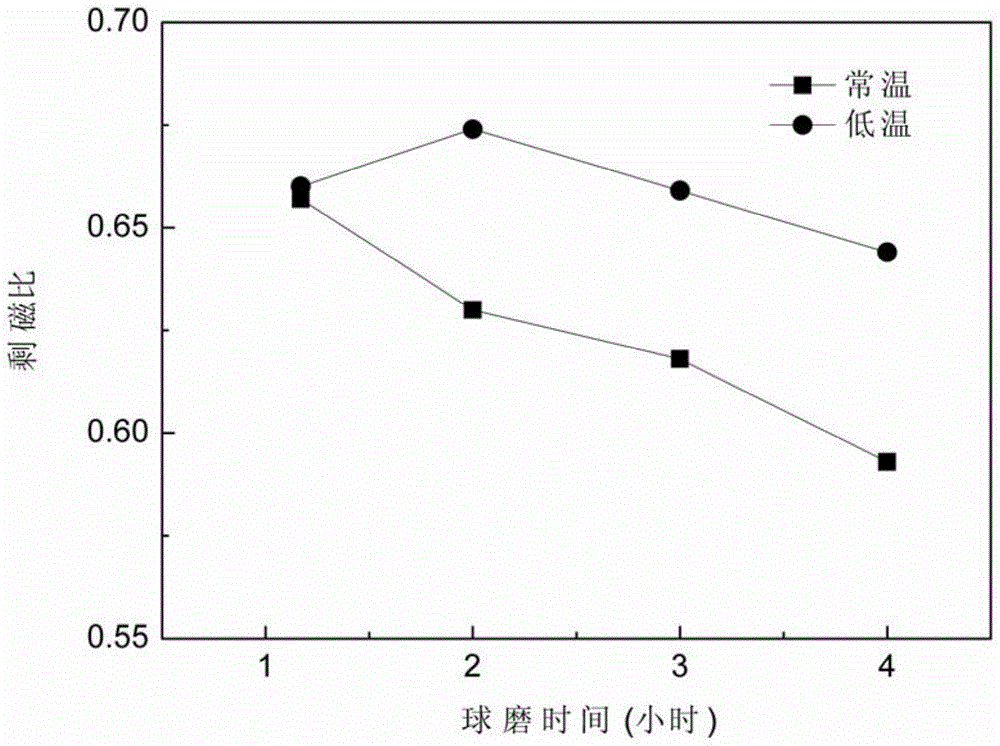
一种具有高剩磁比的稀土-钴永磁颗粒的制备方法技术领域本发明属于磁性材料制备技术领域,具体涉及一种采用低温湿法球磨制备具有高剩磁比的稀土-钴永磁颗粒的方法。
背景技术:稀土-钴合金,例如钐-钴、镨-钴,以及包含其他掺杂元素的永磁合金颗粒等,在制备高温高矫顽力磁体、纳米复合永磁体、高存储磁记录材料、铁磁流体等方面具有重要的研究和应用背景。目前,制备稀土-钴永磁合金颗粒材料的方法主要包括化学合成法,物理沉积法,球磨法等。其中,湿法球磨法由于成本低廉,易操作,可大规模生产,对设备要求低等优点,已经成为一种重要的、使用最普遍的制备稀土-钴永磁颗粒的方法。然而,由于这类合金中稀土元素(钐、镨等)极易氧化,导致制备的颗粒材料永磁性能较低。本课题组在公开号为CN103231066A的中国专利申请中公开了一种制备稀土-过渡族永磁合金微/纳米颗粒的方法,该方法采用低温球磨,不仅抑制了原材料氧化,提高了稀土-过渡族永磁合金颗粒中纳米级颗粒的产量,而且提高了颗粒的矫顽力。但是,该方法并未考虑合金颗粒的剩磁比。然而,稀土-钴永磁合金颗粒在形成的过程中,由于受到磨球高能剧烈的撞击而产生严重的变形,因此破坏了颗粒内部的晶体学各向异性,导致获得的合金颗粒的剩磁比较低。
技术实现要素:本发明的技术目的是改进公开号为CN103231066A的中国专利申请公开的制备方法,提供一种制备稀土-钴永磁颗粒的方法,利用该方法制得的稀土-钴永磁颗粒不仅具有较高的纳米级颗粒含量、较高的矫顽力,而且具有较高的剩磁比。为了实现上述技术目的,本发明人经过大量实验探索后意外发现,将公开号为CN103231066A的中国专利申请公开的制备方法中的有机溶剂限定为熔点温度低于-50℃的有机溶剂,并且在球磨过程中限定球料质量比为8:1~9.5:1,每次球磨时间限定在1.5分钟~5分钟,总球磨时间限定在1小时~10小时的情况下,制得的稀土-钴永磁颗粒不仅具有较高的纳米级颗粒含量、较高的矫顽力,而且具有较高的剩磁比。即,本发明的技术方案为:一种制备高剩磁比的稀土-钴永磁颗粒的方法,该方法以块状或粉末状稀土-钴永磁合金材料为原材料,将原材料装入球磨设备中,在有机溶剂存在条件下,采用低温湿法球磨制备稀土-钴永磁合金颗粒,其特征是:所述的有机溶剂的熔点低于-50℃,球磨温度高于有机溶剂的熔点温度并且低于0℃;并且,球料质量比为8:1~9.5:1,总球磨时间为1小时~10小时。所述的低温球磨方式不限,可以采用专业的低温球磨设备直接进行低温球磨,也可以采用球磨罐进行低温球磨。所述的专业的低温球磨设备的类型不限,包括低温摆动式、行星式、搅拌式球磨机等。当采用球磨罐进行低温球磨时,首先将球磨罐进行冷冻处理,然后在普通球磨机上进行球磨,具体包括如下步骤:(1)将球磨罐置于低温环境,待球磨罐温度等于或低于有机溶剂的熔点温度后取出,在常温环境下安装在球磨机上球磨1.5分钟~5分钟;所述的球磨机不限,包括但不限于行星式、三维振动式、搅拌式、滚动式球磨机等;(2)重复步骤(1),直到总球磨时间为1小时~10小时。