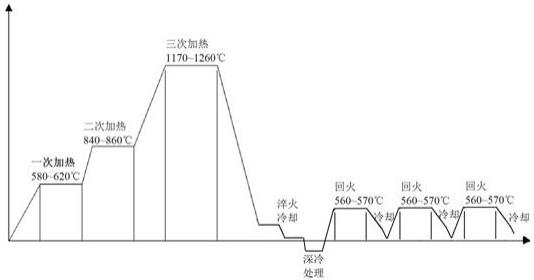
1.本发明涉及粉末冶金技术领域,特别涉及一种粉末冶金高速钢丝材及其制备方法。
背景技术:2.高速钢具有高硬度、高强度、耐磨性好的特点,广泛应用于精密刀具制作以及模具制造业。相比于传统的铸造高速钢,利用粉末冶金法制备得到的高速钢显著地改善了显微组织当中碳化物偏析的问题,极大地提升了材料的力学性能以及工作时的稳定性。目前商用的粉末冶金高速钢主要由气雾化合金粉-热等静压联合法进行制备,得到的高速钢具有明显的细晶组织,碳化物均匀分布,强度性能均在3500mpa以上,部分牌号性能可以达到4000mpa以上,但是由于生产所耗成本居高不下,严重限制了其大规模应用。有研究报道,利用商业m2合金粉掺杂氮化钒粉末通过球磨活化与冷压烧结的方式,在1160℃可以基本实现材料的致密化,相对密度高达99.4%,强度性能也能够维持在2500~3000mpa左右,并极大地降低了生产成本。因此,本发明旨在公开一种冷压烧结法制备低成本、高性能的粉末冶金高速钢的方法。
技术实现要素:3.发明目的:针对高速钢材料寿命低的问题,本发明提供一种粉末冶金高速钢丝材及其制备方法,制备的粉末冶金高速钢组织细小、碳化物均匀、有害杂质量少,抗弯强度、韧性和耐磨性明显提升。
4.技术方案:本发明提供了一种粉末冶金高速钢丝材,包含以下重量百分比的组分: c:1.5~1.8%,mn:0.28~0.38%,si:0.6~0.75%,cr:3.8~4.5%,v或者nb+v:2.8~3.2%,w:5.8~6.5%,mo:4.8~5.5%,co:7.8~8.5%,ti:1.8~2.3%,re:1~3%,s:《0.03%,p:《0.05%,o+n+h:《0.005%,其余为fe。
5.本发明还提供了一种粉末冶金高速钢丝材的制备方法,包括以下步骤:s1:熔炼母合金:按配比取用原料fe的纯金属,w、mo、co、v、nb、cr各自的纯金属或中间合金,以及c-fe、si-fe、mn-fe、ti-c、re-m的中间合金,并对所有原料进行干燥处理;在真空度10-5
~103pa的条件下熔炼母合金;首先在1380~1580℃熔化fe、w、mo、co、v、nb、cr中的纯金属,保温10~15min;其次在1280~1580
º
c加入w、mo、co、v、nb、cr的中间合金以及c-fe、si-fe、mn-fe的中间合金,保温10~15min,搅拌均匀后除渣;再次在1280~1580
º
c加入由ti-c粉末压制成的块体料,保温15~35min;然后在1280~1480
º
c加入re-m的中间合金,保温3~5min,保温过程一直电磁搅拌;最后真空炉内浇铸出炉,得母合金;s2:电渣提纯:对s1制备的母合金进行电渣重熔,电渣的渣系为caf
2-cao-al2o
3-tio2,含量分别为65~70%、10~15%、10~15、5~10%;s3:制粉:将s2电渣提纯后的母合金进行制粉,得到合金粉末;s4:退火压坯:对合金粉末依次进行还原退火和粉末压坯,制备成粉末块体坯料;s5:烧结:对s4所得粉末块体坯料进行烧结;s6:热处理:对s5所得烧结后的粉末块体坯料进行分级热处理;s7:变形:对所述s6所得粉末
块体坯料进行锻造和/或挤压、轧制、拉拔处理,得到φ1-3mm的丝材;s8:热处理:对s7所得丝材再次进行分级热处理。
6.优选地,在所述s2中,在所述电渣重熔的过程中,采取结晶器出料口加强冷却、侧壁适当保温的手段控制熔池的温度梯度,使凝固方向与熔池的侧壁的夹角的锐角部分区间为0~30
