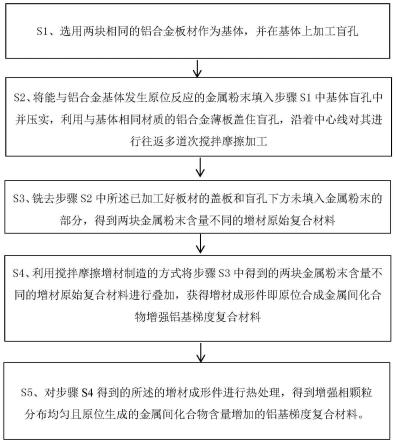
1.本发明涉及金属基复合材料制备领域,具体地涉及一种原位合成金属间化合物增强铝基梯度复合材料制备方法及复合材料。
背景技术:2.随着航空航天领域的快速发展,铝合金材料面临的服役环境日益复杂化,传统单一结构材料已无法同时满足轻量化、高强度和高硬度的要求,铝基复合材料应运而生。金属间化合物颗粒凭借其高强度、高硬度的特点而成为铝合金基体的理想增强体,其在铝合金基体中均匀分布能够产生弥散强化作用。在过去几十年里,铝基复合主要为均质复合材料,然而其在长期的实际使用过程中逐渐表现出一定局限性,例如,用均质铝基复合材料制成的飞机蒙皮,虽然表面具有较高的强度和硬度,但整体塑性、韧性较差。为了克服这一局限性,国内外研究人员逐渐尝试开发铝基梯度复合材料,其与均质复合材料最大的区别是,组织成份及力学性能在几何空间上呈现梯度或准梯度变化,从而使其在满足表面高强度、高硬度的同时仍保持内部的塑性和韧性。
3.传统的金属间化合物增强铝基梯度复合材料制备方法多为第二相外加法,即事先制备好金属间化合物颗粒,然后利用离心铸造、气相沉积、自蔓延高温合成、粉末冶金和激光熔覆等制备方法添加至基体中。然而,利用传统方法制备的非原位金属间化合物增强梯度复合材料不可避免地会出现增强相颗粒团聚、界面浸润性差以及界面污染等问题,且传统制备方法中铝合金基体的融化-凝固过程易造成气孔、微裂纹等缺陷,进而成形件性能。而对于原位复合法,尽管研究历史较短,但由于其具有生产工艺简单、成本低、生产的制件质量好等优点,如今已得到广泛关注。其中,搅拌摩擦加工具有很大的优势,其作为一种固相加工技术,加工过程中不会存在金属融化过程,能够有效避免缺陷的生成,同时加工过程中由填入粉末与基体发生原位反应而生成金属间化合物颗粒增强相,有助于解决界面浸润性差及界面污染等问题。但现阶段原位反应生成增强相的方法仍存在不足之处,例如,容易出现粉末团聚及生成的增强相含量较少的问题。
4.因此,为了有效提升原位合成的金属间化合物含量且改善增强相团聚现象,实现铝合金材料微观组织结构及力学性能在几何空间上的梯度变化,亟需研究一种微观组织结构及力学性能在几何空间上梯度变化的非均质铝基复合材料制备方法,来提升铝基复合材料的性能。
技术实现要素:5.基于上述现有技术的不足,本发明基于细小的金属间化合物颗粒均匀分布于基体中会对其产生弥散强化作用,提出一种原位合成金属间化合物增强铝基梯度复合材料制备方法及复合材料,通过该制备方法得到的复合材料能够大幅度提升金属基体的强度及硬度,并且制备方法整体较为简单,易于制造,不会增加额外的成本。本发明具体的制备过程
中通过成本低廉、绿色环保的搅拌摩擦加工、搅拌摩擦增材制造和热处理工艺制备出原位合成金属间化合物增强的铝基梯度复合材料,该复合材料的硬度及抗拉强度都大幅度得到了优化,并且经过热处理后,原位合成金属间化合物含量具有明显增加且增强相颗粒分布更加均匀。
6.具体地,一方面,本发明提供一种原位合成金属间化合物增强铝基梯度复合材料制备方法,其具体包括以下步骤:
7.s1、选用两块相同的铝合金板材作为基体,在每一块基体上均加工两排交错分布且与中心线距离相等的盲孔,其中,两块基体的盲孔总体积占各自基体体积的百分比具有差异;
8.s2、将能与铝合金基体发生原位反应的金属粉末填入步骤s1中基体盲孔中并压实,利用材质和规格均与基体相同的铝合金薄板覆盖所述盲孔,并沿着中心线对其进行往返多道次搅拌摩擦加工;
9.s3、铣去步骤s2中所述已加工好板材的盖板和盲孔下方未填入金属粉末的部分,得到两块金属粉末含量不同的增材原始复合材料;
