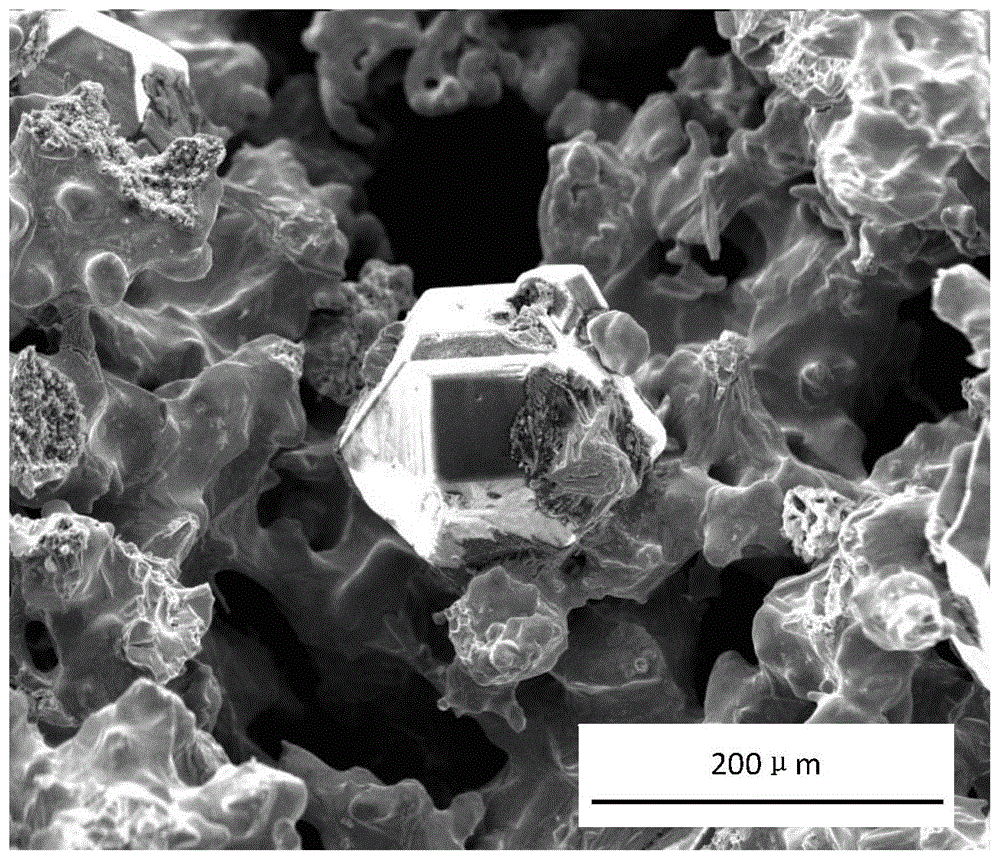
本发明涉及材料加工、制备领域,具体而言,涉及金刚石磨具及其制备方法。
背景技术:
:高强度、耐高温、耐腐蚀的材料如金属间化合物、高温合金、工程陶瓷、硬质合金等难加工材料,具有硬度高、磨削力大、磨削温度高、磨削容易黏附等特点,在磨削过程中容易出现工件烧伤、裂痕、磨具堵塞钝化等问题,影响工件的磨削效率和表面加工质量。金刚石作为超硬磨料,本身具有极高的硬度、较好的导热率和良好的耐磨性。金属结合剂金刚石磨具因具有结合强度高、成型性好、使用寿命长,能满足高速磨削和超精密磨削技术的要求等特征,已成为各种高密度、高硬度和硬脆材料的重要加工工具。一般地,金属结合剂金刚石磨具的性能应当满足如下要求:(1)对金刚石具有较高的把持力;(2)具有接近于金刚石的膨胀系数,以减少两者之间的缝隙;(3)对金刚石的热损伤小;(4)对金刚石具有良好的润湿性。传统的金属结合剂金刚石磨具多采用粉末冶金法制备得到,其结合剂组织致密、孔隙率较低,磨具在磨削过程中自锐性较差,磨屑易堵塞气孔或黏附在金刚石或磨具基体表面,导致磨削力增加,磨削温度升高,最后烧伤工件,且对磨具修整修锐比较困难,在一定程度上限制了其应用。有鉴于此,特提出本发明。技术实现要素:本发明的第一目的在于提供一种金刚石磨具,所述金刚石磨具孔隙率高、磨削效率高,其复合涂层以特定用量的过渡金属氧化物用作填充材料,不仅有利于提高金刚石磨具的孔隙率,还有利于降低金刚石颗粒的热损伤,提高金刚石颗粒的钎焊活性,同时降低熔覆金属的线膨胀系数,使熔覆金属与金刚石颗粒的线膨胀系数更匹配,防止金刚石颗粒在焊接热应力作用下产生裂纹。本发明的第二目的在于提供上述金刚石磨具的制备方法,该方法简单高效、连续性强,周期短,有利于大规模工业推广。为了实现本发明的上述目的,特采用以下技术方案:金刚石磨具,其包括基材以及附着在所述基材表面的至少一层复合涂层;所述复合涂层包括0.5wt.%~5.5wt.%的金刚石颗粒、10wt.%~40wt.%的过渡金属氧化物,以及镍基合金;所述金刚石磨具的孔隙率为20%~50%。可选地,所述过渡金属氧化物选自vb族或vib族元素的氧化物中的至少一种。可选地,所述过渡金属氧化物包括氧化铌和氧化钼;所述氧化铌与所述氧化钼的质量比为(5~15):(5~25)。本发明中,复合涂层以过渡金属氧化物(典型地为氧化铌和氧化钼)在金刚石颗粒表面成膜并附着在金刚石表面,有利于降低高温下金刚石颗粒热损伤的同时,还能够提高液态镍基合金对金刚石颗粒的润湿性。加工过程中经碳还原过渡金属氧化物(氧化钼和氧化铌)产生的过渡金属(铌和钼)溶解在熔覆金属中,能够降低熔覆金属的线膨胀系数,使熔覆金属与金刚石颗粒的线膨胀系数更匹配,降低金刚石颗粒的焊接热应力,防止金刚石颗粒在焊接热应力作用下产生裂纹。