所述的原材料的尺寸没有具体要求,为了提高球磨效率,优选将原材料的尺寸控制在毫米量级以下,进一步优选为50μm~800μm。所述的稀土-钴永磁合金材料主要包括Sm-Co,Pr-Co,Y-Co,La-Co等体系,这些体系中可以掺杂其他掺杂元素。这些体系的永磁合金材料包括1:5型,2:17型,1:7型等化合物,例如:SmCo5,PrCo5,Sm2Co17,SmCo7等。所述的有机溶剂不限,例如乙醇、正己烷、正庚烷、2-甲基戊烷等。所述的有机溶剂的加入量不限,优选能够浸润所述的原材料,进一步优选为所述的原材料质量的1倍~10倍。所述的球磨罐材质和容量不限,包括淬硬钢和不锈钢50ml球磨罐;磨球材质和尺寸不限,包括淬硬钢3mm-20mm磨球。所述的球磨过程中还可以包括表面活性剂,即可以在表面活性剂存在条件下进行所述的低温湿法球磨。所述的表面活性剂不限,包括油酸,油胺,三辛胺等中的一种或几种的混合。作为优选,所述的低温湿法球磨是在表面活性剂存在条件下进行的。综上所述,本发明在利用湿法球磨技术制备稀土-钴永磁合金颗粒的过程中,通过控制有机溶剂熔点温度低于-50℃,并且在球磨过程中控制球料质量比为8:1~9.5:1,每次球磨时间限定在1.5分钟~5分钟,总球磨时间控制在1小时~10小时,获得了不仅具有较高纳米级颗粒含量、较高矫顽力,而且具有较高剩磁比的稀土-钴永磁颗粒。其机理的一种解释是:在该球磨温度、球料质量比与球磨时间条件下,球磨过程中的球磨能量被限定,而该球磨温度抑制了稀土-钴永磁合金材料内部位错缺陷的移动和迁移,使得该稀土-钴永磁合金颗粒内部形成尺寸较大的晶粒和不连续的晶界,这种特殊的微观结构一定程度上阻碍了晶粒在球磨过程中的转动,在材料内部形成了较高的晶粒取向度,从而导致了高的剩磁比。因此,本发明的制备方法能够兼顾稀土-钴永磁合金颗粒的颗粒尺寸、矫顽力,以及剩磁比等性能,制得具有优良综合性能的稀土-钴永磁合金颗粒,从而大大拓展了其实际应用领域。其次,采用低温球磨的方法使稀土-钴永磁合金颗粒不容易发生氧化,因此该方法还有利于降低合金颗粒中的氧含量,而氧含量的控制对这类合金磁性能有着重要的影响。另外,实验证实,该方法成本低、简单易操作,因此具有良好的应用前景。附图说明图1是对比实施例1与实施例1中SmCo5颗粒剩磁比随着球磨时间的变化曲线;图2是对比实施例3与实施例3中PrCo5颗粒剩磁比随着球磨时间的变化曲线。具体实施方式下面结合附图与实施例,进一步阐明本发明。应理解的是,这些实施例仅用于说明本发明,而不用于限制本发明的范围。对比实施例1:本实施例是下述实施例1的对比实施例。本实施例中,原材料为经过粗破碎后得到的粒度为200μm~400μm粉末状SmCo5材料。