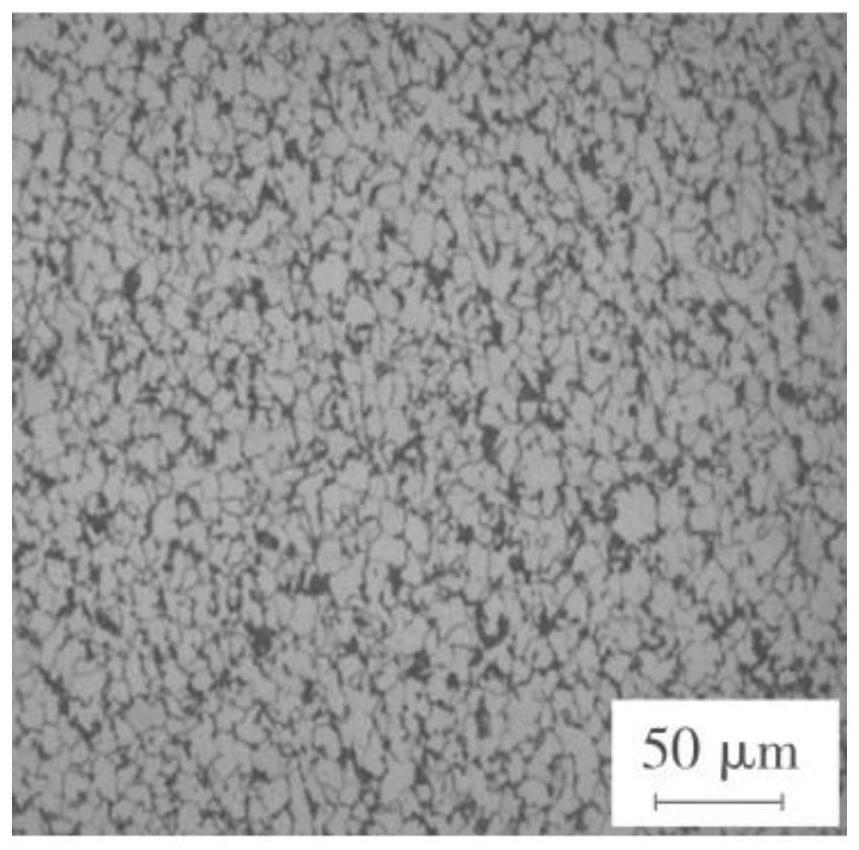
1.本发明涉及一种高冷镦成型性低碳低硅含铝冷镦钢热轧盘条及其制备方法,属于钢材制备领域。
背景技术:2.低碳低硅含铝冷镦钢用于制造紧固件、连接件,要求具有较好的塑性和冷加工性能,c、si、mn、p、s、al各元素的含量不同设计及综合匹配,对抗拉强度、屈服强度、塑性、韧性会、变形抗力、冷镦变形能力都有较大的影响。低碳低硅冷镦钢冶炼过程中经常出现增碳、增硅和回磷的情况,混晶时有发生,冷镦变形过程中也易出现比较严重的表面开裂,力学性能和工艺性能也不够稳定,严重影响产品质量。影响冷镦钢成型性主要因素包括钢的化学成分、表面质量、钢的纯净度、晶粒度和组织状态,合理的成分设计与控制,良好的表面质量、钢的纯净度、晶粒度和组织状态是获得高冷镦成型性的关键。
3.现有同类材料及技术,如cn202011637191.4一种高性能低硅冷镦钢的生产方法等,未能实现在简单工艺路径下,采用低的合金成分设计,制备良好表面质量、纯净度、晶粒度、综合力学性能和组织状态的热轧盘条产品,其冷镦成型性也有不足。
技术实现要素:4.本发明的目的在于提供一种高冷镦成型性低碳低硅含铝冷镦钢qqgch22a热轧盘条及其制备方法。
5.一种高冷镦成型性低碳低硅含铝冷镦钢热轧盘条,所述高冷镦成型性低碳低硅含铝冷镦钢热轧盘条的合金组分为:0.19~0.24%c,≤0.07%si,0.70~0.90%mn,≤0.015%p,≤0.010%s,≤0.035%ni,≤0.03%cr,≤0.05%cu,0.025~0.040%alt,其余为fe。
6.本发明所述成品盘条显微组织为铁素体及少量珠光体,晶粒度9~10级,抗拉强度460~510mpa,断面收缩率不小于50%。
7.本发明所述高冷镦成型性低碳低硅含铝冷镦钢热轧盘条化学成分设计如下:0.19~0.24%c,≤0.07%si,0.70~0.90%mn,≤0.015%p,≤0.010%s,≤0.035%ni,≤0.03%cr,≤0.05%cu,0.025~0.040%alt,其余为fe。
8.本发明的另一目的提供上述高冷镦成型性低碳低硅含铝冷镦钢热轧盘条的制备方法。
9.一种高冷镦成型性低碳低硅含铝冷镦钢热轧盘条的制备方法,所述工艺依次包括转炉冶炼、lf炉精炼、连铸、加热炉加热和轧制的步骤,其中转炉冶炼为:原料为铁水和废钢,其中,废钢占比6~10%;氧气顶底复吹,出钢温度1665~1685℃,出钢终点c≥0.040%,p≤0.012%,严禁下渣;采用钢包合金化,出钢过程加入石灰24~48kg/t,以及1.8~2.4kg/t硅锰和6~8kg/t高碳锰铁;冶炼周期40~50min;静吹氩时间10~20min,处理前温度1610
~1630℃,处理后温度1580~1600℃,静吹氩后喂纯钙包芯线1~1.2kg/t。
10.本发明所述高冷镦成型性低碳低硅含铝冷镦钢热轧盘条的制备方法,所述lf炉精炼为:到站温度1570~1590℃,加入活性石灰6~8.5kg/t及萤石0.70~0.85kg/t造白渣,添加电石0.2~0.47kg/t调整渣的碱度及流动性,lf精炼时间65min~85min,加入铝粒1.3~1.5kg/t进行沉淀脱氧;根据全分析结果,采用增碳剂、硅锰和中碳锰铁微调化学成分,保证满足内控要求:0.20~0.23%c,≤0.06%si,0.72~0.85%mn,≤0.015%p,≤0.008%s,≤0.030%ni,≤0.03%cr,≤0.03%cu,0.028~0.038%alt;静吹氩时间12~20min,喂铝线0.2~0.3kg/t进行终脱氧。
