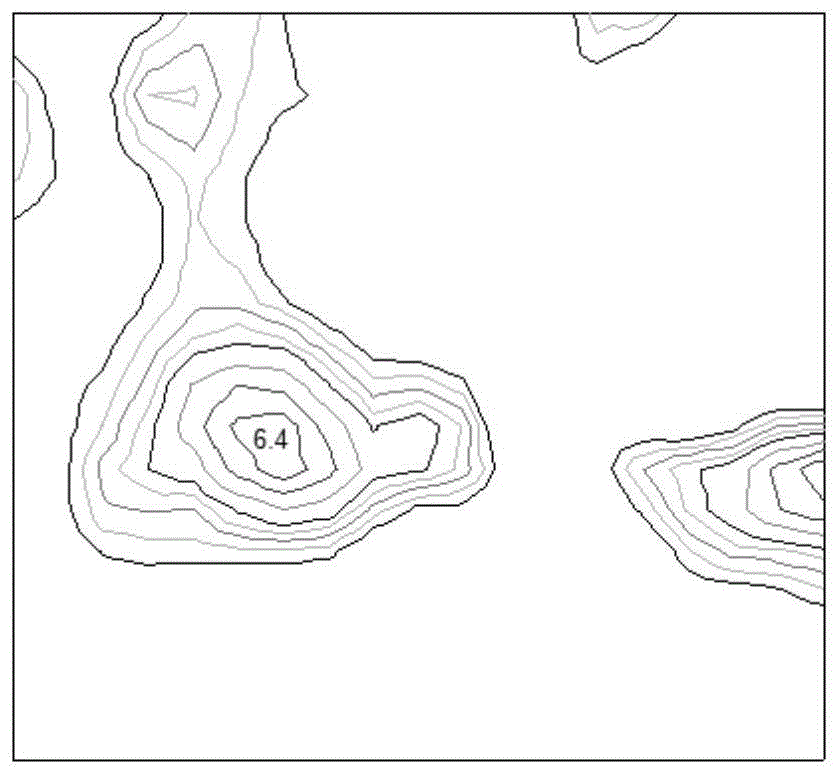
本发明属于合金冶炼领域,具体涉及一种电动汽车驱动电机用高磁感冷轧无取向硅钢薄带及制造方法。
背景技术:
:在市场和政策的双重推动下,新能源电动汽车成为汽车发展的重点,驱动电机作为电动汽车的动力核心,也成为影响电动汽车发展的关键因素之一。硅钢产品作为驱动电机核心,其性能的优劣直接决定着电机各方面性能。驱动电机特殊运行工况,要求硅钢材料具高速运转时实现高效率的高频低铁损、起步时提供高扭矩的高磁感及不同离心力下平稳运转的高强度等特点。目前,国内对电动汽车驱动电机用硅钢虽有研究,但尚未完全成熟,而日本jfe和新日铁、韩国浦项等国外企业在电动汽车驱动电机用硅钢领域研究较早,已形成高频低铁损、高磁感及高强度产品体系,在高端驱动电机领域占据主要份额。2014年3月26日公开的公开号为cn103667900a的专利公开了一种汽车电机用高磁感硅钢的制备方法,该方法采用添加sn、bi、ce、er等元素,并采用非常规热轧、二次冷轧法等方式获得高磁感硅钢产品,但该方法中的热轧及冷轧工序复杂,严重降低工业化生产效率,且sn、bi、ce、er等元素会明显增加产品的合金成本。2012年10月24日公开的公开号为cn102747291a的专利提供了一种高频低铁损磁性优良的无取向硅钢薄带及生产方法,该方法通过添加sn、cr、cu等元素,并采用高温热轧及二次冷轧法获得低铁损、高强度硅钢薄带,但对磁感的改善程度有限。另外,为降低硅钢板的铁损,添加si、als是有效的方法,高性能硅钢的si+als添加量达到3.5%以上,但si、als含量的增加,致使饱和磁化强度的降低,磁通密度变低。为此,在传统的si、als添加方法中,很难生产出磁通密度和铁损特性两者均优的材料。因此,如何通过调整si、al等合金添加量、优化生产工艺来获得磁通密度和铁损平衡,成为电动汽车驱动电机用硅钢开发必须攻克的难题。技术实现要素:本发明的目的在于提供一种电动汽车驱动电机用高磁感冷轧无取向硅钢薄带,需要添加sn、sb等微量元素来改善无取向硅钢织构组分,提高磁感,降低高频铁损,同时在有效提高材料强度。本发明另一目的在于提供一种电动汽车驱动电机用高磁感冷轧无取向硅钢薄带的制造方法,适用于常规热轧工艺,满足现行生产线的设备能力,采用多元素协同作用结合高温常化、热轧、带温冷轧及低张力快速升温连退等工艺生产铁损低、磁感高且各向异性优良的0.30mm厚度无取向硅钢薄带,其p1.0/400≤16.0wkg、磁感b5000≥1.67t,磁各向异性≤10%。本发明具体技术方案如下:一种电动汽车驱动电机用高磁感冷轧无取向硅钢薄带,包括以下质量百分比的元素:c:≤0.0025%,si:2.90~3.40%,mn:0.10~1.00%,p:≤0.010%,als:0.60~1.00%,s:≤0.0015%,n:≤0.0020%,ti:≤0.0025%,sn:0.06~0.14%或sb:0.04-0.12%,其余为fe及不可避免的杂质。本发明提供的一种电动汽车驱动电机用高磁感冷轧无取向硅钢薄带的制造方法,包括以下步骤:1)钢水转炉冶炼;2)rh炉精炼和合金化处理;3)连铸成板坯;4)加热炉加热,热轧、卷取;5)常化;6)酸洗;7)冷轧;8)退火;9)涂层涂覆;10)精整。进一步的,步骤3)中,连铸成厚度为230~250mm的板坯;步骤3)中连铸时进行电磁搅拌,搅拌电流≥300a,铸坯等轴晶率≥50%,降低热轧不利织构组分强度,提高磁感;步骤4)中,连铸完成后将板坯直接装入加热炉,加热温度控制在1050~1150℃;在加热炉中加热4h以上,板坯入炉温度不低于450℃。