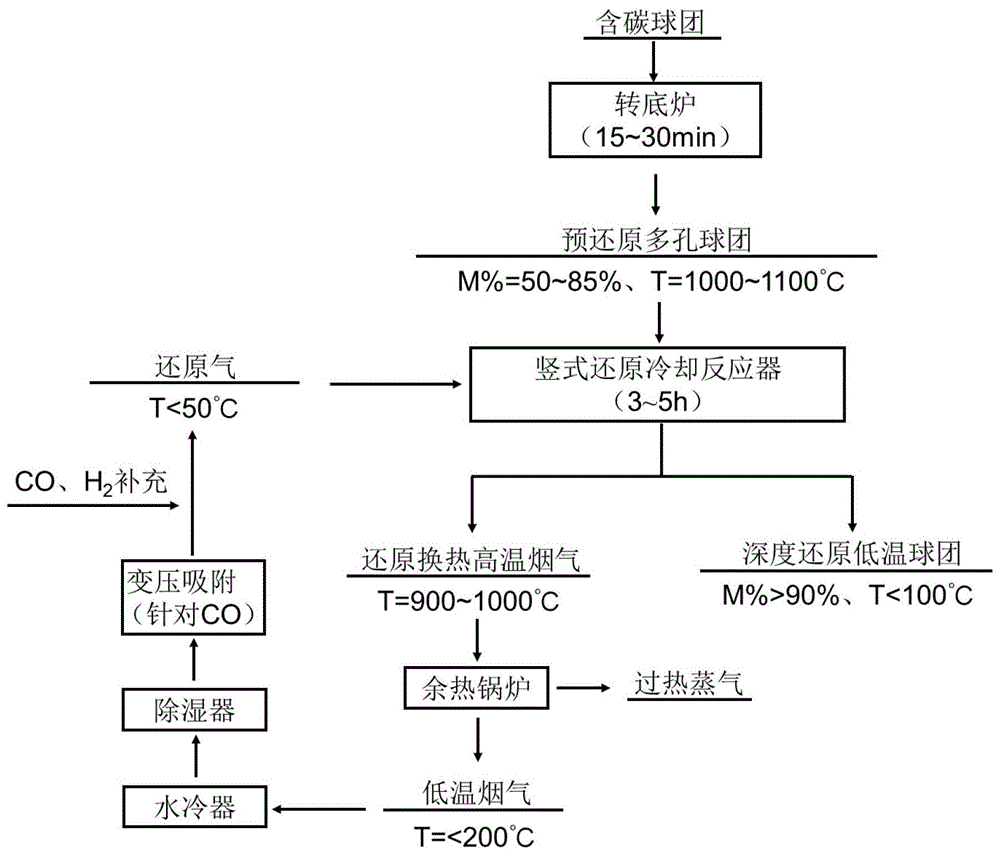
本发明涉及非高炉炼铁方法领域,尤其涉及一种碳热预还原与气基深度还原及同步冷却的炼铁方法。
背景技术:
:高炉炼铁是我国炼铁的主要方法,占据我国铁产量的绝对份额,但高炉冶炼存在两个特征,一是为保证高炉的透气性,必须存在焦炭层,焦炭价格高、炼焦过程环境污染严重;二是对原料的强度要求高,主要采取熟料入炉,包括烧结矿或氧化球团,提高冶炼成本的同时产生大量尾气,加大了治理成本。非高炉炼铁不以烧结矿或氧化球团为原料,降低了原料处理成本,同时避免了焦炭的利用,可以大幅缩短炼铁工艺流程、减少环境污染工序、降低生产成本。直接还原是非高炉炼铁的一个范畴,包括碳热直接还原和气基直接还原,目前的碳热直接还原方法已实现工业化并受到广泛应有,主要包括转底炉、回转窑和隧道窑等工艺。隧道窑为间接加热,加热效率较低,还原球团采取自然通风冷却,还原和冷却耗时较长,生产效率低下,该工艺目前已淘汰。转底炉和回转窑为直接加热,加热效率高,但还原球团的金属化率较低,一般低于70%,且还原球团主要采取水淬冷却或圆筒喷淋冷却,还原球的物理显热无法得到有效利用,且消耗大量的水资源。热态还原产品的物理显热无法得到利用,是造成直接还原炼铁热效率低的主要原因,同时,直接加热条件下难以保证高温气氛的还原性,造成还原度偏低。气基直接还原包括竖炉还原和流化床还原,由于气基还原均设有冷却段,故产品的物理热可以有效回收,对比碳热直接还原具有优势。流化床对原料、设备以及操作要求均较高,粘结失流问题难以控制,目前应用不多,气基还原设备以竖炉为主。竖炉采用氧化球团或生球作为原料,为避免球团之间发生粘结,还原温度一般控制在900℃以下,还原速率较慢、还原周期长,一般为6~8h,冷却阶段为4h,整个还原和冷却过程总共耗时约为10~12h,造成生产效率低下,另外,还原和冷却阶段气源不同,控制难度较大。技术实现要素:鉴于上述的分析,本发明实施例旨在提供一种碳热预还原与气基深度还原及同步冷却的炼铁方法,用以解决现有球团碳热还原度低、气基还原速率慢、冷却时间长以及气基还原时还原段和冷却阶段气源不同导致的气源隔离控制系统复杂的问题。本发明的目的主要是通过以下技术方案实现的:本发明公开了一种碳热预还原与气基深度还原及同步冷却的炼铁方法,包括以下步骤:步骤1、利用转底炉对含碳球团进行预还原,获取多孔预还原金属化球团,预还原温度为1100~1300℃,排料温度为1000~1100℃;步骤2、将多孔预还原金属化球团热态排入竖式还原冷却反应器中,与冷态还原气逆流还原及换热,还原冷却总时长为3~5h,球团金属化率大于90%;步骤3、还原换热后的高温气体经余热锅炉换热后,用于制备过饱和蒸汽用于发电,经余热锅炉换热后的气体温度为<200℃,再经水冷器冷却至50℃以下,冷却后的气体经除湿、除杂后,将未反应的还原气返回竖式还原冷却反应器循环利用。进一步地,在步骤2中,冷态还原气的气体体积多孔预还原金属化球团的质量之比为0.9~1.5nm3/kg。进一步地,在步骤2中,冷态还原气为co,在步骤3中,冷却后的co经除湿后进行变压吸附,剩余的co作为未反应的还原气返回竖式还原冷却反应器中循环利用。