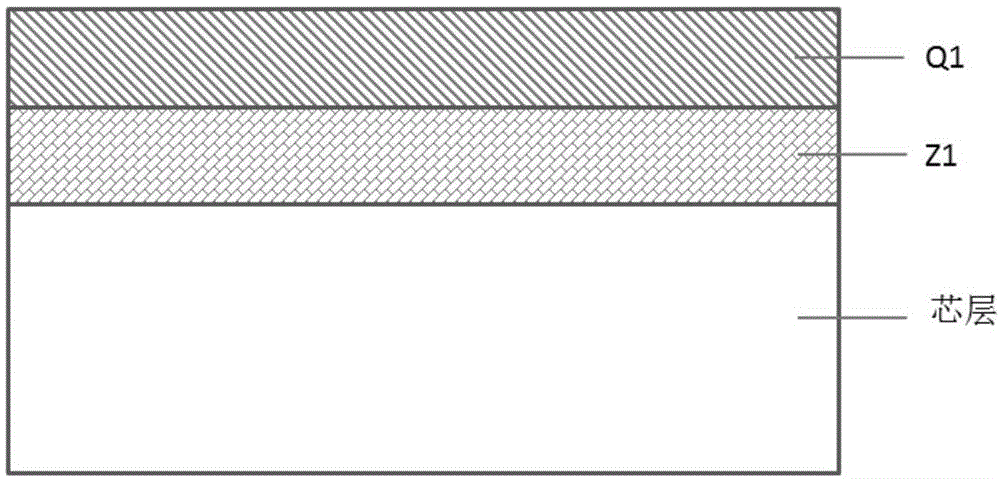
本发明涉及一种铝合金复合材料,具体地,涉及一种用于蜂窝板的高强度可钎焊铝合金复合材料。本发明还涉及制备该铝合金复合材料的方法及其在蜂窝板材料中的用途。
背景技术:
:金属蜂窝具有较好的电磁波屏蔽性能,特别是对高频电磁波具有更好的屏蔽效果。可以用金属蜂窝制成电子设备外壳、防电磁辐射器、静电防护器等。利用其吸能减震性能,可应用于高速公路的防护栏、飞机场等强声源隔音墙、民用建筑装饰隔音等。采用金属复合材料制作的结构可以提高车辆在高速行驶时的平稳性、舒适性和安全性。蜂窝夹芯板是由两层薄而高强度的面板材料,中间夹一层厚而极轻的蜂窝芯组成,通过粘结剂或钎焊将上下面板与蜂窝芯连接而成的整体刚性结构。目前大多数蜂窝板通过粘结剂胶粘而成,一般用于温度和强度要求不太高的领域。传统的胶粘剂蜂窝板,粘结剂强度通常只有100mpa,高低温容易开裂。cn103240923a提供蜂窝夹层板以及轿厢地板采用该蜂窝夹层板的电梯轿厢。该专利涉及的蜂窝夹层板具有蜂窝和以夹入所述蜂窝的方式配置的一对表面板,所述蜂窝和所述表面板被粘接剂粘接固定。胶粘剂存在低温状态下容易开裂的缺陷,其老化后也容易开裂,且遇火灾时存在释放有毒气体等。因此,胶粘蜂窝板上不能承受低温和高温,使铝板应用受到了极大的限制。关于可钎焊蜂窝板,通常采用5、6系合金,虽没有开裂问题,但强度还有待于提高,其通过时效后,强度只有250mpa左右,达不到300mpa。当芯层采用7系合金,高合金含量7系不易轧制,低合金含量7系合金达不到300mpa。cn106335247a涉及一种用于载气钎焊的铝蜂窝结构板及制作方法。铝蜂窝结构板包括上铝合金板、铝蜂窝和下铝合金板,上铝合金板与下铝合金板均包括6系铝硅镁合金的芯材、3系铝锰合金的中间层,4系铝硅合金的皮材。铝蜂窝结构板的制作方法包括将上铝合金板、铝蜂窝和下铝合金板采用保护性气氛钎焊焊接为所述铝蜂窝结构板。该发明含镁的合金板可通过载气钎焊的方式焊接成型。通常地,6系单层合金强度为约300mpa,远低于约500-700mpa的7系单层合金,当中间层为强度约150mpa的普通3系材料时,复合蜂窝板钎焊后强度约为200mpa,难以满足强度要求较高的蜂窝板承重要求。因此,在蜂窝板应用领域中仍需具有高强度的可钎焊铝合金复合材料。技术实现要素:在一方面,本发明涉及一种铝合金复合材料用芯层合金,其特征在于,基于所述芯层合金,所述芯层合金包含0.3-1.2重量%的si,1.0-2.0重量%的mn,3.0-5.4重量%的zn,0.5-1.5重量%的cu,0.6-1.2重量%的mg,<0.45重量%的fe;余量为al和不可避免的杂质。在一个实施方案中,所述芯层合金中si和mg的重量比si/mg为0.5以上,zn和mg的重量比zn/mg为3以上,并且si/mg+zn/mg≥4。在一个优选的实施方案中,基于所述芯层合金,所述芯层合金包含0.33-1.18重量%的si,和/或1.05-1.8重量%的mn,和/或3.2-5重量%的zn,和/或0.8-1.2重量%的cu,和/或0.65-1.1重量%的mg。在另一个实施方案中,芯层合金由包含3系和7系铝合金和/或铝合金废料的原料制备。在另一方面,本发明涉及一种铝合金复合材料,其包含本发明的芯层合金,并且包含阻挡层合金和钎焊层合金。在一个实施方案中,本发明的铝合金复合材料中,基于所述阻挡层合金,所述阻挡层合金包含0-1重量%的si,1.0-2.0重量%的mn,0-4重量%的zn,0.1-0.8重量%的cu,<0.3重量%的fe;余量为al和不可避免的杂质。在另一个实施方案中,基于所述钎焊层合金,所述钎焊层合金包含4-15重量%的si,<0.3重量%的fe,0-4重量%的zn;余量为al和不可避免的杂质。在又一方面,本发明涉及一种铝合金复合材料,其具有至少三层,包括本发明的芯层以及在芯层的至少一侧依次设置的阻挡层和钎焊层。优选的,芯层为选自本发明的芯层合金。在一个实施方案中,本发明的铝合金复合材料中,在所述芯层的一侧依次设置有阻挡层和钎焊层,在相背离的另一侧还设置有阻挡层。在一个优选的实施方案中,阻挡层为本发明的阻挡层合金。在另一个优选的实施方案中,钎焊层为本发明的钎焊层合金。在一个实施方案中,本发明的铝合金复合材料中所述阻挡层相对于整个铝合金复合材料的复合比为0-20%,和/或所述钎焊层相对于整个铝合金复合材料的复合比为5-15%。在一个优选的实施方案中,位于所述芯层和所述钎焊层之间的阻挡层相对于整个铝合金复合材料的复合比为约9-16%。在一个实施方案中,本发明的铝合金复合材料的总厚度为0.1mm-3mm。