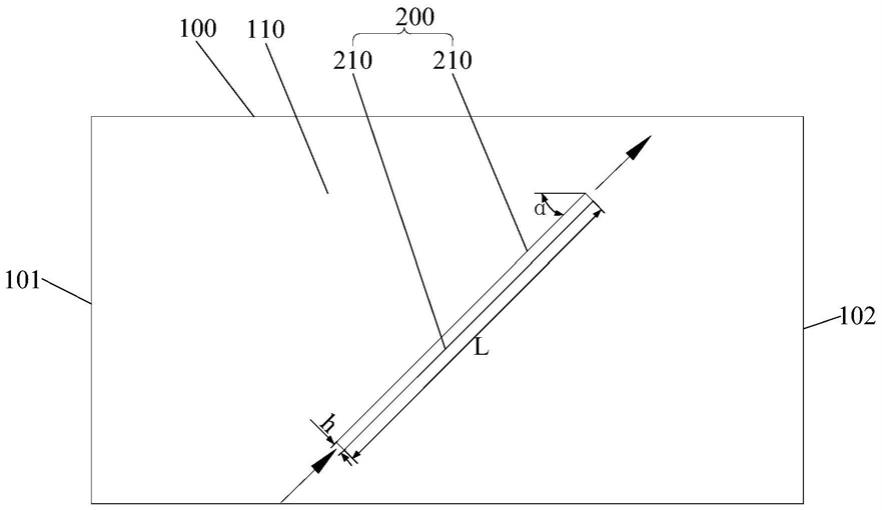
[0001]
本发明涉及炼钢技术领域,特别涉及一种烟气忽米级颗粒分离装置。
背景技术:[0002]
随着的节能环保意识的逐步加强,研究转炉烟气的全余热回收、探寻真正的干法除尘工艺,已经成为众多炼钢厂的关注点。而影响开发转炉全干法余热回收工艺的重要环节是如何解决工艺过程中转炉烟气的防爆问题。引起转炉煤气发生爆炸的三要素分别为12.5%~75%的co浓度、610℃以下的温度以及足够能量的火种。为防止爆炸的产生,必须从这三个必要条件来考虑,如果限制了其中一个必要条件,就限制了爆炸的产生。
[0003]
转炉炼钢是一种间歇式的生产方式。在转炉正常冶炼生产阶段,烟气温度高,烟气量大,含尘量大,管道内烟气流速高,co含量高;为防止因所携带的大颗粒高温火种引燃烟气发生爆炸,需要在余热回收前完成高温大颗粒,特别是忽米级大颗粒(平均粒径不小于50μm的颗粒)的分离,以保证全余热回收阶段无爆炸现象发生。在转炉准备活动阶段,烟气温度降低,烟气量小,含尘量也有所降低,管道烟气流速小,co含量介于爆炸上下限浓度区间,如果同时存在足够能量的大颗粒火种,就很可能会引发爆炸,所以该阶段大颗粒的捕集同样重要。
[0004]
烟气中所含忽米级大颗粒的分离捕集技术目前有很多种,主要有湿法或半干法分离、旋风分离和布袋分离等,利用重力、离心力、惯性力及阻力,将其从烟气中分离出来。由于湿法或半干法分离技术需要额外用水量、粉尘颗粒(主要成分为fe2o3)在高温有水存在的条件下理化性质发生改变,影响灰尘的二次利用;旋风分离技术烟气容易产生涡流;布袋分离技术压力损失较大且不适用于高温烟气。因此需要开发一种高效、简捷且能适用于高中低温、高中低流速间歇转换的干法忽米级大颗粒捕集技术。
[0005]
授权公告号为cn1148264c的中国发明专利公开了一种可降低磨损的气固旋风分离方法及其装置,其步骤为:1、具有一定流速并携带烟尘的烟气通过气固分离器的烟气水平入口段沿切向方向进入旋风分离器筒体,在离心力和惯性力的作用下,烟气携带的颗粒被高速甩向壁面;2、烟气中的大颗粒在筒体内逐渐向入口对侧聚集,形成大颗粒的浓相区,浓相区的大颗粒沿浓相区域范围内的筒体壁面上的开口进入在筒体外壁连接的螺旋向下的粗颗粒螺旋下料管,直接通过旋风分离器的返料腿排出;3、净化后的烟气经旋风分离器中心筒排出。
[0006]
该旋风分离技术,由于旋转气流路径的不确定和气固分离界面处的气流往返等因素,导致在旋风除尘器中的气流不能实现柱塞流的形态,会存在涡流等现象,且可能会存在少量大颗粒的返混携带现象,对转炉烟气有发生爆炸的隐患。
[0007]
申请公布号为cn10949921a的中国发明专利公开了一种移动床颗粒层过滤器,其包括内层筒体、中间筒体和外层筒体,内层筒体与中间筒体之间形成第一环形空腔,该第一环形空腔内设有过滤颗粒层,过滤器的下部设有烟气入口,上部设有烟气出口,含尘烟气从烟气入口首先进入内层筒体的内空腔,然后经过过滤颗粒层的过滤,再进入中间筒体与外
层筒体之间的第二环形空腔,过滤后的净化烟气再从烟气出口排出。
[0008]
该移动床颗粒层过滤器,虽然除尘效率比较高,但气体流经移动颗粒层气固接触面积大,流速要求低,滤料需要定期更新,总体能耗较高、运行成本较高。
[0009]
授权公告号为cn209338597u的中国实用新型专利公开一种转炉烟气除尘及余热回收系统,其步骤为转炉烟气经汽化冷却烟道后,进入熄火塔,在熄火塔内通过喷水降温,熄灭烟气中的火种,同时通过重力沉降的方式去除烟气中的大颗粒烟尘。