进一步地,在步骤3中,向竖式还原冷却反应器中补充冷态还原气co。进一步地,步骤2中的冷态还原气为h2。进一步地,在步骤3中,向竖式还原冷却反应器中补充冷态还原气h2。进一步地,在步骤2中,含碳球团竖式还原冷却反应器内的温度自上而下逐渐降低,球团在竖式还原冷却反应器底部的出口温度<80℃。进一步地,在步骤2中,冷态还原气在竖式还原冷却反应器内自下而上温度逐渐升高,竖式还原冷却反应器顶部的冷态还原气的出口温度为900~1000℃。进一步地,在步骤1中,多孔预还原金属化球团的金属化率为50~85%。进一步地,在步骤1中,利用转底炉对含碳球团进行预还原的时间为15~30min。与现有技术相比,本发明至少可实现如下有益效果之一:(1)本发明提供的碳热预还原与气基深度还原及同步冷却的炼铁方法,将碳热直接还原与气基深度还原联合起来形成一个新的完整工艺,在实现还原含碳球团余热利用的同时,将含碳球团的金属化率提高至大于90%。碳热直接还原速率远高于气基还原速率,以碳热直接还原作为预还原过程,在较短的时间内获取一定的金属化率,再以气基还原作为深度还原手段,在获取相同的还原度下,相对于单独的气基还原过程,碳热预还原与气基还原相结合可以大幅缩短还原时间。(2)现有的竖式冷却器以n2作为冷却介质,是一个纯换热过程,并不涉及还原过程,本申请以h2或co气体取代n2,在对热球团进行冷却的同时,还可以与热球团反应大幅提高还原球团的金属化率(将含碳球团的金属化率由50~85%提高至90%以上),此时竖式冷却器转变为竖式还原冷却反应器,当碳热预还原球团金属化率控制在50%以上时,以h2或co进行同步还原冷却,可达到与n2冷却相同的效果,同时球团的金属化率可提高至90%以上,达到气基竖炉的还原效果。碳热预还原与还原冷却相结合可发展成为新一代直接还原炼铁方法。(3)现有技术中大多采用单独的碳热直接还原或气基还原技术,本发明相对于单独的碳热直接还原,气基深度还原可以大幅提高球团的金属化率到90%以上,同时,气基还原还能促进铁颗粒的长大,改善还原球团中金属铁的磁选效果。(4)本发明相对于单独的气基还原,碳热预还原速率快(15~30min),并且可以创造良好的内部孔隙率,促进后续的气基还原速率,且以热球/冷气还原代替冷球/热气还原,球团的还原与冷却过程同步进行,缩短了处理时间(竖式还原冷却反应器的还原冷却时间为3~5h)。本发明中,上述各技术方案之间还可以相互组合,以实现更多的优选组合方案。本发明的其他特征和优点将在随后的说明书中阐述,并且,部分优点可从说明书中变得显而易见,或者通过实施本发明而了解。本发明的目的和其他优点可通过说明书实施例以及附图中所特别指出的内容中来实现和获得。附图说明附图仅用于示出具体实施例的目的,而并不认为是对本发明的限制,在整个附图中,相同的参考符号表示相同的部件。图1为基于碳热预还原的气基深度还原与同步冷却工艺流程图;图2为本发明提供的还原冷却器示意图;图3为对照例1中传统还原竖炉示意图;图4为对照例2中传统转底炉碳热还原过程示意图。具体实施方式下面结合附图来具体描述本发明的优选实施例,其中,附图构成本申请一部分,并与本发明的实施例一起用于阐释本发明的原理,并非用于限定本发明的范围。