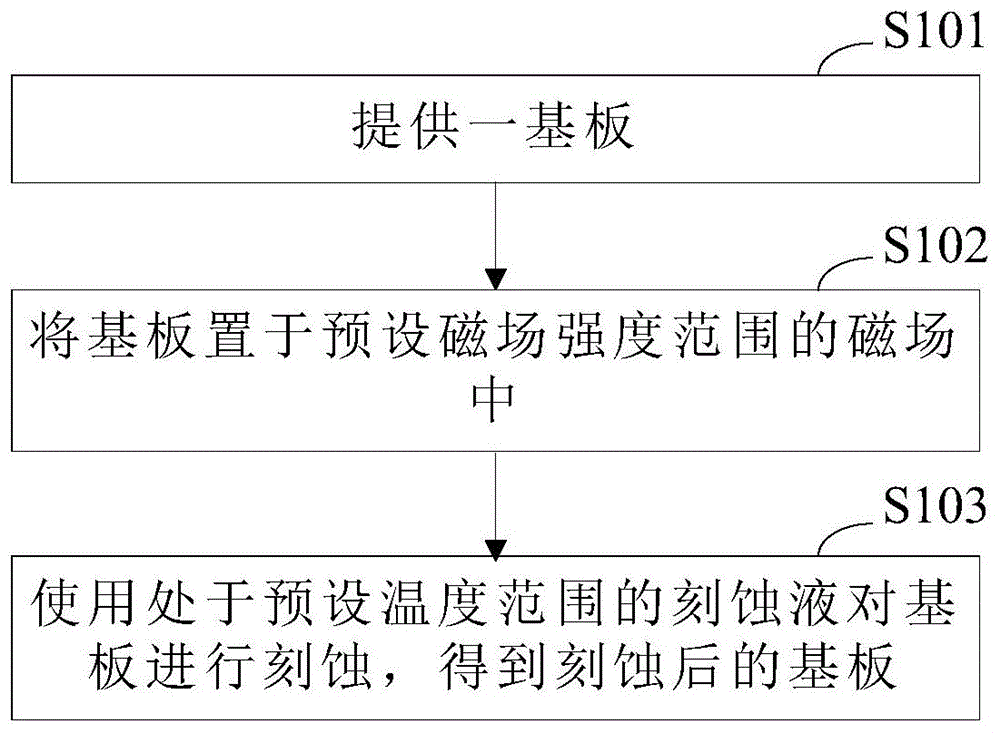
本发明涉及刻蚀领域,特别是涉及一种刻蚀液及刻蚀方法。
背景技术:
:随着智能移动终端的普及,显示面板技术得到广泛应用,其发展越来越迅速。在显示面板制程中,通常采用铜金属制成栅极线、数据线等走线,以传递各种信号,实现显示面板的显示功能。具体的,可以在基板上涂布铜薄膜,然后对铜薄膜进行图案化,形成各种金属线。其中,多余部分的铜需要采用刻蚀液进行刻蚀,然而现有的刻蚀液一般含有氟,对基板中的玻璃材料具有腐蚀作用,造成显示面板的良品率降低。技术实现要素:本发明的目的在于提供一种刻蚀液及刻蚀方法,可以提高显示面板的良品率。本发明实施例提供了一种刻蚀液,其包括:去离子水、双氧水、有机酸、胺类物质、弱酸弱碱盐、双氧水稳定剂以及醇类物质。在一实施例中,所述去离子水在所述刻蚀液中的质量百分比范围为60%至88.35%之间;所述双氧水在所述刻蚀液中的质量百分比范围为5%至8%之间;所述有机酸在所述刻蚀液中的质量百分比范围为5%至15%之间;所述胺类物质在所述刻蚀液中的质量百分比范围为1%至10%之间;所述弱酸弱碱盐在所述刻蚀液中的质量百分比范围为0.1%至1%之间;所述双氧水稳定剂在所述刻蚀液中的质量百分比范围为0.05%至1%之间;所述醇类物质在所述刻蚀液中的质量百分比范围为0.5%至5%之间。在一实施例中,所述有机酸包括柠檬酸,苹果酸,丁二酸,乳酸,乙醇酸,苯甲酸中的一种或多种。在一实施例中,所述胺类物质包括二异丙醇胺,异丙醇胺,乙酰苯胺以及2-氨基-2甲基-1-丙醇中的一种或多种。在一实施例中,所述弱酸弱碱盐包括磷酸氢二铵或醋酸铵。在一实施例中,所述双氧水稳定剂为苯基脲。在一实施例中,所述醇类物质包括乙醇,甲醇,乙二醇,苯甲醇中的一种或多种。本发明实施例提供了一种刻蚀方法,使用如上所述的刻蚀液进行刻蚀,其包括:提供一基板;将所述基板置于预设磁场强度范围的磁场中;使用处于预设温度范围的所述刻蚀液对所述基板进行刻蚀,得到刻蚀后的基板。在一实施例中,所述预设温度范围为30摄氏度至35摄氏度之间。在一实施例中,所述预设磁场强度范围为0.3特斯拉至0.7特斯拉之间。相较于现有的刻蚀液及刻蚀方法,本发明的刻蚀液及刻蚀方法中的刻蚀液包括去离子水、双氧水、有机酸、胺类物质、弱酸弱碱盐、双氧水稳定剂以及醇类物质,不包括氟,避免了氟对基板的腐蚀,提高了显示面板的良品率。为让本发明的上述内容能更明显易懂,下文特举优选实施例,并配合所附图式,作详细说明如下:附图说明图1为本发明实施例提供的刻蚀方法的流程示意图。图2为本发明实施例提供的刻蚀方法的场景示意图。图3为本发明实施例提供的刻蚀方法的另一场景示意图。图4为本发明实施例提供的刻蚀方法的又一场景示意图。具体实施方式以下各实施例的说明是参考附加的图式,用以例示本发明可用以实施的特定实施例。本发明所提到的方向用语,例如「上」、「下」、「前」、「后」、「左」、「右」、「内」、「外」、「侧面」等,仅是参考附加图式的方向。