在一个实施方案中,本发明的芯层合金或本发明的铝合金复合材料,用于蜂窝板。在另一方面,本发明涉及一种制备本发明的铝合金复合材料的方法,其特征在于,包括如下步骤:(1)将芯层合金、钎焊层合金、阻挡层合金铸锭熔铸好;(2)均匀化处理;(3)将钎焊层合金、阻挡层合金铸锭块热轧;(4)将芯层合金、热轧的钎焊层合金与热轧的阻挡层合金复合;(5)热轧;(6)冷轧。在还一方面本发明涉及一种蜂窝板材料,其包含本发明的芯层合金或铝合金复合材料或者由本发明的铝合金复合材料制备。附图简述图1(a)-1(d)铝合金复合材料的结构示意图。图2mg元素在铝合金复合材料中扩散状况面扫描电子探针显微分析(epma)图。图3(a)钎焊前铝合金复合材料中芯层合金的epma图像。图3(b)钎焊前铝合金复合材料中芯层合金的epma能谱图。图4(a)钎焊后铝合金复合材料中芯层合金的epma图像。图4(b)钎焊后铝合金复合材料中芯层合金的epma能谱图。具体实施方式一般定义及术语除非另外定义,本文中使用的所有技术和科学术语具有本发明所属领域普通技术人员通常所理解的同样含义。在抵触的情况下,以本说明书包括定义为准。除非另外说明,所有的百分数、份数、比例等都以重量计。当以范围、优选范围、或者优选的数值上限以及优选的数值下限的形式表述某个量、浓度或其它值或参数的时候,应当理解相当于具体揭示了通过将任意一对范围上限或优选数值与任意范围下限或优选数值结合起来的任何范围,而不考虑该范围是否具体揭示。除非另外指出,本文所列出的数值范围旨在包括范围的端点,和该范围之内的所有整数和分数。例如“1-8”涵盖1、2、3、4、5、6、7、8以及由其中任何两个值组成的任何亚范围,例如2-6、3-5。本文所用的术语“约”、“大约”当与数值变量并用时,通常指该变量的数值和该变量的所有数值在实验误差内(例如对于平均值95%的置信区间内)或在指定数值的±2%、±5%内,或更宽范围内。表述“包含”或与其同义的类似表述“包括”、“含有”和“具有”等是开放性的,不排除额外的未列举的元素、步骤或成分。表述“由…组成”排除未指明的任何元素、步骤或成分。表述“基本上由…组成”指范围限制在指定的元素、步骤或成分,加上任选存在的不会实质上影响所要求保护的主题的基本和新的特征的元素、步骤或成分。应当理解,表述“包含”涵盖表述“基本上由…组成”和“由…组成”。除了在操作的实施例中,或者另外指明,表示本文中的成分、反应条件或定义成分参数的所有数值在所有情况下应当理解为由术语“约”限定。本文所使用的术语“任选”或“任选地”是指随后描述的事件或情况可能发生或可能不发生,该描述包括发生所述事件或情况和不发生所述事件或情况。本文所使用的1系、3系、6系、7系的命名是指本领域的通用合金命名。例如,1系合金为工业纯铝;3系合金为以铝锰为主要元素的一系列合金;4系合金为以铝硅为主要元素的一系列合金;5系合金为以铝镁为主要元素的一系列合金;6系合金为以铝硅镁为主要元素的一系列合金;7系合金为以铝锌镁铜为主要元素的一系列合金。“一个”、“一种”用于描述本发明的元素和组分。这仅仅是为了方便和给出本发明的通常含义。这样的描述应当理解为包含一个或至少一个,并且除非明显具有相反含义,其还包括复数形式。本文所使用的术语“至少一种(个)”指一种、两种、三种、四种或更多种。“至少三层”指三层、四层、五层或更多。本文所使用的术语“一种或多种”指一种、两种、三种、四种、五种、六种、七种、八种、九种或更多种。本文所使用的术语“复合比”指复合材料中某一层的厚度占整个复合材料的总厚度的比例。例如,对于在芯层的两侧分别具有阻挡层的材料而言,阻挡层复合比可以分别为15%和8%。本文所使用的术语“淬火敏感性”指铝合金中第二相析出速度与冷却速度的敏感程度。冷却速度对第二相的析出影响很大:高温时,第二相在铝基体中的固溶度比低温时大,第二相在高温条件下固溶后,若对铝合金进行快速冷却时,第二相来不及析出,仍然固溶在铝基体中,产生过饱和固溶体;若冷却速度较慢,第二相会析出。例如在合金制备过程中,zn、mg在铝合金基体中溶解度随温度降低而减少。在热处理过程中,饱和的zn、mg首先形成大量的mgzn2化合物。特别是在300-400℃冷却过程中,若冷却速度过慢,过饱和的mg、zn不能完全固溶在铝合金基体中,形成mgzn2化合物析出来,因此铝合金中含mg、zn元素较高时,形成淬火敏感性。淬火敏感性对合金强度稳定性影响很大。例如对于含mg、zn元素较高或mgzn2含量较高的铝合金,尽管该铝合金虽然有时通过快速冷却也能达到预期要求强度,但温度稍微控制不好,容易出现合金强度的波动,使得合金强度大多数不稳定,不利于批量稳定生产。