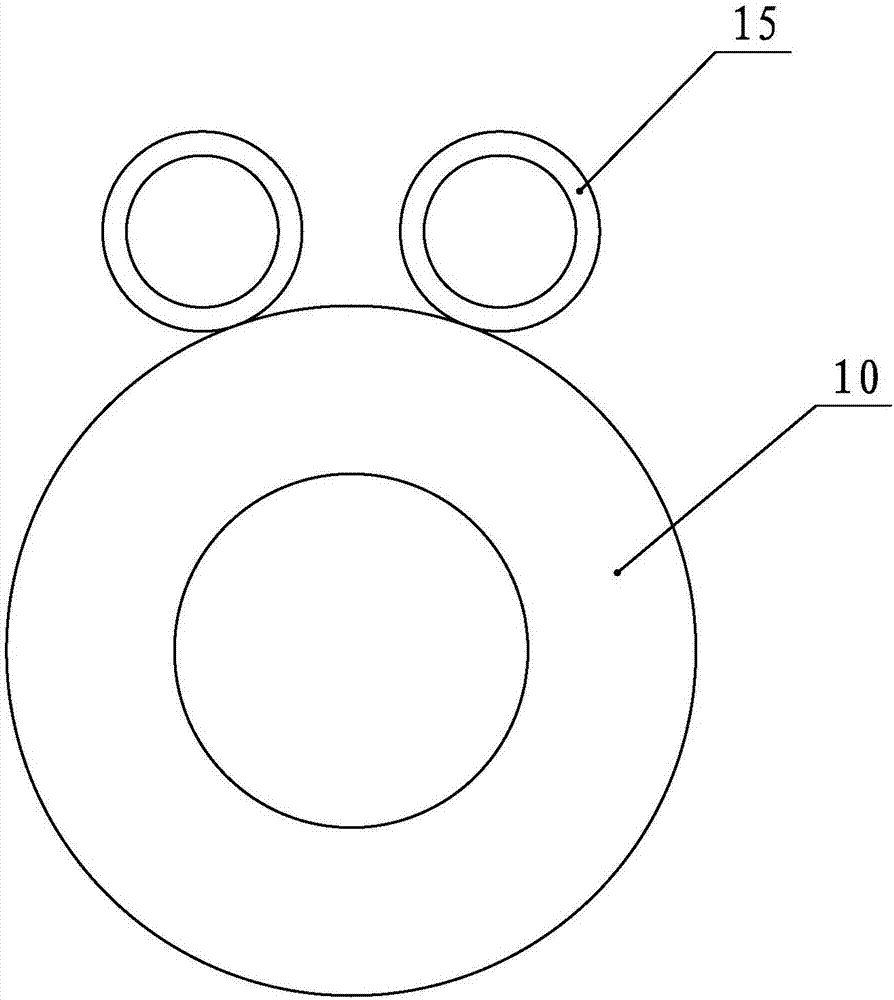
本发明涉及一种挤压丝锥螺纹磨床,特别涉及一种挤压丝锥螺纹磨床的组合式多线磨轮。
背景技术:
:挤压丝锥是利用金属塑性变形原理而加工内螺纹的一种新型螺纹刀具,挤压丝锥挤压内螺纹是无屑加工工艺,特别适用于强度较低、塑性较好的铜合金和铝合金,也可用于不锈钢和低碳钢等硬度低、塑性大的材料攻丝,寿命长。用挤压丝锥挤出的螺纹表面光洁度高,螺纹的金属纤维不断裂,并在表面形成一层冷硬层,可提高螺纹的强度和耐磨性,从根本上解决了攻丝的排屑困难问题,因无屑而更有利于螺纹的装配,在电子、塑料行业应用广泛。目前常规的挤压丝锥为三棱或四棱结构,三棱边的丝锥在挤压螺孔时塑性变形和扭矩值最小,但其横截面积小,因而其强度较四棱边结构的强度差,且测量是用比较仪测量而存在测量误差;而四棱边挤压丝锥塑性变形和扭矩值较三棱边的挤压丝锥稍大,但其测量是用三针在指示千分尺上测量,与比较仪测量方式比较其测量值相对准确。常规的挤压丝锥加工采用金刚石磨轮进行单线磨,由于挤压丝锥多为三棱或四棱结构,采用常规的单线磨具有效率低且加工精度差的缺点,因而多线磨是目前用于挤压丝锥加工的新兴方式。目前,多线磨金刚石磨轮只能采用表面层镀覆结构,该种表面镀覆结构的多线磨金刚石磨轮如果用于加工尖峰r<0.1mm的小螺距型面时则只能使用180#以上的金刚砂进行镀覆,但表面镀覆的金刚砂寿命与粒度成正比,则金刚砂的粒度越小寿命越差,从而导致现有技术的镀覆结构金刚石磨轮用于小螺距型面加工时寿命较差且成本较高。而目前只有单片的金刚石磨轮才能用金刚砂实体烧结并用天然金刚石磨轮磨削精加工而成,但目前的单片金刚石磨轮不能满足三棱或四棱结构挤压丝锥的高效高精度加工且不能用于0.35mm以下小螺距挤压丝锥的加工成型。技术实现要素:为解决上述技术问题,本发明提供了一种挤压丝锥螺纹磨床的组合式多线磨轮,包括磨轮本体及位于所述磨轮本体一侧的一对螺距错位的金刚石修正轮;所述磨轮本体包括:多片并列组合的金刚石轮片,穿过组合的所述金刚石轮片中心定位孔的定位基体,与所述定位基体配合以夹持组合的所述金刚石轮片两侧的夹板,以及用于将所述定位基体、组合的所述金刚石轮片以及夹板进行组装固定的螺钉;所述金刚石轮片的外边缘螺纹尖角的截面呈60°夹角。其中,多片并列组合的所述金刚石轮片的直径依次减小且最大直径与最小直径之差为△h。