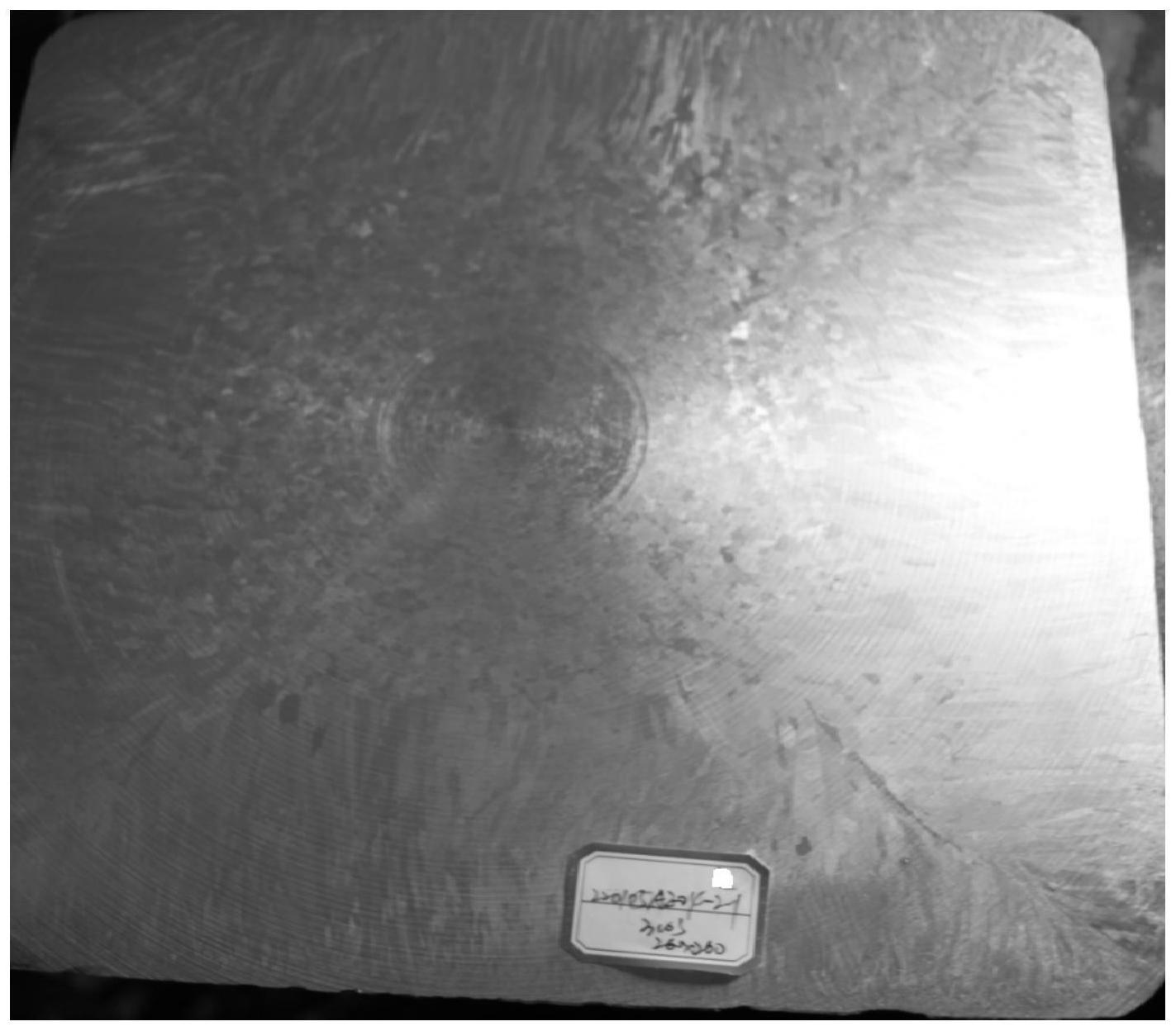
一种310s耐热不锈钢管坯的生产方法
技术领域
1.本发明属于冶金行业的钢铁冶炼技术领域,具体涉及一种大规格310s耐热不锈钢管坯的生产方法。
背景技术:2.310s(0cr25ni20)耐热不锈钢是高铬镍奥氏体不锈钢(典型成分%:0.05c、0.70si、0.95mn、0.025p、0.006s、24.5cr、19.3ni),在氧化介质中具有优良的耐蚀性能,同时具有良好的高温力学性能,因此它既可以用于耐蚀部件又可以用于高温部件。
3.现有技术制备310s(0cr25ni20)耐热不锈钢的大规格管坯(φ80~120)过程中,由于310s(0cr25ni20)耐热不锈钢高铬镍的特点,导致凝固过程传热慢、收缩量大、偏析严重,如果用传统小方坯(≤180方mm)连铸-连轧工艺生产大规格管坯(φ80~120),连铸坯的中心缩孔、中心偏析等凝固缺陷遗传到轧材上,会导致管坯的中心质量缺陷。而相比连铸,模铸钢锭由于尺寸比较大,钢锭到管坯的压缩比较大,中心缩孔、疏松等缺陷能够在锻造及轧制过程中得到焊合。同时,模铸钢锭是经过多火次锻造及轧制成型、高温均质化比较充分,凝固偏析也会在热加工过程中大大的减轻。因此,为保证质量,市面上大规格(φ80~120)310s(0cr25ni20)耐热不锈钢管坯多是通过模铸钢锭-锻造开坯-轧制工艺进行生产。但相比于连铸-连轧工艺,模铸钢锭-锻造开坯-轧制工艺的成材率低15%以上,且吨钢加工费用也高出2000元以上,造成高额的经济成本损耗。因此,开发一种工艺难度较小、成材率高,且产品质量稳定的大方坯连铸-连轧工艺生产大规格(φ80~120)310s耐热不锈钢管坯生产方法是本领域亟待解决的技术难题。
技术实现要素:4.本发明的目的在于解决现有技术中目前模铸工艺生产大规格(φ80~120)310s(0cr25ni20)耐热不锈钢管坯成材率低、成本高,小方坯连铸-连轧工艺生产大规格(φ80~120)310s(0cr25ni20)耐热不锈钢管坯产品质量无法保证的问题,提供一种工艺难度较小、成材率高、产品质量稳定的大方坯连铸-连轧工艺生产大规格(φ80~120)310s耐热不锈钢管坯生产方法。
5.本发明解决其技术问题所采用的技术方案是:
6.一种大规格310s耐热不锈钢管坯的生产方法,所述的方法为采用大方坯连铸得到260mm*260mm的连铸坯后,进行轧制得到φ80~120规格的310s耐热不锈钢管坯。
7.优选的,所述生产方法具体包括如下步骤:
8.(1)原料经电弧炉初炼、aod炉精炼和lf炉精炼后得到钢水,经方坯连铸机连铸得到260mm*260mm的连铸坯;其中,连铸中间包钢水过热度控制在20~40℃;连铸过程结晶器采用电磁搅拌,并采用末端电磁搅拌;
