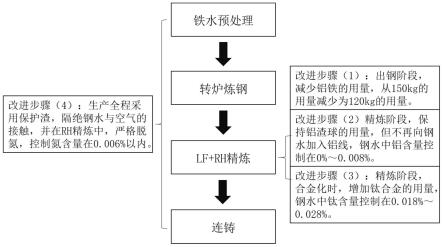
1.本发明涉及炼钢的成分优化技术领域,具体是涉及一种提高微合金钢连铸宽厚板坯表面质量的方法。
背景技术:2.为改善钢的各项性能,学者们提出了钢的微合金化技术。在钢中加入一种或者几种合金元素,并且加入的合金元素总含量在0.20%以下,以此改善钢的可焊接性、成型性、韧性及强度等性能。由于微合金化低合金钢优异的韧性及较高的强度,被广泛应用于石油管道、桥梁建设、交通运输及机械制造等行业。
3.目前,低合金钢的微合金化,主要是向钢中加入nb、ti、v等合金元素,它们能和c、n强烈反应而形成化合物析出。nb、ti、v元素的化合物在奥氏体晶界处析出,抑制了奥氏体的长大,起到细晶强化的作用,同时,这些元素还能在铁素体晶粒内或晶界处析出纳米级析出物而阻碍位错运动,起到沉淀强化的效果,这增加了钢材的强度,但不降低钢材的韧性。但微合金元素在高温下晶界处的析出,破坏了晶界的连续性,增加了铸坯的裂纹敏感性,降低其高温塑性。
4.而al元素在钢中主要以alo、aln存在,而aln析出相有明显的棱角,它多呈四边形、六边形,或不规则形状,尺寸较小。通常情况下,aln在900℃左右析出,使奥氏体区延性大大降低,导致第三脆性变宽,波谷加深,所以它对钢材的断裂韧性有一定的负面影响。
5.ti元素在钢水中与碳、氮的结合能力比铌、钒、铝的能力强,在高温下便会析出tin相,降低钢种的氮含量,起到固氮作用,这减少了nb(c,n)、aln在奥氏体晶界的析出,减少第三脆性区第二相析出的影响。同时,tin对奥氏体晶界有钉扎作用,阻止奥氏体晶界的长大,细化奥氏体晶粒,减少裂纹产生的先决条件,从而提高铸坯的高温塑性。在温度相对较低时,由于钛的析出颗粒较大且分布零散,可作为铌、钒等析出物的形核点,形成复合的碳氮化物,可减轻铌nb、钒v对钢的高温塑性的不良影响。
6.连铸技术,即连续铸钢技术,相比于传统的铸造工艺,其可以连续生产出铸坯,从而具有以下优点:(1)减少铸造工序,缩短铸造流程;(2)金属的收得率提高;(3)降低能量消耗;(4)自动化程度不断提高;(5)连铸坯质量日益提高。运用连铸技术生产微合金钢,能极大发挥两者的优势。
7.但由于微合金元素在高温下的析出,恶化了铸坯的高温热塑性;宽厚板截面积大,湍流严重,温度分布不均匀,铸坯受力不均匀等原因,造成微合金钢连铸宽厚板坯存在严重的表面缺陷,产生严重的资源浪费,降低经济效益。
8.专利《一种提高微合金钢连铸板坯表面质量的试验方法》,利用gleeble3800热实验机研究微合金钢脆性温区,为连铸矫直温度的指定提供了思路。但其只是从试验的角度进行了连铸工艺的模拟,而没有进行实际生产试验,也没有从源头改进连铸坯裂纹的诞生。
技术实现要素:9.为了克服微合金元素对连铸坯高温塑性的不良影响,本发明目的是提供一种提高微合金钢连铸宽厚板坯表面质量的方法,利用该方法获得的微合金钢连铸宽厚板坯的高温塑性好,裂纹敏感性低,表面质量大幅改善。能够降低企业的生产成本,稳定及提高了生产效率。
10.本发明的目的通过以下技术方案实现。
11.微合金钢连铸宽厚板坯的生产工艺流程为:铁水预处理
→
转炉炼钢
→
lf+rh精炼
→
连铸。一种提高微合金钢连铸宽厚板坯表面质量的方法,包括如下步骤:
12.(1)在转炉出钢过程中,减少铝铁的用量;
13.(2)在lf+rh精炼过程中,去除铝线的增加;
14.(3)在lf+rh精炼过程中,增加钢水中钛的含量;
15.(4)在整个生产过程中,控制钢水中氮元素的增加。
