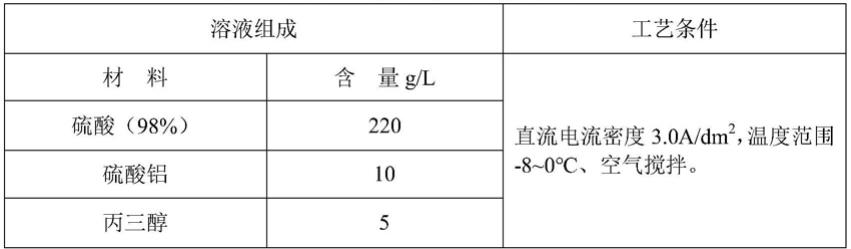
1.本发明涉及金属材料表面处理技术领域,具体为一种钢铁材料复合涂层的制备方法。
背景技术:2.目前,许多处于海洋大气环境条件下的高温锅炉、烟囱、高温烟道、排气管道、散热器等设备及其零部件不仅需要面临高温、高湿、高盐、高辐射等恶劣海洋大气环境的影响,同时还需要面临300℃以上高温、高/低温冲击、摩擦磨损等复杂工况环境影响,使用过程中极易产生腐蚀破坏,直接影响设备使用的安全性、可靠性及使用寿命。
3.现有耐高温防护技术主要包括金属涂/镀层防护技术以及有机耐高温涂层防护技术。金属涂/镀层在严酷海洋环境条件下,极易产生腐蚀损伤;有机耐高温涂层在冷/热交替温度冲击条件下,耐蚀性能会大幅衰减,同时有机耐高温涂层对于摩擦磨损防护性能相对较弱;即使采用热喷涂+有机耐高温涂层的防护形式,也经常会因为热喷涂涂层表面粗糙不平造成的有机耐高温涂层防护薄弱部位热喷涂金属严重腐蚀或高/低温交变作用下有机耐高温涂层自身性能降低引起的热喷涂金属严重腐蚀,从而导致耐高温有机涂层出现大面积剥离现象,极大影响金属表面性能。
技术实现要素:4.本发明的目的在于提供一种钢铁材料复合涂层的制备方法,以同时解决钢铁材料耐高温性能、耐蚀性能和耐磨性能差的问题。
5.为了达到上述目的,本发明提供了一种钢铁材料复合涂层的制备方法,其特征在于,包括以下步骤;步骤1,首先在基体材料表面进行喷砂处理;步骤2,然后在基体表面制备热喷铝涂层;步骤3,然后在热喷铝涂层表面制备耐高温有机涂层;步骤4,对表面打磨,磨掉波峰露出热喷铝涂层,热喷铝涂层露出的部分呈岛链状分布,在露出的热喷铝涂层表面制备硬质阳极氧化膜层;步骤5,最后,在涂层表面制备耐高温有机涂层。
6.为了提高耐高温有机涂层与热喷铝涂层结合的稳定性,在步骤2中,制备完耐高温有机涂层后再进行高温处理。
7.进一步的,热喷铝涂层表面的耐高温有机涂层制备完成后进行高温处理的温度为300℃~600℃,热处理时间为30min~90min。
8.为了防止制备硬质阳极氧化膜极易产生不成膜或烧蚀现象,同时提高了热喷铝涂层表面的耐蚀、耐磨性,打磨处理时,露出的热喷铝涂层占涂层总面积的20%~70%。
9.优选的,为了提高复合涂层整体耐磨性能,热喷铝涂层表面的耐高温有机涂层厚度≤50μm,硬质阳极氧化膜表面制备的耐高温有机涂层厚度≥30μm。
10.优选的,耐高温有机涂层种类采用有机硅涂层或聚酰亚胺涂层。
11.优选的,硬质阳极氧化膜的制备方法采用硫酸法或混合酸法。
12.热喷铝涂层的制备方法采用火焰喷涂、电弧喷涂、超音速火焰喷涂或等离子喷涂。
13.具体包括以下步骤:步骤1,先进行基材喷砂,可分别选用16~200目金刚砂对基材表面进行喷射处理,使钢材表面粗糙度12μm≤rz≤70μm,然后用有机溶剂清洗基材表面;步骤2,在喷砂完成后,先对钢基体进行预热处理,预热处理条件为:80℃~200℃,时间30min~90min;热喷铝应选用al≥99.7%的纯铝丝或mg≤5%的铝合金材料;喷涂时,应使喷枪与作业面保持90
°
