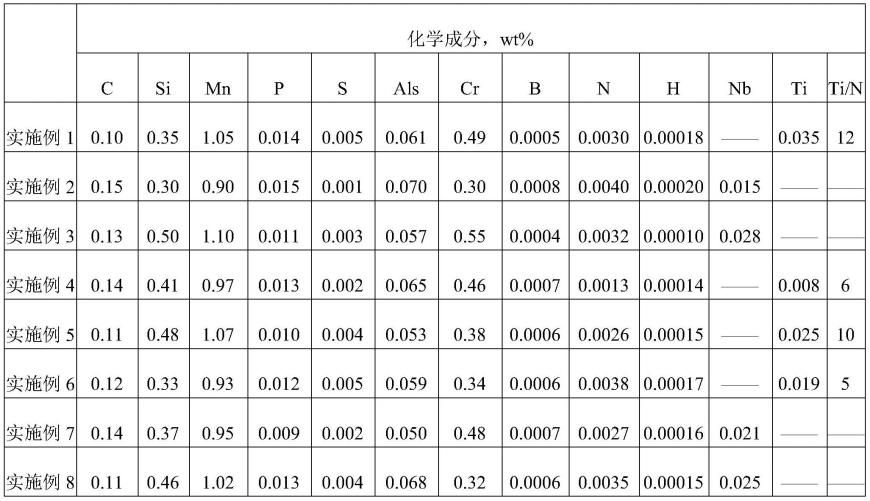
布氏硬度360hbw高强度、高韧性热连轧薄钢板的生产方法
技术领域
1.本发明涉及布氏硬度360hbw钢板的生产方法,尤其涉及布氏硬度360hbw高强度、高韧性热连轧薄钢板的生产方法。
背景技术:2.在绿色制造、低碳环保的大背景下,国内工程机械、商用车等行业越来越重视以高强减重、绿色长寿为方向的产品结构升级,对钢铁材料提出了更高强、更耐磨、更耐蚀等高要求。
3.近年来我国在高强钢研发生产方面进展明显,工程机械用户开始采用屈服960mpa以上的超高强结构钢制造起重机吊臂和泵车布料杆。自卸车用户开始使用屈服强度700mpa甚至1000mpa级以上钢板替代345mpa级别产品。但在冶金、矿山、建材、运输等领域中,许多工件及设备由于磨损而迅速失效,造成材料、能源的巨大浪费,需要钢板还具备高硬度、高耐磨性,降低钢板磨损,延长钢板使用寿命。
技术实现要素:4.为了克服现有技术的不足,提供一种布氏硬度360hbw高强度、高韧性热连轧薄钢板的生产方法,按照本发明钢的化学成分及生产工艺要求生产的产品具有高强度、高韧性、低成本,且布氏硬度360hbw,同时具有良好耐磨性。
5.为了达到上述目的,本发明采用以下技术方案实现:
6.一种布氏硬度360hbw高强度、高韧性热连轧薄钢板,厚度≤10mm,由如下重量百分含量的化学元素组成:
7.c:0.10%~0.15%,si:0.30%~0.50%,mn:0.90%~1.10%,p≤0.015%,s≤0.005%,als:0.050%~0.070%,cr:0.30%~0.55%,b:0.0004%~0.0008%,n≤0.0040%,h≤0.00020%;另外含有nb:0.010%~0.028%、ti:0.008%~0.035%中的一种或两种,若含ti,则需满足ti/n≥5,其余为fe和不可避免杂质。
8.一种布氏硬度360hbw高强度、高韧性热连轧薄钢板的生产方法,具体包括:
9.1)冶炼、铸造
10.按上述成分冶炼、铸造成坯;
11.2)板坯再加热
12.板坯热装入炉,装炉温度≥500℃,加热温度1180~1230℃,保温时间1.5~3.5h,其中均热保温时间不小于35min;
13.3)控制轧制
14.轧制分为粗轧和精轧两个阶段,粗轧阶段采用大压下量轧制,控制道次压下率在18%以上,同时要求中间坯与成品的厚度比≥5,并控制精轧最后一道次压下率不低于12%;终轧温度控制在850~910℃;
15.4)卷取
16.卷取温度控制在685~730℃;
17.5)热处理采用整卷连续热处理方式,淬火
→
回火
→
矫直
→
切板;
18.淬火:加热温度控制在钢种ac3点以上55~100℃,加热温度880~930℃;钢带首先采用中频感应以5~10hz的频率加热到650~700℃,然后加热到淬火温度并保温;
19.回火:钢带淬火后随即进入回火炉,在190~230℃进行回火处理并保温;
20.矫直:钢板的不平度控制在≤3mm/m;
21.切板:钢板的对角线切斜不超过10mm。
22.所述步骤5淬火保温时间为t1,t1=钢板厚度
×
(1.8~2.3)min,钢板厚度单位为mm,t1单位为min。
23.所述步骤5回火保温时间为t2,t2=钢板厚度
×
(3.2~4.0)min,钢板厚度单位为mm,t2单位为min。
24.所述步骤5回火后采用强力矫直机对钢板进行矫直,保证钢板板形及不平度。
25.与现有技术相比,本发明的有益效果是:
26.1)本发明采用经济的c-mn成分设计,辅以少量的nb、ti微合金元素,不需要加入ni、mo等贵重合金元素,进而大幅度降低了生产成本。
