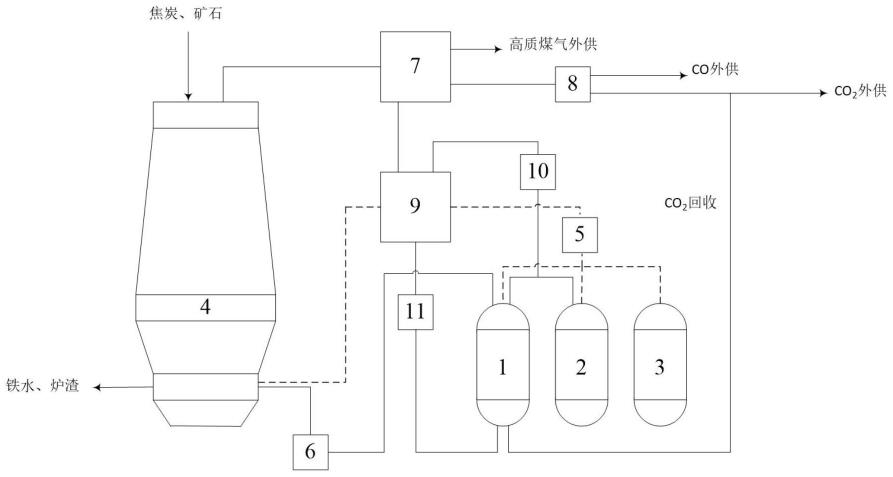
一种基于co2循环的全氧/高富氧炼铁造气系统及运行方法
技术领域
1.本发明属于高炉炼铁绿色高效生产领域,通过尾气二氧化碳捕集后循环回用,实现高炉全氧或高富氧炼铁生产,在降低燃料消耗、提升炼铁效率的同时,既避免了二氧化碳排放,又制备高质煤气并外供,是一种钢铁低碳生产方法。具体是一种基于co2循环的全氧(高富氧)炼铁造气系统及运行方法。
背景技术:2.以铁矿石和煤炭为初始原料的长流程钢铁生产工序是世界主流的钢铁生产方法之一,其中我国钢总产量的85%以上由长流程提供,如何进一步降低长流程钢铁生产工序能耗和碳排放是实现钢铁低碳制造的关键。高炉是“长流程”钢铁生产工艺的核心环节,其产铁量仍占世界铁总产量的95%以上,能量消耗约占整个能耗的50%,并产生了整个钢铁工业70%的碳排放,降低高炉炼铁的能耗及碳排意义重大。
3.高炉炼铁生产具有经济指标好,工艺简单,生产量大,生产效率高等优点,随着近几十年高炉炼铁工艺的发展及完善,诸多节能降耗技术已得到大规模推广应用,如富氧鼓风、燃料喷吹、布料分布控制及余能回收等,目前传统炼铁高炉其能耗水平和运行效率等已接近理论极限,燃料比约为500kg/t,炉身效率约为95%,利用系数2.4~3.5。即便如此,高炉炼铁仍然是钢铁流程内能耗及碳排放最大的工序环节,如何进一步降低高炉炼铁的碳耗、减少二氧化碳的排放,需要突破传统高炉工艺的束缚,发展新一代的低碳炼铁工艺。
4.全氧高炉炼铁技术被视为未来炼铁的发展趋势,主要工艺特征有:
①
采用氧气代替热风;
②
大量喷吹煤粉;
③
炉顶煤气脱除co2后循环喷吹进入高炉。理论上:全氧高炉冶炼强度高,与传统高炉相比利用系数可提高一倍;通过大量喷吹煤粉,改变炼铁过程的能源结构,大幅减少焦炭消耗;煤气循环后可降低燃料比100kg左右。
5.但是,现有氧气高炉工艺方案均存在以下问题未能妥善解决:
①
纯氧燃烧剧烈放热,造成炉体下部炉况恶化,即使采用了煤气循环,依旧影响了高炉寿命;
②
炉顶煤气脱除二氧化碳过程中,气体分离能耗及成本较大,同时循环的一氧化碳受炉内热力学及动力学限制循环利用率较低,需要多次循环才能消耗;
③
炉顶煤气分离出的二氧化碳无有效治理手段,目前只能采用地质封存等方法,治理消耗和成本高,并存在安全风险。
6.另一方面,化工合成领域一般“多氢少碳”,对高品质煤气(co)有着强烈的需求,往往需要使用煤炭进行煤气化制取提供。目前较为先进的煤气化技术比煤耗约为550kg/1000m3(co+h2),co含量约为50%,h2含量约为30%。如能将高炉煤气用于化工合成生产,将对降低化工合成能耗,减少碳排具有重大意义。但是传统高炉煤气品质较差,一氧化碳含量约为18~25%,不适用于化工合成生产;全氧高炉煤气品质高,具备化工应用的可能,但现有氧气高炉工艺方案均为考虑煤气外供。
技术实现要素:7.本发明在高炉风口回旋区内二氧化碳气体与碳发生吸热反应,利用二氧化碳反应
