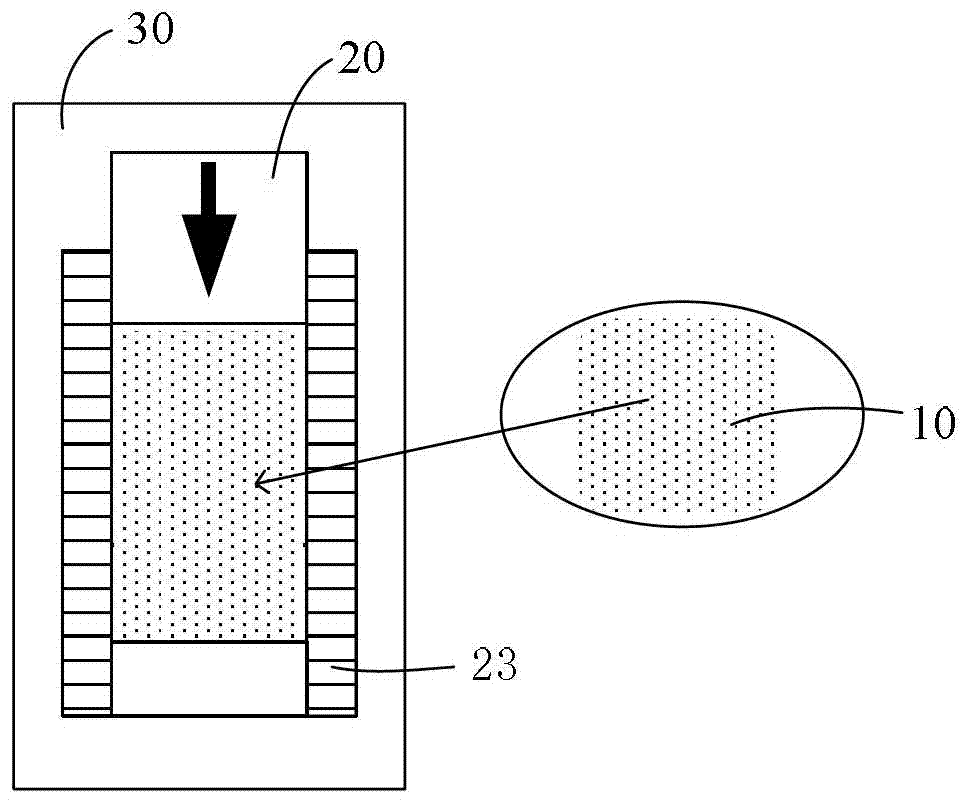
本发明涉及半导体制造领域,尤其涉及一种钼靶材的制作方法。
背景技术:钼是一种银白色金属,硬而坚韧,其熔点2617℃,沸点4612℃。在常温下钼具有良好的耐腐蚀性和稳定性,以及较低的比阻抗、良好的导电性和良好的热膨胀性能。因而,钼被广泛应用于宇航工业、电子工业、玻璃制造业和太阳能光伏等行业。在电子行业中的液晶显示器(简称,LCD)制造领域。由于钼配线相比于传统的铬配线,能更有效地降低配线的比阻抗和膜应力,因此钼用于LCD的元器件则可有效提升液晶显示屏亮度、对比度、色彩并延长寿命;且使用钼的液晶平板显示和触摸屏的环保性能强,体积小,功耗低等优势。现今钼大多通过溅射镀膜工艺以形成薄膜方式应用于LCD制造领域;而在溅射形成钼薄膜工艺中,所使用的钼靶材质量是形成的钼薄膜质量的关键因素。早期的钼靶材是通过熔铸法获得,然而,采用此种方法形成的钼靶材的致密度难以控制。为解决上述问题,行业中通过采用粉末冶金的方法加工钼靶材,即通过制取钼粉末,对钼粉末实施成形和烧结,然后制成钼靶材。钼粉末冶金法由于其具有独特的机械、物理性能,使制造的钼靶材的致密度相较于熔铸法有一定的提高。上述钼靶材粉末冶金技术可参考公开号为CN102392222A的中国专利文献。然而,随着液晶显示器大型化发展要求,靶材的面积也越来越大,目前常用的长条形钼靶材的尺寸可达2300×200×20mm。那么对于靶材的致密度,以及晶粒细致要求越发严格。而现今钼靶材粉末冶金技术获取的大尺寸钼靶材的致密度低,仅仅为80~90%,内部气孔多,无法满足溅射要求,以得到良好的钼薄膜;且在轧制的过程中易出现坯料开裂现象,大大降低了钼靶材制备的成品率。
技术实现要素:本发明解决的问题是采用采用热压烧结和热轧工艺,配合特定的工艺条件以制得致密度高达99.94%,晶粒细小,结构均匀的大尺寸半导体用钼溅射靶材。为解决上述问题,本发明提供一种钼靶材的制作方法,包括:提供钼粉末;采用热压烧结工艺对钼粉末进行致密化处理,形成第一钼靶材坯料;对所述第一钼靶材坯料进行热轧处理,形成第二钼靶材坯料;热轧处理后,对所述第二钼靶材坯料进行退火处理形成钼靶材。可选地,采用热压烧结工艺对钼粉末包括:将钼粉末置于模具中;将所述模具放入热压烧结炉中后,将所述热压烧结炉抽真空;调节所述热压烧结炉温度至1200~1500℃,压强大于20MPa,并保温保压2~5h。可选地,所述热压烧结工艺还包括向所述热压烧结炉中通入保护气体。可选地,所述保护气体包括:Ar、He或N2。可选地,所述热轧处理过程包括,将所述第一钼靶材坯料加热至1200~1500℃,之后进行轧制处理。可选地,所述热轧处理后,所述第一靶材的形变量大于80%。可选地,所述轧制处理包括多阶段轧制。