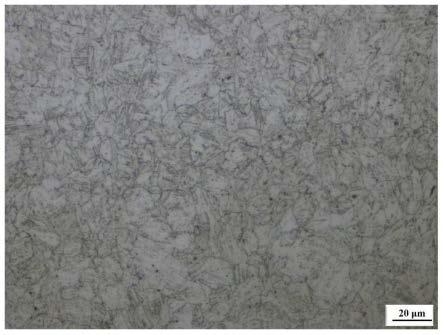
一种改善超厚规格15crmor压力容器钢板心部低温冲击韧性的方法
技术领域
1.本发明涉及冶金技术领域,尤其涉及一种改善超厚规格15crmor压力容器 钢板心部低温冲击韧性的方法。
背景技术:2.15crmor是gb/t713-2014和gb/t35012-2018中的压力容器用钢,标准要求 正火+回火交货,广泛应用于石油化工、煤化工行业,用于制造加氢反应器,还 原反应器,变化炉,汽化炉,换热器,塔器,热高压分离器,降凝器等设备, 服役环境恶劣(400-600℃高温、高压、氢腐蚀、长时间回火脆化),要求钢板 具有高温强度和塑型,良好的低温冲击韧性,优良的抗氧化性和耐腐蚀性,良 好的加工性能和焊接性能,良好的组织稳定性。技术要求高,生产难度大。
3.在低温冲击韧性方面,一般要求-20℃下1/4厚度处和1/2厚度处的冲击功 均合格,生产实践表明,厚度小于60mm的钢板-20℃下1/4厚度处和1/2厚度 处冲击功稳定,但厚度大于60mm的钢板采用传统正火+回火工艺生产时低温冲 击功往往会大幅下降,特别是1/2厚度处冲击功达不到标准要求,造成钢板不 合格,进而给企业带来了损失。因此提高超厚规格钢板的低温冲击韧性成为研 发生产15crmor压力容器用钢的技术难点和创新点。
4.专利cn107760987a公开了一种15crmor钢板及其提高心部低温冲击韧性的 方法,通过正火前预热处理,正火+回火工艺的热处理方法提高了厚规格15crmor 钢板的心部低温冲击韧性。不足之处是该方法只适用于15crmor钢板,不适合 其它品种钢板,且增加了生产成本。
5.专利cn101876001a公开了一种提高高强度厚钢板低温冲击韧性的方法,通 过采用淬火+淬火+回火的热处理工艺,控制钢板二次淬火后的组织为硬相+软相 的混合组织,提高了钢板的低温韧性。不足之处一是采用了两次淬火,显著增 加了生产成本;
6.专利cn105420468a公开了一种保证厚规格高强钢低温韧性的热处理方法, 通过淬火、回火、二次回火的热处理方法提高了厚规格高强钢的低温韧性。不 足之处一是只适用于该钢种,采用了两次回火,显著增加了生产成本。
技术实现要素:7.本发明的目的是提供一种改善超厚规格15crmor压力容器钢板心部低温冲 击韧性的方法,大大提高了超厚规格15crmor压力容器钢板心部低温冲击韧性, 将厚度大于60mm的15crmor压力容器钢板的-20℃心部低温冲击功稳定控制在 100j以上,显著提升厚规格钢板的合格率。
8.为解决上述技术问题,本发明采用如下技术方案:
9.本发明一种改善超厚规格15crmor压力容器钢板心部低温冲击韧性的方法, 前工序工艺路线为铁水预处理—转炉冶炼—lf精炼—rh真空处理—连铸—板坯 缓冷—板坯加
热—高压水除磷—粗轧—精轧—acc冷却,还包括acc冷却后进行 热处理,所述热处理包括亚温淬火+高温回火,所述亚温淬火的淬火加热温度为 奥氏体-铁素体两相区,温度为830~870℃,在炉时间1.4min/mm
×
t(mm)+10~ 20min,t为钢板厚度,钢板出炉后淬火至室温;所述高温回火的回火温度在 680-720℃,在炉时间2.3min/mm
×
t(mm)+30~40min,t为钢板厚度。
10.进一步的,所述钢板的化学成分按重量百分比为c:0.15~0.17%、si:0.25~0.35%、mn:0.52~0.69%、p:≤0.009%、s:≤0.004%、cr:1.06~1.15%、mo:0.50~ 0.59、sb≤0.003%、sn≤0.010%、as≤0.010%、j系数≤150、x系数≤15,余 量为fe和不可避免的杂质。
11.进一步的,钢板厚度65mm,钢板抛丸后进行热处理,淬火加热温度850℃, 在炉时间94分,出炉后淬至室温,之后进行回火处理,回火温度700℃,在炉 时间168分,出炉后空冷。