10.s4、利用搅拌摩擦增材制造的方式将步骤s3中得到的两块金属粉末含量不同的增材原始复合材料进行叠加,获得增材成形件即原位合成金属间化合物增强铝基梯度复合材料;
11.s5、对步骤s4得到的增材成形件进行热处理,得到增强相颗粒分布均匀且原位合成的金属间化合物含量增加的铝基梯度复合材料。
12.优选地,步骤s1中改变所述的盲孔总体积占基体体积的百分比通过固定盲孔深度h,并改变盲孔直径d、盲孔与中心线距离a以及沿中心线方向的孔间距b实现,盲孔直径d、盲孔与中心线距离a以及沿中心线方向的孔间距b之间呈线性相关。
13.优选地,步骤s3中所述利用机械加工的方法铣去已加工好板材的盖板和盲孔下方未填入粉末的部分。
14.优选地,加工盲孔前利用机械打磨、酸洗或碱洗对铝合金表面进行清洁处理。
15.优选地,步骤s2中多道次为四道次。
16.优选地,步骤s2中搅拌装置包括搅拌针、轴肩和夹持端,搅拌针和轴肩与所述夹持端之间为可拆卸连接。
17.优选地,本发明的另一方面提供一种所述方法制备得到的原位合成金属间化合物增强铝基梯度复合材料。
18.与现有技术相比,本发明的有益效果如下:
19.(1)本发明提供了一种原位合成金属间化合物增强铝基梯度复合材料制备方法,其基于细小的金属间化合物颗粒均匀分布于基体中会对其产生弥散强化作用,从而提升金属基体强度、硬度的基本原理,通过增设不同尺寸盲孔的方法,调整各梯度层中填入的金属粉末的含量,利用成本低廉、绿色环保的搅拌摩擦加工、搅拌摩擦增材制造和热处理工艺,制备出金属粉末颗粒与铝合金基体原位反应充分、增强相团聚现象得到明显改善且综合力学性能能大幅度优化的非均质材料。
20.(2)本发明在搅拌摩擦加工阶段通过多道次加工使能够与铝基体发生原位反应得到的金属粉末尽可能分散开来的同时逐步闭合由于材料流动不充分而造成的孔洞缺陷。制
备得到的原位合成金属间化合物增强铝基梯度复合材料显微硬度及抗拉强度均较母材具有明显提高,且上下两梯度层存在明显的微观组织成分和力学性能层间梯度。在此基础上,热处理有效地改善了原位合成金属间化合物增强铝基梯度复合材料中存在的粉末团聚和原位合成金属间化合物含量较少的现象,同时进一步促进了增强相颗粒与铝合金基体界面处通过扩散作用形成了更好的冶金结合。
21.(3)基于本发明的整体步骤,该工艺提出了一种新的铝基梯度复合材料制备思路和方法,其整体步骤较为简单,也不需要额外的复杂方法和装置,并成功克服了现有技术中的不足和缺陷。
附图说明
22.图1为本发明的整体流程示意图;
23.图2为本发明的具体制备流程图;
24.图3a为本发明的原位合成金属间化合物增强铝基梯度复合材料上层扫描电镜下放大图;
25.图3b为本发明的原位合成金属间化合物增强铝基梯度复合材料下层扫描电镜下放大图;
26.图4a和图4b为本发明实施例中热处理前的al-tc4梯度复合材料各梯度层xrd图谱,其中图4a为上层xrd图谱,图4b为下层xrd图谱;
27.图5为本发明实施例中热处理前tc4颗粒与铝合金基体界面附近线扫描结果图;
28.图6为本发明的原位合成金属间化合物增强铝基梯度复合材料的硬度分布图;
29.图7a和图7b为本发明实施例中热处理后的al-tc4梯度复合材料各梯度层xrd衍射图谱,其中图7a为上层xrd衍射图谱,图7b为下层xrd衍射图谱;
30.图8a和图8b为本发明实施例中热处理后的原位合成金属间化合物增强铝基梯度复合材料扫描示意图,其中图8a为上层扫描图,图8b为下层扫描图;
31.图9为本发明实施例中热处理后tc4颗粒与铝合金基体界面附近线扫描结果图。