本发明提供了一种碳热预还原与气基深度还原及同步冷却的炼铁方法,如图1所示,包括以下步骤:步骤1、含碳球团通过转底炉还原,获取多孔预还原金属化球团,为气基还原创造温度条件并能促进气基还原过程,预还原球团的金属化率控制在50~85%,还原温度控制在1100~1300℃,排料温度控制在1000~1100℃;fexoy+yc=xfe+yco(1)含碳球团在转底炉内经历预还原,其有益效果体现在:首先,碳质还原剂与铁氧化物还原产生co气体,还原球团内部产生均匀分布的孔洞,有利于后续的气基还原过程;其次,预还原过程中球团被加热,为后续热球/冷气之间的气基还原过程奠定基础,避免了传统气基还原过程的还原气加热过程;再次,现有的冷球/热气竖炉还原过程中,球团在还原过程中被热还原气加热逐渐升温,还原结束后必须在冷却段以冷氮气冷却降温后排出;而本发明中球团为热态,还原气为冷态,球团在还原过程中被冷还原气降温同步冷却,无需单独设立冷却段,特别是以h2作为还原气时,h2的直接还原反应是吸热反应,大幅缩短了处理时间,约为传统竖炉处理时间的1/5~1/3;最后,球团在预还原阶段的金属化率达到50%以上,能显著提高球团的粘结温度,传统的气基还原最高温度控制在850~900℃,本发明中预还原球团排料温度控制在1000~1100℃,大幅提高了气基还原速率。步骤2、如图2所示,将步骤1制备得到的多孔预还原金属化球团热态排入竖式还原冷却反应器中,与冷态还原气逆流还原及换热,还原冷却总时长为3~5h,冷态还原气的气体体积与多孔预还原金属化球团的质量之比为0.9~1.5nm3/kg,保证较好的还原和冷却效果,球团金属化率大于90%;球团自上而下温度逐渐降低,球团在下部的出口温度<80℃,避免球团排出后在空气中氧化,冷态还原气在竖式还原冷却反应器内的温度自下而上逐渐升高,竖式还原冷却反应器上部的冷态还原气的出口温度控制在900~1000℃,保证气体较高的还原效率;fexoy+yh2=xfe+yh2o(2)fexoy+yco=xfe+yco2(3)步骤3、还原换热后的高温气体经余热锅炉换热制备过饱和蒸汽用于发电,经余热锅炉换热后的气体温度为<200℃,再经水冷器冷却至50℃以下,冷却后的气体经过除湿器除湿后返回竖式还原冷却器循环利用,不足部分补充纯净的co或者h2进行球团深度还原。需要说明的是,当冷态还原气体为co气体时,co气体除湿后需要进行变压吸附,变压吸附后的纯co返回竖式还原冷却反应器中。本发明的含碳球团在转底炉内经历碳热直接还原,获取多孔预还原金属化球团;炽热的多孔金属化球团经排料装置进入竖式还原冷却反应器,经h2或co气体深度还原换热冷却后从反应器底部排出,还原换热的气体从反应器上部排出,经换热器冷却、脱湿、除杂后返回竖式还原冷却器循环利用。现有技术中大多采用单独的碳热直接还原或气基还原技术,本发明采用两者相结合的方式带来的有益效果包括:对比单独的碳热直接还原,气基深度还原可以大幅提高球团的金属化率到90%以上,同时,气基还原还能促进铁颗粒的长大,改善还原球团中金属铁的磁选效果;对比单独的气基还原,碳热直接还原速率快,并且可以创造良好的内部孔隙率,促进后续的气基还原速率,且以热球/冷气还原代替冷球/热气还原,球团的还原与冷却过程同步进行,缩短了处理时间。