步骤4)中所述热轧包括粗轧和精轧。轧成2.0~2.2mm厚度的热轧板。步骤4)中热轧精轧前温度在920~1000℃,热轧的终轧温度在840~900℃,卷取温度在640~700℃;步骤5)中常化热处理温度为840~980℃,保温时间为3~5min。步骤7)中冷轧前板面温度控制在80~200℃,缓解因合金元素及常化温度偏高带来的脆性,在单机架可逆轧机上经5道次冷轧至0.30mm,总压下率85~86%,其中,第一道次压下率控制在30%以上;步骤8)退火在连续退火炉中进行,以≥35℃/s的加热速率加热至退火温度900~1020℃,保温3~7min;炉内单位张力控制在1~3mpa,炉内气氛为干气氛,h2体积占比控制在15%以上。本发明所生产制造的硅钢薄带成品的铁损p1.0/400≤16.0wkg、磁感b5000≥1.67t,磁各向异性≤10%。在本发明的成分设计中,主要元素的作用及要求如下:si、al是获得优良磁性能的关键性元素,提高si、al添加量,增加钢的电阻率以降低铁损,尤其是高频铁损,基于主要合金元素对电阻率和饱和磁感的影响,采取多元合金的优化设计,缓解电磁性能与可制造性的矛盾,降低轧钢的断带风险,因此,本发明中,控制si:2.90~3.40、als:0.60~1.00。sn的表面偏析可以通过降低表面能来促进{100}取向晶粒的生长,sn的晶界偏析可以提高晶界迁移率,抑制不利织构发展,从而提高磁性。sb和sn类似,冷轧后再结晶退火过程中,sb能防止晶界附近的再结晶形核和减少{111}晶粒的形成,通过增加有利的{100}和{110}织构组分和减少不利的{111}织构组分来提高磁感;因此,本发明中,控制sn:0.06~0.14%,sb:0.04-0.12%。sn、sb作为偏聚元素,在本发明的工艺条件下,易在晶界析出,降低γ不利织构强度,提高磁感。c、s、n、ti为杂质元素,通过降低其含量,可对夹杂物尺寸和类型进行有效的控制,降低最终退火时晶粒尺寸长大的阻力。极低的c、s、n和ti可以提高钢液的纯净度可有效改善无取向硅钢的磁性。c含量较低时,有利于避免磁时效现象。s、ti、n的有效控制可以极大地减少夹杂物的数量,提高无取向硅钢的磁性能。当热轧加热温度提高到1150℃时,小于100nm的析出物数量有所增加,这是由于铸坯在加热过程中,mn、s、al、n等第二相粒子形成元素在高温下固溶与铁素体集体中,并在随后的热轧降温过程中弥散析出,细小析出物对晶界具有较强的钉扎作用,阻碍晶粒长大,因此,要求热轧温度在满足热轧稳定性的同时尽可能低,本发明中,要求热轧温度为1050~1150℃。提高热轧精轧前温度、终轧温度以及卷取温度,有利于细小析出相在热轧过程中得以长大,降低其对晶界的钉扎作用,优化成品磁性能,因此,本发明中,要求热轧精轧前温度为920~1000℃、终轧温度为840~900℃、卷取温度为640~700℃。生产过程中,在连退时采用快速加热,有利于使冷轧过程产生的晶粒畸变储能保留至再结晶过程中释放用于晶粒形核,增强{110}有利织构组分,提高产品磁感。本发明通过添加sn、sb等微量元素,配合其它元素合理的控制,同时采用合适的热轧、常化、冷轧及连续退火工艺与之配合,获得一种0.30mm厚度薄规格冷轧无取向硅钢,其磁性能优异,成品高频铁损p1.0/400≤16.0wkg、磁感b50≥1.67t、磁各向异性≤10%,以满足驱动电机用冷轧无取向硅钢薄规格、低铁损、高磁感及优良的各向异性要求,使驱动电机性能得到有效提升,适应其复杂的运行工况。