吸热与氧气反应放热相互平衡稳定风口温度,可进一步提高热风中高富氧率,大幅度提高冶炼强度;同时高炉喷吹二氧化碳和提高富氧率后,热风与碳反应生成更高浓度的一氧化碳,可提高炉内铁矿石的间接还原度,并增加炉顶煤气一氧化碳浓度;热风炉使用高浓度一氧化碳煤气配合富氧燃烧,可提高热风炉热效率,减少煤气消耗量和尾气产生量,同时提高燃烧尾气中二氧化碳浓度。
8.一种基于co2循环的全氧/高富氧炼铁造气系统,其特征在于将从热风炉废气捕集和炉顶煤气中分离获得的二氧化碳,用于高炉鼓风和喷煤,从而实现全氧或高富氧炼铁生产,提升炼铁效率、降低冶炼消耗,并获得高质煤气直接外供或分离二氧化碳后外供。
9.进一步地,热风炉使用全氧或高富氧炼铁的高质煤气与氧气、二氧化碳循环燃烧,大幅提高热风炉尾气二氧化碳浓度,降低二氧化碳捕集难度,并节约热风炉运行能耗。
10.进一步地,本系统由二氧化碳气源、氧气气源、空气气源、高炉本体、鼓风混气装置、煤粉喷吹装置、炉顶煤气处理装置、煤气分离装置、热风炉、助燃风混气装置、热风炉尾气二氧化碳捕集装置及附属管道组成。
11.如上所述一种基于co2循环的全氧/高富氧炼铁造气系统的运行方法,其特征于在其运行过程为:
12.步骤1、由二氧化碳气源、氧气气源或二氧化碳气源、氧气气源、空气气源向鼓风混气装置供气,形成混合反应气,其中二氧化碳比例为15~35%,氧气比例为45~65%,空气比例为0~40%;混合反应气进入热风炉,经加热成为高温混合反应气,再沿热风管道由风口进入高炉本体;
13.步骤2、由二氧化碳气源向煤粉喷吹装置供气,二氧化碳作为载气与煤粉形成二氧化碳-煤粉混合流,再沿喷煤管道由煤粉枪进入高炉本体;
14.步骤3、矿石与焦炭由高炉炉顶加入,随着高炉运行逐步下行升温,并依次形成块状带、软熔带、滴落带,最终反应生成铁水和炉渣由出铁/渣口排出;
15.步骤4、高温混合反应气、二氧化碳-煤粉混合流进入高炉本体后,在风口区域与焦炭发生燃烧反应,生成大量co浓度75~90%的还原性气体;还原性气体上升依次穿过滴落带、软熔带、块状带与下降的矿石发生还原反应,生成高质煤气由炉顶煤气处理装置排出;高质煤气中co浓度为40~55%,二氧化碳浓度为30~40%;
16.步骤5、15~25%部分高质煤气进入热风炉;
17.步骤6、由二氧化碳气源、氧气气源向助燃风混气装置供气,形成助燃风混合气,进入热风炉;其中二氧化碳比例为60~75%,氧气比例为25~40%;
18.步骤7、热风炉内高质煤气与助燃风混合气反应燃烧,产生的co2浓度为70~95%热风炉尾气进入热风炉尾气二氧化碳捕集装置,捕集获得二氧化碳气,再输送至二氧化碳气源;
19.步骤8、剩余75~85%高质煤气直接外供或进入煤气分离装置制取获得二氧化碳气和一氧化碳气,二氧化碳气输送至二氧化碳气源或外供,一氧化碳气外供。
20.本发明实施可基于现有高炉系统进行技术改造或全新建造,适用于所有体积容量的高炉。
