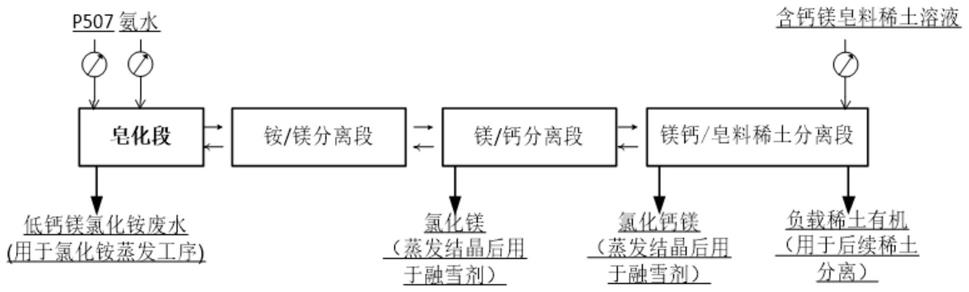
1.本发明属于稀土湿法冶金萃取技术领域,具体涉及一种萃取法去除含钙镁皂料稀土溶液中钙镁离子并提纯钙镁的方法。
背景技术:2.稀土资源在湿法冶炼过程中产生大量的高盐、高氨氮废水,应国家稀土产业环保政策的要求,企业必须对稀土冶炼废水达标处理以保护环境,实现稀土产业的绿色发展、可持续发展。对于稀土湿法冶炼过程中产生的氯化铵废水一般分为两类,一类是氯化稀土碳铵沉淀过程产生的沉淀废水,其特点是废水氨氮浓度低、杂质含量低。另一类为氯化稀土在氯化物体系下氨皂化萃取(稀土萃取分离线)产生的皂化废水,现有氯化稀土在氯化物体系下的氨皂化萃取工艺为:将p507有机相与工业氨水进行皂化反应,得到皂化率为0.30~0.36的皂化有机相,设置多级萃取,将皂化有机相作为初级萃取的起始有机相,以含钙镁皂料稀土溶液为末级萃取的初始水相,每一级萃取之后的有机相均用作下一级的有机相,每一级萃取后的水相均用作上一级的水相,即有机相往后传、水相向前走的过程,最后有机相在末级萃取转出用作稀土萃取生产线的负载有机,水相在首级萃取后转出,即为氯化铵废水,该废水主的特点是废水氨氮浓度较高,但同时钙、镁等杂质也较高,废水处理难度大。
3.氯化铵废水的处理工艺大多数稀土企业采用mvr+三效蒸发技术。对于上述沉淀产生的氯化铵废水由于钙、镁杂质含量较低可直接进行处理,但对于萃取产生的氯化铵废水由于其受稀土分离原料纯度影响钙、镁杂质含量偏高,在实际生产运行过程中容易导致蒸发器堵塞,需设置钙、镁去除工序来避免结垢,通常采用的除钙、镁方法为草酸沉淀法和碳酸氢铵沉淀法。该方法由于消耗大量化学试剂、除钙工序产生大量固废以及工序繁琐导致生产成本偏高。
4.为了去除钙镁,也有技术在废水处理阶段再进行萃取操作的尝试,如公开号为cn105461002a、专利申请名称为一种稀土工业废水中去除钙镁的方法的专利申请中,记载的技术方案为“以稀土酸法冶炼工艺产生的硫酸铵废水为处理对象,以50%体积比的p507加上50%体积比的磺化煤油作为有机萃取剂,在有机相与液相体积比为1~2,皂化率为45%~60%的条件下进行萃取,萃取后静置分层即可”,该方法以硫酸铵废水为处理对象,对稀土酸法冶炼工艺产生的硫酸铵废水采取了再萃取的方案,但该方法也存在明显的技术缺陷:再次使用皂化p507进行萃取,在皂化阶段工艺成本较高,仅能在实验室中存在,大规模应用在经济价值上很难取舍,另萃取过程同样存在钙在萃取剂中富集的状况,如果萃取生产线中没有可选择的钙出口或有效的钙解离手段会容易导致钙富集,当钙在系统内到一定程度时将从生产线的前段水相出口溢出,导致除钙效果下降,固难以推广使用。
5.因此,针对上述氯化铵废水难处理的问题,除了研究如何处理废水,还有必要在前期废水产生阶段改善废水水况,从根本上根除氯化铵废水难治理的问题。
技术实现要素:6.本发明的目的在于提供一种萃取法去除含钙镁皂料稀土溶液中钙镁离子并提纯钙镁的方法,用以解决现有氯化稀土在氯化物体系下氨皂化萃取产生的皂化废水难以处理的技术问题。
7.为实现上述目的,本发明采用的技术方案如下:
8.一种萃取法去除含钙镁皂料稀土溶液中钙镁离子并提纯钙镁的方法,该方法设置多级萃取,将氨皂化p507有机相作为初级萃取的起始有机相,以含钙镁皂料稀土溶液为末级萃取的初始水相,每一级萃取之后的有机相均用作下一级的有机相,每一级萃取后的水相均用作上一级的水相,所述多级萃取前还包括皂化控制段,多级萃取由铵/镁分离控制段、镁/钙分离控制段以及镁钙/皂料稀土分离控制段前后3个分离段组成;所述铵/镁分离控制段的首级出口水相与皂化控制段的皂化废水汇合从皂化控制段排水口排出;所述镁/钙分离控制段的首级出水相一部分排出,用于蒸发结晶后制作融雪剂,一部分用作上一级的水相;所述镁钙/皂料稀土分离控制段的首级出水相一部分排出,用于蒸发结晶后制作融雪剂,一部分用作上一级的水相,镁钙/皂料稀土分离控制段的末级有机相转出用作稀土萃取生产线的负载有机。
9.本发明的原理是利用铵离子与镁离子、钙离子和稀土离子在萃取剂中的萃取平衡差异来实现p507
‑
hcl体系下铵/镁/钙/皂料稀土的分离,使得产生的稀土皂废水钙、镁离子均满足废水处理要求以及元素钙镁的富集与纯化,有效实现原子的经济性。
10.作为优选地,所述铵/镁分离控制段至少设置3级。
11.作为优选地,所述镁/钙分离控制段至少设置4级。
12.作为优选地,所述镁钙/皂料稀土分离控制段至少设置4级。
13.作为优选地,述氨皂化p507有机相为p507与磺化煤油混合配置后经工业氨水皂化后充分澄清而成,皂化度为30%~36%。
14.进一步地,所述工业氨水的浓度为6.0~6.5mol/l。
15.作为优选地,所述作为初始水相的含钙镁皂料稀土溶液,相关元素浓度分别为:ca
2+
离子浓度为4~5g/l、mg
2+
离子浓度为2.5~3g/l、nh
4+
离子浓度不大于0.005g/l、稀土浓度为250~300g/l。
16.进一步地,所述镁钙/皂料稀土分离控制段第一级的水相相关元素浓度分别为:ca
2+
离子浓度为4~5g/l、mg
2+
离子浓度为2.5~3.0g/l、nh
4+
不大于0.01g/l、稀土浓度不大于0.1g/l。
17.更进一步地,所述镁/钙分离控制段第一级的水相相关元素浓度分别为:ca
2+
离子浓度为不大于0.01g/l、mg
2+
离子浓度为2.0~2.5g/l、nh
4+
离子浓度为不大于0.015g/l、稀土浓度为不大于0.01g/l。
18.更优地,所述铵/镁分离控制段第一级的水相相关元素浓度分别为:ca
2+
离子浓度不大于0.005g/l、mg
2+
离子浓度不大于0.005g/ll、nh
4+
离子浓度为150~160g/l、稀土浓度为不大于0.005g/l。
19.与现有技术相比,本发明具有以下有益效果:
20.(1)本发明通过耦合现有萃取生产线工艺,增加原有皂化稀土皂段功能,在不额外消耗其他化学试剂的同时实现传统有机相皂化和负载稀土有机相制备,利用产线现有的分
离功来分离去除整条分离线多余的钙镁离子并生产由氯化镁和氯化钙镁组成的融雪剂;该方法省去废水处理过程沉淀法除钙镁工序,无需引入其他试剂对废液进行前处理,能有效解决传统沉淀法除钙镁生产成本高的现状,提纯的氯化镁和氯化钙镁可作为产品外销来实现废渣的减量化和资源化,有效提高原子的经济性,去除钙、镁的氯化铵废水中可有效避免废水处理过程中设备堵塞严重的问题;
21.(2)本发明相较于传统的转型分离线工艺,在原有实际消耗的基础上,无其他试剂的添加,仅增加萃取级数,在试剂“零消耗”的前提下减轻了废水处理的难度,将废水处理的部分工作前置,同时合并皂化工段的废水,得到氨含量更高的废水,便于蒸发结晶处理。
附图说明
22.图1为本发明的工艺流程示意图。
具体实施方式
23.如图1为本发明的工艺流程示意图,下面结合附图以及各实施例对本发明作进一步说明,本发明的方式包括但不仅限于以下实施例。
24.实施例1
