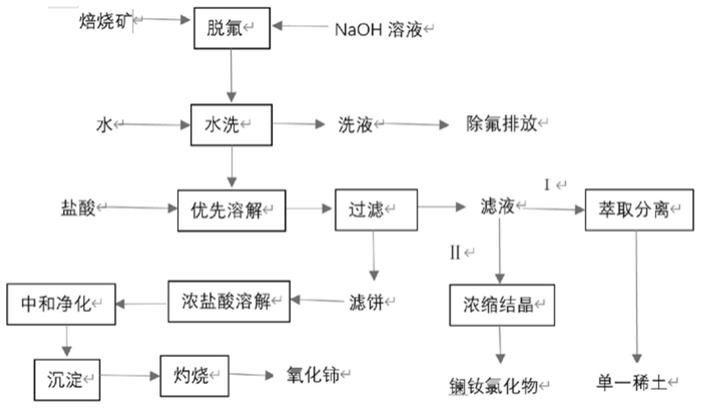
[0017]
无论是优浸工艺或是全浸出工艺,四价铈在与浓盐酸反应时都会产生氯气,因此在实际生产中都需要添加抑氯剂如硫脲来降低氯气的生成,反应式如式5所示。而硫脲的加入又会在酸浸液中产生氯化铵,如式6所示,最终排入沉淀废水中,引起废水中cod含量的增加。
[0018]
4cl2+(h2n)2cs+5h2o
→
8hcl+h2so4+(h2n)2co
ꢀꢀꢀꢀ5[0019]
(h2n)2co+2hcl+h2o
→
2hn4cl+co2ꢀꢀꢀꢀ6[0020]
为此,现有的焙烧氟碳铈矿技术在酸浸提取稀土有价元素的过程中不可避免的会引起废水中的氨氮含量增加或产生大量的氯气,为此本专利针对氟碳铈矿焙烧过程中的铈元素化合价的变化,提出了一种新的工艺。
技术实现要素::
[0021]
本发明的目的是克服上述现有技术存在的不足,提供一种氟碳铈矿的焙烧工艺,针对氟碳铈矿的元素组成及物相特点开发的批量化生产用焙烧矿技术,能够有效减少现有生产过程中的氯气处置量,同时提高化学法冶炼过程中的稀土有价元素浸出率,可用于氟碳铈矿冶炼过程中的焙烧环节。
[0022]
稀土提取是从稀土精矿中提取稀土元素的湿法冶金过程,它包括稀土精矿的分解,从精矿或分解产物中浸出稀土,浸出液的净化,通过浓缩结晶或沉淀、灼烧等过程制备混合稀土化合物或某些稀土元素的富集物。氟碳铈矿矿相为refco3,经空气焙烧后生成ref3,reof及re2o3三种物相(re为la,pr和nd三种元素),而铈元素则存在于ceo2和ceof2两种物相中。含铈物相在酸浸过程中会与浓盐酸发生氧化反应,四价铈被还原为三价,氯被氧化成氯气,如方程式4所示,如果不添加抑氯剂则会产生大量的氯气,在工业生产中需要进行碱喷淋处理,在废水系统中会生成次氯酸钠,需要经过特殊处理才能进行外排;此外,目前工业上常用的抑氯剂为硫脲,与cl2的反应式如5和6所示,虽然避免了氯气的产生,但是会导致废水中产生大量的氨氮,同样需要蒸氨或化学法等治理手段,为此本发明提出了一种真空碱焙烧技术,在不引入其他还原剂的情况下,最大限度抑制焙烧矿中四价铈的生成,使焙烧矿在酸浸过程中产生的次氯酸根浓度在允许外排的范围内。
[0023]
此外,在酸浸反应过程中,四价铈的还原反应会增加氟碳铈矿的反应活化能,进而降低稀土元素的浸出率。因此,无氧碱焙烧工艺不仅从源头减少了湿法冶炼过程中产生的次氯酸根或氨氮等污染物,还能够提高稀土元素从矿物中迁移到氯化稀土溶液中的浸出率。
[0024]
为实现上述目的,本发明采用以下技术方案:
[0025]
一种氟碳铈矿的焙烧工艺,包括以下步骤:
[0026]
步骤1,真空焙烧:
[0027]
取氟碳铈矿,球磨后放入真空旋转炉中,加热至400-500℃,保温2-4h,所述的加热速率为6-8℃/min,加热过程中保持炉内真空度为0.05pa,获得加热矿粉;
[0028]
步骤2,一次酸浸:
[0029]
取底水,按固液比,加热矿粉:底水=1:(1-2),单位g:ml,将加热矿粉与底水混合,搅拌成浆液,向浆液中缓慢加入盐酸溶液,所述的盐酸浓度为2-2.5mol/l,20-25℃下保温搅拌浸出至盐酸余酸浓度为0.3-0.6mol/l后,停止盐酸加入,加入阳离子型絮凝剂,加入质