,距离保持150mm~200mm前提下进行喷涂处理,采用多道均匀喷涂,热喷铝涂层厚度应控制在100μm~250μm;步骤3,在热喷铝涂层上制备耐高温有机涂层,采用喷涂法制备耐高温有机涂层时,固体份含量为10%~60%;采用浸涂法制备时,固体份含量为10%~40%;采用刷涂法制备时,固体份含量为30%~70%;步骤4,耐高温有机涂层制备完成后,对耐高温有机涂层整体进行高温处理;步骤5,热喷铝涂层表面耐高温有机涂层制备完成后,进行打磨处理,磨掉波峰露出热喷铝涂层,热喷铝涂层露出的部分呈岛链状分布;步骤6,在露出的热喷铝涂层表面制备硬质阳极氧化膜层;步骤7,重复步骤3,在硬质阳极氧化膜表面制备耐高温有机涂层。
14.有益效果在于:1.本发明一种钢铁材料复合涂层的制备方法,通过热喷铝涂层和耐高温有机涂层的协同作用,解决了单一金属涂层或有机涂层在海洋大气环境特别是高温/常温交变工况条件下防护性能较差的问题,极大提高了钢铁材料在海洋大气环境条件下的耐蚀性能。
15.2.本发明解决了热喷铝涂层表面制备硬质阳极氧化膜的技术难题,热喷铝涂层具有较高的孔隙率,在热喷铝涂层表面特别是较薄热喷铝涂层表面制备硬质阳极氧化膜极易产生不成膜或烧蚀现象;而本发明通过耐高温有机涂层对热喷铝涂层表面波谷处的封闭作用,较好的解决了这一技术难题,极大提高了热喷铝涂层表面的耐蚀、耐磨性。
16.3.本发明在热喷铝涂层表面制备的岛链状硬质阳极氧化膜,具有与热喷铝涂层结合力强、耐磨性好的特点,能够起到良好的骨架支撑作用,解决了目前耐高温有机涂层使用过程中耐磨性能差的问题,极大提高了复合涂层的耐磨性能及使用寿命。
17.4.本发明通过耐高温有机涂层对热喷铝涂层波谷处的填充作用,通过对波峰处打磨、硬质阳极氧化处理,有效改善了热喷铝/耐高温有机涂层匹配性以及耐高温有机涂层在热喷铝涂层波峰处薄弱部位的耐蚀性能,解决了热喷铝/耐高温有机涂层配合使用过程中由于耐高温有机涂层存在薄弱部位造成涂层极易产生白锈、腐蚀脱落等现象的问题,极大提高了复合涂层使用过程中的综合性能。
18.5.本发明通过耐高温有机涂层对热喷铝涂层波谷处的填充作用,硬质阳极氧化膜对耐高温有机涂层的嵌入作用,较好的解决了耐高温有机涂层在高温/常温冷热循环过程中的性能衰减问题,提高了复合涂层工作过程的稳定性及使用寿命,形成了耐高温、耐蚀、耐磨的一体化复合防护涂层。
具体实施方式
19.下面对本发明的具体实施方式作进一步详细的说明,但本发明并不局限于这些实施方式,在不脱离本发明原理的前提下,针对本发明进行的改进也落入本发明权利要求的保护范围内。
20.一种钢铁材料复合涂层的制备方法,具体步骤如下:步骤1,先进行基材喷砂,可分别选用16~200目金刚砂对基材表面进行喷射处理,去除基材表面的锈蚀、氧化皮以及其他污染物,使钢材表面粗糙度12μm≤rz≤70μm,然后用丙酮等有机溶剂进一步清洗基材表面,形成干燥、清洁表面;步骤2,在喷砂完成后,进行热喷铝涂层的制备,热喷铝涂层的制备可以采用火焰喷涂、电弧喷涂、超音速火焰喷涂或等离子喷涂法中任意一种制备;热喷铝涂层制备前,应对基材进行预热处理,以去除试样表面湿气或水分,预热处理条件为:80℃~200℃,时间30min~90min;热喷铝应选用al≥99.7%的纯铝丝或mg≤5%的铝合金材料;喷涂时,应使喷枪与作业面保持90
°