25.p507有机相为p507与磺化煤油按照一定体积比配置的溶液,其中p507的浓度为1.0mol/l。
26.皂化剂氨水为液氨与纯水按照一定比列配置的溶液,其中氨水的浓度为6.0mol/l。
27.待处理的含钙镁皂料稀土溶液,相关元素浓度分别为:ca
2+
离子浓度为4.26g/l、mg
2+
离子浓度为2.51g/l、nh
4+
离子浓度为0.004g/l、稀土浓度为274.85g/l。
28.按照原始稀土萃取分离线处理后,产生的含钙、镁离子的氯化铵废水的相关元素浓度分别为:ca
2+
=4.15g/l、mg
2+
=2.44g/l、nh4cl=154g/l。
29.按照本实施例的处理方法,具体如下:
30.步骤1,皂化控制段:控制p507有机相的皂化率为0.30,将p507有机相与工业氨水按照皂化率要求加入皂化段混合澄清器1级,步骤2之铵/镁分离控制段1级的平衡水相从该段2级进入皂化控制段的废水中,皂化控制段第1级汇集所有废水,出口水相为达到废水钙、镁含量要求的氯化铵废水,皂化控制段2级出口有机相为铵皂化p507有机相。获得的铵皂化p507有机相用作步骤2铵/镁分离控制段的萃取有机相。所产生的废水为钙、镁离子均满足废水处理要求的氯化铵溶液,可直接用于废水蒸发系统回收氯化铵,回收的氯化铵可作为农用化肥销售。
31.步骤2,铵/镁分离控制段:以步骤1之皂化控制段第2级获得的铵皂化p507有机相为平衡负载,步骤3镁/钙分离段1级获得的平衡水相为洗液。步骤3之镁/钙分离控制段的平衡水相从该段最后1级进入铵/镁分离段。从铵/镁分离控制段第1级出口水相获得钙镁目标纯度满足后续废水处理指标的氯化铵溶液进入步骤1与皂化控制段皂化废水汇合;从铵/镁分离控制段第3级出口有机相获得负载镁的p507有机相为步骤3镁/钙分离控制段提供分离功。
32.步骤3,镁/钙分离控制段:以步骤2铵/镁分离控制段3级获得的含镁的负载p507有
机相为平衡负载,步骤4之镁钙/皂料稀土分离控制段的平衡水相从最后1级进入镁/钙分离段。镁/钙分离控制段第1级出口的部分水相获得的氯化镁溶液,该溶液部分引出后经浓缩处理可作为产品外销,部分根据前段工段铵离子浓度、体积计算用量,用于步骤2之铵/镁分离控制段的洗液;从镁/钙分离控制段4级出口有机相获得负载镁钙的p507有机相为步骤4镁/钙控制分离段提供分离功。
33.步骤4,镁钙/皂料稀土分离控制段:以步骤3镁/钙分离控制段4级获得的含镁钙负载p507有机相为平衡负载,稀土萃取生产线萃取段的平衡水相(萃余液)从最后1级进镁钙/稀土分离控制段。镁钙/稀土分离控制段第1级出口水相获得分离铵/稀土后达到一定纯度的氯化钙镁溶液,该溶液部分引出后经浓缩处理可作为融雪剂外销,部分根据前段工段铵离子浓度、体积计算用量,用于步骤3之镁/钙分离控制段的洗液;从镁钙/稀土分离段第5级出口有机相获得负载皂料稀土的p507有机相用作稀土萃取生产线的负载有机进入分离段。
34.按照本实施例操作处理净化后的氯化铵废水中的相关元素浓度分别为:ca
2+
=0.0038g/l、mg
2+
=0.0034g/l、nh4cl≈153.51g/l,相较于原始稀土萃取分离线处理,实施例萃取得到的废水镁钙离子大大降低。
35.氯化镁废水中的相关元素浓度分别为:nh
4+
=0.013g/l、ca
2+
=0.0087g/l。
36.氯化钙镁废水中的相关元素浓度分别为:nh
4+
=0.047g/l、re0=0.053g/l。
37.实施例2