量为加热矿粉质量的0.2-0.5%,进行沉降,沉降时间为20-35min,完成沉降后,抽离酸浸液,获得酸浸渣,所述的酸浸渣经清水洗至中性,获得洗液,所述的洗液与酸浸液混合,获得一次混合氯化稀土溶液;
[0030]
步骤3,真空碱浸焙烧:
[0031]
水洗后酸浸渣过滤和烘干后,按质量比,水洗后酸浸渣:naoh=1:(1-2),将水洗后酸浸渣与naoh混合均匀后,放入真空旋转炉中,加热至450-550℃,保温1.5-2.5h,所述的加热速率为7-10℃/min,加热过程中保持炉内真空度为0.05pa,获得二次焙烧矿粉;
[0032]
步骤4,二次酸浸:
[0033]
将二次焙烧矿粉水洗至中性后,缓慢加入盐酸溶液,所述的盐酸浓度为1.5-2mol/l,60-80℃下保温搅拌酸浸至酸浸液浓度为0.5-1mol/l,停止盐酸溶液加入,完成二次酸浸;加絮凝剂进行沉降,加入量为水洗后焙烧矿粉0.2-0.4%,沉降时间为20-30min,完成沉降后,抽离二次酸浸液,所述的二次酸浸渣经清水洗至中性,获得二次洗液,所述的二次洗液与二次酸浸液混合,获得二次混合氯化稀土溶液,与一次混合氯化稀土溶液混合,即为最终混合氯化稀土溶液。
[0034]
所述的步骤1中,氟碳铈矿包括组分及质量百分含量为re2o
3 65%,cao 0.46%,bao 11.45%,feo
3 0.61%,f 6.57%,tho
3 0.23%。
[0035]
所述的步骤1中,氟碳铈矿中的reo包括组分及质量百分含量为la2o
3 39.44%,ceo
2 46.89%,pro
11 3.43%,nd2o
3 9.37%,sm2o
3 0.56%,eu2o
3 0.09%,gd2o
3 0.16%,y2o
3 0.06%。
[0036]
所述的步骤1中,真空旋转炉转速为1转/min。
[0037]
所述的步骤1中,氟碳铈矿,球磨至200目后,放入真空旋转炉中。
[0038]
所述的步骤1中,加热后的矿粉包括组分re2o3为82-86wt%,余量杂质;所述的加热后矿粉中的ce元素均以三价化合态存在于re2o3中,主要以ce2o3和ceof2两种物相存在。
[0039]
所述的步骤2中,搅拌浸出时间为0.5-1h。
[0040]
所述的步骤2中,阳离子型絮凝剂为阳离子型聚丙烯酰胺。
[0041]
所述的步骤2中,酸浸过程中生成尾气,对尾气进行收集检测,所述的尾气中包含氯气,氯气浓度为4-6mg/l。
[0042]
所述的步骤2中,酸浸渣中ref3含量36-45%。
[0043]
所述的步骤3中,真空旋转炉转速为1转/min。
[0044]
所述的步骤4中,二次酸浸时间为40-70min。
[0045]
所述的步骤4中,絮凝剂为阳离子型聚丙烯酰胺。
[0046]
所述的步骤4中,二次酸浸过程中生成尾气,对尾气进行收集检测,尾气成分为氯气,浓度为5-7mg/l。
[0047]
所述的步骤4中,混合氯化稀土溶液中稀土元素总浸出率为98.9-99.6%,镨元素浸出率为99.2-99.5%,钕元素浸出率为99.4-99.6%,根据动力学方程以及阿伦尼乌斯公式计算出氟碳铈矿酸浸活化能,氟碳铈矿一次浸出过程中的活化能为29.3-29.5kj/mol。
[0048]
本发明的有益效果:
[0049]