9.(2)连铸坯进行1150~1250℃加热后,经850初轧机开坯得到180mm*180mm中间坯,中间坯热送至750/650/550连轧机组进行轧制得到310s耐热不锈钢管坯;其中,850初轧机
开坯道次不大于15道次,开坯压下量为40~80mm。
10.通过采用上述技术方案,本发明创造性的采用大方坯连铸(260mm*260mm连铸坯)替代模铸钢锭,保证了大规格(φ80~120)310s(0cr25ni20)耐热不锈钢管坯的大压缩比轧制,压缩比不低于6,保证了中心缩孔能够焊合。能够实现大规模连续制备目标310s耐热不锈钢管坯的同时,保证其较高的成材率和稳定并优秀的产品质量。
11.优选的,所述步骤(1)中电弧炉、aod炉、lf炉的容量均为30-50吨。通过采用所述技术方案,能够大批量制备得到目标规格的大方坯。但更小规格的电弧炉、aod炉、lf炉也能够得到目标规格的大方坯,同时,实际生产过程中还可以选择更大规格的电弧炉、aod炉、lf炉等设备,以实现更大规模的方坯制备。
12.优选的,所述步骤(1)中连铸目标拉速0.8
±
0.1m/min。通过采用所述技术方案,可以进一步保证连铸坯表面质量和内部质量,防止拉速过快导致液相穴过长、连铸坯中心质量恶化,拉速过慢结晶器保护渣熔化不好、恶化表面质量的问题。
13.优选的,所述步骤(1)中连铸结晶器的电磁搅拌电流为500
±
20a、频率为3hz。通过采用所述技术方案,可以提高中心等轴晶率,提高连铸坯中心质量。进一步防止电流过大导致结晶器内卷渣,电流过小搅拌效果不佳的现象。
14.优选的,所述步骤(1)中末端电磁搅拌的位置选择为铸坯凝固率70%-8%左右的区域,更优选为离结晶器出口9m,更优选的,末端电磁搅拌电流为600
±
20a、频率为8hz。通过采用所述技术方案,并配合稳定的拉速,可以进一步减少制备得到的连铸坯的中心偏析、疏松、缩孔等缺陷,进一步保证连铸坯后续进行轧制过程的稳定性以及轧制后的产品质量。
15.优选的,所述步骤(2)中连铸坯于步进式连续式加热炉中进行加热,在炉时间为3-6h。通过采用所述技术方案,可以进一步确保连铸坯加热均匀,为轧制提供塑性优良的坯料。
16.优选的,所述步骤(2)中中间坯热送温度不低于1050℃。以进一步减少或避免温度低造成的塑性不好、容易开裂的问题。
17.优选的,所述步骤(2)中850初轧机与750/650/550连轧机组布置在一条直线上;850初轧机和750/650/550连轧机组之间通过传送辊道快速的移动钢坯,移动速度不低于5m/s,更优选移动速度为6-8m/s;以保证进入750/650/550连轧机组时中间坯温度不低于1050℃,并实现大方坯到管坯的一火成材,进一步提高成材率,降低生产成本。
18.与现有技术相比,本发明的有益效果是:
19.(1)用大方坯连铸(260方)替代模铸钢锭,保证了大规格(φ80~120)310s(0cr25ni20)耐热不锈钢管坯的大压缩比轧制,保证了中心缩孔能够焊合。
