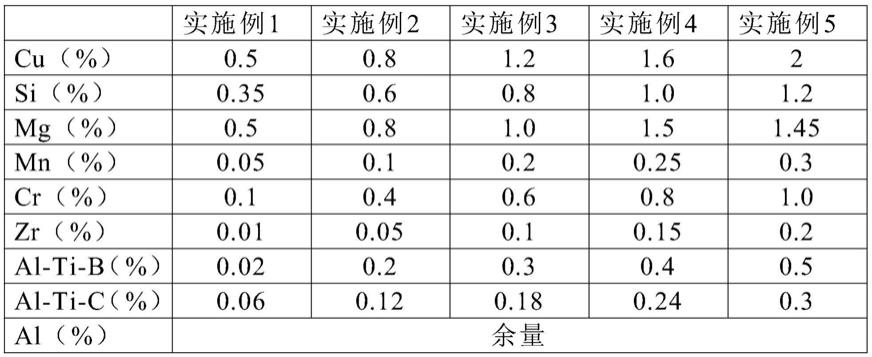
[0001]
本发明涉及一种液压缸缸盖及其制备方法,属于液压机械设备技术领域。
背景技术:[0002]
液压缸是将液压能转变为机械能(直线往复运动或摆动运动) 的液压执行元件,其具有结构简单、工作可靠、成本低的优点,因而在各种机械的液压系统中得到广泛应用。液压缸主要包括缸筒、活塞和活塞杆等零部件,其中活塞可滑动地安装在缸筒的内腔中,活塞杆一端与活塞连接,另一端从缸筒的一端伸出。液压缸的缸盖结构通常指的是缸筒供活塞杆穿出一端的密闭式结构,其起到密封缸筒的有杆腔、以及对活塞杆导向的作用。
[0003]
液压缸在工作过程中很容易导致缸盖热应力分布不均匀,即内应力不一致,同时它还承受髙达5-8mpa爆发力及螺栓紧固压力,因此,机械应力很大。在上述状况下,缸盖会产生压缩、扭曲、热疲劳、弯曲等变形。除了从结构弥补以上缺陷,缸盖的材料选择也至关重要。传统的缸盖材料多为灰铸铁或合金铸铁,灰铸铁或合金铸铁制造的缸盖虽然具有较高强度、变形量小、铸造性能好等优点,但重量大、导热差不利于积聚在缸盖的热量及时排出而使缸盖损坏。因此,需要寻求一种新型材料用于缸盖制备,使得缸盖有足够强度、刚度的同时还具备较轻的重量及良好的导热性能。
技术实现要素:[0004]
本发明的目的是针对现有技术中存在的上述问题,提供了一种高强度、良好导热性能和抗疲劳性能的轻量化液压缸缸盖及其制备方法。
[0005]
本发明的上述目的可以通过下列技术方案来实现:一种液压缸缸盖,所述液压缸缸盖由铝合金制成,所述铝合金由以下质量百分比的成分制成:cu:0.5-2%、si:0.3-1.2%、mg:0.5-1.5%、 mn:0.05-0.3%、cr:0.1-1.0%、zr:0.01-0.2%、al-ti-b中间合金:0.02-0.5%、al-ti-c中间合金:0.06-0.3%,余量为al及不可避免的杂质。
[0006]
本发明合金原料中加入了少量的cu,cu对合金有一定的固溶强化作用,有助于提高合金的抗疲劳性能,但铜过量,合金的抗腐蚀性能会下降,为此,本发明添加了少量的zr,少量的zr 与al形成al3zr粒子钉扎在晶界上,阻碍了位错的滑移和晶界移动,使固溶处理过程中再结晶趋势减弱,细化了合金晶粒,由于晶粒小,晶界多,腐蚀进入铝合金材料内部的时间大大延长,提高了合金的耐腐蚀性能。本发明为了获得均匀的合金铸态组织,还添加了中间合金al-ti-b,al-ti-b与熔融铝发生反应形成tial3和tib2粒子而产生细化作用,但tib2粒子易受zr、cr等原子毒化而失去细化晶粒的作用,为此添加了中间合金al-ti-c,al-ti-c 与熔融铝发生反应形成tial3和tic粒子,tic粒子聚集倾向小和对zr、cr中毒有免疫力,可以弥补因单独添加al-ti-b而带来的缺陷,且二者协同进一步增强细化晶粒作用,有利于提高合金的力学性能及机械加工性能。
[0007]
作为优选,mg/si质量比为(1.2-1.5):1。本发明将mg/si 质量比控制在该范围可以获得导热性能优异的铝合金。
[0008]
本发明的另一个目的是提供一种上述液压缸缸盖的制备方法,包括以下步骤:
[0009]
s1、称取如下质量百分比的原料:cu:0.5-2%、si:0.3-1.2%、 mg:0.5-1.5%、mn:0.05-0.8%、cr:0.1-1.0%、zr:0.01-0.2%、 al-ti-b中间合金:0.02-0.5%、al-ti-c中间合金:0.06-0.3%,余量为al;
[0010]
s2、将铝置于熔炼炉中加热至680-720℃熔化,升温至 1000-1150℃后,加入cu、al-ti-b中间合金、al-ti-c中间合金熔炼30-40min,继续升温至1200-1300℃,加入si、mn、cr、zr,熔炼20-30min,最后调节温度至700-750℃,加入mg至全部熔化,搅拌均匀后扒渣、精炼,制得铝合金液;