[0010]
上述重力沉降分离技术,虽然有效避免了转炉烟气产生爆炸的风险,但其实质上是一种湿法与重力沉降的组合分离技术,一方面浪费了烟气的高温能质,另一方面耗水量大,需要对废水进行二次处理。
[0011]
授权公告号为cn201744260u的中国实用新型专利公开了一种全蒸发喷雾冷却干式除尘装置,其步骤为:烟气从水冷道进入,与双流喷枪喷出的雾滴混合,经补偿器进入蒸发冷却塔,在蒸发冷却塔内,雾滴吸热蒸发汽化,烟气温度下降,粗颗粒与部分细颗粒粉尘与雾滴碰撞凝并落入香蕉弯头,并从输灰机的出灰口经卸灰阀排出,降温并粗除尘后的烟气从香蕉弯头出口连接管道进入静电除尘器精除尘。
[0012]
上述蒸发喷雾冷却干式除尘技术,虽然可以达到快速降温和粗除尘的目的,但仍需要大量的循环水,并不是一种真正的干法除尘,且该技术浪费了烟气的高温能质,蒸发冷却器在使用过程中还存在内壁易结垢的问题。
技术实现要素:[0013]
本发明的目的是提供一种耗能低且能够分离烟气中忽米级颗粒的烟气忽米级颗粒分离装置。
[0014]
为达到上述目的,本发明提供了一种烟气忽米级颗粒分离装置,其设置于烟道的沉降区内,所述烟气忽米级颗粒分离装置包括至少一组沉降组件,每一所述沉降组件包括至少两层间隔设置的斜板,所述斜板沿烟气的流动方向朝向所述烟道的顶壁倾斜设置,且所述斜板与所述烟道的顶壁之间的夹角为5
°
~70
°
。
[0015]
如上所述的烟气忽米级颗粒分离装置,其中,相邻两所述斜板之间的距离为10mm~350mm。
[0016]
如上所述的烟气忽米级颗粒分离装置,其中,各所述斜板等间隔设置。
[0017]
如上所述的烟气忽米级颗粒分离装置,其中,所述斜板的长度为600mm~2500mm。
[0018]
如上所述的烟气忽米级颗粒分离装置,其中,各所述斜板的长度相等。
[0019]
如上所述的烟气忽米级颗粒分离装置,其中,相邻两层所述斜板相互平行设置。
[0020]
如上所述的烟气忽米级颗粒分离装置,其中,所述斜板包括两相对设置的导流面、两相对设置的连接侧面和两相对设置的分流侧面,两所述连接侧面与所述烟道的内表面固定连接。
[0021]
如上所述的烟气忽米级颗粒分离装置,其中,各所述斜板为厚度均匀的平板。
[0022]
如上所述的烟气忽米级颗粒分离装置,其中,所述烟道内设有两组间隔设置的所述沉降组件。
[0023]
如上所述的烟气忽米级颗粒分离装置,其中,两所述沉降组件之间的距离为1100mm,所述斜板的宽度为4500mm。
[0024]
与现有技术相比,本发明的优点如下:
[0025]
本发明的烟气颗粒分离装置,利用全干法重力沉降,耗能低,含尘颗粒的理化性质不受外界干扰,能保持不变,有利于灰尘的二次利用。
[0026]
本发明的烟气忽米级颗粒分离装置,通过设置多层斜板,使得携带颗粒的高温烟气能被分隔成多个扁薄的气流,形成多层流烟气,由于固体颗粒比重远高于烟气,使得固体颗粒在自身重力作用而下落,又由于斜板为沿烟气的流动方向朝向烟道的顶壁倾斜设置,使得固体颗粒的下落距离缩短,从而能更快的触及斜板,进而将忽米级颗粒分离出来,达到分离的目的。
附图说明
[0027]
以下附图仅旨在于对本发明做示意性说明和解释,并不限定本发明的范围。其中:
[0028]
图1是本发明的烟气忽米级颗粒分离装置的第一种结构示意图;
[0029]
图2是本发明的烟气忽米级颗粒分离装置的第二种结构示意图;
[0030]
图3是斜板的结构示意图。
[0031]
附图标号说明:
[0032]
100、烟道;101、进口;102、出口;110、沉降区;