°
,得到净化后的母合金熔体。
7.优选地,在所述s3中,将s2电渣提纯后的母合金转入保护性气氛保护、炉膛内壁镀有保护层的中间炉,然后在中间炉直接制粉,得到所述合金粉末。
8.进一步地,在所述s3中,所述制粉的方式为气雾化制粉,采用氩气雾化,氩气纯度99.9%,雾化压力10~30mpa,制备出来的合金粉末的d50为20~60μm;或者,所述制粉的方式为水、气联合雾化制粉,采用的气体为氩气,纯度为99.9%,雾化压力10~30mpa,水压8~50mpa,制备出来的合金粉末的d50为8~20μm;或者,所述制粉的方式为球磨制粉,制备出来的合金粉末的d50为8~50μm;或者,所述制粉的方式为旋转电离制粉,制备出来的合金粉末的d50为30~70μm。
9.优选地,在所述s4中,所述还原退火的工艺如下:在真空炉内进行,炉内成真空状态或惰性气体保护状态,将粉末平铺在基板上,厚度为5~10mm,多层基板叠加放置,相邻基板间距30~100mm,温度400~680℃,保温时间60~300min,随炉冷却到室温后取出。过程中检测炉内气氛氧含量,使氧含量小于10ppm。
10.进一步地,在所述s4中,所述粉末压坯的工艺为非hip压坯:将经还原退火后的合金粉末称重后放入压坯模具中,将粉末双向模压制成块体坯料;压力500~1200mpa。
11.进一步地,在所述s5中,所述烧结的方式为常压保护性气氛烧结:(1)烧结炉内冲入保护性惰性气体,排出氧气,使烧结炉内的氧含量小于1ppm;(2)以6~10℃/min的速度升温至650~850℃,保温时间t=3~5min/cm
×
d,;(3)以8~10℃/min的速度升温至1180~1260℃,保温时间t=10~30min/cm
×
d;(4)随炉冷却至室温;其中,d为样品的最大壁厚,单位cm。
12.优选地,在所述s6和/或s8中,所述分级热处理的工艺如下:(1)预热:以5~10℃/min的升温速度加热至580~620℃,保温时间t=3~5min/cm
×
d;(2)二次预热:紧接着以5~10℃/min的升温速度加热至840~860℃,保温时间t=2~4min/cm
×
d;(3)淬火保温:紧接着以5~10℃/min的升温速度加热至1170~1260℃,保温时间t=2~4min/cm
×
d;(4)淬火冷却:紧接着,当d≥10时,首先以103~105℃/s的降温速度降温至300~500℃,保温时间t=0.1~1.5min/cm
×
d,然后以103~105℃/s的降温速度降温至20~40℃,保温时间t=0.1~1.5min/cm
×
d;当10≥d≥5时,以103~105℃/s的降温速度降温至200~400℃,保温时间t=0.1~1.5min/cm
×
d,然后以103~105℃/s的降温速度降温至20~40℃,保温时间t=0.1~1.5min/cm
×
d;当d≤5cm时,以103~105℃/s的降温速度降温至20~40℃,保温时间t=0.1~1.5min/cm
×
d;(5)深冷处理:紧接着以105~107℃/s的降温速度降温至-50~-150℃,保温时间t=1~2min/cm
×
d;(6)回火:紧接着以5~10℃/min的升温速度加热至560~570℃,保温时间t=1~3h/cm
×
d;(7)冷却:紧接着快速冷却至200~300℃,保温时间t=0.3~1h/cm
×