附图说明图1为对比例1样品1/2厚度处的织构odf图;图2为本发明实施例1样品1/2厚度处的织构odf图;图3为本发明实施例1热轧状态的显微组织图。具体实施方式实施例1-实施例4一种电动汽车驱动电机用高磁感冷轧无取向硅钢薄带,包括以下质量百分比的元素:如下表1所示。表1没有列出的余量为fe和不可避免的杂质。实施例1-实施例4电动汽车驱动电机用高磁感冷轧无取向硅钢薄带的制造方法,包括以下步骤:1)钢水转炉冶炼;2)rh炉精炼和合金化处理;3)连铸成板坯:连铸时进行电磁搅拌,控制搅拌电流≥300a,铸坯等轴晶率≥50%,连铸成厚度为230~250mm的板坯;4)板坯采用热装装炉,板坯入炉温度不低于450℃;加热温度控制在1050~1150℃;在加热炉中加热4h以上。经过粗轧、精轧;热轧精轧前温度在920~1000℃,热轧的终轧温度在840~900℃,轧成2.0~2.2mm厚度的热轧板;卷取温度在640~700℃;5)常化:常化热处理温度为840~980℃,保温时间为3~5min。6)酸洗;7)冷轧:控制板温在80~200℃时进行冷轧,单机架可逆轧机上经5道次冷轧至0.30mm,总压下率85~86%,其中,第一道次压下率控制在30%以上;8)退火:在连续退火炉中进行,退火时以不低于35℃/s的加热速率加热至920~1020℃并保温3~7min,炉内单位张力控制在1~3mpa,炉内气氛为干气氛,h2体积占比控制在15%以上。9)涂层涂覆;10)精整。实施例1-实施例4电动汽车驱动电机用高磁感冷轧无取向硅钢薄带的制造方法过程中工艺参数如表2,表2中没有列出的按照常规现有技术进行。对比例1-对比例2一种冷轧无取向硅钢薄带,包括以下质量百分比的元素:如下表1所示。表1没有列出的余量为fe和不可避免的杂质。对比例1-对比例2的冷轧无取向硅钢薄带生产方法与本发明实施例的制造方法相同,不同之处在于表2中列出的参数。表1本发明各实施例及对比例的化学成分(wt.%)实施例csimnpalssntisnsb对比例10.00252.810.550.0141.050.00080.00140.0026//对比例20.00213.150.200.0100.870.00120.00120.0030//实施例10.00202.950.300.0090.760.00110.00130.00210.11/实施例20.00183.080.460.0070.680.00090.00110.00190.09/实施例30.00212.910.480.0090.940.00100.00120.0023/0.06实施例40.00173.320.150.0100.610.00070.00100.0020/0.10注:表1没有列出的余量为fe和不可避免的杂质。表2本发明各实施例及对比例的主要工艺参数图1为对比例1样品1/2厚度处的织构odf图;图2为本发明实施例1样品1/2厚度处的织构odf图。图3为本发明实施例1热轧状态的显微组织图。本发明各实施例及对比例生产的0.30mm厚度薄规格冷轧无取向硅钢磁性能如下表3所示。表3本发明各实施例及对比例磁性能检验结果本发明产品高频铁损p1.0/400≤16.0wkg、磁感b50≥1.67t、磁各向异性≤10%,以满足驱动电机用冷轧无取向硅钢薄规格、低铁损、高磁感及优良的各向异性要求,使驱动电机性能得到有效提升,适应其复杂的运行工况。当前第1页12