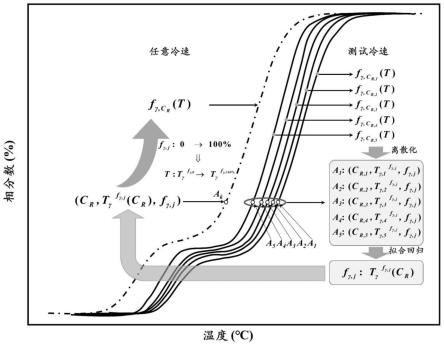
1.本发明涉及冶金连铸技术领域,提供了一种连铸全冷速条件下铸坯裂纹敏感温度区及相分数的预测方法。该方法主要应用于铸坯质量的调控、性能的预测以及连铸生产工艺参数的优化方面,也可为高温下铸坯应力应变分析提供基础数据。
背景技术:2.连铸坯的性能对后续钢产品的最终质量具有至关重要的作用。裂纹缺陷是最常见的影响连铸坯性能的主要因素(占所有缺陷类型的~50%以上)。在连铸凝固冷却过程中,裂纹的萌生与液相凝固、包晶反应等相变过程直接相关,尤以固态下发生的奥氏体分解行为的影响最直接。奥氏体分解的影响如下:(1)奥氏体分解过程中晶体结构的转变及温度变化引起的热胀冷缩效应之间的相互竞争,导致了铸坯内部复杂的热应力变化,成为诱发裂纹的重要潜在因素。(2)奥氏体分解形成的新物相的类型及含量会随温度动态变化,不同温度下的物相组成(各基体相的相分数)很大程度上决定了铸坯在该特定温度下的热塑性,直接影响铸坯在该温度下抵抗变形和外力的能力。mintz等研究表明,奥氏体分解初期晶界处形成的膜状先共析铁素体及a
e3
温度(平衡态下奥氏体分解过程开始温度)附近析出的形变诱导铁素体将导致应力集中,成为诱发裂纹缺陷的主要因素。mintz等还指出,高温下为避免连铸坯裂纹缺陷的产生,铁素体的含量应保持在40~50%以上;此外,奥氏体分解的温度区间对第三脆性区的温度范围具有重要的影响。(3)奥氏体分解结束后,组织的类型和含量决定最终铸坯在低温下的机械性能和质量。由于温度的频繁波动及铸坯不同位置的温度差异,铸坯在连铸二冷区奥氏体的分解不可避免。在不考虑钢种差异时,冷速对奥氏体分解特征温度、各基体相的类型及相分数等均具有显著影响。因此,准确预测铸坯在连铸生产过程中不同冷速下各基体相的相分数及裂纹敏感温度区,是避免裂纹产生、有效提升质量的重要基础。
3.目前对奥氏体分解行为的研究主要有avrami方程、scheil叠加原理、热膨胀法等。相较于应用范围局限于等温转变的avrami方程和推导复杂且需要大量实验辅助的scheil叠加原理而言,热膨胀法操作简单、准确性高、可避免大量繁重的金相检测,是研究材料固态相变最强有力、最简单的技术手段之一。虽然大量研究者对轧制后钢产品的奥氏体分解行为进行了量化分析,但对显微组织和晶粒尺寸与轧制产品存在显著差异的连铸坯的奥氏体相变过程的量化研究仍十分有限,高温下的线性热膨胀系数等基础物性参数(连铸坯高温应力应变数学模拟的关键参数)仍然十分匮乏。此外,连铸生产过程中,由于连铸机二冷结构、各区冷却水量、冷却方式、冷却介质等要素的差异,不同区域的铸坯及铸坯不同位置的冷却状态往往存在较大差异。在空冷区等较低冷速以及强冷区等较高冷速等连铸极端冷速条件下,由于实验设备、测试条件、测试精度等无法达到要求,导致无法准确获取连铸坯相分数及裂纹敏感温度区等关键信息,不利于连铸二冷工艺参数的优化设计及铸坯质量的有效调控。
4.通过专利搜索引擎对连铸冷却过程中奥氏体分解行为的相关研究进行搜索,暂未发现与该内容直接相关的专利技术,部分内容上有关联的专利技术如下:(1)专利“一种利用铁素体相改善铸坯表面裂纹的方法”【cn202010592850.0】中提出,在矫直段前采用冷却水将铸坯表面温度长期控制在奥氏体分解的相变温度附近,从而形成表层高比率的铁素体层(高塑性),改善铸坯表层组织塑性,降低铸坯内弧面在矫直区拉应力作用下产生的裂纹。该专利证实了可以通过控制铸坯奥氏体分解行为而达到避免裂纹产生的可行性,但无法准确预测任意冷速下达到35%铁素体的温度和时间(该专利认为35%铁素体时铸坯具备良好的热塑性)。