d,出炉空冷至20~40℃;(8)重复(6)和(7)0~1次;其中,d为样品的最大壁厚,单位cm。粉末高速钢由于其特殊性,热处理工艺也区别与一般的金属,主要区别是需要预热、淬火温度较高和回火温度高且回火次数多;变形以后的粉末高速钢棒料内应力较大、硬度很高,因此必须首先进行退火。退火温度为840~880℃,退火时间t=2~20min/cm
×
d。高速钢中合金元素含量较多,导热性差,加热前必须进行预热,预
热温度依次为580~620℃和840~880℃,预热时间t=2~5min/cm
×
d。淬火温度为1170~1260℃,淬火后水冷或油冷至室温。最后,560~570℃回火三次,每次保温时间t=1~3h
×
d。高速钢回火必须注意以下四点:(1)淬火后必须及时回火,否则会使奥氏体稳定化,不利于消除残余奥氏体(一般不超过8h),(2)回火温度力求均匀,最好在盐浴炉或带风扇井式回火炉中进行,力求加热均匀,(3)每次回火后必须冷至室温,才能重复以后的各次回火,(4)回火后必须冷至室温方可清洗,否则易变形开裂。此条件下制备出的粉末高速钢晶粒和第二相细化均匀,细小而弥散的颗粒状碳化物分布在回火马氏体基上。未闭合的孔隙呈圆形或者椭圆形。硬度达到67.5hrc,红硬性达到63.2hrc,抗弯强度可达4146.3mpa。优选地,在所述s6中,所述变形前退火处理的工艺如下:将粉末块体坯料在真空炉或盐浴炉中以≤2.5℃/min的升温速率加热到850~870℃,保温110~130min后,以≤400℃/h的升温速率升温至1100~1300℃,保温15~30min,接着降温至850~870摄氏度,保温60~120min,然后在炉中以10~30℃/h的降温速率降温至500~600℃,然后空冷或随炉冷却到200℃左右后出炉空冷至室温。
13.本发明还提供了一种粉末冶金高速钢丝材的制备方法,包括以下步骤:s1:按配比取用原料fe的纯金属,w、mo、co、v、nb、cr各自的纯金属或中间合金,以及c-fe、si-fe、mn-fe、ti-c、re-m的中间合金,并对所有原料进行干燥处理;在真空度10-5
~103pa的条件下,采用真空感应熔炼技术熔炼母合金;首先在1380~1580℃熔化fe、w、mo、co、v、nb、cr中的纯金属,保温10~15min;其次在1280~1580
º
c加入w、mo、co、v、nb、cr的中间合金以及c-fe、si-fe、mn-fe的中间合金,保温10~15min,搅拌均匀后除渣;再次在1280~1580
º
c加入由ti-c粉末压制成的块体料,保温15~35min;然后在1280~1480
º
c加入re-m的中间合金,保温3~5min,保温过程一直电磁搅拌;最后真空炉内浇铸出炉,得母合金;s2:对s1制备的母合金进行电渣重熔;s3:将s2电渣重熔后的母合金在保护性气氛中滴铸到铜模内,得到滴铸的铸锭;s4:将s3的铸锭破碎,并球磨制粉;s5:对s4合金粉末依次进行还原退火和粉末压坯,制备成粉末块体坯料;s6:对s5所得粉末块体坯料进行烧结;s7:对s6所得烧结后的粉末块体坯料进行分级热处理;s8:对所述s7所得粉末块体坯料进行锻造和/或挤压、轧制、拉拔处理,得到φ1-3mm的丝材;s9:对s8所得丝材再次进行分级热处理。
14.优选地,在s4中,所述球磨制粉的工艺如下:s4-1:将s3得到的滴铸铸锭破碎至0.1~1mm; s4-2:用行星球磨机将粉末混合到酒精中,球与粉的重量比为3~6:1,磨粉时间24~72小时;s4-3:将碾磨后的混合料浆在75~80℃下干燥5~10h,过筛后转入低氧分压的干燥室进行一定预氧化;s4-4:将s3获得的粉末密封封存。
