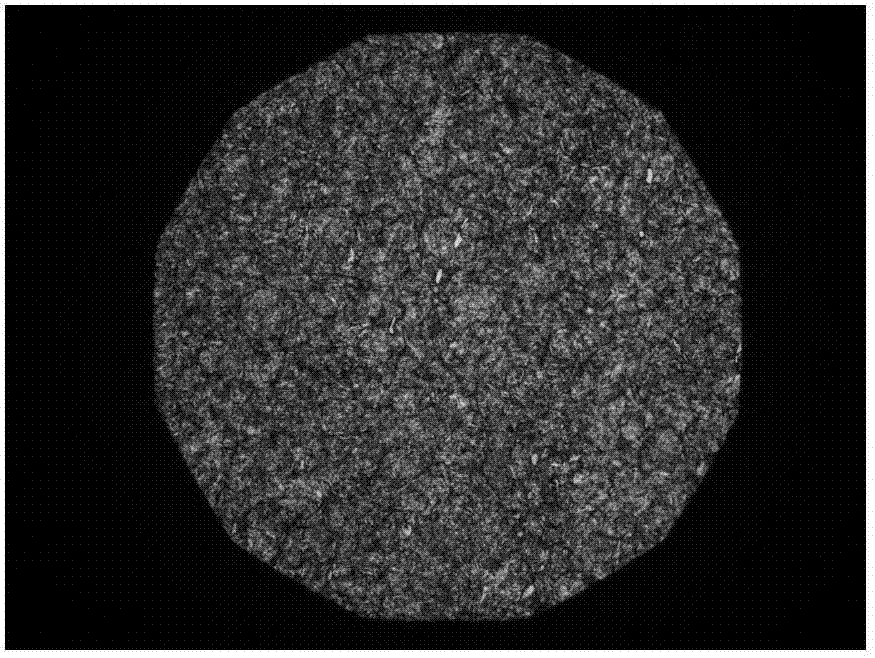
本发明属于刀圈加工制造技术领域,具体涉及一种高性能盘型滚刀刀圈材料及其生产工艺。
背景技术:目前隧道掘进机盘型滚刀刀圈的材料大部分采用美国H13(相当于国内的4Cr5MoSiV1),其成分含量为:C:0.32--0.45%,Si:0.8--1.2%,Mn:0.20--0.50%,P<0.03%,S<0.03%,Cr:4.75--5.50%,Mo:1.10--1.75%,V:0.80--1.20%,Ni<0.30%;用上述材料生产出的刀圈硬度基本在HRC54--56。具有良好的综合机械性能,利用电炉冶炼+LF精炼+真空脱气+电渣重熔的电渣锭加工出的滚刀刀圈,经过热处理后其硬度可以达到HRC54--56。此硬度值可以满足对软岩石的掘进,但遇到硬岩其硬度值达不到要求,刀圈的耐磨性差,刀圈易出现卷边失效缺陷。盘型滚刀刀圈要求高硬度,高耐磨性和良好的冲击韧性,所以目前很多企业为了提高刀圈硬度、提高耐磨性,都在上述成分含量基础上,对部分元素含量进行调整,通过把碳含量的百分比调整为0.45%-0.51%,刀圈加工热处理后硬度可以提高到HRC56--58,刀圈的耐磨性相应的也有所提高,但其韧性下降,在硬岩中使用时刀圈的刃部会出现崩齿、崩裂,严重时会出现刀圈断裂现象。
技术实现要素:本发明的目的是提供高性能盘型滚刀刀圈材料及其生产工艺,解决现有技术中存在的韧性下降,在硬岩中使用时刀圈的刃部会出现崩齿、崩裂,严重时会出现刀圈断裂现象的技术问题。本发明高性能盘型滚刀刀圈材料的成分及重量百分比为:C:0.35--0.42%,Si:0.8--1.2%,Mn:0.20--0.50%,P<0.010%,S<0.005%,Cr:5.00--5.50%,Mo:1.80--2.50%,V:0.80--1.20%,Co:2.00--2.50%,Ni<0.30%,Fe余量。优选的,本发明高性能盘型滚刀刀圈材料的成分及重量百分比为:C:0.39%,Si:0.98%,Mn:0.42%,P:0.009,S:0.004%,Cr:5.32%,Mo:2.14%,V:1.04%,Co:2.38%,Ni:0.23%,Fe余量。优选的,本发明高性能盘型滚刀刀圈材料的成分及重量百分比为:C:0.36%,Si:0.86%,Mn:0.31%,P:0.007%,S:0.005%,Cr:5.02%,Mo:1.84%,V:0.87%,Co:2.13%,Ni:0.27%,Fe余量。优选的,本发明高性能盘型滚刀刀圈材料的成分及重量百分比为:C:0.41%,Si:1.17%,Mn:0.45%,P:0.001%,S:0.004%,Cr:5.43%,Mo:2.46%,V:1.16%,Co:2.47%,Ni:0.18%,Fe余量。用高性能盘型滚刀刀圈材料生产盘型滚刀刀圈的生产方法包括以下步骤:步骤一:真空感应炉熔炼高性能盘型滚刀刀圈材料其化学成分及百分含量按C:0.35--0.42%,Si:0.8--1.2%,Mn:0.20--0.50%,P<0.010%,S<0.005%,Cr:5.0--5.50%,Mo:1.80--2.50%,V:0.80--1.20%,Co:2.00--2.50%,Fe余量进行配料;并熔炼出自耗电极棒;步骤二:对自耗电极棒表面进行精整;步骤三:通过真空电渣炉进行电渣重熔;步骤四:真空电渣炉中生产出的电渣锭,脱模后立即进行高温均质化处理,把电渣锭加热到1260℃,保温24小时,保温结束后随炉冷却到500℃以下出炉空冷;经过高温均质化处理减少了晶内的成分偏析及组织偏析、细化了晶粒,改善和提高了材料的热缩性。