本文所使用的术语“固溶强化”指在合金中当溶质原子以固溶形式溶入基体中,使合金发生强化。例如,si和mg可以进入铝基体中,使得铝合金的强度提高。本文所使用的术语“不可避免的杂质”指在合金生产过程中并非刻意添加的,而是由于例如与生产设备接触等原因不可避免地引入的其他元素。除非另外定义,本发明的公开中使用的所有术语,包括技术和科学术语,具有本发明所属领域技术人员通常理解的含义。通过进一步示例,本文包含术语定义以更好理解本发明的教导。铝合金复合材料用芯层合金本发明提供一种铝合金复合材料用芯层合金,其特征在于,基于所述芯层合金,所述芯层合金包含0.3-1.2重量%的si,1.0-2.0重量%的mn,3.0-5.4重量%的zn,0.5-1.5重量%的cu,0.6-1.2重量%的mg,<0.45重量%的fe;余量为al和不可避免的杂质。本文所述的芯层合金中,si、mn、zn、cu和mg之间具有协同强化作用。为了使得使用该芯层合金的铝合金复合材料具有高强度和可钎焊的特性,芯层合金中各元素含量的特定范围和组合是特别有利的。si、mg、zn之间一定的比例关系可有助于合金的强度、稳定性和可钎焊性。si、mg、zn之间的比例关系应使得mg充分与si、zn结合,合金中si和zn越多或者si/mg+zn/mg的比例越高,si和zn与mg形成含镁化合物如mg2si、mgzn2的可能性越大,从而减少了游离态mg的存在,有利于合金强度以及稳定性,并确保最终复合材料的可钎焊性。本发明的芯层合金中含有稳定的含镁化合物(mg2si、mgzn2),以及淬火低敏感性的多元复杂相,使得合金强度和稳定性提高,同时避免游离态mg扩散挥发,影响钎焊效果。在一个实施方案中,si和mg的重量比(si/mg)为约0.5以上,例如为约0.5-2,0.5-1.5,如约0.5、0.70、1.2、1.4;zn和mg的重量比(zn/mg)为约3以上,例如为约3-9,3-7,如约3.3、3.75、6.5、4.2;并且重量比si/mg+zn/mg≥约4,例如约4-11,4-8,如约4.0、5.0、5.5、7.0。当用作蜂窝板时,复合材料的可钎焊性非常重要。芯层合金中满足si/mg+zn/mg≥4对后续可钎焊加工成蜂窝板是特别有利的。本文所述的芯层合金中,si可与mg形成稳定的含mg化合物mg2si,一定程度上减少了淬火敏感性强的mgzn2的大量形成,即降低了淬火敏感性,保证合金的高强度和稳定性。在本文中,芯层合金可以包含约0.3-1.2重量%,优选约0.33-1.18重量%的si,例如为约0.3-0.7重量%、0.3-0.95重量%、0.7-0.95重量%、0.7-1.2重量%、0.95-1.2重量%,如约0.95、0.33、0.7、1.18重量%。一定含量的si、mg的比例有助于mg2si的形成。在优选的实施方案中,si与mg的重量比(si/mg)为约0.5以上。过高的si含量会使得芯层合金的熔点下降,且容易形成大颗粒的si相,降低芯层合金的强度。过低的si含量使得其与mg的结合量减少。在一个实施方案中,mg、si、zn之间含量的配比使得芯层合金中mg2si的数量远大于mgzn2的数量。在优选的实施方案中,轧制后的芯层合金中含镁化合物以形成晶粒尺寸细小的mg2si为主。在更优选的实施方案中,轧制后的芯层合金中mg2si晶粒尺寸(基本上)为10μm以下。在甚至更优选的实施方案中,芯层合金中90%以上,95以上,99%以上,或100%的mg2si晶粒尺寸为10μm以下。钎焊后,本发明的芯层合金中大多数si与mg固溶到铝合金基体中,mg2si化合物基本消失,从而起到了固溶强化效果,使得焊后强度大大提高。剩余的si会与mn、fe、al形成化合物提高合金强度。mgzn2逐步析出,但因析出数量较少,对芯层合金强度和和稳定性影响不显著。本文所述的芯层合金中,mn可与芯层合金中的其他元素相互作用形成al-mn-fe-si化合物,提高芯层合金的强度。在本文中,芯层合金可以包含约1.0-2.0重量%,优选约1.05-1.8重量%的mn,例如为约1.05-1.2重量%、1.05-1.7重量%、1.2-1.7重量%,如约1.08、1.2、1.07、1.70重量%。过高的mn含量会使得mn形成粗大的颗粒相,影响强度。过低的mn含量会使得对芯层的增强作用不显著。本文所述的芯层合金中,zn可与mg形成mgzn2,提高芯层合金的耐蚀性和强度,中和cu对耐蚀性带来的影响。在本文中,芯层合金可以包含约3.0-5.4重量%,优选约3.2-5重量%,更优选约3.2-4.4重量%的zn,例如为约3.2-4.2重量%、如约3.27、4.2、3.3、3.22重量%。在一个实施方案中,zn和mg的重量比(zn/mg)为约3以上。