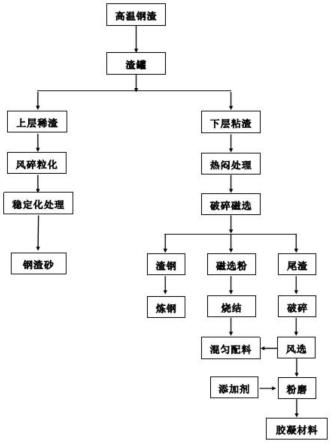
1.本发明涉及资源综合利用技术领域,具体为一种钢渣分类处理及资源化利用方法。
背景技术:2.钢渣的资源化利用一直是钢铁企业面临的难题,资源化利用率不足30%。热态钢渣的冷却粒化处理方式与粒化后的钢渣资源化利用方式紧密相关。目前,普遍采用热闷法、滚筒法、风碎法、热泼法等工艺对热态钢渣进行冷却粒化,根据不同的处理效果再结合不用的钢渣利用途径选择进一步加工方式,热闷工艺处理后的钢渣通过破碎磁选回收不同粒度和品味的渣钢返回转炉、烧结利用,磁选后的尾渣利用途径较多,根本原因在于钢渣尾渣中p含量较高导致返回烧结利用会导致铁水中p含量上升,如此循环则会导致p在冶炼过程中的循环富集,增加转炉脱p成本,因此钢渣返回烧结利用比例较低,大部分寻求在水泥、建材、混凝土等领域的应用,由于在这些方面的应用均受制于钢渣中游离cao含量影响使用比例也较低。总体来看,钢渣内部利用主要受制其自身含p较高的问题而导致用量有限,在水泥、建材、混凝土等外部利用受制于其自身含游离cao含量较高用量也比较有限。
3.实现钢渣中p的分离,从而尽可能提高钢渣返回钢铁冶炼生产循环利用的比例是提高钢渣处理效率和利用价值的重要途径。国内外围绕钢渣脱磷的研究包括磁选磨细后通过浮选或者湿法浸取等方式。
4.申请号为201910915755.7的专利《一种从脱磷钢渣中分离磷和制备磷肥的方
5.法》其特征在于将脱磷钢渣在熔融状态下进行氧化处理,冷却后对其进行破碎研磨。然后将脱磷钢渣在水溶液中进行选择性浸出,控制矿浆的ph值为3.0~4.5,使脱磷钢渣中富磷的固溶体相溶解并分离,反应后得到低磷残渣和含磷浸出液。再通过向含磷浸出液中添加碱性物质,升高浸出液的ph值,使浸出液中的磷形成磷酸钙盐沉淀。分离后的磷酸钙盐沉淀可直接作为磷肥使用,低磷残渣则在烧结或炼钢中使用。该发明方案为了实现选择性浸出的效果,需要对脱磷钢渣在熔融态下进行喷吹氧化或者空气氧化处理,这会导致钢渣中金属铁的氧化而降低钢渣回收利用的价值,另外该发明方案浸出过程引入盐酸,导致低p钢渣中残留cl离子而影响返回烧结利用效果。
6.申请号为201510138476.6的专利《一种对转炉渣中磷进行分离及回收利用转炉渣的方法》其特征在于将碱度2.0~10.0,含fe总量重量百分比5%~30%,含p2o5总量重量百分比0.5%~20%的转炉渣倒入底部平铺适量多空钙质颗粒的容器内,在1300~1600℃保温10~150分钟,冷却至室温后将容器顶部包含多空钙质颗粒的转炉渣作为炼铁烧结料使用。本发明方案设计思路通过cao-sio2-p2o5-30%feo系三元相图分析结合实验室试验基础上提出发明方案,没有考虑实际应用钙质颗粒导致钢渣熔点上升,在1300~1600℃温度区间钢渣的粘度增加,处于底部的低磷高feo钢渣很难通过重力作用而上浮至渣面顶部。
7.申请号为201510318286.2的专利《一种钢渣除磷循环利用方法》其特征在于将钢渣破碎并磨细后,用柠檬酸-naoh-hcl缓冲液浸出处理,得到含磷滤液和低磷钢渣;将所述
低磷钢渣进行干燥处理后,返回烧结、炼铁或炼钢工序,进行循环利用。该发明方案采用对钢渣进行破碎磨细后用柠檬酸-naoh-hcl缓冲液浸出脱磷,缓冲液中hcl导致低p钢渣中残留cl离子而影响返回烧结利用效果。