进一步的,单片的所述金刚石轮片均包括具有中心定位孔的轮片本体,以及环状设置于所述轮片本体外径的金刚石基体,多片并列组合的所述金刚石轮片的轮片本体直径相等,且多片并列组合的所述金刚石轮片的金刚石基体的直径依次减小且最大直径与最小直径之差为△h,其中,所述金刚石基体的外圆与内圆直径之差为h,所述金刚石轮片的外径为d,所述轮片本体的外径为d0=d-2h。其中,所述轮片本体的厚度为b,所述金刚石基体的厚度为b,所述金刚石基体的厚度b小于所述轮片本体的厚度b。其中,按所述金刚石轮片的直径由小到大排列,直径倒数最小的三片所述金刚石轮片之间的两个螺距t2相等,其余n片所述金刚石轮片之间的螺距t1相等。其中,所述金刚石轮片的螺距为0.7~2mm,所述金刚石轮片的数量为6-17片,且螺距越小对应的数量越多。通过上述技术方案,本发明具有如下优点:①采用多片单独精加工而成的金刚石轮片组合形成多线磨轮,相比于现有的单线磨,本发明多线磨轮可以使工件一次性加工吃刀到位,并一次性磨全程而使工效提高数倍;②采用多片单独精加工而成的金刚石轮片组合形成多线磨轮,相比于现有的表面镀覆金刚砂的多线磨轮,本发明多线磨轮具有更长的使用寿命而极大降低了加工成本;③采用主磨轮与一对螺距错位的金刚石修正轮组合结构,通过金刚石修正轮的修正可以获得螺距在0.35~0.7mm之间的小螺距挤压丝锥的高效加工成型,解决了目前单纯的厚度小于0.7mm多线磨轮难以成型的难题;④采用多片金刚石磨轮外径阶梯式结构,可以有效实现精度公差的分配而提高挤压丝锥螺纹的加工精度。附图说明为了更清楚地说明本发明实施例中的技术方案,下面将对实施例描述中所需要使用的附图作简单地介绍。图1为本发明实施例所公开的组合式多线磨轮结构示意图;图2为本发明实施例所公开的磨轮本体截面结构示意图;图3为本发明实施例所公开的金刚石轮片截面示意图;图4为图3中k处放大结构示意图。图中数字表示:10.磨轮本体11.定位基体12.夹板13.螺钉14.金刚石轮片15.金刚石修正轮16.轮片本体17.金刚石基体具体实施方式下面将结合本发明实施例中的附图,对本发明实施例中的技术方案进行清楚、完整地描述。参考图1,本发明提供的挤压丝锥螺纹磨床的组合式多线磨轮,包括磨轮本体10及位于磨轮本体10一侧的一对螺距错位的金刚石修正轮15。参考图2,磨轮本体10包括:多片并列组合的金刚石轮片14,穿过组合的金刚石轮片14中心定位孔18的定位基体11,与定位基体11配合以夹持组合的金刚石轮片14两侧的夹板12,以及用于将定位基体11、组合的金刚石轮片14以及夹板12进行组装固定的螺钉13;金刚石轮片14的外边缘螺纹尖角的截面呈60°夹角;多片并列组合的金刚石轮片14的直径依次减小且最大直径与最小直径之差为△h。