可选地,所述轧制处理包括三个阶段轧制处理,步骤如下:对所述第一钼靶材坯料进行第一阶段轧制,使所述第一钼靶材坯料的形变量为40%~60%;对经过第一阶段轧制后的第一钼靶材坯料进行第二阶段轧制,使所述第一钼靶材坯料的形变量为40%~60%;第二阶段后,对经过第二阶段轧制后的第一钼靶材坯料进行第三阶段轧制,获得第二钼靶材坯料。可选地,所述第一阶段、第二阶段和第三阶段轧制处理均包括多步轧制工艺;在所述第一阶段轧制的每一步轧制工艺后,所述第一钼靶材坯料的形变量为13~40%;在所述第二阶段轧制的每一步轧制工艺后,所述第一钼靶材坯料的型变量为5.5~12%:在所述第二阶段轧制的每一步轧制工艺后,所述第一钼靶材坯料的型变量为12.5~20%。可选地,退火处理的温度小于等于热压烧结工艺的温度,退火处理的温度小于等于热轧处理过程中所述第二靶材的温度。可选地,所述退火处理的方法为:调节温度为800~1200℃,保温加热所述第二钼靶材坯料2~5h。根据权利要求1所述的钼靶材的制作方法,可选地,所述钼粉末的纯度大于等于99.95%,比表面积大于等于1.1m2/g。与现有技术相比,本技术方案具有以下优点:在钼粉末进行热压烧结过程中,加压加热同时进行,在该条件下,钼粉末会出现结晶软化,进而出现热塑性形变,使得钼颗粒间接触扩散,出现流动传质,钼粉末之间错位密度大幅度增加,由此致使钼颗粒间的键连和重排,钼颗粒相互靠拢,钼颗粒之间的空隙的总体积迅速减少,颗粒之间的晶界面积逐渐增加,从而实现钼粉末之间的第一次致密化,得到第一钼靶材坯料;接着进行的热轧处理工艺中,第一钼靶材坯料在大于钼的再结晶温度下进行轧制,一方面较大的钼晶粒被破碎,钼晶粒得到进一步细化,同时第一钼靶材坯料出现动态结晶现象,促使钼晶粒间重新键连和重排,降低第一钼靶材坯料中的空隙,提高了第一钼靶材致密度;而且,热轧处理过程中,第一钼靶材坯料经高温加热后,钼晶粒出现再结晶软化现象,提高第一钼靶材坯料塑性,进而增强了第一钼靶材坯料的形变能力,在压缩第一钼靶材坯料厚度,增大热轧处理工艺后获得的第二钼靶材坯料面积同时,有效避免基于轧制的外力而使得第一钼靶材坯料出现开裂现象。进一步地,将热轧处理分为多个阶段,且各个阶段包括多步形变量不同的轧制步骤以实现第一钼靶材坯料逐步压制、形变,从而进一步加强第一钼靶材坯料的致密化效果,同时上述方案还可有效缓解轧制过程中,在第一钼靶材坯料内部形成的应力,以避免第一钼靶材坯料出现开裂等缺陷。附图说明图1是本发明提供的钼靶材的制作方法的流程图;图2~7是本发明实施例的钼靶材的制作方法各步骤的示意图;图8~9是本发明实施例的获得的钼靶材晶粒均匀度测试方法示意图。具体实施方式正如背景技术所述,现有钼靶材的制备工艺获得的大尺寸钼靶材致密度较低,无法满足靶材溅射要求。为此发明提供了一种钼靶材的制作方法。采用本发明提供的钼靶材的制作方法可以制备致密度高达99.94%,钼靶材的平均晶粒度小于50μm,且晶粒结构均匀的大尺寸钼靶材。完全满足磁控溅射对于大尺寸钼靶材的要求。下面结合附图,通过具体实施例,对本发明的技术方案进行清楚、完整的描述。首先,参考图1所示,执行步骤S1,提供钼粉末。