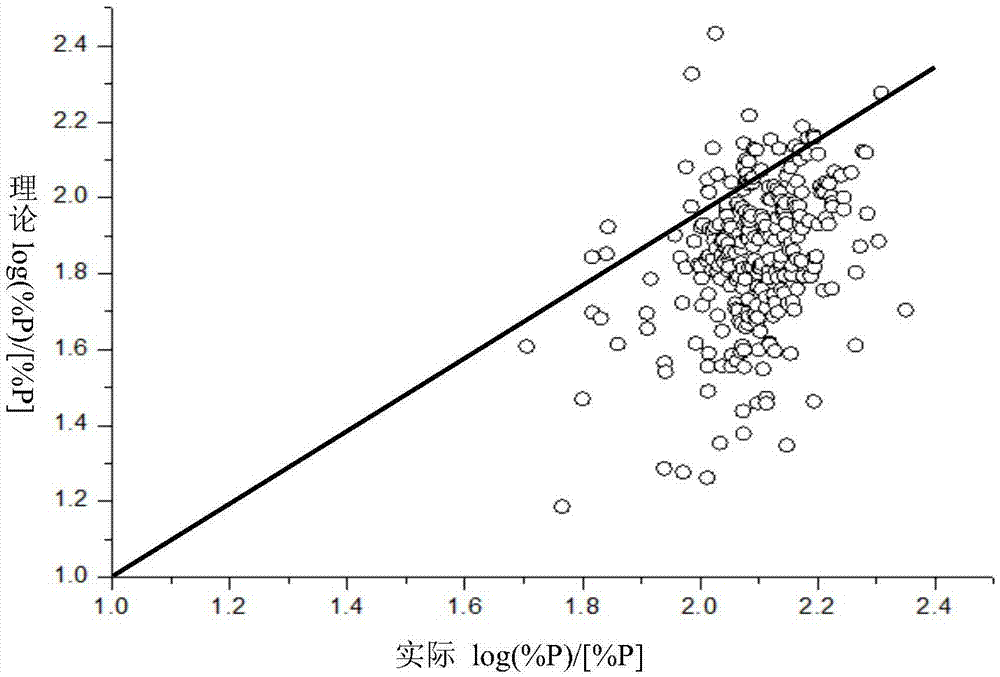
本发明属于转炉炼钢
技术领域:
,具体涉及冷态钢渣再资源化炼钢工艺。
背景技术:
攀钢炼钢采用钒钛磁铁矿进行冶炼,铁水中含0.3%左右的v,因此在转炉炼钢之前,需先提钒,经过转炉提钒,铁水中v被氧化,同时铁水中si、mn等元素也被氧化,c元素部分氧化,因而半钢同普通铁水有明显的差异。由于含钒铁水在转炉中同时脱磷提钒工艺目前还未走通,铁水经过脱硫、提钒预处理后,p含量基本上没有变化,仍然为0.060%左右。因而对于半钢转炉炼钢而言,主要是通过外加含有cao、sio2的造渣材料来保证炼钢过程形成具有一定脱磷能力的炉渣,然后根据磷的分配比,通过加入一定量的造渣材料来使得半钢中的磷含量降至钢种磷含量要求。其中,转炉炼钢通常采用的造渣材料有活性石灰、高镁石灰、复合渣等。节能降耗已成为当前钢铁企业普遍关注的重要课题之一,如何在炼钢生产中既满足冶炼工艺需求同时又降低炼钢成本事关企业发展的经济命脉。对此,攀钢西昌钢钒半钢炼钢曾经采用murc(multi-refiningconverter)工艺进行过转炉试验,murc工艺是铁水在转炉中脱硅、脱磷后倒炉排渣,保留铁水,脱磷渣一般倒出50%,然后造脱碳渣进行脱碳,脱碳后出钢,其脱碳渣可直接留在炉内用于下一炉脱磷吹炼,然而采用murc工艺总体上不经济,主要体现在:(1)由于[si]、[mn]等元素缺失,转炉初期渣形成速度慢,平均形成时间在3分半左右,在转炉前期放渣时,初渣才刚好形成,还未充分参与脱磷反应;(2)脱磷期结束,正直碳氧反应剧烈期,炉渣泡沫化严重,倒渣困难,倒渣过程钢铁料流失严重;(3)由于提钒工序中存在热量损失,造成半钢炼钢热量不足,转炉前期倒炉放渣将进一步增加了热量损失。技术实现要素:本发明解决的技术问题是炼钢产生的冷态钢渣没有得到充分利用,半钢炼钢生产成本高。本发明解决上述技术问题的技术方案是提供冷态钢渣再资源化炼钢工艺,包括转炉下料、吹炼以及出钢的步骤,所述下料的物料包括半钢铁水、石灰8~12kg/t钢、高镁石灰12~16kg/t钢、酸性复合渣7~10kg/t钢以及冷态钢渣15~20kg/t钢,其中酸性复合渣为含有sio2的造渣材料。其中,所述冷态钢渣的成分以质量百分数计包括cao:35~55%、sio2:8~20%、mgo:5~15%、feo:15~25%、fe2o3:5~10%、mno:5~10%、p:≤0.1%、s:≤0.5%、水分:<1%,余为杂质。进一步的,所述冷态钢渣粒度为30~50mm,熔点为1280~1350℃。其中,所述半钢铁水的成分以质量百分数计包括c:3.2~4.1%、si:0.015~0.030%、mn:0.02~0.04%、p:0.06~0.08%、s:≤0.015%,余量为fe和不可避免的杂质。进一步的,所述半钢铁水的入炉温度为1250~1360℃。其中,所述石灰中的cao质量含量为85~90%。其中,所述高镁石灰中的mgo质量含量为30~40%,cao质量含量为48~55%。其中,所述酸性复合渣中的sio2质量含量为45~55%。进一步的,转炉装入半钢铁水,开始吹炼后加入冷态钢渣。进一步的,三分之二的冷态钢渣在吹炼开始后6min内加完,剩下的三分之一冷态钢渣在接下来的4min内加完。