本发明中,过渡金属氧化物(典型地为氧化铌和氧化钼)在镍基合金表面成膜,能够吸收激光熔覆过程中高功率密度激光束的热量分解,降低镍基合金粉末表面高蒸气压元素的烧损;氧化铌和氧化钼形成过程中,钼酸铵和草酸铌铵分解会产生氨气,降低氩气氛围的氧分压,提高激光熔覆过程中气氛保护效果,氨气泡的产生也会提高金刚石磨具的孔隙率。可选地,所述金刚石颗粒的粒度为20目~600目。可选地,所述金刚石颗粒的粒度为35目~500目。可选地,所述金刚石颗粒的粒度为60目~200目。可选地,所述镍基合金选自bni73crfesib(c)、bni74crfesib、bni82crsibfe、bni78crsibconb或bni66mnsicu中的至少一种。可选地,所述镍基合金为粒度42目~325目的球形或近球形。可选地,所述镍基合金的粒度为60目~270目。可选地,所述镍基合金的粒度为70目~150目。可选地,所述复合涂层的厚度为5mm~15mm。可选地,所述复合涂层的厚度为10mm。可选地,所述基材的材质选自低碳钢、中碳钢或合金钢。根据本发明的另一目的,提供了上述任一金刚石磨具的制备方法。所述方法包括:a1)采用激光熔覆将经过表面活化处理的镍基合金熔覆于基材表面,形成熔池,并将经过表面活化处理的金刚石颗粒送入所述熔池;b1)将经过表面活化处理的镍基合金送至位于所述熔池中的金刚石颗粒表面进行激光熔覆,并与金刚石颗粒发生冶金结合。可选地,重复步骤b1)若干次,获得所述金刚石磨具。可选地,所述金刚石颗粒的表面活化处理包括:a2)将金刚石颗粒原料置于80℃~90℃的碱液中超声处理,洗涤后干燥,然后置于酸液中煮沸处理,洗涤后再次干燥;b2)将经过步骤a2)处理的所述金刚石颗粒置于60℃~70℃的含有过渡金属离子的溶液中浸泡处理后,干燥。可选地,步骤a2)中,所述碱液选用浓度为5gl~10g/l的氢氧化钠溶液,所述酸液选用10wt.%~30wt.%的硝酸溶液;所述干燥的温度为60℃~80℃。可选地,步骤a2)中,所述超声处理的频率为20khz~40khz,时间为20min~30min;所述煮沸处理的时间为10min~30min。可选地,步骤a2)中,所述洗涤为洗涤至ph=7。可选地,步骤b2)中,所述含有过渡金属离子的溶液包括钼酸铵溶液和草酸铌铵溶液。可选地,所述钼酸铵溶液的浓度为25g/l~80g/l,所述草酸铌铵溶液的浓度为35g/l~60g/l;所述浸泡的时间为30min~40min;所述干燥的温度为60℃~80℃。可选地,所述镍基合金的表面活化处理包括:将镍基合金原料置于50℃~60℃的含有过渡金属离子的溶液中浸泡20min~30min后,干燥。可选地,所述含有过渡金属离子的溶液包括钼酸铵溶液和草酸铌铵溶液;所述钼酸铵溶液的浓度为25g/l~80g/l,所述草酸铌铵溶液的浓度为35g/l~60g/l。可选地,所述干燥采用回转真空干燥机进行,回转速度为4r/min~6r/min,真空度为103pa~104pa,干燥温度为40℃~60℃。可选地,所述激光熔覆的激光器功率为1kw~10kw,扫描速度为10mm/s~150mm/s。