(2)专利“奥氏体相变区等温停留控制9cr-ods钢中残余铁素体分布的方法”【cn201710090243.2】提出,将9cr-ods马氏体钢加热到奥氏体相变区等温停留,对钢中残余铁素体的分布进行调控,最终达到对钢种性能的控制。该专利证实了奥氏体相变对最终组织性能的影响,但该专利重点关注的9cr氧化物弥散强化马氏体钢中残余应变能的释放或碳化物的溶解对奥氏体相变驱动力的影响。(3)专利“硬线产品显微组织与力学性能预报系统”【cn200410061324.2】中涉及到了连铸坯奥氏体分解模型,铁素体体积分数f=1-exp(-bt2)(其中t为相变时间,b为系数),并未考虑冷速对奥氏体分解的影响。(4)专利“一种避免铁素体轧制混晶的连铸连轧生产线及生产方法”【cn202111522319.7】中设置的中间坯保温装置(以低冷速使奥氏体向铁素体的相变过程充分进行,避免发生两相区轧制而导致的混晶问题),这实质上是考虑了低冷速下奥氏体分解对粗轧和精轧产品的影响,但针对的是轧制过程中的奥氏体分解行为。
5.尽管国内外已有少量通过热膨胀曲线分析连铸坯奥氏体分解行为的研究,但都仅针对特定的冷速条件;研究的冷速范围普遍较小,研究结果无法满足复杂的连铸生产的需要。此外,与连铸过程中铸坯奥氏体分解过程的相关专利技术较少,尚未发现考虑连铸全冷速条件下铸坯裂纹敏感温度区及相分数的相关专利。基于低冷速范围的、特定冷速条件下的研究工作,其普适性已不能满足连铸坯质量调控的需要,亟待找到一种适用于钢铁生产的简单快速准确的连铸全冷速条件下铸坯裂纹敏感温度区及相分数的预测方法,为避免裂纹的产生提供指导。
技术实现要素:6.本发明的目的在于提供一种连铸全冷速条件下铸坯裂纹敏感温度区及相分数的预测方法,简单、快速、准确的预测钢铁连铸生产过程中所有可能出现的冷速条件下奥氏体分解行为的关键信息,为避免铸坯裂纹的产生、有效调控铸坯的性能、优化连铸生产工艺参数提供参考和理论基础。
7.本发明的主要内容为:
8.1)相对热膨胀量及线性热膨胀系数的测试
9.通过热膨胀仪测试不同冷速下连铸坯试样的热膨胀行为,得到试样的相对热膨胀量(dl/l0)-温度(t)曲线、线性热膨胀系数(β)-温度(t)曲线,l为试样的实时长度,l0是试样初始长度;采用c
r,i
表示第i个测试冷速,测试冷速的数量为n,则测试冷速表示为:
10.c
r,1
,...,c
r,i
,...,c
r,n i=1,2,3,...,n
ꢀꢀꢀꢀꢀꢀꢀꢀꢀꢀꢀꢀꢀꢀꢀꢀꢀꢀꢀꢀ
(1)
11.2)线性热膨胀系数曲线的分峰处理及特征温度的获取
12.根据测试得到的测试结果,通过origin软件等数据分析软件对线性热膨胀系数
(β)-温度(t)曲线进行分峰处理,要求拟合峰的函数形式采用内置的gaussian函数,且原始峰数据与拟合峰数据之间的高度和宽度误差控制在5.0%以内;分峰处理后,得到如下五个特征温度:a
r3
(奥氏体γ
→
铁素体α转变的开始温度)、a
αf
(奥氏体γ
→
铁素体α转变的结束温度)、a
r1
(奥氏体γ
→
珠光体p转变的开始温度)、a
pf
(奥氏体γ
→
珠光体p转变的结束温度)、a
int
(奥氏体γ
→
铁素体α及奥氏体γ
→
珠光体p转变的交点温度),n个不同测试冷速下的特征温度表示为:
[0013][0014]
3)特征温度的拟合及奥氏体分解温度区间的计算
[0015]
根据实验得到的n个不同测试冷速c
r,1
、c
r,2
、
…
、c
r,n
下的特征温度,应用统计分析软件研究奥氏体分解特征温度与冷速之间的函数关系,采用同一函数形式拟合确定奥氏体分解特征温度与冷速的函数关系,结果分别表示为a
r3
(cr)、a
αf
(cr)、a
int
(cr)、a
r1
(cr)、a
pf
(cr)的形式;在此基础上,根据公式(3)确定连铸全冷速条件下任意冷速时奥氏体分解的温度区间δt,定量评估第三脆性区的温度范围。