在用盐酸全浸出焙烧矿中有价稀土元素的过程中,由于四价铈的存在会产生大量的氯气,会直接影响操作环境和污染环境。所以在现实生产中不仅需要添加抑氯剂,同时还
需要进行水喷淋或碱喷淋处理等工艺,以碱喷为例,反应方程式如9,10所示。抑氯剂的使用会在酸浸液中产生大量的氯化铵(如反应方程式5和6所示),同时在碱喷过程中又会产生次氯酸钠。
[0050]
cl2+h2o
→
hclo+h
+
+cl-ꢀꢀꢀꢀꢀ9[0051]
hclo+hcl+2naoh
→
naclo+nacl+2h2o
ꢀꢀꢀ
10
[0052]
在本发明中,通过第一步真空焙烧工艺以及第二步真空碱焙烧工艺对矿物进行热处理后,能够明显降低铈的氧化率,因此在两次酸浸过程中不会产生氯气,因此不需要添加抑氯剂或进行碱喷等处理。以日处理50吨氟碳铈精矿为例,空气中氧化焙烧后的精矿在两次酸浸过程中产生的氯气排放量经检测为1884kg/d,若不采用碱喷处理氯气,则需要消耗硫脲505kg/d,产生氨氮(以氮计)186kg/d,以生产中每吨矿产生30吨废水计算,氨氮在废水中的浓度为6.2g/l,远高于稀土工业污染物排放标准(gb26451-2011)中要求的20mg/l的直接排放量以及30mg/l的间接排放量,因此,在工业生产中需要进一步对氨氮进行处理;而采用真空碱焙烧工艺后,现场测得的氯气排放浓度远低于30mg/l,推测来自于酸浸过程中稀盐酸的挥发,因此,能够直接外排,无需采用碱喷等处理手段或添加硫脲等抑氯剂,本发明为稀土冶金企业节约了大量的尾气及污水处理成本。
[0053]
氟碳铈矿的酸浸过程可以用缩核模型来进行描述,浸出效率主要是受矿物表面的氟碳酸稀土以及氟化稀土的扩散所控制,动力学方程如式11所示,阿伦尼乌斯方程如式12所示:
[0054]
1-3(1-x)
2/3
+2(1-x)=k1t
ꢀꢀꢀꢀꢀ
11
[0055]
a
×
exp(-e
a
/rt)=k1ꢀꢀꢀꢀꢀꢀ
12
[0056]
其中,x表示稀土的浸出效率,k1表示速率常数,而t为浸出时间,a为指前因子,e
a
为表观活化能,r为理想气体常数,t表示热力学温度。酸浸过程中,由于氟化稀土尺寸较小,因此会吸附在氟碳铈矿表面,阻碍酸浸的进一步反应,进而增大活化能,降低浸出率,而四价铈与浓盐酸的还原反应能够延缓酸浸的反应速率,因此会导致浸出率的降低。因此,避免四价铈的产生不仅能够降低反应过程中的氯气排放量以及硫脲等还原剂的使用,还能够进一步提高稀土元素的浸出率。
附图说明:
[0057]
图1为现有技术氟碳铈矿优浸制取氧化铈工艺路线图;
[0058]
图2为现有技术氟碳铈矿全浸出制取混合氯化稀土工艺路线图;
[0059]
图3为本发明实施例1的氟碳铈矿真空焙烧差热谱图;
[0060]
图4为本发明实施例1的氟碳铈矿经过第一次无氧焙烧后的xrd谱图;
[0061]
图5为本发明实施例1的氟碳铈矿经一次酸浸与一次真空碱焙烧后的xrd图谱,。
具体实施方式:
[0062]
下面结合实施例对本发明作进一步的详细说明。
[0063]
一种氟碳铈矿的焙烧工艺,包括以下步骤:
[0064]
步骤1,真空焙烧:
[0065]
取氟碳铈矿,球磨至200目后,放入真空旋转炉中,真空旋转炉转速为1转/min,加
热至400-500℃,保温2-4h,所述的加热速率为6-8℃/min,加热过程中保持炉内真空度为0.05pa,获得加热矿粉;其中:
[0066]
氟碳铈矿包括组分及质量百分含量为re2o
3 65%,cao 0.46%,bao 11.45%,feo
3 0.61%,f 6.57%,tho
3 0.23%。
[0067]
氟碳铈矿中的reo包括组分及质量百分含量为la2o
3 39.44%,ceo
2 46.89%,pro
11 3.43%,nd2o
3 9.37%,sm2o
3 0.56%,eu2o
3 0.09%,gd2o
3 0.16%,y2o
3 0.06%。
[0068]
加热后的矿粉包括组分re2o3为82-86wt%,余量杂质;所述的加热后矿粉中的ce元素均以三价化合态存在于re2o3中,主要以ce2o3和ceof2两种物相存在。
[0069]
步骤2,一次酸浸:
[0070]
取底水,按固液比,加热矿粉:底水=1:(1-2),单位g:ml,将加热矿粉与底水混合,搅拌成浆液,向浆液中缓慢加入盐酸溶液,所述的盐酸浓度为2-2.5mol/l,20-25℃下保温搅拌浸出0.5-1h,至盐酸余酸浓度为0.3-0.6mol/l后,停止盐酸加入,加入聚丙烯酰胺,加入质量为加热矿粉质量的0.2-0.5%,进行沉降,沉降时间为20-35min,完成沉降后,抽离酸浸液,获得酸浸渣,所述的酸浸渣经清水洗至中性,获得洗液,所述的洗液与酸浸液混合,获得一次混合氯化稀土溶液;其中,酸浸过程中生成尾气,对尾气进行收集检测,所述的尾气中包含氯气,氯气浓度为4-6mg/l,酸浸渣中ref3含量36-45%。
[0071]
步骤3,真空碱浸焙烧:
[0072]
水洗后酸浸渣过滤和烘干后,按质量比,水洗后酸浸渣:naoh=1:(1-2),将水洗后酸浸渣与naoh混合均匀后,放入真空旋转炉中,真空旋转炉转速为1转/min,加热至450-550℃,保温1.5-2.5h,所述的加热速率为7-10℃/min,加热过程中保持炉内真空度为0.05pa,获得二次焙烧矿粉;
[0073]
步骤4,二次酸浸:
[0074]
将二次焙烧矿粉水洗至中性后,缓慢加入盐酸溶液,所述的盐酸浓度为1.5-2mol/l,60-80℃下保温搅拌40-70min,酸浸至酸浸液浓度为0.5-1mol/l,停止盐酸溶液加入,完成二次酸浸;加聚丙烯酰胺进行沉降,加入量为水洗后焙烧矿粉0.2-0.4%,沉降时间为20-30min,完成沉降后,抽离二次酸浸液,所述的二次酸浸渣经清水洗至中性,获得二次洗液,所述的二次洗液与二次酸浸液混合,获得二次混合氯化稀土溶液,与一次混合氯化稀土溶液混合,即为最终混合氯化稀土溶液,其中,二次酸浸过程中生成尾气,对尾气进行收集检测,尾气成分为氯气,浓度为5-7mg/l;混合氯化稀土溶液中稀土元素总浸出率为98.9-99.6%,镨元素浸出率为99.2-99.5%,钕元素浸出率为99.4-99.6%,根据动力学方程以及阿伦尼乌斯公式计算出氟碳铈矿酸浸活化能,氟碳铈矿一次浸出过程中的活化能为29.3-29.5kj/mol。
[0075]
以下实施例和对比例中处理的氟碳铈矿精矿成分如表1和表2所述。
[0076]
实施例1
[0077]