实施例1国海砂钒钛磁铁矿,tfe含量为56%,化学成分如表1所示,矿粉粒径小于80目。表1海砂钒钛磁铁矿的化学成分(%)tfefeofe2o3tio2v2o5sio2caomgoal2o3knacl5621.855610.670.764.290.723.184.12<0.1<0.1<0.05将钒钛磁铁矿、粘结剂混合均匀后,通过对辊压球机制备含碳球团。将10kg的球团放置在竖式还原炉中加热,以h2为还原气体,在900℃还原4~10h,还原结束后通入n2冷却至4h。还原后的球团破碎、研磨制备粉末试样,并通过化学滴定分析确定试样的金属化率。h2和n2流量均为50l/min,h2和n2的气体体积与球团质量比分别为1.2~3nm3/kg、1.2nm3/kg。实验结果表明,球团还原时间分别为4h、6h、8h、10h时,试样的金属化率分别为47%、74%、82%、89%。可以看出,钒钛磁铁矿的还原性较差,金属化率达到80%以上时还原时间必须控制在8h以上,在考察的时间范围内,无法通过气基还原获得金属化率大于90%的还原球团。实施例2选用与上述相同的钒钛磁铁矿原料。将钒钛磁铁矿、粘结剂、煤粉混合均匀后,通过对辊压球机制备含碳球团,球团c/o=1.2。煤粉化学成分如表2所示。表2还原用无烟煤粉化学组成,%组成(%)固定碳挥发份灰分s水分无烟煤74.535.1617.860.442.45将10kg的含碳球团放置在电加热小型转底炉内加热,在1250℃还原15~30min,模拟含碳球团的碳热还原过程。还原后的球团破碎、研磨制备粉末试样,并通过化学滴定分析确定试样的金属化率。实验结果表明,球团还原时间分别为15min、20min、25min、30min时,试样的金属化率分别为58%、72%、79%、83%。可以看出,由于还原温度较高,钒钛磁铁矿的还原速率大大提高,还原时间超过20min时金属化率达到80%以上,表明碳热直接还原的还原效率远高于气基还原。实施例3本实施例采用实施例1制备的含碳球探进行预还原与深度还原和同步冷却。将10kg的含碳球团放置在小型转底炉内加热,在1250℃预还原15min、20min,还原结束后停止加热,还原结束后通过排料器将热的金属化球团排入竖式还原冷却器,通入h2还原冷却4h,h2流量为50l/min,h2的气体体积与球团的质量比为1.2nm3/kg。还原换热后的高温气体经余热锅炉换热制备过饱和蒸汽用于发电,经余热锅炉换热后的气体温度为200℃,再经水冷器冷却至50℃以下,冷却后的气体经过除湿器除湿后返回竖式还原冷却器循环利用,不足部分补充纯净的h2进行球团深度还原。预还原后的金属化球团以及最终还原冷却后的球团分别破碎、研磨制备粉末试样,并通过化学滴定分析确定试样的金属化率。实验结果表明,球团预还原时间分别为15min、20min时,预还原球团的金属化率分别为58%、72%,预还原球团经气基深度还原及同步冷却后的球团的金属化率分别为92%、94%。实施例4本实施例采用实施例1制备的含碳球探进行预还原与深度还原和同步冷却。