步骤五:将在步骤四中得到的电渣锭经初锻、精锻、加工热处理后得到高硬度、高耐磨及具有良好冲击韧性的滚刀刀圈。在所述步骤一中,在真空感应炉熔炼出自耗电极棒具体为:对入炉前的H13废钢料全部进行喷砂处理及烘烤;在熔炼后期的精炼过程中进行多次扒渣、造渣;在出钢过程中进行脱氧;浇注前确保钢水在钢包内有充分的镇静时间,使钢水中的夹杂物得到充分上浮。本发明的有益技术效果:本发明的高性能盘型滚刀刀圈材料在保证原有H13钢中碳、硅、锰的含量保持不变,铬的百分含量为5.0--5.50%,钼的百分含量在原有1.10--1.75%的基础上调整到1.80--2.50%,提高钼的含量可以进一步提高材料的淬透性、降低钢材的回火脆性、改善钢的延展性、韧性并提高耐磨性;加入新的元素钴,其百分含量为2.00--2.50%,改善和提高钢材的热强性及高温硬度,并与钢中较高含量的钼等相互作用得到良好的综合力学性能,使其具有超强韧性;用此材料加工出的滚刀刀圈的硬度由HRC54-HRC56,提高到了HRC58-HRC60;滚刀刀圈的冲击功由8J--10J提高到14J-16J;高性能盘型滚刀刀圈材料严格控制了P、S等杂质含量(P<0.01%、S<0.005%),提高了材料的纯净度,从而有利于改善和提高刀圈的冲击韧性;钴的加入显著提高耐氧化性和红硬性,大大提高材料的耐磨性;改善和提高了刀圈的综合力学性能,延长了刀圈的使用寿命;本发发明的高性能盘型滚刀刀圈材料生产出的盘型滚刀刀圈具有高硬度、高耐磨性及良好冲击韧性的滚刀刀圈材料;本生产方法中废钢料全部使用H13废模具料,并对入炉前的废钢料全部进行喷砂处理及烘烤,使入炉废钢料保证干燥、表面无锈及其他泥沙等杂物,从而保证熔炼钢液的纯净度及低的杂质含量;感应炉出钢前化学成分的百分含量控制在步骤1中的规定范围,严格控制P、S含量;在熔炼后期的精炼过程中要做到多次扒渣、造渣提高钢水的纯净度;在出钢过程中要做好终脱氧;浇注前钢水在钢包内确保充分的镇静时间,使钢水中的夹杂物得到充分上浮;经过真空感应炉熔炼和真空电渣重熔后得到的电渣锭,其有害元素P的含量小于0.01%、S的含量小于0.005%;真空电渣炉中生产出的电渣锭,在脱模后立即进行高温均质化处理,把电渣锭加热到1260℃,保温24小时,保温结束后随炉冷却到500℃以下出炉空冷。经过高温均质化处理减少了晶内的成分偏析及组织偏析、细化了晶粒,改善和提高了材料的热缩性;电渣锭经初锻、精锻、加工热处理后得到高硬度、高耐磨及具有良好冲击韧性的滚刀刀圈。附图说明图1为本发明高性能盘型滚刀刀圈生产工艺的流程图;图2为本发明在具体实施例中代号为1的盘型滚刀刀圈材料的金相组织图;图3为本发明在具体实施例中代号为2的盘型滚刀刀圈材料的金相组织图;图4为本发明在具体实施例中代号为3的盘型滚刀刀圈材料的金相组织图;图5为本发明在具体实施例中H13钢的盘型滚刀刀圈材料的金相组织图。具体实施方式下面结合附图对本发明作进一步阐述。参见附图1,本发明的目的是提供高性能盘型滚刀刀圈材料及其生产工艺,解决现有技术中增加碳含量,提高硬度造成的韧性下降,在硬岩中使用时刀圈的刃部会出现崩齿、崩裂,严重时会出现刀圈断裂现象的技术问题。本发明高性能盘型滚刀刀圈材料的成分及重量百分比为:C:0.35--0.42%,Si:0.8--1.2%,Mn:0.20--0.50%,P<0.010%,S<0.005%,Cr:5.00--5.50%,Mo:1.80--2.50%,V:0.80--1.20%,Co:2.00--2.50%,Ni<0.30%,Fe余量。