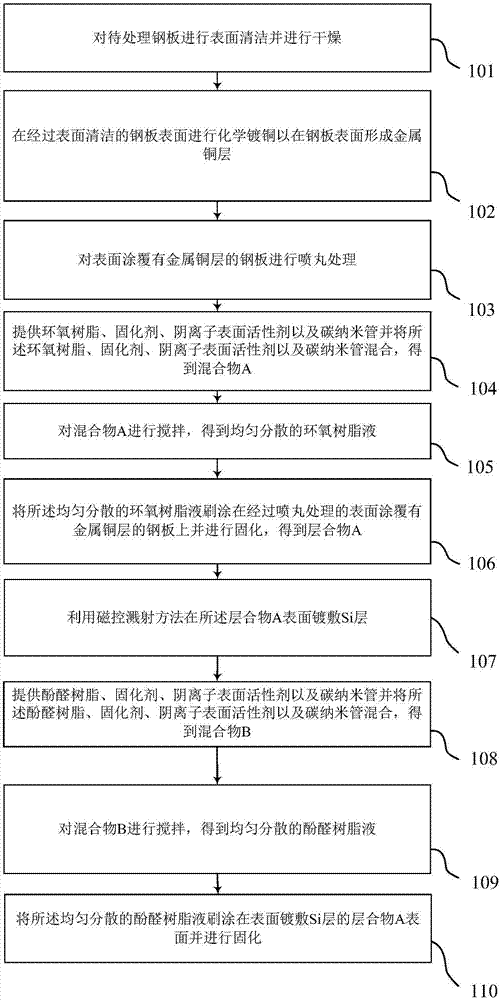
本发明是关于金属表面处理
技术领域:
,特别是关于一种钢板表面环保防腐蚀方法。
背景技术:
由于碳钢中的合金元素比较少,因此在海洋、大气等环境下钢中的fe元素性质非常活泼极易发生氧化腐蚀。而腐蚀是在一定的环境下使物质发生破坏或变质的现象。随着经济建设的发展,腐蚀的危害越来越大,不仅给社会造成了巨大的经济损失,严重时还会诱发各种突发性事故,而且不符合可持续发展的理念,在一定程度上威胁着人类的生存和发展。碳钢的腐蚀可以分为化学腐蚀和电化学腐蚀两类,化学腐蚀是指碳钢与周围环境(氧、水、酸等)直接发生化学反应而引起材料变质与损坏的现象;另外,由于碳钢各部分成分不一样、内部残余应力差、电解质溶液的温度差、浓度差等会使其表面或内部发生电位差,从而发生碳钢的电化学腐蚀。近年来,主要通过在腐蚀环境中添加缓蚀剂和表面钝化的方法来减缓材料的腐蚀。虽然上述表面强化和改性方法可以有效的保护金属,但是其需要特定的设备工艺复杂,有时不仅会对环境造成破坏还会危害人类健康,并且不不适合规模化生产。为此,目前现有技术开发出了在碳钢表面涂覆聚合物膜的防腐蚀方法。公开于该
背景技术:
部分的信息仅仅旨在增加对本发明的总体背景的理解,而不应当被视为承认或以任何形式暗示该信息构成已为本领域一般技术人员所公知的现有技术。技术实现要素:本发明的目的在于提供一种钢板表面环保防腐蚀方法,其能够克服现有技术的缺陷。为实现上述目的,本发明提供了一种钢板表面环保防腐蚀方法,包括如下步骤:对待处理钢板进行表面清洁并进行干燥;在经过表面清洁的钢板表面进行化学镀铜以在钢板表面形成金属铜层;对表面涂覆有金属铜层的钢板进行喷丸处理;提供环氧树脂、固化剂、阴离子表面活性剂以及碳纳米管并将环氧树脂、固化剂、阴离子表面活性剂以及碳纳米管混合,得到混合物a;对混合物a进行搅拌,得到均匀分散的环氧树脂液;将均匀分散的环氧树脂液刷涂在经过喷丸处理的表面涂覆有金属铜层的钢板上并进行固化,得到层合物a;利用磁控溅射方法在层合物a表面镀敷si层;提供酚醛树脂、固化剂、阴离子表面活性剂以及碳纳米管并将酚醛树脂、固化剂、阴离子表面活性剂以及碳纳米管混合,得到混合物b;对混合物b进行搅拌,得到均匀分散的酚醛树脂液;以及将均匀分散的酚醛树脂液刷涂在表面镀敷si层的层合物a表面并进行固化。在一优选的实施方式中,其中,在钢板表面形成的金属铜层的厚度为10-30μm。在一优选的实施方式中,对表面涂覆有金属铜层的钢板进行喷丸处理的具体参数为:喷丸所用刚玉球粒径为50-100目,喷丸压力为1-2mpa。在一优选的实施方式中,在混合物a中,以重量份计,环氧树脂占100-150份,固化剂占10-15份,阴离子表面活性剂占3-5份,碳纳米管占10-15份。在一优选的实施方式中,对混合物a进行搅拌的具体参数为:搅拌温度为40-50℃,搅拌时间为50-100min。在一优选的实施方式中,对环氧树脂液进行固化的具体参数为:固化温度为60-80℃,固化时间为2-4h。在一优选的实施方式中,si层的厚度为100-300nm。在一优选的实施方式中,在混合物b中,以重量份计,酚醛树脂占100-150份,固化剂占8-10份,阴离子表面活性剂占2-4份,碳纳米管占12-17份。在一优选的实施方式中,对酚醛树脂液进行固化的具体参数为:固化温度为60-80℃,固化时间为2-4h。在一优选的实施方式中,碳纳米管掺杂的环氧树脂层的厚度为30-60μm,碳纳米管掺杂的酚醛树脂层的厚度为40-70μm。