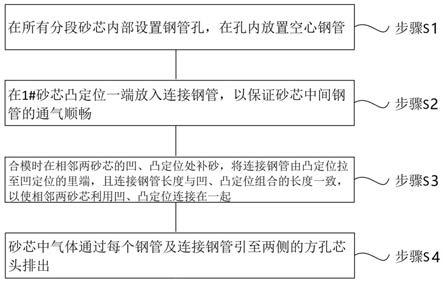
1.本发明涉及立柱砂芯铸造技术领域,尤其涉及一种导轨无孔立柱的铸造方法及系统。
背景技术:2.铁水在浇注时,砂芯在高温金属液体作用下,由于有机物的挥发、分解和燃烧,以及水分的蒸发,浇注后短时间内会产生大量气体,在设计制造砂芯以及在下芯、合模操作的整个过程中,都要采取必要的措施,使浇注时在砂芯中产生的气体,能够及时、顺利地通过芯头排出,除了采用透气性好的芯砂制作砂芯外,制芯时在砂芯中开设适当的通气道是一个很重要的措施,与此同时,砂型与芯头出气孔相对应的位置也应留有通气道连通。
3.在立柱造型过程中,需要保证导轨面的性能,最好的铸造方法是导轨在下箱,上箱有透皮孔可用于砂芯排气,但对于上箱没有透皮孔的大立柱,由于砂芯较大,分段砂芯排气困难,需要在砂芯上部做孔,这对铸件强度有影响,且此孔后期仍需补焊回去,并需要额外做焊块,耗费人力物力,消耗原材料及人工,其次在砂芯间连接处容易出现较大披锋,从而导致打磨工作量大,打磨成本增加。
技术实现要素:4.本发明的目的在于提供一种导轨无孔立柱的铸造方法及系统,用于解决现有的砂芯出气困难,以及砂芯之间连接处易出现披锋的技术问题。
5.为达到上述目的,本发明采用如下技术方案:一种导轨无孔立柱的铸造方法,包括以下步骤:在所有分段砂芯内部设置钢管孔,在孔内放置空心钢管;在1#砂芯凸定位一端放入连接钢管,以保证砂芯中间钢管的通气顺畅;合模时在相邻两砂芯的凹、凸定位处补砂,将连接钢管由凸定位拉至凹定位的里端,且连接钢管长度与凹、凸定位组合的长度一致,以使相邻两砂芯利用凹、凸定位连接在一起;砂芯中气体通过每个钢管及连接钢管引至两侧的方孔芯头排出。
6.其中,在相邻两砂芯的凹、凸定位处补砂时采用树脂砂。
7.具体地,所述空心钢管采用φ130管。
8.进一步地,所述连接钢管采用φ60管。
9.一种导轨无孔立柱的铸造系统,包括:多个分段砂芯,且相邻两砂芯利用凹、凸定位连接在一起;每个所述分段砂芯的内部设置有钢管孔,且所述钢管孔内放置有空心钢管;1#砂芯凸定位一端放置有连接钢管,合模时在相邻两砂芯的凹、凸定位处补砂,并将所述连接钢管由凸定位拉至凹定位的里端,且所述连接钢管的长度与凹、凸定位组合的长度一致。
10.其中,相邻两砂芯的凹、凸定位处补砂时采用树脂砂。
11.具体地,所述空心钢管采用φ130管。
12.进一步地,所述连接钢管采用φ60管。
13.实际应用时,所述1#砂芯的芯头具有第一凸定位,且与所述1#砂芯相邻的2#砂芯匹配具有凹定位,所述第一凸定位与所述凹定位能够对接。
14.其中,所述2#砂芯的芯头具有第二凸定位,且所述第二凸定位远离所述凹定位设置。
15.具体地,所述1#砂芯的内部设置有第一钢管,所述2#砂芯的内部设置有第二钢管,且所述第一钢管与所述第二钢管之间连通有所述连接钢管。
16.进一步地,所述连接钢管与所述第一钢管及所述第二钢管之间通过所述树脂砂连接,且所述树脂砂位于所述连接钢管的外侧。
17.相对于现有技术,本发明所述的导轨无孔立柱的铸造方法及系统具有以下优势:本发明提供的导轨无孔立柱的铸造方法及系统中,通过分段砂芯中分别放置空心钢管,且相邻的两个空心钢管之间通过连接钢管连通,以使气体能够由两端芯头排出,从而不仅解决了砂芯出气困难,以及铸件补焊的问题,而且有效减少了砂芯之间连接处的披锋,进而减少了打磨工作量,并且没有影响铸件的强度,在保证铸件质量的同时降低了成本。
附图说明
18.图1为本发明实施例提供的导轨无孔立柱的铸造方法的流程示意图;图2为本发明实施例提供的导轨无孔立柱的铸造系统的结构示意图;图3为本发明实施例提供的导轨无孔立柱的铸造系统的第一视角剖视结构示意图;图4为本发明实施例提供的导轨无孔立柱的铸造系统的第二视角剖视结构示意图。