将10kg的含碳球团放置在电加热小型转底炉内加热,在1250℃还原30min,还原结束后通过排料器将热的金属化球团排入竖式还原冷却器,通入h2还原冷却3~5h,h2流量为50l/min,h2的气体体积与球团的质量比为0.9~1.5nm3/kg。还原换热后的高温气体经余热锅炉换热制备过饱和蒸汽用于发电,经余热锅炉换热后的气体温度为200℃,再经水冷器冷却至50℃以下,冷却后的气体经过除湿器除湿后返回竖式还原冷却器循环利用,不足部分补充纯净的h2进行球团深度还原。预还原后的金属化球团以及最终还原冷却后的球团分别破碎、研磨制备粉末试样,并通过化学滴定分析确定试样的金属化率。实验结果表明,预还原球团的金属化率为83%,预还原球团的还原冷却时间分别为3h、5h时,试样的金属化率分别为96%、98%,表明预还原球团的金属化率越高,还原冷却对金属化率的影响越小。实施例5本实施例采用实施例1制备的含碳球探进行预还原与深度还原和同步冷却。将10kg的含碳球团放置在电加热小型转底炉内加热,在1250℃预还原20min,还原结束后通过排料器将热的金属化球团排入竖式还原冷却器,通入h2还原冷却3~5h,h2流量为50l/min,h2的气体体积与球团的质量比为0.9~1.5nm3/kg。还原换热后的高温气体经余热锅炉换热制备过饱和蒸汽用于发电,经余热锅炉换热后的气体温度为200℃,再经水冷器冷却至50℃以下,冷却后的气体经过除湿器除湿后返回竖式还原冷却器循环利用,不足部分补充纯净的h2进行球团深度还原。预还原后的金属化球团以及最终还原冷却后的球团分别破碎、研磨制备粉末试样,并通过化学滴定分析确定试样的金属化率。实验结果表明,预还原球团的金属化率为72%,h2还原冷却时间为3h、5h时,气基深度还原及同步冷却后的球团的金属化率为92%、96%。实施例6本实施例采用实施例1制备的含碳球探进行预还原与深度还原和同步冷却。将10kg的含碳球团放置在电加热小型转底炉内加热,在1150℃预还原15~30min,还原结束后通过排料器将热的金属化球团排入竖式还原冷却器,通入co还原冷却4h,co流量为50l/min,co的气体体积与球团的质量比为1.2nm3/kg。还原换热后的高温气体经余热锅炉换热制备过饱和蒸汽用于发电,经余热锅炉换热后的气体温度为200℃,再经水冷器冷却至50℃以下,冷却后的气体经过除湿器除湿后返回竖式还原冷却器循环利用,不足部分补充纯净的co进行球团深度还原。预还原后的金属化球团以及最终还原冷却后的球团分别破碎、研磨制备粉末试样,并通过化学滴定分析确定试样的金属化率。实验结果表明,预还原时间为15min、30min时,预还原球团的金属化率分别为58%、83%,气基深度还原及同步冷却后的球团的金属化率为90%、95%。可以看出,以co或h2代替n2作为冷却气时,球团的金属化率有了显著的提高,特别是碳热直接还原的金属化率较低时更明显。将碳热直接还原与co或h2冷却还原结合起来既可以缩短还原时间,又可以提高球团物理热的利用率,可以发展成为一种全新的直接还原炼铁方式。