可选地,所述激光熔覆在惰性气氛下进行。可选地,所述激光熔覆采用保护气为氩气,露点低于-54℃。作为本发明一种实施方式,所述金刚石磨具的制备方法包括:(1)对金刚石进行表面活化处理;(2)将镍基合金粉末放入钼酸铵和草酸铌铵溶液,使镍基合金粉末表面附着一层盐膜;(3)将步骤(1)中附着盐膜的金刚石颗粒置于送料器料斗中,将步骤(2)中经过处理的镍基合金粉末置于送粉器粉斗中;(4)启动激光熔覆系统,氩气将工件周围完全笼罩,步骤(3)中的送粉器将镍基合金粉末经同轴喷嘴送至工件表面,激光器产生的同轴聚焦激光束辐照工件表面的镍基合金粉末,形成熔池,开启步骤(3)中的金刚石颗粒送料器,金刚石颗粒落入熔池,激光束、送粉器、送料器同步移动,完成第一层金刚石磨粒熔覆过程;(5)回程时,步骤(3)中的送粉器将镍基合金粉末经同轴喷嘴送至金刚石颗粒表面,激光器产生的同轴聚焦激光束辐照金刚石颗粒表面的镍基合金粉末,熔化镍基合金粉与金刚石颗粒发生冶金结合并在重力的作用下形成第一层金刚石网状激光熔覆层;(6)重复步骤(5),获得第n层激光熔覆金刚石磨粒层,制得具有n层金刚石磨粒的激光熔覆金刚石磨具。作为本发明一种实施方式,金刚石的表面活化处理方法包括:a)将金刚石颗粒放入5g/l~10g/l、80℃~90℃的氢氧化钠溶液中20khz~40khz超声波振动20min~30min,采用去离子水清洗至ph=7,60℃~80℃烘干;b)将烘干的金刚石颗粒放入质量分数为10%~30%的硝酸溶液中煮沸10min~30min,采用去离子水清洗至ph=7,60℃~80℃烘干;c)将烘干的金刚石颗粒放入钼酸铵和草酸铌铵的混合溶液中浸泡30min~40min,其中钼酸铵溶液浓度为25g/l~80g/l,草酸铌铵溶液浓度为35g/l~60g/l,混合溶液温度为60℃~70℃;d)将金刚石颗粒从上述混合溶液中捞出,60℃~80℃烘干,获得表面活化的金刚石颗粒。作为本发明一种实施方式,镍基合金的表面活化处理方法包括:a)将镍基合金粉末放入钼酸铵和草酸铌铵的混合溶液中浸泡20min~30min,其中钼酸铵溶液浓度为5g/l~20g/l,草酸铌铵溶液浓度为5g/l~25g/l,混合溶液温度为50℃~60℃;b)将镍基合金粉末从上述混合溶液中捞出,放入回转真空干燥机中烘干,即得表面附有钼酸铵和草酸铌铵盐膜的镍基合金粉末,其中回转速度为4r/min~6r/min,真空度为103pa~104pa,干燥温度为40℃~60℃。本发明中,孔隙率采用空隙所占体积与镍基合金、金刚石组成的复合涂层总体积的比率来评价,并通过排水法测定。与现有技术相比,本发明的有益效果为:(1)本发明提供的金刚石磨具,具有更高的孔隙率及磨削效率,在磨削应用时具有更高的生产效率。(2)本发明提供的金刚石磨具,其复合涂层以特定用量的过渡金属氧化物用作填充材料,有利于降低金刚石颗粒的热损伤,提高金刚石颗粒的钎焊活性,同时降低熔覆金属的线膨胀系数,使熔覆金属与金刚石颗粒的线膨胀系数更匹配,防止金刚石颗粒在焊接热应力作用下产生裂纹。