[0033]
200、沉降组件;210、斜板;211、导流面;212、分流侧面;213、连接侧面。
具体实施方式
[0034]
为了对本发明的技术方案、目的和效果有更清楚的理解,现结合附图说明本发明的具体实施方式。其中,形容词性或副词性修饰语“内”和“外”的使用仅是为了便于多组术语之间的相对参考,且并非描述对经修饰术语的任何特定的方向限制。本发明的描述中,除非另有说明,“多个”的含义是两个或两个以上。在图1和图2中,实线短箭头为烟气流动方向,“高温”的含义是650℃~800℃。
[0035]
如图1和图2所示,本发明提供了一种烟气忽米级颗粒分离装置,其设置于烟道的沉降区110内,该烟气忽米级颗粒分离装置包括至少一组沉降组件200,其中:
[0036]
烟道100具有顶壁和底壁,烟道100设有相对的进口101和出口102,即进口101和出口102的设置位置相对;
[0037]
沉降组件200包括由上至下设置的至少两层间隔排布的斜板210,以利于斜板210的排布,相邻两斜板210之间形成烟气流通通道,斜板210沿烟气的流动方向朝向烟道100的顶壁倾斜设置,且斜板210与烟道100的顶壁之间的夹角α为5
°
~70
°
,使得颗粒在烟气流通通道内随烟气流动时,下落距离缩短,从而能更快的触及斜板210,进而将颗粒分离出来。
[0038]
在使用时,如图1和图2所示,转炉冶炼过程中产生的高温烟气,通过位于转炉上方的转炉烟道,对烟气以辐射换热为主降温至800℃左右,烟气中所携带的颗粒浓度可高达200g/nm3,烟气携带着忽米级及以下的颗粒自进口101进入烟道100,在多层斜板210的作用下忽米级及以下的颗粒沉降在各斜板210上,即完成了忽米级颗粒尘的分离,在转炉炼钢的准备阶段,将捕集到的颗粒集中收集后排出。
[0039]
本发明的烟气忽米级颗粒分离装置,通过设置多层斜板210,使得携带颗粒的高温烟气能被多层斜板210分隔成多个扁薄的气流,形成多层流烟气,由于固体颗粒比重远高于
烟气,使得固体颗粒在自身重力作用而下落,又由于斜板210沿烟气的流动方向朝向烟道100的顶壁倾斜设置,使得固体颗粒的下落距离缩短,从而能更快的触及斜板210,进而将忽米级颗粒分离出来,达到分离的目的,此外,斜板210与烟道100的顶壁之间的夹角为5
°
~70
°
,便于积灰的清理和滑落,当斜板210的倾角大于颗粒的安息角时,沉积在斜板上的灰自行滑落。
[0040]
进一步,相邻两层斜板210相互平行设置,以使得形成的多层流烟气更加均匀,从而更有利于将忽米级颗粒分离出来。
[0041]
进一步,相邻两斜板210之间的距离h为10mm~350mm,这样的距离,既能使得烟气能够顺畅的通过烟气流通通道,又能使得颗粒下落距离缩短,从而能更快的触及斜板210。
[0042]
进一步,斜板210的长度l为600mm~2500mm,这样的长度,能使得烟气携带的颗粒充分的接触斜板210,从而提升分离效果。
[0043]
再进一步,各斜板210的长度相等,以便于将沉降组件200安装于管道内。
[0044]
进一步,斜板210的宽度为2000mm~5000mm,这样的宽度,能够确保烟气与斜板210的接触面积,从而保证分离效果。
[0045]
在本发明的的一种实施方式中,如图3所示,斜板210包括两相对设置的导流面211、两相对设置的连接侧面213和两相对设置的分流侧面212,两连接侧面213与烟道100的内表面固定连接,以使得斜板210不会影响烟气的流动。
[0046]
其中,两连接侧面213与烟道100的内表面可以焊接连接,也可以通过螺栓固定连接,还可以通过铆钉固定连接。