参考图3及4,单片的金刚石轮片14均包括具有中心定位孔18的轮片本体16,以及环状设置于轮片本体16外径的金刚石基体17,多片并列组合的金刚石轮片14的轮片本体16直径相等,且多片并列组合的金刚石轮片14的金刚石基体17的直径依次减小且最大直径与最小直径之差为△h,其中,金刚石基体17的外圆与内圆直径之差为h,金刚石轮片14的外径为d,轮片本体16的外径为d0=d-2h;其中,轮片本体16的厚度为b,金刚石基体17的厚度为b,金刚石基体17的厚度b小于轮片本体16的厚度b;按金刚石轮片14的直径由小到大排列,直径倒数最小的三片金刚石轮片14之间的两个螺距t2相等,其余n片金刚石轮片14之间的螺距t1相等。其中,t与d及△h的对应关系具体参考表1:其中,t与b、b及d的对应关系具体参考表2:当挤压丝锥的螺距≤0.7mm时,采用一对螺距错位的金刚石修正轮15进行修正可获得0.35~0.7mm螺距的挤压丝锥。其中,金刚石轮片14的螺距为0.7-2mm,金刚石轮片14的数量为6-17片,且螺距越小对应的数量越多,具体参考表:3:基本螺纹螺距t(mm)金刚石轮片14数量(片)0.7170.75160.8151121.25101.581.75726本发明采用多片单独精加工而成的金刚石轮片14组合形成多线磨轮,相比于现有的单线磨,本发明多线磨轮可以使工件一次性加工吃刀到位,并一次性磨全程而使工效提高数倍;采用多片单独精加工而成的金刚石轮片14组合形成多线磨轮,相比于现有的表面镀覆金刚砂的多线磨轮,本发明多线磨轮具有更长的使用寿命而极大降低了加工成本;采用主磨轮与一对螺距错位的金刚石修正轮15组合结构,通过金刚石修正轮15的修正可以获得螺距在0.35-0.7mm之间的小螺距挤压丝锥的高效加工成型,解决了目前单纯的厚度小于0.7mm多线磨轮难以成型的难题;采用多片金刚石磨轮外径阶梯式结构,可以有效实现精度公差的分配而提高挤压丝锥螺纹的加工精度。对上述实施例的多种修改对本领域的专业技术人员来说将是显而易见的,本文中所定义-般原理可以在不脱离本发明的精神或范围的情况下,在其它实施例中实现。因此,本发明将不会被限制于本文所示的这些实施例,而是要符合与本文所公开的原理和新颖特点相一致的最宽的范围。当前第1页12