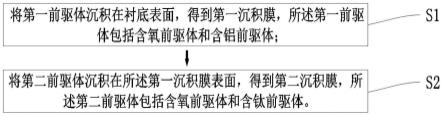
1.本技术涉及原子层沉积领域,尤其涉及一种在贵金属表面制备复合膜的方法、复合膜和贵金属。
背景技术:2.贵金属价格昂贵,大多数拥有美丽的色泽,很多被用来制作成珠宝和纪念品。其中大部分化学性质比较稳定,一般不与其它外界物质发生化学反应。但是在制作的工艺中,难免会混入其它金属杂质。
3.如果贵金属中含有铝元素,表面的铝会因为汗渍而溶解,导致变色。若所述的贵金属中含有银元素,与空气中存在的气体分子反应变色,形成黑色的硫化银。若所述的贵金属中含有汞元素,可能会产生白色的金汞化合物。上述的金属杂质都会影响贵金属表面的颜色和观感。其主要原因是由于贵金属中含有少量的活泼金属,长时间接触汗渍、空气对贵金属有腐蚀性。通常,对于贵金属表面的防护方法主要是真空蒸镀及化学二氧化硅覆膜。但是一方面真空蒸镀温度较高,很难对贵金属进行全部覆膜。另一方面化学二氧化硅覆膜膜厚较厚,附着力不强,容易脱落,同时膜层不致密,结构比较复杂,对于一些图形结构难以全部覆膜。因此,现有技术中,贵金属表面膜层的防贵金属腐蚀性能不强。
技术实现要素:4.本技术提供了一种在贵金属表面制备复合膜的方法、复合膜和贵金属,以解决现有技术的中贵金属表面膜层的防贵金属腐蚀性能不强的技术问题。
5.第一方面,本技术提供了一种在贵金属表面制备复合膜的方法,包括步骤:
6.将第一前驱体沉积在衬底表面,得到第一沉积膜;
7.将第二前驱体沉积在所述第一沉积膜表面,得到第二沉积膜;
8.其中,所述第一前驱体包括含氧前驱体和含铝前驱体,所述第二前驱体包括含氧前驱体和含钛前驱体。
9.可选的,所述含铝前驱体包括alcl3、al(me)3、al(me)2cl、al(et)3和al(oet)3中的一种或多种,其中,所述含钛前驱体包括ti[n(c2h5)2]4、ti[och(ch3)2]4、ticl4和ti[n(ch3)2]4中的一种或多种。
[0010]
可选的,所述含氧前驱体为o2、h2o2、h2o和o3中的一种或多种。
[0011]
可选的,所述衬底的材料为贵金属。
[0012]
可选的,将第一前驱体沉积在衬底表面,得到第一沉积膜,包括步骤:
[0013]
第一沉积:在衬底表面沉积含铝前驱体,得到铝层;
[0014]
第一反应:将含氧前驱体与铝层进行反应,得到第一沉积层;
[0015]
循环进行所述第一沉积和所述第一反应,直至所述第一沉积层达到目标厚度时,得到第一沉积膜。
[0016]
可选的,所述将第二前驱体沉积在所述第一沉积膜表面,得到第二沉积膜,包括步
骤:
[0017]
第二沉积:在所述第一沉积膜表面沉积含钛前驱体,得到钛层;
[0018]
第二反应:将含氧前驱体与钛层进行反应,得到第二沉积层;
[0019]
循环进行所述第二沉积和所述第二反应,直至所述第一沉积层达到目标厚度时,得到第二沉积膜。
[0020]
第二方面,本技术还提供了一种复合膜,所述复合膜根据前述在贵金属表面制备复合膜的方法得到。
[0021]
可选的,所述复合膜的厚度为9~24nm,其中,第一沉积膜的厚度为7~14nm,第二沉积膜的厚度为2~10nm。
[0022]
可选的,所述复合膜的透射率大于等于92%,折射率为1.40-2.00。
[0023]
第三方面,本技术还提供了一种贵金属,包括贵金属基体和复合膜,所述复合膜沉积于所述贵金属基体,所述复合膜为前述复合膜。
[0024]
本技术实施例提供的上述技术方案与现有技术相比具有如下优点:
[0025]
