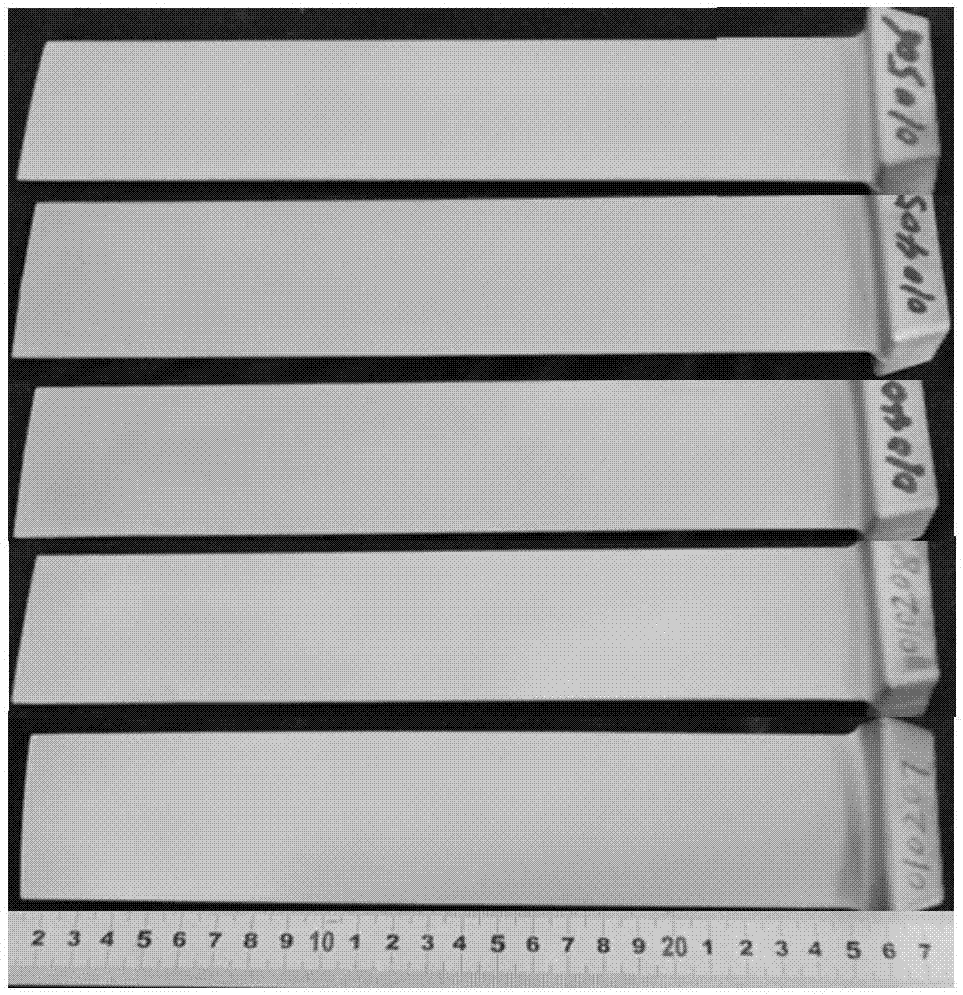
本发明涉及精密铸造的
技术领域:
,具体为一种熔模铸造γ-tial基合金叶片模壳的制备方法。
背景技术:
:γ-tial合金由于其低密度、高强度、高弹性模量及其良好的高温性能而成为新一代航空航天和汽车领域中的轻质结构材料,但影响tial元件广泛应用的最大障碍是其室温脆性和难加工性。熔模精密铸造作为一种可生产形状复杂、近净形结构件的技术是解决上述问题的有效方法,并具有良好的经济性。发明人已发明一项专利《一种制备熔模铸造γ-tial基合金模壳的方法》,适用于合金中al含量大于50at.%的tial精密铸造技术,但目前迫切需要应用的tial合金中al含量的范围40~50at.%,上述专利中主成分刚玉的显现惰性不足,叶片等铸件表面有明显的沾污层。因此,开发一种更为稳定的模壳体系具有重要的意义。美国通用电器(ge)公司已成功将tial合金应用于其先进的航空发动机低压涡轮叶片,其制造方法为重力铸造制备叶片毛坯,再利用电化学加工成净尺寸叶片。tial合金净尺寸铸造的难点在于:熔融状态的tial合金活性高,几乎与所有的耐火材料发生化学反应,损坏tial叶片表面质量和尺寸精度。近年来,氧化钇由于其相对较高的化学稳定性在钛合金精密铸造中应用很多,但与之相适应的粘结剂技术却是各商家与研究工作者严守的秘密,料浆寿命低是目前国内外面临的严峻问题。粘结剂是钛及钛铝基合金铸造工艺中最为关键的环节,必须满足能够粘结耐火材料并具有湿态与高温强度的使用要求。同时,焙烧后的产物应对液态tial有较好的化学稳定性。熔模铸造中常用的粘结剂有水玻璃、硅溶胶和硅酸乙酯,但其焙烧产物sio2与液钛反应强烈而不能用于精密高端部件的制造。经过多年的研发,锆或稀土溶胶是目前钛及钛铝基合金熔模精铸的常用粘结剂,一定程度上满足使用要求,但其料浆稳定性差为精铸件的批量生产带来严重障碍。tial合金精密铸造另一难点在于:tial合金流动性差,疏松倾向高,对于长宽比较大的叶片或结构复杂的扩压器等结构件只有在强大的离心力协助作用下才能完成充型。大量研究表明,铸件心部疏松可以通过调整浇注温度场的方式解决,而表面疏松与模壳表面质量及其组成结构设计密切相关。因此,开发一种tial合金叶片精密铸造用模壳制备方法具有重要的实际意义。技术实现要素:本发明的目的是提供一种结构稳定的熔模铸造γ-tial基合金叶片模壳的制备方法,该方法可以解决高活性、低塑性tial合金叶片近净尺寸成形、消除叶片表面疏松等缺陷控制难题,满足精铸tial叶片批量生产的需求,但不限于叶片零件,也适用于tial扩压器、涡流器、增压器涡轮等大中小型零件的精密铸造。本发明的技术方案是:一种熔模铸造γ-tial基合金叶片模壳的制备方法,包括如下步骤:1)将粒度为200~400目的氧化钇粉与有机溶胶按重量比为5.0:1~7.0:1配制成流杯粘度为10~40秒的料浆;2)将上述料浆涂挂在蜡模上,撒粒度为100~16目的氧化钇砂、刚玉砂、铝钒土砂、上店土砂或石英砂,干燥;如此反复7~8次,最后一层涂挂料浆,干燥;3)脱蜡,烧结。