8.申请号为201811509502.1的专利《一种钢渣回收利用方法》其特征在于钢渣采用浮选的方式进行脱磷处理后再加入到烧结、炼铁或者炼钢工序中。该发明技术方案脱磷方式采用浮选脱磷,将球磨后的细钢渣粉置入加水的槽中,并搅拌调节为浓度10~20%的矿浆,将调浆后的溶液送入浮选装置,同时依次加入ph调节剂、抑制剂、表面活化剂和捕收剂;药剂全部加入后2min开始吹泡浮选,8~10min后结束,得到富含磷的上浮物和低磷的下沉物;所述表面活性剂采用十二烷基磺酸钠并用于改变含磷成分矿物表面化学组成,使其易于吸附捕收剂;捕收剂采用油酸钠并用于改变含磷成分矿物表面疏水性,使其利于黏附于气泡并上浮。钢渣浮选脱磷效率不高,产生的污水量比较大,所用表面活性剂na盐,钠作为一种低熔点碱金属残留在低磷钢渣中返回烧结和炼铁利用会对高炉稳定顺行产生影响。
9.申请号为201811375255.0的专利《一种利用转炉钢渣生产弱酸性液体肥料的
10.方法》其特征在于括用生物质灰渣对熔融转炉钢渣进行改质处理,再将改质转炉钢渣破碎磨细,磨细的转炉钢渣加入苹果酸-hno3混合溶液中,搅拌使转炉钢渣中的钙、硅、磷等元素溶出,之后向滤液中加入氨水溶液,调整滤液酸碱性和成分,获得同时含有氮、钾、镁、钙、硅、铁等多元素的液体肥料。本发明技术方案通过用生物质灰渣对钢渣改质经磨细后采用酸-hno3混合溶液在脱除钢渣中p的同时还脱除镁、钙、硅、铁等多元素,制备液体肥料,其钢渣脱p的目的和最终产品为制备液体肥料。
11.申请号为202111194369.7的专利《一种提高混匀矿中钢渣配比的方法》其特征在于对钢渣进行破碎处理,要求破碎后钢渣的粒度≤10mm;对钢渣进行磁选处理,要求磁选后钢渣的全铁含量为18%≤tfe≤23%;根据炼钢冶炼不同钢种对铁水p含量的要求,调整参与混匀配矿的配料结构;混匀矿的烧结方式为“厚料层、慢机速”。该技术方案主要基于钢渣破碎磁选加工分类利用钢渣,通过结合不同冶炼钢渣对铁水p含量要求来确定烧结配用钢渣的比例,并没有针对钢渣中p的存在形态和特点通过其它技术途径实现p分离与去除。
12.申请号为202011610707.6的专利《一种冶金渣零排放综合利用方法》其特征在于将物料分为0~250mm及250mm以上二组,分为0~30mm及30~250mm二组,将0~30mm的钢渣经过滚筒磁选机进行回收经过5mm筛,得到0~5mm及5~30mm二组最终分选块;将250mm以上的钢渣经过破碎和电磁吸的复选,后得到250mm以上和尾渣;其中30~250mm钢渣进入棒磨机破碎,筛下物30~40mm进入钢渣磁鼓精选机回收,精矿经由5mm震动筛筛分,0~5mm的全铁品位60%的磁选粉;筛上的40~250mm钢渣再经过电磁吸的复选后得到40~250mm组。该技术方案主要通过破碎分级磁选的方式完成钢渣中含铁原料的回收,且仅局限于对冷态钢渣进行加工,没有结合热态钢渣特性在钢渣处理阶段实现钢渣更好的破碎粒化,避免后续破碎加工成本高,且没有考虑回收含铁料后的尾渣的利用问题。
13.申请号为202110425811.6的专利《一种钢渣资源化利用方法》其特征在于将钢渣筛分,选取0.075-1.18mm粒径的钢渣颗粒;对筛分后的钢渣颗粒用酸进行处理,降低钢渣里的游离氧化镁氧化钙,改善安定性,得到钢渣砂。本发明主要仅针对0.075-1.18mm粒径的钢渣的安定性问题提出了一种解决方案。
14.申请号为202011590213.6的专利《一种钢渣处理工艺方法》其特征在于将钢渣倾
翻装置的倾动渣盆将渣子倒在破碎床上;钢渣碾压车沿着破碎床运动将钢渣破碎,并且在碾压过程中,向渣中喷入冷却水;将碾压并喷淋后的钢渣送至焖罐内进行焖渣;将焖好的渣子进行多级除铁、破碎筛分处理;经多级除铁及破碎筛分处理后的渣钢返回炼钢回收利用;经多级除铁及破碎筛分处理后的余料经棒磨破碎后,经多级磁选破碎处理;经多级磁选破碎处理后合格的磁选粉进行回收利用,其余合格尾渣送到尾渣矿外卖做钢渣水泥。该技术方案通过将热态渣先破碎后采用焖罐焖渣,再通过破碎棒磨磁选回收渣钢和磁选粉,尾渣做钢渣水泥,主要涉及是焖罐工艺,没有对热态钢渣进行分类处理。