[0016]
δt=a
r3
(cr)-a
pf
(cr)
ꢀꢀꢀꢀꢀꢀꢀꢀꢀꢀꢀꢀꢀꢀꢀꢀꢀꢀꢀꢀꢀꢀꢀꢀꢀꢀꢀ
(3)
[0017]
4)奥氏体分解过程中各基体相相分数与温度变化关系的确定
[0018]
在分峰处理的基础上,对拟合得到的代表铁素体转变和珠光体转变的独立峰进行积分处理,根据各独立峰积分得到的面积与总面积的比值(其中总面积等于各独立峰面积之和),确定奥氏体分解过程中铁素体相分数、珠光体相分数、奥氏体相分数随温度的变化(以第i个测试冷速为例),具体表示为:
[0019][0020]
其中及分别为第i个测试冷速下的铁素体相分数、珠光体相分数和奥氏体相分数,为代表铁素体转变和珠光体转变的独立峰的面积总和,采用同样的方式,可以得到n个测试冷速下的结果,如式(5)所示:
[0021][0022]
5)连铸全冷速条件下铸坯奥氏体相分数的确定
[0023]
根据n个不同测试冷速下的奥氏体相分数随温度的变化关系,对每个测试冷速下
的结果进行离散化处理;同一相分数情况下,对n个不同测试冷速对应的温度采用相同的函数形式拟合,确定该相分数下对应温度与冷速的关系;对离散化的所有相分数均采用同样的方式拟合处理,据此可以确定任意冷速下的奥氏体相分数随温度的变化关系,具体过程如下:
[0024]
以第i个测试冷速c
r,i
为例,奥氏体相分数的离散化过程如公式(6)所示:
[0025][0026]
在离散化过程中,整个奥氏体相分数离散化后得到的相分数数量为m个,第j个奥氏体相分数f
γ,j
对应的离散化温度为离散化的区间增量δf
γ
=f
γ,i-f
γ,i-1
,其中f
γ,1
=0,0≤f
γ,j
≤100%,f
γ,m
=100%,则n个测试冷速下的离散化坐标如表1所示;采用同一函数形式,分别对每个奥氏体相分数下对应的离散化温度与冷速的关系进行拟合,得到m个不同奥氏体相分数下离散化温度与冷速的函数关系将任意冷速cr带入上述m个函数表达式,得到奥氏体相分数为f
γ,1
,...,f
γ,j
,...,f
γ,m
时对应的坐标进而确定任意冷速cr下的奥氏体相分数随温度的变化关系。
[0027]
表1 n个测试冷速下的离散化坐标及任意冷速cr下奥氏体相分数与温度的变化
[0028][0029]
6)连铸全冷速条件下铸坯铁素体及珠光体相分数、最终组织组成和含量的确定
[0030]
以任意冷速cr的情况为例,为铁素体转变区,为珠光体转变区,在得到连铸全冷速条件下铸坯奥氏体相分数的基础上,计算得到连铸全冷速条件下铸坯铁素体及珠光体相分数随温度的变化;根据奥氏体分解结束时珠光体相分数,确定铸坯最终组织的组成及含量,具体过程如下:
[0031]
在钢铁连铸全冷速条件下,任意冷速cr对应的铁素体相分数珠光体相
分数为:
[0032][0033]
根据公式(7),若奥氏体分解结束时珠光体相分数则铸坯最终组织为铁素体和珠光体,最终铁素体相分数为最终珠光体相分数为若奥氏体分解结束时珠光体相分数则铸坯最终组织全部为铁素体。
[0034]
7)连铸生产过程任意冷速下裂纹敏感温度区的确定
[0035]
以铁素体体积分数为40%时所对应的温度以及平衡态下奥氏体开始分解的温度作为裂纹敏感温度区的上下限温度,任意冷速cr时上下限温度由公式(8)确定,为生产实践提供参考:在连铸生产实践时,为了避免裂纹的产生,连铸坯应尽量避免在该温度区施加如弯曲、矫直、大压下等较大的变形。
[0036][0037]