与现有技术相比,本发明具有如下优点:钢结构防腐蚀一直是工业领域普遍存在的难题。例如对于输电领域而言,钢结构高压电塔防腐蚀一直是研究重点,国家电网集团在钢结构防腐蚀方面投入了大量的人力物力,并且申请了一系列关于钢结构防腐蚀的方法或者防腐蚀剂的发明专利。但是实践表明,利用防腐蚀剂对钢结构进行防腐蚀处理并不是最有效的防腐蚀方法,真正有效的方法是将钢结构“包裹”起来,使钢结构彻底与外界隔绝。目前针对钢表面涂层,现有技术文献(“mwcnts/酚醛树脂复合涂层的制备及性能研究”西安理工大学硕士学位论文)提出了一种思路。该文献提出了在钢结构表面涂覆环氧树脂层以及酚醛树脂层的工艺。不过该现有技术虽然明确了碳纳米管加入量越大,涂层防腐蚀性能越高,涂层表面硬度越高的规律,但是由于工艺的限制,该现有技术无法制备出高碳纳米管含量的涂层,直接限制了该工艺的技术效果。本发明针对现有技术的问题,提出了一种新的钢板表面防腐蚀方法,本发明首先镀敷了过渡层,保证了聚合物层与钢板之间的结合力,同时由于工艺上的改进,本发明真正实现了聚合物层中的碳纳米管的大量掺杂,显著提高了钢板的防腐蚀能力。附图说明图1是根据本发明一实施方式的钢板表面环保防腐蚀方法流程图。图2是根据本发明一实施方式的产品结构图。具体实施方式下面结合附图,对本发明的具体实施方式进行详细描述,但应当理解本发明的保护范围并不受具体实施方式的限制。除非另有其它明确表示,否则在整个说明书和权利要求书中,术语“包括”或其变换如“包含”或“包括有”等等将被理解为包括所陈述的元件或组成部分,而并未排除其它元件或其它组成部分。图1是根据本发明一实施方式的钢板表面环保防腐蚀方法流程图。如图所示,本发明的钢板表面环保防腐蚀方法包括如下步骤:步骤101:对待处理钢板进行表面清洁并进行干燥;步骤102:在经过表面清洁的钢板表面进行化学镀铜以在钢板表面形成金属铜层;步骤103:对表面涂覆有金属铜层的钢板进行喷丸处理;步骤104:提供环氧树脂、固化剂、阴离子表面活性剂以及碳纳米管并将环氧树脂、固化剂、阴离子表面活性剂以及碳纳米管混合,得到混合物a;步骤105:对混合物a进行搅拌,得到均匀分散的环氧树脂液;步骤106:将均匀分散的环氧树脂液刷涂在经过喷丸处理的表面涂覆有金属铜层的钢板上并进行固化,得到层合物a;步骤107:利用磁控溅射方法在层合物a表面镀敷si层;步骤108:提供酚醛树脂、固化剂、阴离子表面活性剂(阴离子表面活性剂可以是本领域常用的任何阴离子表面活性剂,举例而言,烷基苯磺酸盐、α-烯烃磺酸盐、烷基磺酸盐、α-磺基单羧酸酯、脂肪酸磺烷基酯、琥珀酸酯磺酸盐、烷基萘磺酸盐、石油磺酸盐、木质素磺酸盐、烷基甘油醚磺酸盐均可实现本发明的目的)以及碳纳米管并将酚醛树脂、固化剂、阴离子表面活性剂以及碳纳米管混合,得到混合物b;步骤109:对混合物b进行搅拌,得到均匀分散的酚醛树脂液;以及步骤110:将均匀分散的酚醛树脂液刷涂在表面镀敷si层的层合物a表面并进行固化。图2是根据本发明一实施方式的产品结构图。如图所示,本发明的产品由下到上依次包括钢板层201、金属铜层202、环氧树脂层203、si层204以及酚醛树脂层205。