16.进一步地,步骤(1)所述减少铝铁的用量,具体为:在转炉出钢过程中,减少脱氧剂中铝铁的含量,而硅锰合金的含量不变,以保持钢的整体脱氧效果没有改变,但钢水中铝的含量减少。
17.进一步地,步骤(2)所述去除铝线的增加,具体为:lf+rh精炼过程中保持铝渣球的用量,从而防止钢水中氧含量的增加,但在lf精炼过程中不再向钢水中加入铝线,极大地降低钢水中的酸溶铝含量。
18.进一步地,经过步骤(1)和步骤(2),钢水中的铝含量控制在0%~0.008%。
19.进一步地,步骤(3)中,lf+rh精炼的主要任务是脱氧、脱硫、去除夹杂物,并对钢水进行合金化,在合金化过程中,增加钛合金的使用,从而使钢水中的钛含量增加并稳定在0.020%附近。
20.进一步地,经过步骤(3),钢水中的钛含量范围控制在0.018%~0.028%。
21.进一步地,步骤(4)所述控制钢水和空气的接触,具体为:在整个生产过程中,均采用保护渣来隔绝钢水与空气的接触,防止钢水吸入空气中的氮。同时在rh精炼过程中,精炼真空度控制在300pa以内,并进行脱氮,将钢水中的氮含量控制在0.006%以内,后续连铸工艺钢水增氮不明显。
22.本发明提供一种由上述方法获得的表面质量优秀的微合金钢连铸宽厚板坯,其表面良好率为81%~89%。
23.与现有技术相比,本发明具有以下优点:
24.(1)本发明利用优化后的工艺生产的微合金钢连铸宽厚板坯。去除了al元素对钢性能的负面影响,加强了ti元素对钢性能的影响,同时严格控制n元素对钢性能的影响,提高了微合金元素钛在连铸坯高温段的析出强化及细晶强化,从而提高了连铸坯在高温段的热塑性。
25.(2)本发明方法生产的微合金钢连铸宽厚板坯,高温塑性好,铸坯表面质量高,表面良好率为81%~89%,稳定在83%左右。氮控较好的情况下,可直接热送热装,极大地提高了钢厂的生产效率。
附图说明
26.图1为实施例1-3中微合金钢连铸宽厚板坯的生产工艺流程图;
27.图2为实施例1中工艺改进前后的微合金钢q390gjc连铸宽厚板坯的高温塑性对比图;
28.图3为实施例1中工艺改进前的微合金钢q390gjc连铸宽厚板坯拉伸试样在750℃下的断口形貌图;
29.图4为实施例1中工艺改进后的微合金钢q390gjc连铸宽厚板坯拉伸试样在750℃下的断口形貌图。
具体实施方式
30.以下结合实施例及附图对本发明的具体实施方式作进一步的说明,但本发明的实施方式不限于此。
31.实施例1
32.按照图1的生产工艺流程图,钢种为q390gjc,生产工艺流程为:铁水预处理
→
转炉炼钢
→
lf+rh精炼
→
连铸,更具体为:铁水预脱硫处理
→
转炉炼钢
→
lf精炼
→
rh精炼
→
连铸,制造出厚度为270mm、宽度为2260mm的宽厚板坯。
33.在上述生产过程中,提高微合金钢q390gjc连铸宽厚板坯表面质量的方法如下:
34.(1)在转炉出钢过程中,脱氧剂中的硅锰合金含量不变,而铝铁含量减少,从150kg减少为120kg。
35.(2)在lf+rh精炼过程中,保持铝渣球的使用量,但不再加入铝线,防止钢水中氧增加的同时,极大地降低钢水中酸溶铝的含量,als含量由0.020%附近降低到0.005%附近。
36.(3)在lf精炼、rh精炼过程中,对钢水进行充分的脱硫、脱氧、去除夹杂物以及合金化,而在合金化中,增加钛合金的含量,使钢水中ti的目标含量由之前的0.01%附近提高至0.020%附近。在实际生产中允许有所波动,波动范围为0.018%~0.028%。