,距离保持150mm~200mm前提下进行喷涂处理;热喷涂应采用多道喷涂的方式,每道喷涂应保持涂层表面均匀,涂层不能产生脱落、起泡、裂纹、疏松或堆积等缺陷;热喷铝涂层厚度应控制在100μm~250μm;步骤3,在热喷铝涂层上制备耐高温有机涂层,采用喷涂法制备耐高温有机涂层时,固体份含量为10%~60%;采用浸涂法制备时,固体份含量为10%~40%;采用刷涂法制备时,固体份含量为30%~70%,制备均匀的耐高温有机涂层,涂层厚度范围为10μm~50μm;步骤4,耐高温有机涂层制备完成后,对涂层整体进行高温处理,高温处理一般不限定气氛,可以在大气、真空或惰性气体保护气氛下进行。高温处理温度为300℃~600℃,热处理时间为30min~90min,热处理后耐高温有机涂层应与热喷铝涂层具有良好的结合力,没有剥离或脱落等现象发生;步骤5,热喷铝涂层表面耐高温有机涂层制备完成后,应进行打磨处理,使热喷铝涂层波峰处的金属铝露出,以进行下一步硬质阳极氧化膜层的制备;打磨处理主要采用手工或电动工具的方式进行打磨,打磨处理的程度以露出金属铝,但不破坏热喷铝涂层波谷处耐高温有机涂层为前提。根据工件使用工况条件,可以适当增加或减少金属铝的裸露面积,从而控制硬质阳极氧化膜(不连续的岛链状)在后续耐高温有机涂层中所占比例。硬质阳极氧化膜体积百分含量应≥20%;步骤6,热喷铝表面硬质阳极氧化膜的制备,依次进行溶剂除油、碱洗、水洗、酸洗出光、水洗等前处理工艺后,采用电化学方法制备硬质阳极氧化膜层;碱洗液主要成份是氢氧化钠含量45~65g/l,葡萄糖酸钠0.5~10g/l;碱洗温度为40~60℃,时间为1~5min;酸洗出光液主要成份是20%~50%硝酸浓度,酸洗温度为室温,时间为3~10min;电化学制备硬质阳极氧化膜可以采用硫酸法、混合酸法以及其它溶液法制备;硫酸法制备硬质阳极氧化膜溶液的主要成份是硫酸、硫酸铝、丙三醇,其中,硫酸为150~350g/l,硫酸铝为5~30g/l,丙三醇为5~20g/l。硫酸法制备硬质阳极氧化膜一般采用直流电流;工艺条件为温度0℃~-10℃,电流密度2.0~8.0a/dm2,制备时间60~120min;混合酸法制备硬质阳极氧化膜溶液的主要成份是硫酸、酒石酸、柠檬酸以及磺化蒽添加剂以及硫酸铝,其中,硫酸为10~80g/l,酒石酸为25~55g/l,柠檬酸为10~30g/l,
磺化蒽添加剂10~20g/l,硫酸铝为5~30g/l;混合酸法制备硬质阳极氧化膜一般采用直流电流;工艺条件为温度0~-10℃、电流密度1.5~5.5a/dm2,制备时间60~120min;步骤7,硬质阳极氧化膜制备完成后,可以直接进行耐高温有机涂层的制备,制备耐高温有机涂层采用的涂料类型可以是与第3步相同的涂料,也可以选择其它涂料,制备的涂层应与硬质阳极氧化膜以及第3步制备的耐高温有机涂层具有良好的结合力;为了提高复合涂层整体耐磨性能,本步骤制备的耐高温有机涂层厚度应与硬质阳极氧化膜层相匹配,耐高温有机涂层厚度范围为≥30μm,制备后的复合涂层应外观平整、光滑。
21.实施例1试件基材选用40cr钢材,规格150mm
×
100mm
×
3mm,表面铣削加工至粗糙度ra1.6,备用。
22.①
喷砂处理:首先将试样用丙酮清洗,清除表面油脂;然后采用60目金刚砂对基材表面进行喷射处理;然后再次采用丙酮对试样表面进行清洗处理;将试件吹干,形成干燥、清洁表面,备用。
23.②
热喷铝涂层制备:将试样放到烘箱内加热到200℃,保持时间30min,将试样放置在工装架上,采用火焰喷涂法进行喷铝处理,其中,铝材料为al≥99.7%的纯铝丝,热喷涂喷枪为qx-1型高速喷枪。喷涂过程中,乙炔气压为0.05mpa,氧气气压为0.4mpa,空气气压为0.4mpa,喷涂角度控制在90