实施例1钢板表面环保防腐蚀方法包括如下步骤:对待处理钢板进行表面清洁并进行干燥;在经过表面清洁的钢板表面进行化学镀铜以在钢板表面形成金属铜层;对表面涂覆有金属铜层的钢板进行喷丸处理;提供环氧树脂、固化剂、阴离子表面活性剂以及碳纳米管并将环氧树脂、固化剂、阴离子表面活性剂以及碳纳米管混合,得到混合物a;对混合物a进行搅拌,得到均匀分散的环氧树脂液;将均匀分散的环氧树脂液刷涂在经过喷丸处理的表面涂覆有金属铜层的钢板上并进行固化,得到层合物a;利用磁控溅射方法在层合物a表面镀敷si层;提供酚醛树脂、固化剂、阴离子表面活性剂以及碳纳米管并将酚醛树脂、固化剂、阴离子表面活性剂以及碳纳米管混合,得到混合物b;对混合物b进行搅拌,得到均匀分散的酚醛树脂液;将均匀分散的酚醛树脂液刷涂在表面镀敷si层的层合物a表面并进行固化。其中,在钢板表面形成的金属铜层的厚度为10μm。对表面涂覆有金属铜层的钢板进行喷丸处理的具体参数为:喷丸所用刚玉球粒径为50目,喷丸压力为1mpa。在混合物a中,以重量份计,环氧树脂占100份,固化剂占10份,阴离子表面活性剂占3份,碳纳米管占10份。对混合物a进行搅拌的具体参数为:搅拌温度为40℃,搅拌时间为50min。对环氧树脂液进行固化的具体参数为:固化温度为60℃,固化时间为2h。si层的厚度为100nm。在混合物b中,以重量份计,酚醛树脂占100份,固化剂占8份,阴离子表面活性剂占2份,碳纳米管占12份。对酚醛树脂液进行固化的具体参数为:固化温度为60℃,固化时间为2h。碳纳米管掺杂的环氧树脂层的厚度为30μm,碳纳米管掺杂的酚醛树脂层的厚度为40μm。实施例2钢板表面环保防腐蚀方法包括如下步骤:对待处理钢板进行表面清洁并进行干燥;在经过表面清洁的钢板表面进行化学镀铜以在钢板表面形成金属铜层;对表面涂覆有金属铜层的钢板进行喷丸处理;提供环氧树脂、固化剂、阴离子表面活性剂以及碳纳米管并将环氧树脂、固化剂、阴离子表面活性剂以及碳纳米管混合,得到混合物a;对混合物a进行搅拌,得到均匀分散的环氧树脂液;将均匀分散的环氧树脂液刷涂在经过喷丸处理的表面涂覆有金属铜层的钢板上并进行固化,得到层合物a;利用磁控溅射方法在层合物a表面镀敷si层;提供酚醛树脂、固化剂、阴离子表面活性剂以及碳纳米管并将酚醛树脂、固化剂、阴离子表面活性剂以及碳纳米管混合,得到混合物b;对混合物b进行搅拌,得到均匀分散的酚醛树脂液;将均匀分散的酚醛树脂液刷涂在表面镀敷si层的层合物a表面并进行固化。其中,在钢板表面形成的金属铜层的厚度为30μm。对表面涂覆有金属铜层的钢板进行喷丸处理的具体参数为:喷丸所用刚玉球粒径为100目,喷丸压力为2mpa。在混合物a中,以重量份计,环氧树脂占150份,固化剂占15份,阴离子表面活性剂占5份,碳纳米管占15份。对混合物a进行搅拌的具体参数为:搅拌温度为50℃,搅拌时间为100min。对环氧树脂液进行固化的具体参数为:固化温度为80℃,固化时间为4h。si层的厚度为300nm。在混合物b中,以重量份计,酚醛树脂占150份,固化剂占10份,阴离子表面活性剂占4份,碳纳米管占17份。对酚醛树脂液进行固化的具体参数为:固化温度为80℃,固化时间为4h。碳纳米管掺杂的环氧树脂层的厚度为60μm,碳纳米管掺杂的酚醛树脂层的厚度为70μm。实施例3钢板表面环保防腐蚀方法包括如下步骤:对待处理钢板进行表面清洁并进行干燥;在经过表面清洁的钢板表面进行化学镀铜以在钢板表面形成金属铜层;对表面涂覆有金属铜层的钢板进行喷丸处理;提供环氧树脂、固化剂、阴离子表面活性剂以及碳纳米管并将环氧树脂、固化剂、阴离子表面活性剂以及碳纳米管混合,得到混合物a;对混合物a进行搅拌,得到均匀分散的环氧树脂液;将均匀分散的环氧树脂液刷涂在经过喷丸处理的表面涂覆有金属铜层的钢板上并进行固化,得到层合物a;利用磁控溅射方法在层合物a表面镀敷si层;提供酚醛树脂、固化剂、阴离子表面活性剂以及碳纳米管并将酚醛树脂、固化剂、阴离子表面活性剂以及碳纳米管混合,得到混合物b;对混合物b进行搅拌,得到均匀分散的酚醛树脂液;将均匀分散的酚醛树脂液刷涂在表面镀敷si层的层合物a表面并进行固化。