[0011]
s3、将铝合金液于机械振动模具中进行铸造,制得铸件;
[0012]
s4、将铸件于430-450℃/12-18h+480-500℃/20-25h下进行均匀化处理,接着再进行固溶时效处理,制得液压缸缸盖。
[0013]
本发明根据合金元素熔点不同的物理特性及元素的烧损情况采用分段式熔炼,先溶解低熔点及不易烧损的元素,再逐步升温溶解高熔点元素及中间合金,最后降温至一定范围,溶解易烧损元素,通过分段式熔炼大幅度提高了合金材料的利用率,节约材料成本,优化合金材料的综合性能。对熔炼均匀的合金液进行机械振动铸造细化了组织、加强了补缩,减轻了缩松,对液压缸缸盖的力学性能有显著提升。然后通过递进式均匀化处理,先低温将细小的易溶低熔点共晶相溶解完全,再升高温度对粗大的低熔点共晶相和难溶共晶相进行溶解,这种递进式均匀化能使铸态合金中的低熔点共晶相最大限度地溶入基体中,促进主合金元素在晶界、晶内分布趋于均匀,枝晶偏析基本消除,从而提高合金的力学性能。均匀化处理后紧接固溶时效处理,改善材料的抗疲劳性能,抗疲劳寿命达到335万次,缺口室温旋转弯曲疲劳极限达到92mpa。
[0014]
作为优选,步骤s2在熔炼过程中还添加有占铝合金总质量 0.35%的覆盖剂。
[0015]
进一步优选,覆盖剂由5-15份sio2、4-8份na2sif6、30-40 份nacl组成。
[0016]
本发明覆盖剂中sio2粉末对自氧化生长有诱发和引导作用,与熔体接触反应,加快了初期传质过程,使al液传输的微观通道始终处于活性状态,生成的al2o3构筑了材料的初始骨架,使材料氧化生长孕育期消失。但sio2自身表面张力较大,不容易与熔体浸润,为了更好的保护铝合金液,本发明进一步添加na2sif6和与之配合使用。na2sif6进入铝液分解得到sif4和naf,sif4呈气泡上浮,可以起到精炼作用;naf因熔点太高,需要配合低熔点的nacl来降低熔点,部分naf能与铝液进一步反应分解出钠元素,金属钠对a1-si共晶合金的共晶组织有细化作用,能明显提高合金的力学性能,部分naf在铝液表明形成覆盖层,对铝液起保护作用,减少氧化、吸气。
[0017]
作为优选,步骤s2中精炼采取转速为200-300r/min、惰性气体流量为10-12l/min、压力为0.1-0.3mpa的旋转喷粉精炼。
[0018]
作为优选,步骤s3控制振动频率为60-90hz,振幅为 0.5-1.2mm,控制铸造温度为700-750℃。随着铸造注温度的降低晶粒逐渐细化,但机械振动过程中温度过低使得金属液凝固时间较短,大多数枝晶还没来得及被“剪切”,初生α相较多以树枝晶状生长,晶粒具有粗化的趋向,同时过低的铸造温度也会影响金属液的充型能力。随着铸造温度的升高,虽然晶粒尺寸也发生了粗化,但由于机械振动的作用,使得树枝晶的数量明显减少,继续升高铸造温度(超过750℃),温度变化引起的晶粒粗化趋势远大于机械振动效用,最终导致大量粗
晶粒的出现,严重影响合金产品的力学性能和耐蚀性。
[0019]
作为优选,步骤s4中固溶处理为固溶温度为470-500℃、固溶时间为4-8h、水冷,时效处理为时效温度为165-185℃、时效时间为12-24h、空冷。
[0020]
与现有技术相比,本发明具有如下优点:
[0021]
1.本发明将合金元素与中间合金作为共同原料合理配伍,提高合金的耐蚀性、力学性能;再合理控制原料中mg/si质量比改善材料的导热性能。
[0022]
2.液压缸缸盖制备过程采用分段式熔炼,机械振动式铸造,分段式均匀化处理,特定条件固溶时效提高了缸盖的力学性能,还使缸盖的抗疲劳性能大幅度提升,抗疲劳使用寿命达到335万次,缺口室温旋转弯曲疲劳极限达到92mpa。