20.(2)连铸大方坯采用低过热度浇注、结晶器电磁搅拌、末端电磁搅拌等技术,中心等轴晶比例达到60%以上,减少中心偏析、疏松、缩孔等缺陷(图1),保证了大方坯轧制成大规格(φ80~120)管坯后产品质量与模铸钢锭-锻造开坯-轧制工艺生产出来的产品相当,符合310s不锈钢产品的性能要求。
21.(3)本发明用大方坯在850初轧机轧制开坯后,热送到750/650/550连轧机组连轧成棒材,实现了大方坯到管坯的一火成材,比传统钢锭冶炼+锻造开坯+连轧成材的工艺相比,成材率提高10~15%,生产成本降低30%以上,具有极高的经济效益,适用于310s不锈钢的工业化大规模生产。
附图说明
22.图1为260mm*260mm的310s连铸坯的低倍图。
具体实施方式
23.下面通过具体实施例,并结合附图,对本发明的技术方案作进一步的具体说明。
24.本发明提供一种大规格310s耐热不锈钢管坯的生产方法,所述的方法为采用大方坯连铸得到260mm*260mm(260方mm)的连铸坯后,进行轧制得到φ80~120规格的310s耐热不锈钢管坯,具体包括如下步骤:
25.第一步:电弧炉(eaf)出炼
→
aod精炼
→
lf炉精炼
→
大方坯连铸
26.(1)在30~50吨电弧炉中原料进行钢液初炼,经相应吨位的aod精炼、lf炉精炼后钢水成分及温度达到目标要求后,经方坯连铸机生产出260方mm的连铸坯;
27.(2)连铸中间包钢水过热度控制在20~40℃;
28.(3)连铸目标拉速0.8
±
0.1m/min;
29.(4)开启连铸结晶器电磁搅拌,电磁搅拌电流为500
±
20a、频率为3hz;
30.(5)采用末端电磁搅拌,末端电磁搅拌位置选择为离结晶器出口9m,铸坯凝固率70%-80%左右的区域,电磁搅拌电流为600
±
20a、频率为8hz;
31.第二步:连铸大方坯加热
→
850初轧机开坯
→
750/650/550连轧机热连轧至成品
32.(6)连铸大方坯装入步进式连续式加热炉加热,加热温度为1150~1250℃,在炉时间为3~6小时;
33.(7)260方mm大方坯在850初轧机开坯成180方mm中间坯;
34.(8)上述中间坯直接热送至750/650/550连轧机组热连轧至成品;
35.(9)上述850初轧机开坯道次不大于15道次,用大压下量轧制,开坯压下量(δh)为40~80mm,中间坯热送温度不低于1050℃;
36.(10)上述850初轧机和750/650/550连轧机组布置在一条直线上,850初轧机和750/650/550连轧机组之间通过传送辊道快速的移动钢坯。
37.本发明中,所述的原料为生产310s耐热不锈钢管坯的常规原料,电弧炉初炼、aod炉精炼和lf炉精炼的相关方法及工艺参数为生产310s耐热不锈钢管坯的常规工艺。以下通过具体实施例对本发明的技术内容和技术效果做进一步体现,但需要注意的是,以下实施例不应对本发明的技术方案构成限制。
38.实施例1:
39.本实施例生产的是φ110mm规格310s耐热不锈钢管坯,具体步骤如下:
40.电弧炉根据目标成分要求配入相应的310s同钢种返回料及高碳铬铁、镍板、电解锰等合金进行钢水初炼。初炼的钢水兑入aod进行脱碳、脱硫、脱氧、调整成分后出钢。aod出钢后钢水在lf炉升温、去夹杂、成分微调,钢水达到合适的温度和目标成分后到大方坯连铸机浇注成260方mm连铸坯,连铸工艺如下控制:
41.(1)连铸中间包钢水过热度控制在30~40℃
42.(2)连铸拉速0.8m/min
43.(3)开启连铸结晶器电磁搅拌,电磁搅拌电流为500a、频率为3hz
44.(4)采用末端电磁搅拌,末端电磁搅拌位置选择为离结晶器出口9m,电磁搅拌电流
为600a、频率为8hz;制备得到的连铸坯见附图1,中心等轴晶比例达到60%以上,减少中心偏析、疏松、缩孔等缺陷;
45.上述260方连铸大方坯加热
→
850初轧机开坯
→
750/650/550连轧机热连轧至成品,具体工艺如下:
46.(1)连铸大方坯装入步进式连续式加热炉加热,加热温度为1200℃,在炉时间为4小时
47.(2)连铸大方坯在850初轧机开坯成180方mm中间坯
48.(3)上述中间坯直接热送至750/650/550连轧机组热连轧至φ110mm管坯
49.(4)上述850初轧机开坯道次12道次,用大压下量轧制,开坯压下量(δh)为60mm,中间坯热送温度为1100℃
50.(5)上述850初轧机和750/650/550连轧机组布置在一条直线上,850初轧机和750/650/550连轧机组之间通过传送辊道8m/s移动钢坯。
51.本实施例制备得到的φ110mm规格310s耐热不锈钢管坯,其化学成分如表1所示、低倍组织如表2所示、高温抗氧化性能如表3所示。
52.表1本实施例310s化学成分
[0053][0054]
注:余量为fe和不可避免的杂质。
[0055]
表2本实施例管坯低倍组织
[0056][0057]
实施例2
[0058]
本实施例生产的是φ120mm规格310s耐热不锈钢管坯,具体步骤如下:
[0059]
电弧炉根据目标成分要求配入相应的310s同钢种返回料及高碳铬铁、镍板、电解锰等合金进行钢水初炼。初炼的钢水兑入aod进行脱碳、脱硫、脱氧、调整成分后出钢。aod出钢后钢水在lf炉升温、去夹杂、成分微调,钢水达到合适的温度和目标成分后到大方坯连铸机浇注成260方mm连铸坯,连铸工艺如下控制:
[0060]
(1)连铸中间包钢水过热度控制在30~40℃
[0061]
(2)连铸拉速0.8m/min
[0062]
(3)开启连铸结晶器电磁搅拌,电磁搅拌电流为500a、频率为3hz
[0063]
(4)采用末端电磁搅拌,末端电磁搅拌位置选择为离结晶器出口9m,电磁搅拌电流
为600a、频率为8hz;制备得到的连铸坯中心等轴晶比例达到60%以上,减少中心偏析、疏松、缩孔等缺陷;
[0064]