本实施例中,所采用给的钼粉末的纯度大于等于99.95%,比表面积大于等于1.1m2/g。在后续热压烧结、热轧处理以及退火处理过程中,借助钼颗粒基于结晶软化而发生塑性变形过程中,颗粒间摩擦、剪切破碎变形而产生的热以及外部施与的热能,使得钼晶粒间的晶界发生熔化,在此过程中,钼粉末的比表面积越大,则压实过程中晶界熔合面积更大,从而有助于提高形成的靶材致密度。本是实施例中,采用的钼粉末的比表面积大于1.1m2/g,可有助于提高后续形成的靶材致密度,并降低制备过程中促使各晶粒间熔合的能耗。执行步骤S2,采用热压烧结工艺对所述钼粉末10进行致密化处理,形成第一钼靶材坯料。具体过程可参考图2和图3,包括:先参考图2,将足量的钼粉末10置于石墨模具20,之后将石墨模具20放置于热压烧结炉30内,将所述热压烧结炉抽真空;接着参考图3,调节所述调节热压烧结炉30温度至1200~1500℃,如1200℃、1250℃、1300℃、1350℃、1400℃、1450℃和1500℃,调节压强至热压烧结炉30内的压强大于20MPa,保温保压2~5h,实现所述钼粉末10致密化处理,以获得第一钼靶材坯料11。在热压烧结过程中,所述钼粉末10在高温、高压条件下,钼粉末10被激活,钼粉末10结晶软化而出现热塑性形变,呈热塑性状态的钼粉末间接触扩散,出现流动传质运动。而随着时间推进,钼粉末之间错位密度大幅度增加,钼颗粒间的键连和重排,颗粒间相互靠拢,并互相键联,晶粒长大,而钼颗粒之间的空隙迅速减少,晶界渐趋减少,钼颗粒总体积收缩,颗粒之间的晶界面积逐渐增加,使得靶材坯料密度增加,从而实现了钼粉末之间的致密化。经上述热压烧结工艺后,获得的第一钼靶材坯料11的致密度可达到93~98%,平均钼晶粒粒度小于100μm。且为之后的热轧处理作准备。热压烧结过程中,必须保证足够的温度以实现颗粒的结晶软化和塑性形变,以确保颗粒间的键连和重排。但过高的温度会致使钼晶粒结晶过大,从而降低获得的靶材坯料致密度。本实施例中,所述热压烧结温度控制于1200~1500℃,该温度下在确保钼粉末颗粒塑性形变,而实现致密化同时,避免了温度过高而致使钼颗粒结晶过大现象。需要说明的是,通过进一步加强热压烧结工艺的压强可进一步提高获得的第一钼靶材坯料11的致密度,但过高的压力不仅需要消耗更大的能耗,还会进一步增加热压烧结对于设备的要求,如需要抗压性更强的磨具,以避免热压烧结过程中模具受损而导致热压烧结工艺失败。此外在热压烧结工艺中施于过大的压强还会造成钼靶材坯料出现开裂现象。本实施例中,所述热压烧结工艺的压强大于20MPa便可,如20MPa、25MPa、、30MPa、35MPa等,相比于现有60MPa左右的热压烧结压强,本实施例中,通过上述热压烧结工艺配合如热轧处理工艺等后续工艺最终获得高致密度钼靶材的同时,还可有效降低制备钼靶材工艺的能耗,对于如石墨模具或是热压烧结炉等设备要求。