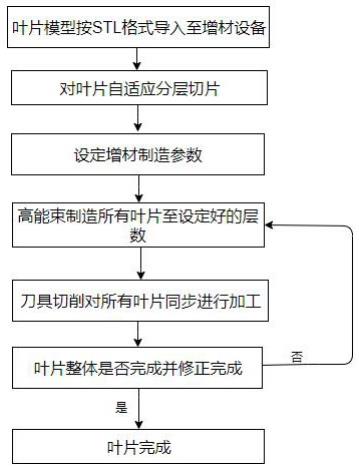
1.本发明涉及水轮机转轮制造技术领域,确切地说涉及对水轮机转轮使用增减材进行制造的方法。
背景技术:2.水轮机是重要的水电设备是水力发电行业必不可少的组成部分,是充分利用清洁可再生能源实现节能减排、减少环境污染的重要设备,其技术发展与我国水电行业的发展规模相适应。在我国电力需求的强力拉动下,我国水轮机及辅机制造行业进入快速发展期,其经济规模及技术水平都有显著提高,我国水轮机制造技术已达世界先进水平。
3.水轮机转轮是水轮机的重要部件,随着社会的不断发展,水轮机转轮的制造技术也越来越完善。现有的水轮机转轮制造通常至少包括叶片、上冠、下环的制造、装配与组焊过程。而水轮机转轮的精密性和制造成本对于水轮机在使用与制造过程显得尤为重要。
4.现有水轮机转轮的制造通常采用分体式制造方案,即单独加工叶片后与上冠、下环装配、焊接成整体转轮,其缺点在于具有不可避免的装配、组焊误差,转轮整体一致性不好,精度不佳,有大量的焊接、装配作业,效率低下。同时叶片采用铸件,有大量的切削材料浪费。由于曲面复杂、空间狭小,属于数控加工难点,因此几乎无法整体制造。3d打印(即增材制造)带来了新的制造方式,然而其表面粗糙度和尺寸误差一直难以达到高标准,相比机械加工相差很多。为此,现有技术中提出了授权公告号为cn108581397a,授权公告日为2020年2月18日的中国发明专利文献,来解决上述所存在的技术问题,该专利文献所公开的技术方案如下:增减材复合制造涡轮叶片的加工方法包括:增材成形和减材加工;增材成形与减材加工交替循环进行;增材成形包括:a1、整体建模分层;a2、局部特殊分层;a3、规划增材路径;a4、单周期增材加工;减材加工分为:端铣和侧铣两种加工类型;根据加工类型不同减材加工方法包括:b1、加工区域划分;b2、设置工艺参数;b3、局部特殊参数设置;b4、单周期减材加工;增材成形和减材加工循环重复,直到完成整个涡轮叶片。本发明具有方法新颖、工艺简便、提高加工精度、尤其细节特征精加工、提高加工效率、适用范围广等特点,故属于一种集经济性与实用性为一体的增减材复合制造涡轮叶片的加工方法。
5.上述技术在实际使用过程中,能部分有效地解决涡轮叶片与减材刀具就存在干涉的问题,并且采用增减材复合制造的方法不受叶片高度的限制,不考虑减材刀具与涡轮叶片的干涉问题,采用铣削或磨削等,得到好的表面质量。但由于其采用的方案主要是直接对叶片使用三维建模软件绘制拟制备的金属工件模型,使用切片软件将三维模型切片,无法避免的会出现台阶效应,使得成型件的表面与理论模型表面存在偏差。该技术以相同的层厚对模型分层,其算法较简单,但无法同时满足成型效率和精度的要求,且上述加工方法是对单个叶片的单独加工,对于叶片的加工一致性无法保证,若要适用于水轮机,还需要对上冠、下环的制造、装配与组焊的过程,转轮的整体一致性较差,且本专利采用铣削或磨削等方式,增材之后减材去除的材料较多,存在造成浪费的问题。
技术实现要素:6.为解决上述技术问题,本发明提出了一种水轮机转轮增减材复合制造方法,本发明避免了装配和焊接误差,整体一致性更好,同时增材之后减材去除的材料更少,保证了叶片的光洁度和尺寸精度,避免了材料浪费,对于水轮机无论是在使用方面,还是水轮机的成本方面考虑,都极为重要。
7.本发明是通过采用下述技术方案实现的:一种水轮机转轮增减材复合制造方法,包括以下步骤:a、将叶片模型按stl格式导入至增材设备,并将该模型自适应分层切片,确定增材制造参数,设定增材制造参数完成;b、设定增材制造参数完成后,利用高能束制造所有叶片至设定好的层数;c、增材所有叶片至设定好的层数后,利用刀具切削进行对所有叶片同步进行加工,去除多余的余量,并修正叶片变形,叶片修正完成后,再次利用高能束增材制造所有叶片至下一设定的层数;d、循环上述增材所有叶片至设定好的层数,利用刀具切削对所有叶片同步进行加工,去除多余的余量,并修正叶片完成变形的步骤直至所有的叶片整体完成并修正完成。