37.(4)在整个生产过程中,均采用保护渣来隔绝钢水与空气的接触,严格控制钢水和空气的接触,防止钢水吸入空气中的n元素。同时在rh精炼过程中,精炼真空度为266pa,并进行脱氮,将钢水中的氮含量控制在0.006%以内。
38.采用上述改进后的生产工艺,能顺利生产出目标成分的微合金钢q390gjc连铸宽厚板坯,改进前后铸坯的部分化学成分及含量如表1所示,其余为fe,含少量的夹杂物。
39.表1
40.化学成分csimnp≤s≤alsnnbticu改进前%0.1600.301.460.0200.0060.0210.00760.0300.0100.028改进后%0.1580.311.450.0200.0060.0020.00530.0290.0230.030
41.对本实施例制备得到的微合金钢q390gjc连铸宽厚板坯进行质量检测。
42.(1)表面质量检测:
43.微合金钢q390gjc连铸宽厚板坯生产后,需要对其表面质量进行检查,防止其在后续的热轧中出现严重的表面缺陷,造成产品报废,浪费产能。表面质量检查方法主要是采用火焰扒皮法,一炉钢大概生产4-6块连铸宽厚板坯,抽2块进行扒皮检查,一块深扒,一块浅扒。浅扒即用火焰枪清理表皮一次,大概去除4mm厚的表皮钢层,而深扒则在浅扒的基础上
再扒一遍,大概去除8mm厚的表面钢层。扒皮后,用led强光手电筒对铸坯的整个表面进行细致的探照检查,一块板坯的检查时间在5-8分钟。当出现表面横裂纹、角裂、网状裂纹、夹渣等缺陷时,对相应缺陷位置进行标记,缺陷数量>1,则判定铸坯为不良。如果抽检中的一块板坯出现问题,则整炉钢其他板坯都需要进行扒皮检查,有缺陷的铸坯在扒皮后进行整修,再送去热轧,如果问题严重,则整块铸坯报废。
44.在工艺改进前,微合金钢q390gjc连铸宽厚板坯的表面质量良好率约为56%,存在较多的表面缺陷,需要扒皮检查整修的连铸坯较多,严重浪费产能,拖长生产周期,影响钢厂的生产效率。而经过工艺改进后,微合金钢q390gjc连铸宽厚板坯的表面质量良好率约为87%,如果氮控情况优异,微合金钢q390gjc连铸宽厚板坯表面质量优异,可直接热送热装,减少中间的缓冷、扒皮检测、加热环节,极大提高了钢厂的生产效率。
45.(2)高温塑性检测:
46.图2为工艺改进前后的微合金钢q390gjc连铸宽厚板坯的高温塑性对比图,从图中可以看出,在650℃~950℃的脆性区间内,改进后钢材试样的断口收缩率明显高于改进前钢材试样的断口收缩率,提高了15%~30%,而断口收缩率是评定钢材塑性的指标。因此,改进后的钢材具有更优异的塑性,从而确保铸坯在生产过程中裂纹的减少。图3为工艺改进前的微合金钢q390gjc连铸宽厚板坯拉伸试样在750℃下的断口形貌图,图4为工艺改进后微合金钢q390gjc连铸宽厚板坯拉伸试样在750℃下的断口形貌图,对比图3和图4可以明显看出两种钢材断裂形式的不同,工艺改进后的微合金钢q390gjc连铸宽厚板坯具有一定的韧性断裂,表现出更强的高温塑性,进一步说明工艺改进的成效显著。
47.实施例2
48.按照图1的生产工艺流程图,钢种q420gjc,生产工艺流程为:铁水预处理
→
转炉炼钢
→
lf+rh精炼
→
连铸,更具体为:铁水预脱硫处理
→
转炉炼钢
→
lf精炼
→
rh精炼
→
连铸,制造出厚度为270mm、宽度为2260mm的宽厚板坯。
49.在上述生产过程中,提高微合金钢q420gjc连铸宽厚板坯表面质量的方法如下:
50.(1)在转炉出钢过程中,脱氧剂中的硅锰合金含量不变,而铝铁含量减少,从150kg减少为120kg。