进一步地,从实验成本、设备性能及结果准确性方面考虑,热膨胀试验测试的温度范围为1000℃-200℃,测试冷速的范围为5-30℃/min,至少进行5个不同冷速下的热膨胀测试试验。在连铸生产过程中,往往会出现一些极端冷速条件(如空冷区可能出现的极低冷速,冷速趋近零;强冷区域可能出现的较高冷速,连铸二冷区最高冷速一般不超过600℃/min,本发明不包含结晶器内的钢液冷却的情况),目前这些连铸极端冷速条件下因实验设备、测试条件、测试精度等无法达到要求,导致无法获取铸坯的相分数及裂纹敏感温度,严重制约了铸坯质量的提升。根据上述的预测方法,能够简单、快速、准确的预测连铸生产过程中所有可能出现的冷速条件下连铸坯的裂纹敏感温度区、奥氏体分解过程中任意温度下的相分数、奥氏体分解结束后的组织组成及含量等关键信息,为铸坯质量的调控和连铸工艺参数的优化奠定了基础。
[0038]
进一步地,在确定冷速与温度的关系时,所采用的函数形式不仅要符合奥氏体分解的物理本质,还得充分考虑函数形式的准确性、普适性、简洁性,因此,采用函数a-exp(b+c/cr)进行拟合,其中cr为冷速,a、b、c为拟合系数。
[0039]
进一步地,在实际生产过程中,由于奥氏体分解初期和末期、铁素体与珠光体转变的交叠期相分数与温度的变化关系较为缓慢,离散化的区间增量δf
γ
对结果的准确性具有重要影响;除了极个别钢种,连铸坯最终组织中珠光体的含量一般不会超过30%。因此,为兼顾预测结果的准确性和实际操作的简洁性,对于任意冷速cr下的测试结果而言,当及时,要求离散化的区间增量δf
γ
≤1%。本预测方法对钢铁连铸生产过程所有钢种均具有广泛的适用性、可移植性和参考价值,预测结果可以为连铸过程铸坯质量的调控及连铸二冷工艺参数的优化提供参考依据。
[0040]
本发明具有如下有益效果:
[0041]
1、本发明提供的一种连铸全冷速条件下铸坯裂纹敏感温度区及相分数的预测方
法,可用于连铸生产过程所有可能出现的冷速条件下,连铸坯的裂纹敏感温度区的简单、快速、准确预测,填补了连铸任意冷速下裂纹敏感温度区准确预测的空白。
[0042]
2、本发明提供的一种连铸全冷速条件下铸坯裂纹敏感温度区及相分数的预测方法,可用于连铸生产过程所有可能出现的冷速条件下,连铸坯在奥氏体分解过程任意温度下的相组成和相分数、奥氏体分解结束后的组织组成等关键信息,为有效避免铸坯裂纹、提高铸坯质量奠定了理论基础。
[0043]
3、本发明提供的一种连铸全冷速条件下铸坯裂纹敏感温度区及相分数的预测方法,适用于连铸生产过程所有可能出现的冷速条件,包括连铸空冷区可能出现的极低冷速和强冷区域可能出现的较高冷速等连铸极端情况,避免了目前这些极端冷速条件下因实验设备、测试条件、测试精度等无法达到要求,导致无法得到连铸坯相分数及裂纹敏感温度区等关键信息的情况。
[0044]
4、本发明提供的一种连铸全冷速条件下铸坯裂纹敏感温度区及相分数的预测方法,通过低冷速范围内的有限个不同测试冷速下热膨胀试验,结合常用的数据分析及相关技术手段,能够简单、快速、准确的预测出连铸生产过程所有可能出现的冷速条件下的结果,对钢铁连铸生产过程所有钢种均具有普适性、可移植性和参考价值,为连铸过程铸坯质量的调控及连铸生产工艺参数的优化提供了依据。
附图说明
[0045]
图1为本发明一种连铸全冷速条件下铸坯裂纹敏感温度区及相分数的预测方法中三类典型钢种连铸坯相对热膨胀量(dl/l0)及线性热膨胀系数(β)随温度的变化(以cr=20℃/min的测试冷速为例)。
[0046]
图2为本发明一种连铸全冷速条件下铸坯裂纹敏感温度区及相分数的预测方法中三类典型钢种连铸坯线性热膨胀系数的分峰结果(以cr=20℃/min的测试冷速为例)。
[0047]
图3为本发明一种连铸全冷速条件下铸坯裂纹敏感温度区及相分数的预测方法中三类典型钢种连铸坯奥氏体分解特征温度与冷速的拟合结果。
[0048]
图4为本发明一种连铸全冷速条件下铸坯裂纹敏感温度区及相分数的预测方法中三类典型钢种连铸坯奥氏体分解过程中各相体积分数随温度的变化(以cr=5、20℃/min的测试冷速为例,其余冷速的规律基本一致,为了图形简洁,不再给出)。