°
,喷涂距离180mm;喷铝过程采用多次喷涂的方式,控制涂层表面均匀,没有脱落、起泡、裂纹、疏松或堆积等缺陷产生,涂层平均厚度为120μm。
24.③
热喷铝表面耐高温有机涂层制备:采用空气喷涂法在热喷铝表面制备耐高温有机涂层,其中,耐高温涂料采用w30-1有机硅涂料,涂料的固体份含量为55%。喷涂时,喷枪距试样平均距离25cm,控制喷枪进料量、进气量以及喷涂速度,经多次喷涂后,控制耐高温有机涂层平均干膜厚度为30μm,将试样放入170℃的烘箱内,固化处理40min,冷却至室温,取出样件。
25.④
高温处理:将试样放入烘箱中加热至400℃,保持时间30min,冷却至室温,取出试样。
26.⑤
耐高温有机涂层打磨处理:用600#砂纸对试样表面进行手工打磨,控制打磨时间、打磨力度,将试样表面波峰磨平,露出部分热喷铝金属,控制露出的金属铝的面积占试样总面积45%,使其呈岛链状分布。
27.⑥
硬质阳极氧化膜的制备:将打磨处理后的试样用蘸有丙酮的脱脂棉擦拭干净;然后在平均温度为50℃的碱洗液中浸泡60s,碱洗溶的主要成份为:氢氧化钠55g/l,葡萄糖酸钠2.5g/l;自来水漂洗40s;室温下在30%稀硝酸中浸泡3min;自来水漂洗30s;按表1给定的溶液配方和工艺条件制备硬质阳极氧化膜,时间90min;然后自来水漂洗60s;将试件吹干,备用。表1硫酸法硬质阳极氧化膜制备工艺
⑦
耐高温有机涂层的制备:采用空气喷涂法在试样
⑥
的表面制备耐高温有机涂层,其中,耐高温涂料采用w30-1有机硅涂料,涂料的固体份含量为55%。喷涂时,喷枪距试样平均距离25cm,控制喷枪进料量、进气量以及喷涂速度,经多次喷涂后,控制耐高温有机涂层平均干膜厚度为35μm,将试样放入170℃的烘箱内,固化处理40min,冷却至室温,取出样件即为钢材料耐高温耐蚀耐磨复合涂层。
29.本实施例制备的钢材料耐高温耐蚀耐磨复合涂层外观为黑色均匀涂层;按照gb/t13452.2-2008色漆和清漆漆膜厚度的测定,该复合涂层的平均厚度为155μm。按照gb/t1768-2006色漆和清漆耐磨性的测定旋转橡胶轮法进行测试,该复合涂层的平均磨耗量为5.1mg/1000r(压力10n,磨耗轮cs-10)。按照gb/t 5210-2006色漆和清漆拉开法附着力试验对复合涂层附着力进行检测,该复合涂层的附着力为17.2mpa。采用热震试验对涂层耐温性能进行考核,具体试验方法是将样件在550℃下保温15min,然后浸入常温水中进行淬火处理,等样件降至室温后,取出,吹干,用10倍放大镜观察涂层表面上是否有开裂、剥离等现象产生;经过10次热震循环试验考核后,试样表面涂层无起皮、脱落或剥落等情况发生,表明涂层具有良好的耐高温及温度冲击性能。经过10次热震循环试验考核后,按照gb/t1771-2007色漆和清漆耐中性盐雾性能的测定方法规定,进行5%中性盐雾试验3000h后,按gb/t1766-2008色漆和清漆涂层老化的评价方法,综合等级为0级。(注:按gb/t1766标准,涂层综合等级0级最好,5级最差。)实施例2试件基材选用45钢,规格150mm
×
100mm
×
3mm,表面铣削加工至粗糙度ra1.6,备用。
30.①
按实施例1的
①
~
②
对试样进行处理。
31.②