51.(2)在lf+rh精炼过程中,保持铝渣球的使用量,但不再加入铝线,防止钢水中氧增加的同时,极大地降低钢水中酸溶铝的含量,als含量由0.020%附近降低到0.005%附近。
52.(3)在lf精炼、rh精炼过程中,对钢水进行充分的脱硫、脱氧、去除夹杂物以及合金化,而在合金化中,增加钛合金的含量,使钢水中ti含量由之前的0.01%附近提高至0.020%附近。
53.(4)在整个生产过程中,均采用保护渣来隔绝钢水与空气的接触,严格控制钢水和空气的接触,防止钢水吸入空气中的n元素。同时在rh精炼过程中,精炼真空度为275pa,并进行脱氮,将钢水中的氮含量控制在0.006%以内。
54.采用上述改进后的生产工艺,能顺利生产出目标成分的微合金钢q420gjc连铸宽厚板坯,改进前后铸坯的部分化学成分及含量如表2所示,其余为fe,含少量的夹杂物。
55.表2
56.化学成分csimnp≤s≤alsnnbticu改进前%0.1540.301.450.0200.0060.0200.00680.0380.0110.029
改进后%0.1570.311.450.0200.0060.0030.00440.0400.0240.030
57.按照实施例1中的检测方法,对生产的微合金钢q420gjc连铸宽厚板坯的表面质量情况进行检查,并对比工艺改进前后两种铸坯的表面良好率。工艺改进前,微合金钢q420gjc连铸宽厚板坯的表面质量良好率约为43%,经过工艺改进后,微合金钢q420gjc连铸宽厚板坯的表面质量良好率约为81%。由于nb元素含量较高的影响,微合金钢q420gjc连铸宽厚板坯表面质量稍差,但相比改进前,铸坯的表面质量提高依旧明显。
58.实施例3
59.按照图1的生产工艺流程图,钢种q345gjb,生产工艺流程为:铁水预处理
→
转炉炼钢
→
lf+rh精炼
→
连铸,更具体为:铁水预脱硫处理
→
转炉炼钢
→
lf精炼
→
rh精炼
→
连铸,制造出厚度为270mm、宽度为2260mm的宽厚板坯。
60.在上述生产过程中,提高微合金钢q345gjb连铸宽厚板坯表面质量的方法如下:
61.(1)在转炉出钢过程中,脱氧剂中的硅锰合金含量不变,而铝铁含量减少,从150kg减少为120kg。
62.(2)在lf+rh精炼过程中,保持铝渣球的使用量,但不再加入铝线,防止钢水中氧增加的同时,极大地降低钢水中酸溶铝的含量,als含量由0.020%附近降低到0.005%附近。
63.(3)在lf精炼、rh精炼过程中,对钢水进行充分的脱硫、脱氧、去除夹杂物以及合金化,而在合金化中,增加钛合金的含量,使钢水中ti含量由之前的0.01%附近提高至0.020%附近。
64.(4)在整个生产过程中,均采用保护渣来隔绝钢水与空气的接触,严格控制钢水和空气的接触,防止钢水吸入空气中的n元素。同时在rh精炼过程中,精炼真空度为261pa,并进行脱氮,将钢水中的氮含量控制在0.006%以内。
65.采用上述改进后的生产工艺,能顺利生产出目标成分的微合金钢q345gjb连铸宽厚板坯,改进前后铸坯的部分化学成分及含量如表3所示,其余为fe,含少量的夹杂物。
66.表3
[0067][0068][0069]
按照实施例1中的检测方法,对生产的微合金钢q345gjb连铸宽厚板坯的表面质量情况进行检查,并对比工艺改进前后的铸坯的表面良好率。在工艺改进前,微合金钢q345gjb连铸宽厚板坯的表面质量良好率约为55%,经过工艺改进后,微合金钢q345gjb连铸宽厚板坯的表面质量良好率约为86%,微合金钢q345gjb连铸宽厚板坯的表面质量提高明显。