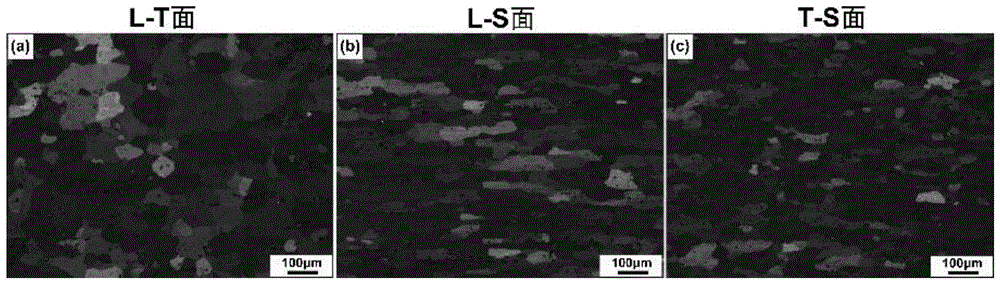
本发明属于铝合金制造
技术领域:
,涉及一种提高6061铝合金表面耐腐蚀性的轧制工艺,尤其涉及一种酸性环境下耐腐蚀性优良的6061-t651铝合金厚板的轧制工艺。
背景技术:
:铝合金具有密度小、比强度高、机械加工性和耐腐蚀性好等综合特性,被广泛应用于航空航天、船舶运输、零件制造等领域。其中,6xxx系铝合金在固溶热处理后强度较低,适用于加工对尺寸精度要求较高的零器件,并可以在后续处理后达到较高的强度和良好的耐腐蚀性能。传统半导体行业的机械零件多采用不锈钢制备,而轻量化、节能化的发展趋势下,采用铝合金(如6061等)替代不锈钢无疑是一种好的选择,可以大幅度减轻活动件的重量,减少工作过程中因其本身动作而消耗的能量,达到降低生产成本的目的。而现有传统工艺生产的普通6061合金经硬质氧化后的耐腐蚀性仍不够理想,达不到半导体零件应用的要求标准,无法替代不锈钢材料。技术实现要素:有鉴于此,本发明为了解决现有生产工艺制备的6061-t651合金厚板耐腐蚀性达不到半导体零件应用要求,无法替代不锈钢材料的问题,提供一种提高6061铝合金表面耐腐蚀性的轧制工艺,极大改善了6061-t651合金厚板在酸性环境下的耐腐蚀能力,提高了采用其加工成的零件的可靠程度和服役寿命,为铝合金在半导体零件制备领域替代不锈钢材料提供了有力支持。为达到上述目的,本发明提供一种提高6061铝合金表面耐腐蚀性的轧制工艺,包括以下步骤:a、配料:将制备铝合金中厚板的铝合金原料按照重量百分比进行配料,即:si:0.50~0.65%、fe≤0.2%、cu:0.25~0.35%、mn≤0.10%、mg:0.9~1.1%、cr:0.13~0.26%、ni≤0.05%、zn≤0.04%、ti≤0.15%、单个杂质≤0.05%,合计≤0.15%,余量为al;b、熔铸:将配制好的铝合金原料置于熔炼炉中熔炼为液态铝合金,经扒渣、过滤后将液态铝合金熔铸为铝合金铸锭;c、均匀化:将铝合金铸锭在加热炉中进行均匀化热处理,均匀化热处理的工艺为:铝合金铸锭升温至530~565℃,保温20~24h;d、锯切铣面:将均匀化热处理后的铝合金铸锭在冷却室冷却后切去头尾并铣去铝合金铸锭表面凝壳层;e、铸锭加热:将锯切铣面后的铝合金铸锭置于加热炉中加热,加热炉温度为480~530℃,保温时间为2~4h;f、热轧:将加热保温后的铝合金铸锭出炉热轧,轧制道次为15~25,轧制中后部有3~5道次的大变形量轧制,单道次变形量不低于50mm,之后转小变形量控温轧制,单道次变形量不高于15mm,根据轧制情况和板材温度反馈实时调节乳液喷淋模式,控制板材终轧温度200~230℃;g、固溶淬火:将热轧后的铝合金板材进行固溶处理,固溶温度为525~545℃,保温时间为15~40min,保温结束后淬火出炉;h、拉伸矫直:将固溶淬火后铝合金板材水冷至室温后进行拉伸矫直,拉伸率为1.5~2.5%;i、时效:将拉伸矫直后的铝合金板材进行时效处理,时效温度为160~180℃,保温时间为12~14h,时效后的板材经硬质阳极氧化得到成品6061-t651板材。进一步,步骤b将配置好的铝合金原料依次投入熔炼炉中进行熔炼,并使用熔剂进行精炼覆盖,投料后待炉内出现铝水时开始搅拌,搅拌均匀后熔炼为液态铝合金,熔炼温度730~750℃,将熔炼后的铝合金熔体倒入精炼炉精炼,精炼温度720~740℃,精炼时间为20min,精炼后的铝合金熔体在720±5℃静置20min,将精炼后的铝合金熔体通入高纯氩气并搅拌熔体,除去铝合金熔体中的杂质气体,然后将除气后的铝合金熔体通过孔径≥50ppi的泡沫陶瓷过滤板过滤,过滤温度为720±5℃。进一步,步骤c和步骤e中加热炉为推进式加热炉。进一步,步骤f在第10~12道次进行大变形量轧制,在第13道次之后转小变形量进行控温轧制。进一步,步骤g将冷轧后的铝合金板材置于辊底炉中进行固溶淬火处理。进一步,步骤g淬火方式为水冷,水冷淬火速度为10~40℃/s。