15.优选地,在所述球磨制粉的过程还加入tic、vn 、wc、mo2c、cr3c2、vc、nbc粉末中的一种或其组合。因为熔炼过程会有元素烧损,制成粉末后成分会有轻微的偏差,通过加入相应合金元素的碳化物或氮化物原粉,可以精确调整成分,至上限或下限,以更好地决定微观组织,并最终决定性能。
16.进一步地,在步骤s6中,所述烧结的方式为hip烧结:(1)将粉末块体坯料装入中空壳体,并抽真空,密封;(2)以8~12℃/min的速度升温至600~700℃,保温时间t=2~8min/cm
×
d;(3)以5~15℃/min的速度升温至1100~1250℃,保温时间t=15~25min/cm
×
d;(4)随炉冷却至室温;其中,d为样品的最大壁厚,单位cm。
17.有益效果:(1)本发明中,在电渣重熔的时候,电渣的渣系为caf
2-cao-al2o
3-tio2,能够去除母合金在熔炼阶段炉膛内壁和浇铸模具表面脱落的非金属夹杂物,提高母合金的
纯净度,降低非金属夹杂物引起的应力集中问题,提高材料的韧性和耐疲劳抗力;并且由于渣系加入tio2,根据化学动力学平衡原理,可以阻止母合金内ti向渣层扩散,提高母合金内ti的收得率,细化晶粒,提高性能。
18.(2)本发明中,电渣提纯后的母合金直接转入中间炉,随后进行雾化制粉,优势在于电渣提纯后的母合金纯净度更高,不会因再次熔化而造成二次污染,这样获得的粉末的纯净度更高,与普通方法相比,非金属夹杂物和有害气体含量减少90%。
19.(3)本发明中,组分中加入re稀土元素,主要是去除组分中的杂质元素氧。由于re元素的化学性质非常活泼,几乎可以还原所有的金属氧化物,生成性质稳定的re-o氧化物,不仅可以净化组分,减少有害元素o的危害,而且形成的re-o氧化物还可以作为异质形核的核心,增大异质形核率,细化晶粒,提高强韧性。并且,在真空熔炼和电渣精炼阶段分别加入re-m的中间合金,目的是提高re-m的利用率,防止真空熔炼阶段全部加入时烧损过于严重,不能确保充分地除去熔体中的氧,最终使熔体更加纯净。
20.(4)制备过程中加入tic、vn、wc、mo2c、cr3c2、vc、nbc等合金粉末,为凝固、再结晶提供大量的非均匀形核的核心,促进异质形核,起到细化晶粒和碳化物尺寸作用,有利于提高材料的硬度、耐磨性和抗弯强度等力学性能。
21.(5)本发明中,将电渣重熔后的母合金在保护性气氛中滴铸到铜模内,得到滴铸的铸锭,益处在于:滴铸液滴尺寸小,凝固速度快,可以有效抑制合金元素的偏析,使合金成分更加均匀,这对保证高速钢的性能非常重要;滴铸到铜模内,铜模可以使热量快速散去,进一步加快凝固的速度,保证成分的均匀性;在保护性气氛中进行滴铸,防止空气中的氧污染溶体,减少氧的危害;滴铸的铸锭存在很多熔接痕,便于下一步的破碎。
22.(6)本发明中,根据材料的壁厚进行分级淬火,并且根据不同的壁厚选择不同的等温温度,可以使材料的温度以及材料的表、里的热量均匀快速散去,不仅可以消除因热量分布不均引起的应力开裂,还可使材料的淬火目的(使奥氏体向马氏体或下贝氏体转变)得以较好地实现。另外,淬火后进行的深冷处理,可以进一步促进残余奥氏体向马氏体转变,提高材料的硬度和韧性。
附图说明
23.图1为分级热处理的工艺图(d≥10或10≥d≥5时);图2为分级热处理的工艺图(d≤5cm时)。
具体实施方式
24.下面结合附图对本发明进行详细的介绍。