采用湿法球磨将该原材料制备为SmCo5颗粒,制备方法如下:(1)选取三维振动Spex8000D型高能球磨机,将原材料装入不锈钢球磨罐中,然后加入4倍原材料质量的低熔点有机溶剂2-甲基戊烷,再加入直径为6.5mm和9.5mm的不锈钢磨球,球料比为9:1;(2)将装有原材料、磨球、有机溶剂的球磨罐在Ar气手套箱中密封,然后将球磨罐安装到球磨机上,设定球磨时间,在常温下进行球磨,待球磨时间达到后取下球磨罐,得到球磨产物倒入观察瓶中;具体制备过程为:分别设定球磨时间为1小时、2小时、4小时、6小时、8小时、10小时、12小时,重复上述步骤(1)与(2),得到球磨1小时、2小时、4小时、6小时、8小时、10小时、12小时的球磨产物。实施例1:本实施例中,原材料、所选取的球磨机、球磨罐、有机溶剂及用量、磨球尺寸及球料比、球磨罐密封方式与上述对比实施例1完全相同。所不同的是采用低温球磨的方法制备SmCo5颗粒,制备方法如下:待球磨罐密封完好后进行如下操作以实现低温球磨:(1)与对比实施例中的步骤(1)相同;(2)将装有原材料、磨球、有机溶剂的球磨罐置于液氮中低温冷却,待球磨罐温度低于-150℃后取出,在常温环境下安装在球磨机上球磨5分钟;(3)设定球磨时间,重复步骤(2),直到总球磨时间达到设定的球磨时间后取下球磨罐,得到球磨产物倒入观察瓶中;具体制备过程为:分别设定球磨时间为1小时、2小时、4小时、6小时、8小时、10小时、12小时,重复上述步骤(1)与(2),得到球磨1小时、2小时、4小时、6小时、8小时、10小时、12小时的球磨产物。对上述对比实施例1及实施例1中获得的球磨产物进行如下测试:(1)将上述对比实施例1及实施例1中获得的球磨产物样品进行对比,该球磨产物均为悬浮颗粒,下层颗粒为SmCo5微米量级,密集、沉淀在瓶底,而上层颗粒为SmCo5纳米量级,悬浮在有机溶剂中,实施例1中低温球磨的纳米颗粒产量明显高于对比实施例1中在相同实验条件下常温球磨的纳米颗粒。(2)分别在上述对比实施例1及实施例1中获得的球磨产物中取少量下层SmCo5微米颗粒样品进行矫顽力与剩磁比测试,所采用的测试方法为将粉末与AB胶树脂混合,填充到内径为3mm的聚四氟乙烯管中,在磁场强度为2.7T的磁场中取向,待胶体完全固化成型后将其从聚四氟乙烯管中取出,利用振动样品磁强计测试其磁滞回线,获得矫顽力、剩磁与饱和磁化强度,测试条件完全相同。测试结果显示如下:(a)在相同的球磨时间下,通过实施例1中的低温球磨得到的微米颗粒的矫顽力明显高于在相同实验条件下通过对比实施例1中的常温球磨得到的微米颗粒的矫顽力;(b)计算剩磁与饱和磁化强度的比值即剩磁比,得到的剩磁比如图1所示,从图1可以明显看出:当总球磨时间为1小时~10小时时,通过实施例1中的低温球磨得到的SmCo5颗粒的剩磁比明显高于在相同实验条件下通过对比实施例1中的常温球磨得到的SmCo5颗粒的剩磁比;但是,当总球磨时间大于10小时后,通过实施例1中的低温球磨得到的SmCo5颗粒的剩磁比下降,低于在相同实验条件下通过对比实施例1中的常温球磨得到的SmCo5颗粒的剩磁比;(3)利用氧氮分析仪对上述对比实例1及实例1中获得的粉末样品进行氧含量测试,测试结果显示:在相同实验条件和球磨时间下,低温球磨获得的SmCo5颗粒的氧含量明显低于常温球磨所获得的样品。