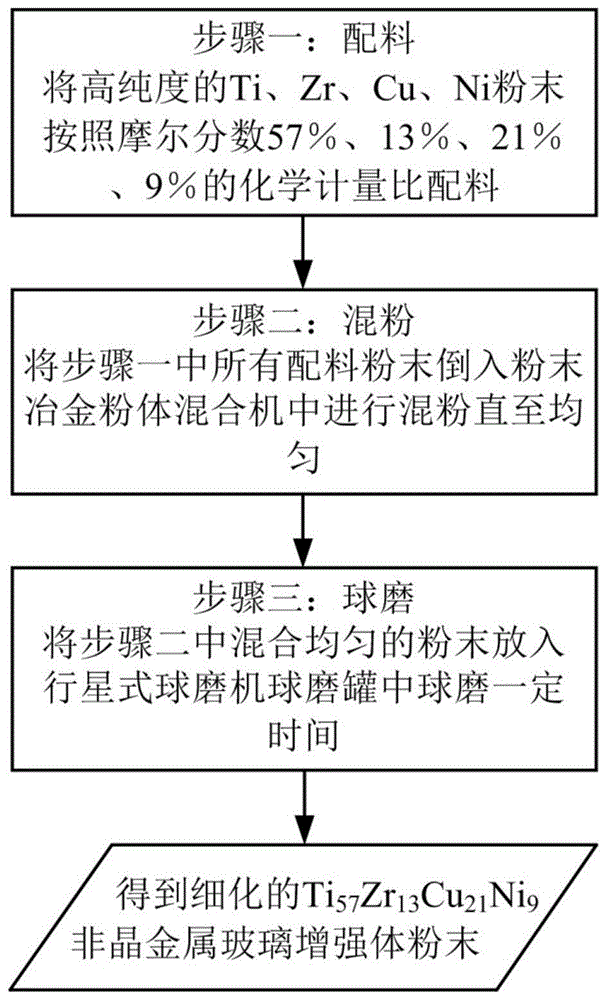
本发明属于非晶金属玻璃及其复合材料
技术领域:
,具体涉及一种钛基金属玻璃增强体的制备方法。
背景技术:
:随着航空、航天、国防、汽车等工业的飞速发展,人们对材料性能要求越来越高,特别是新型高性能轻质金属材料的研发变的越来越迫切,对于金属材料增强体的研究越来越多。非晶金属玻璃由于具有优异的力学、物理、化学和机械性能,包括高强度、高硬度、良好的耐磨及耐蚀性能,是复合材料增强体的重要发展方向与研究热点,而且金属玻璃比陶瓷更容易与金属之间发生元素扩散,改善增强体与基材之间的润湿性能。目前常用的非晶金属玻璃增强体有cu基、zr基、ti基等。ti基金属玻璃不仅密度小,而且强度高、硬度高、韧性好、耐腐蚀性优良,是质轻、高强、生物相容结构及工程增强材料的重要组成部分。此外,钛基金属玻璃与工程常用的铝基基材润湿性较好,使得增强体与基体之间存在良好的界面性能,而被广泛使用。目前制备钛基金属玻璃的方法主要有气雾化法和机械变形法,气雾化法制备金属玻璃粉末设备昂贵,工艺过程复杂,操作不便,效率低,粒径粗大,难以实现低成本规模化制备;而机械变形法制备非晶粉体效率较低,不利于实现规模化生产,且得到的非晶粉体粒径粗大,使得金属材料冲击韧度和疲劳强度增加不明显,难以直接应用。因此探索简单高效的细化钛基金属玻璃增强体制备新技术成为当前非晶金属基复合增强工程材料研究的重要方向和热点。有鉴于此,本发明人通过大量实验分析发现研究出本发明方法,以解决上述问题。技术实现要素:为了解决现有技术中存在的上述问题,本发明提供一种钛基金属玻璃增强体的制备方法,该制备方法过程简单,效率高,操作方便,成本低,易于实现细化钛基非晶金属玻璃粉末的规模化生产。本发明要解决的技术问题通过以下技术方案实现:本发明提供一种钛基金属玻璃增强体的制备方法,该制备方法包括以下步骤:步骤一:配料将高纯度ti、zr、cu、ni粉末按照摩尔分数ti-57%、zr-13%、cu-21%、ni-9%的化学计量比配料;步骤二:混粉将步骤一中所有配料粉末倒入经超声清洗并干燥后的不锈钢料筒中,在粉末冶金粉体混合机中进行混粉直至均匀;步骤三:球磨将步骤二中混合均匀的粉末放入行星式球磨机球磨罐中球磨,一定时间后制备出细化的ti57zr13cu21ni9非晶金属玻璃增强体粉末。进一步地,步骤一中ti、zr、cu、ni粉末纯度分别为99.0%、99.9%、99.8%、99.0%,粉末颗粒大小均为2-50μm。进一步地,步骤二中的超声清洗是将不锈钢料筒依次放入丙酮、无水乙醇以及去离子水中分别进行超声清洗10min,然后经高纯氮气吹干。进一步地,步骤二中的粉末冶金粉体混合机总混合时间设定为20min,叶片正转2min后,自动反转2min,依次循环,直至总混合时间20min,料桶、搅拌叶片停止运动后,取下料桶。进一步地,步骤三中行星式球磨机配用不锈钢磨球,磨球球径分别为15mm、10mm、5mm,球料比为2:1,球磨转速为240r/min,球磨时间为40h-60h。进一步地,步骤三中球磨机的球磨罐中充满氩气。进一步地,步骤三中将球磨程序设定为每转动30min后冷却10min。