27.2)淬火加热温度直接影响后续马氏体组织的粒度,进而影响钢板的韧性。加热温度过高容易使奥氏体晶粒粗化,淬火后马氏体组织粗大,韧性恶化;而加热温度偏低则导致奥氏体化不充分,淬火后无法获得完全马氏体组织,并且避免由于薄钢板降温速度快,出保温炉进入淬火机前温降快不能保证淬火温度。保温时间对淬火性能也有类似的规律,时间过长容易使得晶粒粗大,同时增加能耗,提高成本,时间过短则奥氏体化不充分,淬火后硬度、强度达不到要求。本发明淬火加热升温过程采取中频快速加热,进一步降低微合金元素加入,实现了钢种的高强度、高硬度、良好的低温冲击韧性和冷弯加工性能,并且钢板具有优良的板形。
28.本发明实现≤10mm厚度高硬度高耐磨性钢板的生产,钢板的屈服强度在900mpa以上,抗拉强度超过1100mpa,延伸率≥14%,硬度360
±
20hbw,-40℃冲击功值超过33j,钢板的不平度控制在3mm/m以内。
具体实施方式
29.本发明公开了一种布氏硬度360hbw高强度、高韧性热连轧薄钢板的生产方法。本领域技术人员可以借鉴本文内容,适当改进工艺参数实现。特别需要指出的是,所有类似的替换和改动对本领域技术人员来说是显而易见的,它们都被视为包括在本发明。本发明的方法及应用已经通过较佳实施例进行了描述,相关人员明显能在不脱离本发明内容、精神和范围内对本文所述的方法和应用进行改动或适当变更与组合,来实现和应用本发明技术。
30.一种布氏硬度360hbw高强度、高韧性热连轧薄钢板,厚度≤10mm,由如下重量百分含量的化学元素组成:
31.c:0.10%~0.15%,si:0.30%~0.50%,mn:0.90%~1.10%,p≤0.015%,s≤0.005%,als:0.050%~0.070%,cr:0.30%~0.55%,b:0.0004%~0.0008%,n≤0.0040%,h≤0.00020%;另外含有nb:0.010%~0.028%、ti:0.008%~0.035%中的一种
或两种,若含ti,则需满足ti/n≥5,其余为fe和不可避免杂质。
32.在本发明钢的成分设计中:
33.c:0.10%~0.15%。碳可提高钢板的淬透性,具有强烈的固溶强化作用,显著提高高耐磨性的马氏体耐磨钢板的强度和硬度;适当含量的碳与钛结合形成tic粒子,可显著改善耐磨性。c重量百分含量过高,形成的tic粒子的体积分数过高,高耐磨性的马氏体耐磨钢板的延伸率、冲击功性能降低,焊接性能变差。
34.si:0.30%~0.50%。si在钢种起固溶强化的作用,在金属材料中添加si元素可以明显的提高材料的强度和硬度。si还可以提高材料的抗回火性能,因此可以使材料在较高的温度下进行使用。
35.mn:0.90%~1.10%。在金属材料中添加mn元素可以起到是扩大奥氏体区的作用,除此之外该元素还可以明显的提高钢的淬透性,因此,在相同的冷却速度下可以得到更多的马氏体组织。mn含量的增多会加重钢的高温回火脆性以及热敏性。
36.p≤0.015%,s≤0.005%。硫在钢中与锰等化合形成塑性夹杂物硫化锰,尤其对钢的横向塑性和韧性不利,因此硫的含量应尽可能地低。磷也是钢中的有害元素,严重损害钢板的塑性和韧性。对于本发明而言,硫和磷均是不可避免的杂质元素,应该越低越好。
37.cr:0.30%~0.55%。可以缩小奥氏体相区。由于铬原子与碳原子的结合能力突出,能与钢中的碳形成不同的碳化物。与此同时,铬有时可以将渗碳体中的一些铁原子进行置换,从而形成含铬原子的渗碳体。cr还可以将钢的淬透性提高,这是因为该元素在渗碳体中的量要大于在固溶体中的量,因此在发生相变的时候cr会必然的从渗碳体往固溶体中扩散,然而由于奥氏体晶间间隙小,扩散较为困难,而在扩散过程中cr要与c原子进行结合,这就导致c元素扩散速度也将减慢,最终导致奥氏体分解时间延迟。
38.als:0.05%~0.07%。通常在炼钢过程中作为脱氧剂在钢中添加,微量的al同时有利于细化晶粒,改善钢材的强韧性能。但过高的al将使钢中铁素体脆性增加而导致钢韧性的降低。