具体实施方式
32.以下,参照附图对本发明的实施方式进行说明。
33.本发明提供一种原位合成金属间化合物增强铝基梯度复合材料制备方法,如图1所示,其具体包括以下步骤:
34.s1、选用两块相同的铝合金板材作为基体,本实施例中选用6061铝合金。在每一块基体上分别加工两排交错分布且与中心线距离相等的盲孔,其中,两块基体的盲孔总体积占各自基体体积的百分比具有差异。步骤s1中改变盲孔总体积占基体体积的百分比通过固定盲孔深度h,并改变盲孔直径d、盲孔与中心线距离a以及沿中心线方向的孔间距b进行实现。
35.在具体的实施过程中,在两块板上加工盲孔前首先利用机械打磨、酸洗或碱洗对铝合金表面进行清洁处理,从而更好地进行后续工作。为了有效防止铝合金板材在加工过程中发生横向滑动和轴向变形,影响成形精度及成形件质量,本发明在用砂纸打磨掉其上下表面的氧化膜并用无水乙醇清洗掉油垢后,将其放在一块高强度高刚度金属板上方,并
用夹具固定。
36.s2、将能与铝合金基体发生原位反应的金属粉末填入步骤s1中基体的盲孔中并压实,之后利用与基体相同材质的两块铝合金薄板分别盖住两块基体的盲孔,并沿着中心线对其进行往返多道次搅拌摩擦加工。其中,沿中心线对其进行往返多道次搅拌摩擦加工应尽可能将能够与铝基体发生原位反应得到的金属粉末分散开来,同时逐步闭合由于材料流动不充分而造成的孔洞缺陷。具体应用中,搅拌装置包括搅拌针、轴肩和夹持端。本专利所使用的搅拌工具由钨钢合金制作而成。在进行搅拌摩擦加工时,搅拌头转速较高并不断与铝合金基体进行摩擦,大量的摩擦热使基体待加工区软化,同时搅拌工具逐渐向下移动,直至轴肩具有一定下压量,与周围冷金属一同形成密闭空间,随后沿着加工方向行进。搅拌工具在高温环境下不断对待加工材料进行搅拌的过程中,高温和机械作用使得搅拌针和轴肩不可避免地会受到磨损,而夹持端不直接与待加工材料接触,加工过程中磨损量极小。因此,将搅拌针与轴肩设置为可拆卸的结构,从而便于对搅拌针与轴肩进行更换,不需要对夹持端进行替换,进一步节约成本。
37.s3、铣去步骤s2中所述已加工好板材的盖板和盲孔下方未填入金属粉末的部分,得到两块金属粉末含量不同的增材原始复合材料。在具体的工作过程中,利用机械加工的方法铣去已加工好板材的盖板和盲孔下方未填入金属粉末的部分,具体是为通过搅拌摩擦增材制造技术制备铝基梯度复合材料提供加工区内部各区域均含有金属粉末的增材原始复合材料。
38.s4、利用搅拌摩擦增材制造的方式将步骤s3中得到的两块金属粉末含量不同的增材原始复合材料进行叠加,获得增材制造成形件即原位合成金属间化合物增强铝基梯度复合材料。具体地,利用搅拌摩擦增材制造的方式对两块增材原始复合材料进行叠加,应使获得的增材成形件即原位合成金属间化合物增强铝基梯度复合材料中金属粉末含量在层间呈现梯度变化且层间界面结合良好。
39.s5、对步骤s4中所述的增材制造成形件进行热处理,得到粉末分布更加均匀且原位生成的金属间化合物含量明显升高的铝基梯度复合材料。热处理时的热处理温度应使金属粉末颗粒与铝合金基体发生原位反应,增加铝合金基体中金属间化合物含量,并进一步改善颗粒团聚现象。
40.优选地,本发明的另一方面提供一种所述方法制备得到的原位合成金属间化合物增强铝基梯度复合材料。
41.具体实施例
42.本实施例提供一种原位合成金属间化合物增强铝基梯度复合材料及其制备方法,本实施例中选用6061铝合金材料,其主要性能参数如下表1所示:
43.表1 6061-t6态铝合金主要性能参数
[0044][0045]