因此,使用的方向用语是用以说明及理解本发明,而非用以限制本发明。在图中,结构相似的单元是以相同标号表示。在本文中提及“实施例”意味着,结合实施例描述的特定特征、结构或特性可以包含在本发明的至少一个实施例中。在说明书中的各个位置出现该短语并不一定均是指相同的实施例,也不是与其它实施例互斥的独立的或备选的实施例。本领域技术人员显式地和隐式地理解的是,本文所描述的实施例可以与其它实施例相结合。本发明实施例提供了一种刻蚀液,该刻蚀液用于对显示面板中的基板进行刻蚀,其中基板上有铜cu薄膜和钼mo薄膜。如下表1所示,刻蚀液的组成成分包括去离子水、双氧水、有机酸、胺类物质、弱酸弱碱盐、双氧水稳定剂以及醇类物质。表1刻蚀液的组成成分质量百分比范围去离子水60%-88.35%双氧水5%-8%有机酸5%-15%胺类物质1%-10%弱酸弱碱盐0.1%-1%双氧水稳定剂0.05%-1%醇类物质0.5%-5%双氧水可以将基板中的钼氧化成三氧化钼moo3,铜氧化成氧化铜cuo。如表1所示,双氧水在刻蚀液中的质量百分比范围为5%至8%之间。在本实施例中,双氧水在刻蚀液中的质量百分比低于8%,可以提高刻蚀液生产过程中的安全性。双氧水稳定剂可以避免双氧水在高温下被分解。其中,双氧水稳定剂可以为苯基脲。如表1所示,双氧水稳定剂在所述刻蚀液中的质量百分比范围为0.05%至1%之间。去离子水不仅可以避免双氧水被分解,还可以避免刻蚀液中引入金属离子的干扰。如表1所示,去离子水在刻蚀液中的质量百分比范围为60%至88.35%之间。有机酸可以与cuo、moo3反应,得到铜离子和钼离子,并络合铜离子和钼离子。有机酸包括柠檬酸,苹果酸,丁二酸,乳酸,乙醇酸,苯甲酸中的一种或多种。如表1所示,有机酸在刻蚀液中的质量百分比范围为5%至15%之间。在本实施例中不需要无机酸,可以提高刻蚀液生产过程中的安全性能。胺类物质可以使铜与钼的刻蚀产生速率差,即使铜的刻蚀速度大于钼的刻蚀速度。其中,胺类物质包括二异丙醇胺,异丙醇胺,乙酰苯胺和2-氨基-2甲基-1-丙醇中的一种或多种。如表1所示,胺类物质在所述刻蚀液中的质量百分比范围为1%至10%之间。弱酸弱碱盐可以释放氢离子,调节刻蚀液的ph(hydrogenionconcentration,氢离子浓度指数)值。可以防止ph值过高导致的钼刻蚀过快。其中,弱酸弱碱盐包括磷酸氢二铵或醋酸铵。如表1所示,弱酸弱碱盐在所述刻蚀液中的质量百分比范围为0.1%至1%之间。醇类物质可以使上述有机酸、弱酸弱碱盐等有机物或无机物溶解。其中,醇类物质包括乙醇,甲醇,乙二醇,苯甲醇中的一种或多种。如表1所示,醇类物质在所述刻蚀液中的质量百分比范围为0.5%至5%之间。在一实施例中,刻蚀液可以为表2中所示的刻蚀液a。如下表2所示,刻蚀液a的组成成分包括去离子水、双氧水、柠檬酸、二异丙醇胺、磷酸氢二铵、苯基脲以及乙醇。上述组成成分在刻蚀液a中的质量百分比依次为70.7%、7.5%、10%、9.5%、0.8%、0.5%以及1%。