15.经检索,涉及钢渣处理及资源化利用方面的专利很多,但是均存在以下几个方面的问题:一是没有从全量化解决钢渣资源化利用的角度去设计技术方案;二是没有将钢渣的处理工艺与后续钢渣资源化利用有效统一衔接起来;三是针对钢渣在钢渣企业内部循环利用和在外部循环利用对钢渣性能要求区别没有做针对性处理;四是针对钢渣内部循环利用存在的p的富集问题欠缺经济合理可实施的解决方案;五是针对钢渣在社会利用主要是建材、道路、水泥等领域涉及的游离氧化钙偏高活性偏低等共性问题欠缺经济合理可实施的解决方案。
技术实现要素:16.(一)解决的技术问题
17.针对现有技术的不足,本发明提供了一种钢渣分类处理及资源化利用方法,解决了现有技术中,没有从全量化解决钢渣资源化利用的角度去设计技术方案,没有将钢渣的处理工艺与后续钢渣资源化利用有效统一衔接起来,针对钢渣在钢渣企业内部循环利用和在外部循环利用对钢渣性能要求区别没有做针对性处理,针对钢渣内部循环利用存在的p的富集问题欠缺经济合理可实施的解决方案,针对钢渣在社会利用主要是建材、道路、水泥等领域涉及的游离氧化钙偏高活性偏低等共性问题欠缺经济合理可实施的解决方案的问题。
18.(二)技术方案
19.为实现以上目的,本发明通过以下技术方案予以实现:一种钢渣分类处理及资源化利用方法,具体操作如下:
20.s1、将盛装转电炉排出的高温钢渣的渣罐运至风碎处理线,将渣罐上部的高温液态钢渣进行风碎处理,剩余钢渣采用热闷处理,热闷处理后钢渣通过破碎、磁选、棒磨、磁选等工艺处理,得到渣钢、磁选粉和尾渣,其中,渣钢返回转电炉循环利用,磁选粉返回烧结循环利用,尾渣通过破碎后经风选,选出一定粒度钢渣返回烧结利用,剩余钢渣在添加剂作用下粉磨至一定比表面积的高性能胶凝材料;
21.s2、将步骤s1中渣罐上部高温液态钢渣温度≧1400℃,钢渣粘度值低于0.40pa.s,采用风碎工艺处理,当钢渣温度或者粘度不满足风碎处理要求时,剩余钢渣采用热闷工艺进行粒化冷却处理,经风碎工艺处理后钢渣粒度≧5mm比例≦5%,经热闷工艺处理后钢渣粒度≧20mm比例≦30%;
22.s3、对步骤s2中经风碎处理后的钢渣进行稳定化处理,将钢渣装入渣池,渣池中水温保持80~90℃,同时向渣池中通入co2气体,co2气体加入量为渣池中钢渣质量的0%~10%,反应结束后,钢渣中游离cao含量≦1.0%,可以作为细骨料用于道路、建材等混凝土
制品中;
23.s4、对步骤s2中经热闷处理后的钢渣,先通过150mm筛,选出粒度≧150mm的渣钢,再进行破碎,过30mm筛,选出粒度≧30mm的渣钢,再进行棒磨,过10mm筛,选出粒度≧10mm的渣钢,再进行棒磨,磁选,得到粒度≦10mm的磁选粉和尾渣。渣钢返回转(电)炉炼钢利用,磁选粉返回烧结利用;
24.s5、对步骤s4中粒度≦10mm的尾渣经过辊压破碎,风选分离粒度≧200目的钢渣粉,返回烧结利用;粒度≦200目的钢渣粉进一步粉磨;
25.s6、对步骤s5中粒度≦200目的钢渣粉进一步粉磨,并再粉磨过程中加入0~1%的助磨剂,得到比表面积≧500m2/kg的高性能胶凝材料,其7d活性指数≧70%,28d活性指数≧90%,游离cao含量≦2.0%,其中助磨剂为三乙醇胺、三聚磷酸钠和无水乙醇的混合物。其中三乙醇胺质量分数20~45%,三聚磷酸钠质量分数20~40%,无水乙醇质量分数15~30%。
26.(三)有益效果
27.本发明提供了一种钢渣分类处理及资源化利用方法。具备以下有益效果:
28.该钢渣分类处理及资源化利用方法,结合高温熔融钢渣特性,结合钢渣后续全量高效资源化利用系统考虑,根据钢渣中各矿物相的特点及p的赋存形态特点合理运用钢渣冷却粒化处理工艺进行分类处理,从而在源头实现钢渣中不同p和fe含量的分级,对于含p高的钢渣采用风碎处理工艺进行粒化处理,处理后的风碎钢渣粒度合理,经过稳定化处理后可以直接作为细骨料用于道路、建材等混凝土制品中;而对于p含量低的钢渣采用热闷处理后通过破碎磁选加工分类,渣钢返回炼钢循环利用,磁选粉返回烧结利用,而尾渣先通过破碎,采用风选方式将粒度大于200目低p部分分离出来,返回混匀矿循环利用,粒度大于200目部分在加入添加剂的作用下粉磨至比表面积大于500m2/kg的高性能胶凝材料,从而实现钢渣的分类处理及全量资源化利用。
29.具体的,有益效果为:
30.1)利用高温液态钢渣中,p主要赋存于c2s、c3s中,而比重相对较小的硅酸盐相c2s、c3s容易向渣罐液面上浮,而含铁较高含p低的c2f、ro等则容易下沉;通过将渣罐上部液态钢渣采用风碎处理,从源头实现了不同p含量钢渣的分类处理,为后续钢渣分类处理及利用奠定了基础;
31.2)采用破碎磁选,风选等工艺分离回收低p钢渣返回烧结利用;
32.3)针对高p风碎粒化钢渣通过稳定化处理直接作为细骨料用于道路、建材等混凝土制品中;
33.4)高p尾渣通过添加剂和粉磨作用下获得高比表钢渣粉,实现钢渣稳定化和提高胶凝活性,用作胶凝材料。
附图说明
34.图1为本发明流程示意图;
35.图2为cao-sio2-p2o5-30%feo系三元相图。
具体实施方式
36.下面将结合本发明实施例中的附图,对本发明实施例中的技术方案进行清楚、完整地描述,显然,所描述的实施例仅仅是本发明一部分实施例,而不是全部的实施例。基于本发明中的实施例,本领域普通技术人员在没有做出创造性劳动前提下所获得的所有其他实施例,都属于本发明保护的范围。
37.请参阅图1-2,本发明提供一种技术方案:一种钢渣分类处理及资源化利用方法,具体操作如下:
38.s1、将盛装转电炉排出的高温钢渣的渣罐运至风碎处理线,将渣罐上部的高温液态钢渣进行风碎处理,剩余钢渣采用热闷处理,热闷处理后钢渣通过破碎、磁选、棒磨、磁选等工艺处理,得到渣钢、磁选粉和尾渣,其中,渣钢返回转电炉循环利用,磁选粉返回烧结循环利用,尾渣通过破碎后经风选,选出一定粒度钢渣返回烧结利用,剩余钢渣在添加剂作用下粉磨至一定比表面积的高性能胶凝材料;
39.s2、将步骤s1中渣罐上部高温液态钢渣温度≧1400℃,钢渣粘度值低于0.40pa.s,采用风碎工艺处理,当钢渣温度或者粘度不满足风碎处理要求时,剩余钢渣采用热闷工艺进行粒化冷却处理,经风碎工艺处理后钢渣粒度≧5mm比例≦5%,经热闷工艺处理后钢渣粒度≧20mm比例≦30%;
40.s3、对步骤s2中经风碎处理后的钢渣进行稳定化处理,将钢渣装入渣池,渣池中水温保持80~90℃,同时向渣池中通入co2气体,co2气体加入量为渣池中钢渣质量的0%~10%,反应结束后,钢渣中游离cao含量≦1.0%,可以作为细骨料用于道路、建材等混凝土制品中;
41.s4、对步骤s2中经热闷处理后的钢渣,先通过150mm筛,选出粒度≧150mm的渣钢,再进行破碎,过30mm筛,选出粒度≧30mm的渣钢,再进行棒磨,过10mm筛,选出粒度≧10mm的渣钢,再进行棒磨,磁选,得到粒度≦10mm的磁选粉和尾渣。渣钢返回转(电)炉炼钢利用,磁选粉返回烧结利用;
42.s5、对步骤s4中粒度≦10mm的尾渣经过辊压破碎,风选分离粒度≧200目的钢渣粉,返回烧结利用;粒度≦200目的钢渣粉进一步粉磨;