热喷铝表面耐高温有机涂层制备:采用空气喷涂法在热喷铝表面制备耐高温有机涂层,其中,耐高温涂料采用ws120聚酰亚胺涂料,涂料的固体份含量为30%。喷涂时,喷枪距试样平均距离25cm,控制喷枪进料量、进气量以及喷涂速度,经多次喷涂后,控制耐高温有机涂层平均干膜厚度为30μm,将试样放入180℃的烘箱内,固化处理30min,冷却至室温,取出样件。
32.③
高温处理:将试样放入烘箱中加热至350℃,保持时间30min,冷却至室温,取出试样。
33.④
按实施例1的
⑤
对试样进行处理。
34.⑤
按实施例1的
⑥
对试样进行处理。
35.⑥
耐高温有机涂层的制备:采用空气喷涂法在试样
⑤
的表面制备耐高温有机涂层,其中,耐高温涂料采用ws120聚酰亚胺涂料,涂料的固体份含量为30%。喷涂时,喷枪距
试样平均距离25cm,控制喷枪进料量、进气量以及喷涂速度,经多次喷涂后,控制耐高温有机涂层平均干膜厚度为35μm,将试样放入180℃的烘箱内,固化处理30min,冷却至室温,取出样件即为钢材料耐高温耐蚀耐磨复合涂层。
36.本实施例制备的钢材料耐高温耐蚀耐磨复合涂层外观为灰黑色均匀涂层;按照gb/t13452.2-2008色漆和清漆漆膜厚度的测定,该复合涂层的平均厚度为150μm。按照gb/t1768-2006色漆和清漆耐磨性的测定旋转橡胶轮法进行测试,该复合涂层的平均磨耗量为4.3mg/1000r(压力10n,磨耗轮cs-10)。按照gb/t 5210-2006色漆和清漆拉开法附着力试验对复合涂层附着力进行检测,该复合涂层的附着力为16.3mpa。采用热震试验对涂层耐温性能进行考核,具体试验方法是将样件在350℃下保温15min,然后浸入常温水中进行淬火处理,等样件降至室温后,取出,吹干,用10倍放大镜观察涂层表面上是否有开裂、剥离等现象产生;经过10次热震循环试验考核后,试样表面涂层无起皮、脱落或剥落等情况发生,表明涂层具有良好的耐高温及温度冲击性能。经过10次热震循环试验考核后,按照gb/t1771-2007色漆和清漆耐中性盐雾性能的测定方法规定,进行5%中性盐雾试验3000h后,按gb/t1766-2008色漆和清漆涂层老化的评价方法,综合等级为0级。
37.实施例3试件基材选用q235b,规格150mm
×
100mm
×
3mm,表面铣削加工至粗糙度ra1.6,备用。
38.①
按实施例1的
①
~
②
对试样进行处理。
39.②
热喷铝表面耐高温有机涂层制备:采用空气喷涂法在热喷铝表面制备耐高温有机涂层,其中,耐高温涂料采用ws120聚酰亚胺涂料,涂料的固体份含量为30%。喷涂时,喷枪距试样平均距离25cm,控制喷枪进料量、进气量以及喷涂速度,经多次喷涂后,控制耐高温有机涂层平均干膜厚度为30μm,将试样放入180℃的烘箱内,固化处理30min,冷却至室温,取出样件。
40.③
高温处理:将试样放入烘箱中加热至350℃,保持时间30min,冷却至室温,取出试样。
41.④
按实施例1的
⑤
对试样进行处理。
42.⑤
硬质阳极氧化膜的制备:将打磨处理后的试样用蘸有丙酮的脱脂棉擦拭干净;然后在50
±
5℃的碱洗液中浸泡60s,碱洗溶的主要成份为:氢氧化钠55g/l,葡萄糖酸钠2.5g/l;自来水漂洗60s;室温下在30%稀硝酸中浸泡3min;自来水漂洗30s;按表2给定的溶液配方和工艺条件制备硬质阳极氧化膜,时间100min;然后自来水漂洗60s;将试件吹干,备用。表2混合酸法硬质阳极氧化膜制备工艺
