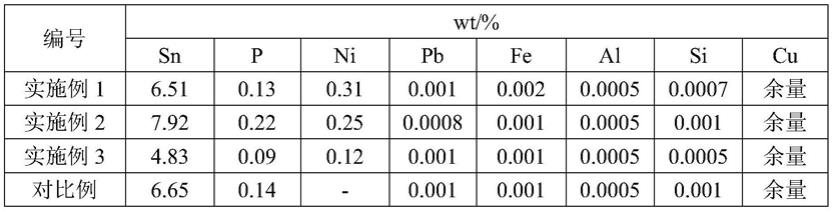
1.本发明属于铜合金技术领域,具体涉及一种耐腐蚀锡磷青铜线材的制备方法。
背景技术:2.锡磷青铜一种以sn和p作为主要合金元素的青铜,一般含有0.4~9%sn,0.1~0.4%p,余量为cu。国标中的合金牌号主要有qsn4-0.3、qsn6.5-0.1、qsn8-0.3等10余种,锡磷青铜在工业上主要用精密弹簧、电气连接件、接线端子等。
3.锡磷青铜线材规格一般在φ0.4-10mm,常规的生产工艺路线:水平连铸
→
过道拉伸
→
中间退火
→
酸洗
→
成品拉伸。刚经过模具拉伸生产的锡磷青铜线材表面光亮,有美丽的金属光泽,但常规方法生产的锡磷青铜线材在生产、储存以及使用过程中,因大气中含有n2o、so2、nh3、h2s等微量腐蚀性气体,对铜合金都会产生腐蚀,而且它们与湿度、其他腐蚀性物质共同作用,加速锡磷青铜的腐蚀变色。此外,因为人体汗液的成分有nh4cl、nacl等,人体皮肤接触到没有防护的产品表面,也会对锡磷青铜表面产生腐蚀,腐蚀会导致表面变色,影响产品的美观度和使用性能。而导致腐蚀变色的最主要影响因素是常规方法生产锡磷青铜的晶粒度粗大,粗晶粒拉伸后线材表面粗糙度也大,表面粗糙度越大,放大镜下观察线材表面凹凸不平现象越严重,腐蚀性物质易藏匿在凹凸不平的表面,从而造成锡磷青铜易腐蚀变色。
技术实现要素:4.本发明所要解决的技术问题是提供一种晶粒细小且表面粗糙度小的耐腐蚀锡磷青铜线材的制备方法。
5.本发明解决上述技术问题所采用的技术方案为:一种耐腐蚀锡磷青铜线材的制备方法,其特征在于:该锡磷青铜的质量百分比组成为,sn:2~10%,p:0.08~0.3%,ni:0.1~0.5%,pb≤0.005%,fe≤0.005%,al≤0.002%,si≤0.002%,余量为cu和不可避免的杂质;该锡磷青铜线材的工艺流程包括:熔炼
→
铸造
→
剥皮
→
中间拉伸
→
退火
→
成品拉伸,所述铸造时,铜水由结晶器从保温炉内水平连续引出,铸造温度1000~1200℃,冷却水进水温度:25~35℃,出水温度:32~45℃,牵引工艺采用“拉伸—停顿—反推—停顿”牵引动作,牵引参数:牵引速度0.2~1.8m/min,拉坯长度1~30mm、拉伸时间0.05~0.5s、拉停时间0.02~0.5s、反推长度0.1~3mm、反推时间0.02~0.5s,推停时间:0.02~0.5s。
6.锡磷青铜中的p含量一般不超过0.45%,超过这个值,会引起热脆,当p含量>0.3%时,组织中会出现cu3p共晶体,cu3p作为第二相颗粒会降低锡磷青铜的耐腐蚀性能。当锡磷青铜中p残留量低于0.08%以下时,脱氧除气的效果变差,熔体中会出现金属氧化物的颗粒以及气体,凝固后,细小的金属氧化物以夹杂物形成存在于合金中,气体则形成气孔,金属氧化物在金属拉伸变形过程中脱落,线材表面留下凹坑,气孔在线材加工变形过程破裂形成起皮现象,线材表面缺陷容易藏污纳垢,容易被腐蚀。因此,本发明锡磷青铜合金中p含量应控制在0.08~0.3%。
7.ni在cu中可以无限互溶,ni能显著提高cu的耐腐蚀性能,但ni加入量高,会造成原料成本的上升,ni加入量不超过0.5%。
8.fe常温下在铜中的固溶度极低,几乎不溶于cu,因此微量的fe在锡磷青铜中以质点形式存在,起到细化晶粒的作用,但由于fe质点耐蚀性很差,容易最先产生锈蚀,所以本发明锡磷青铜的fe含量必须严格控制在0.005%以下。
9.pb不溶于cu中,以呈黑色质点分布于枝晶之间和晶界上,降低锡磷青铜的耐腐蚀性,pb在本发明锡磷青铜合金含量越低越好,不宜超过0.005%。