与现有技术相比,本发明具有如下有益效果:1.本发明的一种钛基金属玻璃增强体的制备方法采用高能球磨技术,制备ti57zr13cu21ni9非晶金属玻璃增强体粉末,该制备方法步骤少,效率高,操作方便,成本低,易于实现钛基非晶金属玻璃粉末的规模化制备。2.本发明方法制备的ti57zr13cu21ni9非晶金属玻璃增强体粉末,经实验验证粉体细化程度达到0.5-2μm,粒径细化显著提高材料冲击韧度和疲劳强度,表现出的硬度明显增大,可作为复合材料中承受载荷的良好增强组分。3.本发明在对混合均匀的粉末进行球磨时,在球磨机的球磨罐中充满氩气,有效避免了氧气对粉末的氧化影响。4.本发明在对混合均匀的粉末进行球磨时,将球磨程序设定为每转动30min后冷却10min,目的是在提高出粉率的同时防止罐体过热及过热产生的粘壁现象,降低安全隐患。5.本发明在完成配料后,倒入料筒进行混粉前,需对料筒进行超声清洗,具体包括将料筒依次放入丙酮、无水乙醇以及去离子水中分别进行超声清洗10min,然后经高纯氮气吹干,经上述超声清洗确保料筒无有机物、油污和杂质,排除干扰因素,提高非晶产物纯度。附图说明图1为本发明钛基非晶金属玻璃增强体ti57zr13cu21ni9的制备流程图;图2为本发明ti、zr、cu、ni粉末混粉后的扫描电子显微镜图;图3为本发明ti、zr、cu、ni粉末混粉后的x射线衍射图谱;图4为采用本发明方法球磨40h后粉体的扫描电子显微镜图;图5为采用本发明方法球磨40h后粉体的x射线衍射图谱。具体实施方式为使本发明所解决的技术问题、技术方案及有益效果更加清晰,以下结合附图及实施例,对本发明作进一步详细说明。应当理解,此处所描述的具体实施例仅用以解释本发明,并不限定本发明,详细说明如下。发明构思:发明人经过探索发现现有制备钛基金属玻璃的方法主要有气雾化法和机械变形法,气雾化技术可以较为理想的实现金属玻璃的制备,但其处理工艺过程复杂,操作不便,效率低,粒径粗大,难以实现低成本规模化制备。而现有机械变形法制备非晶粉体效率较低,不利于实现规模化生产,且得到的非晶粉体粒径粗大,使得金属材料冲击韧度和疲劳强度增加不明显,难以直接应用。为了更简单有效制备钛基非晶金属玻璃增强体粉末,本发明人开始向机械合金化制备方法构思,经过不断的实验分析发现,采用高能球磨技术制备出ti57zr13cu21ni9非晶粉体,其制备过程简单,效率高,成本低,非晶形成能力强,适合规模化生产,且制备的非晶粉体细化,硬度增高,可作为复合材料中承受载荷的良好增强组分。发明人通过不断调整实验参数和步骤,作出了本发明更为理想的球磨制备工艺,参见图1,本发明还通过对所得到的ti57zr13cu21ni9非晶粉体扫描电子显微镜图、x射线衍射图及力学性能结果进行相应的验证。以下结合实施例和附图对本发明的特征和性能作进一步的详细描述。实施例1步骤一、配料:将质量分数为99.0%、99.9%、99.8%、99.0%的ti、zr、cu、ni粉末(颗粒大小均在2-50μm之间)按照ti-57%、zr-13%、cu-21%、ni-9%摩尔分数计量比配料,各元素粉末称重采用精度为0.01g的电子天平。