8.优选的,所述水轮机转轮增减材复合制造方法还包括制造上冠的步骤和制造下环的步骤。
9.优选的,所述的转轮叶片是在上冠上直接采用增减材复合加工方式进行制造,然后将带有叶片的上冠与下环组焊形成整体转轮。
10.优选的,所述的转轮叶片经增减材复合加工完成后,与制造好的上冠和下环分别组焊形成整体转轮。
11.优选的,所述自适应分层切片是先对叶片模型进行倾斜度分析,再针对叶片模型成型方向倾斜度更大的区域采用较小层厚的切片,针对叶片模型成型方向倾斜度更小的区域采用较大层厚的切片。
12.优选的,所述高能束为激光束、电弧、等离子束或电子束的一种。
13.优选的,所述增材制造参数包括分层参数、加工速度、保护气体充盈、预热温度、高能束的能量大小、持续时间、运动轨迹划分、加工过程中的温度控制和保护气体控制。
14.优选的,所述分层参数由刀具的切削范围、增材的变形需求和对增减材效率的需求决定。
15.优选的,所述高能束为激光束、电弧、等离子束或电子束的一种。
16.优选的,在步骤c和步骤b中的任意两次相邻刀具切削进行加工的减材过程中设置有部分重叠区域,优选的,所述叶片的增材与利用刀具切削过程采用多轴联动的方式。
17.与现有技术相比,本发明的有益效果表现在:1、本发明中,对叶片模型自适应分层切片,针对叶片的不同部位,采用自适应分层技术,以满足表面精度需求,同时降低加工风险,提高加工效率。同时,与公告号为cn108581397a专利文献相比,由于本发明是对叶片采取自适应分层,而非直接对叶片使用三维建模软件绘制拟制备的金属工件模型,使用切片软件将三维模型切片,需要将模型离散化生成二维数据轮廓,其中切片层厚即每一层的厚度,由于增材制造是由每一层切片堆
积而成,因此无法避免的会出现台阶效应,使得成型件的表面与理论模型表面存在偏差。因而很好地解决了专利文献中所存在的叶片在制作过程中存在的无法同时满足成型效率和精度的要求的技术问题,使叶片在后续制造过程中能够有更快的效率与精度。
18.同时,本发明是对利用刀具切削进行对所有叶片同步进行加工,与公告号为cn108581397a专利文献相比,所加工出的叶片整体一致性好,加工效率更高。
19.2、本发明中,根据实际需求,水轮机转轮由叶片、上冠、下环组成,所述水轮机转轮增减材复合制造方法还包括制造上冠的步骤和制造下环的步骤。
20.3、本发明中,所述的转轮叶片是在上冠上直接采用增减材复合加工方式进行制造,然后将带有叶片的上冠与下环组焊形成整体转轮。这样的制造方式,相对于公告号为cn108581397a专利文献的方式单独制造叶片,其成型方式属于整体成型,去除了叶片和上冠装配和组焊的工序,避免了装配和焊接误差,整体一致性更好。
21.4、本发明中,所述的转轮叶片经增减材复合加工完成后,与制造好的上冠和下环分别组焊形成整体转轮,具有更广的适用性。
22.5、本发明中,所述先所述自适应分层切片是先对叶片模型进行倾斜度分析,再针对叶片模型成型方向倾斜度更大的区域采用较小层厚的切片,针对叶片模型成型方向倾斜度更小的区域采用较大层厚的切片,如下所述:在对三维模型进行切片处理时,需要将模型离散化生成二维数据轮廓,其中切片层厚h即每一层的厚度。由于增材制造是由每一层切片堆积而成,因此无法避免的会出现台阶效应,使得成型件的表面与理论模型表面存在偏差d,可得出公式如下:d=h
×ꢀ
cos θ理论上层厚h越大,加工效率越高,但台阶效应就越明显,实际成型表面和理论模型表面之间的偏差d就越大,表面更为粗糙。同时台阶效应也与模型表面和堆积平面的夹角θ有关,当层厚h保持一致时,偏差d与夹角θ成反比关系。
23.目前常规方式是采用定层厚切片,该技术以相同的层厚对模型分层,其算法较简单,但无法同时满足成型效率和精度的要求。因此针对叶片的不同部位,首先采用倾斜度分析,继而采用针对成型方向倾斜度更大的区域(如叶片出水边)采用较小层厚,以满足表面精度需求,同时降低加工风险,可有效避免较大的变形,反之则选择较大层厚,以提高加工效率。