10.al、si在锡青铜中的含量均不能超过0.002%,因为这两种元素的易与o形成氧化物,以坚硬的小质点形式存在合金基体中,线材在拉伸变形过程中从基体中脱落形成小坑。
11.作为优选,所述剥皮前先将铸坯拉伸,加工率控制在10~30%,拉伸后毛坯的椭圆度控制在≤0.03mm。剥皮前先将铸坯拉伸一是提高铸坯硬度,避免铸坯硬度软而造成剥皮时啃刀,啃刀会造成坯料表面出现破皮缺损,破损处容易藏污纳垢,是最容易产生腐蚀的地方;二是减小铸坯外圆的椭圆度,剥皮前毛坯的椭圆度控制在≤0.03mm,如果毛坯椭圆度过大,会造成剥皮厚度不均匀,影响剥皮效果,严重时甚至会出现剥不干净的情况。
12.作为优选,所述退火的温度区间420~480℃,升温时间:20~40min,保温时间2.5~4h,升温段保护气体流量12-18m3/h,保温段保护气体流量:10-15m3/h,保护性气体压力:75-85mbar;所述保护性气体为n2和h2的混合气体,h2体积占比≥75%,o2体积占比≤1ppm,残氨≤2ppm。退火温度对再结晶晶粒大小起主导作用,快速升温、较低退火温度、适当延长保温时间的退火工艺有利于获得晶粒度细小均匀的再结晶组织,细晶粒线坯拉伸后表面光洁度高,不容易氧化。
13.作为优选,所述中间拉伸和成品拉伸通过多模连续拉丝机拉细,模具数量1~12只,拉伸速度:1~5m/s,拉伸时线材采用乳化液进行润滑和冷却。乳化液主要作用是润滑、防止铜线氧化作用,同时带走所拉丝过程产生的热量,起到冷却的作用。
14.作为优选,所述乳化液的质量百分比浓度控制在3.5~4.5%,乳化液ph值控制在7.0~7.6,乳化液温度控制在25~35℃。乳化液的浓度控制要求润滑性能良好,浓度太低,润滑效果差,铜线表面与模具摩擦力大,表面光洁度差;乳化液浓度过高,会造成拉伸打滑,影响线材表面质量,本发明产品拉伸乳化液浓度要求控制在3.5~4.5%;ph值低于7,乳化液呈酸性,会加速铜线表面的腐蚀;ph值过高,大于7.6,乳化液会产生析皂现象,乳化液性能下降。乳化液温度应控制在25~35℃,过高会使乳化液稳定性变差,过低会使润滑性能变差。
15.作为优选,所述乳化液的质量百分比组成为,植物油:60~70%,表面活性剂:2~3%,尿素:1.0~2%,抗氧化剂:0.01~0.05%,椰子油二乙醇酰胺:2~3%,乳化剂:1~3%,苯骈三氮唑:2~5%,余量为水。本技术乳化液添加了表面活性剂和乳化剂,改善了乳化液的润滑性能,表面活性剂对各类油污清洗能力洗较强,使线材表面更洁净,添加的抗氧化剂增强线材表面抵抗空气氧化变色的能力。
16.作为优选,该磷青铜线材的平均晶粒度5~10μm,表面粗糙度ra≤0.05μm。
17.与现有技术相比,本发明的优点在于:本发明对锡磷青铜线材的化学成分进行改进,铸造工艺上通过高频率拉伸,铜水结晶时受到震动破碎枝晶的作用明显,枝晶间距<20μm,获得了铸态组织致密、晶内偏析小的铸坯,为后续获得晶粒细小的线坯奠定了基础。该
磷青铜线材的平均晶粒度5~10μm,表面粗糙度ra≤0.05μm,提高了锡磷青铜线材的耐腐蚀性,满足市场对线材耐腐蚀性能的高要求。
附图说明
18.图1为本发明实施例1的金相组织照片。
19.图2为本发明对比例的金相组织照片。
具体实施方式
20.以下结合附图实施例对本发明作进一步详细描述。
21.本发明提供3个实施例和1个对比例,合金成分见表1。
22.实施例所用乳化液中,表面活性剂为水山梨醇油酸酯,乳化剂为基酚聚氧乙烯醚,抗氧化剂为叔丁基对苯二酚,具体成分见表2。
23.实施例1:
24.一种规格为φ4mm耐腐蚀锡磷青铜线材制备方法以下:
25.1)熔炼:按照所需成分进行配料,然后在熔炼炉中进行熔炼,熔炼温度为1100~1160℃,待全部金属熔化后,化验成分合格后保温;
26.2)铸造:铜水由结晶器从保温炉内水平连续引出,铸坯规格φ10mm,铸造温度1160~1190℃,冷却水进水温度:28℃,出水温度:35℃,牵引工艺采用“拉伸—停顿—反推—停顿”牵引动作,牵引参数:牵引速度1.45m/min,拉坯长度16mm、拉伸时间0.18s、拉停时间0.25s、反推长度2mm、反推时间0.12s、推停时间:1s;
27.3)剥皮:φ10mm铸坯先一道次拉伸至φ9mm,加工率19.0%,φ9mm线坯椭圆度0.02mm,剥皮总厚度为0.5mm,剥皮后线径为φ8.5;
28.4)中间拉伸:剥皮后的φ8.5线坯通过多模连续拉丝机连拉至φ6mm,模具数量5只,拉伸速度:2m/s,拉伸采用乳化液进行润滑和冷却;
29.5)退火:φ6mm硬态线坯在光亮退火炉里进行无氧化退火,退火温度450℃,升温时间30min,保温时间180min,升温段保护气体流量15m3/h,保温段保护气体流量:13m3/h,保护性气体压力:80mbar;保护性气体为n2和h2的混合气体,h2体积占比80%,o2体积占比≤1ppm,残氨≤2ppm,余量为n2;
30.6)成品拉伸:退火后的φ6mm线坯通过多模连续拉丝机拉伸至φ4mm成品规格,模具数量7只,模具材质为cd聚晶模,拉伸速度:3m/s,拉伸采用乳化液进行润滑和冷却;拉伸完成后,操作人员穿戴干净纱手套,用透明塑料薄膜将产品进行封装。
31.7)检验包装入库:成品线材表面采用40x放大镜进行表面检测,无起皮、丝流、凹坑等缺陷,检验合格后包装入库,库房的温度:20℃,相对湿度33%。
32.本实施例中,乳化液质量百分比浓度为3.8%,ph值7.3,乳化液温度:29℃。
33.实施例2:
34.一种规格为φ5.8mm耐腐蚀锡磷青铜线材制备方法以下:
35.1)熔炼:按照所需成分进行配料,然后在熔炼炉中进行熔炼,熔炼温度为1100~1160℃,待全部金属熔化后,化验成分合格后保温;
36.2)铸造:铜水由结晶器从保温炉内水平连续引出,铸坯规格φ12mm,铸造温度1170
~1200℃,冷却水进水温度:30℃,出水温度:38℃,牵引工艺采用“拉伸—停顿—反推—停顿”牵引动作,牵引参数:牵引速度1.25m/min,拉坯长度12mm、拉伸时间0.20s、拉停时间0.30s、反推长度0.2mm、反推时间0.1s,推停时间:0.12s;
37.3)剥皮:φ12mm铸坯先一道次拉伸至φ10.5mm,加工率23.4%,φ10.5线坯椭圆度0.03mm,剥皮总厚度为0.5mm,剥皮后线径为φ10.0mm;
38.4)中间拉伸:剥皮后的φ10.0线坯通过多模连续拉丝机连拉至φ8mm,模具数量4只,拉伸速度:2m/s,拉伸采用乳化液进行润滑和冷却;
39.5)退火:φ8mm硬态线坯在光亮退火炉里进行无氧化退火,退火温度460℃,升温时间30min,保温时间180min,升温段保护气体流量12m3/h,保温段保护气体流量:12m3/h,保护性气体压力:75mbar;保护性气体为n2和h2的混合气体,h2体积占比80%,o2体积占比≤1ppm,残氨≤2ppm,余量为n2;
40.6)成品拉伸:退火后的φ8mm线坯通过多模连续拉丝机拉伸至成品规格φ5.8,模具数量7只,模具材质为cd聚晶模,拉伸速度:2.5m/s,拉伸采用乳化液进行润滑和冷却;拉伸完成后,操作人员穿戴干净纱手套,用透明塑料薄膜将产品进行封装。