(3)本发明提供的金刚石磨具的制备方法简单高效、连续性强,周期短,有利于大规模工业推广。附图说明为了更清楚地说明本发明具体实施方式或现有技术中的技术方案,下面将对具体实施方式或现有技术描述中所需要使用的附图作简单地介绍,显而易见地,下面描述中的附图是本发明的一些实施方式,对于本领域普通技术人员来讲,在不付出创造性劳动的前提下,还可以根据这些附图获得其他的附图。图1为本发明一种实施方式中,金刚石磨具的复合涂层的扫描电镜照片。具体实施方式下面将结合实施例对本发明的实施方案进行详细描述,但是本领域技术人员将会理解,下列实施例仅用于说明本发明,而不应视为限制本发明的范围。实施例中未注明具体条件者,按照常规条件或制造商建议的条件进行。所用试剂或仪器未注明生产厂商者,均为可以通过市购获得的常规产品。实施例1金刚石颗粒的活化处理选择50目的金刚石颗粒进行表面处理,具体步骤如下:a)将金刚石颗粒放入10g/l、80℃的氢氧化钠溶液中20khz超声波振动30min,采用去离子水清洗至ph=7,60℃烘干;b)将烘干的金刚石颗粒放入质量分数为20%的硝酸溶液中煮沸10min,采用去离子水清洗至ph=7,60℃烘干;c)将烘干的金刚石颗粒放入钼酸铵和草酸铌铵的混合溶液中浸泡30min,其中钼酸铵溶液浓度为40g/l,草酸铌铵溶液浓度为60g/l,混合溶液温度为60℃;d)将金刚石颗粒从上述混合溶液中捞出,60℃烘干,获得表面活化的金刚石颗粒。镍基合金的表面活化处理选择60目的bni74crfesib镍基合金球形粉末进行表面处理,具体步骤如下:a)将镍基合金粉末放入钼酸铵和草酸铌铵的混合溶液中浸泡30min,其中钼酸铵溶液浓度为20g/l,草酸铌铵溶液浓度为5g/l,混合溶液温度为50℃;b)将镍基合金粉末从上述混合溶液中捞出,放入回转真空干燥机中烘干,即得表面附有钼酸铵和草酸铌铵盐膜的镍基合金粉末,其中回转速度为5r/min,真空度为104pa,干燥温度为50℃。金刚石磨具的制备选择q235碳钢板作为基材制备金刚石磨具,具体方法如下:(1)将前述经过表面活化处理的金刚石颗粒置于送料器料斗中,将前述经过表面活化处理的镍基合金粉末置于送粉器粉斗中;(2)启动激光熔覆系统,激光器的功率为2.0kw,扫描速度为10mm/s;采用露点低于-54℃的氩气将10mm厚的q235碳钢板周围完全笼罩,以送粉器将镍基合金粉末经同轴喷嘴送至基材表面,激光器产生的同轴聚焦激光束辐照基材表面的镍基合金粉末,形成熔池;开启金刚石颗粒送料器,金刚石颗粒落入熔池,激光束、送粉器、送料器同步移动,完成第一层金刚石磨粒熔覆过程;(3)回程时,送粉器将镍基合金粉末经同轴喷嘴送至金刚石颗粒表面,激光器产生的同轴聚焦激光束辐照金刚石颗粒表面的镍基合金粉末,熔化镍基合金粉与金刚石颗粒发生冶金结合并在重力的作用下形成第一层金刚石网状激光熔覆层;(4)重复步骤(3),获得第n层激光熔覆金刚石磨粒层,制得具有n层金刚石磨粒的激光熔覆金刚石磨具;镍基合金与金刚石复合层厚度为10mm,其中金刚石颗粒质量占涂层总质量的1.2%。