24.层厚的选择与加工效率、精度呈反比关系,层厚越厚,加工效率越高,但精度越差,层厚越薄,加工效率低,但精度好。
25.本技术的这一点是专门针对水轮机叶片的需求,基于理论分析和实际经验而选定的技术,依靠对叶片倾斜度分析的标准来进行自适应分层,能综合效率和精度需求,得出最优解。
26.如某一案例中(仅作为参考)叶片总高165mm,设备可用的层厚范围为0.04
‑
0.2mm,通过对模型倾斜度分析,最上端叶片最为倾斜,因此最上端叶片加工风险最大,最终选定自适应分层,将整个叶片划分为区域1至区域4,各部分的层厚分别为0.2,0.12,0.06和0.04mm,最终每一个单叶片仅计算其增材时间为10小时,是综合了效率和成型精度,降低成型风险的最优结果。
27.若单叶片均选择层厚为0.2mm,其总共增材时间约为6小时,效率提升了一点,但加
工风险更大,同时由于层厚大,表面尺寸误差更大,后续需要更多的精加工处理;若单叶片均选择层厚为0.04mm,则需要近30个小时。
28.6、本发明中,通过基于倾斜度分析的自适应分层与实际需求结合所产生的需要设定的增材制造参数包括分层参数、加工速度、保护气体充盈、预热温度、高能束的能量大小、持续时间、运动轨迹划分、加工过程中的温度控制和保护气体控制。
29.7、本发明中,分层参数,即增材制造与减材制造的交换时机,即增材至设定好的层数与以下因素有关:(1)与刀具的有效且高效切削范围有关,如增材过厚,则单次的多轴联动切削将耗时过多,同时刀具需要更长,加工效果略差;(2)与增材的变形有关,对于较易产生变形的区域,应当增材至较少层数即减材,否则变形过大无法加工;(3)与效率有关,过于频繁的进行增减材,由于需更换主轴头、切削刀具,同时保证加工时的温度在一定范围,因此将使得暂停和间隙时间过多,加工效率低下。
30.8、本发明中,根据实际需求,所述高能束为激光束、电弧、等离子束或电子束的一种。
31.9、本发明中,在步骤c和步骤b中的任意两次相邻刀具切削进行加工的减材过程中设置有部分重叠区域,本发明采用增材与减材相循环的方式对叶片进行制造,减材过后的再次增材部分容易与上一次已减材部分产生出明显的分界面,通过在步骤c和步骤b中的任意两次相邻刀具切削进行加工的减材过程中设置部分重叠区域,以保证两次加工没有明显的分界面,同时保证叶片的光洁度与加工精度。
32.10、本发明中,所述叶片的增材过程采用多轴联动增材,由于叶片形状复杂,仅仅依靠三轴增材,将在部分区域需要添加支撑防止变形,刀具切削进行加工的方式采用多轴联动减材,由于叶片形状复杂,仅仅依靠三轴减材,有很多加工不到的区域,同时可以提高了生产效率,减少了材料切削浪费,提高加工精度,更利于叶片曲面的形成,保证叶片的光洁度。
33.本发明与授权公告号为cn107150208a专利文献为代表的现有技术相比,存在明显区别:虽然cn107150208a专利文件中有在成型的上冠上,采用电弧增材制造技术,其并未对叶片有分层次的减材工艺,而是通过后续抛光的方式来处理叶片,无法保证叶片的精密度和一致性,且cn107150208a专利文献用冷金属过渡的堆焊方式,将模型转轮数学模型导入计算机,通过软件完成叶片的切片与焊接路径规划,控制机器人系统完成叶片的增材制造,由于增材制造是由每一层切片堆积而成,因此无法避免的会出现台阶效应,使得成型件的表面与理论模型表面存在偏差,理论上层厚越大,加工效率越高,但台阶效应就越明显,实际成型表面和理论模型表面之间的偏差就越大,表面更为粗糙,制作过程中存在无法同时满足成型效率和精度的要求的技术问题,同时对于加大随后续材料的去除消耗,增加成本,且叶片完成之后,很可能由于间隙狭小,使得相邻叶片由于刀具干涉、或主轴干涉而无法减材。
34.同时,cn201882265u专利和本发明所达到的效果也不一样,该专利文献是使用电弧增材制造技术形成近净成型的叶片,最后再对上冠和叶片整体进行抛光,而本专利文献