11.本发明所述高冷镦成型性低碳低硅含铝冷镦钢热轧盘条的制备方法,所述连铸为:结晶器电磁搅拌采用正反转交替转动模式,电流280a,频率5hz,正转6s,停6s,反转6s,过热度保持35~45℃,拉速2.2~2.6m/min;全过程保护浇铸,结晶器保护渣使用中碳钢保护渣。
12.本发明所述高冷镦成型性低碳低硅含铝冷镦钢热轧盘条的制备方法,所述加热炉加热为:采用推钢式加热炉加热,预热段温度880
±
30℃,时间60~80min;加热段1100
±
30℃,时间60~80min;均热段1150
±
30℃,时间30~50min;总加热时间2.5~3.5h。
13.本发明所述高冷镦成型性低碳低硅含铝冷镦钢热轧盘条的制备方法,所述轧制工艺为:粗轧温度:980
±
10℃;精轧入口温度:870
±
10℃;吐丝温度:870
±
10℃;联合使用风冷辊道及保温罩调整线材冷速,设定头部辊道速度0.09~0.12m/s,调整保温通道长度,控制冷速0.95~1.05℃/s;机前采用高压水除磷去除氧化铁皮,水压≥14mpa。
14.本发明所述高冷镦成型性低碳低硅含铝冷镦钢热轧盘条的制备方法还包括制备钢材的常规步骤,如在转炉冶炼步骤前还包括高炉铁水、铁水预处理(脱s、扒渣)的步骤;在轧制吐丝后包括检查、集卷、保温通道缓冷、检验、包装交库等工艺步骤,上述工艺步骤按现有技术公开的方式进行,满足工艺要求即可。
15.本发明的有益效果为:
16.1、低碳低硅加铝加锰的合金成分设计,保证热轧盘条冷变形硬化率低,强度和塑性、韧性匹配良好,不易混晶,具有良好的冷成型性。
17.2、采用该制备方法生产的热轧盘条,尺寸精度达到gb/t1 4981中b+,过程表面氧化铁皮去除良好,成品氧化铁皮结构、厚度合理,拉丝前可有效机械除磷,成品金相组织均匀,晶粒度细小,无混晶,强度适中,韧、塑性良好。
18.3、热轧盘条金属制品生产过程中冷镦比已达到1/4,冷镦成型性良好。
附图说明
19.图1为高冷镦成型性低碳低硅含铝冷镦钢热轧qqgch22a盘条横向金相组织照片。从图中可以看出,成品盘条金相组织为铁素体及少量珠光体组织,组织均匀致密,晶粒度9.5级。
具体实施方式
20.下述非限制性实施例可以使本领域的普通技术人员更全面地理解本发明,但不以任何方式限制本发明。
21.下述实施例中所述试验方法,如无特殊说明,均为常规方法;所述试剂和材料,如无特殊说明,均可从商业途径获得。
22.具体实施方式之一:
23.一种高冷镦成型性低碳低硅含铝冷镦钢热轧盘条:
24.一、化学成分设计
25.热轧盘条qqgch22a化学成分设计如下:0.19~0.24%c,≤0.07%si,0.70~0.90%mn,≤0.015%p,≤0.010%s,≤0.035%ni,≤0.03%cr,≤0.05%cu,0.025~0.040%alt,其余为fe
26.本发明所述高冷镦成型性低碳低硅含铝冷镦钢热轧盘条成分设计原理如下:
27.c含量对冷镦钢的综合力学性能有较大的影响,c含量高,其抗拉强度、屈服强度高,塑性、韧性相应较低,变形抗力增大,冷镦变形能力差低,因此,冷镦钢c含量的范围,一定设计合理且保证在窄的范围内波动,以获得较好的冷镦性能。