所述的熔模铸造γ-tial基合金叶片模壳的制备方法,步骤1)所述料浆制备过程中,添加活性剂、消泡剂、分散剂,活性剂占料浆的重量含量为1~5‰,消泡剂占料浆的重量含量为1~3‰,分散剂占料浆的重量含量为1~5%,在搅拌状态下将氧化钇粉与活性剂、分散剂加入到有机溶胶中,再加入消泡剂,搅拌5小时以上,然后放置4~12小时。所述的熔模铸造γ-tial基合金叶片模壳的制备方法,步骤2)所述的蜡模组浸入流杯粘度为30~40秒的料浆中3~10秒,撒粒度为100~65目的氧化钇砂、刚玉砂或石英砂,室温下干燥3~15小时,重复上述操作第2层,形成面层;然后涂挂第3~7层料浆,料浆流杯粘度为10~30秒,每层涂挂后撒粒度为45~16目的刚玉砂、铝钒土砂或上店土砂,室温下干燥4~30小时,形成加固层;最后一层涂挂流杯粘度为10~30秒的料浆,室温下干燥时间40~60小时。所述的熔模铸造γ-tial基合金叶片模壳的制备方法,加固层料浆为刚玉粉或铝钒土与硅溶胶按重量比3.0:1~4.0:1配制而成。所述的熔模铸造γ-tial基合金叶片模壳的制备方法,最后一层料浆为刚玉粉、铝钒土、上店土和煤矸石粉之一与硅溶胶按重量比3.0:1~4.0:1配制而成。所述的熔模铸造γ-tial基合金叶片模壳的制备方法,有机溶胶为过渡元素氧化物的有机溶胶;或者,有机溶胶为ti、zr、th过渡元素的有机金属化合物的有机溶胶;或者,有机溶胶为稀土元素的有机溶胶;有机溶胶的流杯粘度为10~30秒。所述的熔模铸造γ-tial基合金叶片模壳的制备方法,步骤3)脱腊后形成的模壳在室温放置4~10小时后再进行烧结,烧结温度在600~1200℃,保温1~4小时后,冷却至室温。本发明的设计原理是:本发明是基于分散剂位阻效应或一定的电荷排斥原理,抑制粉料颗粒之间相互团聚的一种方法,从而达到延长料浆寿命的目的。本发明基于模壳结构设计,使tial熔融液在充型凝固瞬间在其表面形成快冷层,实现由表及里的凝固顺序,从而将表面疏松引至叶片心部,通过后续热等静压工序消除疏松缺陷。本发明的优点及有益效果是:1.本发明制备的模壳系统适合于浇注高活性tial合金,达到净尺寸精铸tial叶片及其它结构件的表面精度要求。2.本发明采用的耐火材料是电熔y2o3,其结构致密,热膨胀系数小,有良好的化学稳定性,是一种优良的精铸用耐火材料。3.本发明采用的粘结剂是一种有机溶胶,该溶胶性质稳定,可放置几个月到三年内性能不变,用流杯粘度计测定其流杯粘度为10~30秒,该溶胶在适当的条件下会发生水解-缩合反应,形成三维网络结构,将耐火材料颗粒粘结在一起,形成一定的强度。4.本发明中采用的添加助剂是一种无机铵或有机铵或混合物,有利于分散料浆团聚,延长料浆寿命。5.