[0049]
图5为本发明一种任意冷速下连铸坯相分数及裂纹敏感温度区的预测方法中连铸生产过程任意冷速下奥氏体相分数确定过程的示意图。
[0050]
图6为本发明一种任意冷速下连铸坯相分数及裂纹敏感温度区的预测方法中三类典型钢种连铸坯奥氏体分解过程中各相体积分数随温度的变化及裂纹敏感温度区的结果(以cr=100℃/min为例,其余任意冷速下的结果均可采用同样的方法直接计算得到)。
具体实施方式
[0051]
本发明提供了一种连铸全冷速条件下铸坯裂纹敏感温度区及相分数的预测方法,下面将结合附图及实施例对本发明进一步说明,实施例包含三类典型的普碳钢,(a)、(b)、(c)分别代表三类典型的普碳钢连铸坯。具体实施方式如下:
[0052]
热膨胀试样的制备与试验测试:针对三类典型的普碳钢铸坯,沿拉坯方向,在距离
上下表面和侧面一定距离的柱状晶区内的取样;按要求将所有试样加工成直径为4mm,长度为25mm的圆柱体,测试之前用酒精超声清洗并烘干。在确保试样两端截面光滑且平行后,将圆柱试样夹在膨胀仪的两个石英推杆之间,温度制度如下:以5℃/min的升温速率从室温加热至1000℃,样品在1000℃下保温5min,然后将样品以5℃/min、10℃/min、15℃/min、20℃/min、30℃/min共5个不同的测试冷速冷却至200℃,全程高纯氩气保护,流量为80ml/min;采用位移传感器实时记录小圆柱试样与推杆之间因试样内部发生膨胀或收缩而产生的位移变化,最终输出降温过程中相对热膨胀量(dl/l0)、线性热膨胀系数(β)随温度的变化。
[0053]
基于测试得到的相对热膨胀量(dl/l0)、线性热膨胀系数(β)随温度的变化,根据本发明一种连铸全冷速条件下铸坯裂纹敏感温度区及相分数的预测方法的发明内容中步骤1)-7),得到了如图1所示的测试冷速cr=20℃/min下的相对热膨胀量(dl/l0)及线性热膨胀系数(β)随温度的变化,如图2所示的测试冷速cr=20℃/min下的线性热膨胀系数的分峰结果,如图3所示的奥氏体分解特征温度与冷速的拟合结果,如图4所示的测试冷速cr=5、20℃/min下的各基体相相分数随温度的变化,如图5所示的任意冷速下奥氏体相分数确定过程的示意图,如图6所示的任意冷速下(以cr=100℃/min为例)各基体相相分数随温度变化及裂纹敏感温度区的预测结果。
[0054]
从图1可知,以cr=20℃/min的测试冷速为例,在奥氏体分解过程中,由于基体相的类型及含量的变化,连铸坯试样的相对热膨胀量(dl/l0)和线性热膨胀系数(β)发生显著变化;奥氏体分解前后的稳定区域,相对热膨胀量(dl/l0)随温度呈线性变化,线性热膨胀系数(β)基本保持一致。线性热膨胀系数(β)的两个“隆起峰”分别代表奥氏体向铁素体的转变(图1中阶段ii)以及奥氏体向珠光体的转变(图1(b)、(c)中阶段iii),值得注意的是,图1(a)中所使用的钢种属于超低碳钢,奥氏体分解时直接转变为铁素体,不会发生珠光体的转变。
[0055]
从图2可知,以cr=20℃/min的测试冷速为例,基于gaussian函数的分峰处理和定量计算,得到了奥氏体γ
→
铁素体α转变的开始温度a
r3
、奥氏体γ
→
铁素体α转变的结束温度a
αf
、奥氏体γ
→
珠光体p转变的开始温度a
r1
、奥氏体γ
→
珠光体p转变的结束温度a
pf
、奥氏体γ
→
铁素体α及奥氏体γ
→
珠光体p转变的交点温度a
int
;并明确奥氏体分解过程中铁素体转变和珠光体转变的函数关系,为各基体相相分数随温度变化的定量计算提供基础。此外,本实施例中使用钢种的铁素体转变温度区间大于珠光体转变温度区间,(b)、(c)钢种铁素体转变和珠光体转变的温度区间分别为177.1℃和96℃、162.5℃和137.5℃。