28.si能提高冷镦钢的抗拉强度、屈服强度、硬度,降低塑性和韧性,但si含量增高,其强度、硬度提高,塑韧性降低,变形抗力增大,冷镦变形能力就会降低,而且还会使钢中的c、d夹杂物数量增加,在冷镦变形时引起冷镦开裂,所以si含量应偏低控制。
29.mn能提高钢的强度,降低钢的塑韧性,适当含量的mn,不会对冷镦性能造成较大的影响,但mn含量较高,冷镦成型将较为困难。
30.p降低钢的塑性,容易引起冷脆,发生断裂,在冷镦钢中能促进延迟断裂,含量越低越好。
31.s在钢中以硫化物的形式偏聚在晶界,降低冷镦性能。在含铝冷镦钢生产过程中,水口容易出现堵塞,它的存在还会降低标准件强度,因此,应严格控制s含量,越低越好。
32.al作为强脱氧剂,配合钙处理用来深脱氧并控制夹杂物的含量和尺寸,同时细化晶粒,提高拉拔和冷镦性能。
33.二、制备方法
34.1、工艺步骤:高炉铁水
→
铁水预处理(脱s、扒渣)
→
转炉(顶底复吹)
→
lf炉精炼
→
小方坯连铸(150mm
×
150mm)
→
加热炉加热
→
盘条轧制
→
吐丝
→
检查
→
集卷
→
保温通道缓冷
→
检验
→
包装交库
35.2、关键工艺
36.转炉冶炼:原料为铁水和废钢,其中,废钢占比6~10%;氧气顶底复吹,出钢温度1665~1685℃,出钢终点c≥0.040%,p≤0.012%,严禁下渣;采用钢包合金化,出钢过程加入石灰24~48kg/t,以及1.8~2.4kg/t硅锰和6~8kg/t高碳锰铁;冶炼周期40~50min;静吹氩时间10~20min,处理前温度1610~1630℃,处理后温度1580~1600℃,静吹氩后喂纯钙包芯线1kg~1.2kg/t。
37.lf炉精炼:到站温度1570~1590℃,加入活性石灰6~8.5kg/t及萤石0.70~0.85kg/t造白渣,添加电石0.2~0.47kg/t调整渣的碱度及流动性,lf精炼时间65min~85min,加入铝粒1.3~1.5kg/t进行沉淀脱氧;根据全分析结果,采用增碳剂、硅锰和中碳锰铁微调化学成分,保证满足内控要求:0.20~0.23%c,≤0.06%si,0.72~0.85%mn,≤0.015%p,≤0.008%s,≤0.030%ni,≤0.03%cr,≤0.03%cu,0.028~0.038%alt;静吹氩时间12~20min,喂铝线0.2~0.3kg/t进行终脱氧。
38.连铸:结晶器电磁搅拌采用正反转交替转动模式,电流280a,频率5hz,正转6s,停6s,反转6s,过热度保持35~45℃,拉速2.2~2.6m/min;全过程保护浇铸,结晶器保护渣使用中碳钢保护渣。
39.加热工艺:采用推钢式加热炉加热,预热段温度880
±
30℃,时间60~80min;加热段1100
±
30℃,时间60~80min;均热段1150
±
30℃,时间30~50min;总加热时间2.5~3.5h。
40.轧制工艺:粗轧温度:980
±
10℃;精轧入口温度:870
±
10℃;吐丝温度:870
±
10℃;联合使用风冷辊道及保温罩调整线材冷速,设定头部辊道速度0.09~0.12m/s,适当调整保温通道长度,控制冷速0.95~1.05℃/s;机前采用高压水除磷去除氧化铁皮,水压≥14mpa。