本发明用于制备模壳时,在搅拌状态下将粉料与活性剂、分散剂加入到粘结剂中,再加入少量的消泡剂,充分搅拌,最好在5小时以上,然后放置4~12小时,利于料浆回性;充分回性的料浆,涂挂性与流动性均好,硬化时胶凝收缩小,型壳强度高。5.本发明中的活性剂具有良好的润湿与渗透能力,泡沫少且易于消泡,不影响料浆的稳定性,无毒、价廉。6.本发明中的面层料浆粉液重量比控制在5.0:1至7.0:1之间变化,主要取决于所需叶片铸件表面粗糙度的要求;加固层可采用硅溶胶与刚玉粉配制的料浆,也可采用硅溶胶与铝钒土/上店土配制的料浆,加固层料浆粘度依次降低,以利于涂浆能渗入到上一层涂料的撒砂间隙中并能良好的润湿,以排除砂粒间隙中的空气,使各层之间形成均匀连续而又紧密镶嵌的整体,防止形成孔洞、裂隙和分层,可以保证型壳结构强度。7.本发明方法制备模壳时,撒砂用氧化钇砂/刚玉砂/铝钒土砂/上店土砂从里到外逐渐加粗,1~2层撒较细的砂子,如:100~65目,加固层通常撒较粗的砂子,如:45~16目。为了避免分层,所选用砂子的粒度与料浆的粘度要适宜,既不会影响型壳表面质量,也有利于形成比较粗糙的背面,从而有利于同加固层涂料牢固地结合。8.本发明可以用水蒸汽进行脱蜡,方便无毒性。附图说明图1-图2是采用本发明得到的γ-tial叶片样件及在1000lux光度下表面形貌。其中,图1是γ-tial叶片样件;图2是1000lux光度下表面形貌。图3是采用本发明得到的γ-tial叶片x射线检测结果,未见明显氧化钇高密度夹杂缺陷。图4是电子探针检测γ-tial叶片表面各元素沿横截面由表及里分布情况,结果显示叶片铸件表面没有明显的成分变化。图中,横坐标distancefromcastsurface代表至铸件表面的距离(mm);纵坐标counts代表计数。具体实施方式在具体实施过程中,本发明熔模铸造γ-tial基合金叶片模壳的制备方法,包括如下步骤:1)将粒度为200~400目的氧化钇粉与有机溶胶按重量比为5.0:1~7.0:1配制成流杯粘度为10~40秒的料浆,氧化钇粉为烧结态或融熔态;其中,有机溶胶为过渡元素氧化物的有机溶胶、ti、zr、th过渡元素的有机金属化合物的有机溶胶或稀土元素(主要是y或la系元素)的有机溶胶,流杯粘度为10~30秒。2)将上述料浆涂挂在蜡模上,撒粒度为100~16目的加固砂,干燥;如此反复7~8次,最后一层涂挂料浆,干燥;3)脱蜡,烧结。脱腊后形成的模壳在室温放置4~10小时后再进行烧结,烧结温度在600~1000℃,保温1~4小时后,冷却至室温。步骤1)所述料浆制备过程中,添加活性剂、消泡剂、分散剂,其中活性剂占料浆的重量含量为1~5‰,消泡剂占料浆的重量含量为1~3‰,分散剂占料浆的重量含量为1~5%,在搅拌状态下将氧化钇粉与活性剂、分散剂加入到有机溶胶中,再加入消泡剂,搅拌5小时以上(一般为5~10小时),然后放置4~12小时。其中,消泡剂可以是醇类,如:正辛醇、异辛醇等,还可以为乙二醇丁醚磷酸酯;常用的活性剂可以为jfc(聚氧乙烯烷基醇醚)、环氧化合物(如:聚氧乙烯烷基醇醚)或聚乙二醇类活性剂等,分散剂可以选择常用的无机铵类或有机铵类或混合物。