在另一个实施方案中,重量比si/mg+zn/mg≥约4。过低的zn含量会使得zn无法与mg充分结合,且改善耐蚀性效果不明显。过高的zn含量会使得合金难以轧制,且导致含mg、zn元素较高时形成的淬火敏感性,使得难以批量生产。例如在冷却速度过慢时,mgzn2化合物不能充分起到固溶强化作用,导致强度降低,从而使得批量生产时芯层合金的强度产生波动。本文所述的芯层合金中,cu可起到增强复合材料的抗拉强度的作用。在本文中,芯层合金可以包含约0.5-1.5重量%,优选约0.8-1.2重量%的cu,例如约0.9-1.0重量%、约0.9-1.2重量%、约1.0-1.2重量%,如约1.17、0.9、1.01、0.91重量%。过高的cu含量会使得容易形成al2cu粗大相,导致轧制开裂,难以轧制,还会导致电位偏正,降低材料的耐腐蚀性。过低的cu含量会使得强度提高不明显。相对于5系、6系和7系铝合金中的mg含量,本文所述的芯层合金中mg含量相对较低。一定量的mg可提高芯层合金的强度。通常,mg可优先与si结合形成mg2si,然后为与zn结合。在合金的热处理过程中,si和mg会固溶在铝合金基体中。300-400℃冷却过程中,由于mg含量相对较低,大部分仍可固溶在铝合金基体中,只有少部分mg析出。析出的mg与zn结合形成少量mgzn2化合物。si、mg大部分固溶在基体中,起到固溶强化效果,提高焊后时效强度。在本文中,芯层合金可以包含约0.6-1.2重量%,优选约0.65-1.1重量%的mg,例如约0.7-0.85重量%、0.7-1.0重量%、0.85-1.0重量%,如0.78、0.65、1.00、0.86重量%。过高的mg含量会使得轧制容易开裂从而使得合金不易轧制,且会增加mg向外部的挥发扩散的可能性,从而对钎焊产生不利影响。过低的mg含量会使得其和si、zn形成化合物的概率和数量减少,少量的含镁化合物使得对芯层合金的增强作用不大。本文所述的芯层合金中,fe可增加芯层合金的强度。在一个实施方案中,fe可在制备合金的过程中使用废料熔炼时例如由废料带入到芯层合金中。在本文中,芯层合金可以包含约<0.45重量%,优选约≤0.44重量%的fe,例如约0.01至0.44重量%的fe,如约0.2-0.35重量%、0.35至0.44重量%、0.2至0.44重量%,如约0.21、0.22、0.37、0.44重量%。过高的fe含量会使得形成al3fe和复杂含铁相,不利于轧制。在一个示例性实施方案中,铝合金复合材料的芯层包含约0.95重量%的si、0.21重量%的fe、1.08重量%的mn、1.17重量%的cu、0.78重量%的mg、3.27重量%的zn。在另一个示例性实施方案中,铝合金复合材料的芯层包含约0.33重量%的si、0.22重量%的fe、1.2重量%的mn、0.9重量%的cu、0.65重量%的mg、4.2重量%的zn。在又一个示例性实施方案中,铝合金复合材料的芯层包含约0.7重量%的si、0.37重量%的fe、1.07重量%的mn、1.01重量%的cu、1.00重量%的mg、3.3重量%的zn。在还一个示例性实施方案中,铝合金复合材料的芯层包含约1.18重量%的si、0.44重量%的fe、1.70重量%的mn、0.91重量%的cu、0.86重量%的mg、3.22重量%的zn。在一个实施方案中,本文所述的芯层合金特别适合用于蜂窝板,特别是蜂窝面板。在另一个实施方案中,包含本文的芯层合金的铝合金复合材料特别适合用于蜂窝板,特别是蜂窝面板。铝合金复合材料本发明涉及一种铝合金复合材料,其包含上述的芯层合金,并且还包含阻挡层合金和钎焊层合金。本发明的铝合金复合材料中,基于所述阻挡层合金,所述阻挡层合金包含0-1重量%的si,1.0-2.0重量%的mn,0-4重量%的zn,0.1-0.8重量%的cu,<0.3重量%的fe;余量为al和不可避免的杂质。本文所述的阻挡层为3系加强型合金。本文所述的阻挡层合金中,si的选择很重要。相比于一般的3系合金,阻挡层合金中si的比例相对较高。si可与mg形成含mg化合物mg2si,阻挡从芯层中迁移的mg向钎焊层的扩散,减少mg的扩散挥发,削弱mg的扩散挥发对钎焊产生的不利影响,降低材料由于mg带来的淬火敏感性,提高钎焊性且使得钎焊后力学性能稳定。在本文中,阻挡层合金可以包含约0-1重量%,优选约0.03-0.7重量%,更优选约0.05-0.5重量%的si,例如约0.05、0.33、0.5重量%。过高的si含量会使得阻挡层熔点降低,无法发挥阻挡层的作用。过低的si含量可使得其与mg的结合不足,对复合材料的钎焊性产生不利影响。本文所述的阻挡层合金中,zn与si基本上同比例增加。zn与mg形成的mgzn2,同样减少了mg向钎焊层的扩散。