通过刻蚀液a对基板进行刻蚀后,如图3所示,基板100中铜101的断面倾斜度可以达到34.5度,即锥角θ可以达到34.5度,cdloss(条宽损失)l为0.8微米。如图4所示,钼没有残留。表2刻蚀液a的组成成分质量百分比去离子水70.7%双氧水7.5%柠檬酸10%二异丙醇胺9.5%磷酸氢二铵0.8%苯基脲0.5%乙醇1%本发明实施例的刻蚀液中不包含氟,可以避免对基板中的玻璃造成腐蚀。进一步的,本发明实施例中的刻蚀液双氧水的质量百分比低于8%,可以提高刻蚀液生产过程中的安全性。并且本发明实施例中的刻蚀液不包含无机酸,可以提高刻蚀液生产过程中的安全性能。本发明实施例还提供了一种刻蚀方法,该刻蚀方法采用如上的刻蚀液进行刻蚀。请参照图1,图1为本发明实施例提供的刻蚀方法的流程图,该刻蚀方法包括如下步骤:步骤s101,提供一基板。其中,基板上有铜cu薄膜和钼mo薄膜。其中,钼薄膜设置在基板本体和铜薄膜之间,以增加铜与基板本体之间的贴附性。通过对铜薄膜图案化,可以形成栅极线、数据线等金属配线。对于多余的铜或钼,可以采用本实施例的刻蚀液进行刻蚀。步骤s102,将基板置于预设磁场强度范围的磁场中。如图2所示,在一实施例中,可以将基板1置于预设磁场强度范围为0.3特斯拉至0.7特斯拉之间的磁场2中。其中,磁场2可以促进刻蚀液对流,加快刻蚀液与铜的反应。需要说明的是,在上述预设磁场强度范围内,磁场2的磁场强度越大,刻蚀液与铜的反应越快,得到的锥角越小。步骤s103,使用处于预设温度范围的刻蚀液对基板进行刻蚀,得到刻蚀后的基板。在一实施例中,可以对刻蚀液加热,使刻蚀液达到30摄氏度至35摄氏度之间的预设温度范围。需要说明的是,在上述预设温度范围内,刻蚀液的刻蚀速率随着温度的升高而提高。然后将刻蚀液均匀喷洒到基板表面进行刻蚀。约100-120秒后,可以完成刻蚀。在本实施例中,不需要添加刻蚀抑制剂,通过调整刻蚀液的温度即可以对刻蚀速率进行调节,降低了刻蚀成本。现有的刻蚀液对基板进行刻蚀后,一般得到50度至60度范围的锥角,此范围的锥角较大,导致基板的电学性能降低。采用本实施例的刻蚀液对基板进行刻蚀,可以得到33度至45度范围的锥角,可以使基板具有较好的电学性能。接下来,以如表2所示的刻蚀液a为例,对基板进行刻蚀。首先将基板1置于磁场强度为0.6特斯拉的均匀磁场2中。然后将刻蚀液a加热到32摄氏度。再将加热后的刻蚀液a均匀喷洒到基板1的表面进行刻蚀。刻蚀时间达到110秒后,即完成刻蚀。其中,如图3所示,铜10的断面倾斜度可以达到34.5度,即锥角θ可以达到34.5度,cdloss(条宽损失)l为0.8微米。如图4所示,钼没有残留。本发明实施例的刻蚀方法,通过磁场调节刻蚀液的对流情况以及刻蚀液的温度,来控制刻蚀液与铜的反应速率,使铜得到较小的锥角。综上所述,虽然本发明已以优选实施例揭露如上,但上述优选实施例并非用以限制本发明,本领域的普通技术人员,在不脱离本发明的精神和范围内,均可作各种更动与润饰,因此本发明的保护范围以权利要求界定的范围为准。当前第1页12