上述260方连铸大方坯加热
→
850初轧机开坯
→
750/650/550连轧机热连轧至成品,具体工艺如下:
[0065]
(1)连铸大方坯装入步进式连续式加热炉加热,加热温度为1200℃,在炉时间为4小时
[0066]
(2)连铸大方坯在850初轧机开坯成180方mm中间坯
[0067]
(3)上述中间坯直接热送至750/650/550连轧机组热连轧至φ120mm管坯
[0068]
(4)上述850初轧机开坯道次12道次,用大压下量轧制,开坯压下量(δh)为60mm,中间坯热送温度为1080℃
[0069]
(5)上述850初轧机和750/650/550连轧机组布置在一条直线上,850初轧机和750/650/550连轧机组之间通过传送辊道7m/s动钢坯。
[0070]
本实施例制备得到的φ120mm规格310s耐热不锈钢管坯,其化学成分如表1所示、低倍组织如表2所示、高温抗氧化性能如表3所示。
[0071]
表4本实施例310s化学成分
[0072][0073]
表6本实施例310s管坯高温抗氧化性能
[0074][0075]
对比例:
[0076]
本对比例生产的是φ120mm规格310s耐热不锈钢管坯,采用传统生产方式模铸钢锭-锻造开坯-轧制工艺进行生产,具体步骤如下:
[0077]
电弧炉根据目标成分要求配入相应的310s同钢种返回料及高碳铬铁,镍板,电解锰等合金进行钢水初炼。初炼的钢水兑入aod进行脱碳、脱硫、脱氧、调整成分后出钢。aod出钢后钢水在lf炉升温、去夹杂、成分微调,钢水达到合适的温度和目标成分后浇注成17吋钢锭。
[0078]
上述17吋钢锭加热
→
锻造开坯成200*200mm中间坯
→
中间坯修磨
→
中间坯加热
→
热连轧至φ120mm。
[0079]
本对比例制备得到的φ100mm规格310s耐热不锈钢管坯,其化学成分如表4所示、低倍组织如表5所示、高温抗氧化性能如表6所示。
[0080]
表4本例310s化学成分
[0081][0082]
注:余量为fe和不可避免的杂质。
[0083]
表5本例管坯低倍组织
[0084][0085]
表6本例310s管坯高温抗氧化性能
[0086][0087]
将本技术实施例与对比例的310s耐热不锈钢管坯的传统制备工艺进行经济指标对比,结果见表7:
[0088]
表7传统工艺和本发明技术经济指标对照表
[0089][0090][0091]
由表中数据可知,本发明所提供的制备工艺能够进一步提高310s耐热不锈钢管坯的成材率,并能够大规模大批量的制备得到产品质量稳定的310s耐热不锈钢管坯,符合310s耐热不锈钢的相关性能要求,同时进一步降低了生产成本,具有较高的经济效益,非常适用于310s耐热不锈钢管坯的工业化大规模生产制备。
[0092]
以上所述的实施例只是本发明的较佳方案,并非对本发明作任何形式上的限制,在不超出权利要求所记载的技术方案的前提下还有其它的变体及改型。