现有技术中大多采用单独的碳热直接还原或气基还原技术,本发明采用两者相结合的方式带来的有益效果包括:对比单独的碳热直接还原,气基深度还原可以大幅提高球团的金属化率到90%以上,同时,气基还原还能促进铁颗粒的长大,改善还原球团中金属铁的磁选效果;对比单独的气基还原,碳热直接还原速率快,并且可以创造良好的内部孔隙率,促进后续的气基还原速率,且以热球/冷气还原代替冷球/热气还原,球团的还原与冷却过程同步进行,缩短了处理时间。对照例1本对照例提供了一种利用传统气基还原方法制备金属化球团的过程,如图3所示,具体包括以下步骤:步骤1、还原气加热;以co或h2作为还原气,还原气需要加热至900~950℃,从竖炉还原段下部通入,自下向上流动,温度逐渐降低;步骤2、冷球团从竖炉还原段顶部加入,自上向下运动,在运动过程中球团温度逐渐升高,并被还原气还原6~8h;步骤3、还原气从竖炉顶部排出,球团到达还原段底部时还原结束,球团温度达到850℃以上,经排料器排料进入竖炉冷却段上部;步骤4、热球团在冷却段自上而下运动,经历约4h冷却至小于80℃排出。与本发明提供的一种碳热预还原与气基深度还原及同步冷却的炼铁方法相比,对照例1提供的利用传统气基还原方法制备金属化球团的过程存在以下缺陷:首先,整个制备过程耗时长,需要10~12h;其次,还原气需要加热,加热设备复杂,危险性高,对加热设备要求高;再次,还原气与冷却气成分不同,需要隔离排放,隔离设备操作要求高。与现有技术相比,本发明提供的碳热预还原与气基深度还原及同步冷却的炼铁方法具有以下优势:首先,球团经预还原后,具有较高的温度,还原气不需要加热,避免了加热设施;其次,本发明以还原气进行的还原的同时并冷却(现有竖炉采用氮气冷却),无需设置冷却段布气设施以及还原段与冷却段之间的隔离装置,不仅减小了竖炉高度,而且整个过程只有3~5h,对比传统竖炉工艺节约了处理时间;再次,本发明只有一种还原气体(co或h2),不需要隔离气体,简化了设备。对照例2本对照例提供了一种利用传统转底炉碳热还原过程,如图4所示,具体包括以下步骤:步骤1、球团在转底炉内还原30min,通过排料器排出,进入竖式冷却器;步骤2、热球团在竖式冷却器内以氮气为介质冷却4h,温度降低至低于80℃排出。与本发明相比,上述工艺中金属球团在冷却过程中不进行还原,只是单纯的冷却,球团只在转底炉内还原,金属化率仅为50~85%,不仅球团金属化率低,而且得到的铁晶粒小,磁选效果不好,需要进行熔分处理。本发明通过含碳球团在转底炉内经历碳热直接还原,获取多孔预还原金属化球团;炽热的多孔金属化球团经排料装置进入竖式还原冷却反应器,本发明将竖式冷却器的冷却介质由氮气变为还原气(h2或co),在冷却的同时也进行球团的深度还原,经h2或co气体深度还原换热冷却后的多孔金属化球团的金属化率达到90%以上,该多孔金属化球团的铁晶粒比较大,经磁选后能够直接得到金属铁;另外,本发明还原换热的气体从反应器上部排出,经换热器冷却、脱湿、除杂后返回竖式还原冷却器循环利用。以上所述,仅为本发明较佳的具体实施方式,但本发明的保护范围并不局限于此,任何熟悉本
技术领域:
的技术人员在本发明揭露的技术范围内,可轻易想到的变化或替换,都应涵盖在本发明的保护范围之内。当前第1页12