本技术实施例通过首先在衬底上沉积第一前驱体,得到第一沉积膜,第一沉积膜的表面致密且能够很好地贴合贵金属表面,然后再将第二前驱体沉积在第一沉积膜表面,得到第二沉积膜,第二沉积膜性质更加稳定,不易被氧化或溶解。第一沉积膜与第二沉积膜共同组成复合膜,第一沉积膜贴合贵金属,增强复合膜的附着力和致密程度,第二沉积膜置于最外层,增强复合膜的化学稳定性和物理稳定性,进而使得复合膜具有良好的防贵金属腐蚀性能。
附图说明
[0026]
此处的附图被并入说明书中并构成本说明书的一部分,示出了符合本发明的实施例,并与说明书一起用于解释本发明的原理。
[0027]
为了更清楚地说明本发明实施例或现有技术中的技术方案,下面将对实施例或现有技术描述中所需要使用的附图作简单地介绍,显而易见地,对于本领域普通技术人员而言,在不付出创造性劳动性的前提下,还可以根据这些附图获得其他的附图。
[0028]
图1为本技术实施例提供的一种在贵金属表面制备复合膜的方法的流程图;
[0029]
图2为本技术实施例提供的复合膜的结构示意图;
[0030]
图3为本技术实施例提供的未在衬底表面制备的复合膜的防腐蚀性能实验示意图;
[0031]
图4为本技术实施例提供的在衬底表面制备的复合膜的防腐蚀性能实验示意图。
[0032]
图5为本技术实施例提供的未在衬底表面制备的复合膜的防划擦性能光学显微镜图像;
[0033]
图6为本技术实施例提供的在衬底表面制备的复合膜的防划擦性能光学显微镜图像;
[0034]
附图标记:
[0035]
1-衬底,2-第一沉积膜,3-第二沉积膜。
具体实施方式
[0036]
为使本技术实施例的目的、技术方案和优点更加清楚,下面将结合本技术实施例中的附图,对本技术实施例中的技术方案进行清楚、完整地描述,显然,所描述的实施例是本技术的一部分实施例,而不是全部的实施例。基于本技术中的实施例,本领域普通技术人员在没有做出创造性劳动的前提下所获得的所有其他实施例,都属于本技术保护的范围。
[0037]
第一方面,本技术提供了一种在贵金属表面制备复合膜的方法,包括步骤:
[0038]
s1、将第一前驱体沉积在衬底表面,得到第一沉积膜;
[0039]
s2、将第二前驱体沉积在所述第一沉积膜表面,得到第二沉积膜;
[0040]
其中,所述第一前驱体包括含氧前驱体和含铝前驱体,所述第二前驱体包括含氧前驱体和含钛前驱体。
[0041]
在本技术实施例中,所述步骤s1在150℃~250℃条件下进行,所述步骤s2在100℃~200℃条件下进行。
[0042]
本技术实施例通过首先在衬底上沉积第一前驱体,得到第一沉积膜,在本技术实施例中,第一沉积膜为三氧化二铝膜,三氧化二铝结构致密,一方面提高了和贵金属表面的结合力,能够防止三氧化二铝膜脱落,另一方面能够很好地配合贵金属表面的图案,第三方面致密的结构能够防止空气从结构孔隙中钻入,然后再将第二前驱体沉积在第一沉积膜表面,得到第二沉积膜,在本技术实施例中,第二沉积膜为二氧化钛膜,第二沉积膜性质更加稳定,不易被氧化或溶解。第一沉积膜与第二沉积膜共同组成复合膜,第一沉积膜贴合贵金属,增强复合膜的附着力和致密程度,第二沉积膜置于最外层,增强复合膜的化学稳定性和物理稳定性,进而使得复合膜具有良好的防贵金属腐蚀性能。
[0043]
具体地,所述步骤s1包括:
[0044]
s11、在衬底表面沉积含铝前驱体,得到铝层;
[0045]
s12、将含氧前驱体与铝层进行反应,得到第一沉积层;
[0046]
循环进行所述步骤s11和所述步骤s12,直至所述第一沉积层达到目标厚度时,得到第一沉积膜。
[0047]
所述步骤s2包括:
[0048]
s21、在所述第一沉积膜表面沉积含钛前驱体,得到钛层;
[0049]
s21、将含氧前驱体与钛层进行反应,得到第二沉积层;
