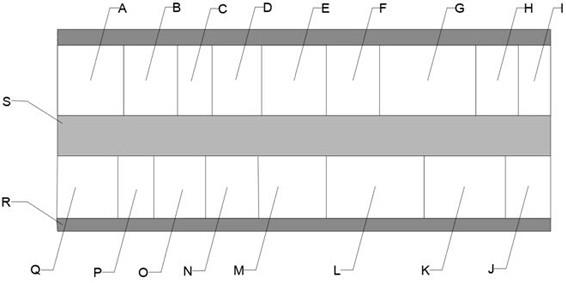
1.本实用新型属于城市轨道交通技术领域,具体涉及一种智能化轮对检修整体布局结构。
背景技术:2.转向架是城轨车辆中一个重要组成部分,车辆的自重和载重通过转向架本身传递到轮轨接触点,从而继续向下传递。城轨车辆转向架分为动车转向架和拖车转向架,轮对又是转向架必不可少的部件,轮对分为动车轮对和拖车轮对,主要区别在于动车轮对上除车轮、车轴以外,还安装有齿轮箱。一般情况下,轮对(含齿轮箱)大修周期为120万公里运行里程或10年运行期限。城轨车辆大修修程时,需要将车轮、车轴退卸,车轮更新,齿轮箱进行拆解,检修合格后重新进行组装,车轮、车轴压装。因此,大修时,轮对(含齿轮箱)须整体进行分解、检修。
3.对于车轮、车轴机加工部分,制造厂家往往采用自动化生产流水线形式,通过机械臂抓取车轮、车轴,再经由流水线输送滚筒传送到机加工工位。这种布局结构投资金额巨高,适用于生产任务重且市场需求稳定的大规模企业,不适用于只做城轨车辆架修或大修的企业,相对来说,市场需求不稳定,生产任务较集中,易出现空窗期。目前,螺栓紧固较前沿的工艺方法是使用智能扭矩设备配套智能提升装置,汽车行业减速箱力矩紧固率先采用该工艺,相比较而言,齿轮箱制造厂家以及主机厂力矩紧固方式落后,多为人工紧固、人工核验,效率低且容易出现过扭矩、漏检的现象。
4.北京新联铁科技股份有限公司早在2011年公布了一种轨道交通机车车辆轮对组装检修系统集成方法(专利公开号cn 102951127 a),主要讲述的是动车组轮对检修系统的工艺方法,并非检修现场整体布局方案;主要涉及对象为轮对(不含齿轮箱)、轴承轴箱,无齿轮箱的检修系统及其布局方案;该方法中未介绍各系统使用的设备及其智能化方式。
5.中车青岛四方车辆研究所有限公司在2021年公布了一种城轨车辆转向架检修系统(专利公开号cn 114104631 a),其中描述的轮对大修线主要体现的是自动化方向而非科技革新中的智能化、数字化方向,利用输送线的形式贯穿轮对大修线,该方式投入成本高、占地面积大,适用于生产任务繁重且市场需求稳定的大规模企业,而不适用于中小型企业或者只做轨道交通车辆架修或者大修的企业。
6.目前城轨车辆轮对检修生产线不论是检修作业还是运输,主要都是通过人工实现,配套设备自动化、数字化、智能化程度低,主要有以下缺点:
7.1)智能化程度低,进料、加工、转运、紧固、校核等多以操作人员手动实现,运输方式多为天车吊运,无法实现自动运输,且作业工单多为人工记录、填写、核对;
8.2)检修成本高,操作人员的数量决定了检修成本,传统制造业的模式需要大量的人力,且城轨车辆检修市场不稳定,经常出现空窗期,无疑是对人力、物力、财力的浪费;
9.3)检修效率低,检修设备自动化、数字化、智能化程度低,增加了零部件重复流转造成作业时间的浪费,纸质工单的填写也同样造成作业时间的加长,设备的智能化程度低
导致检修工步多;
10.4)检修质量不可控,人工作业大多受操作人员的责任意识影响,零部件来回流转增大磕碰伤的概率,设备智能化程度低无自动校核功能、操作稳定性差,工单人工填写容易出现错写、漏写的情况等。
技术实现要素:11.针对现有技术中存在的问题,本实用新型设计的目的在于提供一种智能化轮对检修整体布局结构,该整体布局结构利用当下前沿的科技方法,结合城轨车辆大修时的实际情况,精准把握检修需求,定位智能化、数字化轮对检修生产线,该检修生产线针对中小型企业的经营模式,打造城轨车辆轮对检修生产线数字化工厂,解决投入成本高、占地面积大的现状,利用智能化设备、信息化管理系统,打造具有针对性的智能化、信息化、数字化城轨车辆轮对大修体系;智能化设备功能的稳定性得到充分地展示,减少作业过程中因人为因素造成的质量不可控要素。