[0047]
进一步,各所述斜板为厚度均匀的平板,以使得烟气能够顺畅的通过相邻两斜板210之间形成烟气流通通道。
[0048]
在本发明的的一种实施方式中,如图1所示,烟道100内设有两组间隔设置的沉降组件200,以使得烟气经由两级沉淀后排出,从而提高忽米级颗粒分离的效果。
[0049]
进一步,两沉降组件200之间的距离h为1100mm,以使得烟气在一级沉淀后,速度降低再进行二级沉降,从而进一步提高忽米级颗粒分离的效果。
[0050]
当然,烟道100内设有两组以上间隔设置的沉降组件200,如三组、六组或九组沉降组件200,在此不再赘述。
[0051]
下面结合附图,具体说明本发明的烟气忽米级颗粒分离装置的使用过程:
[0052]
如图1所示,在烟道100内设有一组沉降组件,斜板210与烟道100的顶壁之间的夹角为45
°
,斜板210的长度为1414mm,斜板210的宽度为4500mm,进入烟道100的烟气的温度为700℃,烟气流速范围为1.5m/s~7m/s,烟气中含尘颗粒浓度为120g/nm3,计入分析统计范围内的颗粒粒径范围为20μm~100μm。
[0053]
通过模拟仿真,计算分析烟气忽米级颗粒分离装置对烟气中含尘颗粒的分离捕集效果,统计结果显示,在烟气流速为1.5m/s~7m/s范围内,沉降组件对20μm粒径颗粒的捕集率不低于70%,对30μm粒径颗粒的捕集率不低于96.2%,对50μm及以上粒径颗粒的捕集率均能达到100%。
[0054]
如图2所示,在烟道100内设有两组沉降组件,每组沉降组件包括四层斜板210,相邻两斜板之间的距离为45mm,斜板210与烟道100的顶壁之间的夹角为11
°
,斜板210的长度为1100mm,斜板210的宽度为4500mm,进入烟道100的烟气的温度为700℃,烟气流速范围为
1.5m/s~7m/s,烟气中含尘颗粒浓度为120g/nm3,计入分析统计范围内的颗粒粒径范围为20μm~100μm。
[0055]
通过模拟仿真,计算分析烟气忽米级颗粒分离装置对烟气中含尘颗粒的分离捕集效果,统计结果显示,烟气流速为7m/s时,斜板沉降区对20μm粒径颗粒的捕集率为37.3%,对30μm粒径颗粒的捕集率为71.6%,对50μm及以上粒径颗粒的捕集率为100%;烟气流速越低,斜板沉降区对相应粒径颗粒的捕集率越高;烟气流速为1.5m/s时,斜板沉降区对20μm粒径颗粒的捕集率为64.4%,对30μm及以上粒径颗粒的捕集率为100%。
[0056]
综上所述,本发明的烟气颗粒分离装置,利用全干法重力沉降,耗能低,含尘颗粒的理化性质不受外界干扰,能保持不变,有利于灰尘的二次利用。
[0057]
本发明的烟气忽米级颗粒分离装置,通过设置多层斜板,使得携带颗粒的高温烟气能被分隔成多个扁薄的气流,形成多层流烟气,由于固体颗粒比重远高于烟气,使得固体颗粒在自身重力作用而下落,又由于斜板为沿烟气的流动方向朝向烟道的顶壁倾斜设置,使得固体颗粒的下落距离缩短,从而能更快的触及斜板,进而将忽米级颗粒分离出来,达到分离的目的。
[0058]
以上所述仅为本发明示意性的具体实施方式,并非用以限定本发明的范围。任何本领域的技术人员,在不脱离本发明的构思和原则的前提下所作出的等同变化与修改,均应属于本发明保护的范围。而且需要说明的是,本发明的各组成部分并不仅限于上述整体应用,本发明的说明书中描述的各技术特征可以根据实际需要选择一项单独采用或选择多项组合起来使用,因此,本发明理所当然地涵盖了与本案发明点有关的其它组合及具体应用。