优选的,本发明高性能盘型滚刀刀圈材料的成分及重量百分比为:C:0.39%,Si:0.98%,Mn:0.42%,P:0.009,S:0.004%,Cr:5.32%,Mo:2.14%,V:1.04%,Co:2.38%,Ni:0.23%,Fe余量。优选的,本发明高性能盘型滚刀刀圈材料的成分及重量百分比为:C:0.36%,Si:0.86%,Mn:0.31%,P:0.007%,S:0.005%,Cr:5.02%,Mo:1.84%,V:0.87%,Co:2.13%,Ni:0.27%,Fe余量。优选的,本发明高性能盘型滚刀刀圈材料的成分及重量百分比为:C:0.41%,Si:1.17%,Mn:0.45%,P:0.001%,S:0.004%,Cr:5.43%,Mo:2.46%,V:1.16%,Co:2.47%,Ni:0.18%,Fe余量。用高性能盘型滚刀刀圈材料加工盘型滚刀刀圈的生产方法包括以下步骤:步骤一:真空感应炉熔炼高性能盘型滚刀刀圈材料其化学成分及百分含量按C:0.35--0.42%,Si:0.8--1.2%,Mn:0.20--0.50%,P<0.010%,S<0.005%,Cr:5.0--5.50%,Mo:1.80--2.50%,V:0.80--1.20%,Co:2.00--2.50%,Fe余量进行配料;并熔炼出自耗电极棒;步骤二:对自耗电极棒表面进行精整;步骤三:通过真空电渣炉进行电渣重熔;步骤四:真空电渣炉中生产出的电渣锭,脱模后立即进行高温均质化处理,把电渣锭加热到1260℃,保温24小时,保温结束后随炉冷却到500℃以下出炉空冷;经过高温均质化处理减少了晶内的成分偏析及组织偏析、细化了晶粒,改善和提高了材料的热缩性。步骤五:将在步骤四中得到的电渣锭经初锻、精锻、加工热处理后得到高硬度、高耐磨及具有良好冲击韧性的滚刀刀圈。在所述步骤一中,在真空感应炉熔炼出自耗电极棒具体为:对入炉前的H13废钢料全部进行喷砂处理及烘烤;在熔炼后期的精炼过程中进行多次扒渣、造渣;在出钢过程中进行脱氧;浇注前确保钢水在钢包内有充分的镇静时间,使钢水中的夹杂物得到充分上浮。具体实施例二:本实施例与实施例1的区别在于,钴的重量百分比为2.00%。具体实施例三:本实施例与实施例1的区别在于,钴的重量百分比为2.5%。具体实施例四:本实施例与实施例1的区别在于,钴的重量百分比为2.25%。具体实施例五:本实施例与实施例1的区别在于,优选的,钼的重量百分比为1.80%。具体实施例六:本实施例与实施例1的区别在于,钼的重量百分比为2.30%。具体实施例七:本实施例与实施例1的区别在于,钼的重量百分比为2.15%。具体实施例八:本实施例与实施例1的区别在于,铬的重量百分比为5.00%。具体实施例九:本实施例与实施例1的区别在于,铬的重量百分比为5.50%。具体实施例十:本实施例与实施例1的区别在于,铬的重量百分比为5.25%。具体实施例十一:本实施例的区别在于,钴的重量百分比为2.00%,钼的重量百分比为1.80%。具体实施例十二:本实施例与实施例1的区别在于,钴的重量百分比为2.00%,钼的重量百分比为2.30%。具体实施例十三:本实施例与实施例1的区别在于,钴的重量百分比为2.00%,钼的重量百分比为2.15%。具体实施例十四:本实施例与实施例1的区别在于,钴的重量百分比为2.00%,铬的重量百分比为5.00%。具体实施例十五:本实施例与实施例1的区别在于,钴的重量百分比为2.00%,铬的重量百分比为5.50%。具体实施例十六:本实施例与实施例1的区别在于,钴的重量百分比为2.00%,铬的重量百分比为5.25%。