对比实施例2:本实施例是下述实施例2的对比实施例。本实施例中,原材料与对比实施例1完全相同。采用湿法球磨将该原材料制备为SmCo5颗粒,制备方法与对比实施例1中的制备方法基本相同,所不同的是在步骤(1)中,采用的球料比为8:1,在步骤(2)中,球磨时间为4分钟。实施例2:本实施例中,原材料与对比实施例2完全相同。采用湿法球磨将该原材料制备为SmCo5颗粒,制备方法与实施例1中的制备方法基本相同,所不同的是在步骤(1)中,采用的球料比为8:1,在步骤(2)中,球磨时间为4分钟。对上述对比实施例2及实施例2中获得的球磨产物进行如下测试:(1)将上述对比实施例2及实施例2中获得的球磨产物样品进行对比,该球磨产物均为悬浮颗粒,下层颗粒为SmCo5微米量级,密集、沉淀在瓶底,而上层颗粒为SmCo5纳米量级,悬浮在有机溶剂中,实施例2中低温球磨的纳米颗粒产量明显高于对比实施例2中在相同实验条件下常温球磨的纳米颗粒。(2)分别在上述对比实施例2及实施例2中获得的球磨产物中取少量下层SmCo5微米颗粒样品进行矫顽力与剩磁比测试,所采用的测试方法为将粉末与AB胶树脂混合,填充到内径为3mm的聚四氟乙烯管中,在磁场强度为2.7T的磁场中取向,待胶体完全固化成型后将其从聚四氟乙烯管中取出,利用振动样品磁强计测试其磁滞回线,获得矫顽力、剩磁与饱和磁化强度,测试条件完全相同。测试结果显示如下:(a)在相同的球磨时间下,通过实施例2中的低温球磨得到的微米颗粒的矫顽力明显高于在相同实验条件下通过对比实施例2中的常温球磨得到的微米颗粒的矫顽力;(b)计算剩磁与饱和磁化强度的比值即剩磁比,得到的剩磁比结果显示:当总球磨时间为1小时-10小时时,通过实施例2中的低温球磨得到的SmCo5颗粒的剩磁比明显高于在相同实验条件下通过对比实施例2中的常温球磨得到的SmCo5颗粒的剩磁比;但是,当总球磨时间大于10小时后,通过实施例2中的低温球磨得到的SmCo5颗粒的剩磁比下降,低于在相同实验条件下通过对比实施例2中的常温球磨得到的SmCo5颗粒的剩磁比;(3)利用氧氮分析仪对上述对比实例2及实例2中获得的粉末样品进行氧含量测试,测试结果显示,相同实验条件和球磨时间下,低温球磨获得的SmCo5颗粒的氧含量明显低于常温球磨所获得的样品。对比实施例3:本实施例是下述实施例3的对比实施例。本实施例中,原材料为经过粗破碎后得到的粒度为200μm~400μm粉末状PrCo5材料。