步骤二、混粉:1)将不锈钢料筒置于丙酮中超声清洗10min,以去除料筒表面有机物;2)将丙酮超声清洗后的不锈钢料筒置于无水乙醇中超声清洗10min,以去除料筒表面油污;3)将无水乙醇超声清洗后的不锈钢料筒置于去离子水中超声清洗10min,以去除料筒表面杂质,然后经高纯氮气99.999%(o2≤0.001%)吹干;4)将步骤一中的所有配料粉末装入经超声清洗并干燥后的不锈钢料筒中,在粉末冶金粉体混合机中进行混粉直至均匀,其中设置总混合时间为20min,叶片正转2min后,自动反转2min,依次循环,然后启动电源及叶片运行开关开始混合,直至总混合时间20min,料桶、搅拌叶片停止运动后,取下料桶。混合后的粉体扫描电子显微镜结果如图2所示,此时粉体粒径尺度较大,硬度仅为1880mpa(表1)。混合后的粉体x射线衍射谱(xrd)如图3所示,由图谱可以明显观察到ti、zr、cu、ni4种高强度晶体衍射峰。实施例2步骤一、配料:将质量分数为99.0%、99.9%、99.8%、99.0%的ti、zr、cu、ni粉末(颗粒大小均在2-50μm之间)按照ti-57%、zr-13%、cu-21%、ni-9%摩尔分数计量比配料,各元素粉末称重采用精度为0.01g的电子天平。步骤二、混粉:1)将不锈钢料筒置于丙酮中超声清洗10min,以去除料筒表面有机物;2)将丙酮超声清洗后的不锈钢料筒置于无水乙醇中超声清洗10min,以去除料筒表面油污;3)将无水乙醇超声清洗后的不锈钢料筒置于去离子水中超声清洗10min,以去除料筒表面杂质,然后经高纯氮气99.999%(o2≤0.001%)吹干;4)将步骤一中的所有配料粉末装入经超声清洗并干燥后的不锈钢料筒中,在粉末冶金粉体混合机中进行混粉直至均匀,其中设置总混合时间为20min,叶片正转2min后,自动反转2min,依次循环,然后启动电源及叶片运行开关开始混合,直至总混合时间20min,料桶、搅拌叶片停止运动后,取下料桶。步骤三、球磨:1)采用行星式球磨机,其配用不锈钢磨球,磨球球径分别为15mm、10mm、5mm,优选球料比为2:1,将步骤二中混合均匀的粉末放入球磨罐中,并固定安装在球磨机托罐上,优选的,在球磨罐中充满氩气,避免氧气对粉末的氧化影响。2)接通电源,打开空气开关,将球磨程序设定为每转动30min后冷却10min,防止球磨罐体过热以及过热产生的粘壁现象,提高出粉率,降低安全隐患。然后设置球磨时间为10h,转速为240r/min,顺时针旋转安全开关,启动运行开关;3)球磨过程结束后,拧松两角螺母,取下球磨罐,分离磨球与物料,得到如表1所示粉体结构(xrd)为晶体,经测试粉体硬度为2690mpa,粉体粒径为1-20μm。实施例3步骤一、配料:将质量分数为99.0%、99.9%、99.8%、99.0%的ti、zr、cu、ni粉末(颗粒大小均在2-50μm之间)按照ti-57%、zr-13%、cu-21%、ni-9%摩尔分数计量比配料,各元素粉末称重采用精度为0.01g的电子天平。