具体实施例十七:本实施例与实施例1的区别在于,钴的重量百分比为2.00%,钼的重量百分比为1.80%,铬的重量百分比为5.00%。具体实施例十八:本实施例与实施例1的区别在于,钴的重量百分比为2.00%,钼的重量百分比为1.80%,铬的重量百分比为5.50%。具体实施例十九:本实施例与实施例1的区别在于,钴的重量百分比为2.00%,钼的重量百分比为1.80%,铬的重量百分比为5.25%。具体实施例二十:本实施例与实施例1的区别在于,钴的重量百分比为2.00%,钼的重量百分比为2.50%,铬的重量百分比为5.00%。具体实施例二十一:本实施例与实施例1的区别在于,钴的重量百分比为2.00%,钼的重量百分比为2.50%,铬的重量百分比为5.50%。具体实施例二十二:本实施例与实施例1的区别在于,钴的重量百分比为2.00%,钼的重量百分比为2.50%,铬的重量百分比为5.25%。具体实施例二十三:本实施例与实施例1的区别在于,钴的重量百分比为2.00%,钼的重量百分比为2.35%,铬的重量百分比为5.00%。具体实施例二十四:本实施例与实施例1的区别在于,钴的重量百分比为2.00%,钼的重量百分比为2.35%,铬的重量百分比为5.50%。具体实施例二十五:本实施例与实施例1的区别在于,钴的重量百分比为2.00%,钼的重量百分比为2.35%,铬的重量百分比为5.25%。对具体实施例二至具体实施例二十五的盘型滚刀刀圈材料加工滚刀刀圈的生产方法与实施例一唯一不同的是:在步骤一中的配料过程中,按照各具体实施例中的成分重量百分比进行配料。刀圈进行了各项性能检测,其结果详见下表:表1高性能盘型滚刀刀圈的化学成分代号C%Si%Mn%P%S%Cr%Mo%V%Co%Ni%10.390.980.420.0090.0045.322.141.042.380.2320.360.860.310.0070.0055.021.840.872.130.2730.411.170.450.0010.0045.432.461.162.470.18表2钢中非金属夹杂物其中:A为硫化物;B为氧化铝;C为硅酸盐;D为球状氧化物;DS为单颗粒夹杂物。表3高性能盘型滚刀刀圈的性能参见附图2、3和4,成品刀圈的金相组织:金相评级2--3级,组织为细针状回火马氏体+极少量残余奥氏体;通过上述实验数据可得出:滚刀刀圈的硬度由HRC54-HRC56,提高到了HRC58-HRC60;滚刀刀圈的冲击功由8J--10J提高到14J-16J;高性能盘型滚刀刀圈材料严格控制了P、S等杂质含量(P<0.01%、S<0.005%),提高了材料的纯净度,从而有利于改善和提高刀圈的冲击韧性;钴的加入显著提高耐氧化性和红硬性,大大提高材料的耐磨性;改善和提高了刀圈的综合力学性能,延长了刀圈的使用寿命。H13钢生产出的滚刀刀圈的各项性能如下表:表4H13钢化学成分代号C%Si%Mn%P%S%Cr%Mo%V%Ni%H13钢0.410.940.470.0190.0095.171.541.060.17表5H13钢中非金属夹杂物表6H13钢成品刀圈的性能参见附图5,H13钢成品刀圈的金相组织:金相评级4级,组织为针状回火马氏体+少量残余奥氏体从表1-3与表4-6一一对比,以及附图2-4与附图5一一对比中可得出,高性能盘型滚刀刀圈材料的非金属夹杂物含量远低于H13钢;高性能盘型滚刀刀圈材料生产的成品刀圈金相组织比H13钢的金相组织,马氏体的形状更加细小,残余奥氏体的含量更加少;从力学性能看高性能盘型滚刀刀圈材料的各项性能指标都高于H13钢。