本发明的有益效果在于:1、本发明所公开的提高6061铝合金表面耐腐蚀性的轧制工艺,在成分方面,主要通过控制较低的fe元素含量、适量的mg、si元素含量,以及部分cr元素添加。富fe相常析出于晶界位置会导致板材的耐腐蚀性降低,因此通过控制较低的fe元素添加,进一步控制成品板材中的附fe相数量,可有效改善合金耐腐蚀性。mg、si元素是6xxx系铝合金中的主合金元素,添加的量决定了成品板材的力学性能。添加cr元素有助于细化晶粒,改善合金的力学和耐腐蚀性能。组织方面控制晶粒组织细小且均匀,有助于控制合金在后续硬质氧化过程中生长出均匀致密的氧化层,提高合金的耐腐蚀性能。本专利主要通过控制热轧工艺过程来达到调控晶粒组织的目的,具体为热轧过程中采用大变形量轧制和小变形量控温轧制相结合工艺。其中大变形量轧制可促进附fe相的破碎,减少大尺寸附fe相的比例,有利于提高晶粒的均匀性,并对合金耐腐蚀性能提升有益;小变形量控温轧制可以控制轧制后的板材中保留有较大的畸变能,有利于促进后续的固溶过程中的晶粒再结晶,使得晶粒组织细小。2、本发明所公开的提高6061铝合金表面耐腐蚀性的轧制工艺,对传统6061合金的成分进行了优化,采用大变形量轧制和小变形量控温轧制相结合的热轧工艺,制备获得了一种耐腐蚀性优良的6061-t651合金厚板,板材晶粒组织细小、均匀,在不损失力学性能的情况下,极大改善了该种板材在酸性环境下的耐腐蚀能力,提高了采用其加工成的零件的服役寿命,为铝合金在半导体零件制备领域替代不锈钢材料提供了有力支持。本发明的其他优点、目标和特征在某种程度上将在随后的说明书中进行阐述,并且在某种程度上,基于对下文的考察研究对本领域技术人员而言将是显而易见的,或者可以从本发明的实践中得到教导。本发明的目标和其他优点可以通过下面的说明书来实现和获得。附图说明为了使本发明的目的、技术方案和优点更加清楚,下面将结合附图对本发明作优选的详细描述,其中:图1为本发明实施例1制备的铝合金板材沿各个截面的金相图;图2为本发明实施例2制备的铝合金板材沿各个截面的金相图;图3为本发明对比例制备的铝合金板材沿各个截面的金相图。具体实施方式以下通过特定的具体实例说明本发明的实施方式,本领域技术人员可由本说明书所揭露的内容轻易地了解本发明的其他优点与功效。本发明还可以通过另外不同的具体实施方式加以实施或应用,本说明书中的各项细节也可以基于不同观点与应用,在没有背离本发明的精神下进行各种修饰或改变。实施例1一种提高6061铝合金表面耐腐蚀性的轧制工艺,包括以下步骤:a、配料:计算各铝合金原料用量并按配比准备铝合金原料,6061铝合金原料各元素质量百分数配比如下:sifecumnmgcrniznti杂质al含量0.580.140.280.070.960.210.0030.0070.020.06余量b、熔铸:将配置好的铝合金原料依次投入熔炼炉中进行熔炼,并使用熔剂进行精炼覆盖,投料后待炉内出现铝水时开始搅拌,搅拌均匀后熔炼为液态铝合金,熔炼温度730℃,将熔炼后的铝合金熔体倒入精炼炉精炼,精炼温度720℃,精炼时间为20min,精炼后的铝合金熔体在720℃静置20min,将精炼后的铝合金熔体通入高纯氩气并搅拌熔体,除去铝合金熔体中的杂质气体,然后将除气后的铝合金熔体通过孔径≥50ppi的泡沫陶瓷过滤板过滤,过滤温度为720℃;c、均匀化:将铝合金铸锭在推进式加热炉中进行均匀化热处理,均匀化热处理的工艺为:铝合金铸锭升温至565℃,保温24h;d、锯切铣面:将均匀化热处理后的铝合金铸锭在冷却室冷却后切去头尾并铣去铝合金铸锭表面凝壳层;e、铸锭加热:将锯切铣面后的铝合金铸锭置于推进式加热炉中加热,加热炉温度为480℃,保温时间为2h;f、热轧:将加热保温后的铝合金铸锭出炉热轧,轧制道次为22,在第10~12道次进行大变形量道次轧制,单道次变形量不低于50mm。