步骤二、混粉:1)将不锈钢料筒置于丙酮中超声清洗10min,以去除料筒表面有机物;2)将丙酮超声清洗后的不锈钢料筒置于无水乙醇中超声清洗10min,以去除料筒表面油污;3)将无水乙醇超声清洗后的不锈钢料筒置于去离子水中超声清洗10min,以去除料筒表面杂质,然后经高纯氮气99.999%(o2≤0.001%)吹干;4)将步骤一中的所有配料粉末装入经超声清洗并干燥后的不锈钢料筒中,在粉末冶金粉体混合机中进行混粉直至均匀,其中设置总混合时间为20min,叶片正转2min后,自动反转2min,依次循环,然后启动电源及叶片运行开关开始混合,直至总混合时间20min,料桶、搅拌叶片停止运动后,取下料桶。步骤三、球磨:1)采用行星式球磨机,其配用不锈钢磨球,磨球球径分别为15mm、10mm、5mm,优选球料比为2:1,将步骤二中混合均匀的粉末放入球磨罐中,并固定安装在球磨机托罐上,优选的,在球磨罐中充满氩气,避免氧气对粉末的氧化影响。2)接通电源,打开空气开关,将球磨程序设定为每转动30min后冷却10min,防止球磨罐体过热以及过热产生的粘壁现象,提高出粉率,降低安全隐患。然后设置球磨时间为20h,转速为240r/min,顺时针旋转安全开关,启动运行开关;3)球磨过程结束后,拧松两角螺母,取下球磨罐,分离磨球与物料,得到如表1所示粉体结构(xrd)为晶体,经测试粉体硬度为4030mpa,粉体粒径为1-10μm。实施例4步骤一、配料:将质量分数为99.0%、99.9%、99.8%、99.0%的ti、zr、cu、ni粉末(颗粒大小均在2-50μm之间)按照ti-57%、zr-13%、cu-21%、ni-9%摩尔分数计量比配料,各元素粉末称重采用精度为0.01g的电子天平。步骤二、混粉:1)将不锈钢料筒置于丙酮中超声清洗10min,以去除料筒表面有机物;2)将丙酮超声清洗后的不锈钢料筒置于无水乙醇中超声清洗10min,以去除料筒表面油污;3)将无水乙醇超声清洗后的不锈钢料筒置于去离子水中超声清洗10min,以去除料筒表面杂质,然后经高纯氮气99.999%(o2≤0.001%)吹干;4)将步骤一中的所有配料粉末装入经超声清洗并干燥后的不锈钢料筒中,在粉末冶金粉体混合机中进行混粉直至均匀,其中设置总混合时间为20min,叶片正转2min后,自动反转2min,依次循环,然后启动电源及叶片运行开关开始混合,直至总混合时间20min,料桶、搅拌叶片停止运动后,取下料桶。步骤三、球磨:1)采用行星式球磨机,其配用不锈钢磨球,磨球球径分别为15mm、10mm、5mm,优选球料比为2:1,将步骤二中混合均匀的粉末放入球磨罐中,并固定安装在球磨机托罐上,优选的,在球磨罐中充满氩气,避免氧气对粉末的氧化影响。2)接通电源,打开空气开关,将球磨程序设定为每转动30min后冷却10min,防止球磨罐体过热以及过热产生的粘壁现象,提高出粉率,降低安全隐患。然后设置球磨时间为30h,转速为240r/min,顺时针旋转安全开关,启动运行开关;3)球磨过程结束后,拧松两角螺母,取下球磨罐,分离磨球与物料,得到如表1所示粉体结构(xrd)为晶体,经测试粉体硬度为6030mpa,粉体粒径为1-5μm。实施例5步骤一、配料:将质量分数为99.0%、99.9%、99.8%、99.0%的ti、zr、cu、ni粉末(颗粒大小均在2-50μm之间)按照ti-57%、zr-13%、cu-21%、ni-9%摩尔分数计量比配料,各元素粉末称重采用精度为0.01g的电子天平。