足量si、zn形成一个动态平衡,防止游离态mg扩散挥发,也有利于后续热处理以及钎焊。在本文中,阻挡层合金可以包含约0-4重量%,优选约0.03-3.4重量%的zn,例如约0.04、0.05、3.22重量%。过高的zn含量会使得合金难以轧制,且由于zn蒸气压较低,zn在阻挡层含量过高时,其容易扩散或挥发扩散到钎焊层外面,并挥发至钎焊炉内,污染炉体;zn也会扩散到钎焊接头,改变接头耐蚀性,不利于钎焊处铝合金复合材料和翅片的匹配关系。过低的zn含量会使得其与mg的结合不足,削弱复合材料的钎焊性。本文所述的阻挡层合金中,mn的加入可提高阻挡层合金的强度。在本文中,阻挡层合金可以包含约1.0-2.0重量%,优选约1.4-1.8重量%的mn,例如约1.48、1.6、1.70重量%。过多的mn会使得合金中形成粗大颗粒相,不利于轧制。本文所述的阻挡层合金中,cu的加入有助于屈服强度和抗拉强度的提高,从而使得阻挡层合金的强度能与芯层合金的强度相匹配。在本文中,阻挡层合金可以包含约0.1-0.8重量%,例如约0.1-0.7重量%,如约0.1、0.65重量%的cu。过高的cu含量会使得不利于轧制,并影响合金的耐蚀性。过低的cu含量会使得由cu带来的增强的作用减弱。本文所述的阻挡层合金中,fe并非有意加入。阻挡层合金可以包含约<0.3重量%的fe。例如约0.1至<0.3重量%的fe,如约0.15、0.21、0.22重量%。本文所述的阻挡层合金中,mg的含量应尽可能低,以避免其向钎焊层的转移。在一个实施方案中,不向阻挡层合金中添加mg元素。在一个示例性实施方案中,本发明的铝合金复合材料中,阻挡层合金包含约0.05重量%的si、0.21重量%的fe、1.48重量%的mn、0.1重量%的cu、0.03重量%的mg、0.04重量%的zn。在另一个示例性实施方案中,本发明的铝合金复合材料中,阻挡层合金包含约0.33重量%的si、0.22重量%的fe、1.6重量%的mn、0.65重量%的cu、0.04重量%的mg、0.05重量%的zn。在又一个示例性实施方案中,本发明的铝合金复合材料中,阻挡层合金包含约0.5重量%的si、0.15重量%的fe、1.70重量%的mn、0.1重量%的cu、0.02重量%的mg、3.22重量%的zn。本发明的铝合金复合材料中,基于所述钎焊层合金,所述钎焊层合金包含4-15重量%的si,<0.3重量%的fe,0-4重量%的zn;余量为al和不可避免的杂质。若mg在钎焊层合金中的含量较高,对钎焊性能存在较大影响。在本文中,控制钎焊层中mg含量在低水平。在优选的实施方案中,钎焊层中不添加mg,并通过其他方式尽可能减少或避免mg向钎焊层的扩散。钎焊层合金例如可以为4系铝合金,如aa4045。钎焊层合金的添加和比例应使得能顺利进行钎焊,且结合考虑钎焊接头的耐蚀性。本发明涉及一种铝合金复合材料,其具有至少三层,包括芯层以及在所述芯层的至少一侧依次设置的阻挡层和钎焊层。在一个优选的实施方案中,在所述芯层的一侧依次设置有阻挡层和钎焊层,在相背离的另一侧还设置有阻挡层。在一个实施方案中,芯层为选自本发明的芯层合金。在优选的实施方案中,基于所述芯层合金,所述芯层合金包含0.3-1.2重量%的si,1.0-2.0重量%的mn,3.0-5.4重量%的zn,0.5-1.5重量%的cu,0.6-1.2重量%的mg,<0.45重量%的fe;余量为al和不可避免的杂质。在另一个实施方案中,阻挡层为本发明的阻挡层合金。在优选的实施方案中,所述阻挡层合金包含,基于所述阻挡层合金,0-1重量%的si,1.0-2.0重量%的mn,0-4重量%的zn,0.1-0.8重量%的cu,<0.3重量%的fe;余量为al和不可避免的杂质。在又一个实施方案中,钎焊层为本发明的钎焊层合金。在优选的实施方案中,所述钎焊层合金包含,基于所述钎焊层合金,4-15重量%的si,<0.3重量%的fe,0-4重量%的zn;余量为al和不可避免的杂质。在一个实施方案中,本发明的铝合金复合材料包含至少一个阻挡层。在另一个实施方案中,铝合金复合材料中具有多于一个阻挡层,各阻挡层具有相同的元素组成。在又一个实施方案中,铝合金复合材料中具有多于一个阻挡层,各阻挡层具有不同的元素组成。在一个实施方案中,在芯层的至少一侧设置有阻挡层。在又一个实施方案中,芯层的两侧均设置有阻挡层。在一个优选的实施方案中,铝合金复合材料中至少一个阻挡层位于芯层与钎焊层之间。在一个实施方案中,本发明的铝合金复合材料包含至少一个钎焊层。在另一个实施方案中,铝合金复合材料中具有多于一个钎焊层,各钎焊层具有相同的元素组成。在又一个实施方案中,铝合金复合材料中具有多于一个钎焊层,各钎焊层具有不同的元素组成。