12.进一步的,钢板厚度70mm,钢板抛丸后进行热处理,淬火加热温度850℃, 在炉时间108分,出炉后淬至室温,之后进行回火处理,回火温度700℃,在炉 时间191分,出炉后空冷。
13.进一步的,钢板厚度75mm,钢板抛丸后进行热处理,淬火加热温度850℃, 在炉时间115分,出炉后淬至室温,之后进行回火处理,回火温度700℃,在炉 时间202分,出炉后空冷。
14.与现有技术相比,本发明的有益技术效果:
15.(1)通过亚温淬火+高温回火的热处理方法,大大提高了超厚规格15crmor 压力容器钢板心部低温冲击韧性,将厚度大于60mm15crmor压力容器钢板的
ꢀ‑
20℃心部低温冲击功稳定控制在100j以上,钢板其他性能均满足标准要求, 显著提升厚规格钢板的合格率。
16.(2)为采用厚度250-300mm连铸板坯稳定生产超厚规格压力容器钢板创造了 条件。经实际生产并检验,其力学性能优异,,解决了厚规格容器钢生产技术难 点。
附图说明
17.下面结合附图说明对本发明作进一步说明。
18.图1为本发明实施例1钢板的金相组织。
具体实施方式
19.以下用实施例对本发明作更详细的描述。这些实施例仅仅是对本发明最佳 实施方式的描述,并不对本发明的范围有任何限制。
20.实施例1
21.实施例1的15crmor压力容器钢的化学成分见表1。生产工艺路线为铁水预 处理—转炉冶炼—lf精炼—rh真空处理—连铸—板坯缓冷—板坯加热—高压水 除磷—粗轧—精轧—acc冷却,钢板厚度65mm。钢板抛丸后进行热处理,淬火 加热温度850℃,在炉时间94分,出炉后淬至室温。之后进行回火处理,回火 温度700℃,在炉时间168分,出炉后空冷。钢板性能见表2.
22.实施例2
23.实施方式同实施例1,生产工艺路线为铁水预处理—转炉冶炼—lf精炼— rh真空处理—连铸—板坯缓冷—板坯加热—高压水除磷—粗轧—精轧—acc冷 却,钢板厚度70mm。钢板抛丸后进行热处理,淬火加热温度850℃,在炉时间 108分,出炉后淬至室温。之后进行回火处理,回火温度700℃,在炉时间191 分,出炉后空冷。钢板性能见表2.
24.实施例3
25.实施方式同实施例1,生产工艺路线为铁水预处理—转炉冶炼—lf精炼— rh真空处理—连铸—板坯缓冷—板坯加热—高压水除磷—粗轧—精轧—acc冷 却,钢板厚度75mm。钢板抛丸后进行热处理,淬火加热温度850℃,在炉时间 115分,出炉后淬至室温。之后进行回火处理,回火温度700℃,在炉时间202 分,出炉后空冷。钢板性能见表2.
26.表1本发明实施例1~3的化学成分(wt%)
27.实施例csimnpscrmosbsnasjx10.1550.250.590.0080.0021.100.550.00010.00130.001812613.520.1610.260.600.0070.0011.080.540.00010.00160.001812713.630.1530.280.560.0070.0021.050.560.00010.00150.002012813.7
28.对发明实施例1~3的钢板进行常规力学性能、冲击性能、弯曲性能检验, 结果见表2。
29.表2本发明实施例1~3的钢板的力学性能
[0030][0031]
从表2可看出,对比例为采用常规正火+回火热处理方法后的钢板性能,由 于钢板厚度过大,压缩比小,1/2厚度处-20℃下的冲击性能恶化,冲击功不稳 定,已经达不到标准要求。实施例1~3为采用本发明后钢板的性能,1/2厚度 处的-20℃下冲击性能及其稳定性显著提高,解决了厚度大于60mm的超厚规格 15crmor压力容器钢生产技术难点。
[0032]
以上所述的实施例仅是对本发明的优选方式进行描述,并非对本发明的范 围进行限定,在不脱离本发明设计精神的前提下,本领域普通技术人员对本发 明的技术方案做出的各种变形和改进,均应落入本发明权利要求书确定的保护 范围内。