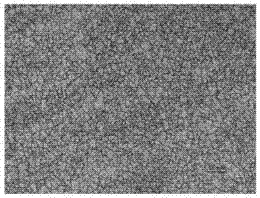
本发明涉及金属塑性成形
技术领域:
,尤其涉及一种均匀低应力值锥形药型罩的制备方法。
背景技术:
:典型的聚能装药射流具有较高的头部速度(≥8500m/s)和低的尾部速度(约3000m/s),这种速度梯度使射流在一定的炸高条件下能拉得很长(达到20~100倍药型罩口径长度),具有高侵彻能力。射流的侵彻能力是与连续射流长度成正比,但是由于金属内部缺陷与射流膨胀性作用,射流最终在轴向会断裂成一段段的颗粒,而限制了连续射流的长度,以及侵彻能量的传递,且断裂颗粒间相互扰动,其侵彻能力急剧下降。现有98%破甲战斗部采用铜药型罩,其成形工艺主要有电铸、旋压、冲压、冷挤压、温挤压,其中电铸、冷挤压成形药型罩是发展的重点。国外研究机构对铜药型罩内部组织(晶粒度、形貌、晶界等)、制造工艺和破甲性能之间的关系作了大量而深入的研究。研究表明,药型罩产品尺寸精度、表面质量,以及内在应力状态、晶粒尺寸、晶界形貌等参数对侵彻能力影响明显,其中药型罩产品尺寸精度、内部应力值与分布是影响侵彻稳定性的关键因子。在药型罩产品设计、验收标准中提出“三高一低”要求,即“高尺寸精度、高几何对称性、高光洁度、低应力值均匀分布”。随着新一代反应装甲、陶瓷装甲、复合装甲的发展,对药型罩毁伤威力、稳定性提出更高要求,制备高品质药型罩已成为发展高性能战斗部的关键技术之一。在相同装药、炸高,以及药型罩结构与材料条件下,国外的药型罩破甲跳差≤8%,国内药型罩产品破甲跳差高达30%以上。通过逆向工程分析,采用现代材料分析方法研究表明,国外冷挤压成形纯铜药型罩的平均应力值10~30mpa,锥角偏差≤2′,国内冷挤压成形锥形药型罩顶部应力值达到120~200mpa,且分布不均匀,严重影响产品质量稳定性。技术实现要素:本发明解决的技术问题在于提供一种均匀低应力值锥形药型罩的制备方法,制备的药型罩尺寸精度高、几何对称性好、应力值低,在精密切削加工和使用过程中尺寸稳定性好,能显著提升破甲战斗部药型罩的侵彻能力和稳定性。一种均匀低应力值锥形药型罩的制备方法,包括多道次挤压成形、振动时效处理、深冷处理步骤,所述多道次挤压成形是在三向压应力和变形速率为5~10mm/s的作用下,经过4~8道次的挤压变形,每道次的变形量在5~50%。优选的,所述多道次挤压成形中在坯料表面和模具型腔内表面涂布润滑剂。所述多道次挤压成形的锥形药型罩圆周壁厚差≤0.1mm。上述振动时效处理进行1~3次,处理时间20~60分钟。上述深冷处理,深冷介质为液氮,冷却温度-135~-145℃,冷却次数2~4次,每次15~45分钟。本发明实现锥形药型罩成形与表面质量控制,消除和均化锥形药型罩不同部位应力梯度,释放和均匀精整形药型罩的应力,保证药型罩的尺寸精度与表面质量,同时获得均匀低应力值。本发明是通过下列技术方案实现:一种均匀低应力值锥形药型罩的制备方法,经过下列工艺步骤实现:(1)坯料的制备:依据设计的锥形铜药型罩形状结构,计算得出原材料的体积,并依据塑性加工成形理论与近均匀塑性变形原理,以及数值模拟仿真分析,选取合适的坯料尺寸,根据零件体积不变原理切取相应的铜棒材长度,铜棒材的直径φ20~170mm,铜材料可以是tu1、tu2、t2、t3等。(2)均匀化热处理:将步骤(1)所得坯料在真空热处理炉中380~550℃条件下保温退火1~3h,再随炉冷却至100℃以下出炉,真空度≥3×10-3pa,以获得均匀的组织,并降低材料的加工硬度,提高材料的塑性成形性。(3)多道次挤压成形:将步骤(2)所得的坯料放入挤压模具模腔内,在三向压应力和变形速率为5~10mm/s的作用下,经过4~8道次的挤压变形,每道次的变形量在5~50%之间,在成形过程中坯料表面和模具型腔内表面涂布一层润滑剂,使多道次挤压成形后锥形药型罩圆周壁厚差≤0.1mm,从而获得所需形状、尺寸的锥形药型罩。