在一个实施方案中,在芯层的一侧依次设置有阻挡层(z1)和钎焊层(q1),如图1(a)所示。在另一个实施方案中,在芯层的一侧依次设置有阻挡层(z1)和钎焊层(q1),在相背离的另一侧还设置有阻挡层(z2),如图1(b)所示。在又一个实施方案中,在芯层合金的一侧依次设置有阻挡层(z1)和钎焊层(q1),在相背离的另一侧还设置有钎焊层(q2),如图1(c)所示。在还一个实施方案中,在芯层合金的一侧依次设置有阻挡层(z1)和钎焊层(q1),在相背离的另一侧还依次设置有阻挡层(z2)和钎焊层(q2),如图1(d)所示。在一个实施方案中,钎焊层相对于整个铝合金复合材料的复合比为约5-15%,如约8%、9%、10%。在另一个实施方案中,阻挡层相对于整个铝合金复合材料的复合比为约0-20%,如约10%、15%。在优选的实施方案中,位于芯层和钎焊层之间的阻挡层的复合比尽可能加厚。较大的复合比可以减小mg向钎焊层合金扩散的几率,避免mg冲破阻挡层的阻碍从芯层向钎焊层扩散,增强铝合金复合材料的可钎焊性。但由于阻挡层合金强度较低,若其厚度过大,也将影响材料整体强度。因此该复合比的设计需要综合考虑mg扩散的影响以及复合材料的整体强度。复合比的设计为阻挡层的厚度与阻挡层合金各元素含量综合考量的结果。在一个实施方案中,位于芯层和钎焊层之间的阻挡层相对于整个铝合金复合材料的复合比为约9-16%,例如约15%。本发明的铝合金复合材料的厚度可以为约0.1mm-3mm,例如约1mm、2mm。制备方法本发明还涉及本发明的铝合金复合材料的制备方法。包括如下步骤:(1)将芯层合金、钎焊层合金、阻挡层合金铸锭熔铸好;(2)均匀化处理;(3)将钎焊层合金、阻挡层合金铸锭块热轧;(4)将芯层合金、热轧的钎焊层合金与热轧的阻挡层合金复合;(5)热轧;(6)冷轧。在一个实施方案中,步骤(1)中包括将各元素进行熔炼,加入除渣剂,扒渣;随后浇铸成铸锭的步骤。在优选的实施方案中,熔炼温度为约720-780℃。在一个实施方案中,钎焊层合金的熔点为约560-600℃。在另一个实施方案中,阻挡层合金熔点为约620-660℃。在还一个实施方案中,芯层合金的熔点为约620-660℃。本发明的铝合金复合材料的芯层合金的制备原料可以包含3系和7系铝合金和/或铝合金废料。在一个实施方案中,芯层合金由3系和7系铝合金原料熔炼。其不同于传统3系铝合金,也不同于传统7系铝合金。在另一个实施方案中,芯层合金可以由纯金属熔炼配置而成。在又一个实施方案中,芯层合金可以包含熔炼铝合金、铝合金废料、纯金属中的一种或多种。在还一个实施方案中,芯层合金可以由铝合金、铝合金废料、纯金属中的一种或多种熔炼而成。在另一个实施方案中,芯层合金可以由3系铝合金废料与7系铝合金废料熔炼回收利用而成。在又一个实施方案中,芯层合金可以包含熔炼3系铝合金废料、7系铝合金废料、任选的4系或5系铝合金废料以及其他铝合金废料。在另一个实施方案中,芯层合金可以由3系铝合金废料、7系铝合金废料、任选的4系或5系铝合金废料以及其他铝合金废料熔炼而成。所述其他铝合金废料为元素种类少于或等于本申请的芯层合金的元素种类的铝合金废料。对废料的可利用性大大丰富了回收铝合金的种类,同时环保节能。用废料熔炼而成的芯层合金制备的铝合金复合材料具有高强度。在上述实施方案中所述的铝合金废料也可用铝合金替代。在一个实施方案中,步骤(1)中对芯层合金的熔炼为选择质量分数99.99%的高纯铝、质量分数99.9%的zn、质量分数99.9%的mg、质量分数99.9%硅粉,以及al-50%cu、al-10%mn中间合金为原料进行熔炼。在另一个实施方案中,步骤(1)中对芯层合金的熔炼为选择4系铝硅合金废料、3系铝锰合金废料、以及7系合金废料为原料,同时辅助质量分数99.99%的高纯铝、质量分数99.9%的mg、质量分数99.9%硅粉,以及al-50%cu、al-10%mn中间合金进行熔炼。在一个实施方案中,步骤(2)中对芯层合金进行均匀化处理,任选地对钎焊层和阻挡层进行均匀化处理。在一个实施方案中,步骤(2)的均匀化处理的温度为约470-510℃,例如可以为约500℃。均匀化处理的时间例如可以为约1-24h,例如约14h。在一个实施方案中,在步骤(2)后还包括对铸锭切割、铣面,去除冒口和表皮的步骤。在一个实施方案中,步骤(3)中热轧轧制的厚度具体可根据复合比决定。热轧可以在退火炉中进行。在一个实施方案中,阻挡层轧至约10-40mm。在另一个实施方案中,钎焊层轧至约10-40mm。在又一个实施方案中,不对芯层进行热轧。步骤(3)中热轧的温度为约470-500℃,例如约470℃。在一个实施方案中,热轧前保温时间为约1-5h,例如约3h。