以1吨牦牛坪氟碳铈矿为例,具体的焙烧工艺如下:将氟碳铈矿放入真空旋转炉体中,炉体转速为1转/min,加热前用真空泵将炉体内的真空度降低到0.05pa,然后以7℃/min的加热速率从室温加热至550℃,保温2h,然后矿粉随炉自然冷却,在加热的整个过程中,炉体内的真空度保持在0.05pa。在此过程中,精矿的热力学行为如附图3所示,其分解温度的起点与终点同在空气中分解时一致,但只发生方程式1的反应,由真空焙烧矿的xrd曲线可
知(附图4),图中的特征峰对应的都是三价稀土氟氧化物的特征峰,焙烧矿中的ce元素主要以三价化合态存在于re2o3中。
[0078]
获得的加热后的矿粉包括组分re2o3为86wt%,将加热矿粉进行第一次酸浸,酸浸过程中,首先将加热矿粉倒入酸浸罐中,按照固液比加热矿粉:底水=1:1,单位为kg:l,加入1l的底水,搅拌成浆,在浸出槽中搅拌条件下,加入浓度为2mol/l的盐酸,加入量以加热矿粉中的re2o3全部溶解为准,酸浸反应完全后,酸浸液中的余酸浓度为0.5mol/l,根据表1和表2中的数值以及方程式1可知,1吨氟碳铈精矿需要一次酸浸盐酸用量为5.76m3,保温搅拌浸出1h后,加絮凝剂阳离子型聚丙烯酰胺,加入量为加热矿粉质量的0.5%,进行沉降,酸浸过程中通过排风系统收集尾气,并对尾气进行cl2浓度的测量,经检测,尾气中cl2浓度为4mg/l。完成一次酸浸后,抽离酸浸液,获得一浸酸浸渣,一浸酸浸渣经清水洗至中性,获得一次洗液,一次洗液与酸浸液混合,获得一次混合氯化稀土溶液;一浸酸浸渣中ref3含量36%。
[0079]
一浸酸浸渣通过洗涤、过滤和烘干方式处理后进行真空碱焙烧处理。由于一浸渣中的稀土元素主要以稀土氟化物的物相存在,为此,添加的固体naoh用量为酸浸渣中氟化稀土全部转化为氢氧化稀土的用量,具体为,按质量比,将后,按照质量比烘干一浸渣:naoh=1:2,7℃/min下加热至550℃,保温1.5h,反应方程式如式7所示。
[0080]
ref3+3naoh
→
re(oh)3+3naf
ꢀꢀꢀꢀꢀ7[0081]
在碱焙烧过程中,由于当温度达到500度以上时,会发生如式8所示的反应,因此,碱焙烧后矿渣的xrd图谱(图5所示)中能够发现稀土氧化物的特征峰,可知,经碱焙烧后的矿物中只含有稀土氧化物。
[0082]
2re(oh)3→
re2o3+3h2o
ꢀꢀꢀꢀꢀꢀ8[0083]
二次焙烧矿经过多次水洗后(水洗液ph值达到7时,停止水洗),再与2mol/l的稀盐酸进行二次酸浸,反应终点控制在1mol/l的酸余度,时间为50min,完成二次酸浸后,加入聚丙烯酰胺进行沉降,加入量为水洗后焙烧矿粉0.2%,沉降时间为30min,完成沉降后,抽离酸浸液,获得二次酸浸渣,二浸酸浸渣经清水洗至中性,获得二次洗液,二次洗液与酸浸液混合,获得二次混合氯化稀土溶液,得到的二次混合氯化稀土溶液与一次混合氯化稀土溶液用于萃取分离过程,进而获得单一的氯化稀土产品。二次酸浸过程中生成尾气,对尾气进行收集检测,尾气成分为氯气,浓度为3mg/l。
[0084]
最终获得的稀土浸出率为99.6%,镨元素浸出率为99.5%,钕元素浸出率为99.6%,氟碳铈矿一次浸出过程中的活化能为29.38kj/mol。
[0085]
对比例1
[0086]