其中,制备方法具体包括以下步骤:
[0046]
s1、选用两块尺寸相互匹配的6061铝合金板(本实例中两块方板尺寸为200mm长
×
80mm宽
×
8mm厚),其具体的制备流程如图2所示,对其进行表面处理,在每一块基体上均加工两排交错分布且与中心线距离相等的盲孔,通过固定盲孔深度h,改变盲孔直径d,与中心线距离a以及沿中心线方向的孔间距b来实现(本实例中h=6mm;盲孔直径d=2mm,3mm;与中心线距离a=1.5mm,2mm;沿中心线方向的孔间距b=5mm,6mm),tc4粉末含量分别为1.9%和3.3%。
[0047]
s2、本实施例中选用平均尺寸为42.34μm的tc4粉末,将该粉末填入已加工好的铝合金基体盲孔中并压实,用6061铝合金薄板(本实例中尺寸为200mm长
×
80mm宽
×
2mm厚)盖住盲孔,固定于自行改装的铣床上,并沿着中心线对其进行多道次搅拌摩擦加工(本实例中进行了四道次)。
[0048]
s3、利用机械加工的方法铣去已加工好板材的盖板和盲孔下方未填入tc4粉末的部分,获得两块tc4粉末含量不同且内部各区域均含有tc4粉末增材原始复合材料。
[0049]
在完成tc4粉末的填充后,用棉球擦去基体表面残留的tc4粉末。为了防止搅拌摩擦加工过程中tc4粉末溢出。将事先准备好的盖板覆盖于盲孔上方压紧并用专用夹具一同固定在铣床上,经过前期探索选用旋转速度300r/min,行进速度15mm/min,轴肩下压量0.3mm和倾斜角0
°
进行搅拌摩擦加工,将此加工成形件定义为al-tc4原始复合材料。为了在保证加工效率的前提下尽可能将tc4粉末分散开来,本专利在制备al-tc4原始复合材料时先分别采用了单道次、往返双道次和往返四道次三种搅拌摩擦加工工艺。al-tc4原始复合材料制备工艺如表1所示。通过对三种不同工艺制备出的al-tc4原始复合材料内部tc4粉末分布情况进行对比选定往返四道次作为最优制备工艺。选择最优工艺下制备出的al-tc4原始复合材料,通过机械加工的方法除去表面盖板部分和初始盲底部2mm未加入粉末的部分,剩余板厚度为6mm。将盲孔尺寸参数不同的另一块板重复上述过程即可获得两块tc4粉末体积占比不同的al-tc4增材原始复合材料。
[0050]
表2原始复合材料制备工艺
[0051][0052]
s4、利用搅拌摩擦增材制造的方式将所述的两块增材原始复合材料按照由上至下tc4粉末含量减少的方式进行叠加,获得增材制造成形件即原位合成金属间化合物增强铝基梯度复合材料。
[0053]
得到两块tc4粉末含量不同的al-tc4增材原始复合材料基础上,用丙酮除去其表面油污,用酒精擦拭表面进行清洗。随后将tc4粉末体积占比为3.3%的增材原始复合材料置tc4粉末含量占比为1.9%的增材原始复合材料之上并对齐,使用专用的夹具将两块增材原始复合材料一同固定于自行改进的铣床上。使用与加工原始复合材料相同的搅拌工具及工艺参数(旋转速度300r/min,行进速度15mm/min,下压量0.3mm和倾斜角0
°
)进行搅拌摩擦增材制造,其增材成形件即为al-tc4梯度复合材料。
[0054]
结合上述对搅拌摩擦加工过程中待加工材料热塑化材料流的受力及流动分析,可
以认为搅拌针、轴肩和较远处冷金属形成了一个模腔,tc4粉末颗粒和6061铝合金基体热塑化材料流受搅拌工具强烈的热-机耦合作用而发生剧烈的沿搅拌针轴向环状运动。在进行往返四道次搅拌摩擦加工时,6061铝合金基体热塑化材料及tc4粉末颗粒相对多次剧烈沿搅拌针轴向环状循环流动为团聚tc4粉末的分散创造了条件,同时剧烈的流动有利于填充上一道次因未充分填充而遗留的孔洞缺陷。
