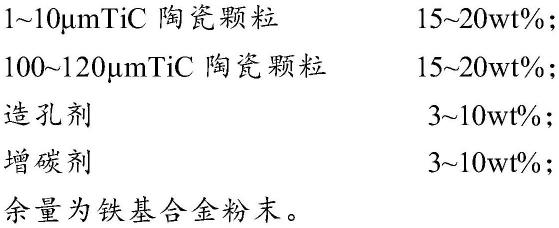
一种tic陶瓷/铁基复合涂料、碳钢基复合材料及其制备方法
技术领域
1.本发明涉及复合涂层技术领域,尤其涉及一种tic陶瓷/铁基复合涂料、碳钢基复合材料及其制备方法。
背景技术:2.钢铁材料被广泛应用在各个工业领域中,支撑着各行业领域的快速发展。然而,金属的腐蚀现象在各种工业和自然环境下都非常容易发生,遍及国民经济各个领域,给国民经济带来了巨大的损失。据统计,腐蚀造成的经济损失占国民经济总产值5%,每年高达5万亿元,每年腐蚀生锈的钢铁约占产量的20%,约有30%的设备因腐蚀而报废。
3.目前,在钢铁材料表面通过激光熔覆方法制备无机陶瓷涂层可以获得具有高硬度和高强度的耐腐蚀涂层,但是陶瓷材料与钢铁基体的匹配性不佳,存在润湿性差和脆性大等缺点,因此常采用陶瓷/金属复合体系能有效降低熔覆层的热应力,减少熔覆层中出现的裂纹缺陷,提高陶瓷与钢铁基体的结合力;并且铁基合金具有成本低廉、力学性能好、机加工和焊接性能好、耐腐蚀等一系列优点。
4.铁基合金作为熔覆材料与钢铁材料表面结合强度高,因此常被用于表面防护和表面修复领域。但是,复合涂层的强度、硬度、耐腐蚀性等重要性能仍然与陶瓷增强相的质量分数相关。陶瓷相的质量分数增大会明显提高复合涂层的强度、硬度、耐磨和耐腐蚀性能,满足长期服役的性能需求;但是传统激光熔覆时增大陶瓷粉末的质量分数会导致复合涂层结合力下降,增强相脱落,裂缝缺陷增加等问题,造成性能严重下降,不能满足对高性能涂层长期服役的需求。
技术实现要素:5.本发明解决的技术问题在于提供一种具有高硬度、高耐磨性和耐腐蚀性的碳钢基复合材料。
6.有鉴于此,本技术提供了一种tic陶瓷/铁基复合涂料,包括:
[0007][0008][0009]
优选的,所述造孔剂为陶瓷造孔剂,所述造孔剂的粒径为1~5μm。
[0010]
优选的,所述增碳剂为石墨粉增碳剂,所述增碳剂的粒径为100~150μm。
[0011]
本技术还提供了一种碳钢基复合材料,由碳钢基体和复合于所述碳钢基体表面的
涂层组成,所述涂层由所述的tic陶瓷/铁基复合涂料制备得到。
[0012]
优选的,所述碳钢基体选自低碳钢基材、中碳钢基材或高碳钢基材。
[0013]
优选的,所述涂层的厚度为1.0~1.5mm。
[0014]
本技术还提供了所述的碳钢基复合材料的制备方法,包括以下步骤:
[0015]
将50~100nmtic陶瓷颗粒、1~10μmtic陶瓷颗粒、100~120μmtic陶瓷颗粒、造孔剂、增碳剂和铁基合金粉末按照比例混合后干燥,得到tic陶瓷/铁基复合粉末;
[0016]
将所述tic陶瓷/铁基复合粉末在碳钢基体表面进行激光熔覆。
[0017]
优选的,所述混合的时间为50~150min,所述干燥的温度为50~100℃,时间为5~10h。
[0018]
优选的,所述激光熔覆的保护气体为氩气。
[0019]
优选的,所述激光熔覆的激光功率为1500~3000w,扫描速度为300~1000mm/min,送粉器转速为3~10r/min。
[0020]
本技术提供了一种碳钢复合材料,其包括碳钢基体和碳钢基体表面的涂层,其中涂层中包括不同粒径的tic陶瓷颗粒、造孔剂、增碳剂和铁基合金粉末,其中tic陶瓷颗粒具有高硬度、高耐磨性、高熔点和化学稳定性优异等特性;并采用纳米、微米级多尺度碳化钛陶瓷颗粒的复配,提高了陶瓷增强相与铁基合金粉末的结合力,提高了tic陶瓷/铁基复合涂层材料在服役过程中的硬度、耐磨性和耐腐蚀性能,降低缺陷的产生。
[0021]