在第13道次开始转为小变形量道次轧制单道次变形量不高于15mm,根据轧制情况和板材温度反馈实时调节乳液喷淋模式,控制板材终轧温度202℃;其中铝合金铸锭热轧道次表1为:g、固溶淬火:将热轧后的铝合金板材置于辊底炉中进行固溶处理,固溶温度为530℃,保温时间为15min,保温结束后淬火出炉;h、拉伸矫直:将固溶淬火后铝合金板材水冷至室温后进行拉伸矫直,拉伸率为2.0%;i、时效:将拉伸矫直后的铝合金板材进行时效处理,时效温度为170℃,保温时间为12h,时效后的板材经硬质阳极氧化得到成品6061-t651板材。实施例1中6061-t651板材晶粒结构如图1所示。实施例2实施例2与实施例1的区别在于,步骤f轧制道次为19,在第10~12道次引入3个道次的大变形量道次轧制,保证单道次变形量不低于50mm。在第13道次开始前,对板材进行测温,其温度为472℃,暂停轧制,通过喷淋乳液使其降温至370℃。然后转成小变形量道次轧制,根据轧制情况和板材反馈温度实时乳液喷淋模式,控制板材温度,板材终轧温度205℃。其中铝合金铸锭热轧道次表2为:实施例2中6061-t651板材晶粒结构如图2所示。对比例对比例与实施例1的区别在于,步骤a中6061铝合金原料各元素质量百分数配比如下:sifecumnmgcrniznti杂质al含量0.620.340.270.080.970.100.0060.0020.020.06余量步骤f轧制道次为22,热轧过程采用常规产品轧制道次表,按道次顺序连续轧制,最大单道次变形量不高于25mm,属传统工艺生产,板材终轧温度358℃。其中铝合金铸锭热轧道次表3为:对比例中6061-t651板材晶粒结构如图3所示。对实施例1、2和对比例的板材晶粒结构进行比较可以发现:传统工艺(对比例)生产的6061-t651厚板晶粒形貌沿轧向拉长趋势明显,且l-t、l-s、t-s面晶粒尺寸差异明显,晶粒尺寸远大于200μm。本专利公布的工艺(实施例1、2)生产的6061-t651厚板晶粒基本消除了晶粒分布的方向性,三个面上的晶粒尺寸普遍较小且分布均匀,平均晶粒尺寸约为60μm。此种晶粒分布特性有助于控制合金在后续硬质氧化过程中生长出均匀致密的氧化层,提高合金的耐腐蚀性能。为测试板材在酸性环境下的耐腐蚀性能,采用的测试方法为:配置浓度为5%的盐酸溶液,用大试管装取,之后试管紧扣于样品表面,并用特殊手段密封防止泄露,对样品表面进行局部腐蚀,观察其表面是否有气泡出现,并记录出现气泡的时间,以产品表面保持不出现气泡时间的长短来测试板材在酸性环境下的耐腐蚀性。实施例1、2和对比例中6061-t651板材的耐盐酸腐蚀时间如表4所示,可以发现:本专利公布的工艺(实施例1、2)生产的6061-t651厚板l-t、l-s、t-s面的耐腐蚀时间均可达到220min以上,明显高于传统工艺(对比例)生产的6061-t651厚板的耐腐蚀时间。半导体领域机械零件的生产和使用环境经常为酸性氛围,因此铝合金产品应用于此领域的首要条件就是能在此种氛围下一定时间内保证不被腐蚀,本专利公布的工艺极大改善了6061-t651厚板在酸性条件下的耐腐蚀能力。表4为实施例1、2和对比例中6061-t651板材的耐盐酸腐蚀时间表4:耐腐蚀时间/min实施例1实施例2对比例l-t面235240100l-s面24023080t-s面24022090对实施例1、2和对比例的成品6061-t651厚板力学性能进行测试,测试标准为gb/t3880-2012,结果如表5所示,可以发现:传统工艺(对比例)和本专利公布的工艺(实施例1、2)生产的6061-t651厚板的力学性能均符合gb/t3880-2012的要求;本专利公布的工艺生产的6061-t651厚板的抗拉强度和屈服强队与传统工艺接近,延伸率要略优于传统工艺。说明本专利公布的工艺在提升产品耐腐蚀性的同时,不仅未损失产品力学性能,甚至略有提升,综合性能良好。表5为实施例1、2与对比例样品的力学性能表5最后说明的是,以上实施例仅用以说明本发明的技术方案而非限制,尽管参照较佳实施例对本发明进行了详细说明,本领域的普通技术人员应当理解,可以对本发明的技术方案进行修改或者等同替换,而不脱离本技术方案的宗旨和范围,其均应涵盖在本发明的权利要求范围当中。当前第1页12