在其他的实施例中,在热压烧结工艺过程中,还可向所述热压烧结炉中通入诸如Ar、He或N2等保护气体,以进一步减少形成的第一钼靶材坯料11中的杂质成分,并确保热压烧结工艺稳定性。继续参考图1所示,执行步骤S3,对所述第一钼靶材坯料11进行热轧处理,从而进一步致密化所述第一钼靶材坯料11结构,获得第二钼靶材坯料。本实施例中,具体步骤可结合参考图4~图6:先参考图4所示,本实施例中,所述热轧的方式为将第二钼靶材坯料12在压延机的两个辊筒40a和40b之间进行挤压,从而由相对的两个方向同时对于所述第一钼靶材坯料11进行单轴挤压。该技术方案可有效提高第一钼靶材坯料11的轧制效率同时,所述第一钼靶材坯料11沿厚度方向的各部分的形变均匀度,以确保热轧处理后获得的第二钼靶材坯料12颗粒结构的均匀度。所述热轧处理包括:先将所述第二钼靶材坯料12进行预加热处理,使得所述第二钼靶材坯料12的温度为1200~1500℃,此时,所述钼靶材坯料11的温度大于再结晶温度,之后再进行轧制处理。在所述轧制过程中,所述第一钼靶材坯料11中较大的钼晶粒被破碎,钼晶粒得到进一步细化,以降低第一钼靶材坯料中的空隙,而且轧制过程中,所述钼靶材坯料11出现动态再结晶现象,只是破碎后的钼晶粒间重新键连和重排,从而可有效提高第一钼靶材坯料内的晶粒均的致密度。此外,轧制过程中,所述钼靶材坯料11的温度大于再结晶温度,使得所述第一钼靶材坯料11中的钼颗粒再结晶软化,处于塑性状态,有效提升了所述第一钼靶材坯料11的塑性,进而降低第一钼靶材坯料11的抗形变能力。在高温状态下的第一钼靶材坯料11的轧制过程中,压缩第一钼靶材坯料厚度增大靶材坯料面积的同时,还可有效防止靶材坯料出现开裂现象。接着参考图5所示,所述热轧处理后,所述第一钼靶材坯料11的形变量大于80%,优选为80~90%,即,所述第一钼靶材坯料11的厚度为h,热轧处理后获得的第二钼靶材坯料12的厚度为H,(h-H)/h=80~90%(如图5所示)。在热轧处理过程中,所述第一钼靶材坯料11的厚度被压缩,上下表面积变大,从而获得大尺寸的第二钼靶材坯料12。在轧制过程中,过大的形变量很可能导致靶材坯料出现开裂,本实施例中,为防止第一钼靶材坯料11开裂,对预热后的第一钼靶材坯料11的轧制处理分多个阶段轧制处理。且不同阶段中,可通过如逐步增加施于第一钼靶材坯料11的压力,从而实现靶材逐步轧制变形。其中,每个阶段的轧制处理又可分为多个步骤进行。具体地,所述轧制处理包括三个阶段:结合参考图6所示:a、先对所述第一钼靶材坯料11进行第一阶段轧制,所使述第一钼靶材坯料11的厚度形变量为40%~60%。本实施例中,经热压烧结后获得第一钼靶材坯料11的厚度为100~150mm,第一阶段轧制后,获得的所述第一钼靶材坯料的厚度为40~90mm。其中,所述第一阶段的轧制工艺又分可为多步进行,且每一步轧制后,所述第一钼靶材坯料11的形变量为13~40%,如图6中,第A步轧制前的第一钼靶材坯料11为h1,第A步轧制后的第一钼靶材坯料11为h2,(h1-h2)/h1=13~40%。