41.7)检验包装入库:成品线材表面采用40x放大镜进行表面检测,无起皮、丝流、凹坑等缺陷,检验合格后包装入库,库房的温度:20℃,相对湿度33%。
42.本实施例中,乳化液质量百分比浓度为3.5%,ph值7.3,乳化液温度:31℃。
43.实施例3:
44.一种规格为φ2.8mm耐腐蚀锡磷青铜线材制备方法以下:
45.1)熔炼:按照所需成分进行配料,然后在熔炼炉中进行熔炼,熔炼温度为1120~1170℃,待全部金属熔化后,化验成分合格后保温;
46.2)铸造:铜水由结晶器从保温炉内水平连续引出,铸坯规格φ10mm,铸造温度1150~1180℃,冷却水进水温度:26℃,出水温度:33℃,牵引工艺采用“拉伸—停顿—反推—停顿”牵引动作,牵引参数:牵引速度1.50m/min,拉坯长度16mm、拉伸时间0.17s、拉停时间0.25s、反推长度2mm、反推时间0.08s,推停时间:0.05s;
47.3)剥皮:φ10mm铸坯先一道次拉伸至φ8.5mm,加工率10.8%,φ8.5线坯椭圆度0.02mm,剥皮总厚度为0.5mm,剥皮后线径为φ8mm;
48.4)中间拉伸:剥皮后的φ8.5线坯通过多模连续拉丝机连拉至φ4.2mm,模具数量4只,拉伸速度:2m/s,拉伸采用乳化液进行润滑和冷却;
49.5)退火:φ4.2mm硬态线坯在光亮退火炉里进行无氧化退火,退火温度420℃,升温时间20min,保温时间240min,升温段保护气体流量18m3/h,保温段保护气体流量:15m3/h,保护性气体压力:85mbar;保护性气体为n2和h2的混合气体,h2体积占比85%,o2体积占比≤1ppm,残氨≤2ppm,余量为n2;
50.6)成品拉伸:退火后的φ4.2线坯通过多模连续拉丝机拉伸至成品规格φ2.8,模具数量7只,模具材质为cd聚晶模,拉伸速度:3m/s,拉伸采用乳化液进行润滑和冷却;拉伸完成后,操作人员穿戴干净纱手套,用透明塑料薄膜将产品进行封装。
51.9)检验包装入库:成品线材表面采用40x放大镜进行表面检测,无起皮、丝流、凹坑等缺陷,检验合格后包装入库,库房的温度:16℃,相对湿度30%。
52.本实施例中乳化液质量百分比浓度为3.4%,ph值7.3,乳化液温度:35℃。
53.对比例:规格为φ4mm锡磷青铜线材常规生产工艺路线:熔炼
→
水平连铸
→
过道拉伸
→
氧化退火
→
酸洗
→
成品拉伸。水平连铸牵引工艺只有一次反推动作。
54.对实施例与对比例进行以下测试,测试结果见表3。
55.盐雾试验:按照gb/t 10125-2012(人造气氛腐蚀试验盐雾试验)试验方法(中性盐雾试验法)进行盐雾对比试验,试验条件为:温度:35
±
2℃,ph值:6.5-7.2,盐雾浓度:5%nacl溶液,试验时间为24h,试样长度为100mm,试验结束后取出试样,洗净干燥后通过肉眼观察试样表面变色情况以及点蚀数量来判断耐腐蚀效果。
56.晶粒度测量:金相试样按照gb/t 13298规定制备,晶粒度测量按照gb/t 6394-2017(金属平均晶粒度测定方法)规定的比较法测量,即通过与标准评级图对比来评定晶粒度。
57.粗糙度测量:按照gb/t 1031-2016(产品几何规范(gps)表面结构轮廓法)进行盐粗糙度测量,采用中线制(轮廓法)评定表面粗糙度,具体检测方法是:将粗糙度测量仪金刚石触针沿线材表面径向缓慢滑行,从指示仪表直接得出一个测量行程的ra值,测量三次取平均值。
58.表1本发明实施例、对比例的化学成分
[0059][0060]
表2本发明实施例中乳化液的组成
[0061][0062]
表3本发明实施例、对比例的检测结果
[0063]