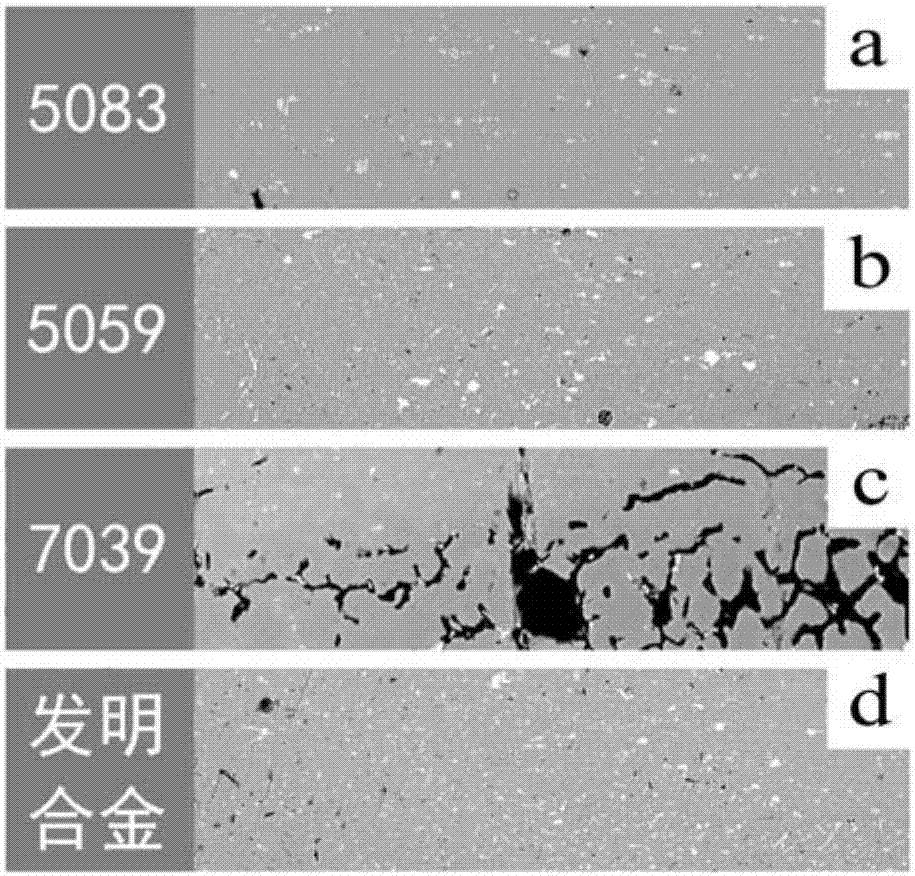
本发明属于有色金属及其制备领域,尤其涉及一种提升铝合金焊缝强度和抗裂能力的方法,适用于船舶以及装甲板的生产制造过程。
背景技术:
:在船舶运输、军用装甲行业中,使用高比强度铝合金材料替换传统的钢铁材料已经成为一种新的趋势,其可以保证合金使用强度不变的同时显著减轻船舶、装甲车辆的整体重量,从而大幅提升船舶燃油的利用效率以及装甲车的作战机动性能。由于船舶以及装甲用材均具有大面积、高跨度的特征,在生产过程中必须使用金属连接工艺(主要是焊接)将小尺寸原料相互连接进而得到,因此,所用铝合金材料的可焊性以及焊后性能必须作为一种重要选材考量指标。现阶段大量用于上述行业的铝合金材料主要为5xxx系和7xxx系。常用的5xxx系铝合金(例如aa5083)可焊性优异,但其基体和焊缝强度相对较低,且该类合金的强化手段主要为加工硬化,焊接后焊缝强度损失较大,故应用上存在一定局限;传统7xxx系铝合金(例如aa7039和aa7017)强度等力学性能相对较好,但由于mg、zn以及cu元素的含量都处于易发生焊接结晶裂纹的区间导致其可焊性不及5xxx系铝合金,在焊接过程中容易产生焊接裂纹以及微裂纹,焊缝服役可靠性较差。因此,开发一种提升铝合金焊缝强度和抗裂能力的技术对于船舶以及军事工业具有重要意义。首先在选择合金成分上,1999年,美国铝业协会登记注册的aa5059合金在常规5xxx系合金的基础之上提高了mg和zn的含量,使得合金晶内析出较多的t-al32(mgzn)49相。这种合金在保留常规5xxx系合金优秀的耐蚀性、可焊性的同时,屈服及抗拉强度也得到了较大程度的提升。已公开的上述典型合金的组成范围分别为:aa5083:mg含量为4.0~4.9,mn含量为0.4~1.0,cr含量为0.05~0.25,zn含量不高于0.25,cu含量不高于0.1,ti含量不高于0.15,fe含量不高于0.4,si含量不高于0.4;aa7039:mg含量为2.3~3.3,mn含量为0.1~0.4,cr含量为0.15~0.25,zn含量为3.5~4.5,cu含量不高于0.1,ti含量不高于0.1,fe含量不高于0.4,si含量不高于0.3;aa5059:mg含量为5.0~6.0,mn含量为0.6~1.2,cr含量不高于0.25,zn含量为0.4~0.9,cu含量不高于0.25,ti含量不高于0.2,fe含量不高于0.5,si含量不高于0.45,zr含量为0.05~0.25。其中aa5059的合金含量也公开在us-6695935-b1、us-6238495-b1、cn-101233252-a和cn-101631882-a专利中。发明专利zl201410577461.5又在aa5059合金的基础上将zn含量上调,降低mg在基体中的固溶量,借鉴7xxx系铝合金时效强化的思想,最终得到晶粒内部含大量t-al32(mgzn)49相的高强al-mg-zn合金并成功制备其板材,为时效强化型5xxx系铝合金的设计和制备奠定了基础。但此类合金由于合金度相对于7xxx系合金较低,焊接接头强度仍然没有达到7xxx系合金的强度级别,使得其应用具有一定局限性。技术实现要素:本发明的目的在于,基于高zn含量的al-mg合金,通过焊接、焊后人工时效工艺,使焊缝在焊接过程中具有良好的抵抗焊接裂纹的能力,焊缝强度接近7xxx系合金的强度级别,但焊缝抵御焊接裂纹能力明显优于7xxx系,并具有较高的服役可靠性,适用于船舶以及装甲板的生产制造过程,因而具有良好的工业以及军事应用前景。实现本发明采用如下步骤:将质量百分含量为4.0~7.0%mg、2.0~4.0%zn、0~0.6%cu、0.1~1.2%mn、0~0.1%cr、0~0.25%ti、0~0.3%zr、0~0.6%fe、0~0.6%si,其余为al的al-mg-zn系合金板材进行mig焊接,焊接后实行人工时效处理,其人工时效处理是将板材加热至60~160℃并保温100~180h,然后空冷。