实施例2金刚石磨具的制备金刚石颗粒的活化处理选择60目的金刚石颗粒进行表面处理,具体步骤与实施例1中相同。镍基合金的表面活化处理选择60目的bni74crfesib镍基合金球形粉末进行表面处理,具体步骤与实施例1中相同。金刚石磨具的制备选择q235碳钢板作为基材制备金刚石磨具,具体方法如下:(1)将前述经过表面活化处理的金刚石颗粒置于送料器料斗中,将前述经过表面活化处理的镍基合金粉末置于送粉器粉斗中;(2)启动激光熔覆系统,激光器的功率为2.2kw,扫描速度为10mm/s;采用露点低于-54℃的氩气将10mm厚的q235碳钢板周围完全笼罩,以送粉器将镍基合金粉末经同轴喷嘴送至基材表面,激光器产生的同轴聚焦激光束辐照基材表面的镍基合金粉末,形成熔池;开启金刚石颗粒送料器,金刚石颗粒落入熔池,激光束、送粉器、送料器同步移动,完成第一层金刚石磨粒熔覆过程;(3)回程时,送粉器将镍基合金粉末经同轴喷嘴送至金刚石颗粒表面,激光器产生的同轴聚焦激光束辐照金刚石颗粒表面的镍基合金粉末,熔化镍基合金粉与金刚石颗粒发生冶金结合并在重力的作用下形成第一层金刚石网状激光熔覆层;(4)重复步骤(3),获得第n层激光熔覆金刚石磨粒层,制得具有n层金刚石磨粒的激光熔覆金刚石磨具;镍基合金与金刚石复合层厚度为10mm,其中金刚石颗粒质量占涂层总质量的1.5%。实施例3金刚石颗粒的活化处理选择70目的金刚石颗粒进行表面处理,具体步骤如下:a)将金刚石颗粒放入10g/l、80℃的氢氧化钠溶液中20khz超声波振动30min,采用去离子水清洗至ph=7,60℃烘干;b)将烘干的金刚石颗粒放入质量分数为20%的硝酸溶液中煮沸10min,采用去离子水清洗至ph=7,60℃烘干;c)将烘干的金刚石颗粒放入钼酸铵和草酸铌铵的混合溶液中浸泡30min,其中钼酸铵溶液浓度为50g/l,草酸铌铵溶液浓度为60g/l,混合溶液温度为60℃;d)将金刚石颗粒从上述混合溶液中捞出,60℃烘干,获得表面活化的金刚石颗粒。镍基合金的表面活化处理选择60目的bni74crfesib镍基合金粉末进行表面处理,具体步骤如下:a)将镍基合金粉末放入钼酸铵和草酸铌铵的混合溶液中浸泡30min,其中钼酸铵溶液浓度为20g/l,草酸铌铵溶液浓度为15g/l,混合溶液温度为50℃;b)将镍基合金粉末从上述混合溶液中捞出,放入回转真空干燥机中烘干,即得表面附有钼酸铵和草酸铌铵盐膜的镍基合金粉末,其中回转速度为5r/min,真空度为104pa,干燥温度为50℃。