25.本发明提供了一种粉末冶金高速钢丝材,包含以下重量百分比的组分: c:1.5~1.8%,mn:0.28~0.38%,si:0.6~0.75%,cr:3.8~4.5%,v或者nb+v:2.8~3.2%,w:5.8~6.5%,mo:4.8~5.5%,co:7.8~8.5%,ti:1.8~2.3%,re:1~3%,s:《0.03%,p:《0.05%,o+n+h:《0.005%,其余为fe。
26.上述粉末冶金高速钢丝材的制备方法如下:实施例1:本实施方式提供了一种粉末冶金高速钢丝材的制备方法,包括以下步骤:s1:熔炼
母合金:按配比取用原料fe的纯金属,w、mo、co、v、nb、cr各自的纯金属或中间合金,以及c-fe、si-fe、mn-fe、ti-c、re-m的中间合金,并对所有原料进行干燥处理;在真空度10-5
~103pa的条件下熔炼母合金;首先在1380~1580℃熔化fe、w、mo、co、v、nb、cr中的纯金属,保温12min;其次在1280~1580
º
c加入w、mo、co、v、nb、cr的中间合金以及c-fe、si-fe、mn-fe的中间合金,保温12min,搅拌均匀后除渣;再次在1280~1580
º
c加入由ti-c粉末压制成的块体料,保温30min;然后在1280~1480
º
c加入re-m的中间合金,保温4min,保温过程一直电磁搅拌;最后真空炉内浇铸出炉,得母合金;s2:电渣提纯:对s1制备的母合金进行电渣重熔,电渣的渣系为caf
2-cao-al2o
3-tio2,含量分别为70%、12%、12%、8%,得电渣提纯后的母合金;在上述电渣重熔的同时,通过加强结晶器出料口的冷却能力(用冷却水或直接将坯料一端拉入水中)、保温熔池侧壁的方法(线圈加热+传感器)控制熔池的温度梯度,使凝固方向与熔池侧壁的夹角保持20~30
°
,得到净化后的母合金熔体。
27.s3:制粉:将s2电渣提纯后的母合金进行制粉,得到合金粉末;上述制粉的方式为气雾化制粉,采用氩气雾化,氩气纯度99.9%,雾化压力10mpa,制备出来的合金粉末的d50为20μm。
28.s4:退火压坯:对合金粉末依次进行还原退火和粉末压坯,制备成粉末块体坯料;上述还原退火的工艺如下:在真空炉内进行,炉内成真空状态或惰性气体保护状态,将粉末平铺在基板上,厚度为5mm,多层基板叠加放置,相邻基板间距30mm,温度400℃,保温时间60min,随炉冷却到室温后取出。过程中检测炉内气氛氧含量,使氧含量小于10ppm。
29.上述粉末压坯的工艺为非hip压坯:将经还原退火后的合金粉末称重后放入压坯模具中,将粉末双向模压制成块体坯料;压力1200mpa。
30.s5:烧结:对s4所得粉末块体坯料进行烧结;上述烧结的方式可以为常压保护性气氛烧结:(1)烧结炉内冲入保护性惰性气体,排出氧气,使烧结炉内的氧含量小于1ppm;(2)以10℃/min的速度升温至650℃,保温时间t=5min/cm
×
d,;(3)以10℃/min的速度升温至1220℃,保温时间t=20min/cm
×
d;(4)随炉冷却至室温;其中,d为样品的最大壁厚,单位cm。
31.s6:热处理:对s5所得烧结后的粉末块体坯料进行分级热处理;上述分级热处理的工艺如下(如图1和2):(1)预热:以5℃/min的升温速度加热至580℃,保温时间t=3min/cm
×
d;(2)二次预热:紧接着以5℃/min的升温速度加热至840℃,保温时间t=2min/cm
×
d;(3)淬火保温:紧接着以5℃/min的升温速度加热至1170℃,保温时间t=2min/cm
×
d;(4)淬火冷却:紧接着,当d≥10时,首先以104℃/s的降温速度降温至300℃,保温时间t=1min/cm