本技术还提供了碳钢基复合材料的制备方法,其通过铁基合金粉末和多尺度tic陶瓷颗粒混合获得预制粉末层,在激光熔覆过程中,借助于合金中化学反应的原位自生法直接生成尺寸细小、分布均匀的tic陶瓷增强相,这种增强相与基体之间原位匹配,界面结合性和热力学稳定性好,熔覆层与基体结合性好;同时增碳剂与造孔剂的复配在熔覆层中形成充足、分布均匀的细小孔隙,提高碳化钛陶瓷增强相的占比,提升增强效果,并避免陶瓷相的聚集造成增强相的脱落、结合力下降等问题。
附图说明
[0022]
图1为本发明实施例1制备的复合材料的微观照片;
[0023]
图2为图1中对应区域的局部高分辨率微观照片。
具体实施方式
[0024]
为了进一步理解本发明,下面结合实施例对本发明优选实施方案进行描述,但是应当理解,这些描述只是为进一步说明本发明的特征和优点,而不是对本发明权利要求的限制。
[0025]
针对现有技术中陶瓷涂层与碳钢基体存在的诸多问题,本技术提供了碳钢基复合材料及其制备方法,在制备的过程中通过激光熔覆原位生长自渗透孔隙原理,与造孔剂和增碳剂协同作用,通过原位生长细化晶粒使得陶瓷增强相均匀分布并提高其质量分数;采用不同尺度tic粉末复配,进一步提高复合涂层性能的同时避免陶瓷相增加导致的性能下降的问题,由此制备了具有高性能的高质量分数陶瓷相增强的陶瓷/铁基复合涂层。具体的,本发明实施例首先公开了一种tic陶瓷/铁基复合涂料,包括:
[0026][0027][0028]
在本技术提供的tic陶瓷/铁基复合涂料中,所述tic陶瓷颗粒具有高硬度、高耐磨性、高熔点以及化学稳定性优异等特性,并采用纳米、微米级多尺度碳化钛陶瓷颗粒的复配,提高陶瓷增强相与铁基合金粉末的结合力,以提高陶瓷/铁基复合涂层材料在服役过程中的硬度、耐磨性和耐腐蚀性能,降低缺陷的产生。为了避免增强相tic颗粒占比的增加导致对涂层产生负面效应,进一步的本技术选用纳米级和微米级的多尺度tic陶瓷颗粒复配,提高陶瓷与铁基合金相的结合作用;同时高硬度、高熔点的多尺度碳化钛粉末复配相比于单一尺度陶瓷粉末,进一步提高复合涂层的性能。在本技术中,50~100nmtic颗粒的含量为15~20wt%,具体的,所述50~100nmtic颗粒的含量为15wt%、16wt%、17wt%、18wt%、19wt%或20wt%;1~10μmtic颗粒的含量为15~20wt%,具体的,所述1~10μmtic颗粒的含量为15wt%、16wt%、17wt%、18wt%、19wt%或20wt%;100~120μmtic颗粒的含量为15~20wt%,具体的,所述1~10μmtic颗粒的含量为15wt%、16wt%、17wt%、18wt%、19wt%或20wt%。
[0029]
所述造孔剂和所述增碳剂与tic陶瓷颗粒复配,可以使得陶瓷增强相均匀分布并提高tic陶瓷颗粒的质量分数,有利于涂层各项性能的提高。所述造孔剂选自本领域技术人员熟知的陶瓷造孔剂,对其来源本技术没有特别的限制,其含量为3~10wt%,具体的,所述造孔剂的含量为3wt%、4wt%、5wt%、6wt%、7wt%、8wt%、9wt%或10wt%。所述增碳剂选自本领域技术人员熟知的石墨粉增碳剂,对其来源本技术没有特别的限制,其含量为3~10wt%,具体的,所述增碳剂的含量为3wt%、4wt%、5wt%、6wt%、7wt%、8wt%、9wt%或10wt%。
[0030]
相应的,余量为铁基合金粉末,所述铁基合金粉末具体选自奥氏体不锈钢粉末和马氏体不锈钢粉末。
[0031]
上述tic陶瓷颗粒、造孔剂、增碳剂和铁基合金粉末的来源本技术没有特别的限制,为市售产品或按照本领域常规方法制备得到即可。
[0032]