本实施例中,在第一阶段轧制过程中,经每一步轧制后,所述第一钼靶材坯料11的厚度减少10~20mm。b、在经第一阶段轧制后获得的第一钼靶材坯料11进行第二阶段轧制,使得所述第一钼靶材坯料11的厚度形变量达到40%~60%。本实施例中,第一阶段轧制后,获得的所述第一钼靶材坯料的厚度为40~90mm,在经第二阶段的轧制后,所述第一钼靶材坯料11的厚度变为16mm~54mm。其中,所述第二阶段的轧制工艺同样分可为多步进行,且每一步轧制后,所述第一钼靶材坯料11的形变量为5.5~12%。如图6中,第B步轧制前的第一钼靶材坯料11为h1,第B步轧制后的第一钼靶材坯料11为h2,(h1-h2)/h1=5.5~12%。本实施例中,在第二阶段轧制过程中,经每一步轧制后,所述第一钼靶材坯料11的厚度减少2~3mmc、对经第二阶段轧制获得的第一钼靶材坯料11进行第三阶段轧制,直至轧制最终需要的钼靶材坯料的厚度,得到第二钼靶材坯料12。其中,所述第三阶段的轧制工艺同样分可为多步进行,且每一步轧制后,所述第一钼靶材坯料11的形变量为12.5~20%。如图6中,第B步轧制前的第一钼靶材坯料11为h1,第B步轧制后的第一钼靶材坯料11为h2,(h1-h2)/h1=12.5~20%。本实施例中,在第三阶段轧制过程中,每一步轧制后,所述第一钼靶材坯料11的厚度减少1mm左右。上述三个阶段中随着轧制进行,获得的第一钼靶材坯料11的致密度不断提升。而且配合所述第一钼靶材坯料11致密度提升,各阶段分步轧制的量逐渐减小,从而有效避免轧制过程中,靶材坯料出现开裂现象,进而获得高致密度钼靶材同时,提升钼靶材制备的成品率。通过上述热轧处理后,有效降低了第一钼靶材坯料11的厚度,增加了靶材坯料的面积。同时,在热轧处理后,进一步优化了钼靶材坯料的内部结构,本实施例中,获得的所述第二钼靶材坯料12中的钼晶粒粒度小于50μm(测试方法:GBT6394-2002,金属平均晶粒测定方法),而致密度高达99.94%(测试方法:GB3850-83≈ISO3369-1975,致密烧结金属材料与硬质合金密度测定方法)。在本实施例的热轧处理的可选方案中,在完成所述第一钼靶材坯料11预加热后,所述第一钼靶材坯料11可在H2或诸如Ar、He、或是N2等惰性气体的保护下进行轧制。从而有效避免轧制过程中所述第一钼靶材坯料11发生严重的氧化现象。继续参考图1所示,执行步骤S4,对所述第二钼靶材坯料12进行退火处理形成钼靶材。具体地可参考图7所示,本实施例中,经上述热轧处理获得所述第二钼靶材坯料12后,将所述第二钼靶材坯料12放入加热炉50中进行退火处理,获得钼靶材。所述退火过程包括:将所述第二钼靶材坯料12加热至800~1200℃,并持续保温加热2~5h。所述退火的温度以及加热时间根据实际情况作具体调整,且所述退火温度低于之前热压烧结以及热轧处理中的温度。