进一步的,开始吹炼后将石灰、高镁石灰和酸性复合渣总用量的三分之二加入到转炉中,剩下三分之一的石灰、高镁石灰和酸性复合渣将分批在冶炼过程中加完。其中,所述吹炼的氧气流量为28000nm3/h,吨钢氧耗40~60nm3,所述吹炼的氧枪喷头距熔池金属液面基本枪位1.4~1.6m,吹炼枪位1.4m~1.6m,开吹枪位1.8m,拉碳枪位1.4m。本发明的有益效果是:本发明转炉半钢炼钢使用冷态钢渣替代部分石灰、高镁石灰和酸性复合造渣剂,有效减少了石灰、高镁石灰和酸性复合造渣剂等炼钢辅料的用量,与常规工艺相比,石灰的用量减少4~6kg/t钢,高镁石灰用量减少3~5kg/t钢,酸性复合造渣剂的用量减少2~4kg/t钢,降低了生产成本,实现了炼钢炉渣资源的循环利用,减少了堆放冷态钢渣的场地面积,减少了企业的环保压力,有助于钢铁企业的可持续发展;本发明转炉半钢炼钢使用冷态钢渣替代部分石灰、高镁石灰和酸性复合造渣剂,出钢钢水磷和硫含量均≤0.011%,满足钢种要求;本发明控制相应的炼钢参数、并优化加料方式,保证了熔渣的流动性和脱硫、脱磷能力。附图说明图1为半钢转炉脱磷理论磷分配比与实际磷分配比关系图。具体实施方式一方面,因为普通铁水中含有si元素,炼钢过程中氧化生产sio2,因而必须通过加入大量的石灰来使得炉渣具有一定的碱度,而攀钢采用半钢炼钢,原料铁水中只有很少量的si元素,加入石灰等材料只需要满足脱磷即可,因此能够使用p含量未达到饱和值的转炉渣。另一方面,有关钢铁液的脱磷热力学,尤其是铁水脱磷热力学,冶金工作者们已做了很多研究工作,形成了一套成熟的研究思路,得到了一系列的经验及半经验公式,用于指导实践生产,其中脱磷渣系的healy公式为当前最被认可:log(%p)/[%p]=0.072[(%cao)+0.3(%mgo)+0.6(%p2o5)+0.2(%mno)+1.2(%caf2)-0.5(%al2o3)]+11570/t-10.52采用上述公式对攀钢半钢转炉脱磷的理论和实际磷分配比进行对比分析,得到理论磷分配比与实际磷分配比之间的关系如图1所示,其中,直线代表理论平衡状态时的磷分配比情况,小圆代表实际磷分配比情况,从图上可以看出实际磷分配比低于理论分配比,表明转炉终渣磷含量未能达到理论平衡值,转炉终点钢渣仍然具备较好的脱磷能力。本发明基于上述研究,提出冷态钢渣再资源化炼钢工艺,既能充分利用冷态钢渣中大量的cao、sio2、mgo、feo等有益于炼钢的成分,又有助于降低转炉炼钢过程的钢铁料消耗,最终在实际使用过程中显著降低生产成本,步骤包括转炉下料、吹炼以及出钢,所述下料的物料包括半钢铁水、石灰8~12kg/t钢、高镁石灰12~16kg/t钢、酸性复合造渣剂7~10kg/t钢以及冷态钢渣15~20kg/t钢,其中酸性复合造渣剂为主要含有sio2的造渣材料。具体的,所述冷态钢渣的成分以质量百分数计包括cao:35~55%、sio2:8~20%、mgo:5~15%、feo:15~25%、fe2o3:5~10%、mno:5~10%、p:≤0.1%、s:≤0.5%、水分:<1%,余为杂质。进一步的,为了达到更好的使用效果,将所述冷态钢渣进行机械破碎,加工成粒度为30~50mm的块。进一步的,为了达到更好的使用效果,调整冷态钢渣的熔点为1280~1350℃。