智能化设备具有工件检测功能,能提前识别质量问题,提高产品质量的稳定性,减少返修、返工的概率。智能化设备能够将设备情况、工件状态、尺寸记录等信息传送到终端控制系统,进行筛选、保存、导出等;现场转运采用潜伏式agv机器人,实现无人化运输、流转,减少人工转运,降低劳动强度,缩短作业时间,避免工件造成磕碰。智能化设备测量工件后,自动传输数据到终端,替代人工手动记录、填写工单,提高工作效率;智能化设备能够解决现场长期无法破除的弊端,诸如可以利用智能扭矩设备感应装置上的传感器克服螺栓紧固过程中出现过扭矩的现象,可以利用物料管理系统实时监控物料的信息,有序进厂,杜绝浪费,排查质保期限等。
12.本实用新型通过以下技术方案加以实现:
13.一种智能化轮对检修整体布局结构,该结构包括由物料存放区和检修作业区组成的作业流程、贯穿整个作业流程的物流运输通道、沿作业流程两侧设置的员工通道,物料存放区包括待检修产品存放区、待压装轮对存放区、报废产品存放区、智能立体物流中心及功能预留区;检修作业区包括轮对清洗区、轮对退卸区、超声波清洗区、齿轮箱分解检修区、磁粉探伤区、齿轮箱组装区、齿轮箱试验区、车轮加工区、轮对压装区、轮对交验区、轮对油漆区。
14.进一步地,所述轮对清洗区配制有激光清洗机,用于对车轴进行除漆除锈作业;轮对退卸区设置有轮对退卸机,用于将车轮和车轴进行注油退卸分解。
15.进一步地,所述齿轮箱分解检修区安装有齿轮箱分解检修作业平台及框架式行车,所述齿轮箱分解检修作业平台用于对齿轮箱进行分解、检修,框架式行车用于轮对及齿轮箱在该区域内的转运工作;超声波清洗区安装有超声波清洗机,用于齿轮箱分解后,其零部件的粗洗、精洗、漂洗及油浸。
16.进一步地,所述磁粉探伤区包括磁粉探伤机,用于车轴、大齿轮、小齿轮的探伤作业;齿轮箱组装区安装有智能提升装置和智能扭矩设备,所述智能提升装置用于齿轮箱零部件的移动和组装定位;所述智能扭矩设备用于齿轮箱组装时螺栓紧固作业;
17.进一步地,所述齿轮箱试验区安装有齿轮箱跑合试验机,用于齿轮箱组装完成后的跑合试验,所述齿轮箱跑合试验机集成了齿轮箱油洗机,用于齿轮箱组装完成后内部清洗作业;所述车轮加工区安装有数控立式车床,用于对新制车轮进行轮毂孔机加工作业。
18.进一步地,所述轮对压装区安装有轮对压装机,用于对车轮、车轴进行组装作业;所述轮对交验区用于轮对组装后的尺寸检查、电阻测试,以及轮对检查合格后的存放;所述轮对油漆区配置有轮对油漆间,所述轮对油漆间内安装有自动喷涂装置、空气过滤循环系统及干燥系统,用于车轴的油漆及烘干作业。
19.进一步地,所述待压装轮对存放区,用于存放预压装的车轮和车轴,并在轮对压装前对其进行预组装;所述智能立体物流中心配置有叉车式agv机器人,结合二维码管理系统将物料有条不紊的调取出来。
20.进一步地,该整体布局结构还包括动平衡试验区,所述动平衡试验区配置有轮对动平衡试验机,用于检测轮对动不平衡值。
21.本实用新型的整体布局结构,打破了现有技术中城轨车辆转向架轮对检修系统传统制造业的模式,解决了检修流程混乱、作业工序重复、劳动力浪费、检修质量不稳定、工作效率低下、信息不共享、安全隐患众多等问题。
附图说明
22.图1为本实用新型布局示意图;
23.图2为本实用新型整体布局结构示意图;
24.图3为本实用新型轮对检修工艺流程图;
25.图中,a-待检修产品存放区、b-轮对清洗区、b01-激光清洗机、c-轮对退卸区、c01-轮对退卸区、d-齿轮箱分解区、d01-齿轮箱分解检修作业平台、d02-框架式行车、e-超声波清洗区、e01-超声波清洗机、f-磁粉探伤区、f01-磁粉探伤机、g-齿轮箱组装区、g01-智能扭矩设备、g02-智能提升装置、h-功能预留区、i-报废产品存放区、j-轮对油漆区、j01-轮对油漆间、k-齿轮箱试验区、k01-齿轮箱跑合试验机、l-智能立体物流中心、l01-叉车式agv机器人、m-车轮加工区、m01-数控立式车床、n-待压装轮对存放区、o-轮对压装区、o01-轮对压装机、p-动平衡试验区、p01-轮对动平衡试验机、q-轮对交验区、r-员工通道、s-物流通道。