在上述退火处理过程中,所述第二钼靶材坯料12内部组织进行再结晶以达到平衡状态,使得所述第二铜靶材坯料内部的晶粒变为更加均匀的等轴晶粒;此外退火处理可使得之前热轧工艺中,形成于所述第二铜靶材坯料12内的应力得到充分释放,使得靶材坯料的内部结构得到进一步优化,提高第二铜靶材的机械性能和稳定性。在所述第二钼靶材坯料12在退火处理过程中,若温度过低,加热时间过短,第二钼靶材坯料12的晶粒受热不均匀,无法充分释放第二钼靶材坯料内的应力;但若温度过高,加热时间过长,第二钼靶材坯料12的晶粒容易长大,且晶粒间的空隙变大,从而影响形成的铜靶材的致密度。本实施例中,所述退火的温度小于等于上述热压烧结工艺中的温度,以及小于等于上述热锻处理过程中,所述第一钼靶材坯料11的温度。具体地,所述的退火过程中的温度为800~1200℃,退火的时间持续2~5小时。经检验,退火后获得的钼靶材中的钼晶粒粒度仍然低于50μm(测试方法:GBT6394-2002,金属平均晶粒测定方法),致密度仍达到99.94%(测试方法:GB3850-83≈ISO3369-1975,致密烧结金属材料与硬质合金密度测定方法)。本实施例中上述退火工艺,既可确保第二钼靶材坯料12中的应力充分释放,又可避免获得的钼靶材致密度降低。在退火处理后,对获得的钼靶材坯料进行机械加工,形成所需尺寸的钼靶材13。参考图8所示,在获得钼靶材13后,在木靶材13上划分多个断面(图中显示为3各断面),并在各个断面上获取多个取样点,进行钼晶粒的大小测试。图9为本实施的一些测试数据曲线。图9显示的是在本实施例中,在获得的钼靶材上沿一直线上均匀划分的3个断面上,分别随机获取的10个取样点上的晶粒大小数据。根据数据曲线显示,本实施例中获得的钼靶材的晶粒大小鉴于32~47μm之间,最大的跨度不超过15μm。由此可知,本实施例获得的钼靶材的具有优异的晶粒均匀度。本实施例中,先通过温度为1200~1500℃,压力达20MPa的热压烧结工艺实现钼粉末的致密化处理,以得到钼颗粒晶粒小于100μm,致密度为93~98%的第一钼靶材坯料,之后再通过多阶段的热轧处理工艺逐步实现第一钼靶材坯料进一步致密化处理,从而获得钼颗粒晶粒小于50μm,致密度高达99.94%的钼靶材;而退火工艺可以在进一步优化靶材内部结构的基础上,提高靶材的机械性能,以及稳定性。相比于现有的感应烧结技术和热轧技术获得的钼靶材,本实施获得的钼靶材的钼晶粒粒度更小,晶粒大小更均匀,致密度更高,从而具有更好的电学性能和机械加工性能,从而满足钼靶材溅射要求。此外,本实施例中各加工步骤的条件温和,更易控制,并有效避免了加工过程中,各阶段靶材开裂的现象,有效提高了钼靶材制备的成品率。本发明虽然已以较佳实施例公开如上,但其并不是用来限定本发明,任何本领域技术人员在不脱离本发明的精神和范围内,都可以利用上述揭示的方法和技术内容对本发明技术方案做出可能的变动和修改,因此,凡是未脱离本发明技术方案的内容,依据本发明的技术实质对以上实施例所作的任何简单修改、等同变化及修饰,均属于本发明技术方案的保护范围。