其中,半钢炼钢的原料除了半钢铁水,还可同时加入废钢,吹炼前控制半钢铁水的成分以质量百分数计包括c:3.2~4.1%、si:0.015~0.030%、mn:0.02~0.04%、p:0.06~0.08%、s:≤0.015%,余量为fe和不可避免的杂质。进一步的,控制半钢铁水的入炉温度为1250~1360℃。其中,所述石灰中的cao质量含量为85~90%。其中,所述高镁石灰中的mgo质量含量为30~40%,cao质量含量为48~55%。其中,所述酸性复合造渣剂中的sio2质量含量为45~55%。作为优选的,转炉装入半钢铁水,开始吹炼后加入冷态钢渣。作为优选的,三分之二的冷态钢渣在吹炼开始后6min内加完,剩下的三分之一冷态钢渣在接下来的4min内加完。作为优选的,开始吹炼后将石灰、高镁石灰和酸性复合造渣剂总用量的三分之二加入到转炉中,剩下三分之一的石灰、高镁石灰和酸性复合造渣剂将分批在冶炼过程中加完。在炉渣较活跃时加剩下的石灰、高镁石灰和酸性复合造渣剂,以保证炉渣有足够的流动性和脱硫、脱磷能力,剩下三分之一的石灰、高镁石灰和酸性复合造渣剂主要根据转炉的化渣状态分批次加入,主要是为了避免炼钢过程返干。其中,吹炼的氧气流量为28000nm3/h,吨钢氧耗40~60nm3。其中,为了保证熔渣具有很好的流动性,以达到快速脱磷的目的,防止烧枪,吹炼的氧枪喷头距熔池金属液面基本枪位1.4~1.6m,吹炼枪位1.4m~1.6m,开吹枪位1.8m,拉碳枪位1.4m。炼钢过程,初渣碱度控制在2.0~2.5,终渣碱度控制在3.0~4.0,总的吹炼原则:快速化渣,早化渣,炉渣活跃,过程不返干、不喷溅。本发明中t钢中的钢均指是冶炼后得到的钢水,下面结合实施例对本发明进行进一步说明。实施例1在某钢厂120吨转炉上冶炼u71钢种的钢,实际入炉半钢铁水重量是132t,废钢重量是5t,出钢重量是128.8t,具体操作是在上一炉次溅渣护炉结束后,装入半钢铁水和废钢,开始吹炼后将冷态钢渣加入至转炉内,再将石灰、高镁石灰和酸性复合渣分批加入到转炉中,其中半钢铁水成分及温度情况如下表1所示,实际加入的辅料量和吹氧量如表2所示,出钢成分及出钢温度如下表3所示。炼钢过程炉渣活跃,并有较强的脱磷能力,出钢结束采用常规溅渣护炉工艺,炉壁挂渣良好,此炉冶炼终渣碱度3.9,终渣中全铁为19.5%,氧活度是500ppm。表1半钢铁水成分(%)和入炉温度(℃)csimnps入炉温度3.840.020.030.0750.0121300表2半钢炼钢辅料实际加入量(kg)及实际吹氧量(m3)表3出钢钢水成分(%)和出钢温度(℃)csimnps出钢温度0.060.0230.030.0110.0101675实施例2在某钢厂120吨转炉上冶炼q235-dg钢种的钢,实际入炉半钢铁水重量是141t,废钢重量是0t,出钢重量是131.56t,具体操作是在上一炉次溅渣护炉结束后,装入半钢铁水,开始吹炼后将三分之二的冷态钢渣在吹炼开始后6min内加完,剩下的三分之一冷态钢渣在接下来的4min内加完,再将石灰、高镁石灰和酸性复合造渣剂分批加入到转炉中,其中半钢铁水成分及温度情况如下表4所示,实际加入的辅料量和吹氧量如表5所示,出钢成分及出钢温度如下表6所示。炼钢过程炉渣活跃,并有较强的脱磷能力,出钢结束采用常规溅渣护炉工艺,炉壁挂渣良好,此炉冶炼终渣碱度4.2,终渣中全铁为19.2%,氧活度是460ppm。