在另一个实施方案中,终轧温度为约250-380℃,例如约310℃。在一个实施方案中,步骤(4)的复合应使得芯层、各阻挡层、各钎焊层各自具有预设的复合比。在一个实施方案中,步骤(5)的热轧温度为约470-500℃,例如约470℃。在另一个实施方案中,步骤(5)热轧之前保温时间为约1-5h,例如约3h。在一个实施方案中,步骤(5)的热轧后铝合金复合材料的轧制厚度为约5-10mm。在一个实施方案中,步骤(6)冷轧成品道次加工率为约30-40%。冷轧的轧制厚度为约0.1-3mm,例如为约1mm、2mm。根据产品需求,步骤(6)之后还可任选地结合轧制进行退火工艺。退火温度为约300-450℃,例如约380℃。步骤(7)的退火时间为约1-3h,例如约2h。在一个实施方案中,当本发明的铝合金复合材料用作蜂窝板材料时,钎焊炉体温度为约560-620℃。本发明的铝合金复合材料具有高强度,为可钎焊的铝合金复合材料,可特别适用于蜂窝板领域,特别是作为蜂窝板,尤其是蜂窝面板材料。本发明还涉及一种蜂窝板,其包含本发明的芯层合金。本发明还涉及一种蜂窝板,其由本发明的铝合金复合材料制备或者包含本发明的铝合金复合材料。有益效果本发明的用于蜂窝板的铝合金复合材料具有高强度、良好的钎焊性,钎焊后稳定性好、轧制不易开裂,解决了现有胶粘蜂窝板不能承受高低温、低温、老化开裂、抗高强度冲击较差、加工硬化系数低、隔音效果和保温效果差等问题。改善了胶粘和钎焊蜂窝板材料在二次加工过程中容易变形,强度差的问题。本发明的铝合金复合材料无需复杂精确的工艺控制即可达到稳定的强度,适合批量生产。本发明的铝合金复合材料钎焊后可以通过热处理强化,通过自然或人工时效后抗拉强度接近300mpa或大于300mpa,屈服强度大于150mpa。相比于常规5、6系和7系合金,本发明的铝合金复合材料可满足高铁或地铁耐压落球实验或踩踏试验要求。本发明的铝合金复合材料,在保证重量减轻的同时仍然维持其强度不下降,并且适用于保护气氛钎焊。该合金也可以通过自钎焊完成,提高钎焊生产效率并降低生产成本。本发明的铝合金复合材料可以用在运输工具如高铁、地铁上,具有高强度。本发明的复合材料的芯层合金是在7系高强合金的基础创造性加入3系耐蚀材料的元素,即解决3系强度不够的问题,又改善了7系的耐蚀性和淬火敏感性。在cu、mg、zn含量相同的情况下,其强度强于7系合金,经过钎焊后,在通过不同时间时效,复合材料的强度和稳定性大大提高。本发明的芯层合金具有高强度(例如抗拉强度为约500mpa以上)、良好的钎焊性,钎焊后稳定性好、轧制不易开裂。其中mn含量较高,si、mn、cu、mg、zn之间具有协同强化作用,是一种新合金,其特别适用于蜂窝板领域。本发明的阻挡层合金在3系材料基础上,加大cu含量,大大提高阻挡层合金的强度,使得使用本发明的芯层合金和阻挡层合金制备的铝合金复合材料为不同于任何以往适用于蜂窝板的性能优异的铝合金复合材料。实施例本发明将借助下面的实施例详细描述,应注意本发明的实施例只是对本发明的内容予以解释说明,并不构成对本发明技术方案的限制。铝合金复合材料的制备(1)采用常用铝合金熔炼工艺熔炼芯层合金,浇铸成板状铸锭,其中熔炼选择4系铝硅合金废料、3系铝锰合金废料、以及7系合金废料为原料,同时辅助质量分数99.99%的高纯铝、质量分数99.9%的mg、质量分数99.9%硅粉,以及al-50%cu、al-10%mn中间合金进行。芯层合金具有表1中实施例a1-a4与对比例a5-a8的化学组成。采用常用铝合金熔炼工艺熔炼阻挡层合金,阻挡层合金具有实施例b1-b3的化学组成,将熔炼后的阻挡层合金和采用常用铝合金熔炼工艺熔炼的钎焊层合金aa4045分别铸锭,浇铸成板状铸锭;(2)然后对芯层铸锭在500℃下均匀化处理14h;(3)对各合金铸锭进行切割铣面,去除冒口和表皮;(4)铣面后在退火炉中加热至470℃,保温3h,对阻挡层和钎焊层进行热轧,终轧温度310℃,阻挡层轧薄至10-40mm,钎焊层轧薄至10-40mm;(5)按照表3中复合比进行复合,根据复合比将热轧后阻挡层、钎焊层与未轧芯层焊接在一起;(6)在退火炉中加热至470℃,保温3h,进行热轧,轧制厚度5-10mm;(7)然后冷轧成品道次加工率30-40%,轧薄以获得1mm和2mm的产品。表1芯层合金成分组成(重量%,符号“-”表示cu元素未添加。)表2阻挡层合金成分组成(重量%)编号sifemncumgznal实施例b1(aa3003)0.050.211.480.100.030.04余量实施例b2(hf329)0.330.221.600.650.040.05余量实施例b3(hf321)0.500.151.700.100.023.22余量表3铝合金复合材料铝合金复合材料的测试力学性能测试对制备的铝合金复合材料进行轧制开裂程度以及可钎焊性评价,并进行模拟钎焊,测试钎焊后和自然时效后的力学性能,如表4、表5所示。