38.p507有机相为p507与磺化煤油按照一定体积比配置的溶液,其中p507的浓度为1.5mol/l。
39.皂化剂氨水为液氨与纯水按照一定比列配置的溶液,其中氨水浓度为6.5mol/l。
40.待处理的含钙镁皂料稀土溶液,相关元素浓度分别为:ca
2+
离子浓度为4.87g/l、mg
2+
离子浓度为2.74g/l、nh
4+
离子浓度为0、稀土浓度为285g/l。
41.原始稀土萃取分离线产生的含钙、镁离子的氯化铵废水的相关元素浓度分别为:ca
2+
=4.15g/l、mg
2+
=2.74g/l、nh4cl=157g/l。
42.步骤1,皂化控制段:控制p507有机相的皂化率为0.36,将p507有机相与工业氨水按照皂化率要求加入皂化段混合澄清器1级,步骤2之铵/镁分离控制段1级的平衡水相从该段2级进入皂化控制段的废水中,皂化控制段第1级汇集所有废水,出口水相为达到废水钙、镁含量要求的氯化铵废水,皂化控制段2级出口有机相为铵皂化p507有机相。获得的铵皂化p507有机相用作步骤2铵/镁分离控制段的萃取有机相。所产生的废水为钙、镁离子均满足废水处理要求的氯化铵溶液,可直接用于废水蒸发系统回收氯化铵,回收的氯化铵可作为农用化肥销售。
43.步骤2,铵/镁分离控制段:以步骤1之皂化控制段第2级获得的铵皂化p507有机相为平衡负载,步骤3镁/钙分离控制段1级获得的平衡水相为洗液。步骤3之镁/钙分离控制段的平衡水相从该段最后1级进入铵/镁分离段。从铵/镁分离控制段第1级出口水相获得钙镁目标纯度满足后续废水处理指标的氯化铵溶液进入步骤1与皂化控制段皂化废水汇合;从铵/镁分离控制段第3级出口有机相获得负载镁的p507有机相为步骤3镁/钙分离控制段提供分离功。
44.步骤3,镁/钙分离控制段:以步骤2铵/镁分离控制段3级获得的含镁的负载p507有机相为平衡负载,步骤4之镁钙/皂料稀土分离控制段的平衡水相从最后1级进入镁/钙分离
段。镁/钙分离控制段第1级出口的部分水相获得的氯化镁溶液,该溶液部分引出后经浓缩处理可作为产品外销,部分根据前段工段铵离子浓度、体积计算用量,用于步骤2之铵/镁分离控制段的洗液;从镁/钙分离控制段4级出口有机相获得负载镁钙的p507有机相为步骤4镁/钙控制分离段提供分离功。
45.步骤4,镁钙/皂料稀土分离段:以步骤3镁/钙分离控制段4级获得的含镁钙负载p507有机相为平衡负载,稀土萃取生产线萃取段的平衡水相(萃余液)从最后1级进镁钙/稀土分离控制段。镁钙/稀土分离控制段第1级出口水相获得分离铵/稀土后达到一定纯度的氯化钙镁溶液,该溶液部分引出后经浓缩处理可作为融雪剂外销,部分根据前段工段铵离子浓度、体积计算用量,用于步骤3之镁/钙分离控制段的洗液;从镁钙/稀土分离段第5级出口有机相获得负载皂料稀土的p507有机相用作稀土萃取生产线的负载有机进入分离段。
46.按照本实施例操作处理净化后的氯化铵废水中的相关元素浓度分别为:ca
2+
=0.0038g/l、mg
2+
=0.0034g/l、nh4cl≈156.51g/l,相较于原始稀土萃取分离线处理,实施例萃取得到的废水镁钙离子大大降低。
47.氯化镁废水中的相关元素浓度分别为:nh
4+
=0.013g/l、ca
2+
=0.0087g/l。
48.氯化钙镁废水中的相关元素浓度分别为:nh
4+
=0.047g/l、re0=0.053g/l。
49.实施例3
50.p507有机相为p507与磺化煤油按照一定体积比配置的溶液,其中p507的浓度为1.5mol/l。