步骤二、混粉:1)将不锈钢料筒置于丙酮中超声清洗10min,以去除料筒表面有机物;2)将丙酮超声清洗后的不锈钢料筒置于无水乙醇中超声清洗10min,以去除料筒表面油污;3)将无水乙醇超声清洗后的不锈钢料筒置于去离子水中超声清洗10min,以去除料筒表面杂质,然后经高纯氮气99.999%(o2≤0.001%)吹干;4)将步骤一中的所有配料粉末装入经超声清洗并干燥后的不锈钢料筒中,在粉末冶金粉体混合机中进行混粉直至均匀,其中设置总混合时间为20min,叶片正转2min后,自动反转2min,依次循环,然后启动电源及叶片运行开关开始混合,直至总混合时间20min,料桶、搅拌叶片停止运动后,取下料桶。步骤三、球磨:1)采用行星式球磨机,其配用不锈钢磨球,磨球球径分别为15mm、10mm、5mm,优选球料比为2:1,将步骤二中混合均匀的粉末放入球磨罐中,并固定安装在球磨机托罐上,优选的,在球磨罐中充满氩气,避免氧气对粉末的氧化影响。2)接通电源,打开空气开关,将球磨程序设定为每转动30min后冷却10min,防止球磨罐体过热以及过热产生的粘壁现象,提高出粉率,降低安全隐患。然后设置球磨时间为40h,转速为240r/min,顺时针旋转安全开关,启动运行开关;3)球磨过程结束后,拧松两角螺母,取下球磨罐,分离磨球与物料。球磨40h后得到的粉体物料扫描电子显微镜结果如图4所示,由图可以看出球磨后粉体粒径明显细化(0.5-2μm),硬度显著提高到7050mpa(表1)。球磨40h后粉体的x射线衍射谱如图5所示,由图可以发现球磨40h后ti、zr、cu、ni四种晶体衍射峰消失,衍射峰强度不断降低,且衍射谱主要表现为漫散射峰,表明ti57zr13cu21ni9非晶粉体已经形成,从而实现细化钛基非晶金属玻璃颗粒增强体的高能球磨制备。实施例6步骤一、配料:将质量分数为99.0%、99.9%、99.8%、99.0%的ti、zr、cu、ni粉末(颗粒大小均在2-50μm之间)按照ti-57%、zr-13%、cu-21%、ni-9%摩尔分数计量比配料,各元素粉末称重采用精度为0.01g的电子天平。步骤二、混粉:1)将不锈钢料筒置于丙酮中超声清洗10min,以去除料筒表面有机物;2)将丙酮超声清洗后的不锈钢料筒置于无水乙醇中超声清洗10min,以去除料筒表面油污;3)将无水乙醇超声清洗后的不锈钢料筒置于去离子水中超声清洗10min,以去除料筒表面杂质,然后经高纯氮气99.999%(o2≤0.001%)吹干;4)将步骤一中的所有配料粉末装入经超声清洗并干燥后的不锈钢料筒中,在粉末冶金粉体混合机中进行混粉直至均匀,其中设置总混合时间为20min,叶片正转2min后,自动反转2min,依次循环,然后启动电源及叶片运行开关开始混合,直至总混合时间20min,料桶、搅拌叶片停止运动后,取下料桶。步骤三、球磨:1)采用行星式球磨机,其配用不锈钢磨球,磨球球径分别为15mm、10mm、5mm,优选球料比为2:1,将步骤二中混合均匀的粉末放入球磨罐中,并固定安装在球磨机托罐上,优选的,在球磨罐中充满氩气,避免氧气对粉末的氧化影响。2)接通电源,打开空气开关,将球磨程序设定为每转动30min后冷却10min,防止球磨罐体过热以及过热产生的粘壁现象,提高出粉率,降低安全隐患。