金刚石磨具的制备选择q235碳钢板作为基材制备金刚石磨具,具体方法如下:(1)将前述经过表面活化处理的金刚石颗粒置于送料器料斗中,将前述经过表面活化处理的镍基合金粉末置于送粉器粉斗中;(2)启动激光熔覆系统,激光器的功率为2.4kw,扫描速度为10mm/s;采用露点低于-54℃的氩气将10mm厚的q235碳钢板周围完全笼罩,以送粉器将镍基合金粉末经同轴喷嘴送至基材表面,激光器产生的同轴聚焦激光束辐照基材表面的镍基合金粉末,形成熔池;开启金刚石颗粒送料器,金刚石颗粒落入熔池,激光束、送粉器、送料器同步移动,完成第一层金刚石磨粒熔覆过程;(3)回程时,送粉器将镍基合金粉末经同轴喷嘴送至金刚石颗粒表面,激光器产生的同轴聚焦激光束辐照金刚石颗粒表面的镍基合金粉末,熔化镍基合金粉与金刚石颗粒发生冶金结合并在重力的作用下形成第一层金刚石网状激光熔覆层;(4)重复步骤(3),获得第n层激光熔覆金刚石磨粒层,制得具有n层金刚石磨粒的激光熔覆金刚石磨具;镍基合金与金刚石复合层厚度为10mm,其中金刚石颗粒质量占涂层总质量的1.8%。实施例4金刚石颗粒的活化处理选择80目的金刚石颗粒进行表面处理,具体步骤与实施例3中相同。镍基合金的表面活化处理选择60目的bni74crfesib镍基合金粉末进行表面处理,具体步骤与实施例3中相同。金刚石磨具的制备选择q235碳钢板作为基材制备金刚石磨具,具体方法如下:(1)将前述经过表面活化处理的金刚石颗粒置于送料器料斗中,将前述经过表面活化处理的镍基合金粉末置于送粉器粉斗中;(2)启动激光熔覆系统,激光器的功率为2.4kw,扫描速度为10mm/s;采用露点低于-54℃的氩气将10mm厚的q235碳钢板周围完全笼罩,以送粉器将镍基合金粉末经同轴喷嘴送至基材表面,激光器产生的同轴聚焦激光束辐照基材表面的镍基合金粉末,形成熔池;开启金刚石颗粒送料器,金刚石颗粒落入熔池,激光束、送粉器、送料器同步移动,完成第一层金刚石磨粒熔覆过程;(3)回程时,送粉器将镍基合金粉末经同轴喷嘴送至金刚石颗粒表面,激光器产生的同轴聚焦激光束辐照金刚石颗粒表面的镍基合金粉末,熔化镍基合金粉与金刚石颗粒发生冶金结合并在重力的作用下形成第一层金刚石网状激光熔覆层;(4)重复步骤(3),获得第n层激光熔覆金刚石磨粒层,制得具有n层金刚石磨粒的激光熔覆金刚石磨具;镍基合金与金刚石复合层厚度为10mm,其中金刚石颗粒质量占涂层总质量的2.0%。实施例5金刚石颗粒的活化处理选择70目的金刚石颗粒进行表面处理,具体步骤与实施例3中相同。镍基合金的表面活化处理选择60目的bni74crfesib镍基合金粉末进行表面处理,具体步骤与实施例3中相同。金刚石磨具的制备选择q235碳钢板作为基材制备金刚石磨具,具体方法如下:(1)将前述经过表面活化处理的金刚石颗粒置于送料器料斗中,将前述经过表面活化处理的镍基合金粉末置于送粉器粉斗中;(2)启动激光熔覆系统,激光器的功率为2.6kw,扫描速度为10mm/s;采用露点低于-54℃的氩气将10mm厚的q235碳钢板周围完全笼罩,以送粉器将镍基合金粉末经同轴喷嘴送至基材表面,激光器产生的同轴聚焦激光束辐照基材表面的