(4)振动时效处理:将步骤(3)所得的药型罩构件进行振动时效处理1~3次,采用智能振动时效ifvsr-2000型设备,通过扫频由设备自动选择共振峰,处理时可由加速度幅值来控制,偏心为2档,处理时间20~60分钟;(5)再结晶热处理:将步骤(4)获得的锥形药型罩放入真空热处理炉中,在150~350℃条件下保温45~75min,通过再结晶退火处理进行晶界优化,以及位错的滑移、攀移,使局部点阵和晶界面取向变动,促使退火过程中动态再结晶和孪晶的形成,降低加工硬化效应,锥形药型罩平均晶粒尺寸≤10μm。(6)精整形:将步骤(5)所得的构件放入挤压模具模腔内,在三向压应力和变形速率为5~10mm/s的作用下,经过1~4道次的精整形,每道次的变形量≤2%,使锥形药型罩圆周壁厚差≤0.1mm、表面粗糙度达到ra0.2μm。(7)深冷处理:将步骤(6)所得的构件放入深冷处理装置中,深冷介质为液氮(-196℃),冷却温度-135~-145℃,冷却次数2~4次,每次15~45分钟。所述步骤(3)中4~8道次的挤压变形,根据锥形药型罩的口径尺寸、内锥角度、壁厚等形状结构特点,设计所需的变形道次等工序,尺寸规格小、形状简单的零件变形道次,相同口径药型罩内形为单锥角比双锥角的变形道次少。所述步骤(3)中变形量为5~50%,根据变形道次和零件结构特点,合理分配每道次的变形量,随变形道次的增加变形量降低,通过阶梯变形量控制药型罩的塑性成形。所述步骤(3)中润滑剂,包括茶油、精冲油、蓖麻油、菜籽油等常用润滑剂中一种或几种混合,在每道次成形过程中涂布在坯料、模具型腔表面,减少坯料与模具接触面间的摩擦力,提高成形过程中金属的流动性,并改善成形构件的表面质量。所述步骤(4)中1~3次的振动时效处理,根据药型罩内孔深度、底部与口部壁厚尺寸等参数确定,在4~8道次的挤压变形过程中增加振动时效处理工序。所述步骤(6)中1~4道次的精整形,根据药型罩形状、口径等参数确定精整形次数。所述步骤(7)中2~4次的深冷处理,根据单件药型罩重量及壁厚等参数,确定冷却次数。有益效果本发明通过累积大变形控制技术、振动时效处理、深冷处理技术等工艺步骤和参数的调整,实现锥形药型罩成形与表面质量控制,消除和均化锥形药型罩不同部位应力梯度,释放和均匀精整形药型罩的应力,保证药型罩的尺寸精度与表面质量,同时获得均匀低应力值。通过该方法获得均匀、细小等轴晶组织结构,不同部位应力值低,且均匀,为高性能细晶铜锥形药型罩的研制提供了一种新的制备方法。本发明克服了常规制备方法获得构件表面质量差、内部晶粒尺寸差异大、应力分布不均等技术难题,同时还具有生产效率高、工艺稳定性好、易于实现工业化生产等优点。(1)产品尺寸一致性好。多道次挤压成形+振动时效+再结晶热处理+深冷处理工艺方法,产品不同部位应力值达到电铸药型罩水平,平均应力值≤30mpa,锥度角度偏差≤2′。(2)产品材料利用率高。采用多道次挤压成形方法生产的锥形药型罩外表面仅留0.7~1.2mm的机械切削加工余量,内表面完全不加工,可以显著提高锥形药型罩材料利用率。(3)产品性能好。采用多道次挤压成形方法生产的锥形药型罩,其金属纤维沿零件轮廓形状分布,且连续致密,通过振动时效+再结晶热处理+深冷处理,获得低应力状态等轴细晶组织;同时锥形药型罩内形不加工,克服了加工切削刀痕对药型罩高温、高压作用下射流塑性流动性、延展性不好的技术难题。(4)产品质量有效控制。通过对变形道次、变形量、温度与时间等工艺参数窄规格控制,获得所需的组织结构,实现零件产品质量的有效性控制,提高产品的稳定性与一致性。附图说明图1紫铜坯料的晶粒组织(金相显微镜放大100倍,平均晶粒尺寸约为130μm)图2双锥药型罩多道次挤压成形工序图图3振动时效工序图4精整形后的显微组织(金相显微镜放大500倍,平均晶粒尺寸约为10μm)图5药型罩不同部位应力测试示意图具体实施方式以下结合具体实施例对本发明作进一步说明。