[0050]
循环进行所述步骤s21和所述步骤s22,直至所述第一沉积层达到目标厚度时,得到第二沉积膜。
[0051]
在本技术实施例中,所述步骤s11具体包括:
[0052]
根据待含铝前驱体的类型,获得第一沉积参数;
[0053]
向沉积室内通入含铝前驱体,在所述第一沉积参数下将含铝前驱体沉积在衬底表面,得到铝层;
[0054]
向所述沉积室内通入惰性气体,清除所述沉积室内的含铝前驱体。
[0055]
在本技术实施例中,所述步骤s12具体包括:
[0056]
根据待含氧前驱体的类型,获得第一反应参数;
[0057]
向沉积室内通入含氧前驱体,在第一反应参数下将含氧前驱体与所述铝层进行反应,得到第一沉积层;
[0058]
向所述沉积室内通入惰性气体,清除所述沉积室内的含氧前驱体。
[0059]
在本技术实施例中,所述步骤s21具体包括:
[0060]
根据待含钛前驱体的类型,获得第二沉积参数;
[0061]
向沉积室内通入含钛前驱体,在第二沉积参数下将含钛前驱体沉积在第一沉积膜表面,得到钛层;
[0062]
向所述沉积室内通入惰性气体,清除所述沉积室内的含钛前驱体。
[0063]
在本技术实施例中,所述步骤s22具体包括:
[0064]
根据待含氧前驱体的类型,获得第二反应参数;
[0065]
向沉积室内通入含氧前驱体,在第二反应参数下将含氧前驱体与所述钛层进行反应,得到第二沉积层;
[0066]
向所述沉积室内通入惰性气体,清除所述沉积室内的含氧前驱体。
[0067]
在本技术实施例中,先将含铝前驱体沉积在贵金属的表面,形成铝层,使得贵金属表面被铝层完全覆盖,防止贵金属表面被含氧前驱体氧化;再通入含氧前驱体,使铝层转变为致密的三氧化二铝层,即可得到一层第一沉积层,如此反复多次,即可得到致密的三氧化二铝膜,即第一沉积膜。然后以同样的方法在第一沉积膜表面沉积出二氧化钛膜,即第二沉积膜。
[0068]
同时,在每次通入含铝前驱体、含钛前驱体或含氧前驱体后,均向沉积室内部通入惰性气体,将沉积过程中通入的前驱体清除,使得在进行下一步反应的时候,前一步残余的前驱体不会影响后续的反应。
[0069]
在一些实施例中,所述含铝前驱体包括alcl3、al(me)3、al(me)2cl、al(et)3和al(oet)3中的一种或多种。在本技术实施例中,将al(me)3作为含铝前驱体,该前驱体能与衬底表面结合致密,不对贵金属表面造成损伤。
[0070]
在一些实施例中,所述含钛前驱体包括ti[n(c2h5)2]4、ti[och(ch3)2]4、ticl4和ti[n(ch3)2]4中的一种或多种。在本技术实施例中,将ti[n(ch3)2]4作为含钛前驱体,该前驱体反应温度较低,易于反应,反应产物及副反应物呈惰性,不对贵金属表面造成损伤。
[0071]
在一些实施例中,所述含氧前驱体为o2、h2o2、h2o和o3中的一种或多种。在本技术实施例中,将h2o作为含氧前驱体,该前驱体的氧化性较低,不会造成贵金属氧化。
[0072]
在本技术实施例中,所述第一沉积参数为:
[0073]
薄膜生长温度:150℃~250℃;本底压强<10-3
torr;工艺压强:10-2
torr~1torr;气体流量:0sccm~100sccm;各前驱体剂量:80ms~104ms;载气吹扫时间:10s~100s;生长厚度:7nm~14nm。
[0074]
所述第一反应参数为:
[0075]
薄膜生长温度:150℃~250℃;本底压强<10-3
torr;工艺压强:10-2