×
d,然后以104℃/s的降温速度降温至20℃,保温时间t=1.5min/cm
×
d(如图1);当10≥d≥5时,以105℃/s的降温速度降温至200℃,保温时间t=1min/cm
×
d,然后以104℃/s的降温速度降温至40℃,保温时间t=1.5min/cm
×
d(如图1);
当d≤5cm时,以105℃/s的降温速度降温至40℃,保温时间t=1.5min/cm
×
d(如图2);(5)深冷处理:紧接着以105℃/s的降温速度降温至-100℃,保温时间t=1min/cm
×
d;(6)回火:紧接着以5℃/min的升温速度加热至560℃,保温时间t=1h/cm
×
d;(7)冷却:紧接着随炉冷却至200℃,出炉空冷至40℃;(8)重复(6)和(7)至少一次;其中,d为样品的最大壁厚,单位cm。
32.s7:变形:对所述s6所得粉末块体坯料进行锻造和/或挤压、轧制、拉拔处理,得到φ2mm的丝材;上述锻造的工艺如下:预热:首先以8℃/min的加热速度将坯料加热至620℃,保温时间t=3min/cm
×
d ;然后以8℃/min的升温速度加热至860℃,保温时间t=2min/cm
×
d;其中,d为样品的最大壁厚,单位cm;锻造:对坯料进行锻造,每次减小量为5%,每次锻造完后直接将坯料重新放入840℃的炉中加热,加热时间t=3min/cm
×
d,直至将坯料锻造至所需尺寸;冷却:将锻造完成的坯料放入炉中随炉冷却至200℃,然后出炉空冷至室温。
33.上述挤压的方式为热挤压,工艺如下:预热:首先以7℃/min的加热速度将坯料加热至620℃,保温时间t=5min/cm
×
d;然后以7℃/min的升温速度加热至900℃,保温时间t=4min/cm
×
d;其中,d为样品的最大壁厚,单位cm;热挤压:挤压方式为卧式挤压,挤压速度5mm/s,单次挤压截面减小8%,挤压模具预热温度750℃;冷却:将挤压完成的坯料放入炉中随炉冷却至260℃,然后出炉空冷至室温。
34.s8:热处理:对s7所得丝材再次进行分级热处理。本步骤中的分级热处理工艺如图1和2,与上述s6中的工艺相同,此处不做赘述。
35.实施例2:本实施例与实施例1大致相同,不同点仅在于,本实施方式中,在步骤s3中,将s2电渣提纯后的母合金进行制粉的方式为水、气联合雾化制粉,气体为氩气,纯度99.9%,雾化压力10mpa,水压20mpa,制备出来的合金粉末的d50为10μm。
36.除此之外,本实施例与实施例1完全相同,此处不做赘述。
37.实施例3:本实施例与实施例1大致相同,不同点仅在于,本实施方式中,在步骤s3中,将s2电渣提纯后的母合金进行制粉的方式为球磨制粉,制备出来的合金粉末的d50为50μm。
38.除此之外,本实施例与实施例1完全相同,此处不做赘述。
39.实施例4:本实施方式提供了一种粉末冶金高速钢丝材的制备方法,包括以下步骤:s1:熔炼母合金:按配比取用原料fe的纯金属,w、mo、co、v、nb、cr各自的纯金属或中间合金,以及c-fe、si-fe、mn-fe、ti-c、re-m的中间合金,并对所有原料进行干燥处理;在真空度10-5
~103pa
的条件下熔炼母合金;首先在1380~1580℃熔化fe、w、mo、co、v、nb、cr中的纯金属,保温12min;其次在1280~1580
º
c加入w、mo、co、v、nb、cr的中间合金以及c-fe、si-fe、mn-fe的中间合金,保温12min,搅拌均匀后除渣;再次在1280~1580
º
c加入由ti-c粉末压制成的块体料,保温30min;然后在1280~1480