然后设置球磨时间为60h,转速为240r/min,顺时针旋转安全开关,启动运行开关;3)球磨过程结束后,拧松两角螺母,取下球磨罐,分离磨球与物料,得到如表1所示粉体结构(xrd)为非晶体,经测试粉体硬度为7020mpa,粉体粒径为0.5-1μm。球磨不同时间下的粉体结构及粒径如表1所示。由表中数据分析可知,随着球磨时间的延长,粉体粒径不断细化。球磨40h能够实现钛基非晶金属玻璃的球磨细化制备,且制备粉体硬度高,力学性能好。球磨时间过低(0-30h)得到的粉体结构(xrd)为晶体,因此表现出的硬度低,力学性能差。球磨时间过高(60h),虽可实现钛基非晶金属玻璃的球磨制备,但其粉体硬度基本趋于稳定,力学性能变化不明显。因此,40h球磨时间作为本发明专利的优选实施例。表1:实施例球磨时间(h)粉体结构(xrd)粉体硬度(mpa)粉体粒径(μm)10晶体18802-50210晶体26901-20320晶体40301-10430晶体60301-5540非晶体70500.5-2660非晶体70200.5-1为进一步验证本发明方法优选得到的非晶金属玻璃增强体粉末硬度优良,发明人通过实验验证了多种现有技术中的粉末冶金颗粒增强体的硬度,结果如表2所示:表2粉末冶金颗粒增强体粉体硬度(mpa)(本发明)ti57zr13cu21ni97050ti55.5cu18.5ni7.5al8.56300-6500zr65ni355850zr65ti5ni305600mo40fe40b201910对比表2数据可知,本发明方法制备的非晶金属玻璃增强体粉末硬度高于其他增强体粉末冶金颗粒,其力学性能优良,因此可作为复合材料中承受载荷的良好颗粒增强组分。具体的,本发明采用行星式球磨机,配用不锈钢磨球,磨球球径分别为15mm、10mm、5mm,球磨时间为40h,球磨转速为240r/min,为了得到更佳细化的ti57zr13cu21ni9非晶金属玻璃增强体粉末,发明人通过调整球磨工艺过程中的球料比参数,通过实验得到不同球料比下的粉体粒径如表3所示:表3球料比粉体粒径(μm)1:12.5-52:10.5-25:12-310:14-520:18-10对比表3数据可知,当球料比由1:1增加到2:1,粉体晶粒不断细化,粒径达到最小值0.5-2μm。然而,当球料比进一步增加到20:1,粉体粒径开始增加,这是由于球料比增加,粉体吸收磨球传递的冲击功增大,温度升高,粉体团聚驱动力增强,导致粉体粒径增加。一般情况下粒径越细,不同取向晶粒越多,位错移动阻力越强,因此粒径细化可以显著提高金属材料塑性、屈服点、冲击韧度、疲劳强度和硬度。基于此,作为本发明专利的优选球料比为2:1。综上所述,本发明方法制备过程简单,效率高,成本低,非晶形成能力强,适合规模化生产,制备的ti57zr13cu21ni9非晶金属玻璃粉体细化,硬度优良,可直接应用于复合材料中承受载荷。以上内容是结合具体的优选实施方式对本发明所作的进一步详细说明,不能认定本发明的具体实施只局限于这些说明。对于本发明所属
技术领域:
的普通技术人员来说,在不脱离本发明构思的前提下,还可以做出若干简单推演或替换,都应当视为属于本发明的保护范围。当前第1页12