同实施例1相同的氟碳铈矿,区别在于,空气中碱焙烧,具体过程为:将稀土矿在空气中500℃下进行氧化焙烧后,进行一次酸浸,盐酸浓度为10mol/l,反应结束后的余酸浓度为0.5mol/l;将酸浸渣水洗至中性后,再基于矿物中的稀土氧化物含量混合一定比例的naoh在500℃下进行有氧碱焙烧;将经碱焙烧后的矿物水洗至中性,然后进行第二次酸浸,盐酸浓度为2mol/l,反应终点至0.5mol/l。以两次酸浸液中稀土元素折合氧化物的质量进行浸出率的计算。最终获得的稀土浸出率为95.39%,镨元素浸出率为95.2%,钕元素浸出率为94.5%,氟碳铈矿一次浸出过程中的活化能为45.69kj/mol。
[0087]
对比例2
[0088]
同实施例1相同的氟碳铈矿,区别在于,采用现有酸浸及液态碱转工艺,具体过程为:将氟碳铈矿在空气中500℃下进行2h氧化焙烧后,进行一次酸浸,盐酸浓度为10mol/l,反应结束后的余酸浓度为0.5mol/l;将酸浸渣水洗至中性后,再基于矿物中的稀土氧化物含量将酸浸渣在130℃下60wt%的液碱中进行碱转,然后将碱转后的矿物洗至中性,并进行第二次酸浸,盐酸浓度为2mol/l,反应终止时的余酸浓度为0.5mol/l。以两次酸浸液中稀土元素折合氧化物的质量进行浸出率的计算。最终获得的稀土浸出率为90.33%,镨元素浸出率为91.6%,钕元素浸出率为89.3%,氟碳铈矿一次浸出过程中的活化能为51.26kj/mol。
[0089]
实施例2
[0090]
将一吨氟碳铈精矿(稀土氧化物占到总质量的65%)通过球磨磨至200目,然后投入真空回转窑。第一次真空焙烧前首先通过真空泵将窑内的真空度降至0.05pa,然后以5℃/min的速率将炉内温度升至450℃,并在该温度下保温4h。获得的加热后矿粉包括组分re2o3为82wt%。
[0091]
然后将加热后矿粉晾至常温后,投入酸浸罐中进行第一次酸浸。基于精矿中稀土氧化物的含量,在酸浸罐中缓慢加入5.625m3体积的稀盐酸,盐酸浓度为1.5mol/l,并搅拌30min,待余酸浓度稳定在0.5mol/l时,完成酸浸,加入聚丙烯酰胺,加入量为加热矿粉质量的0.2-0.5%,进行沉降,酸浸过程中通过排风系统收集尾气,并对尾气进行cl2浓度的测量,经检测,尾气中cl2浓度为6mg/l;完成一次酸浸后,抽离酸浸液,获得一浸酸浸渣,一浸酸浸渣经清水洗至中性,获得一次洗液,一次洗液与酸浸液混合,获得一次混合氯化稀土溶液;一浸酸浸渣中ref3含量45%;
[0092]
将一浸渣烘干后,按照质量比2:1与naoh混合,然后在真空回转窑中进行二次焙烧,真空度为0.5pa,焙烧温度为500℃,时间为1.5h,焙烧过程中窑炉转速为1转/min。将真空碱焙烧后的矿通过板框过滤水洗至洗液为中性,然后在酸浸罐中进行第二次酸浸,缓慢加入2mol/l的稀盐酸,70℃下保温搅拌浸出40min,直至酸浸液的酸度值为0.5mol/l,停止搅拌,二次酸浸渣加絮凝剂阳离子型聚丙烯酰胺进行沉降,加入量为水洗后焙烧矿粉0.2%,沉降时间为30min,完成沉降后,将酸浸液抽离酸浸罐,二次酸浸渣经清水洗至中性,获得二次洗液,二次洗液与二次酸浸液混合,获得二次混合氯化稀土溶液,并与一次酸浸液混合作为湿法过程中的最终混合氯化稀土溶液。二次酸浸过程中生成尾气,对尾气进行收集检测,尾气成分为氯气,浓度为5mg/l。
[0093]
最终获得的稀土浸出率为98.9%,镨元素浸出率为99.2%,钕元素浸出率为99.4%,氟碳铈矿一次浸出过程中的活化能为29.5kj/mol。