º
c加入re-m的中间合金,保温4min,保温过程一直电磁搅拌;最后真空炉内浇铸出炉,得母合金;s2:对s1制备的母合金进行电渣重熔;在上述电渣重熔的同时,通过加强结晶器出料口的冷却能力(用冷却水或直接将坯料一端拉入水中)、保温熔池侧壁的方法(线圈加热+传感器)控制熔池的温度梯度,使凝固方向与熔池侧壁的夹角保持20~30
°
,得到净化后的母合金熔体。
40.s3:将s2电渣重熔后的母合金在保护性气氛中滴铸到铜模内,得到滴铸的铸锭;s4:将s3的铸锭破碎,并球磨制粉;上述球磨制粉的工艺如下:s4-1:将s3得到的滴铸铸锭破碎至0.1~1mm;s4-2:用行星球磨机将粉末混合到酒精中,球与粉的重量比为5:1,磨粉时间50小时;s4-3:将碾磨后的混合料浆在78℃下干燥8h,过筛后转入低氧分压的干燥室进行一定预氧化;s4-4:将s4-3获得的合金粉末密封封存。
41.在上述球磨制粉的过程中,通过检测粉末的平均成分,若合金元素的含量不满足要求,还相应的加入tic、vn 、wc、mo2c、cr3c2、vc、nbc粉末中的一种或其组合,使得最终制成的合金粉末符合成分要求。
42.s5:对s4合金粉末依次进行还原退火和粉末压坯,制备成粉末块体坯料;上述还原退火的工艺如下:在真空炉内进行,炉内成真空状态或惰性气体保护状态,将粉末平铺在基板上,厚度为5mm,多层基板叠加放置,相邻基板间距30mm,温度400℃,保温时间60min,随炉冷却到室温后取出。过程中检测炉内气氛氧含量,使氧含量小于10ppm。
43.上述粉末压坯的工艺为非hip压坯:将经还原退火后的合金粉末称重后放入压坯模具中,将粉末双向模压制成块体坯料;压力1200mpa。
44.s6:对s5所得粉末块体坯料进行烧结;上述烧结的方式可以为常压保护性气氛烧结:(1)烧结炉内冲入保护性惰性气体,排出氧气,使烧结炉内的氧含量小于1ppm;(2)以10℃/min的速度升温至650℃,保温时间t=5min/cm
×
d;(3)以10℃/min的速度升温至1220℃,保温时间t=20min/cm
×
d;(4)随炉冷却至室温;其中,d为样品的最大壁厚,单位cm。
45.s7:对s6所得烧结后的粉末块体坯料进行分级热处理;上述分级热处理的工艺如下(如图1和2):(1)预热:以5℃/min的升温速度加热至580℃,保温时间t=3min/cm
×
d;(2)二次预热:紧接着以5℃/min的升温速度加热至840℃,保温时间t=2min/cm
×
d;(3)淬火保温:紧接着以5℃/min的升温速度加热至1170℃,保温时间t=2min/cm
×
d;(4)淬火冷却:紧接着,当d≥10时,首先以104℃/s的降温速度降温至300℃,保温时间t=1min/cm
×
d,然后以104℃/s的降温速度降温至20℃,保温时间t=1.5min/cm
×
d(如图1);当10≥d≥5时,以105℃/s的降温速度降温至200℃,保温时间t=1min/cm
×
d,然后以104℃/s的降温速度降温至40℃,保温时间t=1.5min/cm
×
d(如图1);当d≤5cm时,以105℃/s的降温速度降温至40℃,保温时间t=1.5min/cm
×
d(如图2);(5)深冷处理:紧接着以105℃/s的降温速度降温至-100℃,保温时间t=1min/cm
×
d;(6)回火:紧接着以5℃/min的升温速度加热至560℃,保温时间t=1h/cm
×