具体实施方式
26.以下结合说明书附图对本实用新型做进一步详细描述,以便更好地理解本技术方案。
27.如图1所示,本实用新型包括由物料存放区和检修作业区组成的作业流程、贯穿整个作业流程的物流运输通道、沿作业流程两侧设置的员工通道,物料存放区包括待检修产品存放区、待压装轮对存放区、报废产品存放区、智能立体物流中心及功能预留区;检修作业区包括轮对清洗区、轮对退卸区、超声波清洗区、齿轮箱分解检修区、磁粉探伤区、齿轮箱组装区、齿轮箱试验区、车轮加工区、轮对压装区、轮对交验区、轮对油漆区,整个作业流程采用流水线作业模式,杜绝了零部件来回流转造成质量不受控、工作效率低下的问题,本实用新型智能化轮对检修作业还具有自动化、信息化等功能,提高了检修质量,监管检修过程。
28.本实用新型轮对检修的整体布局依据计算机辅助制造系统建立物理实体虚拟模型,通过数字孪生技术,对工艺系统进行仿真,利用3d max或bim软件构建1:1的工厂虚拟空间,模拟工艺路线流程,进行产线布局分析、工位平衡分析、产能平衡分析、路径规划,对整
体工艺布局的合理性进行检验,及时发现整体布局规划中存在不合理的地方,并可对其进行反复修改、完善,利用数字化工艺规划系统,最终达到预期的效果。整体布局结构示意图见图2所示。
29.轮对检修工艺流程如图3所示,按照生产流水线的形式贯穿整个布局,避免零部件反复流转,造成检修场地混乱,管理复杂且效果甚微。待检修轮对进厂后,先存放在待检修产品存放区a,外观检查后进入轮对清洗区b,对车轴进行激光清洗,然后再到轮对退卸区c进行退轮处理,退卸后的车轴放置在轮对存放转运工装上,可进行车轴外观检查。动车车轴(带齿轮箱)进入齿轮箱分解区d,分解后的齿轮箱零部件进入超声波清洗区e即超声波清洗机内,清洗完后进入磁粉探伤区f,进行车轴(带大齿轮)、小齿轮的探伤作业。然后进入齿轮箱组装区g进行组装,齿轮箱分解、检修、组装整个区域内配置框架式行车、电动环链葫芦、智能提升装置配合完成作业流程。车轴完全分解后,须进入磁粉探伤区f进行探伤作业。齿轮箱组装完成后,进入齿轮箱试验区k进行跑合试验以及齿轮箱油洗作业。跑合试验结束后,车轴进入轮对油漆区j即轮对油漆间进行封闭式涂装作业。与此同时,新制车轮从智能立体物流中心l流转至车轮加工区m,对车轮轮毂孔进行机加工,完成加工的车轮和待压装的车轴存放至待压装轮对存放区n,随后被送往轮对压装区o进行组装,组装完成后送至动平衡试验区p,进行动不平衡测试。检测合格后,进入轮对交验区q检验,并完成配车。
30.整个布局的转运方式以潜伏式agv机器人智能转运为主,轮对放置于存放工装上,潜伏式agv机器人到达指定位置进行托举,接收指令后送至目的区域。齿轮箱分解区、磁粉探伤区、超声波清洗区、齿轮箱组装区安装框架式行车,通过电动环链葫芦方便进行局部反复多次的吊运,且适用于重量小、体积小的齿轮箱零部件。
31.整个布局转运方式还配置有天车,如发生紧急情况(潜伏式agv机器人集体故障等),可以用该转运方式替代,即转运应急方案,现场生产不至于瘫痪。另外,个别区域使用天车的吊运方式,能够增强安全系数,更加方便作业。
32.轮对清洗区b采用激光清洗机b01作业,该设备为自动化通过式结构,可自动去除车轴、防尘板座、车轮内外辐板的锈迹、油漆以及油污。能够根据轮对型式进行编程,自动判断轮对有无齿轮箱以及轴承轴箱装置,依据判断结果自动进行作业。通过式结构,通过驱动装置和上下料机构使轮对自动通过设备,大大减少人力成本。利用激光除锈、脱漆,不需要额外添加清洗液等介质,产生的烟尘会被烟尘净化系统实时吸取,对环境无污染。