51.皂化剂氨水为液氨与纯水按照一定比列配置的溶液,其中氨水的浓度为6.5mol/l。
52.待处理的含钙镁皂料稀土溶液,相关元素浓度分别为:ca
2+
离子浓度为4.87g/l、mg
2+
离子浓度为2.91g/l、nh
4+
离子浓度为0.0042、稀土浓度为296.49g/l,
53.原始稀土萃取分离线产生的含钙、镁离子的氯化铵废水的相关元素浓度分别为:ca
2+
=4.93g/l、mg
2+
=2.84g/l、nh4cl=157.32g/l。
54.步骤1,皂化控制段:控制p507有机相的皂化率为0.36,将p507有机相与工业氨水按照皂化率要求加入皂化段混合澄清器1级,步骤2之铵/镁分离控制段1级的平衡水相从该段2级进入皂化控制段的废水中,皂化控制段第1级汇集所有废水,口水相为达到废水钙、镁含量要求的氯化铵废水,皂化控制段3级出口有机相为铵皂化p507有机相。获得的铵皂化p507有机相用作步骤2铵/镁分离控制段的萃取有机相。所产生的废水为钙、镁离子均满足废水处理要求的氯化铵溶液,可直接用于废水蒸发系统回收氯化铵,回收的氯化铵可作为农用化肥销售。
55.步骤2,铵/镁分离段:以步骤1之皂化控制段第3级获得的铵皂化p507有机相为平衡负载,步骤3镁/钙分离控制段1级获得的平衡水相为洗液。步骤3之镁/钙分离控制段的平衡水相从该段最后1级进入铵/镁分离段。从铵/镁分离控制段第1级出口水相获得钙镁目标纯度满足后续废水处理指标的氯化铵溶液进入步骤1与皂化控制段皂化废水汇合;从铵/镁分离控制段第4级出口有机相获得负载镁的p507有机相为步骤3镁/钙分离控制段提供分离功。
56.步骤3,镁/钙分离段:以步骤2铵/镁分离控制段4级获得的含镁的负载p507有机相为平衡负载,步骤4之镁钙/皂料稀土分离控制段的平衡水相从最后1级进入镁/钙分离段。
镁/镁/钙分离控制段第1级出口的部分水相获得的氯化镁溶液,该溶液部分引出后经浓缩处理可作为产品外销,部分根据前段工段铵离子浓度、体积计算用量,用于步骤2之铵/镁分离控制段的洗液;从镁/钙分离控制段5级出口有机相获得负载镁钙的p507有机相为步骤4镁/钙控制分离段提供分离功。
57.步骤4,镁钙/皂料稀土分离控制段:以步骤3镁/钙分离控制段4级获得的含镁钙负载p507有机相为平衡负载,稀土萃取生产线萃取段的平衡水相(萃余液)从最后1级进镁钙/稀土分离控制段。镁钙/稀土分离控制段第1级出口水相获得分离铵/稀土后达到一定纯度的氯化钙镁溶液,该溶液部分引出后经浓缩处理可作为融雪剂外销,部分根据前段工段铵离子浓度、体积计算用量,用于步骤3之镁/钙分离控制段的洗液;从镁钙/稀土分离段第6级出口有机相获得负载皂料稀土的p507有机相用作稀土萃取生产线的负载有机进入分离段。
58.按照本实施例操作处理净化后的氯化铵废水中的相关元素浓度分别为:ca
2+
=0.0021g/l、mg
2+
=0.0024g/l、nh4cl≈158.51g/l,相较于原始稀土萃取分离线处理,实施例萃取得到的废水镁钙离子大大降低。
59.氯化镁废水中的相关元素浓度分别为:nh
4+
=0.011g/l、ca
2+
=0.0064g/l。
60.氯化钙镁废水中的相关元素浓度分别为:nh
4+
=0.032g/l、re0=0.021g/l。
61.上述实施例仅为本发明的优选实施方式之一,不应当用于限制本发明的保护范围,但凡在本发明的主体设计思想和精神上作出的毫无实质意义的改动或润色,其所解决的技术问题仍然与本发明一致的,均应当包含在本发明的保护范围之内。