优选地,所述al-mg-zn系合金质量百分含量为4.0~6.0%mg,2.5~3.5%zn,0~0.4%cu,0.5~1.0%mn,0~0.1%cr,0~0.15%ti,0.05~0.25%zr,0~0.4%fe,0~0.4%si,其余为al。所述mig焊接过程中焊机工艺参数为:焊机工作电流70~110a,工作电压8~18v,起弧停留时间小于4.0s,填丝速度5.0~10.0m/min,焊接速度5.0~18.0mm/s,氩气流量12~18l/min。进一步地,所述mig焊接过程中,焊机的工作参数具体为:焊机工作电流80~100a,工作电压10~15v,起弧停留时间小于2.0s,填丝速度5.0~8.0m/min,焊接速度8.0~15.0mm/s,氩气流量12~18l/min。进一步地,所述焊后人工时效的具体工艺为:将焊接后的板材加热至80~120℃并保温150~170h,然后空冷。本发明的优越性在于,第一,本发明所述al-mg-zn合金由于具有时效析出能力,经过焊接和焊后时效强化后的焊缝强度相比5xxx系参考合金(aa5059以及aa5083)有较大幅提升,已经接近7xxx系参考合金(aa7039)的焊缝强度水平,达到243.9mpa;第二,使用本发明所述焊接工艺对发明合金进行焊接,其焊缝抵御焊接裂纹能力与5xxx系参考合金相近,且明显优于7xxx系参考合金,无焊接热裂纹。本发明所述al-mg-zn合金的焊接工艺,非常适用于船舶以及装甲板的生产制造过程。附图说明图1是鱼骨状焊接结晶裂纹实验的试样尺寸示意图。图2是焊接液化裂纹实验试样断口显微图像。a为5083合金断口;b为5059合金断口;c为7039合金断口;d为本发明实施例1合金断口。实施方式参考以下实施例来进一步说明本发明。实施例1本例所涉及的所有实验合金及参考合金均在实验室范围内制备完成,合金制备环节所用设备以及通用工艺(熔炼、轧制、退火等)完全相同,制备不同成分的合金共计四种,其成分及用途见表1。表1本例发明所用合金化学成分及用途表(质量百分数,wt%)本例所述合金板材的制备工艺流程如下:熔炼铸造→双级均匀化退火→热轧变形→中间退火→冷轧变形→固溶淬火→双级时效至t6状态。铸锭的双级均匀化退火工艺具体为:将铸锭以20~40℃/s的速率从室温升温至420~440℃并保温3~8h,随后以20~40℃/s的速率升温至500~535℃保温5~15h,最后以20~40℃/s的速率将铸锭随炉降温至室温。热轧变形工艺具体为:将试样加热至470~500℃保温2~3h,然后进行变形量90%以上的热变形,变形温度区间为380~480℃。中间退火及冷轧变形工艺具体为:将试样在350~400℃进行60~90min的再结晶退火,然后进行变形量为50%的冷轧变形。固溶及时效工艺具体为:将处于冷轧态的试样在500~535℃的盐浴炉中保温10~30min后立即水淬,随后进行80~100℃和130~150℃的双级时效处理,至t6状态,此状态为合金板材用于焊接的最终状态。本例所述合金板材的焊接及焊后时效工艺流程如下:所使用mig焊机的工作参数具体为:装填er5556焊丝,焊机工作电流焊机工作电流90a,工作电压12v,起弧停留时间1.0s,填丝速度8m/min,焊接速度10mm/s,氩气流量15l/min,将焊接后的板材进行适当的自然时效或人工时效,所述焊后人工时效的具体工艺为:将焊接后的板材加热至100℃并保温160h,然后空冷得到最终焊后板材。使用拉伸试验机测量所制得合金焊缝的强度,合金焊缝的力学性能如表2所示。本发明合金焊缝在强度级别上与传统5xxx系参考合金相比更加接近于7xxx系参考合金,且大幅超过两种5xxx系参考合金。表2合金焊接后力学性能。