采用湿法球磨将该原材料制备为PrCo5颗粒,制备过程如下:(1)选取三维振动型高能球磨机,将原材料装入淬硬钢球磨罐中,然后加入原材料质量30%的油胺表面活性剂,以及8倍原材料质量的低熔点有机溶剂正庚烷,再加入直径为4mm、6.5mm和9.5mm的淬硬钢磨球、球料比为8.5:1;(2)将装有原材料、磨球、表面活性剂、有机溶剂的球磨罐在高纯Ar气手套箱中密封,然后将球磨罐安装到球磨机上,设定球磨时间,在常温下进行球磨,待球磨时间达到后取下球磨罐,得到球磨产物倒入观察瓶中;具体制备过程为:分别设定球磨时间为1.17小时、2小时、3小时以及4小时,重复上述步骤(1)与(2),得到球磨1.17小时、2小时、3小时以及4小时的球磨产物。实施例3:本实施例中,原材料、所选取的球磨机、球磨罐、有机溶剂及用量、表面活性剂及用量、磨球尺寸及球料比、球磨罐密封方式与上述对比实施例3完全相同。所不同的是采用低温球磨的方法制备PrCo5颗粒,制备方法如下:待球磨罐密封完好后进行如下操作以实现低温球磨:(1)与对比实施例中的步骤(1)相同;(2)将装有原材料、磨球、、表面活性剂、有机溶剂的球磨罐置于液氮中低温冷却,待球磨罐温度保持在低于-90℃后取出,在常温环境下安装在球磨机上球磨3分钟;(3)设定球磨时间,重复步骤(2),直到总球磨时间达到设定的球磨时间后取下球磨罐,得到的球磨产物倒入观察瓶中;具体制备过程为:分别设定球磨时间为1.17小时、2小时、3小时以及4小时,重复上述步骤(1)与(2),得到球磨1.17小时、2小时、3小时以及4小时的球磨产物。对上述对比实施例3及实施例3中获得的球磨产物进行如下测试:(1)将上述对比实施例3及实施例3中获得的球磨产物样品进行对比,该球磨产物均为悬浮颗粒,下层颗粒为PrCo5微米量级,密集、沉淀在瓶底,而上层颗粒为PrCo5纳米量级,悬浮在有机溶剂中,实施例3中低温球磨的纳米颗粒产量明显高于对比实施例3中在相同实验条件下常温球磨的纳米颗粒。(2)分别在上述对比实施例3及实施例3中获得的球磨产物中取少量下层PrCo5微米颗粒样品进行矫顽力与剩磁比测试,所采用的测试方法为将粉末与AB胶树脂混合,填充到内径为3mm的聚四氟乙烯管中,在磁场强度为2.7T的磁场中取向,待胶体完全固化成型后将其从聚四氟乙烯管中取出,利用振动样品磁强计测试其磁滞回线,获得矫顽力值、剩磁与饱和磁化强度,测试条件完全相同。测试结果显示如下:(a)在相同的球磨时间下,通过实施例3中的低温球磨得到的微米颗粒的矫顽力明显高于在相同实验条件下通过对比实施例3中的常温球磨得到的微米颗粒的矫顽力;(b)计算剩磁与饱和磁化强度的比值即剩磁比,得到的剩磁比结果如图2所示,从图2中可以看到:通过实施例3中的低温球磨得到的PrCo5颗粒的剩磁比明显高于在相同实验条件下通过对比实施例3中的常温球磨得到的PrCo5颗粒的剩磁比。(3)利用氧氮分析仪对上述对比实施例3及实施例3中获得的粉末样品进行氧含量测试,测试结果显示,相同实验条件和球磨时间下,低温球磨获得的PrCo5颗粒的氧含量明显低于常温球磨所获得的样品。以上所述的实施例对本发明的技术方案进行了详细说明,应理解的是以上所述仅为本发明的具体实施例,并不用于限制本发明,凡在本发明的原则范围内所做的任何修改、补充或类似方式替代等,均应包含在本发明的保护范围之内。