实施例1(1)坯料的制备:以内部形状是双锥结构的变壁厚药型罩为例,药型罩口径尺寸为φ185mm、高度170mm、内锥深度162mm、壁厚4~5.5mm,药型罩的顶部小锥角30°、大锥角60°,大锥角与小锥角之间过渡圆弧为r152mm;依据塑性加工成形理论与近均匀塑性变形原理,在药型罩外表面留1mm的加工余量,并在药型罩锥顶设计有φ20mm的成形工艺凸台;采用ug、deform软件对成形过程进行模拟分析与优化,并计算出坯料的体积,选取φ90mm的挤制t2铜棒为原材料,下料并车削外表面制成直径88mm、高度55mm的坯料;该t2紫铜棒材的杂质元素含量如表1所示:表1t2铜棒材的杂质元素含量牌号bisbasfenisns0zn总和t20.0010.0020.0020.0050.0020.0020.0040.0050.0040.1(2)均匀化热处理:将步骤(1)所得坯料在vqg-2500型智能控温真空热处理炉中480±1℃保温1小时,真空度为1.5×103pa,保温热处理后进行随炉冷却至80℃出炉,以获得成分、组织均匀的坯料,硬度hb35~38,cu晶粒尺寸约为130μm,如图1所示。(3)多道次挤压成形:将步骤(2)所得的坯料放入挤压模具模腔内,在三向压应力和一定的变形速率作用下,经过7道次的挤压变形,获得锥形药型罩构件,成形工序如图2所示,每道次变形量分配如表2所示。多道次挤压成形模具包括凹模系统、凸模系统、顶出系统,多道次挤压成形设备为1600吨的液压机,液压机的变形速率5~10mm/s,挤压模具的凹模系统安装在液压机的工作台面上,顶出系统与液压机的顶出机构相连接,凸模系统和液压机的工作滑块相连接,通过液压机的工作滑块带动挤压凸模进行挤压成形,挤压凸模与挤压凹模配合使坯料处于三向应力状态。第1道次为坯料的大变形开坯成形,获得锥形坯;后续2-6道次成形为扩孔挤压成形(变形量小于40%),使药型罩的壁部逐渐减薄,随着挤压道次增加加工硬化效应增强,变形量逐渐减小;最后1道次为终成形,提高成形件的尺寸精度与尺寸稳定性,变形量一般小于10%。经过多道次挤压变形后,获得所需形状、尺寸、表面质量以及具有一定力学性能的锥形药型罩。表2挤压变形工艺参数等(4)振动时效处理:采用智能振动时效ifvsr-2000型设备,通过扫频由设备自动选择共振峰,处理时可由加速度幅值来控制,偏心为2档,在步骤(3)中设置3次振动时效处理,如图3所示。第1次振动时效处理在变形道次2后,振动时间25分钟;第二次振动时效出在变形道次5后,振动时间35分钟;第3次振动时效处理在变形道次7后,振动时间45分钟。(5)再结晶热处理:将步骤(4)获得的锥形药型罩放入真空热处理炉中,在320℃条件下保温60min,通过再结晶退火处理进行晶界优化,以及位错的滑移、攀移,使局部点阵和晶界面取向变动,促使退火过程中动态再结晶和孪晶的形成,降低加工硬化效应,锥形药型罩平均晶粒尺寸10μm,如图4所示。(6)精整形:将步骤(5)所得的构件放入挤压模具模腔内,在三向压应力和变形速率为5mm/s的作用下,经过2道次的精整形,每道次的变形量约1%,锥形药型罩圆周壁厚差0.04~0.07mm、表面粗糙度ra0.12~0.2μm、锥角度偏差不大于2′。(7)深冷处理:将步骤(6)所得的构件放入深冷处理装置中,深冷介质为液氮(-196℃),冷却温度-135~-145℃,冷却次数2次,每次30分钟,中间间隔1小时。将上述得到的药型罩,采用x射线应力测试方法,得到的应力值如表3所示,沿药型罩圆周方向、母线方向的平均应力值19~22mpa。