33.轮对退卸区c采用轮对退卸机c01对轮对进行退轮处理,该设备采用双端活塞缸结构,机械弹性顶尖进行车轴中心孔自动定位功能。采用双侧油缸活动压头退卸方式,避免轮对掉头浪费作业时间,也降低了轮对退卸会带来二次伤害的风险。设备配备送料小车装置,在退卸过程中,不接触车轴即可完全独立进行退卸。并且轮对退卸机c01与激光清洗机b01两者的轨道相连接,轮对退卸机c01送料小车装置可进行180
°
旋转,从激光清洗机b01承接待退卸轮对,送至轮对退卸机作业。
34.超声波清洗区e配置超声波清洗机e01,对齿轮箱零部件进行粗洗、精洗、漂洗、烘干,该设备利用高于28khz的超声频率信号,通过换能器转换成高频机械振荡,传入到清洗液中。超声波在清洗液中疏密相间的向前辐射,使液体流动并产生大量的微小气泡,气泡的闭合形成超过1000个大气压的瞬间高压,连续不断产生的瞬间高压冲击物体表面,使杂质能够迅速剥落。
35.磁粉探伤区f配置有磁粉探伤机f01,该设备中大齿轮空中线圈复合磁化系统及升降装置在大齿轮复合磁化的过程中,工件上下料和伸缩线圈伸缩时线圈升降装置下降,不影响工件的上下料和伸缩线圈伸缩;小齿轮(车轴)周向磁化系统及电极箱移动系统、夹紧机构由周向磁化主变压器、左右周向电极、电极箱移动机构、电极夹紧、电流回路等组成,采用双气缸夹紧车轴、小齿轮;小齿轮(车轴)纵向磁化系统及线圈移动装置由纵向磁化主变压器、左右环形线圈、线圈移动装置、电流回路等组成,采用伸缩线圈串联,对线圈通电,进行纵向磁化,4只缠绕线圈被分成两组,由气缸带动进行自由伸缩;工件水平进出料系统及托起装置由上下料小车、运动机构、气缸、托起装置等组成。
36.磁粉探伤机f01作用对象是车轴和齿轮,一台设备同时实现车轴和齿轮的磁粉探伤,全方位复合磁化,行程范围大。车轴和小齿轮探伤周向磁化采用直接通电法,纵向磁化采用伸缩式线圈,该磁化方式有效地杜绝传统开口线圈磁化时易打火的现象,一次磁化即可发现工件表面及近表面各个方向的缺陷,探伤灵敏度高。大齿轮探伤不采用直接通电法磁化,节能减耗。且在探伤前后均能对工件进行清洗,结构新颖。
37.齿轮箱组装区g配置智能提升装置g02和智能扭矩设备g01。智能提升装置g02使用工业处理器控制的伺服驱动系统,既可以快速移动又可以慢速精准对位;操作手柄的内部集成光学传感器,只有当感知到操作人员到位后才允许装置移动;当发生断电时,智能提升装置g02的安全刹车主动闭锁,不会发生载荷坠落的现象;能够感知载荷的重量,如果超过额定载荷,将立即报警且不允许载荷被提升。
38.智能扭矩设备g01通过网络环境,使用集成控制器与上层系统连接,智能驱动,并提供数据分析,过程数据可以保存到本地的生产设备中,也可以保存到云端;使用“位置追踪”功能,可以确定车间内无线拧紧机的确切位置,基于该确定的位置和已知待拧紧部件的放置,可以自动选择和运行相关的拧紧程序,然后将单个拧紧结果精确地匹配到相应的螺栓。通过网络工具,提升生产效率和产品质量。
39.报废产品存放区i用于存放报废车轮、检修不合格车轴等报废产品,该区域位置设置在通道右侧,靠近厂房门口,便于报废物料的存储、装运。
40.齿轮箱组装区g和报废产品存放区i中间预留一块区域,用作检修功能预留区h,不同项目的城轨车辆轮对检修标准会存在细微的差异。为此,整体布局须充分考虑因功能需求、市场项目、科技发展等不同因素导致的区别,提前预留检修区域,预估风险,降低风险带来的不可抗力。
41.齿轮箱试验区k即对齿轮箱进行跑合试验,跑合试验台集成了齿轮箱油洗功能,二者合一,布局更优化,有效减少设备的占地面积,减少工步及转运次数,提高工作效率。跑合试验台由plc、工业控制计算机、变频器共同控制,温度探头和振动变送器采集到各个位置的数据传送到智能巡检仪,再通过智能巡检仪送往pc机,能够自主完成调节工况、测量、记录数据以及试验后的数据处理等一系列工作。