19.附图标记:1-分段砂芯;11-1#砂芯;111-第一凸定位;12-2#砂芯;121-凹定位;122-第二凸定位;2-空心钢管;21-第一钢管;22-第二钢管;3-连接钢管;4-树脂砂。
具体实施方式
20.为了便于理解,下面结合说明书附图,对本发明实施例提供的导轨无孔立柱的铸造方法及系统进行详细描述。
21.本发明实施例提供一种导轨无孔立柱的铸造方法,如图1所示,包括以下步骤:步骤s1、在所有分段砂芯内部设置钢管孔,在孔内放置空心钢管;步骤s2、在1#砂芯凸定位一端放入连接钢管,以保证砂芯中间钢管的通气顺畅;步骤s3、合模时在相邻两砂芯的凹、凸定位处补砂,将连接钢管由凸定位拉至凹定位的里端,且连接钢管长度与凹、凸定位组合的长度一致,以使相邻两砂芯利用凹、凸定位连接在一起;步骤s4、砂芯中气体通过每个钢管及连接钢管引至两侧的方孔芯头排出。
22.一种导轨无孔立柱的铸造系统,如图2和图3所示,包括:多个分段砂芯1,且相邻两
砂芯利用凹、凸定位连接在一起;每个分段砂芯1的内部设置有钢管孔,且钢管孔内放置有空心钢管2;1#砂芯11凸定位一端放置有连接钢管3,合模时在相邻两砂芯的凹、凸定位处补砂,并将连接钢管3由凸定位拉至凹定位的里端,且连接钢管3的长度与凹、凸定位组合的长度一致。
23.相对于现有技术,本发明实施例所述的导轨无孔立柱的铸造方法及系统具有以下优势:本发明实施例提供的导轨无孔立柱的铸造方法及系统中,通过分段砂芯1中分别放置空心钢管2,且相邻的两个空心钢管2之间通过连接钢管3连通,以使气体能够由两端芯头排出,从而不仅解决了砂芯出气困难,以及铸件补焊的问题,而且有效减少了砂芯之间连接处的披锋,进而减少了打磨工作量,并且没有影响铸件的强度,在保证铸件质量的同时降低了成本。
24.其中,本发明实施例提供的导轨无孔立柱的铸造系统中,如图2和图3所示,相邻两砂芯的凹、凸定位处补砂时可以采用树脂砂4。树脂砂是指以人工合成树脂作为砂粒的粘结剂的型砂或芯砂;用树脂砂制成铸型或型芯后,通过固(硬)化剂的作用,树脂发生不可逆的交联反应而固化,从而给予铸型或型芯以必要的强度。
25.具体地,本发明实施例提供的导轨无孔立柱的铸造系统中,如图2和图3所示,上述空心钢管2可以优选为采用φ130管。
26.进一步地,本发明实施例提供的导轨无孔立柱的铸造系统中,如图2和图3所示,上述连接钢管3可以优选为采用φ60管。
27.实际应用时,本发明实施例提供的导轨无孔立柱的铸造系统中,如图2和图3所示,上述1#砂芯11的芯头具有第一凸定位111,且与该1#砂芯11相邻的2#砂芯12匹配具有凹定位121,第一凸定位111与凹定位121能够对接,从而使相邻两砂芯利用凹、凸定位连接在一起。
28.其中,本发明实施例提供的导轨无孔立柱的铸造系统中,如图2和图3所示,上述2#砂芯12的芯头具有第二凸定位122,且该第二凸定位122远离凹定位121设置,以便于与其它分段砂芯1的凸定位进行对接。
29.具体地,本发明实施例提供的导轨无孔立柱的铸造系统中,如图2和图3所示,上述1#砂芯11的内部可以设置有第一钢管21,上述2#砂芯12的内部可以设置有第二钢管22,且第一钢管21与第二钢管22之间可以连通有上述连接钢管3,从而有效保证砂芯中间钢管的通气顺畅。
30.进一步地,本发明实施例提供的导轨无孔立柱的铸造系统中,如图2和图3所示,上述连接钢管3与第一钢管21及第二钢管22之间可以通过树脂砂4连接,且该树脂砂4位于连接钢管3的外侧,从而通过合模时在相邻两砂芯的凹、凸定位处进行补砂实现。
31.以上所述,仅为本发明的具体实施方式,但本发明的保护范围并不局限于此,任何熟悉本技术领域的技术人员在本发明揭露的技术范围内,可轻易想到变化或替换,都应涵盖在本发明的保护范围之内。因此,本发明的保护范围应以所述权利要求的保护范围为准。