torr~1torr;气体流量:0sccm~100sccm;各前驱体剂量:80ms~104ms;载气吹扫时间:10s~100s;生长厚度:7nm~14nm。
[0076]
所述第二沉积参数为:
[0077]
薄膜生长温度:100℃~200℃;本底压强<10-3
torr;工艺压强:10-2
torr~1torr;气体流量:0sccm~100sccm;各前驱体剂量:80ms~104ms;载气吹扫时间:10s~100s;生长厚度:2nm~10nm。
[0078]
所述第二反应参数为:
[0079]
薄膜生长温度:100℃~200℃;本底压强<10-3
torr;工艺压强:10-2
torr~1torr;气体流量:0sccm~100sccm;各前驱体剂量:80ms~104ms;载气吹扫时间:10s~100s;生长厚度:2nm~10nm。
[0080]
在本技术实施例的基础上,所述步骤s1之前,还包括步骤:
[0081]
采用无水乙醇溶液超声清洗所述衬底3min~30min,再采用去离子水超声清洗所述衬底3min~30min,最后用高纯氮气吹干所述衬底。通过对衬底进行预处理,去除贵金属表面的吸附的杂质,提高前驱体在贵金属表面的吸附性。
[0082]
在本技术实施例的基础上,所述采用无水乙醇溶液超声清洗所述衬底3min~30min,再采用去离子水超声清洗所述衬底3min~30min,最后用高纯氮气吹干所述衬底之后,还包括步骤:
[0083]
将所述沉积室抽真空。
[0084]
通过将沉积室抽真空,防止沉积第一前驱体时,沉积室内存在的氧气将贵金属氧化。
[0085]
在本技术实施例的基础上,所述步骤s2之后,还包括步骤:
[0086]
向所述沉积室内通入高纯载气,使沉积室内气压与大气压相等,取出沉积有复合膜的衬底。
[0087]
由于此前步骤将沉积室内抽真空,设置此步骤通过向沉积室内通入载气,以使沉积室的门能够被打开。
[0088]
如图2所示,第二方面,本技术还提供了一种复合膜,所述复合膜根据前述在贵金属表面制备复合膜的方法得到,包括第一沉积膜和第二沉积膜。
[0089]
在一些实施方式中,所述复合膜的厚度为9~24nm,其中,第一沉积膜2的厚度为7~14nm,第二沉积膜3的厚度为2~10nm。在此厚度下,所述复合膜的透射率大于等于92%,折射率为1.40-2.00,不影响贵金属的光泽度。在本技术实施例中,第一沉积膜2为三氧化二铝膜,第二沉积膜3为二氧化钛膜。
[0090]
实施例:
[0091]
s1、将沉积室的第一沉积参数设置为:薄膜生长温度:150℃~250℃;本底压强<10-3
torr;工艺压强:10-2
torr~1torr;气体流量:0sccm~100sccm;各前驱体剂量:80ms~104ms;载气吹扫时间:10s~100s;生长厚度:7nm~14nm;
[0092]
s2、向沉积室内通入含铝前驱体al(me)3,在所述第一沉积参数下将含铝前驱体沉积在衬底表面,得到铝层;
[0093]
s3、向所述沉积室内通入氮气,清除所述沉积室内的含铝前驱体。
[0094]
s4、将沉积室的第一反应参数设置为:薄膜生长温度:150℃~250℃;本底压强<10-3
torr;工艺压强:10-2
torr~1torr;气体流量:0sccm~100sccm;各前驱体剂量:80ms~104ms;载气吹扫时间:10s~100s;生长厚度:7nm~14nm;
[0095]
s5、向沉积室内通入含氧前驱体h2o,在第一反应参数下将含氧前驱体与所述铝层进行反应,得到第一沉积层;
[0096]
s6、循环进行所述步骤s1-s5,直至所述第一沉积层达到目标厚度时,得到第一沉积膜;
[0097]
s7、向所述沉积室内通入氮气,清除所述沉积室内的含氧前驱体。