为了避免陶瓷材料与钢铁基体润湿性差的问题,本发明采用的铁基合金粉末与陶瓷粉末的复合体系,铁基合金粉末与钢铁材料良好的相容性提高了复合涂层与钢铁基体材料的结合性能。
[0033]
本技术还提供了一种碳钢基复合材料,其包括碳钢基体和复合于所述碳钢基体表面的涂层,所述涂层由上述tic陶瓷/铁基复合涂层制备得到。
[0034]
在本技术中,所述碳钢基体为本领域技术人员熟知的碳钢基体,其具体选自低碳钢基材、中碳钢基材或高碳钢基材;对其来源本技术没有特别的限制。
[0035]
在本技术提供的碳钢基复合材料中,所述涂层的厚度为1.0~1.5mm。
[0036]
本技术还提供了碳钢基复合材料的制备方法,包括以下步骤:
[0037]
将50~100nmtic陶瓷颗粒、1~10μmtic陶瓷颗粒、100~120μmtic陶瓷颗粒、造孔剂、增碳剂和铁基合金粉末混合后干燥,得到tic陶瓷/铁基复合粉末;
[0038]
将所述tic陶瓷/铁基复合粉末在碳钢基体表面进行激光熔覆。
[0039]
在制备碳钢基复合材料的过程中,首先将50~100nmtic陶瓷颗粒、1~10μmtic陶瓷颗粒、100~120μmtic陶瓷颗粒、造孔剂、增碳剂和铁基合金粉末按照比例混合、干燥,即得到tic陶瓷/铁基复合粉末;所述混合采用本领域技术人员熟知的混合方式,可以在混料机中高速混合,所述混合的时间为50~150min,更具体地,所述混合的时间为90~120min。所述干燥的温度为50~100℃,时间为5~10h;更具体地,所述干燥的温度为60~70℃,时间为6~8h。
[0040]
在得到tic陶瓷/铁基复合粉末之后,本技术则将其在碳钢基体表面进行激光熔覆;所述激光熔覆的操作手段按照本领域技术人员熟知的方式进行即可;在激光熔覆的过程中,所述激光熔覆在保护性气体氩气中进行,所述激光熔覆的激光功率为1500~3000w,扫描速度为300~1000mm/min,送粉器转速为3~10r/min;更具体地,所述激光熔覆的激光功率为1800~2500w,扫描速度为300~900mm/min,送粉器转速为3~5r/min。
[0041]
本技术通过激光熔覆的办法在原位生长陶瓷增强相,得到碳化物陶瓷增强铁基复合涂层材料;通过不同种类碳化物陶瓷增强相复配获得最佳耐磨、强度的复合涂层。
[0042]
本技术通过铁基合金粉末和多尺度tic陶瓷颗粒混合获得预制粉末层,在激光熔覆过程中,借助于合金中的化学反应的原位自生法直接生成尺寸细小、分布均匀的碳化钛陶瓷增强相,这种增强相与基体之间原位匹配,界面结合性和热力学稳定性好,熔覆层与基体结合性好;增碳剂与造孔剂的复配在熔覆层中形成充足、分布均匀的细小孔隙,提高碳化钛陶瓷增强相的占比,提升增强效果,并避免陶瓷相的聚集造成增强相的脱落、结合力下降等问题。
[0043]
本发明采用的激光熔覆的方法,基材形状尺寸不受限制,制备工艺简单,操作方便,易于实现自动化,无污染,且熔覆不需要在真空条件下进行,因此可用于复杂表面的修复;采用的多尺度tic陶瓷颗粒熔解再析出的过程中,与铁基合金粉末和钢铁基体进行重新结合,并充分渗透由于造孔剂和增碳剂获得的均匀细小的孔隙中,从而提高tic陶瓷相的占比,提升复合涂层的性能;铁基合金粉末提高了复合涂层的韧性,使得熔覆层与钢铁基体良好结合得到高耐磨、高硬度、耐腐蚀的高增强相质量分数的多尺度碳化钛陶瓷/铁基复合涂层。
[0044]
为了进一步理解本发明,下面结合实施例对本发明提供的碳钢基复合材料及其制备方法进行详细说明,本发明的保护范围不受以下实施例的限制。
[0045]
实施例
[0046]