43.s6、对步骤s5中粒度≦200目的钢渣粉进一步粉磨,并再粉磨过程中加入0~1%的助磨剂,得到比表面积≧500m2/kg的高性能胶凝材料,其7d活性指数≧70%,28d活性指数≧90%,游离cao含量≦2.0%,其中助磨剂为三乙醇胺、三聚磷酸钠和无水乙醇的混合物。其中三乙醇胺质量分数20~45%,三聚磷酸钠质量分数20~40%,无水乙醇质量分数15~30%。
44.通过本发明方法产生的实施效果在于:
45.利用高温液态钢渣中,p主要赋存于c2s、c3s中,而比重相对较小的硅酸盐相c2s、c3s容易向渣罐液面上浮,而含铁较高含p低的c2f、ro等则容易下沉;通过将渣罐上部液态钢渣采用风碎处理,从源头实现了不同p含量钢渣的分类处理,为后续钢渣分类处理及利用奠定了基础;
46.通过对风碎钢渣粒度控制,并采用水浴下通入co2方式控制风碎钢渣游离cao含量≦1.0%,使风碎钢渣可直接作为细骨料用于道路、建材等混凝土制品中,而不用返回到烧结利用避免了高p钢渣造成的铁水p含量偏高问题,实现风碎钢渣的高效资源化利用;
47.通过将低p高铁的钢渣经过热闷处理,并通过破碎、磁选及棒磨、磁选后,得到不同粒度的渣钢产品返回炼钢利用,低p磁选粉返回烧结利用,尾渣通过辊压破碎风选出≧200目的高铁低p部分返回烧结利用,小于200目的高p部分在助磨剂作用下粉磨至比表面积≧500m2/kg的钢渣微粉,得到一种高活性胶凝材料。
48.本发明通过分析钢渣自身性能和矿物组成特点,根据资源化利用最优化原则,合理分类处理钢渣,并针对钢渣在返回内部利用和社会化利用过程中存在的主要问题采取了有针对性的创新技术措施,在充分利用钢渣自身性能特点基础上,将钢渣的处理与资源化利用作为一个整体考虑提出了一种钢渣分类处理及资源化利用方法。
49.实施例1
50.300t转炉铁水装入量285t,废钢装入量45t,入炉铁水p含量0.102%,排出的高温钢渣,重28吨,温度1512℃,粘度0.65pa.s,将渣罐上部液态渣通过风碎处理,直至液态渣流动性变差无法从渣罐口自然流出为止,剩余钢渣约14吨,采用热闷处理。
51.风碎渣p含量1.25%,粒度≧5mm占比4.3%;热闷钢渣p含量0.95%,粒度≧20mm占比25%。将风碎处理的钢渣送进渣池并加满水,水温保持在80~90℃,同时通入650kgco2气体,占风碎钢渣质量的4.6%,反应结束后风碎渣游离cao含量0.6%,用作混凝土细集料替代细砂,替代比50%。
52.热闷钢渣先通过150mm筛,选出粒度≧150mm的渣钢105kg,再进行破碎,过30mm筛,选出粒度≧30mm的渣钢230kg,再进行棒磨,过10mm筛,选出粒度≧10mm的渣钢360kg,渣钢全部通过废钢斗加入返回转炉炼钢利用,再进行棒磨,磁选,得到粒度≦10mm的磁选粉2.01t,p含量0.44%尾渣,配入烧结使用,吨烧结矿配入25kg。尾渣约12t,通过辊压机破碎后经过风选,选出粒度大于200目的钢渣粉1.5t,p含量0.67%,返回混匀矿利用,剩余200目以上部分通过球磨,并加入0.4%助磨剂,助磨剂组成为:三乙醇胺质量分数35%,三聚磷酸钠质量分数40%,无水乙醇质量分数25%,磨制钢渣微粉比表面积525m2/kg,游离cao含量1.4%,7d活性指数72%,28d活性指数96%。通过该技术方案,实现低p高铁部分钢渣返回生产利用,高p低铁钢渣通过稳定化处理,及磨制钢渣粉实现全量资源化利用。
53.实施例2
54.300t转炉铁水装入量288t,废钢装入量43t,入炉铁水p含量0.105%,排出的高温钢渣,重29吨,温度1526℃,粘度0.54pa.s,将渣罐上部液态渣通过风碎处理,直至液态渣流动性变差无法从渣罐口自然流出为止,剩余钢渣约12吨,采用热闷处理。