[0055]
所制备的原位合成金属间化合物增强铝基梯度复合材料上层和下层扫描电镜镜下放大图分别如图3a和图3b所示,原位合成金属间化合物增强铝基梯度复合材料上层和下层xrd衍射图谱分别如图4a和图4b所示。
[0056]
图3a和图3b所示的材料,增强相颗粒弥散分布于6061铝合金基体中,且颗粒数量有明显的层间梯度。因此,图3a和图3b所示的两梯度层微观组织结构具有明显的层间梯度,并有望实现6061铝合金基体力学性能在层间的梯度变化。
[0057]
通过图4a及图4b可以看出,tc4粉末含量不同的梯度层存在明显的成分梯度,tc4粉末含量为3.3%的梯度层中tc4粉末颗粒含量,原位反应生成tial3含量均高于tc4粉末含量为1.9%的梯度层。
[0058]
通过图5可以看出,tc4粉末颗粒与6061铝合金基体主要通过扩散结合,其界面处扩散层约为3.3μm。
[0059]
下表3示出了得到的复合材料热处理前的拉伸性能。
[0060]
表3 al-tc4梯度复合材料的拉伸性能
[0061][0062]
注:表中,σb和δ分别代表三次拉伸实验抗拉强度和延伸率,σb′
和δ'分别代表三次实验抗拉强度和延伸率平均值。
[0063]
由表3和表1的对比可以得知,由于原位合成的金属间化合物弥散分布于铝合金基体中。经过本发明方法得到的复合材料在拉伸性能上具有非常大的提高。
[0064]
另外,参见图6,综合而言,al-tc4梯度复合材料各梯度层显微硬度及抗拉强度均较母材明显提高,且上下两梯度层存在明显的力学性能层间梯度。tc4粉末含量为3.3%和1.9%的梯度层平均显微硬度分别为146hv和129hv,抗拉强度分别为367mpa和342mpa,延伸率分别为13.9%和13.5%。
[0065]
步骤s5、进行热处理,具体为:针对s4中所述的增材制造成形件开展热处理,热处
理选择的温度和保温时间应使增材成形件内部tc4粉末颗粒与6061铝合金基体发生充分原位反应。根据钛-铝二元相图,钛元素和铝元素发生冶金反应生成稳定的硬脆型金属间化合物tial3的温度范围为500℃~665℃。本实例中,选用570℃保温7h+空冷的热处理工艺。
[0066]
图7a和图7b为本发明实施例中热处理后的al-tc4梯度复合材料各梯度层xrd衍射图谱,其中图7a为上层xrd衍射图谱,图7b为下层xrd衍射图谱;图8a和图8b为本发明实施例中热处理后的原位合成金属间化合物增强铝基梯度复合材料扫描示意图,其中图8a为上层扫描图,图8b为下层扫描图。从图中可以看出,tc4粉末颗粒与6061铝合金基体充分反应生成金属间化合物主要为tial3,并伴随少量的tial2、tial和ti3al生成,且金属间化合物生成量随着填入tc4粉末含量的降低而减少,同时均比热处理前相应层明显增多。图9为本发明实施例中热处理后增强相颗粒与铝合金基体界面附近线扫描结果图,从图中可以看出,热处理后扩散层厚度进一步增加,相比未热处理的tc4粉末颗粒与6061铝合金界面处扩散层厚,达到8.4μm。
[0067]
综上分析,热处理有效地改善了原位合成金属间化合物增强铝基梯度复合材料中存在的粉末团聚和原位合成金属间化合物含量较少的现象,同时进一步促进了增强相颗粒与铝合金基体界面处通过扩散作用形成良好的冶金结合。
[0068]
以上所述的实施例仅是对本发明的优选实施方式进行描述,并非对本发明的范围进行限定,在不脱离本发明设计精神的前提下,本领域普通技术人员对本发明的技术方案做出的各种变形和改进,均应落入本发明权利要求书确定的保护范围内。