42.轮对油漆间j主要对车轴、齿轮箱进行涂装作业,配有自动喷涂装置和加热元器件,自动喷涂装置使得工件的漆膜厚度均匀,加热元器件能够使环境温度处于恒定状态,促进漆膜快速干燥,减少工件停滞等待的时间。另外,轮对油漆间送、回风系统和过滤及吸附系统,保证室内风场均匀,利用活性炭作为吸附剂,把气体中的有害物质成分在活性炭庞大的固相表面进行吸附浓缩,采用玻璃纤维过滤毡吸附漆雾,从而达到净化废气的目的。为便
于送、回风系统工作,综合考虑工艺路线和降本增效,轮对油漆间设计在厂房最边缘,靠近端墙的位置。
43.智能立体物流中心用来存放物料,包括新制车轮、新制车轴、紧固件以及其他备品备件等。智能立体物流中心通过计算机控制系统控制物料的自动存取作业,通过控制叉车式agv机器人实现物料的存、取,可实现无人化作业。物流中心立体化设计能有效减少占地面积,最大化利用存储空间。替代传统的人工模式对物料进行摆放、拿取、复位等,能有效节省劳动力,减轻劳动强度;点对点的方式能够有效降低出错的概率,并且加快货物的存取节奏,提高物料转运的作业效率。
44.车轮加工区m配置数控立式车床m01,对车轮进行机加工作业,可以用来对车轮轮毂孔、幅板以及轮缘进行车削作业。数控立式车床可根据西门子或法兰科系统进行编程,配置工件检测装置、刀具检测装置,能够实现自动校准、补偿、测量工件的功能,测量后的数据通过控制系统传送到数据管理系统,进行数据处理、存档、导出等操作。数控立式车床由底板、立柱、鞍座、主轴结构、二轴进给系统、排屑输送机、冷却装置、atc刀库、控制系统等组成。
45.加工后的车轮和检修后的车轴被送至轮对压装区o,进行车轮、车轴的组装。轮对压装区o配置轮对压装机o01,多功能专用设备,主要用于轨道车辆车轴、车轮、制动盘的压装、退卸、反压试验等,可满足不同压装、退卸工艺要求,包括冷压、冷退、注油压装、注油退卸等。设备采用双主油缸结构,可实现一次定位、不掉头作业。设备配有工件测量系统,自动测量压装后轮对尺寸,测量后的数据以及压装曲线等接口信息可接入检修中心管理系统,实现数据分析、存储、导出等功能。
46.轮对交验区用来轮对存放、校核、检测、配对,主要包括轮对尺寸测量、电阻测试、轮对配车等。综合实际检修经验考虑,该区域预留空间应足够大,检修后若因其他不可控因素导致轮对无法按照合同计划安排交车,则需要继续存放在轮对交验区,累积数量逐渐增多,需要的场地自然不容忽视。相对来说,待检修产品存放区占地面积可根据预估订单数量设计,临时存放,正常按照日检修能力进行流转即可,此区域轮对积压的可能性较小。
47.二维码物料管理系统贯穿整个工艺布局,物料(包括待检修车轴、齿轮箱)入库时会被粘贴二维码或条形码,通过扫码枪将基础信息录入系统,包含物料编码、名称、制造日期、序列号、制造厂家、基本尺寸等信息,信号会被反馈至计算机控制端,经过处理、存储、读取等功能,获取信息。
48.上述整个轮对检修数字化工厂依托结构化工艺管理系统,包括工艺bom结构树设计、结构化工艺编辑平台、工艺管理平台、系统集成接口(cad、pdm、mes、erp等)。工艺管理是极其典型又复杂的问题,包含了分析、选择、规划、优化等不同性质的各种功能要求,所涉及的范围十分广泛,用到的信息量相当庞大,和生产环境、个人经验水平密切相关。从现代制造业整个产品生命周期对工艺设计的需求出发,以智能制造数字化信息化为背景,建立工艺设计管理为一体的结构化工艺管理系统,是制造业企业信息化建设的重要基础。
49.本实用新型各区内设置的设备,如轮对清洗区内设置的激光清洗机、轮对退卸区设置的轮对退卸机、超声波清洗区内设置的超声波清洗机、磁粉探伤区内设置的磁粉探伤机、齿轮箱组装区内设置的智能提升装置、轮对油漆区内设置的轮对油漆间、齿轮箱试验区内设置的齿轮箱跑合试验机等设备,均采用现有的设备进行各功能的处理。