其中,在钢板表面形成的金属铜层的厚度为15μm。对表面涂覆有金属铜层的钢板进行喷丸处理的具体参数为:喷丸所用刚玉球粒径为60目,喷丸压力为1.5mpa。在混合物a中,以重量份计,环氧树脂占110份,固化剂占11份,阴离子表面活性剂占3.5份,碳纳米管占11份。对混合物a进行搅拌的具体参数为:搅拌温度为42℃,搅拌时间为60min。对环氧树脂液进行固化的具体参数为:固化温度为65℃,固化时间为2.5h。si层的厚度为150nm。在混合物b中,以重量份计,酚醛树脂占110份,固化剂占8.5份,阴离子表面活性剂占2.5份,碳纳米管占13份。对酚醛树脂液进行固化的具体参数为:固化温度为65℃,固化时间为2.5h。碳纳米管掺杂的环氧树脂层的厚度为40μm,碳纳米管掺杂的酚醛树脂层的厚度为50μm。实施例4钢板表面环保防腐蚀方法包括如下步骤:对待处理钢板进行表面清洁并进行干燥;在经过表面清洁的钢板表面进行化学镀铜以在钢板表面形成金属铜层;对表面涂覆有金属铜层的钢板进行喷丸处理;提供环氧树脂、固化剂、阴离子表面活性剂以及碳纳米管并将环氧树脂、固化剂、阴离子表面活性剂以及碳纳米管混合,得到混合物a;对混合物a进行搅拌,得到均匀分散的环氧树脂液;将均匀分散的环氧树脂液刷涂在经过喷丸处理的表面涂覆有金属铜层的钢板上并进行固化,得到层合物a;利用磁控溅射方法在层合物a表面镀敷si层;提供酚醛树脂、固化剂、阴离子表面活性剂以及碳纳米管并将酚醛树脂、固化剂、阴离子表面活性剂以及碳纳米管混合,得到混合物b;对混合物b进行搅拌,得到均匀分散的酚醛树脂液;将均匀分散的酚醛树脂液刷涂在表面镀敷si层的层合物a表面并进行固化。其中,在钢板表面形成的金属铜层的厚度为20μm。对表面涂覆有金属铜层的钢板进行喷丸处理的具体参数为:喷丸所用刚玉球粒径为70目,喷丸压力为1.5mpa。在混合物a中,以重量份计,环氧树脂占120份,固化剂占12份,阴离子表面活性剂占4份,碳纳米管占12份。对混合物a进行搅拌的具体参数为:搅拌温度为45℃,搅拌时间为70min。对环氧树脂液进行固化的具体参数为:固化温度为70℃,固化时间为3h。si层的厚度为200nm。在混合物b中,以重量份计,酚醛树脂占120份,固化剂占9份,阴离子表面活性剂占3份,碳纳米管占15份。对酚醛树脂液进行固化的具体参数为:固化温度为70℃,固化时间为3h。碳纳米管掺杂的环氧树脂层的厚度为40μm,碳纳米管掺杂的酚醛树脂层的厚度为60μm。实施例5钢板表面环保防腐蚀方法包括如下步骤:对待处理钢板进行表面清洁并进行干燥;在经过表面清洁的钢板表面进行化学镀铜以在钢板表面形成金属铜层;对表面涂覆有金属铜层的钢板进行喷丸处理;提供环氧树脂、固化剂、阴离子表面活性剂以及碳纳米管并将环氧树脂、固化剂、阴离子表面活性剂以及碳纳米管混合,得到混合物a;对混合物a进行搅拌,得到均匀分散的环氧树脂液;将均匀分散的环氧树脂液刷涂在经过喷丸处理的表面涂覆有金属铜层的钢板上并进行固化,得到层合物a;利用磁控溅射方法在层合物a表面镀敷si层;提供酚醛树脂、固化剂、阴离子表面活性剂以及碳纳米管并将酚醛树脂、固化剂、阴离子表面活性剂以及碳纳米管混合,得到混合物b;对混合物b进行搅拌,得到均匀分散的酚醛树脂液;将均匀分散的酚醛树脂液刷涂在表面镀敷si层的层合物a表面并进行固化。其中,在钢板表面形成的金属铜层的厚度为25μm。