41.控制成品盘条显微组织为铁素体+少量珠光体,晶粒度9~10级,抗拉强度不大于460~510mpa,断面收缩率不小于50%。
42.该制备方法采用高炉铁水
→
铁水预处理(脱s、扒渣)
→
转炉(顶底复吹)
→
lf炉精炼
→
小方坯连铸(150mm
×
150mm)
→
加热炉加热
→
盘条轧制
→
吐丝
→
检查
→
集卷
→
保温通道缓冷
→
检验
→
包装交库工艺路线,生产制造qqgch22a钢热轧盘条,满足了强度、韧性等综合力学性能要求,钢质纯净度高、晶粒细小、组织均匀、表面质量良好,拉拔加工性能和冷镦成型性优良,冷镦比已达到1/4。
43.实施例1
44.采用本发明的技术方案制造高冷镦成型性热轧盘条qqgch22a最佳实施案例,其化学成分如下,余量fe:
45.%
46.熔炼号csimnpscrnicualt2e216340.230.060.790.0140.0080.02970.01090.01050.036
47.具体实施生产步骤如下:
48.1、转炉冶炼
49.原料铁水151t,废钢配入14.6t,废钢占比8.82%;氧气顶底复吹,出钢温度1684℃,出钢终点c:0.116%,p:0.011%,严禁下渣;采用钢包合金化,出钢过程加入石灰6808kg,硅锰359kg,和高碳锰铁1162kg;冶炼周期41min;静吹氩时间14min,处理前温度1625℃,处理后温度1592℃,静吹氩后喂纯钙包芯线172kg。
50.2、lf炉精炼
51.到站温度1575℃,加入活性石灰1113kg,萤石115kg造白渣,添加电石60kg调整渣的碱度及流动性;lf精炼时间82min,加入铝粒202kg进行沉淀脱氧;根据全分析结果,加入增碳剂30kg,中碳锰铁80kg微调化学成分,保证满足内控要求:0.20~0.23%c,≤0.06%si,0.72~0.85%mn,≤0.015%p,≤0.008%s,≤0.030%ni,≤0.03%cr,≤0.03%cu,0.028~0.038%alt;静吹氩时间12~20min;静吹氩时间14min,喂铝线38kg进行终脱氧。
52.3、连铸
53.结晶器电磁搅拌采用正反转交替转动模式,电流280a,频率5hz,正转6s,停3s,反转6s。过热度保持38℃,拉速2.5m/min。全过程保护浇铸,结晶器保护渣使用中碳钢保护渣。
54.4、加热工艺
55.采用推钢式加热炉加热,预热段温度900℃,时间70min,加热段1080℃,时间70min,均热段1130℃,时间40min,总加热时间3h。
56.5、轧制工艺
57.产品规格φ6.5mm,粗轧温度990℃,精轧入口温度880℃,吐丝温度:880℃;联合使用风冷辊道及保温罩调整线材冷速风冷辊道速度,设定头部辊道速度0.12m/s,保温罩1、2号关闭,其余打开,控制冷速1.0℃/s,机前高压水水压15mpa除磷处理。
58.6、成品性能
59.成品盘条抗拉强度498mpa,断面收缩率64%,显微组织为铁素体+少量珠光体,晶粒度9.5级。
60.上述高冷镦成型性低碳低硅含铝冷镦钢热轧盘条的制备方法还包括制备钢材的常规步骤,如在转炉冶炼步骤前还包括高炉铁水、铁水预处理(脱s、扒渣)的步骤;在轧制吐丝后包括检查、集卷、保温通道缓冷、检验、包装交库等工艺步骤,上述工艺步骤按现有技术公开的方式进行,满足工艺要求即可。