39.b:0.0004%~0.0008%。钢中固溶的b偏聚到奥氏体晶界处使界面能降低,阻碍了铁素体晶核的形成,从而延长先共析铁素体和上贝氏体转变的孕育期,而对下贝氏体和马氏体转变基本上没有什么影响,因而b在低合金耐磨钢的主要作用是极大地提高钢的淬透性。同时以微量b替代部分ni、cr和mo等贵重合金元素,有利于节约合金成本。当b含量过高后,奥氏体晶界上过量的固溶b与c结合,降低钢的淬透性和冲击韧性,钢的断裂方式也从解理断裂逐渐转变为沿晶断裂。
40.ti:0.008%~0.035%,ti/n≥5。ti是非常活泼的金属元素,与o、n和c等元素都有极强的亲和力。在熔炼过程中,ti可以优先与n结合形成tin,能够抑制bn的形成,保证b元素固溶于基体中。另外,在凝固过程中,析出的tin能作为初生相&-铁素体的异质形核核心,并可降低铁素体与液相向奥氏体转变的包晶反应速率,阻碍随后的奥氏体枝晶长大,从而明显细化凝固组织。
41.nb:0.010%~0.028%。是强烈的碳氮化物形成元素,在钢中的作用与ti类似,主要是通过形成细小稳定的mx型析出相,起到高温下抑制晶粒长大和低温下沉淀强化的微合金化作用。尤其是与控轧控冷等热变形技术相结合时,nb微合金化的作用效果更加明显。另外,在低温回火过程中,nb可以延迟碳化物的析出和残余奥氏体的分解,提高回火组织的稳
定性。
42.一种布氏硬度360hbw高强度高韧性连轧薄钢板的生产方法,包括如下步骤:
43.1)冶炼、铸造
44.按上述成分冶炼、铸造成坯。
45.2)板坯再加热
46.板坯需要热装入炉,装炉温度≥500℃,加热温度1180~1230℃,保温时间1.5h~3.5h,其中均热保温时间不小于35min。
47.3)控制轧制
48.轧制分为粗轧和精轧两个阶段,粗轧阶段采用大压下量轧制,控制道次压下率在18%以上,同时要求中间坯与成品的厚度比≥5,并控制精轧最后一道次压下率不低于12%;终轧温度控制在850~910℃。
49.4)卷取
50.卷取温度控制在685~730℃。
51.5)热处理采用整卷连续热处理方式,淬火
→
回火
→
矫直
→
切板。
52.淬火,加热温度控制在钢种ac3点以上55~100℃,加热温度880~930℃;钢带首先采用中频感应以10hz的频率快速加热到650~700℃,热后采用电阻炉加热到淬火温度并保温。保温时间t1,min=钢板厚度mm
×
(1.8-2.3)min,钢带出炉后直接水淬至室温,形成马氏体组织,要求冷速≥30℃/s。
53.回火,钢带淬火后随即进入回火炉,在190~230℃区间进行回火处理,回火保温时间t1,min=钢板厚度mm
×
(3.2-4.0)min。回火后钢板基体为回火马氏体组织,具有合适的硬度及良好的低温冲击韧性,同时改善冷弯性能。
54.回火后线利用强力矫直机对钢板进行矫直,保证钢板板形及不平度,钢板的不平度控制在3mm/m以内,最后对钢板切板,要求钢板的对角线切斜不超过10mm。
55.在本发明钢板的生产方法中:
56.板坯需要热装入炉,装炉温度≥500℃,一是铸坯放冷至常温后,发生开裂的倾向就会大幅增加,威胁生产安全,二十可以能够降低能源消耗。加热温度1180~1230℃,保温时间1.5~3.5h,其中均热保温时间不小于35min,是为保证铸坯烧均烧透,为轧制提供有力条件,但又不至于出现过烧情况而造成脱碳现象发生。轧制分为粗轧和精轧两个阶段,为获得细的原始奥氏体晶粒度,铸坯在粗轧阶段采用大压下量轧制,控制道次压下率在18%以上或道次压下量42mm以上。为获得细的晶粒度及良好的板形,同时要求中间坯与成品的厚度比≥5,并控制精轧最后一道次压下率不低于12%,以保证变形超过临界变形量,从而获得良好的板形及均匀的基体组织。