步骤2)所述的蜡模组浸入流杯粘度为30~40秒的料浆中3~10秒,撒粒度为100~65目的氧化钇砂、刚玉砂或石英砂,室温下干燥3~15小时,重复上述操作第2层,形成面层;然后涂挂第3~7层料浆,料浆流杯粘度为10~30秒,每层涂挂后撒粒度为45~16目的刚玉砂、铝钒土砂或上店土砂,室温下干燥4~30小时,形成加固层,加固层料浆为刚玉粉或铝钒土与硅溶胶按重量比3.0:1~4.0:1配制而成。最后一层涂挂流杯粘度为10~30秒的料浆,室温下干燥时间40~60小时,最后一层料浆为刚玉粉、铝钒土、上店土和煤矸石粉之一与硅溶胶按重量比3.0:1~4.0:1配制而成,刚玉粉、铝钒土、上店土和煤矸石粉为烧结态或融熔态。本发明中,干燥方法为温湿度适宜的干燥车间,干燥车间温度为22±2℃,湿度为30~70%。下面结合实施例对本发明做详细说明,但本发明的保护范围不仅限于下述的实施例。实施例1本实施例中,采用320目氧化钇与钇溶胶(金属钇的有机溶胶)重量比为5.5:1,活性剂(聚氧乙烯烷基醇醚,又称jfc)的重量含量为4‰,消泡剂gp(乙二醇丁醚磷酸酯)的重量含量为2‰,分散剂的重量含量为3%,在搅拌状态下将氧化钇粉与活性剂、分散剂加入到有机溶胶中,再加入消泡剂,充分搅拌5小时,然后放置4小时,配制料浆100kg,所得料浆流杯粘度为30秒。将清洗好的蜡模组浸入料浆中5秒后取出,取出控净多余的料浆,撒100~60目刚玉砂,干燥后重复上述操作第二层,每层室温下干燥12小时,形成面层;涂挂第3~7层料浆,料浆流杯粘度为20秒,每层涂挂后撒粒度为45~24目的刚玉砂,每层室温下干燥24小时,形成加固层,加固层料浆用刚玉粉与硅溶胶按重量比3.5:1配制而成;最后一层只涂挂加固层所采用的料浆,室温下干燥时间48小时,具体工艺参数如表1。充分干燥后的蜡模用水蒸汽脱蜡,脱好蜡的模壳在室温放置6小时后进行烧结,烧结温度为1100℃,保温2小时冷却至室温,所得模壳内表面光洁,强度高。表1层数流杯粘度(秒)温度(℃)湿度(%)室温(℃)撒砂干燥时间1~2层3015~2040~8022±2100~60目12小时3~7层2015~2030~6022±245~24目24小时8层2015~2030~6022±2不撒砂48小时将上述方法制备的模壳进行长度为300mm的ti-46al合金叶片的精密铸造试验。将模壳放入砂箱调正固定好,在马弗炉中预热至950℃保温2小时。用水冷铜坩埚感应炉熔炼γ-tial合金,离心铸造γ-tial叶片。叶片表面光洁、无粘砂现象,在1000lux的照度下没有肉眼可见的疏松。结果分析:如图1-图2所示,利用本发明得到的γ-tial叶片样件表面在1000lux光度下观察未发现肉眼可见的表面疏松。如图3所示,采用本发明得到的γ-tial叶片在x射线探伤检测中未见到氧化钇高密度夹杂缺陷,可见本发明方法制备的模壳质量稳定,可以有效控制叶片冶金质量。