⑥
耐高温有机涂层的制备:采用空气喷涂法在试样
⑤
的表面制备耐高温有机涂层,其中,耐高温涂料采用w30-1有机硅涂料,涂料的固体份含量为55%。喷涂时,喷枪距试样平均距离25cm,控制喷枪进料量、进气量以及喷涂速度,经多次喷涂后,控制耐高温有机涂层平均干膜厚度为35μm,将试样放入170℃的烘箱内,固化处理40min,冷却至室温,取出样件即为钢材料耐高温耐蚀耐磨复合涂层。
44.本实施例制备的钢材料耐高温耐蚀耐磨复合涂层外观为黑色均匀涂层;按照gb/t13452.2-2008色漆和清漆漆膜厚度的测定,该复合涂层的平均厚度为155μm。按照gb/t1768-2006色漆和清漆耐磨性的测定旋转橡胶轮法进行测试,该复合涂层的平均磨耗量为5.5mg/1000r(压力10n,磨耗轮cs-10)。按照gb/t 5210-2006色漆和清漆拉开法附着力试验对复合涂层附着力进行检测,该复合涂层的附着力为14.5mpa。采用热震试验对涂层耐温性能进行考核,具体试验方法是将样件在450℃下保温15min,然后浸入常温水中进行淬火处理,等样件降至室温后,取出,吹干,用10倍放大镜观察涂层表面上是否有开裂、剥离等现象产生;经过10次热震循环试验考核后,试样表面涂层无起皮、脱落或剥落等情况发生,表明涂层具有良好的耐高温及温度冲击性能。经过10次热震循环试验考核后,按照gb/t1771-2007色漆和清漆耐中性盐雾性能的测定方法规定,进行5%中性盐雾试验3000h后,按gb/t1766-2008色漆和清漆涂层老化的评价方法,综合等级为0级。
45.对照实验1试件基材选用q235b,试样规格100mm
×
100mm
×
3mm,按实施例1的
①
对试样进行处理后喷涂w30-1有机涂层,涂层平均干膜厚度75μm,采用gb/t1768-2006测试涂层耐磨性能,涂层平均磨耗量为27.3mg/1000r(压力10n,磨耗轮cs-10);采用gb/t1771进行5%中性盐雾试验480h后,按gb/t1766-2008色漆和清漆涂层老化的评价方法,涂层综合等级5级。
46.对照实验2试件基材选用q235b,试样规格100mm
×
100mm
×
3mm,按实施例1的
①
对试样进行处理后喷涂ws120聚酰亚胺涂层,涂层平均干膜厚度50μm,采用gb/t1768-2006测试涂层耐磨性能,涂层平均磨耗量为17.7mg/1000r(压力10n,磨耗轮cs-10);采用gb/t1771进行5%中性盐雾试验480h后,按gb/t1766-2008色漆和清漆涂层老化的评价方法,涂层综合等级2级。
47.实施例1-3与w30-1有机涂层和ws120聚酰亚胺涂层相比,其耐磨性、耐蚀性能大幅提高。
48.综上,通过本发明制备方法形成的钢铁材料耐高温耐蚀耐磨复合涂层,按照gb/
t13452.2-2008,其厚度范围为140μm~160μm;按照gb/t1768-2006测量,其平均磨耗量为3~10mg/1000r(压力10n,磨耗轮cs-10);经过10次热震循环试验考核后,按照gb/t1771-2007测量,其5%中性盐雾试验3000h后,综合评级为0级;按照gb/t 5210-2006测量,复合涂层的附着力为10mpa~20mpa;按照热震试验方法进行测量,复合涂层耐温性能为≤600℃。