具体实施方式
[0023]
以下是本发明的具体实施例,并说明对本发明的技术方案作进一步的描述,但本发明并不限于这些实施例。如果无特殊说明,本发明的实施例中所采用的原料均为本领域常用的原料,实施例中所采用的方法,均为本领域的常规方法。
[0024]
实施例1-5
[0025]
实施例1-5中液压缸缸盖由以下质量百分比的成分制成:cu: 0.5-2%、si:0.3-1.2%、mg:0.5-1.5%、mn:0.05-0.3%、cr:0.1-1.0%、 zr:0.01-0.2%、al-ti-b中间合金:0.02-0.5%、al-ti-c中间合金: 0.06-0.3%,余量为al及不可避免的杂质;其中,优选mg/si质量比为(1.2-1.5):1。
[0026]
实施例1-5中液压缸缸盖材料成分如表1所示:
[0027][0028]
实施例6
[0029]
称取如实施例1中所述的液压缸缸盖原料,先将原料中铝置于熔炼炉中加热至680℃熔化,升温至1000℃后,加入cu、al-ti-b中间合金、al-ti-c中间合金熔炼30min,继续升温至1200℃,加入si、 mn、cr、zr,熔炼20min,最后调节温度至700℃,加入mg至全部熔化,搅拌均匀后扒渣、采取转速为200r/min、惰性气体流量为 10l/min、压力为0.1mpa的旋转喷粉精炼,制得铝合金液;其中在熔炼过程中还添加重量份数及组成为5份sio2、4份na2sif6、30份 nacl的占铝合金总质量0.35%的覆盖剂;
[0030]
将铝合金液于机械振动模具中进行铸造,控制振动频率为 60hz,振幅为0.5mm,控制铸造温度为700℃,制得铸件;
[0031]
将铸件于430℃/12h+480℃/20h下进行均匀化处理,接着于 470℃下固溶处理4h、水冷,然后再于165℃、时效处理12h、空冷,制得液压缸缸盖。
[0032]
实施例7
[0033]
称取如实施例2中所述的液压缸缸盖原料,先将原料中铝置于熔炼炉中加热至690℃熔化,升温至1050℃后,加入cu、al-ti-b中间合金、al-ti-c中间合金熔炼35min,继续升温至1220℃,加入si、 mn、cr、zr,熔炼22min,最后调节温度至710℃,加入mg至全部熔化,搅拌均匀后扒渣、采取转速为220r/min、惰性气体流量为 10.5l/min、压力为0.15mpa的旋转喷粉精炼,制得铝合金液;其中在熔炼过程中还添加重量份数及组成为8份sio2、5份na2sif6、32 份nacl的占铝合金总质量0.35%的覆盖剂;
[0034]
将铝合金液于机械振动模具中进行铸造,控制振动频率为 65hz,振幅为0.7mm,控制铸造温度为710℃,制得铸件;
[0035]
将铸件于435℃/14h+485℃/21h下进行均匀化处理,接着于 475℃下固溶处理5h、水冷,然后再于170℃、时效处理15h、空冷,制得液压缸缸盖。
[0036]
实施例8
[0037]
称取如实施例3中所述的液压缸缸盖原料,先将原料中铝置于熔炼炉中加热至700℃熔化,升温至1100℃后,加入cu、al-ti-b中间合金、al-ti-c中间合金熔炼36min,继续升温至1250℃,加入si、 mn、cr、zr,熔炼25min,最后调节温度至730℃,加入mg至全部熔化,搅拌均匀后扒渣、采取转速为250r/min、惰性气体流量为 11l/min、压力为0.2mpa的旋转喷粉精炼,制得铝合金液;其中在熔炼过程中还添加重量份数及组成为10份sio2、6份na2sif6、35份 nacl的占铝合金总质量0.35%的覆盖剂;
[0038]
将铝合金液于机械振动模具中进行铸造,控制振动频率为 75hz,振幅为0.9mm,控制铸造温度为730℃,制得铸件;