其中屈服强度、抗拉强度采用gb/t228-2002金属材料室温拉伸试验方法检测。表4实施例和对比例于603℃×3min钎焊后力学性能测试结果*难钎焊:表示焊接不上。表5实施例和对比例于603℃×3min钎焊后21天自然时效后力学性能测试结果编号屈服强度rp0.2(mpa)抗拉强度rm(mpa)延伸率(%)实施例1170.5296.211.4实施例2154.0292.115.2实施例3185.2320.713.5实施例4179.7316.814.3实施例5187.1326.412.6实施例6182.7319.613.4对比例1148.4213.73.3对比例2157.6283.317.1对比例3154.3278.916.8对比例4152.6263.316.5由上表4、5可见,本发明的实施例1-6具有良好的力学性能和可钎焊性,且轧制不易开裂。实施例1-6中使用的芯层合金a1-a4中,si/mg分别为1.22、0.51、0.70、1.37,均为0.5或更高;zn/mg分别为4.19、6.46、3.30、3.74,均为3或更高;si/mg+zn/mg分别为5.41、6.97、4.00、5.12,均为4或更高。而对比例中使用的芯层合金中,芯层合金a5、a7的si/mg分别为0.0056、0.02,小于0.5;芯层合金a7的zn/mg为0.08,小于3;芯层合金a5-a8的si/mg+zn/mg分别为3.11、3.74、0.1、1.5,小于4。与对比例1-4的芯层合金相比,本发明的实施例1-6的芯层合金在7系合金中加入si和mn,焊后以及时效后力学性能得到显著提高,淬火敏感性大大降低,力学性能稳定性明显提高。对比例1的材料强度相对较低,可钎焊性差;对比例2的材料可钎焊性差,且容易轧制开裂。虽然对比例1、2芯层合金都是7系,但由于mg和zn含量较高,且si含量相当低,不但使得基体中不会形成mg2si相,而且mg可大量挥发,对钎焊造成一定的不利影响,使得无法加工成蜂窝板。此外由于mg、zn含量高,mgzn2也偏高,mgzn2的淬火敏感性使得热处理工艺中如果冷却速度较慢,时效后强度提高不大且强度不稳定,达不到蜂窝板要求强度,且导致批量生产的产品不具有基本一致的强度。与对比例3的芯层合金相比,实施例1-6的芯层合金虽然降低了mg含量,但由于加入高含量的cu,力学性能得到了显著提升。此外由于mg降低,避免了轧制易开裂导致的不易轧制的问题,且因mg元素扩散较少,复合材料钎焊性较好。而对比例3的材料极易轧制开裂且难钎焊。对比例3的芯层合金中mg的含量较高,为5重量%,且si和zn含量较少,使得mg无法与大量si和zn结合形成化合物,后续钎焊因游离态mg大量扩散导致钎焊不上,不能加工成蜂窝板。对比例4的材料强度较低。对比例4的芯层6系合金虽然都含有si、mn、cu、mg、zn,但含量都不高,含量平均为约0.5重量%左右;这些元素都没有达到饱和固溶度,没有达到充分固溶强化,获得材料强度不高。此外,实施例的阻挡层合金中加入相对较高的cu含量,使复合材料的屈服强度和抗拉强度显著提高。mg元素扩散状况测试通过epma(电子探针显微分析,jeolepma-1720)面扫描测试mg元素在实施例3的铝合金复合材料中的扩散情况,如图2所示。从mg元素面扫描可知,在阻挡层复合比为约15%的复合材料中,mg元素扩散到阻挡层厚度50%左右。因此,当阻挡层复合比为约8%时,mg元素会冲破阻挡层阻碍,扩散到钎焊层,对钎焊性能产生较大影响。钎焊前后芯层合金元素分析对钎焊前实施例5的铝合金中的芯层合金用能谱仪分析元素的种类和含量,如图3所示。能谱仪使用jeolepma-1720eds。根据能谱仪检测结果,图3(a)中大量黑色弥散黑色颗粒为mg2si,且基本上具有10μm以下的晶粒尺寸。合金中的白色颗粒中仅少量为mgzn2。对钎焊后实施例5的铝合金中的芯层合金用能谱仪分析元素的种类和含量,如图4所示。从图4(a)可看出大量黑色弥散颗粒已消失,表明绝大多数mg2si固溶到铝合金基体中,mg、si元素的固溶使得合金的强度增加,且mg元素大量固溶减少了mgzn2的形成数量和概率,仅微量mgzn2析出,降低了材料淬火敏感性。本领域技术人员会清楚,可以进行本发明的许多修改和变化而不背离其精神和范围。本文所述的具体实施方案仅通过实例的方式提供,并不意味着以任何方式限制。本发明的真正范围和精神通过所附权利要求书示出,说明书和实施例仅是示例性的。当前第1页1 2 3