55.风碎渣p含量1.34%,粒度≧5mm占比3.7%;热闷钢渣p含量1.05%,粒度≧20mm占比28%。将风碎处理的钢渣送进渣池并加满水,水温保持在80~90℃,同时通入1.5tco2气体,占风碎钢渣质量的8.8%,反应结束后风碎渣游离cao含量0.2%,用作混凝土细集料替代细砂,替代比50%。
56.热闷钢渣先通过150mm筛,选出粒度≧150mm的渣钢116kg,再进行破碎,过30mm筛,选出粒度≧30mm的渣钢212kg,再进行棒磨,过10mm筛,选出粒度≧10mm的渣钢336kg,渣钢全部通过废钢斗加入返回转炉炼钢利用,再进行棒磨,磁选,得到粒度≦10mm的磁选粉1.95t,p含量0.46%尾渣,配入烧结使用,吨烧结矿配入25kg。尾渣约10t,通过辊压机破碎后经过风选,选出粒度大于200目的钢渣粉1.2t,p含量0.63%,返回混匀矿利用,剩余200目以上部分通过球磨,并加入0.7%助磨剂,助磨剂组成为:三乙醇胺质量分数40%,三聚磷酸
钠质量分数40%,无水乙醇质量分数20%,磨制钢渣微粉比表面积536m2/kg,游离cao含量1.0%,7d活性指数76%,28d活性指数95%。
57.通过该技术方案,实现低p高铁部分钢渣返回生产利用,高p低铁钢渣通过稳定化处理,及磨制钢渣粉实现全量资源化利用。
58.综上所述,该钢渣分类处理及资源化利用方法,结合高温熔融钢渣特性,结合钢渣后续全量高效资源化利用系统考虑,根据钢渣中各矿物相的特点及p的赋存形态特点合理运用钢渣冷却粒化处理工艺进行分类处理,从而在源头实现钢渣中不同p和fe含量的分级,对于含p高的钢渣采用风碎处理工艺进行粒化处理,处理后的风碎钢渣粒度合理,经过稳定化处理后可以直接作为细骨料用于道路、建材等混凝土制品中;而对于p含量低的钢渣采用热闷处理后通过破碎磁选加工分类,渣钢返回炼钢循环利用,磁选粉返回烧结利用,而尾渣先通过破碎,采用风选方式将粒度大于200目低p部分分离出来,返回混匀矿循环利用,粒度大于200目部分在加入添加剂的作用下粉磨至比表面积大于500m2/kg的高性能胶凝材料,从而实现钢渣的分类处理及全量资源化利用。
59.具体的,有益效果为:
60.1)利用高温液态钢渣中,p主要赋存于c2s、c3s中,而比重相对较小的硅酸盐相c2s、c3s容易向渣罐液面上浮,而含铁较高含p低的c2f、ro等则容易下沉;通过将渣罐上部液态钢渣采用风碎处理,从源头实现了不同p含量钢渣的分类处理,为后续钢渣分类处理及利用奠定了基础;
61.2)采用破碎磁选,风选等工艺分离回收低p钢渣返回烧结利用;
62.3)针对高p风碎粒化钢渣通过稳定化处理直接作为细骨料用于道路、建材等混凝土制品中;
63.4)高p尾渣通过添加剂和粉磨作用下获得高比表钢渣粉,实现钢渣稳定化和提高胶凝活性,用作胶凝材料。
64.需要说明的是,在本文中,诸如第一和第二等之类的关系术语仅仅用来将一个实体或者操作与另一个实体或操作区分开来,而不一定要求或者暗示这些实体或操作之间存在任何这种实际的关系或者顺序。而且,术语“包括”、“包含”或者其任何其他变体意在涵盖非排他性的包含,从而使得包括一系列要素的过程、方法、物品或者设备不仅包括那些要素,而且还包括没有明确列出的其他要素,或者是还包括为这种过程、方法、物品或者设备所固有的要素。
65.尽管已经示出和描述了本发明的实施例,对于本领域的普通技术人员而言,可以理解在不脱离本发明的原理和精神的情况下可以对这些实施例进行多种变化、修改、替换和变型,本发明的范围由所附权利要求及其等同物限定。