合金用途屈服强度(mpa)50835xxx参考合金172.650595xxx参考合金177.770397xxx参考合金245.6al-mg-zn发明合金243.9使用鱼骨状裂纹扩展实验定量评定实验合金焊接过程中产生结晶裂纹的倾向,鱼骨状试样尺寸见附图1,焊接该试样的工艺与上述mig焊接工艺完全相同。该试样可以在焊接过程中对焊缝部分的金属熔体施加由大到小的约束使得焊缝开裂,开裂的长短可以定量评价合金抵御焊接结晶裂纹的能力的强弱。通过表3可知,发明合金与两种5xxx系参考合金相同,在焊接过程中均未产生结晶裂纹,而7xxx系参考合金在mig焊接过程中产生了明显的焊接结晶裂纹,且裂纹长度远远超过其他三种合金。由此可见,发明合金具有与常规5xxx系合金相近的抵御焊接结晶裂纹的能力,且远远超过常规7xxx系合金。表3鱼骨状裂纹扩展实验结果合金用途裂纹长度(mm)50835xxx参考合金050595xxx参考合金070397xxx参考合金38al-mg-zn发明合金0使用环形拘束实验定量评测合金在焊接过程中发生液化裂纹的倾向,焊接该试样的工艺与上述mig焊接工艺完全相同。该实验模具可以对凝固中的焊缝金属提供拘束,模拟较大拘束下的焊缝凝固产生液化裂纹或微裂纹的行为。经过环形拘束实验后的焊缝横截面部分熔化区的显微图像如图2,从中可见,本发明合金(d)和5xxx系参考合金(a)、(b)相同,焊后部分熔化区没有微裂纹产生,而7xxx系参考合金(c)焊后部分熔化区则出现明显微裂纹。由此可见,发明合金抵御焊接液化裂纹能力与5xxx系参考合金接近,强于7xxx系参考合金。实施例2本例所用发明和金成分如表4,主合金元素zn含量质量分数降至2.5%,mg含量质量分数降至4.5%。表4本例发明所用合金化学成分及用途表(质量百分数,wt%)本例所述合金板材的焊接及焊后时效工艺流程如下:所使用mig焊机的工作参数具体为:装填er5556焊丝,焊机工作电流焊机工作电流75a,工作电压10.5v,起弧停留时间2.0s,填丝速度7m/min,焊接速度8mm/s,氩气流量16.5l/min,将焊接后的板材进行适当的自然时效或人工时效,所述焊后人工时效的具体工艺为:将焊接后的板材加热至95℃并保温170h,然后空冷得到最终焊后板材。使用本例工艺参数对改变主合金元素的合金进行焊接及焊后时效处理后,焊缝强度和抗焊接裂纹能力与实施例1展现出相同的趋势,即焊缝强度接近7xxx系合金,同时具有接近5xxx系合金的优异抗焊接裂纹能力。实施例3本例所用发明和金成分如表5,主合金元素zn含量质量分数升至3.5%,mg含量质量分数升至6%。表5本例发明所用合金化学成分及用途表(质量百分数,wt%)本例所述合金板材的焊接及焊后时效工艺流程如下:所使用mig焊机的工作参数具体为:装填er5556焊丝,焊机工作电流焊机工作电流105a,工作电压14.5v,起弧停留时间0.5s,填丝速度8m/min,焊接速度12mm/s,氩气流量15l/min,将焊接后的板材进行适当的自然时效或人工时效,所述焊后人工时效的具体工艺为:将焊接后的板材加热至105℃并保温150h,然后空冷得到最终焊后板材。使用本例工艺参数对改变主合金元素的合金进行焊接及焊后时效处理后,焊缝强度和抗焊接裂纹能力与实施例1展现出相同的趋势,即焊缝强度接近7xxx系合金,同时具有接近5xxx系合金的优异抗焊接裂纹能力。综上所述,本发明所设计的合金成分及对应的焊接和焊后热处理工艺很好的解决了船舶以及装甲用铝合金焊缝无法同时具备高强度和良好可焊性的问题。zn元素的提升使得合金焊接后可以被时效强化,因此可以有效避免焊缝在焊接之后由于再结晶带来的强度损失,从而使得焊缝强度相对于不可时效强化的5083以及5059合金有了较大程度的提升,并基本趋近于7039合金的焊缝强度水平;同时,本发明合金在所述焊接工艺下可焊性表现与5083以及5059合金持平,在焊接过程中不易产生焊接结晶、液化裂纹,焊缝具有较高可焊性和服役可靠性。当前第1页12