57.由于本发明涉及钢种在轧后采用离线热处理,对铸坯的轧制温度无特别要求。但为了降低轧制载荷,所以采用尽量高的终轧温度,较高的卷取温度也是为了降低卷取机载荷和保证良好的卷形。
58.热处理采用整卷连续热处理方式具有处理效率高的优点,并且在热处理过程中,钢带一直在机组中一直是带张力运行,可以有效的保证钢板在热处理过程中和热处理后具有良好的原始板形。钢板采用中频快速加热,一个是可以提高钢板的升温速度,二是可以有效的避免晶粒长大,从而获得细的原始奥氏体晶粒度,有效的提高钢板淬火厚度强度和硬
度,起到节约合金的作用。
59.淬火加热温度直接影响后续马氏体组织的粒度,进而影响钢板的韧性。加热温度过高容易使奥氏体晶粒粗化,淬火后马氏体组织粗大,韧性恶化;而加热温度偏低则导致奥氏体化不充分,淬火后无法获得完全马氏体组织,并且避免由于薄钢板降温速度快,出保温炉进入淬火机前温降快不能保证淬火温度。保温时间对淬火性能也有类似的规律,时间过长容易使得晶粒粗大,同时增加能耗,提高成本,时间过短则奥氏体化不充分,淬火后硬度、强度达不到要求。淬火,加热温度控制在钢种ac3点以上55℃-100℃,加热温度880℃-930℃;钢带首先采用中频感应以10hz的频率快速加热到650~700℃,热后采用电阻炉加热到淬火温度并保温。保温时间t1,min=钢板厚度mm
×
(1.8.0-2.3)min,钢带出炉后直接水淬至室温,形成马氏体组织,要求冷速≥30℃/s。
60.回火主要是减缓、消除淬火应力,改善韧性和韧性。较高的回火温度容易使得钢板的强度、硬度降低过多,无法满足设计要求,同时成本增加。所以应对钢板的回火工艺参数加以限定。本发明中对钢板在190~230℃区间进行回火处理,回火保温时间t1,min=钢板厚度mm
×
(3.2-4.0)min。对淬火、回火的钢板进行冷矫直,保证钢板板形及不平度,钢板的不平度控制在3mm/m,最后对钢板切板,要求钢板的对角线切协不超过10mm。
61.实施例:
62.本发明实施例的化学成分见表1;相应实施例的轧制工艺见表2;相应实施例的热处理工艺见表3;相应实施例的力学性能和钢板不平度见表4。
63.表1本发明实施例的化学成分wt%
[0064][0065]
表2本发明实施例的轧制工艺
[0066][0067]
表3本发明实施例的热处理工艺
[0068][0069]
表4本发明实施例的力学性能和钢板不平度
[0070][0071]
本发明采用经济的c-mn成分设计,辅以少量的nb、ti微合金元素,不需要加入ni、mo等贵重合金元素,进而大幅度降低了生产成本。
[0072]
淬火加热温度直接影响后续马氏体组织的粒度,进而影响钢板的韧性。加热温度过高容易使奥氏体晶粒粗化,淬火后马氏体组织粗大,韧性恶化;而加热温度偏低则导致奥氏体化不充分,淬火后无法获得完全马氏体组织,并且避免由于薄钢板降温速度快,出保温炉进入淬火机前温降快不能保证淬火温度。保温时间对淬火性能也有类似的规律,时间过长容易使得晶粒粗大,同时增加能耗,提高成本,时间过短则奥氏体化不充分,淬火后硬度、强度达不到要求。本发明淬火加热升温过程采取中频快速加热,进一步降低微合金元素加入,实现了钢种的高强度、高硬度、良好的低温冲击韧性和冷弯加工性能,并且钢板具有优良的板形。
[0073]
本发明实现≤10mm厚度高硬度高耐磨性钢板的生产,钢板的屈服强度在900mpa以上,抗拉强度超过1100mpa,延伸率≥14%,硬度360
±
20hbw,-40℃冲击功值超过33j,钢板的不平度控制在3mm/m以内。
[0074]
以上所述,仅为本发明较佳的具体实施方式,但本发明的保护范围并不局限于此,任何熟悉本技术领域的技术人员在本发明揭露的技术范围内,根据本发明的技术方案及其发明构思加以等同替换或改变,都应涵盖在本发明的保护范围之内。