如图4所示,采用本发明得到的γ-tial叶片铸件由表面及里元素成分没有明显的波动,表明本发明制备的模壳未与γ-tial合金发生界面反应。比较例用常规的方法制备氧化钇模壳进行浇铸ti-46al合金叶片试验,将模壳放入砂箱调正固定好,在马弗炉中预热至950℃保温2小时。用水冷铜坩埚感应炉熔炼γ-tial合金,离心铸造纯钛的拉伸试棒,以与实施例1进行比较。结果发现,叶片表面粘砂严重,存在严重的表面疏松,表明此发明明显改善叶片表面质量。实施例2与实施例1不同之处是:本实施例中,采用300目氧化钇粉与钇溶胶(金属钇的有机溶胶)重量比为6:1,活性剂(聚氧乙烯烷基醇醚)的重量含量为3‰,消泡剂(异辛醇)的重量含量为2‰,分散剂的重量含量为2%,在搅拌状态下将氧化钇粉与活性剂、分散剂加入到有机溶胶中,再加入消泡剂,充分搅拌8小时,然后放置8小时,配制料浆100kg,所得料浆流杯粘度为35秒。将清洗好的蜡模组浸入料浆中4秒后取出,取出控净多余的料浆,撒100~65目刚玉砂,干燥后重复上述操作第二层,每层室温下干燥10小时,形成面层;涂挂第3~7层料浆,料浆流杯粘度为25秒,每层涂挂后撒粒度为45~24目的刚玉砂,每层室温下干燥20小时,形成加固层,加固层料浆用刚玉粉与硅溶胶按重量比3:1配制而成;最后一层涂挂加固层所采用的料浆,室温下干燥时间40小时,具体工艺参数如表1。充分干燥后的蜡模用水蒸汽脱蜡,脱好蜡的模壳在室温放置4小时后进行烧结,烧结温度为1000℃,保温4小时冷却至室温,所得模壳内表面光洁,强度高。实施例3与实施例1不同之处是:本实施例中,采用325目氧化钇粉与锆溶胶(金属锆的有机溶胶)重量比为4:1,活性剂(聚异丙二醇醚)的重量含量为1‰,消泡剂(正辛醇)的重量含量为1‰,分散剂的重量含量为4%,在搅拌状态下将氧化钇粉与活性剂、分散剂加入到有机溶胶中,再加入消泡剂,充分搅拌6小时,然后放置12小时,配制料浆10kg,所得料浆流杯粘度为22秒。将清洗好的蜡模组浸入料浆中3秒后取出,取出控净多余的料浆,撒100~65目氧化钇砂,干燥后重复上述操作第二层,每层室温下干燥15小时,形成面层;涂挂第3~7层料浆,料浆流杯粘度为15秒,每层涂挂后撒粒度为24~16目的刚玉砂,每层室温下干燥30小时,形成加固层,加固层料浆用刚玉粉与硅溶胶按重量比4:1配制而成;最后一层涂挂加固层所采用的料浆,室温下干燥时间60小时,具体工艺参数如表1。充分干燥后的蜡模用水蒸汽脱蜡,脱好蜡的模壳在室温放置10小时后进行烧结,烧结温度为950℃,保温1小时冷却至室温,所得模壳内表面光洁,强度高。实施例和比较例结果表明,本发明制备模壳工艺简单,料浆性能容易控制,寿命长,模壳内表面质量好,具有适宜的强度,浇铸叶片表面光滑,没有明显的表面疏松,此发明不仅限于精密铸造tial叶片,同样适合于浇注tial基合金其它结构件。当前第1页12