采用自适应分层的方式,通过增减材复合制造,利用已加工好的上冠,无需后续抛光,削减的操作,同时由于叶片完成之后,很可能由于间隙狭小,使得相邻叶片由于刀具干涉、或主轴干涉而无法增减材,增材成型所有的叶片的同时对叶片进行同步减材切削,并对工艺过程有相应控制技术,可有效保证表面光洁度和尺寸精度,无论是对于叶片的处理还是整个转轮结构的而言,都更具有一致性和精密度,同时减少对多余材料的浪费。
35.因而本发明与该专利文件不论是从技术方案,还是所达到的技术效果上均存在明显区别。
附图说明
36.为了更清楚地说明本发明实施例的技术方案,下面将对实施例的附图作简单地介绍,显而易见地,下面描述中的附图仅仅涉及本发明的一些实施例,而非对本发明的限制。
37.图1为转轮传统结构示意图;图2为切片处理时,成型件的表面与理论模型表面存在偏差的示意图;图3为单叶片的自适应分层示意图;图4为转轮成型步骤前半段示意图;图5为转轮成型后半段步骤示意图;图6为转轮叶片成型步骤流程图。
38.图中标记:1、下环,2、叶片,3、上冠,4、实际成型表面,5、理论模型表面,6、成型方向,7、倾斜度高的区域,8、倾斜度小的区域,9、高能束头,10、切削刀具。
具体实施方式
39.为使本发明实施例的目的、技术方案和优点更加清楚,下面将结合本发明实施例的附图,对本发明实施例的技术方案进行清楚、完整地描述。
40.除非另外定义,本公开使用的技术术语或者科学术语应当为本公开所属领域内具有一般技能的人士所理解的通常意义。本公开中使用的“包括”或者“包含”等类似的词语意指出现该词前面的元件或者物件涵盖出现在该词后面列举的元件或者物件及其等同,而不排除其他元件或者物件。“上”、“下”、“左”、“右”等仅用于表示相对位置关系,当被描述对象的绝对位置改变后,则该相对位置关系也可能相应地改变。
41.下面结合附图和实施例对本发明进一步说明。
42.实施例1作为本发明的一个较佳实施方式,本发明包括转轮叶片的制造包括以下步骤:a、将叶片2模型按stl格式导入至增材设备,将叶片2模型按stl格式导入至增材设备,并对该模型进行采用自适应分层切片,先对叶片2模型进行倾斜度分析,再针对叶片2模型成型方向6倾斜度更大的区域采用较小层厚的切片,针对叶片2模型成型方向6倾斜度更小的区域采用较大层厚的切片,确定增材制造参数,设定增材制造参数完成;b、设定分层参数、加工速度、保护气体充盈、高能束的能量大小、持续时间、运动轨迹划分、加工过程中的温度控制和保护气体控制完成后,利用等离子束制造所有叶片2至设定好的层数;
c、增材所有叶片2至设定好的层数后,利用多轴数控加工刀具切削进行对所有叶片2同步进行加工,去除多余的余量,并修正叶片2变形,叶片2修正完成后,再次利用等离子束增材制造所有叶片2至下一设定的层数;d、循环上述增材所有叶片2至设定好的层数,利用刀具切削对所有叶片2同步进行加工,去除多余的余量,并修正叶片2完成变形的步骤,直至所有的叶片2整体完成并修正完成,直至所有的叶片2整体完成并修正完成;所述的转轮叶片2经增减材复合加工完成后,与制造好的上冠3和下环1分别组焊形成整体转轮。
43.实施例2作为本发明的最佳实施方式,参照说明书附图4和附图5,包括以下步骤:a、对转轮上冠3进行加工;b、将叶片2模型按stl格式导入至增材设备,将叶片2模型按stl格式导入至增材设备,并对该模型进行采用自适应分层切片,先对叶片2模型进行倾斜度分析,再针对叶片2模型成型方向6倾斜度更大的区域采用较小层厚的切片,针对叶片2模型成型方向6倾斜度更小的区域采用较大层厚的切片,确定增材制造参数,设定增材制造参数完成;c、设定分层参数、加工速度、保护气体充盈、高能束的能量大小、持续时间、运动轨迹划分、加工过程中的温度控制和保护气体控制完成后,通过多轴联动增材的方式利用电子束于转轮上冠3上直接同步制造所有的叶