d;(7)冷却:紧接着随炉冷却至200℃,出炉空冷至40℃;(8)重复(6)和(7)至少一次;其中,d为样品的最大壁厚,单位cm。
46.s8:对所述s7所得粉末块体坯料进行锻造和挤压、轧制、拉拔处理,得到φ2mm的丝材;上述锻造的工艺如下:预热:首先以8℃/min的加热速度将坯料加热至620℃,保温时间t=3min/cm
×
d ;然后以8℃/min的升温速度加热至860℃,保温时间t=2min/cm
×
d;其中,d为样品的最大壁厚,单位cm;锻造:对坯料进行锻造,每次减小量为5%,每次锻造完后直接将坯料重新放入840℃的炉中加热,加热时间t=3min/cm
×
d,直至将坯料锻造至所需尺寸;冷却:将锻造完成的坯料放入炉中随炉冷却至200℃,然后出炉空冷至室温。
47.上述挤压的方式为热挤压,工艺如下:预热:首先以7℃/min的加热速度将坯料加热至620℃,保温时间t=5min/cm
×
d;然后以7℃/min的升温速度加热至900℃,保温时间t=4min/cm
×
d;其中,d为样品的最大壁厚,单位cm;热挤压:挤压方式为卧式挤压,挤压速度5mm/s,单次挤压截面减小8%,挤压模具预热温度750℃;冷却:将挤压完成的坯料放入炉中随炉冷却至260℃,然后出炉空冷至室温。
48.s9:对s8所得丝材再次进行分级热处理。本步骤中的分级热处理工艺如图1和2,与上述s6中的工艺相同,此处不做赘述。
49.实施例5:本实施例与实施例4大致相同,不同点仅在于,本实施方式中,s5:对s4合金粉末依次进行还原退火和粉末压坯,制备成粉末块体坯料;上述粉末压坯的工艺为hip压坯:将经还原退火后的合金粉末称重后放入压坯模具中,进行hip压坯,将粉末模压制成块体坯料,压力120~500mpa。
50.s6:对s5所得粉末块体坯料进行烧结;上述烧结的方式为hip烧结:(1)将粉末块体坯料装入中空壳体,并抽真空,密封;
(2)以10℃/min的速度升温至650℃,保温时间t=5min/cm
×
d;(3)以10℃/min的速度升温至1180℃,保温时间t=20min/cm
×
d;(4)随炉冷却至室温;其中,d为样品的最大壁厚,单位cm。
51.除此之外,本实施例与实施例4完全相同,此处不做赘述。
52.实施例6:本实施例与实施例4大致相同,不同点仅在于,本实施方式中,s8:对所述s7所得粉末块体坯料进行锻造、轧制、拉拔处理,得到φ2mm的丝材;上述锻造的工艺如下:预热:首先以8℃/min的加热速度将坯料加热至620℃,保温时间t=3min/cm
×
d ;然后以8℃/min的升温速度加热至860℃,保温时间t=2min/cm
×
d;其中,d为样品的最大壁厚,单位cm;锻造:对坯料进行锻造,每次减小量为5%,每次锻造完后直接将坯料重新放入840℃的炉中加热,加热时间t=3min/cm
×
d,直至将坯料锻造至所需尺寸;冷却:将锻造完成的坯料放入炉中随炉冷却至200℃,然后出炉空冷至室温。
53.除此之外,本实施例与实施例4完全相同,此处不做赘述。
54.对比例1:使用论文“彭翰林, 精冲模具用粉末冶金高速钢s390/s790的热处理规律研究, 华中科技大学, 2020.
ꢀ”
中公开的配方和方法制备丝材。
55.通过下表1展示实施例a至c的配方分别使用实施例1至6制备得到的丝材性能以及对比例1制备得到的丝材性能。
56.表1
上述实施方式只为说明本发明的技术构思及特点,其目的在于让熟悉此项技术的人能够了解本发明的内容并据以实施,并不能以此限制本发明的保护范围。凡根据本发明精神实质所做的等效变换或修饰,都应涵盖在本发明的保护范围之内。