21.本发明技术利用尾气co2循环实现全氧或高富氧高炉炼铁生产,风口回旋区碳燃烧速率较普通高炉可提高1~2倍,有效容积利用系数可提高40%~90%;
22.生产吨铁燃料比为600~650kg,并实现外供一氧化碳450~600m3,与相同规模的氧气高炉炼铁和煤气化生产相比可降低燃料比70~100kg;
23.炼钢过程产生的二氧化碳可全部回收利用,避免了二氧化碳排放,吨铁直接减少排放二氧化碳约700~750m3;
24.热风炉能耗降低约60~80%,降低尾气co2捕集难度,减少捕集能耗约约50~70%。
附图说明
25.图1为一种基于co2循环的全氧(高富氧)炼铁造气系统及运行方法工艺流程示意图,
26.1—二氧化碳气源、2—氧气气源3—空气气源、4—高炉本体、5—鼓风混气装置、6—煤粉喷吹装置、7—炉顶煤气处理装置、8—煤气分离装置、9—热风炉、10—助燃风混气装置、11—热风炉尾气二氧化碳捕集装置。
具体实施方式
27.实施例1
28.(1)基于某5500m3高炉改造为co2循环的高富氧炼铁造气系统。
29.(2)如图1所示,本发明由二氧化碳气源1、氧气气源2、空气气源3、高炉本体4、鼓风混气装置5、煤粉喷吹装置6、炉顶煤气处理装置7、煤气分离装置8、热风炉9、助燃风混气装置10、热风炉尾气二氧化碳捕集装置11及附属管道组成。
30.(3)具体运行方法为:
31.(步骤1)由二氧化碳气源1、氧气气源2、空气气源3向鼓风混气装置供气5,形成混合反应气,其中二氧化碳比例为15%,氧气比例为45%,空气比例为40%;混合反应气进入热风炉9,经由热风炉9加热后,成为高温混合反应气,沿热风管道由风口进入高炉本体4;
32.(步骤2)由二氧化碳气源1向煤粉喷吹装置6供气,二氧化碳1作为载气与煤粉形成二氧化碳-煤粉混合流,沿喷煤管道由煤粉枪进入高炉本体4;
33.(步骤3)矿石与焦炭由高炉炉顶加入,随着高炉运行逐步下行升温,并依次形成块状带、软熔带、滴落带,最终反应生成铁水和炉渣由出铁/渣口排出;
34.(步骤4)高温混合反应气、二氧化碳-煤粉混合流进入高炉本体4后,在风口区域与焦炭发生燃烧反应,生成大量还原性气体(co浓度75%);还原性气体上升依次穿过滴落带、软熔带、块状带与下降的矿石发生还原反应,生成高质煤气由炉顶煤气处理装置7排出。高质煤气中co浓度为40%,二氧化碳浓度约为30%;
35.(步骤5)部分高质煤气(25%)进入热风炉9。
36.(步骤6)由二氧化碳气源1、氧气气源2向助燃风混气装置10供气,形成助燃风混合气进入热风炉。其中二氧化碳比例为75%,氧气比例为25%;
37.(步骤7)热风炉内高质煤气与助燃风混合气反应燃烧,产生的热风炉尾气(co2浓度为70%)进入热风炉尾气二氧化碳捕集装置11,制取获得二氧化碳气,输送至二氧化碳气源1;
38.(步骤8)剩余高质煤气(75%)直接外供或进入煤气分离装置8制取获得二氧化碳
气和一氧化碳气,二氧化碳气输送至二氧化碳气源1或外供,一氧化碳气外供。
39.本技术实施后:
40.利用尾气co2循环实现高富氧高炉炼铁生产,风口回旋区碳燃烧速率较原高炉提高1倍,有效容积利用系数提高40%;
41.生产吨铁燃料比为600kg,并实现外供一氧化碳450m3,与相同规模的氧气高炉炼铁和煤气化生产相比降低燃料比70kg。
42.炼钢过程产生的二氧化碳可全部回收利用,避免了二氧化碳排放,吨铁直接减少排放二氧化碳约700m3。
43.热风炉能耗降低约60%,降低尾气co2捕集难度,减少捕集能耗约50%。
44.实施例2
45.(1)基于某1780m3高炉改造为co2循环的全氧炼铁造气系统。
46.(2)如图1所示,本发明由二氧化碳气源1、氧气气源2、空气气源3、高炉本体4、鼓风混气装置5、煤粉喷吹装置6、炉顶煤气处理装置7、煤气分离装置8、热风炉9、助燃风混气装置10、热风炉尾气二氧化碳捕集装置11及附属管道组成。
47.(3)具体运行方法为:
48.(步骤1)由二氧化碳气源1、氧气气源2向鼓风混气装置供气5,形成混合反应气,其中二氧化碳比例为35%,氧气比例为65%;混合反应气进入热风炉9,经由热风炉9加热后,成为高温混合反应气,沿热风管道由风口进入高炉本体4;
49.(步骤2)由二氧化碳气源1向煤粉喷吹装置6供气,二氧化碳1作为载气与煤粉形成二氧化碳-煤粉混合流,沿喷煤管道由煤粉枪进入高炉本体4;
50.(步骤3)矿石与焦炭由高炉炉顶加入,随着高炉运行逐步下行升温,并依次形成块状带、软熔带、滴落带,最终反应生成铁水和炉渣由出铁/渣口排出;
51.(步骤4)高温混合反应气、二氧化碳-煤粉混合流进入高炉本体4后,在风口区域与焦炭发生燃烧反应,生成大量还原性气体(co浓度90%);还原性气体上升依次穿过滴落带、软熔带、块状带与下降的矿石发生还原反应,生成高质煤气由炉顶煤气处理装置7排出。高质煤气中co浓度为55%,二氧化碳浓度约为40%;
52.(步骤5)由二氧化碳气源1、氧气气源2向助燃风混气装置10供气,形成助燃风混合气,其中二氧化碳比例为60%,氧气比例为40%进入热风炉;
53.(步骤6)部分高质煤气(15%)进入热风炉9。
54.(步骤7)热风炉内高质煤气与助燃风混合气反应燃烧,产生的热风炉尾气(co2浓度为95%)进入热风炉尾气二氧化碳捕集装置11,制取获得二氧化碳气,输送至二氧化碳气源1;
55.(步骤8)剩余高质煤气(85%)直接外供或进入煤气分离装置8制取获得二氧化碳气和一氧化碳气,二氧化碳气输送至二氧化碳气源1或外供,一氧化碳气外供。
56.本技术实施后:
57.利用尾气co2循环实现全氧高炉炼铁生产,风口回旋区碳燃烧速率较普通高炉可提高2倍,此时高炉有效容积利用系数提高了90%;
58.生产吨铁燃料比为650kg,并实现外供一氧化碳600m3,与相同规模的氧气高炉炼铁和煤气化生产相比降低燃料比100kg。
59.炼钢过程产生的二氧化碳可全部回收利用,避免了二氧化碳排放,吨铁直接减少排放二氧化碳约750m3。
60.热风炉能耗降低约80%,降低尾气co2捕集难度,减少捕集能耗约70%。