建立薄壁半球形零件的模型,并导入到有限元软件中,选用多组液室压力加载曲线进行拉深成形仿真,分析下层板料的成形情况,确定成形板料的最佳预胀压力为6mpa,预胀时间为0.1秒,以及其最佳的液室压力加载曲线如图3。
31.2.在此基础上,在有限元软件中对上层板料在成形过程中持续施加固定的径向压力,并分别设置0mpa、7mpa、15mpa三个径向压力进行模拟分析,图4、图5分别是成行零件的零件轮廓图和壁厚分布图,通过对比可以发现随着径向压力的增加,零件的贴模性没有明显变化,但球底和悬空区的板料厚度出现稳步上升的趋势,零件的成形质量得到了提高。
技术特征:1.一种提高大型曲面薄壁件成形质量的充液拉深工艺手法,所述方法的实现过程如下:所述装置包括凸模(1)、压边圈(2)、凹模(7)、液室(8)、橡胶密封圈(5)、异型阶梯顶杆(3)和液压缸(4)。其中异型阶梯顶杆(3)一端连接液压缸(4),另一端被进行阶梯处理,其中上层要比下层突出一块,以便更好地接触上层板料。如图1所示。异型阶梯杆围绕板料进行周向布置,液压缸(4)通过活塞对异型阶梯顶杆施加压力。s1将预成形的板料和辅助成形板料先后放置在凹模上方,并与凹模保持同轴状态,然后通过通道(6)将液室内的液体加到与下层板料齐平的位置,紧接着合模,将凸模下行至与上层板料齐平的位置并保持不动。s2通过液压泵对液室加压,进行板料预胀的工序。同时通过异型顶杆(3)对上层板料持续施加固定的径向压力,使其充分贴膜,从而提高下层板的贴模性。s3加载合理的凹模液压的同时,凸模下行进行充液拉深,在此阶段,在较大的液室压力作用下,两层板料紧紧的贴合在一起,上层板料对下层板料有一定的支撑作用,从而减少了曲面零件悬空区起皱的程度,同时异型顶杆(3)对上层板料持续施加固定的径向压力直至变形结束,通过促进上层板料充分变形,从而更好的带动下层板料均匀变形,控制破裂,进一步提高薄壁件底部和悬空区的壁厚值。s4该充液拉深成形工序完成,卸压开模取件。2.根据权利要求1所述的一种提高大型曲面薄壁件成形质量的充液拉深工艺方法,其特征在于,所述步骤s1具体为:本工艺方法采用定间隙的方式固定板料,即压边圈与凹模的距离固定为上层板料厚度与下层板料厚度之和的1.1倍,其中下层板料与凹模之间设置一个橡胶密封圈,防止液体从液室(8)内流出。3.根据权利要求1所述的一种提高大型曲面薄壁件成形质量的充液拉深工艺方法,其特征在于异型阶梯顶杆促使上层辅板优先变形,所述步骤s2具体为:通过外接的液压泵将液室压力加到一定的压力后,保压一段时间,使双层板料反胀贴模,与此同时,压力缸(4)对异型阶梯顶杆施加推力,进而对上层辅板施加恒定的径向压力,促使上层板相对下层板提前变形并充分贴模。上层板的提前变形通过板间摩擦力带动了下层板的变形,使得成形板料在反胀阶段变形充分。4.根据权利要求1所述的一种提高大型曲面薄壁件成形质量的充液拉深工艺方法,其特征在于,所述步骤s3具体为:在此阶段继预胀液室压力后设定单调递增的液室加载路径直至成形结束,此阶段的径向压力与预胀时相同。通过对上层板设置不同的恒定径向压力,对比最终成形件的贴模性和壁厚分布,并选择最优的径向压力对板料进行成形。
技术总结本发明涉及薄壁曲面零件充液拉深成形领域,采用增加辅板来辅助下层板料成形,并对上层辅板施加径向应力的方式促使其优先变形,从而提高薄壁件成形质量。将预成形的板料和辅助成形板料先后放置在凹模上方,将凸模下行至与上层板齐平的位置并保持不动,施加液压进行板料的预胀工序,继预胀的压力值后加载合理的液室压力,与此同时凸模下行进行充液拉深工序,并在这两个工序期间通过异型阶梯顶杆对上层板料施加固定的径向压力。从而通过上层板料的辅助支撑作用,以及预胀阶段形成的软拉延筋对板料切向应力的抑制,可以显著降低板料悬空区失稳起皱的风险。再加上辅助板料在径向压力下提前变形,可以更好的带动下层板料均匀成形,提高板料的成形质量。提高板料的成形质量。提高板料的成形质量。
技术研发人员:刘晓晶 张智贺 张广禹 刘金星
受保护的技术使用者:哈尔滨理工大学
技术研发日:2022.06.06
技术公布日:2022/8/30