将70nm的tic陶瓷颗粒、5μm的tic陶瓷颗粒、110μm的tic陶瓷颗粒、造孔剂型号为pl-2、增碳剂型号为fc99-1和铁基合金粉末为fe60a,按比例在混料机中高速混合90~120min,混合均匀后在60~70℃下干燥6~8h,得到tic陶瓷/铁基复合粉末;以q235碳钢作为基体材料,基材表面使用角磨机抛光并用丙酮清洗表面并干燥;
[0047]
将上述得到的复合粉末在基材表面进行激光熔覆,在激光熔覆时,采用氩气作为保护气体,激光功率为1500~3000w,扫描速率为300~900mm/min,送粉器转速为3~5r/
min;
[0048]
原料的比例具体如表1所示,对制备的涂层进行性能检测,检测结果如表2所示;
[0049]
图1和图2为实施例1制备的复合材料的微观照片和对应区域的局部高分辨率微观图像;由图1和图2可知,熔覆层内部呈现出三维网格状形貌,组织细小致密且无明显裂纹出现,存在大量白亮相与灰质相弥散分布,试样横截面三层结构也无明显裂纹,涂层与基体界面间结合紧密;在高分辨率围观图像中可以更清楚的发现:熔覆层表面到内部,粘接层间无明显杂质和缺陷的产生。
[0050]
表1 实施例1~8提供的具体成分数据表(wt%)
[0051][0052]
表2 实施例1~8制备的涂层的性能测试数据表
[0053][0054][0055]
注:1)采用hvs-1000维氏硬度计测试复合涂层表面显微硬度分布,法向载荷300g,加载时间为15s,每个表面测量三个点取平均值作为表面显微硬度值;
[0056]
2)采用mrh-3w高速摩擦磨损试验机,根据gb/t 12444-2006对碳化物陶瓷/铁基复合涂层的耐磨性进行测试;测试前后分别对样品表面进行清洗烘干处理,通过分析天平称
重计算磨损失重(磨损失重=磨损前质量-磨损后质量)。
[0057]
以下对比例的制备方法与实施例相同,区别仅在于下述表中的组分的差别,具体数值与性能数据如表3~8所示;
[0058]
表3 对比例1~6不同组分的成分数据表
[0059][0060]
表4 对比例1~6制备的涂层的性能测试数据表
[0061][0062][0063]
表5 对比例7~12不同组分的成分数据表
[0064][0065]
表6 对比例7~12制备的涂层的性能测试数据表
[0066]
组别硬度/hv磨损失重/mg对比例74768.8对比例84888.6对比例95028.2对比例105117.8对比例115308.1对比例125427.7
[0067]
表7 对比例7~12不同组分的成分数据表
[0068]
组别对比例13对比例14对比例1550~100nm tic2020251~10μm tic202525100~120μm tic252525造孔剂555增碳剂555铁基合金粉末252015
[0069]
表8 对比例13~15制备的涂层的性能测试数据表
[0070]
组别硬度/hv磨损失重/mg对比例1388015.7对比例1486918.8对比例1588419.5
[0071]
以上实施例的说明只是用于帮助理解本发明的方法及其核心思想。应当指出,对于本技术领域的普通技术人员来说,在不脱离本发明原理的前提下,还可以对本发明进行若干改进和修饰,这些改进和修饰也落入本发明权利要求的保护范围内。
[0072]
对所公开的实施例的上述说明,使本领域专业技术人员能够实现或使用本发明。对这些实施例的多种修改对本领域的专业技术人员来说将是显而易见的,本文中所定义的一般原理可以在不脱离本发明的精神或范围的情况下,在其它实施例中实现。因此,本发明
将不会被限制于本文所示的这些实施例,而是要符合与本文所公开的原理和新颖特点相一致的最宽的范围。