[0056]
从图3可知,图中的“计算值(验证)”及“测试值(验证)”分别代表通过热力学软件计算得到的结果以及冷速cr为100℃/min时的测试结果,由图可知,该方法预测的特征温度与计算及实验测试结果基本一致。对于同一个实验钢种的奥氏体分解过程而言,所有的特征温度与冷速cr的变化都应遵循同一个物理规律,采用a-exp(b+c/cr)的函数形式来拟合奥氏体分解的特征温度与冷速cr的关系时,拟合度较高,且符合奥氏体分解的物理本质,其中a、b、c为系数。同时,根据预测结果,cr=100℃/min时,三个钢种奥氏体分解的起始温度分别为894.4℃和858.6℃、763.1℃和509.3℃、807.4℃和534.5℃;分解的温度区间δt分别为35.9℃、253.9℃和272.9℃。
[0057]
从图4可知,以cr=5、20℃/min的测试冷速为例,对于同一类试验钢种而言,不同冷速下各基体相相分数随温度的变化规律是一致的。随着冷速的增加,奥氏体分解的温度
区间整体下移,连铸坯最终的铁素体相数逐渐减小,珠光体相分数逐渐增加。对于同一测试冷速而言,随着温度的降低,奥氏体相分数逐渐减小,铁素体相分数逐渐增加;对于存在珠光体转变的钢种而言,珠光体相分数随温度降低而逐渐增加,当珠光体转变结束后基本稳定。此外,图中的f
α
(om)和f
p
(om)代表通过金相显微镜(om)对组织检测和统计,得到的连铸坯最终组织的类型和含量,结果如下:(a)类钢种奥氏体分解结束后连铸坯最终的组织为全铁素体;(b)类钢种为75.04%铁素体和24.96%珠光体(cr=20℃/min时)、82.19%铁素体和17.81%珠光体(cr=5℃/min时);(c)类钢种为82.53%铁素体和17.47%珠光体(cr=20℃/min时)、84.94%铁素体和15.06%珠光体(cr=5℃/min时)。
[0058]
从图5可知,当奥氏体相分数为f
γ,j
时,5个测试冷速所对应的点分别为a1、a2、a3、a4、a5,根据5个点所对应的坐标,可以拟合回归出奥氏体相分数为f
γ,j
时离散化温度与冷速的函数关系f
γ,j
:在此基础上,可以计算得到任意冷速cr下奥氏体相分数为f
γ,j
时对应的点ak;随着奥氏体相分数f
γ,j
从0取到100%,可以按照同样的方法得到一组与之对应的温度,进而可以得到任意冷速cr下奥氏体相分数与温度的变化关系。
[0059]
从图6可知,以cr=100℃/min的任意冷速为例,连铸全冷速条件下铸坯相分数及裂纹敏感温度区的预测结果如图所示。由图可知,该方法能够简单快速地预测冷速cr为100℃/min时奥氏体分解过程各基体相相分数随温度的变化,且该方法预测得到的铸坯最终各基体相相分数的结果较为准确(预测结果与试验测试结果基本一致);此外,奥氏体分解的典型的三个特征温度a
r3
、a
int
、a
pf
与试验结果基本一致(图3中的“测试值(验证)”与预测结果基本一致);该方法可以简单、快速、准确预测连铸全冷速条件下任意冷速时铸坯相分数及裂纹敏感温度区。三种试验钢种在cr=100℃/min的任意冷速时的裂纹敏感温度区分别为915.0℃~874.2℃、842.4℃~664.7℃、877.5℃~712.0℃,在连铸实际生产中,应尽量避免在该温度区间内对铸坯施加较大的变形和外力,如弯曲、矫直、大压下等较大的变形。
[0060]
最后需要说明的是,以上实施例仅用以说明本发明的技术方案而非限制技术方案,本领域的普通技术人员应当理解,那些对本发明的技术方案进行修改或者等同替换,而不脱离本技术方案的宗旨和范围,均应涵盖在本发明的权利要求范围当中。