对表面涂覆有金属铜层的钢板进行喷丸处理的具体参数为:喷丸所用刚玉球粒径为80目,喷丸压力为1.5mpa。在混合物a中,以重量份计,环氧树脂占140份,固化剂占14份,阴离子表面活性剂占4.5份,碳纳米管占12份。对混合物a进行搅拌的具体参数为:搅拌温度为48℃,搅拌时间为80min。对环氧树脂液进行固化的具体参数为:固化温度为75℃,固化时间为3.5h。si层的厚度为250nm。在混合物b中,以重量份计,酚醛树脂占140份,固化剂占9.5份,阴离子表面活性剂占3.5份,碳纳米管占16份。对酚醛树脂液进行固化的具体参数为:固化温度为75℃,固化时间为3.5h。碳纳米管掺杂的环氧树脂层的厚度为55μm,碳纳米管掺杂的酚醛树脂层的厚度为65μm。对比例1与实施例1不同的步骤或者参数在于:在经过表面清洁的钢板表面进行化学镀铜以在钢板表面形成金属铜层。对比例2与实施例1不同的步骤或者参数在于:在制备环氧树脂液时,不添加提阴离子表面活性剂。对比例3与实施例1不同的步骤或者参数在于:不在层合物a表面镀敷si层。对比例4与实施例1不同的步骤或者参数在于:在钢板表面形成的金属铜层的厚度为50μm。对比例5与实施例1不同的步骤或者参数在于:对表面涂覆有金属铜层的钢板进行喷丸处理的具体参数为:喷丸所用刚玉球粒径为200目,喷丸压力为3mpa。对比例6与实施例1不同的步骤或者参数在于:在混合物a中,以重量份计,环氧树脂占90份,固化剂占10份,阴离子表面活性剂占10份,碳纳米管占20份。对比例7与实施例1不同的步骤或者参数在于:对混合物a进行搅拌的具体参数为:搅拌温度为30℃,搅拌时间为120min。对比例8与实施例1不同的步骤或者参数在于:对环氧树脂液进行固化的具体参数为:固化温度为90℃,固化时间为5h。对比例9与实施例1不同的步骤或者参数在于:si层的厚度为500nm。对比例10与实施例1不同的步骤或者参数在于:在混合物b中,以重量份计,酚醛树脂占90份,固化剂占9份,阴离子表面活性剂占8份,碳纳米管占20份。对比例11与实施例1不同的步骤或者参数在于:对酚醛树脂液进行固化的具体参数为:固化温度为90℃,固化时间为5h。对比例12与实施例1不同的步骤或者参数在于:碳纳米管掺杂的环氧树脂层的厚度为20μm,碳纳米管掺杂的酚醛树脂层的厚度为30μm。测试实施例1-5以及对比例1-12在75摄氏度下,被硫酸腐蚀的速率(单位为10-4g/(m2h)),其中,硫酸浓度为3wt%;同时测试表面复合薄膜与基材之间到的层间结合强度(单位为mpa),测试方法是本领域公知的方法。测试结果见表1。表1腐蚀速率结合强度实施例141.34.89实施例245.55.12实施例338.75.08实施例439.54.96实施例541.65.09对比例155.82.32对比例262.72.12对比例352.12.30对比例456.32.05对比例557.22.11对比例658.82.32对比例759.72.12对比例853.12.10对比例951.32.25对比例1057.22.11对比例1158.81.92对比例1262.12.07前述对本发明的具体示例性实施方案的描述是为了说明和例证的目的。这些描述并非想将本发明限定为所公开的精确形式,并且很显然,根据上述教导,可以进行很多改变和变化。对示例性实施例进行选择和描述的目的在于解释本发明的特定原理及其实际应用,从而使得本领域的技术人员能够实现并利用本发明的各种不同的示例性实施方案以及各种不同的选择和改变。本发明的范围意在由权利要求书及其等同形式所限定。当前第1页12