[0039]
将铸件于440℃/15h+490℃/23h下进行均匀化处理,接着于 480℃下固溶处理6h、水冷,然后再于175℃、时效处理18h、空冷,制得液压缸缸盖。
[0040]
实施例9
[0041]
称取如实施例4中所述的液压缸缸盖原料,先将原料中铝置于熔炼炉中加热至710℃熔化,升温至1130℃后,加入cu、al-ti-b中间合金、al-ti-c中间合金熔炼38min,继续升温至1270℃,加入si、 mn、cr、zr,熔炼28min,最后调节温度至740℃,加入mg至全部熔化,搅拌均匀后扒渣、采取转速为270r/min、惰性气体流量为 11.5l/min、压力为0.25mpa的旋转喷粉精炼,制得铝合金液;其中在熔炼过程中还添加重量份数及组成为12份sio2、7份na2sif6、36 份nacl的占铝合金总质量0.35%的覆盖剂;
[0042]
将铝合金液于机械振动模具中进行铸造,控制振动频率为 80hz,振幅为1.0mm,控制铸造温度为735℃,制得铸件;
[0043]
将铸件于445℃/16h+490℃/23h下进行均匀化处理,接着于 485℃下固溶处理7h、水冷,然后再于180℃、时效处理22h、空冷,制得液压缸缸盖。
[0044]
实施例10
[0045]
称取如实施例5中所述的液压缸缸盖原料,先将原料中铝置于熔炼炉中加热至720℃熔化,升温至1150℃后,加入cu、al-ti-b中间合金、al-ti-c中间合金熔炼40min,继续升温至1300℃,加入si、 mn、cr、zr,熔炼30min,最后调节温度至750℃,加入mg至全部熔化,搅
拌均匀后扒渣、采取转速为300r/min、惰性气体流量为 12l/min、压力为0.3mpa的旋转喷粉精炼,制得铝合金液;其中在熔炼过程中还添加重量份数及组成为15份sio2、8份na2sif6、40份 nacl的占铝合金总质量0.35%的覆盖剂;
[0046]
将铝合金液于机械振动模具中进行铸造,控制振动频率为 90hz,振幅为1.2mm,控制铸造温度为750℃,制得铸件;
[0047]
将铸件于450℃/18h+500℃/25h下进行均匀化处理,接着于 500℃下固溶处理8h、水冷,然后再于185℃、时效处理24h、空冷,制得液压缸缸盖。
[0048]
对比例1
[0049]
与实施例8的区别在于,原料中si含量为0.5%,mg含量为0.5%,即mg/si质量比为1。
[0050]
对比例2
[0051]
与实施例8的区别在于,原料中si含量为0.6%,mg含量为1.2%,即mg/si质量比为2。
[0052]
对比例3
[0053]
与实施例8的区别在于,熔炼过程将所有原料一次性加入到熔炼炉中。
[0054]
对比例4
[0055]
与实施例8的区别在于,铸造过程将合金液直接浇注进入常规模具,不添加机械振动方式。
[0056]
对比例5
[0057]
与实施例8的区别仅在于,对铸件不进行均匀化处理。
[0058]
对比例6
[0059]
与实施例8的区别在于,对铸件仅进行一次均匀化处理。
[0060]
对比例7
[0061]
与实施例8的区别在于,对均匀化后的铸件不进行固溶时效处理。
[0062]
将实施例6-10及对比例1-7中制得的液压缸缸盖进行性能测试,测试结果如表1所示。
[0063]
表1:实施例6-10及对比例1-7中制得的液压缸缸盖的性能参数
[0064]
[0065]
鉴于本发明方案实施例众多,各实施例实验数据庞大众多,不适合于此处逐一列举说明,但是各实施例所需要验证的内容和得到的最终结论均接近。
[0066]
尽管对本发明已作出了详细的说明并引证了一些具体实施例,但是对本领域熟练技术人员来说,只要不离开本发明的精神和范围可作各种变化或修正是显然的。