表3药型罩不同部位的应力值测试部位12345平均值1-小锥23.920.121.522.824.322.522-圆弧22.319.420.417.319.419.763-大锥16.518.320.719.620.119.044-口部23.219.718.320.218.620.00平均值21.47519.37520.22519.97520.6实施例2(1)坯料的制备:以内部形状是单锥结构的等壁厚药型罩为例,药型罩口径尺寸为φ160mm、高度152mm、内锥深度138mm、壁厚4.2mm,内锥角60°,依据塑性加工成形理论与近均匀塑性变形原理,在多道次挤压药型罩成形件外表面留0.8mm的加工余量,并在药型罩成形件顶部设计有φ15mm的成形工艺凸台;采用ug、deform软件对成形过程进行模拟,并计算出坯料的体积,选取φ50mm的拉制t2铜棒为原材料,下料并车削外表面制成直径49mm、高度80mm的坯料。(2)均匀化热处理:将步骤(1)所得坯料在vqg-2500型智能控温真空热处理炉中420±1℃保温1小时,真空度为1.5×10-3pa,保温热处理后进行随炉冷却至80℃出炉,以获得成分、组织均匀的坯料,硬度hb32~35,cu晶粒尺寸约为70μm。(3)多道次挤压成形:将步骤(2)所得的坯料放入挤压模具模腔内,在三向压应力和一定的变形速率作用下,经过6道次的挤压变形,每道次变形量分配如表4所示。多道次挤压成形模具包括凹模系统、凸模系统、顶出系统,多道次挤压成形设备为1600吨的液压机,液压机的变形速率5~10mm/s,挤压模具的凹模系统安装在液压机的工作台面上,顶出系统与液压机的顶出机构相连接,凸模系统和液压机的工作滑块相连接,通过液压机的工作滑块带动挤压凸模进行挤压成形,挤压凸模与挤压凹模配合使坯料处于三向应力状态。第1道次为坯料的大变形开坯成形,获得锥形坯;后续2-5道次成形为扩孔挤压成形(变形量小于40%),使药型罩的壁部逐渐减薄,随着挤压道次增加加工硬化效应增强,变形量逐渐减小;最后1道次为终成形,提高成形件的尺寸精度与尺寸稳定性,变形量一般小于10%。经过多道次挤压变形后,获得所需形状、尺寸、表面质量以及具有一定力学性能的锥形药型罩。表4道次变形量等参数(4)振动时效处理:采用智能振动时效ifvsr-2000型设备,通过扫频由设备自动选择共振峰,处理时可由加速度幅值来控制,偏心为2档,在步骤(3)中设置2次振动时效处理。第1次振动时效处理在变形道次3后,振动时间30分钟;第二次振动时效处理在变形道次6后,振动时间45分钟。(5)再结晶热处理:将步骤(4)获得的锥形药型罩放入真空热处理炉中,在250℃条件下保温60min,通过再结晶退火处理进行晶界优化,以及位错的滑移、攀移,使局部点阵和晶界面取向变动,促使退火过程中动态再结晶和孪晶的形成,降低加工硬化效应,锥形药型罩平均晶粒尺寸5μm。(6)精整形:将步骤(5)所得的构件放入挤压模具模腔内,在三向压应力和变形速率为5mm/s的作用下,经过1道次的精整形,变形量约1.5%,锥形药型罩圆周壁厚差0.03~0.05mm、表面粗糙度达到ra0.08~0.16μm、锥角度偏差不大于2′。(7)深冷处理:将步骤(6)所得的构件放入深冷处理装置中,深冷介质为液氮(-196℃),冷却温度-135~-145℃,冷却次数5次,冷却时间1小时,中间间隔1小时。将上述得到的药型罩,采用x射线应力测试方法,得到的应力值如表5所示,沿药型罩圆周方向、母线方向的平均应力值18~22mpa。表5药型罩不同部位的应力值测试部位12345平均值1-小锥20.621.320.922.822.721.662-圆弧19.519.618.818.917.218.803-大锥18.318.917.419.718.118.484-口部21.120.419.318.316.519.12平均值19.87520.0519.1019.92518.625结果表明,通过该方法获得低应力、均匀细小等轴晶组织药型罩,平均晶粒尺寸≤10μm,圆周方向、母线方向的平均应力值约22mpa;药型罩圆周壁厚差≤0.07mm、表面粗糙度达到ra0.2μm、锥角度偏差不大于2′。当前第1页12