片2至设定好的层数;d、多轴联动增材所有的叶片2至设定好的层数后,利用多轴数控加工刀具切削对所有叶片2同步进行多轴联动减材加工,去除多余的余量,保证光洁度至一定要求,并修正叶片2变形叶片2修正完成后,再次利用电子束多轴联动增材制造所有叶片2至下一设定的层数;e、循环上述增材所有叶片2至设定好的层数,利用刀具切削对所有叶片2同步进行加工,去除多余的余量,并修正叶片2完成变形的步骤,直至所有的叶片2整体完成并修正完成,上述步骤中每两次相邻刀具切削进行加工的减材过程中设置有部分重叠区域,直至所有的叶片2整体完成并修正完成;f、与加工后的下环1装配和组焊形成整体转轮。
44.实施例3作为本发明的另一较佳实施例,包括以下步骤:a、对转轮上冠3进行加工;b、将叶片2模型按stl格式导入至增材设备,并对该模型利用stl模型中的三角面片三个顶点的三维坐标以及其单位法向量数据作为判定特征,及先采用最大分层厚度对stl模型进行切片,然后查找与当前切片层中所有相交的三角形面片的特征三角面片作为本层的表征三角面片,然后通过“尖端高度方法”来判定是否需要再次细分的层厚,同时再判定当前层是否含有特征面,特征线,以及特征点,如果有,则以最小的分层高度对当前层进行再次细分的自适应分层对叶片2进行切片,确定增材制造参数,设定增材制造参数完成;c、设定激光功率、扫描速度、扫描间距、扫描路径、保护气体控制完成后,通过多轴联动增材的方式利用激光于转轮上冠3上直接同步制造所有的叶片2至设定好的层数;
d、多轴联动增材所有的叶片2至设定好的层数后,利用多轴数控加工使用刀具切削对所有叶片2同步进行多轴联动减材加工,去除多余的余量,保证光洁度至一定要求,并修正叶片2变形叶片2修正完成后,再次利用激光多轴联动增材制造所有叶片2至下一设定的层数;e、循环上述增材所有叶片2至设定好的层数,利用刀具切削对所有叶片2同步进行加工,去除多余的余量,并修正叶片2完成变形的步骤,直至所有的叶片2整体完成并修正完成,直至所有的叶片2整体完成并修正完成;f、与加工后的下环1装配和组焊形成整体转轮。
45.实施例4作为本发明的又一较佳实施方式,参照说明书附图6,包括以下步骤:a、对转轮上冠3进行加工;b、将叶片2模型按stl格式导入至增材设备,将叶片2模型按stl格式导入至增材设备,并对该模型进行采用自适应分层切片,先对叶片2模型进行倾斜度分析,再针对叶片2模型成型方向6倾斜度更大的区域采用较小层厚的切片,针对叶片2模型成型方向6倾斜度更小的区域采用较大层厚的切片,确定增材制造参数,设定增材制造参数完成;c、设定分层参数、加工速度、保护气体充盈、高能束的能量大小、持续时间、运动轨迹划分、加工过程中的温度控制和保护气体控制完成后,通过三轴联动增材的方式利用等离子束于转轮上冠3上直接同步制造所有的叶片2至设定好的层数;d、三轴联动增材所有的叶片2至设定好的层数后,利用三轴立式加工使用刀具切削对所有叶片2同步进行三轴联动减材加工,去除多余的余量,保证光洁度至一定要求,并修正叶片2变形叶片2修正完成后,再次利用等离子束三轴联动增材制造所有叶片2至下一设定的层数;e、循环上述增材所有叶片2至设定好的层数,利用刀具切削对所有叶片2同步进行加工,去除多余的余量,并修正叶片2完成变形的步骤,直至所有的叶片2整体完成并修正完成,上述步骤中每两次相邻刀具切削进行加工的减材过程中设置有部分重叠区域,直至所有的叶片2整体完成并修正完成;f、与加工后的下环1装配和组焊形成整体转轮。
46.以上所述,仅是本发明的较佳实施例而已,并非对本发明作任何形式上的限制,虽然本发明已以较佳实施例揭露如上,然而并非用以限定本发明,任何熟悉本专业的技术人员,在不脱离本发明技术方案范围内,当可利用上述揭示的技术内容作出些许更动或修饰为等同变化的等效实施例,但凡是未脱离本发明技术方案的内容,依据本发明的技术实质对以上实施例所作的任何简单修改、等同变化与修饰,均仍属于本发明技术方案的范围内。