镍基合金粉末,形成熔池;开启金刚石颗粒送料器,金刚石颗粒落入熔池,激光束、送粉器、送料器同步移动,完成第一层金刚石磨粒熔覆过程;(3)回程时,送粉器将镍基合金粉末经同轴喷嘴送至金刚石颗粒表面,激光器产生的同轴聚焦激光束辐照金刚石颗粒表面的镍基合金粉末,熔化镍基合金粉与金刚石颗粒发生冶金结合并在重力的作用下形成第一层金刚石网状激光熔覆层;(4)重复步骤(3),获得第n层激光熔覆金刚石磨粒层,制得具有n层金刚石磨粒的激光熔覆金刚石磨具;镍基合金与金刚石复合层厚度为10mm,其中金刚石颗粒质量占涂层总质量的2.4%。对比例1~5作为对比例1~5,将与实施例1~5中相同比例、相同粒度的金刚石粉末,相同成分、相同用量的镍基合金粉混合均匀,在相同露点的氩气保护热压烧结炉中烧结镍基合金与金刚石复合层,烧结温度为1050℃,烧结时间为25min,并使其附着在10mm厚q235钢板试样表面,涂层厚度为10mm。实验例1表面形貌的表征以phenomxl型扫描电子显微镜(sem)表征金刚石磨具的表面形貌,结果如图1所示。由图1可以发现,金刚石磨具表面的复合涂层无裂纹,金刚石颗粒埋入熔覆金属,熔覆金属对金刚石颗粒润湿性良好。实验例2孔隙率评价孔隙率指标采用空隙所占体积与镍基合金、金刚石组成的复合层总体积的比率,通过排水法测得孔隙率。每个实施例和对比例分别做5组试验,并分别取平均值和标准差,测定结果如表1所示。表1孔隙率评价结果实施例试样孔隙率(均值±标准差)对比例试样孔隙率(均值±标准差)实施例132.1±1.3对比例15.7±1.1实施例238.9±3.7对比例26.5±2.4实施例333.5±4.6对比例35.6±2.3实施例441.8±2.7对比例46.9±3.1实施例530.3±5.2对比例56.7±2.8从表1中孔隙率测定结果可以看出,采用本发明所提供的制备方法制备得到的金刚石磨具,其金刚石耐磨块的孔隙率显著高于对比例中采用传统钎涂方法制备的金刚石涂层试样,生产效率相比传统金刚石磨具制备方法大大提高。实验例3磨损指标评价磨损试验条件:试验载荷为20n,磨料为120号棕刚玉砂,橡胶轮转速为100r/min,进给速度为0.5mm/s,磨损时间为1min;橡胶轮的磨损采用失重量表示,每个实施例和对比例分别做5组试验,并分别取平均值和标准差,测试结果如表2所示。表2磨损指标评价从表2中磨损试验结果可以看出,采用本发明所提供的制备方法制备得到的金刚石磨具,其金刚石耐磨块的磨削效率显著高于对比例中采用传统钎涂方法制备的金刚石涂层试样,磨削性能优异。最后应说明的是:以上各实施例仅用以说明本发明的技术方案,而非对其限制;尽管参照前述各实施例对本发明进行了详细的说明,但本领域的普通技术人员应当理解:其依然可以对前述各实施例所记载的技术方案进行修改,或者对其中部分或者全部技术特征进行等同替换;而这些修改或者替换,并不使相应技术方案的本质脱离本发明各实施例技术方案的范围。当前第1页1 2 3