[0098]
s8、将沉积室的第二沉积参数设置为:薄膜生长温度:100℃~200℃;本底压强<10-3
torr;工艺压强:10-2
torr~1torr;气体流量:0sccm~100sccm;各前驱体剂量:80ms~104ms;载气吹扫时间:10s~100s;生长厚度:2nm~10nm;
[0099]
s9、向沉积室内通入含钛前驱体ti[n(ch3)2]4,在第二沉积参数下将含钛前驱体沉积在第一沉积膜表面,得到钛层;
[0100]
s10、向所述沉积室内通入氮气,清除所述沉积室内的含钛前驱体。
[0101]
s11、将沉积室的第二反应参数设置为:薄膜生长温度:100℃~200℃;本底压强<10-3
torr;工艺压强:10-2
torr~1torr;气体流量:0sccm~100sccm;各前驱体剂量:80ms~104ms;载气吹扫时间:10s~100s;生长厚度:2nm~10nm;
[0102]
s12、向沉积室内通入含氧前驱体h2o,在第二反应参数下将含氧前驱体与所述钛层进行反应,得到第二沉积层;
[0103]
s13、向所述沉积室内通入氮气,清除所述沉积室内的含氧前驱体。
[0104]
s14、循环进行所述步骤s7-s13,直至所述第一沉积层达到目标厚度时,得到第二沉积膜。
[0105]
对比例:
[0106]
在本对比例中,贵金属表面无二氧化硅膜。
[0107]
通过将表面制备有复合膜的贵金属放置于常温浓度为0.1%~5%的k2s溶液中静置验证所述复合膜防贵金属腐蚀性能。
[0108]
具体地,测试防贵金属腐蚀性能的方法为:
[0109]
将未制备复合膜的衬底1及制备复合膜的衬底2放入常温浓度为0.1%~5%的k2s溶液中静置120分钟,每隔30分钟记录表面情况。
[0110]
测试复合膜的耐划擦性能的方法为:
[0111]
将未制备复合膜的衬底1及制备复合膜的衬底2用手进行擦拭,施加200g~500g的载荷进行匀速的来回擦拭。
[0112]
测试结果如图3-图6所示,从图3和图4能看出,图3中银币的右上部出现了明显的腐蚀区域,图4中未出现明显腐蚀区域,相对于图3中未制备复合膜的衬底1,图4中复合膜对贵金属表面起到了有效的防腐蚀作用;从图5和图6能看出,图5中出现了明显的纵向划痕,图6中未出现明显划痕,相对于图5中未制备复合膜的衬底1,图6中复合膜对贵金属表面起到了有效的防划擦作用。
[0113]
第三方面,本技术还提供了一种贵金属,包括贵金属基体和复合膜,所述复合膜沉积于所述贵金属基体,所述复合膜为前述复合膜。
[0114]
需要说明的是,在本文中,诸如“第一”和“第二”等之类的关系术语仅仅用来将一个实体或者操作与另一个实体或操作区分开来,而不一定要求或者暗示这些实体或操作之间存在任何这种实际的关系或者顺序。而且,术语“包括”、“包含”或者其任何其他变体意在涵盖非排他性的包含,从而使得包括一系列要素的过程、方法、物品或者设备不仅包括那些要素,而且还包括没有明确列出的其他要素,或者是还包括为这种过程、方法、物品或者设备所固有的要素。在没有更多限制的情况下,由语句“包括一个
……”
限定的要素,并不排除在包括所述要素的过程、方法、物品或者设备中还存在另外的相同要素。
[0115]
以上所述仅是本发明的具体实施方式,使本领域技术人员能够理解或实现本发明。对这些实施例的多种修改对本领域的技术人员来说将是显而易见的,本文中所定义的一般原理可以在不脱离本发明的精神或范围的情况下,在其它实施例中实现。因此,本发明将不会被限制于本文所示的这些实施例,而是要符合与本文所申请的原理和新颖特点相一致的最宽的范围。