表4半钢铁水成分(%)和入炉温度(℃)csimnps入炉温度3.950.0250.0350.0680.0201280表5半钢炼钢辅料实际加入量(kg)及实际吹氧量(m3)表6出钢钢水成分(%)和出钢温度(℃)csimnps出钢温度0.060.0230.030.0110.0101675实施例3在某钢厂120吨转炉上冶炼q195钢种的钢,实际入炉半钢铁水重量是130t,废钢重量是6t,出钢重量是125.12t,具体操作是在上一炉次溅渣护炉结束后,装入半钢铁水和废钢,开始吹炼后将三分之二的冷态钢渣在吹炼开始后6min内加完,剩下的三分之一冷态钢渣在接下来的4min内加完,再将石灰、高镁石灰和酸性复合造渣剂总用量的三分之二加入到转炉中,剩下三分之一的石灰、高镁石灰和酸性复合造渣剂将分批在冶炼过程中加完,其中半钢铁水成分及温度情况如下表7所示,实际加入的辅料量和吹氧量如表8所示,出钢成分及出钢温度如下表9所示。炼钢过程炉渣活跃,有较强的脱磷能力,出钢结束采用常规溅渣护炉工艺,炉壁挂渣良好,此炉冶炼终渣碱度4.0,终渣中全铁为20.2%,氧活度是480ppm。表7半钢铁水成分(%)和入炉温度(℃)csimnps入炉温度3.810.030.040.0650.0111330表8半钢炼钢辅料实际加入量(kg)及实际吹氧量(m3)表9出钢钢水成分(%)和出钢温度(℃)csimnps出钢温度0.080.020.030.0100.0111670对比例在某钢厂120吨转炉上冶炼q235钢种的钢,实际入炉半钢铁水重量是130t,废钢重量是6t,出钢重量是125.12t,半钢铁水成分及温度情况如上表7所示,实际加入的辅料量和吹氧量如表10所示,出钢成分及出钢温度如上表9所示。冶炼结束,虽然钢水成分满足钢种要求,但是需要消耗大量的炼钢辅料,生产成本相对本发明要高。表10半钢炼钢辅料实际加入量(kg)及实际吹氧量(m3)再如,采用本发明的方法,2017年炼钢用石灰、高镁石灰、酸性复合造渣剂价格分别为513、363、390元/t,按照理论每炉钢加入冷态钢渣吨钢8.668kg,则转炉炼钢主要辅料石灰+高镁石灰+酸性复合造渣剂用量平均为5764.06kg/炉,相对于正常冶炼炉次,其主要辅料石灰+高镁石灰+酸性复合造渣剂用量平均为6521.36kg/炉,转炉加入冷态钢渣较正常冶炼炉次主要辅料平均减少757.3kg/炉,吨钢辅料消耗降低5.694kg/t钢,以每炉钢重量130t/炉,年产钢540万吨计,加入冷态钢渣炉次成本:y1=(1152.8/1000*100+2046.2/1000*513+2269.4/1000*363+1448.5/1000*390+(2046.2+2269.4+1448.5)/(1-0.193)/1000*0.193*1800)/132=38.14元/t钢正常冶炼炉次成本:y2=(2380.2/1000*513+2558.1/1000*363+1583.1/1000*390+(2380.2+2558.1+1583.1)/(1-0.184)/1000*0.184*1800)/132=41.01元/t钢,则吨钢效益y=41.01-38.14=2.87元/t钢。基于以上,采用本发明的方法,预计创造效益在1000万以上。当前第1页12